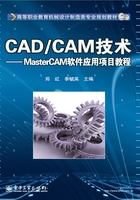
第三步 实施
1.采用MasterCAM进行图形的绘制
具体操作方式如下。
(1)启动MasterCAM铣削加工模块:。键盘【F9】键可以调取显示或取消显示直角坐标系。
(2)选择主功能表中的“C绘图\R矩形\1一点”,在弹出如图1-7所示的对话框中进行如下设置。在“矩形之宽度”中输入“125”,在“矩形之高度”中输入“110”,点的位置选择中间的黄色小矩形,单击“确定”按钮。

图1-7 “绘制矩形”对话框
(3)这时可以看到跟随鼠标位置移动的一个矩形,如果看不到,可以单击快捷命令图标区中的“适度化”图标,以使图形能够显示到屏幕区域。
(4)系统提示选择矩形中心点位置,即在屏幕左上角显示抓点方式,并在主功能表位置显示一些点的形式,这时可以通过键盘输入坐标的位置(0,0),也可以通过鼠标捕捉到直角坐标“十”字交叉线的交点(注意:键盘【F9】键用来切换“十”字交叉线的显示和隐藏),即选择原点(0,0)作为矩形的中心点,如图1-8所示。

图1-8 选择原点作为矩形的中心点
(5)矩形绘制完成后,可以单击主功能表下面的“回主功能表”按钮,回到主功能表的最上一级。选择主功能表中的“X转换\O单体补正”,在弹出的对话框中的“处理方式”中选择“复制”单选按钮,“次数”输入“1”,“补正之距离”输入“20”,如图1-9所示。单击“确定”按钮之后,鼠标左键单击矩形下面的直线,使其变成黄色即为选中,如图1-10所示;并在直线上方任一点单击鼠标左键,确定补正方向是向上偏移的,得到补正的直线如图1-11所示。

图1-9 “补正”对话框

图1-10 选择矩形下面的直线

图1-11 得到补正的直线
同理,根据所给零件图尺寸,补正其他所需要的直线。按键盘【Esc】键返回主功能表的上一级菜单,继续选择“O单体补正”,补正距离分别为10、10、10、35、35、60等(注意如果补正距离相同可以不必每次都返回上一级菜单),补正结果如图1-12所示。

图1-12 补正其他所需要的直线
(6)现在需要将一些直线连接起来,在主功能表中选择“C绘图\L直线\E任意线段”,连接两段斜线,如图1-13所示。

图1-13 连接两段斜线
(7)单击快捷命令图标区的“删除”图标,用鼠标左键单击要删除的辅助直线。单击快捷命令图标区的“修整两个物体”图标
对剩下的直线进行修整两个物体,注意修剪两条交叉的直线时,用鼠标左键分别单击的是两条线段需要保留的部分。单击快捷命令图标区的“清除颜色”图标
,得到修剪之后的图形,如图1-14所示。

图1-14 修剪之后的图形
(8)单击快捷命令图标区的“倒圆角”图标,倒圆角2-R20和4-R10,注意先修改圆角半径
,在屏幕下方的信息提示区
输入相应的圆角半径值后按【Enter】键,然后分别单击圆角位置的两条直线,倒圆角如图1-15所示。

图1-15 倒圆角
(9)在主功能表中选择“C绘图\P点\P指定位置”,用键盘输入坐标值:(50.5,43)、(-50.5,43)、(50.5,-43)、(-50.5,-43)(注意一定是半角状态的逗号否则系统不识别),如图1-16所示。

图1-16 绘制钻孔的中心点
上面已经用 MasterCAM 进行了必要的图形绘制,下面来进行挖槽和钻孔刀具路径的规划。
2.采用MasterCAM进行刀具路径的规划
(1)进行挖槽粗、精加工刀具路径的规划
① 选择主功能表中的“T刀具路径\P挖槽\C串连”,系统提示。
② 用鼠标左键单击已经绘制的槽图形的任意位置,出现了一个黄色的箭头,如图1-17所示。然后选择主菜单区的“D执行”。

图1-17 选择挖槽形状
③ 弹出“挖槽(一般挖槽)”对话框,如图1-18所示。在弹出的对话框中选择“刀具参数”选项卡,在空白区域单击鼠标右键,选择“从刀具库中选取刀具”选项。

图1-18 从刀具库中选取刀具
④ 这时弹出“刀具管理”对话框,拖动右侧滚动条选择一把φ16 的平刀刀具,如图1-19所示。然后单击“确定”按钮,这时在空白区域出现了图标。

图1-19 选一把φ16的平刀刀具
⑤ 在“挖槽(一般挖槽)”对话框中有“刀具参数”、“挖槽参数”和“粗铣/精修参数”三个选项卡,接下来首先规划“刀具参数”选项卡,主要设定进给率“1000”、Z轴进给率“100”、提刀速率“1000”以及主轴转速“1000”和冷却液“喷雾M07”等,如图1-20所示。具体输入参数值需要根据实际工作条件来调整,并不是一成不变的。

图1-20 “刀具参数”选项卡
⑥ 单击“挖槽参数”标签,在“挖槽参数”选项卡中主要做如下设置,参考高度“30”、绝对坐标(参考高度是刀具由快进到工进相互转换时提升的高度,不宜设置过大;而安全高度是在程序开始和结尾处提升的高度,所以安全高度要设置到一个不会撞刀的位置),进给下刀位置“5”、增量坐标,要加工的表面“0”、绝对坐标,加工深度“-13”、绝对坐标,如图1-21所示。

图1-21 “挖槽参数”选项卡
⑦ 选中“分层铣深”复选框,在弹出的“Z 轴分层铣深设定”对话框中,设置最大粗切深度“1.0”、精修次数“0”、精修量“1.0”,选中“不提刀”复选项,在“分层铣深之顺序”选项区域中选中“依照区域”单选按钮,如图1-22所示。

图1-22 Z轴分层铣深设定
⑧ 在“粗铣/精修参数”选项卡中,选中“粗铣”复选框,单击“等距环切图标,刀间距设置刀具直径的“75%”,选中“精修”复选框,设定精修次数为“1”,精修量为“0.2”,系统会在粗铣之后对槽进行精修,如图1-23所示。

图1-23 “粗铣/精修参数”选项卡
⑨ 单击“确定”按钮之后完成了挖槽加工的刀具路径设置,下面对生成的刀具路径进行观察和模拟仿真。选择主功能表中的“T 刀具路径/J 工作设定”,“工作设定”对话框中进行设置:X“125”,Y“110”,Z“125”;选中“显示工件”复选框,这样工件的线框会显示到工作区域当中,如图1-24所示。

图1-24 “工作设定”对话框
单击快捷命令图标区的“视角-等角视图”图标,观看生成的刀具路径,如图1-25所示。

图1-25 挖槽粗、精加工刀具路径
选择主功能表中的“T 刀具路径\O 操作管理”,单击“实体切削验证”按钮,然后单击“播放”按钮
,如图1-26所示。

图1-26 实体切削验证
进行实体切削验证结果,如图1-27所示。

图1-27 挖槽的实体切削验证结果
(2)进行钻孔刀具路径的规划
① 在主功能表中选择“T刀具路径\D钻孔\M手动输入”,用鼠标左键依次单击已经绘制的四个孔的中心点,如图1-28所示。系统提示,按【Esc】按钮退出选择,选择主菜单区的“D执行”,弹出“深孔钻-无啄钻”对话框。

图1-28 选择已经绘制的四个孔的中心点
② 在该对话框中的空白区域单击鼠标右键,选择“从刀具库中选取刀具”选项,如图1-29所示。

图1-29 从刀具库中选择刀具
③ 在弹出的“刀具管理”对话框中,选择一把φ6的钻头刀具,如图1-30所示。

图1-30 选择一把φ6的钻头刀具
④ 在“刀具参数”选项卡中,主要设定进给率“30”、主轴转速“300”、冷却液“喷雾M07”等,如图1-31所示。

图1-31 “刀具参数”选项卡
⑤ 在“自设钻孔参数”选项卡中,设置参考高度“5.0”、要加工的表面“0”、深度“-30”、钻孔循环“深孔钻(G81/G82)”,注意设定的钻孔深度要大于坯料的厚度,保证钻透,如图1-32所示。

图1-32 “自设钻孔参数”选项卡
⑥ 生成钻孔的刀具路径,如图1-33所示。钻孔刀具路径实体切削验证结果,如图1-34所示。

图1-33 钻孔刀具路径

图1-34 钻孔的实体切削验证结果