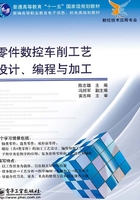
1.3 任务3 对刀及对刀设备的使用
活动情境
对刀点是程序的起点,对刀就是使刀具的刀位点与对刀点重合的操作。对刀操作对零件加工质量有重要影响,是造成人为误差的一个最重要环节。本任务中要求学生通过观看录像、师傅演示、讲解等方式,掌握常用对刀设备的使用方法,并能熟练进行对刀操作。
任务要求
(1)了解对刀仪的结构原理。
(2)能说出常用对刀设备名称、作用。
(3)掌握对刀操作技能。
1.3.1 对刀点与换刀点的确定
1.对刀点
对刀点是指通过对刀确定刀具与工件相对位置的基准点。对于数控机床来说,在加工开始时,确定刀具与工件的相对位置是很重要的,这一相对位置是通过确认对刀点来实现的。对刀点可以设置在被加工零件上,也可以设置在夹具上与零件定位基准有一定尺寸联系的某一位置,对刀点往往就选择在零件的加工原点。对刀点的选择原则如下。
(1)对刀点的位置应该容易确定,所选的对刀点应使程序编制简单。
(2)对刀点应选择在容易找正、便于确定零件加工原点的位置。
(3)对刀点应选在加工时检验方便、可靠的位置。
(4)对刀点的选择应有利于提高加工精度。
(5)批量加工时,为应用调整法获得尺寸,即一次对刀可加工一批工件,对刀点应选在夹具定位元件的起始基准上,并将编程原点与定位基准重合,以便直接按定位基准对刀或将对刀点选在夹具中专设的对刀元件上,以方便对刀。
2.刀位点
刀位点是指刀具的定位基准点。在进行数控加工编程时,往往是将整个刀具缩视为一个点,那就是“刀位点”,它是在刀具上用于表现刀具位置的参照点。一般来说,立车刀、端车刀的刀位点是刀具轴线与刀具底面的交点;圆弧形车刀的刀位点为圆弧中心。常用车刀的刀位点如图1.50所示。

图1.50 常用车刀的刀位点
在使用对刀点确定加工原点时,就需要进行“对刀”。所谓对刀指使“刀位点”与“对刀点”重合的操作。每把刀具的半径与长度尺寸都是不同的,刀具装在机床上后,应在控制系统中设置刀具的基本位置。
3.换刀点
在数控车床上加工零件时,需要经常换刀,在程序编制时就要设置换刀点。换刀点是指刀架转位换刀时的位置,换刀点可以是某一固定点(如车削中心,其换刀点的位置是固定的),也可以是任意的一点(如数控车床)。普通数控车床的换刀点由编程员指定。为防止换刀时碰伤零件及其他部件,换刀点常常设置在被加工零件或夹具的轮廓之外,并留有一定的安全量。不能将换刀点与对刀点混为一谈。
1.3.2 数控车床上的对刀方法
1.采用G92X Z建立工件坐标系对刀
该指令规定了刀具起点(此时该点为对刀点)在工件坐标系中的坐标值。如图1.51所示工件坐标系的设定。工件定位夹紧后,工件坐标系原点在机床上的位置已确定,对刀就是按工件已安装确定的位置,使刀具的刀位点在程序运行前准确停在G92指令要求的坐标位置,即对刀点上。

图1.51 工件坐标系的建立
具体对刀步骤如下:
(1)机床回参考点。建立机床坐标系,此时CRT上将显示刀架中心在机床坐标系中的当前位置的坐标值。代表刀具刀位点的当前位置。
(2)试切测量。采用点动或MDI方式将工件或端面试车一刀,保持刀具Z轴方向位置不变,沿X轴方向退刀,测量试切端面至工件原点的距离度L,并记录CRT上显示的刀架中心(对刀参考点)在机床坐标系中Z轴方向上的当前位置的坐标值Zt。再将工件外圆表面试切一刀,沿纵向Z轴方向退刀,保持刀具在X轴方向上的位置尺寸不变,然后测量工件试切后的直径D,即可知道刀尖在X轴方向上的当前位置在工件坐标系内的坐标值,并记录CRT上显示的刀架中心在机床坐标系中X轴方向上的当前位置的坐标值Xt。
(3)计算坐标增量。根据试切后测量的工件直径D、端面距离长度L与程序所要求的起刀点位置(X,Z),即可计算出刀尖移到起刀点位置所需的X轴坐标移动增量X-D与Z轴坐标移动增量Z-L。由于刀尖的X轴和Z轴坐标移动增量与刀架中心的移动增量值完全相等,移动时可通过CRT上显示的刀架中心的移动增量值来控制。
(4)对刀。根据计算出的坐标增量,用手摇脉冲发生器移动刀具,使前面记录的刀架中心坐标值(Xt,Zt)增加相应的坐标值增量,即将刀具移至使CRT屏幕上所显示的刀架中心在机床坐标系中的坐标值为(Xt+X-D,Zt+Z-L)为止,这样就实现了将刀位点置于程序所要求的起刀点位置上,实现了对刀。
(5)建立工件坐标系。若执行程序段G92X Z,则屏幕将会变为显示当前刀位点在工件坐标系中的位置,即数控系统用新建立的工件坐标系取代了前面建立的机床坐标系。
2.采用G54~G59零点偏置指令建立工件坐标系对刀
G54指令中的(X,Z)值是指机床坐标系下的坐标值代表刀位点的坐标时,工件坐标系原点在机床坐标系中的坐标值。用此指令的对刀方法是求出当刀尖(刀位点)与工件坐标系原点重合时,刀架中心在机床坐标系中的坐标值,此值即表示工件原点在机床坐标系中的坐标值,在对完刀后要把此值输人到CNC系统零点偏置寄存器中。具体对刀过程与G92的操作基本相同。
3.改变参考点位置,通过回参考点直接对刀
对于批量生产,工件采用夹具定位装夹的,若采用G92指令建立工件坐标系,刀具每加工完一件后回参考点,使每次加工的起刀点位置重合,也可一次对刀加工一批工件,但应使参考点到工件的距离适当,这时可通过调整机床各坐标轴的机械挡块位置和精确测量并重设数控系统参数,将参考点设置在与起刀点相对应的位置上,这样在进行回参考点操作时,即能使刀尖到达起刀点位置实现直接对刀。
4.多刀加工时的对刀——利用刀具长度补偿功能对刀
此种对刀的目的是使所换刀具的刀位点位于对刀点上,不是建立工件坐标系。刀具补偿功能由程序中指定的T代码来实现。T代码由字母T后面跟4位数字组成,其中前两位为刀具号,后两位为刀具补偿号。
1.3.3 数控车床对刀仪
使用对刀器有利于提高生产效率,控制产品质量,降低生产成本。现在很多车床上都装备了对刀仪,使用对刀仪对刀可免去测量时产生的误差,大大提高对刀精度。由于使用对刀仪可以自动计算各把刀的刀长与刀宽的差值,并将其存入系统中,在加工另外的零件的时候就只需要对标准刀,这样就大大节约了时间。需要注意的是使用对刀仪对刀一般都设有标准刀具,在对刀的时候先对标准刀。
1.机外对刀仪对刀
图1.52所示是一种比较典型的车床用机外对刀仪,它由导轨、刻度尺、光源、投影放大镜、微型读数器、刀具台安装座和底座等组成。这种对刀仪可通用于各种数控车床。

图1.52 机外对刀仪
机外对刀仪的本质是测量出刀具假想刀尖点到刀台上某一基准点之间的X及Z方向的距离,也称为刀具X及Z向的长度,即刀具的长度补偿值。
机外对刀时必须连刀夹一起校对,所以刀具必须通过刀夹再安装在刀架上。某把刀具固紧在某刀夹上,尔后一起不管安装到哪个刀位上,对刀得到的刀具长度总是一样的。针对某台具体的数控车床(主要是具体的刀架及其相应的刀夹)还应制作相应的对刀刀具台,并将其安装在刀具台安装座上。这个对刀刀具台与刀夹的连接结构和尺寸应该同机床刀台每个刀位的结构和尺寸完全相同,甚至制造精度也要求与机床刀台该部位一样。
机外对刀的顺序是这样的:将刀具随同刀夹一起紧固在对刀刀具台上,摇动X向和Z向进给手柄,使移动部件载着投影放大镜沿着两个方向移动,直到假想刀尖点与放大镜中的十字线交点重合为止。对称刀(如螺纹刀)的假想刀尖点在刀尖实体上,它在放大镜中的正确投影见图1.53(b)所示。不少假想刀尖点不在刀具(尖)实体上,所以所谓它与十字线交点重合,实际是刀尖圆弧与从十字线交点出发的某两条放射线相切,如端面外径刀和端面内径刀在放大镜中的正确投影,见图1.53(a)和图1.53(c)所示。此时,通过X和Z向的微型读数器分别读出的X和Z向刻度值,就是这把刀的对刀长度。如果这把刀具马上使用,那么将它连同刀夹一起移装到机床某刀位上之后,把对刀长度输入到相应的刀补号或程序中就可以了。使用机外对刀仪对刀的最大优点是对刀过程不占用机床的时间,从而可提高数控车床的利用率。这种对刀方法的缺点是刀具必须连同刀夹一起进行对刀。如果采用机外对刀仪对刀,那么刀具和刀夹都应准备双份:一份在机床上用,另一份在对刀仪上对刀。

图1.53 刀尖在放大镜中的对刀投影
2.ATC对刀
在机外对刀场合,用投影放大镜(对刀镜)能较精确地校订刀具的位置,但装卸带着刀夹的刀具比较费力,因此在生产中又有了ATC对刀。它是在机床上利用对刀显微镜自动地计算出车刀长度的一种对刀方法。对刀镜实际是一架低倍显微镜(一般放大10倍左右),不过对刀镜内有如图1.53所示的6条30°等分线,有的还有坐标尺。对刀时,用手动方式将刀尖移到对刀镜的视野内,再用手动脉冲发生器微移刀架使假想刀尖点像图1.53所示的那样与对刀镜内的中心点重合,再将光标移至相应的刀补号,并按“自动计算(对刀)”按键,这时这把刀两个方向的长度就被自动计算出来并自动存入它的刀补号区域。
3.自动对刀
使用对刀镜无论是在机外对刀还是在机内对刀,由于整个过程基本上还是手工操作,所以仍没有跳出手工对刀的范畴。利用CNC装置自动、精确地测出刀具两个坐标方向的长度、自动修正刀具补偿值,并且不用停顿就接着开始加工工件,这就是刀具检测功能,也叫自动对刀。
刀检传感器上带有超硬触头(一般为边长7mm的立方体),它安装在以枢轴轴承为支点的杠杆的一端,杠杆的另一端与四个接触式传感元件的探针接触。刀检时,刀尖推动触头,与此对应的某个传感探针就被杠杆压迫,内部电路接通,发出电信号;当刀尖离开时,杠杆靠四个带弹簧的支承复位。整个传感器的使用精度主要取决于传感元件的重复精度。好的传感元件重复精度可达2μm。
刀检时,刀尖随刀架按刀检用户宏程序向已设定了位置的触头缓缓行进,并与之接触,直到内部电路接通,发出电信号,数控系统立即“记下”该瞬时的坐标值,接着将此值与设定值做比较,并将差值自动修正到刀具补偿值中去。
4.ETC-4M型对刀器
ETC-4M型对刀器是数控车床专用对刀器,使用这种对刀器能在数控车床上直接进行X轴和Z轴的对刀,如图1.54所示。

图1.54 ETC-4M型对刀器
ETC-4M型对刀器采用手动方式工作,即:对刀时机床的运动由操作者手动控制。其特点是使用手动对刀,操作简便、安全,操作者容易掌握;声、光指示信号清晰、明确,便于对刀操作;采用便携式结构,安装和存放十分方便。
ETC-4M型对刀器的工作原理分为导电式和触发式。一般数控车床使用导电式工作原理的对刀器;如果机床主轴采用陶瓷轴承或刀具采用陶瓷刀片时,应当选用触发式工作原理的对刀器。
对刀环可以摆动15°,并可以向内浮动4mm,可保护刀具和对刀器。对刀环与对刀器主体采用标准M4螺纹连接,可更换。
对刀器工作时同时发出声、光指示信号,便于操作者识别对刀器的状态。对刀器内置可充电电源,配备专用充电器,用户无须频繁更换电池。
在对刀精度方面,闭环控制机床,综合对刀精度约为0.004~0.006mm;半闭环控制机床,综合对刀精度约为0.010~0.013mm。开环控制机床,综合对刀精度约为0.018~0.025mm。
对刀器的操作如下:
(1)对刀器的安装。直接用机床卡盘夹持对刀器的圆柱柄,并使圆柱柄的端面靠紧卡盘的端面。
(2)X轴对刀。手动控制刀架移动,使刀架上车刀的刀尖缓慢地与对刀环的圆周面精确接触,根据对刀环的半径与工件被加工尺寸的半径差值,即可确定刀尖的X轴位置。
(3)Z轴的相对对刀。Z轴的相对对刀是指确定刀架上各个车刀刀尖在Z轴方向上的差值。
对第一把刀时,手动控制刀架移动,使刀架上车刀的刀尖缓慢地与对刀环的端面精确接触,记录机床当前的Z轴坐标值。按此操作过程将刀架上所有的刀尖在Z轴上的位置逐一确定,即完成Z轴的相对对刀。
技能训练
(1)在车床上进行对刀操作。
(2)收集其他形式的对刀设备,了解其性能、特点。
课堂评估
根据对刀操作步骤的正确性、对刀操作的熟练程度进行评估。