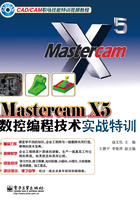
1.2 鼠标面壳大身铜公编程特训
例题1-1
铜公说明:如图1-1所示是本节将要编程的产品、模具及铜公图。这是一款鼠标的面壳,注塑面壳的前模型腔由于尖角部分太多,无法直接用CNC加工到位,需要设计并加工出铜公进行EDM放电加工才行。精加工电极通常称为幼公,粗加工电极称为粗公。本章将对主要成型的大身外形铜公的粗公和幼公进行数控编程。任务:根据已经分模及拆好的铜公图的通用转化格式mcbook-8-01.igs,进行数控编程。要求:火花位为幼公单边-0.1,粗公单边-0.3。

图1-1 鼠标面壳模具及铜公
编程思路及主要步骤:
该铜公的要点是顶面的精加工,在编程时要先补好面再加工。编程时,先完成幼公编程,再复制刀路,修改参数进行粗公的编程,基本步骤如下:
(1)图形处理,设定零点。
(2)铜公加工工艺分析及规划,建立刀具、毛坯、操作群组名。
(3)建立开粗群组中的各个刀路操作。
(4)建立外形基准平面的光刀刀路。
(5)建立局部开粗及清角刀路。
(6)建立孔位光刀。
(7)建立曲面的半精加工(即中光)及精加工刀路。
(8)建立粗公的刀路。
(9)模拟检查,修正错误。
(10)后置处理。
1.2.1 图形处理及设定零点
本节任务:将铜公图调入,检查零点。
1.调入铜公图
(1)打开软件。
(2)执行主菜单【文件】|【打开文件】命令,或直接在工具栏中单击【打开】按钮,系统弹出【打开】对话框,选择
,选取mcbook-8-01-0.igs文件。该文件为用Pro/E软件所拆的铜公。
2.检查铜公零点及坐标系
检查铜公零点及坐标系基本符合要求,如图1-2所示。

图1-2 调出铜公图
3.文件存盘
文件另外存盘为mcbook-8-01-ok.mcx-5,在以后每完成一步重要步骤都要及时存盘,以防止意外情况发生因忘记存盘而使工作丢失。
1.2.2 工艺分析及规划
本节任务:铜公加工工艺分析及规划,建立毛坯、空操作群组名。
1.铜公加工工艺分析及规划
(1)铜公加工要求:台阶面以上部分的型面包括孔位留-0.1的火花位,孔的底部,碰穿位的底部属于避空面加工到位即可,不必给火花位,台阶位平位及四周基准按图加工到位。
(2)开料尺寸:用【画边界盒】的方法可以把所有曲面图绘制一个线框图,测量尺寸为120×60×45,最后开料为125×65×45,材料为铜。
(3)刀路规划。
① 操作群组K02A,用ED12平底刀开粗,留0.2余量。
② 操作群组K02B,用ED12平底刀对基准面光刀,留-0.1余量。
③ 操作群组K02C,用ED8平底刀对按键安装位清角,底部余量为0,侧面留-0.1余量。
④ 操作群组K02D,用ED3平底刀对按键安装位光刀,留-0.1余量。
⑤ 操作群组K02E,用ED2平底刀对孔位光刀,留-0.1余量。
⑥ 操作群组K02F,用BD8R4球头刀对曲面进行半精加工,留0余量。
⑦ 操作群组K02G,用BD8R4球头刀对曲面进行光刀,留-0.1余量。
2.进入加工模块建立毛坯
执行主菜单【机床类型】|【铣床】|【默认】命令,在左边的【操作管理】中出现了新的项目,单击【属性】前的“+”号,展开其中的项目,如图1-3所示。

图1-3 展开项目
在图1-3所示中单击【材料设置】按钮,系统弹出【机器群组属性】对话框,自动选取【材料设置】选项卡。单击【所有曲面】按钮,系统自动计算出材料的尺寸,然后设置为实际开料尺寸,如图1-4所示。

图1-4 设置材料
3.建立空群组
在图1-3所示的【操作管理】中,用鼠标右键单击,在弹出的快捷菜单中选择【群组】|【重命名】命令,将其名字改为K02A。
再右键单击,在弹出的快捷菜单中,选择【群组】|【新建刀具路径】,生成新的刀具路径群组
,将其名字改为K02B。
同理,生成新的刀具路径群组,将其改名为K02C、K02D、K02E、K02F和K02G,如图1-5所示。

图1-5 建立新的刀具路径群组
1.2.3 建立群组K02A用于开粗
本节任务:建立开粗刀路。完成两个操作:一是对台阶面以上部分进行开粗,二是对铜公最大外形台阶位从上到下进行开粗。
1.对台阶面以上部分进行开粗
方法:采取粗加工曲面挖槽的方法进行加工,在做刀路之前应该创建边界线,该线要足够大,以保证开粗切削干净。
(1)创建辅助线。
检查此时的构图平面为顶视图,2D绘图模式,设定构图深度Z=0。工作层为第9层,命名为linshi-xk。工作颜色号为2。单击工具栏中的【矩形】按钮,创建以铜公零点为中心,边长为125mm×65mm的矩形。要保证这个矩形比铜公的有效型面的最大轮廓多出至少一个刀具半径以上的数值,这样才能使挖槽刀路完整,如图1-6所示。

图1-6 创建辅助线
(2)在【操作管理】的【刀具路径】选项卡中用鼠标拖动箭头,移到K02A群组下方。
(3)设置系统参数,使生成的NC文件名和群组名相同。
方法:执行主菜单【设置】|【系统配置】命令,系统弹出【系统配置】对话框,单击【刀具路径管理】按钮,在右侧栏中设置【NC文件】,选择【刀具路径群组名称】选项,和【始终提示】选项。单击【确定】按钮,在系统弹出的【系统配置】信息框中单击【是】按钮,将这些参数保存在mcamxm.config配置文件中,如图1-7所示。

图1-7 设置NC文件名参数
(4)在主菜单中,选取【刀具路径】|【曲面粗加工】|【粗加工挖槽加工】命令。系统弹出【输入新NC名称】对话框,系统给定的名称默认为群组名,不要改名,单击【确定】按钮,如图1-8所示。

图1-8 进入NC操作
(5)系统要求选取加工面,将图形放置在前视图,用框选的方法选取加工面,按Enter键,如图1-9所示。

图1-9 选取加工面
(6)系统弹出【刀具路径的曲面选取】对话框,单击【边界范围】的【选择】按钮,系统弹出【串连选项】对话框,这时将图形切换到等角视图并再次确认构图平面为顶视图。选取【串连】模式,在图形上选取刚创建的边界线,如图1-10所示。

图1-10 选取边界线
(7)定义刀具。在图1-10所示中单击【确定】按钮,系统弹出【曲面粗加工挖槽】对话框。选取【刀具路径参数】选项卡,在刀具选择框中,按鼠标右键,弹出【定义刀具】对话框,在相应的选项卡中按如图1-11所示设置ED12平底刀的参数。【夹头】参数不变,不用另外定义。

图1-11 定义刀具
(8)设置曲面加工参数。在【曲面粗加工挖槽】对话框,选取【曲面加工参数】选项中,按如图1-12所示设置。
其中,【安全高度】为60.0,中间如果有频繁提刀的情况,这中间过程的提刀安全高度则在【参考高度】中设置为40.0,为绝对坐标方式,比工件的最高处高出5左右即可。余量参数【预留量】为0.2,比最终加工的-0.1多出一定的预留量。其余参数取按系统默认值。
(9)设置粗加工参数。选取【粗加工参数】选项卡,按如图1-13所示设置【整体误差】为0.025,【Z轴最大进给量】为1.0,勾选【由切削范围外下刀】复选项,这样可以保证每一层都在料外下刀。

图1-12 设置加工参数

图1-13 设置粗加工参数
(10)设置螺旋下刀参数。在图1-13所示中,勾选【螺旋式下刀】复选项,单击【螺旋式下刀】按钮,系统弹出【螺旋/斜插式下刀参数】对话框,设置参数,如图1-14所示。

图1-14 设置螺旋/斜插式下刀参数
要注意
(1)在图1-14所示中,未勾选【以圆弧进给G2/G3】选项,含义是在后处理的NC程序中,使螺旋线以一系列直线的方式来表示,否则,以G02 X Y Z R或G03 X Y Z R方式表示。但是有些旧机床可能不支持这种方式,为了使NC程序更具有通用性,本例未选此方式。在实际工作中可以根据机床性能灵活处理。
(2)本例中的凹槽面积较小,不能真正形成一个完整的螺旋线,将按照右侧的选项【沿着边界逐渐下刀】的方式进行斜线切削。这样设置可以防止直接踩刀现象的发生,提高切削平稳性。
(11)设置切削深度参数。在图1-13所示中,单击【切削深度】按钮,系统弹出【切削深度的设定】对话框,设置【最高的位置】为35.0,【最低的位置】为0.1,单击【确定】按钮,如图1-15所示。

图1-15 设置切削深度
小提示
由图1-12所示得知铜公图形的Z最高为34.83482,实际加工对刀时要按照Z=35进行,以保证顶部有一定的余量。最低设置Z=0.1,可以保证在铜公的台阶平面上留0.1的余量。
(12)设置挖槽参数。在【曲面粗加工挖槽】对话框中,选取【挖槽参数】选项,按如图1-16所示设置。
其中,加工方式选取“双向”。【切削间距(直径%)】为75.0,【距离】为9.0,【粗切角度】为0.0,即与X轴的夹角为0°。勾选【精加工】复选框,并且给【次数】为1,【间距】为0.5,【修光次数】为0。不勾选【精修切削范围的轮廓】复选框,以减少边界外形光刀的空刀。

图1-16 设置挖槽参数
(13)检查刀具平面。在【曲面粗加工挖槽】对话框中,选取【刀具路径参数】选项卡,单击按钮,系统弹出【刀具面/构图面的设定】对话框,检查【工作坐标系统】、【刀具平面】、【绘图平面】均为俯视图,如果不是这样,需要单击按钮
给予设定。单击【确定】按钮
,如图1-17所示。

图1-17 检查刀具平面
(14)其余参数不变,单击【确定】按钮,生成刀路,单击【重画】按钮
,生成的开粗刀路如图1-18所示。为了后续编程清晰,在【操作管理】中单击按钮
以关闭刀路显示。

图1-18 生成的开粗刀路
2.对铜公最大外形台阶面从上到下进行开粗
方法:采取2D等高外形方式分层对工件进行加工。
(1)根据曲面产生外形线条。确认此时构图平面为顶视图,工作层为第9层,工作颜色为号2。按Alt+E组合键,单独显示台阶面。执行主菜单【绘图】|【曲面曲线】|【所有曲线边界】命令,选取台阶面,在弹出的参数表中单击【适合弧和线】按钮,单击【确定】按钮
,生成其边界线。再次按Alt+E组合键,显示所有图素。再次按Alt+E组合键单独显示所有线框图,如图1-19所示。

图1-19 生成边界线
(2)在主菜单中执行【刀具路径】|【外形铣削】命令,如图1-20所示。
(3)系统弹出【串连选项】对话框,选取2D及【串连】模式,在图形上选取边界线1,如图1-21所示。

图1-20 进入NC操作

图1-21 选取边界线
(4)单击【确定】按钮,系统弹出【2D刀具路径-等高外形】对话框。在【刀具路径类型】中,设定为【等高外形】,如图1-22所示。
(5)定义刀具。在【2D刀具路径-等高外形】对话框中,选取ED12刀具。
(6)设置加工参数。在【2D刀具路径-等高外形】对话框中,选取【切削参数】选项,在右侧参数栏中,设置余量【壁边预留量】为0.2,【底面预留量】为0.0,如图1-23所示。

图1-22 选取等高外形

图1-23 设置切削参数
(7)设置深度切削参数。在【2D刀具路径-等高外形】对话框中,选取【深度切削】选项,右侧参数按如图1-24所示设置。勾选【深度切削】复选项,并给定【最大粗切步进量】为1.0,勾选【不提刀】复选项。

图1-24 设置深度切削
(8)设置进/退刀参数。进/退刀参数也称非切削参数,是主切削部分的辅助部分,必须保证平稳进刀和退刀。在【2D刀具路径-等高外形】对话框中,选取【进/退刀参数】选项,右侧参数按如图1-25所示设置。设置进刀参数,然后单击按钮,可以复制到退刀参数栏中去。

图1-25 设置进/退刀参数
(9)设置共同参数。在【2D刀具路径-等高外形】对话框中,选取【共同参数】选项,右侧参数按如图1-26所示设置。其中,加工的最高位置【工件表面】为绝对值Z=0,最低位置【深度】为相对值Z=-8。

图1-26 设置共同参数
(10)其余参数不变,单击【确定】按钮,生成刀路,按Alt+E组合键,显示所有图形,如图1-27所示。

图1-27 生成外形开粗刀路
本节讲课视频
以上操作的视频文件为\ch08\03-video\K02A.exe。
1.2.4 建立群组K02B进行基准面精加工
本节任务:建立基准面的精加工刀路。完成三个操作:一是对铜公的基准外形面进行精加工,二是对台阶水平面进行精加工,三是对铜公的有效型直身面进行精加工。
1.对铜公基准外形面进行精加工
方法:复制上述刀路2,修改参数。
(1)在【操作管理】的【刀具路径】选项卡中用鼠标拖动箭头,移到K02B群组的下方。
(2)在【操作管理】中,右键单击操作,在弹出的快捷菜单中选择【复制】选项,再次右键单击该操作,在弹出的快捷菜单中选取【粘贴】选项,系统弹出【输入新NC名称】对话框,系统默认的名称为K02B,单击【确定】按钮
,则生成新的操作
,观察此时的操作3应该在K02B群组里,如图1-28所示。

图1-28 复制刀路3
(3)在新的操作3中,单击,在弹出的【2D刀具路径-等高外形】对话框中修改参数。在【切削参数】选项中设定【壁边预留量】为0.0,【底面预留量】也为0.0,其余参数不变,如图1-29所示。
(4)在【深度切削】选项中,取消选取【深度切削】复选项。这样可以使生成的刀路为一层,如图1-30所示。
(5)在【进/退刀参数】选项中,设置【重叠】距离为0.5,这样可以消除接刀痕迹,如图1-31所示,其余参数不变。
(6)设置分层进刀切削参数,在【分层切削】选项中,勾选【分层切削】复选项,设置【粗加工次数】为0,【精加工次数】为2,每次精加工进刀【间距】为0.05,选取【不提刀】复选项,如图1-32所示。

图1-29 设置切削参数

图1-30 设置深度切削参数

图1-31 设置进/退刀参数

图1-32 设置分层切削参数
(7)参数设置完成后,单击【确定】按钮。在【操作管理】中,单击【重建所有已失败操作】按钮
,生成刀路,如图1-33所示。
2.对台阶水平面进行精加工
方法:复制刀路操作1的曲面挖槽,修改深度参数。
(1)在【操作管理】中,用鼠标左键选择操作1,按Ctrl+C组合键,再按Ctrl+V组合键,文件名按系统提示的K02B给定,将其复制到群组K02B中成为操作4,如图1-34所示。

图1-33 外形基准光刀

图1-34 复制刀路4
(2)在【操作管理】中选取操作4,单击【参数】按钮,系统弹出【曲面粗加工挖槽】对话框,选取【粗加工参数】选项卡,单击【切削深度】按钮,系统弹出【切削深度的设定】对话框,设定【最高的位置】及【最低的位置】均为0.0,如图1-35所示。
(3)参数设置完成后,单击【确定】按钮。在【操作管理】中,单击【重建所有已失败操作】按钮
,生成刀路。关闭刀路3,显示本次刀路4,如图1-36所示。检查刀路,无误后再关闭刀路4。

图1-35 深度设定

图1-36 生成铣平面刀路
3.对铜公的有效型直身面进行精加工
方法:复制操作3,修改参数。
(1)在【操作管理】中,右键单击操作3,在弹出的快捷菜单中选择【复制】选项,再次右键单击该操作,在弹出的快捷菜单中选取【粘贴】选项,文件名按系统提示的K02B给定,则生成新的操作5。
(2)在新的操作中,单击,在弹出的【串连管理】参数框中,右键单击选取
,在弹出的快捷菜单中选取
,将其删除。再次右键单击鼠标,在弹出的快捷菜单中选取
,在图形的台阶面上选取图1-19所示生成的边界线2。注意使起点在右侧,观察箭头,并且为左补偿,即补偿箭头朝外,走刀方向为顺时针,如图1-37所示。

图1-37 编辑线条
知识拓展
如果选取加工线条后,发现方向或起点不满意可以编辑。右键单击,在系统弹出的快捷菜单中选取相应的选项,进行调整,如图1-38所示。

图1-38 修改编辑线条
(3)在新的操作5中,单击,在系统弹出的【2D刀具路径-等高外形】对话框中修改参数。在【切削参数】选项卡中,设置【壁边预留量】为-0.1,使侧面留出火花位,其余参数不变,如图1-39所示。
(4)在【共同参数】选项中设定加工的最低位置为。其余参数不变,这样在底部的基准平面上留余量为0。
(5)在【圆弧过滤/公差】选项中,设置公差过滤参数。【过滤的比率】设置为1:1,再设置【过滤的误差】为0.01,按Enter键,此时其他参数将自动设置,如图1-40所示。

图1-39 设置余量参数

图1-40 设置过滤参数
(6)在【操作管理】中,单击【重建所有已失败操作】按钮,生成刀路,如图1-41所示。检查无误后就可以关闭该刀路显示。

图1-41 生成台阶外形光刀
本节讲课视频
以上操作的视频文件为\ch08\03-video\K02B.exe。
1.2.5 建立群组K02C进行按键安装位清角加工
本节任务:用ED8平底刀建立按键安装位清角加工及光刀刀路。完成三个操作:一是用平面等高铣进行清角加工,二是对平面底部光刀,三是对侧面光刀。
1.局部按键安装位清角
方法:复制刀路,修改参数。
(1)在【操作管理】的【刀具路径】选项卡中用鼠标拖动箭头,移到K02C群组的下方,这样可以使产生的刀路操作产生在群组K02C中。
(2)在【操作管理】中,用鼠标左键选择操作2,按Ctrl+C组合键,再按Ctrl+V组合键,将其复制到群组K02C中成为操作6。文件名取系统默认的K02C,单击【确定】按钮如图1-42所示。

图1-42 复制新的操作
(3)生成加工线条。按Alt+E组合键,在图形中选取按键安装位底部面,使其单独显示。执行主菜单【绘图】|【曲面曲线】|【所有曲线边界】命令,选取这个面,在弹出的参数表中单击【适合弧和线】按钮,单击【确定】按钮
,生成其边界线3。再次按Alt+E组合键,显示所有图素。再次按Alt+E组合键单独显示所有线框图,如图1-43所示。

图1-43 生成边界线3
(4)在新的操作6中,右键单击,在弹出的【串连管理】参数框中,右键单击选取
,在弹出的快捷菜单中选取
,将其删除。再右键单击鼠标,在弹出的快捷菜单中选取
,在图形的台阶面上选取图1-43所示生成的边界线3。注意使起点在右侧,观察箭头,并且为左补偿,即补偿箭头朝内,走刀方向为逆时针,如图1-44所示。

图1-44 编辑线条
(5)在新的操作6中,单击,在系统弹出的【2D刀具路径-等高外形】对话框中,选取【刀具】选项,定义新的平底刀ED8,如图1-45所示。

图1-45 定义刀具
(6)在【切削参数】选项中,【外形铣削类型】选择“残料加工”;【剩余材料的计算是来自】选取【粗切刀具直径】选项,【粗切刀具直径】为12.0;此处的【安全高度】英文原意是Clearance,软件菜单的翻译不准确,其含义应该是刀具残留加工时刀具路径的延伸量,设置该参数的目的是防止下刀时踩刀,此处给定0.5;【残料加工的误差】给定为0.1。再选取【显示材料】复选项,设置该参数的目的是以便清晰地观察残留材料的范围大小,也可以不用选,不影响刀路计算。余量参数不变,如图1-46所示。

图1-46 设置切削参数
(7)设置深度切削参数。在【2D刀具路径-等高外形】对话框中,选取【深度切削】选项,右侧参数按如图1-47所示设置。勾选【深度切削】复选项,并修改给定【最大粗切步进量】为0.5,勾选【不提刀】复选项。另外,还要注意选取【依照轮廓】复选项,这样可以确保先完整加工一个角落轮廓,再提刀加工另外一部分轮廓,减少提刀次数。

图1-47 设置深度切削
知识拓展
该操作刀路完成后,请读者试着修改选取【依照深度】选项,观察刀路的变化。这时刀路会先加工完各个轮廓的一层,再加工下一层,有很多提刀。这种方式适合薄壁零件的加工,加工过程中可以保证工件的强度未破坏,可以有效地防止工件变形。
(8)设置进/退刀参数。选取【进/退刀参数】选项,右侧参数按如图1-48所示设置。修改设置进刀参数,然后单击按钮,复制到退刀参数栏中去。

图1-48 设置进/退刀参数
(9)在【共同参数】选项中,按如图1-49所示设置。因为开粗在底部已经留出了0.2的余量,所有此处最低加工深度也为相对值0.2。

图1-49 设置安全高度参数
(10)在【操作管理】中,单击【重建所有已失败操作】按钮,当系统显示出加工区域和未加工区域时只需要按Enter键两次,生成刀路,如图1-50所示。按Alt+E组合键显示所有图形,检查无误后就可以关闭该刀路显示。

图1-50 生成清角刀路
要注意
此处的铜公曲面高度不同,而编程时却使用了同一个加工最高深度,这会导致有一些空刀,为了减少这些空刀,还可以分别使用边界线来做加工刀路。但是由于此处加工区域小,空刀时间所占比例不大,为了说明清角刀路的用法,提高编程效率,在此就不用进一步处理了。
2.局部按键安装位清角
方法:复制刀路6,修改参数,采用平面挖槽的方法加工底平面。
(1)在【操作管理】中,用鼠标左键选择操作6,按Ctrl+C组合键,再按Ctrl+V组合键,将其复制到群组K02C中成为操作7。文件名按系统默认的K02C,单击【确定】按钮,如图1-51所示。

图1-51 复制刀路7
(2)在新的操作7中,单击,在弹出的【2D刀具路径-标准挖槽】对话框中,选取【刀具路径类型】选项,在右侧对话框中选取【标准挖槽】选项,如图1-52所示。

图1-52 设置刀具路径类型
(3)选取【切削参数】选项,按如图1-53所示设置参数。在【挖槽类型】中选择“标准”方式,余量设置【壁边预留量】为0.3,【底面预留量】为0.0。

图1-53 设置切削参数
(4)选取【粗加工】选项,按如图1-54所示设置参数。选取【粗加工】复选框及【双向】加工方式,步距为刀具直径的75%,实际步距为6,角度为0°。

图1-54 设置粗加工参数
(5)设置进刀参数。选取【进刀模式】选项,按如图1-55所示设置参数,选取【螺旋形】下刀方式。
(6)设置精加工参数。选取【精加工】选项,按如图1-56所示设置参数。选取【精加工】复选框及【间距】为0.5。
(7)设置进/退刀参数。选取【进/退刀参数】选项,按如图1-57所示设置参数。设置进/退刀圆弧半径为2.0,角度为45.0。
(8)设置深度切削参数。选取【深度切削】选项,按如图1-58所示设置参数。选取【深度切削】复选项,【最大粗切步进量】为0.15。

图1-55 设置进刀参数

图1-56 设置精加工参数

图1-57 设置进/退刀参数

图1-58 设置深度切削参数
(9)设置共同参数。选取【共同参数】选项,按如图1-59所示设置参数。加工最高位置为相对值0.3,最低位置为加工线条所在的位置,即增量值为0。

图1-59 设置安全高度参数
(10)生成刀路。参数设置完成后,单击【确定】按钮。在【操作管理】中,单击【重建所有已失败操作】按钮
,生成刀路,如图1-60所示,检查无误后就可以关闭该刀路显示。

图1-60 生成底面光刀
3.对侧壁直身面进行精加工
方法:复制刀路6,修改参数。
(1)在【操作管理】中,用鼠标左键选择操作6,按Ctrl+C组合键,再按Ctrl+V组合键,将其复制到群组K02C中成为操作8。文件名按系统默认的K02C,单击【确定】按钮,如图1-61所示。

图1-61 复制刀路8
(2)修改切削参数。在新的操作8中,单击,在弹出的【2D刀具路径-等高外形】对话框中,选取【切削参数】选项,按如图1-62所示修改参数。修改【外形铣类型】为“2D”,设置【壁边预留量】为-0.1,其余参数不变。

图1-62 修改切削参数
(3)设置深度切削参数。选取【深度切削】选项,取消选取【深度切削】复选项,如图1-63所示,这样可以使生成的刀路为一层。

图1-63 设置深度切削参数
小提示
因为根据测量图形得知,此处加工位置最高为Z=35,最低为Z=26.967,加工深度为8.03,而从图1-45所示得知ED8平底刀的刀锋长度为32,刀锋长度大于加工深度,为了提高效率,可以采取一层切削进行光刀。如果今后遇到的加工深度比刀锋长度长,就要采取分层切削,每层的层深要小于刀锋长度,这样可以防止刀杆挤压工件。
(4)设置分层切削进刀参数。选取【分层切削】选项,按如图1-64所示设置进刀分层参数。【精加工次数】为2,每一次进刀【间距】为0.05。

图1-64 设置进刀参数
(5)设置进/退刀参数。选取【进/退刀参数】选项,设置【重叠】为0.5,其余参数不变,如图1-65所示。

图1-65 设置重叠参数
(6)设置加工最低面参数。选取【共同参数】选项,设置加工的最低位置【深度】为,其余参数不变。单击【确定】按钮
,完成参数设置。
(7)生成刀路。在【操作管理】中,单击【重建所有已失败操作】按钮,生成刀路,如图1-66所示。按Alt+E组合键,显示所有图形,检查无误后就可以关闭该刀路显示。

图1-66 生成光刀
本节讲课视频
以上操作的视频文件为\ch08\03-video\K02C.exe。
1.2.6 建立群组K02D对按键安装位光刀
本节任务:根据对按键安装位处曲面半径的分析测量得知,此处圆角半径为R2,需要用ED3平底刀对按键安装位清角及对φ5.2孔光刀。完成5个操作:一是用平面等高铣进行清角加工,二是对斜面进行光刀,三是对直身面进行光刀,四是对φ5.2孔位进行开粗,五是对φ5.2孔位斜面进行光刀。
1.用平面等高铣进行清角加工
方法:复制之前的清角刀路,然后修改参数。
(1)在【操作管理】的【刀具路径】选项卡中用鼠标拖动箭头,移到K02D群组的下方。这样可以使产生的刀路操作产生在群组K02D中。
(2)在【操作管理】中,用鼠标左键选择操作6,按Ctrl+C组合键,再按Ctrl+V组合键,将其复制到群组K02D中成为操作9。文件名取系统默认的K02D,单击【确定】按钮,如图1-67所示。
(3)在新的操作9中,单击,在系统弹出的【2D刀具路径-等高外形】对话框中,选取【定义刀具】选项,定义新的平底刀ED3,按如图1-68所示设置参数。

图1-67 复制刀路9

图1-68 定义刀具
要注意
本例ED3平底刀的直径是按2.8来定义的,实际切削时所用刀具的直径仍为3,这样就会对工件单边过切-0.1,正好是铜公所需要的火花位。这就是用减刀半径的方法来编铜公程序,此方法通常用于平底刀对曲面进行的多面外形加工。因为在Mastercam中,平底刀对曲面进行加工编程时不能给负余量,如果给负余量,系统是按照0来计算的。这是一种近似的方法,为了能尽量接近实际情况,加工时可以通过修改机床设定的长度补偿H,使整体刀路降低一个火花位的数值。
知识拓展
另外,将平底刀设置R0.1,即定义成圆鼻刀也可以近似对铜公曲面进行加工编程。但是,最精确的方法是将曲面做成等距面成为铜公的真实图形,然后用真实的刀具编程。这些方法可以在实际工作中灵活应用,如果可能尽量用球刀对铜公曲面进行加工。
4)在【切削参数】选项中,修改【粗切刀具直径】为8.0,【壁边预留量】为0.01,如图1-69所示。

图1-69 设置切削参数
小提示
一般来说,小刀具在装夹时由于误差的原因,会导致其旋转后形成的半径比名义刀具直径大一些,这里之所以留出0.01余量是为了和之前加工部位接刀顺畅。在实际工作中,可以结合工厂的实际刀具误差,灵活调整这个数据。
(5)设置深度切削参数。在【2D刀具路径-等高外形】对话框中,选取【深度切削】选项,设置【最大粗切步进量】为0.15,其余参数不变,如图1-70所示。

图1-70 设置深度切削参数
(6)设置进/退刀参数。选取【进/退刀参数】选项,按如图1-71所示设置参数。

图1-71 设置进/退刀参数
(7)在【共同参数】选项中,设置加工最低点为,其余参数不变。
(8)在【操作管理】中,单击【重建所有已失败操作】按钮,当系统显示出加工区域和未加工区域,按Enter键两次,生成刀路,如图1-72所示。按Alt+E组合键显示所有图形,检查无误后就可以关闭该刀路显示。
2.对斜面进行光刀
方法:采取曲面精加工等高外形。
(1)在【操作管理】中检查确保箭头在最下端。按Alt+S组合键给图形上色。执行主菜单【刀具路径】|【曲面精加工】|【精加工等高外形】命令,系统提示文件名为K02D,单击【确定】按钮
,接受这个命名。然后在图形上选取如图1-73所示的斜面,按Enter键结束曲面的选择。

图1-72 生成清角刀路

图1-73 选取曲面
(2)完成图素的选取后,系统会弹出【刀具路径的曲面选取】对话框,边界等图素不用定义,单击【确定】按钮。系统又弹出【曲面精加工等高外形】对话框,在【刀具路径参数】选项卡中,选取刀具ED3,其余参数不变,如图1-74所示。
(3)在【曲面加工参数】选项卡中,按如图1-75所示设置【安全高度】及【预留量】均为0.0,其余参数不变。

图1-74 选取刀具

图1-75 设置余量参数
(4)在【等高外形精加工参数】选项卡中,设置层深参数【Z轴最大进给量】为0.05,选取【双向】和【斜降】选项,其余参数不变,如图1-76所示。

图1-76 设置加工参数
知识拓展
这里的【Z轴最大进给量】表示加工完成一层后再加工下一层时的层深。设置用平底刀加工斜面的层深参数,对于半精加工要考虑刀具的承受能力,对于精加工主要考虑加工出面的残留高度。如果残留高度按0.003时,可以按照直角三角形的函数公式0.003/sinα计算,α表示斜面的拔模角。用动态分析得知,此处曲面的拔模斜度角为3°,利用三角形几何原理来推导的层深计算公式计算0.003/sin(3°)=0.5073≈0.05。
(5)在图1-76中单击【切削深度】按钮,系统弹出【切削深度的设定】对话框,选取【绝对坐标】选项,设置加工的【最高的位置】为35.0,【最低的位置】为28.4,如图1-77所示,单击【确定】按钮。这样设置的目的是为了减少最高层的空刀,在设置前应用动态分析的方法分析出图形的最高点和最低点坐标,实际设置时可以适当调整这些数值。

图1-77 设置切削深度
(6)在图1-76中单击【间隙设定】按钮,系统弹出【刀具路径的间隙设置】对话框,参数取系统默认值。设置这个参数的目的是为了减少不必要的提刀,如图1-78所示,单击【确定】按钮。
(7)在图1-76中单击【高级设置】按钮,系统弹出【高级设置】对话框,按如图1-79所示设置参数,其目的是为了减少在曲面边缘产生不必要的圆角,单击【确定】按钮。
(8)在完成各个参数的设定后,在如图1-76所示的【曲面精加工等高外形】对话框中单击【确定】按钮,忽略系统的提示信息,系统会开始计算刀具路径,生成如图1-80所示的刀具路径10。

图1-78 设置提刀参数

图1-79 设置高级参数

图1-80 生成刀路
3.对直身面进行光刀
方法:复制刀路,修改参数。
(1)在【操作管理】中,用鼠标左键选择操作8,按Ctrl+C组合键,再按Ctrl+V组合键,将其复制到群组K02D中成为操作11。文件名按系统默认的K02D,单击【确定】按钮,如图1-81所示。

图1-81 复制刀路11
(2)在新的操作11中,单击按钮,在系统弹出的【2D刀具路径-等高外形】对话框中,选取【刀具】选项,选取ED3。
(3)在【切削参数】选项中,修改【壁边预留量】为0.0,如图1-82所示,其余参数不变,单击【确定】按钮。

图1-82 设置余量参数
(4)在【操作管理】中,单击【重建所有已失败操作】按钮,生成刀路,如图1-83所示,检查无误后就可以关闭该刀路显示。

图1-83 生成精加工刀路
4.对孔位φ5.2进行开粗
方法:复制刀路11,修改加工方式为斜线。
(1)在【操作管理】中,用鼠标左键选择操作11,按Ctrl+C组合键,再按Ctrl+V组合键,将其复制到群组K02D中成为操作12。文件名按系统默认的K02D,单击【确定】按钮,如图1-84所示。
(2)生成加工线条。注意工作层为第9层。按Alt+E组合键,在图形中选取孔位φ5.2底部面,使其单独显示。执行主菜单【绘图】|【曲面曲线】|【所有曲线边界】命令,选取这个面,在弹出的参数表中单击【适合弧和线】按钮,单击【确定】按钮
,生成其边界线4。再次按Alt+E组合键,显示所有图素。再次按Alt+E组合键单独显示所有线框图,如图1-85所示。

图1-84 复制刀路12

图1-85 生成边界线4
(3)在新的操作12中,右键单击,在弹出的【串连管理】参数框中,右键单击选取
,在弹出的快捷菜单中选取
,将其删除。再右键单击鼠标,在弹出的快捷菜单中选取
,在图形上选取边界线4。注意使起点在右侧,观察箭头,为左补偿,即补偿箭头朝内,走刀方向为逆时针,如图1-86所示。单击【确定】按钮
。

图1-86 编辑线条
(4)在【切削参数】选项卡中,修改【壁边预留量】为0,右【外形铣类型】中选取“斜降”选项,【斜插的位移方式】选择【深度】选项,【斜降深度】为0.15,再选取【在最终深度处补平】及【将3D螺旋打断成若干线段】复选项,【线性公差】设置为0.01,如图1-87所示,其余参数不变,单击【确定】按钮。

图1-87 设置切削参数
(5)设置进/退刀参数。在【进/退刀参数】选项中,取消选取【进/退刀参数】复选项,如图1-88所示。

图1-88 取消进/退刀参数
小提示
因为此处为螺旋式加工,进/退刀就没有必要设置,都能保证切削平稳。如果设置不当反而会使系统显示补偿错误的提示。
(6)在【操作管理】中,单击【重建所有已失败操作】按钮,生成刀路,按Alt+E组合键,显示全部图形,如图1-89所示,检查无误后就可以关闭该刀路显示。

图1-89 生成孔开粗刀路
要注意
该刀路虽然是对φ5.2孔位进行了开粗,但是余量却给定为0,实际上是对底部的直身面也进行了光刀。
5.对φ5.2孔位的斜面进行光刀
方法:复制之前的曲面精加工等高外形刀路,重新选面修改参数。
(1)在【操作管理】中,用鼠标左键选择操作10,按Ctrl+C组合键,再按Ctrl+V组合键,将其复制到群组K02D中成为操作13。文件名按系统默认的K02D,单击【确定】按钮,如图1-90所示。

图1-90 复制刀路13
(2)选取加工面。为了方便选取曲面,可以按Alt+S组合键给图形上色。在【操作管理】中,用鼠标左键选择刀路操作13的,在系统弹出的【刀具路径的曲面选取】对话框中,单击【加工曲面】的【移除】按钮
,将之前的曲面删除,再单击【选择曲面】按钮
,在图形上选取孔的斜面。单击【确定】按钮
,如图1-91所示。

图1-91 选取加工面
(3)在【操作管理】中,用鼠标左键选择,系统弹出【曲面精加工等高外形】对话框,在【等高外形精加工参数】选项卡中,单击【切削深度】按钮,系统弹出【切削深度的设定】对话框,修改【最低的位置】为18.7,如图1-92所示,单击【确定】按钮
。

图1-92 设置切削深度
(4)在完成各个参数的设定后,在【曲面精加工等高外形】对话框中单击【确定】按钮。在【操作管理】中,单击【重建所有已失败操作】按钮
,生成刀路,如图1-93所示,检查无误后就可以关闭该刀路显示。

图1-93 生成刀路
本节讲课视频
以上操作的视频文件为\ch08\03-video\K02D.exe。
1.2.7 建立群组K02E对孔位光刀
本节任务:用ED2平底刀对孔光刀。完成三个操作:用平面等高铣的斜线方式对按键安装孔2-φ4光刀,对2-φ3.4孔位进行开粗,对2-φ3.4孔位进行光刀。
1.用平面等高铣的斜线方式对按键安装孔2-Φ4光刀
方法:复制之前的刀路,然后修改参数。
(1)在【操作管理】的【刀具路径】选项卡中用鼠标拖动箭头,移到K02E群组的下方。这样可以使产生的刀路操作在群组K02E中。
(2)在【操作管理】中,用鼠标左键选择操作12,按Ctrl+C组合键,再按Ctrl+V组合键,将其复制到群组K02E中成为操作14。文件名按系统默认的K02E,单击【确定】按钮,如图1-94所示。

图1-94 复制刀路14
(3)修改加工线条。
按Alt+E组合键,显示所有线框图。然后在新的操作14中,单击,在弹出的【串连管理】对话框中,右键单击选取
,在弹出的快捷菜单中选取
,将其删除。再右键单击鼠标,在弹出的快捷菜单中选取
,在图形上选取2-φ4孔的边界线。注意使起点在右侧,观察箭头,为左补偿,即补偿箭头朝内,走刀方向为逆时针,如图1-95所示,单击【确定】按钮
。
小提示
此处选线时,如果观察到线条的切削方向不对时,可以通过单击【方向】按钮进行调整。选完一条线在【串连选项】对话框中先单击【确定】按钮
后再选取另外的线条。如果发现补偿方向不对时,可以在【串连管理】参数框中右键单击该线条,在弹出的快捷菜单中选取【换边】选项。

图1-95 编辑线条
(4)在新的操作14中,单击,在系统弹出的【2D刀具路径-等高外形】对话框中,选取【刀具】选项,定义新的平底刀ED2,按如图1-96所示设置参数。

图1-96 定义刀具4
要注意
本例ED2平底刀的直径仍然按照比实际刀具的切削直径2小的数值1.8来定义的。实际切削时所用的刀具的直径仍为2,这样就会对工件过切单边-0.1,正好是铜公所需要的火花位,这是一种近似的方法。
(5)在【切削参数】选项卡中,检查【壁边预留量】仍然为0.0,【外形铣类型】选取“斜降”选项,参数不变。在【进/退刀参数】选项中,仍然取消选取【进/退刀】复选项,
(6)在【共同参数】选项中,按如图1-97所示设置。按Alt+E组合键显示所有图形,测量图形中2-φ4孔的要加工的曲面处最高位置Z=26.967和最低位置Z=25,然后设置相应的参数。因为此处加工线条在孔的上边缘,所以最高处用相对值,为了平稳切削多出0.1。
(7)在【操作管理】中,单击【重建所有已失败操作】按钮,生成刀路,如图1-98所示,检查无误后就可以关闭该刀路显示。

图1-97 设置共同参数

图1-98 生成孔加工刀路
要注意
该孔位为直身面,使用斜线方式可以将开粗与光刀一起进行。
2.对2-φ3.4孔位进行开粗
方法:仍然采取斜线方法加工,通过复制刀路,修改参数来完成。
(1)在【操作管理】中,用鼠标左键选择操作14,按Ctrl+C组合键,再按Ctrl+V组合键,将其复制到群组K02E中成为操作15。文件名按系统默认的K02E,单击【确定】按钮,如图1-99所示。
(2)生成加工线条。按Alt+E组合键,在图形上选取2-φ3.4孔位底部的曲面,使其单独显示。执行主菜单【绘图】|【曲面曲线】|【所有曲线边界】命令,选取这两个面,在弹出的参数表中单击【适合弧和线】按钮,单击【确定】按钮
,生成其边界线6及7。再次按Alt+E组合键,显示所有图素。再次按Alt+E组合键单独显示所有线框图,如图1-100所示。

图1-99 复制刀路15

图1-100 生成边界线6及7
(3)选取修改加工线条。然后在新的操作15中,右键单击,在弹出的【串连管理】对话框中,用鼠标左键选取
,再按Del键将其删除,同理删除另外的线条
。再右键单击鼠标,在弹出的快捷菜单中选取
,在图形上选取2-φ3.4孔的底部边界线。注意选取方式为左补偿,即补偿箭头朝内,走刀方向为逆时针,如图1-101所示,单击【确定】按钮
。

图1-101 编辑线条
(4)在【切削参数】选项卡中,【刀具】仍然为ED2,检查【壁边预留量】仍然为0,【外形铣类型】选取“斜降”选项,参数不变。在【进/退刀参数】选项中,仍然取消选取【进/退刀】复选项。
(5)在【共同参数】选项中,按如图1-102所示设置。按Alt+E组合键显示所有图形,测量图形中2-φ3.4孔的要加工的曲面处最高位置Z=26.5和最低位置Z=19.226和Z=15.608,然后设置相应的参数。因为此处加工线条在孔的下边缘,所以最低处用相对值。

图1-102 设置共同参数
(6)在【操作管理】中,单击【重建所有已失败操作】按钮,生成刀路,如图1-103所示,检查无误后就可以关闭该刀路显示。

图1-103 生成孔加工刀路
3.对2-φ3.4孔位进行光刀
方法:复制之前的曲面精加工等高外形刀路,重新选面,修改参数。
(1)在【操作管理】中,用鼠标左键选择操作13,按Ctrl+C组合键,再按Ctrl+V组合键,将其复制到群组K02D中成为操作16。文件名按系统默认的K02E,单击【确定】按钮,如图1-104所示。

图1-104 复制刀路16
(2)选取加工面。为了方便选取曲面,可以按Alt+S组合键给图形上色(如果图形已经上色这一步就不用做)。在【操作管理】中,用鼠标左键选择刀路操作16的,在系统弹出的【刀具路径的曲面选取】对话框中,单击【加工曲面】的【移除】按钮
,将之前的曲面删除,再单击【选择曲面】按钮
,在图形上选取孔的斜面,单击【确定】按钮
,如图1-105所示。

图1-105 选取加工面
(3)在【操作管理】中,用鼠标左键选择,系统弹出【曲面精加工等高外形】对话框,在【刀具路径参数】选项卡中,选取ED2刀具。在【曲面加工参数】选项卡中设置余量仍然为0。
(4)在【等高外形精加工参数】选项卡中,修改层深参数【Z轴最大进给量】为0.03,设置【斜插长度】为1.0,其余参数不变,如图1-106所示。

图1-106 设置精加工参数
知识拓展
(1)这里的【斜插长度】表示加工完成一层再加工下一层时刀路的过渡长度。如果原来默认是5,如果此处不修改,会导致多冗长的过渡刀路,降低加工效率。
(2)【Z轴最大进给量】,按照理论计算0.003/sin2°≈0.08,而实际却给定为0.03,主要是考虑刀具较小,防止切削过程中断刀而有意识将层深减少。在实际编程中可以灵活处理这些参数。
(5)设置切削深度参数。测量图形中2-φ3.4孔的要加工的曲面处最高位置Z=26.5和最低位置Z=19.226和Z=15.608。在图1-106所示的对话框中,单击【切削深度】按钮,系统弹出【切削深度的设定】对话框,修改【最高的位置】为26.5,【最低的位置】为15.6,如图1-107所示,单击【确定】按钮。

图1-107 设置切削深度
(6)在完成加工各个参数的设定后,在【曲面精加工等高外形】对话框中单击【确定】按钮。在【操作管理】中,单击【重建所有已失败操作】按钮
,生成刀路,如图1-108所示。检查无误后就可以关闭该刀路显示。

图1-108 生成光刀刀路
本节讲课视频
以上操作的视频文件为\ch08\03-video\K02E.exe。
1.2.8 建立群组K02F对顶面进行半精加工
本节任务:用BD8R4球头刀,完成两个操作:一是沿着45°方向半精加工,二是沿着135°方向半精加工。
1.沿着45°方向半精加工
方法:先补面、补线,利用曲面精加工平行方式按划分的区域进行加工。
(1)创建辅助边界线。
检查此时的构图平面为顶视图,2D绘图模式,设定构图深度Z=40。工作层为第9层,工作颜色号为4。单击工具栏中的【矩形】按钮,创建矩形1,给定角点为(0,0,40)和(67,37,40),单击【应用】按钮。创建矩形2,对角点为(0,0,40)和(-67,-37,40)。创建矩形3,对角点为(1,-1,40)和(-66,36,40)。创建矩形4,对角点为(-1,1,40)和(66,-36,40),如图1-109所示。

图1-109 创建边界线
(2)创建辅助面。工作层为第10层,层名称为linshi-mian,工作颜色号为3。在工具栏中,单击,选取曲面,移动箭头到孔边缘,系统提示
,单击【是】按钮,在工具栏中单击【确定】按钮
,完成填补曲面,如图1-110所示。

图1-110 填补孔面
(3)在【操作管理】的【刀具路径】选项卡中用鼠标拖动箭头,移到K02F群组下方。
(4)在主菜单中,选取【刀具路径】|【曲面精加工】|【精加工平行铣削】命令。系统弹出【输入新NC名称】对话框,系统给定的名称默认为群组名K02F,不用改名,单击【确定】按钮,如图1-11所示。

图1-111 进入NC操作
(5)系统要求选取加工面,按如图1-112所示选取顶部曲面,包括上一步刚填补的曲面,单击【结束选择】按钮,或者按Enter键。
要注意
注意此处选面时,初学者最好在上色状态,一个一个面进行选取,不要多选也不要漏选。不要盲目贪图快,而发生选面错误,导致数控程序出错。
(6)曲面选取完成后,系统弹出【刀具路径的曲面选取】对话框,单击【边界范围】的【选择】按钮,系统弹出【串连选项】对话框,这时将图形切换到等角视图并再次确认构图平面为顶视图。选取【串连】模式,在图形上选取刚创建的矩形1及矩形2边界线,如图1-113所示。

图1-112 选取加工面

图1-113 选取边界线
(7)定义刀具。在图1-113所示的【刀具路径的曲面选取】对话框中单击【确定】按钮,系统弹出【曲面精加工平行铣削】对话框。选取【刀具路径参数】选项卡,在刀具选择框中,按鼠标右键,弹出【定义刀具】对话框,在相应的选项卡中按如图1-114所示设置BD8R4球头刀的参数。

图1-114 定义刀具5
(8)设置曲面加工参数。在【曲面精加工平行铣削】对话框中,选取【曲面加工参数】选项卡,按如图1-115所示设置。其中,【安全高度】为50.0,【参考高度】为10.0,是相对坐标方式。余量参数【预留量】为0.0,其余参数取系统默认值。

图1-115 设置曲面加工参数
(9)设置平行铣削参数。选取【精加工平行铣削参数】选项卡,按如图1-116所示设置参数,其中,【整体误差】为0.025,【最大切削间距】为0.4,【加工角度】为45.0。

图1-116 设置铣削参数
(10)设置间隙参数。在图1-116所示中,单击【间隙设定】按钮,系统弹出【刀具路径的间隙设置】对话框,选取【切削顺序最佳化】复选项,其余参数不变,如图1-117所示。这样设置参数的目的是减少提刀次数。
(11)设置高级设置参数。在图1-116所示中,单击【高级设置】按钮,系统弹出【高级设置】对话框,选取【只在两曲面(实体面)之间】选项,其余参数不变,如图1-118所示。这样设置参数的目的是防止刀路弯曲对工件的过切。单击【确定】按钮,返回到【曲面精加工平行铣削】对话框中。

图1-117 设置间隙参数

图1-118 设置高级设置参数
(12)其余参数不变,在【曲面精加工平行铣削】对话框中,单击【确定】按钮,生成刀路,生成的半精加工刀路(也称中光)如图1-119所示。为了后续编程清晰,在【操作管理】中单击按钮
以关闭刀路显示。

图1-119 生成的中光刀路
2.沿着135°方向半精加工
方法:复制刀路,修改参数。
(1)复制刀路。在【操作管理】中,用鼠标左键选择刚产生的刀路操作17,按Ctrl+C组合键,再按Ctrl+V组合键,将其复制到群组K02F中成为操作18。文件名按系统默认的K02F,单击【确定】按钮,如图1-120所示。
(2)重新选取边界线。在新的操作18中,单击,系统弹出【刀具路径的曲面选取】对话框,在【边界范围】中先单击【移除】按钮
将之前所选的线条删除,再单击【选择】按钮
,系统弹出【串连选项】对话框,这时将图形适当旋转到方便选线的位置,在图形上选取矩形3及矩形4边界线作为边界线,如图1-121所示。

图1-120 复制刀路18

图1-121 选取边界线
(3)修改加工参数。在操作18中,单击,系统弹出【曲面精加工平行铣削】对话框。选取【精加工平行铣削参数】选项卡,修改【加工角度】为135,其余参数不变,如图1-122所示。

图1-122 设置铣削参数
(4)在完成各个参数的设定后,在【曲面精加工平行铣削】对话框中单击【确定】按钮。在【操作管理】中,单击【重建所有已失败操作】按钮
,生成刀路,如图1-123所示,检查无误后就可以关闭该刀路显示。

图1-123 生成的中光刀路
本节讲课视频
以上操作的视频文件为\ch08\03-video\K02F.exe。
1.2.9 建立群组K02G对顶面进行精加工
本节任务:用BD8R4球头刀。完成两个操作:一是沿着45°方向精加工;二是沿着135°方向精加工。
1.沿着45°方向精加工
方法:复制刀路,修改参数。
(1)在【操作管理】的【刀具路径】选项卡中用鼠标拖动箭头,移到K02G群组下方。
(2)复制刀路。在【操作管理】中,用鼠标左键选择刚产生的刀路操作17,按Ctrl+C组合键,再按Ctrl+V组合键,将其复制到群组K02G中成为操作19。文件名按系统默认的K02G,单击【确定】按钮,如图1-124所示。
(3)修改加工参数。在操作19中,单击,系统弹出【曲面精加工平行铣削】对话框。选取【曲面加工参数】选项卡,修改【预留量】为-0.1,其余参数不变。
选取【精加工平行铣削参数】选项卡,修改【整体误差】为0.01,单击【最大切削间距】按钮,系统弹出【最大步进量】对话框,设置【大约环绕高度在45度】为0.001,单击【确定】按钮,系统自动计算出【最大步进量】为0.126。其余参数不变,如图1-125所示。

图1-124 复制刀路19

图1-125 设置铣削参数
(4)设置间隙参数。在图1-125所示中,单击【间隙设定】按钮,系统弹出【刀具路径的间隙设置】对话框,在【容许的间隙】中选取【距离】选项,并给定其值为2.5。选取【切削顺序最佳化】复选项。其余参数不变,如图1-126所示,这样设置参数的目的是减少提刀次数。
(5)在完成各个参数的设定后,在【曲面精加工平行铣削】对话框中单击【确定】按钮。在【操作管理】中,单击【重建所有已失败操作】按钮
,单击生成刀路,如图1-127所示。单击【切换显示所选择的操作】按钮
,可以使其显示,检查无误后就可以关闭该刀路显示。

图1-126 设定间隙参数

图1-127 生成的精加工刀路
2.沿着135°方向精加工
方法:复制刀路,修改参数。
(1)复制刀路。在【操作管理】中,用鼠标左键选择刀路操作18,按Ctrl+C组合键,再按Ctrl+V组合键,将其复制到群组K02G中成为操作20。文件名按系统默认的K02G,单击【确定】按钮。
(2)修改加工参数。在刚产生的操作20中,单击,系统弹出【曲面精加工平行铣削】对话框。选取【曲面加工参数】选项卡,修改【预留量】为-0.1,其余参数不变。
选取【精加工平行铣削参数】选项卡,修改【整体误差】为0.01,单击【最大切削间距】按钮,系统弹出【最大步进量】对话框,设置【大约环绕高度在45度】为0.001,单击【确定】按钮,系统自动计算出【最大步进量】为0.126。其余参数不变,如图1-128所示。

图1-128 设置铣削参数
(3)设置间隙参数。在图1-128所示中,单击【间隙设定】按钮,系统弹出【刀具路径的间隙设置】对话框,在【容许的间隙】中选取【距离】选项,并给定其值为2.5。选取【切削顺序最佳化】复选项。其余参数不变,如图1-126所示。这样设置参数的目的是减少提刀次数。
(4)在完成各个参数的设定后,在【曲面精加工平行铣削】对话框中单击【确定】按钮。在【操作管理】中,单击【重建所有已失败操作】按钮
,单击生成刀路,如图1-129所示。单击【切换显示所选择的操作】按钮
,可以使其显示,检查无误后就可以关闭该刀路显示。

图1-129 生成的精加工刀路
1.2.10 建立粗公加工刀路
本节任务:根据刚刚完成的幼公的数控程序进行粗公数控程序的编制。
方法:先建立空的程序操作组,然后复制幼公程序,修改余量、步进量、公差而成为粗公。重新生成刀路。粗公的加工方法和幼公基本相同,只是火花位不同。
1.建立空的群组
在【操作管理】中,用鼠标右键单击,在弹出的快捷菜单中选【群组】|【重命名】,将其名字改为K02H。再右键单击
,在弹出的快捷菜单中,选择【群组】|【新建刀具路径】,生成新的刀具路径群组
,将其名字改为K02I。
同理,生成新的刀具路径群组,将其改名为K02J、K02K、K02L、K02M和K02N,如图1-130所示。
2.建立开粗刀路K02H
(1)复制刀路。首先在【操作管理】的【刀具路径】选项卡中用鼠标拖动箭头,移到K02H群组的下方。再在【操作管理】中,选取K02A群组中的刀路操作1及操作2,按Ctrl+C组合键,再按Ctrl+V组合键,将它们复制到K02H群组中。文件名按系统默认的K02H,成为刀路操作21及22,如图1-131所示。

图1-130 建立新的刀具路径群组

图1-131 复制刀路21和22
(2)修改参数。单击刀路操作21的,在系统弹出的【曲面粗加工挖槽】对话框中选取【曲面加工参数】选项卡,修改【预留量】为0.1,即
。其余参数不变,单击【确定】按钮
。不用理会窗口系统弹出的警告。
刀路操作22的参数不变。
3.建立基准面精加工刀路K02I
(1)复制刀路。
首先在【操作管理】的【刀具路径】选项卡中用鼠标拖动箭头,移到K02I群组的下方。
再在【操作管理】中,单击K02B群组前的加号将其展开,再单击该群组名K02B,这样可以把刀路操作3、4及5都选上,按Ctrl+C组合键,再按Ctrl+V组合键,将它们复制到K02I群组中。文件名按系统默认的K02I给定。成为刀路操作23、24、25,如图1-132所示。
(2)修改参数。
刀路操作23和24参数不变。
单击刀路操作25的,在系统弹出的【2D刀具路径-等高外形】对话框中选取【切削参数】选项卡,修改【壁边预留量】为-0.3。其余参数不变,单击【确定】按钮
,如图1-133所示。,不用理会窗口系统弹出的警告。
4.建立清角加工刀路K02J
(1)复制刀路。
首先在【操作管理】的【刀具路径】选项卡中用鼠标拖动箭头,移到K02J群组的下方。

图1-132 复制刀路23~25

图1-133 设置余量参数
再在【操作管理】中,单击K02C群组前的加号将其展开,再单击该群组名K02C,这样可以把刀路操作6、7及8都选上,按Ctrl+C组合键,再按Ctrl+V组合键,将它们复制到K02J群组中。文件名按系统默认的K02J给定。成为刀路操作26、27、28,如图1-134所示。
(2)修改参数。
单击刀路操作26的,在系统弹出的【2D刀具路径-等高外形】对话框中选取【切削参数】选项卡,修改【壁边预留量】为0.0。其余参数不变,单击【确定】按钮
。
刀路操作27参数不变。
单击刀路操作28的,在系统弹出的【2D刀具路径-等高外形】对话框中选取【切削参数】选项卡,修改【壁边预留量】为-0.3。其余参数不变,单击【确定】按钮
。
5.建立按键安装位精加工刀路K02K
(1)复制刀路。
首先在【操作管理】的【刀具路径】选项卡中用鼠标拖动箭头,移到K02K群组的下方。
再在【操作管理】中,单击K02D群组前的加号将其展开,再单击该群组名K02D,这样可以把刀路操作9、10、11、12及13都选上,按Ctrl+C组合键,再按Ctrl+V组合键,将它们复制到K02K群组中。文件名按系统默认的K02K给定。成为刀路操作29、30、31、32、33,如图1-135所示。
(2)修改参数。
单击刀路操作29的,在系统弹出的【2D刀具路径-等高外形】对话框中选取【刀具】选项,重新定义ED3刀具,刀号为6,切削直径为2.4,如图1-136所示。其余参数不变。

图1-134 复制刀路26~28

图1-135 复制刀路29~33

图1-136 定义刀具6
其他操作30、31、32、33都选取刚定义的6号刀具ED3作为加工刀具,其余参数不变,单击【确定】按钮。
6.建立按键安装位精加工刀路K02L
(1)复制刀路。
首先在【操作管理】的【刀具路径】选项卡中用鼠标拖动箭头,移到K02L群组的下方。
再在【操作管理】中,单击K02E群组前的加号将其展开,再单击该群组名K02E,这样可以把刀路操作14、15、16都选上,按Ctrl+C组合键,再按Ctrl+V组合键,将它们复制到K02L群组中。文件名按系统默认的K02L给定。成为刀路操作34、35、36,如图1-137所示。

图1-137 复制刀路34~36
(2)修改参数。
单击刀路操作34的,在系统弹出的【2D刀具路径-等高外形】对话框中选取【刀具】选项,重新定义ED2刀具,刀号为7,切削直径为1.4,如图1-138所示。其余参数不变。

图1-138 定义刀具7
其他操作35、36都选取刚定义的7号刀具ED2作为加工刀具,其余参数不变,单击【确定】按钮。
7.建立顶面中光刀路K02M
(1)复制刀路。
首先在【操作管理】的【刀具路径】选项卡中用鼠标拖动箭头,移到K02M群组的下方。
再在【操作管理】中,单击K02F群组前的加号将其展开,再单击该群组名K02F,这样可以把刀路操作17、18都选上,按Ctrl+C组合键,再按Ctrl+V组合键,将它们复制到K02M群组中。文件名按系统默认的K02M给定。成为刀路操作37、38,如图1-139所示。
(2)修改参数。
单击刀路操作37的,在系统弹出的【曲面精加工平行铣削】对话框中选取【曲面加工参数】选项卡,修改【预留量】为-0.15,其余参数不变,单击【确定】按钮
。
同理,修改刀路操作38的【预留量】也为-0.15,单击【确定】按钮。
8.建立顶面中光刀路K02N
(1)复制刀路。
首先在【操作管理】的【刀具路径】选项卡中用鼠标拖动箭头,移到K02N群组的下方。
再在【操作管理】中,单击K02G群组前的加号将其展开,再单击该群组名K02G,这样可以把刀路操作19、20都选上,按Ctrl+C组合键,再按Ctrl+V组合键,将它们复制到K02N群组中。文件名按系统默认的K02N给定。成为刀路操作39、40,如图1-140所示。

图1-139 复制刀路37和38

图1-140 复制刀路39和40
(2)修改参数。单击刀路操作39的,在系统弹出的【曲面精加工平行铣削】对话框中选取【曲面加工参数】选项卡,修改【预留量】为-0.3,其余参数不变。
选取【精加工平行铣削参数】选项卡,修改【整体误差】为0.02,单击【最大切削间距】按钮,系统弹出【最大步进量】对话框,设置【大约环绕高度在45度】为0.002,单击【确定】按钮,系统自动计算出【最大步进量】为0.178。其余参数不变,如图1-141。这样做的目的是在满足制模要求的条件下,尽量提高粗公的加工效率。所示,单击【确定】按钮

图1-141 设置平行铣削参数
同理,修改刀路操作40的参数。
9.重新生成刀路
在【操作管理】中,单击【重建所有已失败操作】按钮,生成刀路。检查无误后就可以关闭路显示。
1.2.11 刀路模拟检查
数控编程完成后,必须对其进行检查,以便及时发现问题及时解决。检查的方法有静态检查;动态检查。
先对幼公进行实体模拟。事先把图形存为STL文件。检查定义的毛坯要符合实际开料大小。在【操作管理】中,按Alt+E组合键,将各个群组的操作全部展开,先选取操作1,再按Shift键,选取操作20,这样可以把操作1~20全部选上。单击【验证已选择的操作】按钮,结果如图1-142所示。

图1-142 实体模拟
同理可以对粗公进行模拟验证。
1.2.12 后置处理
本章介绍的方法已经使各个操作的文件名默认为各个群组名。
在【操作管理】中,单击按钮全选所有操作,单击【后置处理已经选择的操作】按钮
,系统弹出【后处理程式】对话框,按如图1-143所示设置参数。单击【确定】按钮
,系统就将各个群组的操作,分别处理为群组名相同的NC文件。
要注意记录数控文件生成在哪个文件夹。
本例默认存储文件夹为C:\Users\kou\Documents\my mcamx5\Mill\NC,这个文件夹也可以在参数配置文件中进行修改。
最后文件存盘,文件名为mcbook-8-01-ok.mcx-5,单击【保存】按钮。

图1-143 设置后处理参数
本节讲课视频
以上操作的视频文件为\ch08\03-video\K02G.exe。
1.2.13 填写CNC程序工作单
CNC加工程序单如表1-1所示。
表1-1 CNC加工程序单
续表
1.2.14 本例总结及要注意的问题
要注意
要完成好本图形,还要注意以下问题:
(1)开粗采取了曲面挖槽。关键在于边界线的绘制,单边要大于一个刀具半径的距离,过小会导致部分位置不能铣到位。
(2)稍微复杂的形状要先用大刀具开粗完成后,再用较小刀具清角。本例采取了2D等高外形的清角方法,希望读者仔细体会。
(3)本例加工铜公孔位,开粗时使用了2D等高外形线的螺旋线加工方式。光刀用曲面等高外形采取减刀半径的方法。
(4)由于平行铣削加工是投影式的刀路,在形状起伏较大、较复杂的曲面上会使刀路某些部分不均匀,所以在加工本例顶面时划分了4个区域,以便能够尽量使刀路均匀。
(5)完成刀路后要从提高效率的方面给予审查评判,发现问题及时改进。注意提刀不能过于频繁。