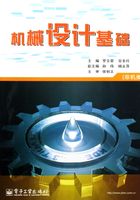
1.1 金属材料的性能
在生产实际中,不同的材料有不同的性能和用途。在选用机械零件材料时,熟悉材料的性能是非常必要的。金属材料的性能包括力学性能、物理性能、化学性能和工艺性能。
1.1.1 金属材料的力学性能
金属材料受到外力作用时表现出来的性能称为力学性能。力学性能主要是指强度、塑性、硬度、冲击韧性和疲劳强度等。力学性能是机械零件设计和选材的主要依据。
1.强度
强度(strength)是指材料在外力作用下抵抗塑性变形和断裂的能力。根据受力状况的不同,材料的强度可分为抗拉、抗压、抗剪、抗扭和抗弯强度等。其中,抗拉强度是最基本的强度指标。工程上常用的强度指标有屈服强度σs和抗拉强度σb。金属的屈服强度、抗拉强度是通过拉伸实验测定的,拉伸实验在拉伸实验机上进行。实验时,首先将试样装夹在拉伸实验机上,用静拉伸力对试样进行轴向拉伸,直至拉断。在整个拉伸过程中,拉伸实验机会自动记录载荷和试样相应的伸长量。屈服强度是指试样在拉伸过程中开始产生塑性变形时的最小应力值,用σs表示,对没有明显屈服现象的材料(如铸铁),规定产生0.2%塑性变形时,试样单位面积上所承受的拉力作为屈服强度,用 σ0.2表示。抗拉强度是指试样在拉断前所能承受的最大应力值,用σb表示。
2.塑性
塑性(plastic)是指材料在外力作用下产生塑性变形而不断裂的能力。常用的塑性指标有伸长率δ和断面收缩率ψ,它们在标准试样的拉伸试验中可同时测出。
材料的δ和ψ越大,材料塑性越好。具有良好塑性的材料,有利于进行锻压、冷压和冷拔等压力加工,也是保证零件工作安全,不发生突然脆断的必要条件。
3.硬度
硬度(hardness)是指材料表面抵抗硬物压入的能力,是衡量材料软硬的依据。硬度的测试方法很多,生产中常用布氏硬度试验法和洛氏硬度试验法两种。
(1)布氏硬度试验法
如图1-1所示,用一直径为D的淬火钢球或硬质合金球为压头,在载荷P的作用下压入被测试材料的表面,保持一定时间后卸除载荷,测量材料表面留下的压痕直径,以压痕的单位面积所承受的平均压力作为被测材料的布氏硬度值。

图1-1 布氏硬度测试原理
在实际应用中,布氏硬度值一般不用计算方法求得,而是先测出压痕直径,然后从专门的硬度表中查得相应的布氏硬度值。
布氏硬度指标有HBS和HBW两种。前者压头为淬火钢球,适用于布氏硬度值低于450的材料;后者压头为硬质合金,适用于布氏硬度值为450~650的材料。布氏硬度试验法常用于测定经退火、正火、调质处理的钢及铸铁、有色金属的硬度,但因压痕较大,不宜测试成品或薄壁金属的硬度。
(2)洛氏硬度试验法
用一锥顶角为120℃的金刚石圆锥体或直径为1.588mm(1/16英寸)的淬火钢球为压头,在规定载荷作用下压入被测试材料表面,保留一定时间后,卸除主载荷,然后可直接从硬度计的指示盘上读出硬度值。常用的洛氏硬度指标有HRA、HRB、HRC三种。
洛氏硬度试验法操作简便,压痕小,可以直接测定薄壁件和成品件,且硬度测试范围大。但因压痕小,准确度较差,故需在零件的不同部位测量数点,取其平均值。
4.冲击韧性
冲击韧性(percussive tenacity)用以反映金属材料在冲击载荷作用下抵抗破坏的能力,其值以冲击韧度AK来表征。冲击韧度是通过冲击试验测定的。冲击试验中一次冲断试样单位截面积所消耗的冲击吸收功即为 AK,其大小可从冲击试验机的刻度盘上直接读出。AK值越大,材料的韧性就越好,在受到冲击时越不容易断裂。
5.疲劳强度
疲劳强度(fatigue strength)是指材料抵抗疲劳破坏的能力。疲劳破坏是指材料在交变应力作用下的破坏。
测试材料的疲劳强度,最简单的方法是旋转弯曲疲劳试验。实验测得的材料所受循环应力σ与其断裂前的应力循环次数N的关系曲线称为疲劳曲线,如图1-2所示。由图中可以看出,循环应力越小,则材料断裂前所承受的循环次数越多。当应力降低到某一值时,曲线趋于水平,即表示在该应力作用下,材料经无数次的应力循环而不发生疲劳断裂。工程上规定,材料在循环应力作用下达到某一基数而不断裂时,其最大应力就作为该材料的疲劳极限。按GB 4337 — 84规定,一般钢铁材料的循环次数取107次。当材料承受对称循环应力时,材料的疲劳极限用σ-1表示。

图1-2 疲劳曲线示意图
1.1.2 金属材料的物理、化学性能
1.物理性能
金属材料的物理性能(physics property)主要包括比重、熔点、热膨胀性、导热性、导电性和磁性等。由于机器零件的用途不同,对金属材料的物理性能要求也有所不同。例如,飞机零件是用比重小、强度高的铝合金制造的,这样可以增加有效载重量;制造内燃机的活塞,要求材料具有较小的热膨胀系数;制造变压器用的硅钢片,要求具有良好的磁性。
金属材料的一些物理性能,对热加工工艺也有一定的影响。例如,导热性对热加工具有十分重要的意义。在进行铸造、锻造、焊接或热处理时,由于导热性的缘故,金属材料在加热或冷却过程中产生内外温度差,导致各部位不同的膨胀或收缩,产生内应力,从而引起金属材料的变形和裂纹。
2.化学性能
化学性能(chemistry property)是指金属材料在常温或高温条件下抵抗外界介质对其化学浸蚀的能力。它主要包括耐酸性、耐碱性和抗氧化性等。
一般金属材料的耐酸性、耐碱性和抗氧化性都是很差的,为了满足化学性能的要求,必须使用特殊的合金钢及某些有色金属,或者使之与介质隔离。如化工设备、医疗器械等采用不锈钢,工业用的锅炉、喷气发动机、汽轮机叶片选用耐热钢等。
1.1.3 金属材料的工艺性能
金属材料的工艺性能是指材料加工成形的难易程度。金属材料加工成为零件的四种基本加工方法是:铸造、锻压、焊接和切削加工(通常前三种加工方法称为热加工,而切削加工称为冷加工)。金属材料的工艺性能(technology property)包括加工工艺性能和热处理工艺性能。
按照加工工艺的不同,又分为铸造性、锻造性、焊接性、切削加工性等。工艺性能往往是由物理性能、化学性能和力学性能综合作用所决定的,不能简单用一个物理参数来表示。在生产中,对于导热性差的金属材料(如合金钢,尤其是高合金钢),应采取适当的措施,避免急剧加热或冷却,防止材料产生裂纹。
材料的热处理工艺性(heat treatment capability)是指材料的淬透性、淬硬性、变形开裂倾向、热处理介质的渗透能力等。热处理能够提高和改善钢的力学性能,因此应充分利用热处理来发挥材料的潜力。
据统计,机床、汽车、拖拉机中约70%的零件需要进行热处理。各种切削刀具、量具、模具及滚动轴承几乎都必须进行热处理。零件进行铸、锻、焊等热加工后产生的内应力及表面的硬化,都必须通过热处理来消除。因此,热处理在机械制造工业中占有十分重要的地位。
热处理分为普通热处理和表面热处理,普通热处理是对工件整体进行热处理,根据加热温度和冷却方式不同,又分为退火、正火、淬火、回火。其中退火和正火常作为预先热处理,目的是消除铸、锻件的缺陷和内应力,改善切削加工性能,为最终热处理做组织准备;淬火加回火常作为最终热处理,目的是改善零件的力学性能,从而延长零件的寿命。表面热处理只对工件表层进行热处理,又分为表面淬火和化学热处理。