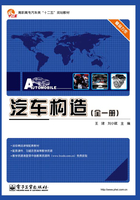
5.2 柱塞喷油泵燃油供给系统
5.2.1 柴油机燃油供给系统的组成
柴油机燃油供给系统一般由燃油供给装置、空气供给装置、混合气形成装置和废气排出装置组成,见图5-3。
(1)燃油供给装置
燃油供给装置主要由柴油箱、油管、输油泵、柴油滤清器、喷油泵、调速器和喷油器等组成。
柴油箱储存有经过沉淀和滤清的柴油。柴油从油箱被吸入输油泵并泵出,经柴油滤清器滤去杂质后,进入喷油泵。自喷油泵输出的高压柴油经高压油管、喷油器喷入燃烧室。由于输油泵的供油量比喷油泵供油量大得多,过量的柴油便经回油管回到输油泵和柴油箱。

图5-3 柴油机燃油供给系统
1-空气滤清器;2-进气管;3-喷油器回油管;4-喷油器;5-排气管;6-燃烧室;7-高压油管;8-喷油泵回油管;9-喷油泵;10-输油泵;11-柴油滤清器;12-低压油管;13-油箱
从柴油箱到喷油泵入口的这段油路中的油压是由输油泵建立的,而输油泵的出油压力一般为0.15~0.3MPa,这段油路称为低压油路。低压油路是向喷油泵供给滤清的燃油。从喷油泵到喷油器这段油路中的油压是由喷油泵建立的,一般在10MPa以上,故称此段油路为高压油路。高压柴油通过喷油器呈雾状喷入燃烧室,与空气混合形成可燃混合气。
为了在柴油机启动时将柴油充满喷油泵,排除整个油路中的空气,在输油泵上装有手动输油泵。
(2)空气供给装置
空气供给装置主要由空气滤清器、进气管、进气道等组成,在有些柴油发动机上还装有进气增压装置和中冷器等。
(3)混合气形成装置
燃烧室是混合气形成装置,主要作用是使燃油与空气混合形成可燃混合气。
(4)废气排出装置
其作用为在做功后排出汽缸内的燃烧废气,包括排气歧管、排气管和排气消声器等。
5.2.2 直列柱塞式喷油泵
1.喷油泵简介
(1)功用
喷油泵即高压油泵(简称油泵),一般与调速器连成一体。其功用是升高柴油压力,按照发动机的工作顺序、负荷大小等不同工况要求,定时、定量、定压地向喷油器输送高压柴油。
(2)多缸柴油机对喷油泵的要求
① 各缸供油次序符合所要求的发动机发火次序;
② 各缸供油量相等,供油量应随柴油机工况的变化而变化,为此喷油泵必须有供油量调节机构;
③ 各缸供油提前角一致,供油提前角也应随柴油机工况的变化而变化;
④ 供油开始和结束,动作敏捷,断油干脆,以避免喷油器产生滴油或不正常喷射现象。
(3)喷油泵的类型
喷油泵的结构形式很多。车用柴油机的喷油泵按其工作原理不同可分为直列柱塞式喷油泵、PT泵和转子分配式喷油泵三类。
2.直列柱塞式喷油泵的结构和工作原理
直列柱塞式喷油泵使用性能良好,使用可靠,结构简单紧凑,便于维修和供油调节,目前为多数汽车柴油机所采用,它主要由柱塞分泵、油量调节机构、分泵驱动机构和泵体四部分组成,其结构见图5-4。

图5-4 柱塞式喷油泵结构示意图
1-凸轮轴;2-喷油泵体;3-调节齿杆;4-出油阀紧固座;5-柱塞弹簧;6-凸轮
(1)分泵
分泵的主要零件有柱塞偶件、柱塞弹簧、弹簧下座、出油阀偶件、出油阀弹簧、减容器、出油阀压紧座等,其结构见图5-5。
分泵是带有一套柱塞副、出油阀副等零件组成的高压泵油机构,分泵的数目与发动机的缸数相等,每一副柱塞与柱塞套只向一个汽缸供油。对于多缸柴油机,则由多套泵油机构分别向各缸供油。中、小功率柴油机大多将各缸的泵油机构组装在同一壳体中,称为多缸泵,而其中每套泵油机构则称为分泵。
柱塞泵的泵油机构包括两套精密偶件,由柱塞和柱塞套构成的柱塞偶件,见图5-6(a);由出油阀和出油阀座构成出油阀偶件,见图5-6(b)。
柱塞和柱塞套是一对精密偶件,经配对研磨后不能互换,要求有高的精度和光洁度和好的耐磨性,其径向间隙为0.002~0.003mm。
柱塞头部圆柱面上切有斜槽,并通过径向孔、轴向孔与顶部相通,其目的是改变循环供油量;柱塞套上制有进、回油孔,均与泵上体内低压油腔相通,柱塞套装入泵上体后,应用定位螺钉定位。柱塞头部斜槽的位置不同,改变供油量的方法也不同。

图5-5 分泵的结构示意图
1-管接;2-出油阀;3-出油阀座;4-泵体;5-柱塞套;6-柱塞;7-上承盘;8-弹簧;9-滚轮体;10-滚轮;11-凸轮轴;12-调整螺钉;13-下承盘;14-转动套;15-齿条;16-齿圈;17-弹簧

图5-6 泵油机构的精密偶件
出油阀偶件配对研磨后不能互换,其配合间隙为0.01mm。
出油阀是一个单向阀,在弹簧压力作用下,阀上部圆锥面与阀座严密配合,其作用是在停止供油时,将高压油管与柱塞上端空腔隔绝,防止高压油管内的油倒流入喷油泵内。
出油阀的下部呈十字断面,既能导向,又能通过柴油。出油阀的锥面下有一个小的圆柱面,称为减压环带,其作用是在供油终了时,使高压油管内的油压迅速下降,避免喷孔处产生滴油现象。当环带落入阀座内时则使上方容积很快增大,压力迅速减小,停喷迅速。
工作时,在喷油泵凸轮轴上的凸轮与柱塞弹簧的作用下,迫使柱塞作上下往复运动,从而完成泵油任务,泵油过程可分为以下三个阶段:
① 进油过程。
进油过程见图5-7(a)。当曲轴驱动喷油泵凸轮轴转动时,如果凸轮的凸起部分尚未与滚轮相接触,在弹簧力的作用下,柱塞向下运动,柱塞上部空间(称为泵油室)产生真空度,当柱塞上端面把柱塞套上的进油孔打开后,充满在油泵上体油道内的柴油经油孔进入泵油室,柱 塞运动到下止点,进油结束。
② 供油过程。
供油过程见图5-7(b)。当凸轮轴转到凸轮的凸起部分顶起滚轮体时,柱塞弹簧被压缩,柱塞向上运动,燃油受压,一部分燃油经油孔流回喷油泵上体油腔。当柱塞顶面遮住套筒上进油孔的上缘时,由于柱塞和套筒的配合间隙很小(0.0015~0.0025mm),从而使柱塞顶部的泵油室成为一个密封油腔,柱塞继续上升,泵油室内的油压迅速升高,泵油压力大于出油阀弹簧力和高压油管剩余压力之和时,推开出油阀,高压柴油经出油阀进入高压油管,通过喷油器喷入燃烧室。

图5-7 柱塞泵的泵油过程
③ 回油过程。
回油过程见图5-7(c)。柱塞向上供油,当上行到柱塞上的斜槽的上边沿(停供边)与套筒上的回油孔的下边沿相通时,泵油室的高压油即通过柱塞中心的油孔和斜槽中的径向孔流入到低压油腔,柴油压力骤然下降,出油阀在弹簧力的作用下迅速关闭,停止供油。此后柱塞可能仍在上行,当凸轮的凸起部分转过去后,在弹簧的作用下,柱塞又下行。此时便开始了下一个循环。
柱塞自开始供油到供油结束这一段行程称为有效压油行程。显然,改变有效压油行程即可以改变供油量。喷油泵凸轮轴每转一转,泵油机构通过喷油器可向燃烧室供油一次。
(2)油量调节机构
改变供油量的办法是转动柱塞,通过改变有效供油行程来完成。有效供油行程的数值则等于柱塞开始压油时,回油孔处斜槽的上边沿与回油孔的下边沿的距离。此距离越长,有效供油行程越长,则供油量越大。这一段距离可以通过转动柱塞加以改变。
油量调节机构的作用是执行驾驶员或调速器的指令,转动柱塞改变各分泵的供油量,以适应柴油机负荷和转速变化的需要,并通过它来调整各缸供油的均匀性。
油量调节机构有拉杆拨叉式和齿杆齿圈式两种。
① 拉杆拨叉式油量调节机构
该机构由调节臂、拨叉、供油拉杆等组成,见图5-8。驾驶员或调速器轴移动供油拉杆时,拨叉带动调节臂使柱塞相对柱塞套转动,从而调节了供油量。当各缸供油量不等时,可松开固定螺钉改变拨叉在供油拉杆上的位置予以调整。
② 齿杆齿圈式油量调节机构
齿杆齿圈式油量调节机构由齿杆、齿扇(齿圈)和传动套等组成,见图5-9。齿杆的轴向位置由驾驶员或调速器控制,齿扇通过传动套带动柱塞套筒相对于柱塞转动,便可调节供油量。各缸供油均匀性的调整,通过改变齿扇与传动套圆周方向的相对位置来实现。

图5-8 拉杆拨叉式油量调节机构
1-柱塞套;2-柱塞;3-调节臂;4-拨叉;5-供油拉杆

图5-9 齿杆齿圈式油量调节机构
1-柱塞套筒;2-齿杆;3-可调齿圈;4-传动套;5-柱塞
(3)分泵驱动机构
分泵驱动机构主要由喷油泵凸轮轴和滚轮体等传动部件组成。其功能是推动柱塞往复运动,完成进油、供油、回油过程,并保证供油正时。
① 凸轮轴
其结构见图5-10。凸轮轴上的凸轮数目与缸数相同,排列顺序与柴油机的工作顺序相同。四冲程柴油机曲轴转两周,喷油泵的凸轮轴转一周,各分泵都供一次油。相邻工作两缸凸轮间的夹角叫供油间隔角,角度的大小等同配气机构凸轮轴同名凸轮的排列,四缸柴油机为90°,六缸柴油机为60°。

图5-10 凸轮轴(四缸机)结构
1-密封垫;2-圆锥滚子轴承;3-连接锥面;4-油封;5-前端盖;6-泵体;7-调整垫片;8、9、10、11-凸轮;12-输油泵偏心轮
② 滚轮体传动件
滚轮体传动件的作用是变凸轮的旋转运动为自身的直线往复运动,推动柱塞上行供油,并且用来调整各分泵的供油提前角和供油间隔角。
滚轮体的高度多为可调式,主要分为调整垫块式和调整螺钉式两种。
调整垫块式滚轮体见图5-11。带有滑动配合衬套的滚轮体松套在滚轮轴上,滚轮轴也松套在滚轮架座孔中,因此凸轮与滚轮体相对运动为滚动摩擦,减轻了磨损,且磨损均匀。
调整垫块安装在滚轮架的座孔中,它的上端面到滚轮下沿的距离h称为滚轮体的工作高度。调整垫块用耐磨材料制成,制有不同厚度的垫块,厚度差为0.1mm,相应凸轮轴转角为0.5°,反映到曲轴上为1°。
调整螺钉式滚轮体见图5-12。在滚轮架上端有工作高度可调节的调整螺钉,拧出调整螺钉,h值增大,供油提前角即增大;拧入螺钉,h值减小,供油提前角即减小。

图5-11 调整垫块式滚轮体
1-调整垫块;2-滚轮;3-滚轮衬套;4-滚轮轴;5-滚轮架

图5-12 调整螺钉式滚轮体
1-滚轮轴;2-滚轮;3-滚轮架;4-锁紧螺母;5-调整螺钉
(4)泵体
泵体是喷油泵的基础件,多用铝合金铸成。泵体分为组合式和整体式两种。组合式有上下两部分,用螺栓连接在一起。上体安装分泵和油量调节机构零件,下体安装驱动件。整体式泵体可使刚度加大,在较高的喷油压力下工作而不变形,但分泵和驱动件等零件的拆装较麻烦。
3.喷油泵的供油正时
(1)供油提前角调节的必要性
供油提前角指的是柱塞顶面封闭柱塞套油孔到活塞上止点为止曲轴所转过的角度。
供油提前角过大时,燃油是在汽缸内空气温度较低的情况下喷入,混合气形成条件差,燃烧前集油过多,会引起柴油机工作粗暴、怠速不稳和启动困难;供油提前角过小时,将使燃料产生过后燃烧,燃烧的最高温度和压力下降,燃烧不完全和功率下降,甚至排气冒黑烟,柴油机过热,导致动力性和经济性降低。
最佳的供油提前角不是一个常数,应随柴油机负荷(供油量)和转速变化,即随转速的增高而加大。车用柴油机根据其常用的某个供油量和转速范围来确定一个供油提前初始角,其值的获得可通过联轴器或转动喷油泵的壳体来进行微量的变化。因柴油机转速变化范围较大,还必须使供油提前角在初始角的基础上随转速而变化,所以车用柴油机多装有供油提前角自动调节器。
为使最佳喷油提前角随转速升高而增大,近年来国内外车用柴油机常用机械离心式供油提前角自动调节器,可根据转速变化自动改变喷油提前角。
(2)供油提前角自动调节机构
供油提前角自动调节器位于联轴节和喷油泵之间。驱动盘与联轴节相连。其结构见图5-13。驱动盘前端面压装两个销钉,两个飞块即套在此销钉上。飞块另一端各压装一个销钉,每个销钉上松套着一个滚轮和内座圈。筒状从动盘的毂部用半圆键与喷油泵凸轮轴相连。从动盘两臂的弧形侧面与滚轮接触,平侧面压在两个弹簧上,弹簧另一端支于松套在驱动盘销钉上的弹簧座上。

图5-13 机械式供油提前角自动调节机构示意图
1-驱动盘;2-飞块;3-弹簧;4-从动盘;5-滚轮;6-销钉;7-提前器盖
(3)工作原理
供油提前角自动调节器工作原理见图5-14。当柴油机工作时,驱动盘通过销钉带动飞块和从动盘一起旋转。飞块在离心力的作用下绕驱动盘上的销钉向外摆动,迫使滚轮沿从动盘上的弧形侧面E向外移动,并推动从动盘沿着旋转的方向转动一个角度α,即供油提前角的增大量,与此同时弹簧受到压缩,直至弹簧力与离心力平衡为止,主动盘重新与从动盘同步旋转。柴油机的转速上升越高,飞块的离心力越大,供油提前角增大越多;反之,柴油机转速降低时,供油提前角相应减小。

图5-14 机械式供油提前角自动调节器工作原理
1-弹簧;2-弹簧座;3-飞块;4-滚轮;5-滚轮内座圈;6-驱动盘;7-从动盘
5.2.3 调速器
喷油泵每个工作循环的供油量主要取决于调节拉杆的位置,此外还受到发动机转速的影响。在调节拉杆位置不变时,随着发动机曲轴转速的增大,柱塞有效行程略有增加,而供油量也略有增大;反之,供油量略有减少。这种供油量随转速变化的关系称为喷油泵的速度特性。
喷油泵的速度特性对工况多变的柴油机是非常不利的。当发动机负荷稍有变化时,导致发动机转速变化很大。当负荷减小时,转速升高,转速升高导致柱塞泵循环供油量增加,循环供油量增加又导致转速进一步升高,这样不断地恶性循环,造成发动机转速越来越高,最后飞车;反之,当负荷增大时,转速降低,转速降低导致柱塞泵循环供油量减少,循环供油量减少又导致转速进一步降低,这样不断地恶性循环,造成发动机转速越来越低,最后熄火。
要改变这种恶性循环,就要求有一种能根据负荷的变化,自动调节供油量、使发动机在规定的转速范围内稳定运转的自动控制机构,移动供油拉杆改变循环供油量,使发动机的转速基本不变。因此,柴油机要满足使用要求,就必须安装调速器。
调速器根据发动机负荷变化而自动调节供油量,从而保证发动机的转速稳定在很小的范围内变化。
调速器按功能分有两速调速器、全速调速器、定速调速器和综合调速器。
1.两速调速器
两速调速器能自动稳定和限制柴油机最低与最高转速,而柴油机的正常工作转速则由驾驶员通过加速踏板直接控制。
中、小型汽车柴油机多数采用两速调速器,以起到防止超速和稳定怠速的作用,具有低速稳定、高速控制灵敏、操作轻便、易于修复调整等特点。
图5-15为解放牌CA1091K3型载货汽车柴油机所用的RAD型两速调速器。其结构示意图见图5-16。

图5-15 RAD型两速调速器
1-飞块;2-调速手柄;3-控制杠杆;4-滚轮;5-凸轮轴;6-浮动杠杆;7-高速弹簧;8-速度调定杠杆;9-供油齿条;10-拉力杠杆;11-速度调整螺栓;12-启动弹簧;13-稳速弹簧;14-导动杠杆;15-怠速弹簧;16-全负荷限位螺钉
(1)启动加浓
发动机静止时,两飞快在启动弹簧的作用下处于向心极限位置。启动前,将调速手柄从停车挡块移至最高速挡块I上。在此过程中,调速手柄绕D点逆时针转动,浮动杠杆也绕B点逆时针转动,带动供油调节齿条向增加供油的方向(图5-16向左)移动。启动弹簧对浮动杠杆向左的一个拉力使其绕C点逆时针转动,同时带动B点(销轴)和A点(滑套)进一步向左移动,直到飞块到达向心极限位置为止,从而保证供油调节齿杆越过全负荷进入启动最大供油量位置,使得启动油量多于全负荷油量,旨在加浓混合气,以利柴油机低温启动。

图5-16 RAD型两速调速器结构示意图
1-连杆;2-启动弹簧;3-转速调定杠杆;4-拉力杠杆;5-转速调整螺栓;6-导动杠杆;7-调速手柄;8-支持杠杆;9-怠速弹簧;10-全负荷限位螺钉;11-滑套;12-飞块;13-滚轮;14-凸轮轴;15-浮动杠杆;16-高速弹簧;17-供油齿条
(2)怠速稳定
柴油机启动之后,将调速手柄置于怠速位置Ⅱ,见图5-17。飞块的离心力使滑套右移而压缩怠速弹簧,当飞块离心力与怠速弹簧及启动弹簧的合力平衡时,供油调节齿条便保持在某一位置,发动机就相应地处在某一转速下稳定工作。

图5-17 RAD型两速调速器的怠速工作示意图(图中标注同图5-16)
若柴油机由于某种原因转速降低,则飞块离心力减小,在怠速弹簧及启动弹簧的作用下,飞块移向回转中心,同时带动滑套左移,从而使导动杠杆向左偏转,带动B点左移,同时浮动杠杆绕C点逆时针转动,推动供油量调节齿条向左移,增加供油量,使转速回升。反之,当转速增高时,飞块的离心力增大,飞块便压缩怠速弹簧远离回转中心,同样通过导动杠杆使浮动杠杆绕C点顺时针转动,推动供油量调节齿条则向右移动,减小供油量,使转速降低。可见,调速器可以保持怠速转速稳定。
(3)中速
将调速手柄从怠速位置移至中速位置,供油量调节齿条处于部分负荷供油位置,柴油机转速较高,飞块的离心力不足以克服怠速弹簧和高速弹簧的共同作用力,飞块始终紧靠在内弹簧座上而不能移动,即调速器在中等转速范围内不起调节供油量的作用。但此时驾驶员可根据汽车行驶的需要改变调速手柄的位置,使供油量调节齿条向左或向右移动,以增加或减少供油量。
(4)最高转速
将调速手柄置于最高速挡块上,供油量调节齿条相应地移至全负荷供油位置,柴油机转速由中速升高到最高速。此时,飞块的离心力相应增大,并克服全部高速弹簧的作用力,使飞块连同内弹簧座一起向外移到一个新的位置。在此位置,飞块离心力与弹簧作用力达到新的平衡。若柴油机转速超过规定的最高转速,则飞块的离心力便超过调速弹簧的作用力,使供油量调节齿条向减油方向移动,从而防止了柴油机超速。
2.全速调速器
在柴油机全工况范围内任意选定的转速下,全速调速器都能自动调节供油量,保持调节的转速稳定工作。
图5-18是全速调速器的工作原理简图。调速器的速度感测元件由飞块和调速弹簧组成,当柴油机运转时带动支撑盘旋转;飞块铰接在支撑盘上,既可以随支撑盘一起旋转又可以绕支点摆动;滑动盘在调速弹簧预紧力的作用下,压在飞块的钩脚上。当柴油机发出的功率与外界负荷刚好平衡时,便在某一转速下稳定工作。此时,飞块产生的离心力通过钩脚作用在滑动盘左端,该轴向力恰好与调速弹簧作用在滑动盘右端上的预紧力相平衡,油量调节杆也处于某一供油量位置。
当外界负荷减少时,在一定供油量下柴油机发出的功率大于外界负荷而使转速升高,这时飞块所产生的离心力增加,于是钩脚将克服弹簧预紧力推动滑动盘右移,同时也就带动油量调节杆移动,使供油量减少,待调节过程结束,柴油机的功率与外界负荷达到平衡,喷油泵套筒重新稳定在某一位置上。反之,负荷增加时,调速器工作过程与上述相反。如果柴油机的转速需要改变时,只要将调速器弹簧预紧力调到一定值即可。例如,若想增加转速,就要加大预紧力,使飞块作用转速提高。

图5-18 全速式机械调速器原理
1-操纵杆;2-支撑盘;3-飞块;4-滑动盘;5-调速弹簧;6-杠杆;7-油量调节杆
5.2.4 喷油器
喷油器的功用是将来自喷油泵的高压柴油喷射雾化,并按一定的要求将柴油喷射到燃烧室中。对喷油器的要求是:
① 应具有一定的喷射压力和射程,以及合适的喷注锥角;
② 在规定的停止喷油时刻应立即切断燃油的供给,不发生滴油现象;
③ 油束形状与方向适应燃烧室。
常见的喷油器有孔式和轴针式两种形式。
喷油器具有各种不同的结构形式,可分为两大类,即开式喷油器与闭式喷油器。喷油器内部通过喷孔与燃烧室经常相连通的称为开式喷油器;除了喷射柴油的时间外,平时喷油器内部与燃烧室之间被一针阀隔开,这种喷油器称为闭式喷油器。车用柴油机绝大多数采用闭式喷油器,其常见的形式有铀针式与孔式两种。
1.孔式喷油器
孔式喷油器主要用于具有直接喷射式燃烧室的柴油机。喷油孔的数目一般为1~8个,喷孔直径为0.2~0.8mm。喷孔数目和喷孔角度的选择依据燃烧室的形状、大小和空气涡流情况而定。
喷油器主要由针阀、针阀体、顶杆、调压弹簧、调压螺钉及喷油器体等组成,其结构见图5-19。
其中最主要的是优质合金钢制成的针阀和针阀体,两者合称针阀偶件,见图5-20。针阀上部的圆柱表面与针阀体的相应圆柱面作高精度的滑动配合,配合间隙为0.001~0.0025mm。针阀偶件的配合面通常是经过精磨后再研磨,从而保证其配合精度。所以选配和研磨好的一副针阀偶件是不能互换的,这点在维修过程中应特别注意。

图5-19 孔式喷油器结构示意图
1-喷油器体;2-调压螺钉;3-调压弹簧;4-回油管螺栓;5-进油管接头;6-滤芯;7-顶杆;8-针阀;9-针阀体

图5-20 喷油器喷嘴结构示意图
1-针阀;2-针阀体;3-高压油腔;4-承压锥面;5-密封锥面;6-喷孔;7-压力室;8-进油道;A-限位面;h-针阀升程
装在喷油器上部的调压弹簧通过顶杆使针阀紧压在针阀体的密封锥面上,将喷孔关闭。喷油泵输出的高压柴油从进油管接头经过喷油器体与针阀体中的油孔道进入针阀中部周围的环状空间——高压油腔。油压作用在针阀的承压锥面上,形成一个向上的轴向推力,当此推力克服了调压弹簧的预紧力及针阀与针阀体间的摩擦力(此力很小),针阀即上移而打开喷孔,高压柴油便从针阀体下端的喷油孔喷入到燃烧室中。当喷油泵停止供油时,由于油压迅速下降,针阀在调压弹簧作用下及时回位,将喷孔关闭。
喷油的开启压力即喷油开始时的喷油压力大小,取决于调压弹簧的预紧力,后者可用调压螺钉调节。
在喷油器工作过程中,会有少量柴油从针阀与针阀体的配合表面之间的间隙漏出。这部分柴油对针阀起润滑作用,并沿顶杆周围的空隙上升,通过回油管螺栓上的孔进入回油管,流回柴油滤清器。
对多缸柴油机,为使各缸喷油器工作一致,各缸应采用长度相等的高压油管。喷油器用压板及螺钉固定在汽缸盖上的喷油器孔座内,用钢制的锥体密封,以防止漏气。
孔式喷油器主要特点:
① 喷孔的位置和方向与燃烧室形状相适应,以保证油雾直接喷射在球形燃烧室壁上;
② 喷射压力较高;
③ 喷油头细长,喷孔小,雾化质量好,但易阻塞,加工精度要求高。
2.轴针式喷油器
轴针式喷油器的工作原理与孔式的相同。其结构特点是在针阀下端的密封锥面以下还延伸出一段,其形状可以是倒锥形或圆柱形,见图5-21。轴针伸出喷孔外,使喷孔成为圆环状的狭缝(轴针与孔的径向间隙为0.05mm)。这样,喷油时的喷注将呈空心的锥状或柱形。喷孔通过端面与喷注锥角的大小取决于轴针的升程和形状,见图5-22,因此要求轴针的形状加工得很精确。

图5-21 轴针式喷油嘴的结构形式

图5-22 喷油器的喷油情况
常见的轴针式喷油器只有一个直径1~3mm的喷孔。由于喷孔直径较大,孔内有轴针上下运动,喷孔不易积炭,而且还能自行清除积炭。
轴针式喷油器孔径较大,喷油压力较低(12~14MPa),故比较易于加工。它适用于对喷雾要求不高的涡流室式燃烧室和预燃室式燃烧室。
轴针式喷油器特点:
① 不喷油时针阀关闭喷孔,使高压油腔与燃烧室隔开,燃烧气体不致冲入油腔内引起积炭堵塞。
② 喷孔直径较大,便于加工且不易堵塞。
③ 针阀在油压达到一定压力时开启,供油停止时,又在弹簧作用下立即关闭,因此,喷油开始和停止都干脆利落,没有滴油现象。
④ 不能满足对喷油质量有特殊要求的燃烧室的需要。