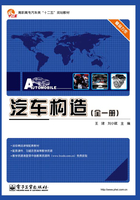
5.5 电控共轨燃油系统
5.5.1 概述
柴油机电控燃油喷射系统的研究开发始于20世纪70年代,80年代进入应用阶段,90年代得到迅速发展。它对提高柴油机的动力性能、经济性能、运转性能和排放性能都产生了极大的影响。
(1)电子控制柴油喷射系统的优点
传统的柴油喷射系统采用机械方式进行喷油量和喷油时间调节和控制,由于机械运动的滞后性,调节时间长,精度差,喷油速率、喷油压力和喷油时间难于准确控制,导致柴油机动力经济性能不能充分发挥,排气超标。研究表明,一般机械式喷油系统对喷油定时的控制精度为2°CA(曲轴转角)左右。而喷油始点每改变1°CA,燃油消耗率会增加2%,HC排放量增加16%,NOX排放量增加6%。
与传统的机械方式比较,电控柴油喷射系统具有如下优点:
① 对喷油定时的控制精度高(高于0.5°CA),反应速度快;
② 对喷油量的控制精确、灵活、快速,喷油量可随意调节,可实现预喷射和后喷射,改变喷油规律;
③ 喷油压力高(高压共轨电控喷油系统高达200MPa),不受发动机转速影响,优化了燃烧过程;
④ 无零部件磨损,长期工作稳定性好;
⑤ 结构简单,可靠性好,适用性强,可以在新老发动机上应用。
(2)电子控制柴油喷射系统的基本原理
电控柴油喷射系统由传感器、控制单元(ECU)和执行机构三部分组成。传感器采集转速、温度、压力、流量和加速踏板位置等信号,并将实时检测的参数转换为电信号输入计算机;ECU是电控系统的“指挥中心”,对来自传感器的信息同储存的参数值进行比较、运算,确定最佳运行参数;执行元件主要是执行ECU的指令,按照最佳参数对喷油压力、喷油量、喷油时间、喷油规律等进行控制,驱动喷油系统,使柴油机工作状态达到最佳。不同柴油机电控系统的执行元件有很大差异,常用的执行元件有电子调速器和电磁阀。
(3)电子控制柴油喷射系统的类型
柴油机电控喷射系统可分为两大类,即位置控制系统和时间控制系统。
第一代柴油机电控喷射系统采用位置控制系统。
它基本保留了传统燃油供给系统的组成和结构,只是采用电控组件,代替调速器和供油提前器,对分配式喷油泵的油量调节套筒或柱塞式喷油泵的供油齿杆的位置,以及油泵主动轴和从动轴的相对位置进行调节,并且通过高速电磁阀直接控制高压燃油的适时喷射。因此既可实现供油量控制,又可实现供油正时的控制。
其优点是无须对柴油机的结构进行较大改动,生产继承性好,便于对现有机型进行技术改造;缺点是控制系统执行频率响应仍然较慢、控制频率低、控制精度不够稳定。喷油率和喷油压力难于控制,而且不能改变传统喷油系统固有的喷射特性,因此很难较大幅度地提高喷射压力。
第二代柴油机电控喷射系统采用时间控制系统,其特点是在高压油路中利用电磁阀直接控制喷油开始时间和结束时间,以改变喷油量和喷油定时。它具有直接控制、响应快等特点。
时间控制系统又包括电控泵喷嘴系统和共轨式电控燃油喷射系统两类。电控泵喷嘴系统除了能自由控制喷油量和喷油定时外,喷射压力十分高(峰值压力可达240MPa),但其无法实现喷油压力的灵活调节,且较难实现预喷射或分段喷射。
第三代柴油机电控系统中最典型的是电控共轨式燃油喷射系统。在电控共轨式燃油喷射系统中,各缸喷油器共用一个高压油轨(即高压油管),把高压油泵输出的燃油蓄积起来并稳定压力,再通过高压油管输送到每个喷油器上,由喷油器上的电磁阀控制喷射的开始和终止。对喷油量的控制采用时间-压力控制或压力控制,用的最多的是时间-压力控制方式。
5.5.2 柴油机电控系统的基本原理
1.位置控制系统
(1)特点
位置控制系统的控制特点:
① 用电子调速器取代传统的机械离心式调速器;
② 用发动机转速传感器和加速踏板位置传感器代替原有的转速和负荷传感机构(如离心飞块、真空室等);
③ 用ECU控制的电子执行元件来代替机械离心式调速执行机构和加速踏板传动机构。
(2)直列式柱塞泵式电控系统
它是在原直列喷油泵基础上装有齿杆位移传感器、凸轮轴或曲轴的转角位移及转速传感器、线性电磁铁的执行器、电控单元等组成的控制系统,对喷油量进行调节。喷油量的计量按位置控制方式,根据加速踏板位置、转速等输入信息,以柱塞的供油始点和供油终点间的物理长度,即有效行程(位置)来确定,而有效行程又是由供油齿杆的位置决定的。
图5-28为德国博世公司的电控直列泵。

图5-28 博世公司的电控直列泵
1-供油齿杆;2-比例电磁阀;3-油泵凸轮轴;4-转速传感器;5-电控单元
直列喷油泵的机械控制喷射系统通过加速踏板和调速器作用于齿杆,反馈的控制信息是柴油机转速和加速踏板的位置,二者通过机械联系改变供油齿杆位置而控制喷油量,电控后喷射系统则通过传感器检测柴油机的运行状态和环境条件,并由电控单元ECU计算出适应柴油机运行状况的控制量,然后由执行器实施。具体说来,加速踏板位置为一可变电压信号,它反映的是驾驶员愿望,通过标定加速踏板位置电压信号和转速信号与供油齿杆位置的对应关系,同时包括由其他传感器,如各种温度、进气压力、车速、制动、离合器分离等信号对供油齿杆位置进行修正的关系,并以软件的形式存储于ECU中,ECU检测到各种信息后,通过线性电磁铁的执行器改变齿杆位置。例如,当采集到离合器分离信号时,线性电磁铁的执行器将齿杆拉到怠速位置。因此,它比纯机械喷射系统控制精确、灵敏;而且在需要扩大控制功能时,只需改变电控单元的存储软件,便可实现综合控制。
(3)转子分配泵式电控系统
用电控装置取代机械调速器和提前器,对VE分配泵供油量调节套筒的位置以及液压提前器进行低频连续调节,以实现油量和定时的控制。
图5-29是日本电装公司VE分配泵的电控喷油系统。

图5-29 日本电装公司VE分配泵的电控喷油系统
1-供油量调节套筒位置传感器;2-供油量控制电磁阀;3-转速传感器;4-定时器位置传感器;5-供油量调节套筒;6-定时器控制阀;7-加速踏板位置传感器;8-进气压力传感器;9-冷却液温度传感器;10-进气温度传感器;11-加速踏板
供油量的控制方法与电控直列泵类似,电控单元ECU根据加速踏板位置传感器和柴油机转速传感器的输入信号,首先算出基本供油量;然后根据来自冷却液温度、进气温度和进气压力等传感器信号以及启动信号,对基本供油量进行修正;再按供油量调节套筒位置传感器信号进行反馈修正之后,确定最佳供油量(调节套筒位置)。
电控单元把计算和修正的结果作为控制信号传到供油量控制电磁阀,产生磁力,吸引可动铁芯。控制信号的电流越大,磁场就越强,可动铁芯向左的移动量越大,通过杠杆将供油量调节套筒向右推移的就越多,供油量也就越大。
2.时间控制系统
其特点是供油仍维持传统的脉动式柱塞泵油方式,如博世公司的电控泵喷嘴系统,但供油量和喷油定时的调节则由电脑控制的强力快速响应电磁阀的开闭时刻所决定,柱塞副只起加压、供油作用,没有油量调节功能。一般情况下,电磁阀关闭时,执行喷油,电磁阀打开时,喷油结束;喷油始点取决于电磁阀关闭时刻,喷油量则取决于电磁阀关闭时间的长短。时间控制系统的控制自由度更大。
高速强力电磁阀安装在回油通道中,取代滑套控制回油通道的开闭,因此可取消油量控制滑套,还可取消泵油柱塞上的回油槽。
图5-30是德国博世公司电控泵喷嘴系统在柴油机上的安装图。
电控泵喷嘴工作原理是:柱塞在凸轮轴和摇臂的驱动下给燃油加压,旁通油路在电磁溢流阀关闭时,柱塞腔内压力升高。压力升高到一定值时,喷油器打开,燃油喷入汽缸;旁通油路在电磁溢流阀打开时,柱塞腔泄压,喷油器处于关闭状态。因此,电磁溢流阀打开的时刻决定喷油提前角,打开的时间决定喷油量,同时可以得到所需要的喷油率。

图5-30 电控泵喷嘴在柴油机上的安装图
1-加速踏板位置传感器;2-电控单元;3-驱动凸轮轴;4-摇臂;5-泵喷嘴喷油器;6-增压压力传感器;7-转速传感器;8-冷却液温度传感器;9-曲轴位置传感器
3.高压共轨式电控柴油喷射系统
(1)高压共轨式电控柴油喷射技术的原理
汽车传统柴油机在喷射过程中高压油管各处的压力是随时间和位置的不同而变化的。压力的变化会引起不稳定的喷射,尤其在低转速区域容易产生上述现象,严重时不仅喷油不均匀,而且会发生间歇性不喷射现象。为了解决柴油机这个燃油压力变化的缺点,现代柴油机采用了一种称为“共轨”的技术。
共轨技术是指由高压油泵、压力传感器和ECU组成的闭环系统中,将喷射压力的产生和喷射过程彼此完全分开的一种供油方式,由高压油泵把高压燃油输送到公共供油管,通过对公共供油管内的油压实现精确控制,使高压油管压力大小与发动机的转速无关,可以大幅度减小柴油机供油压力随发动机转速的变化,因此也就减少了传统柴油机的缺陷。ECU控制喷油器的喷油量,喷油量大小取决于共轨管(公共供油管)压力和电磁阀开启时间的长短。
共轨式电控燃油喷射技术,通过共轨可以直接或间接地将已形成的恒定的高压燃油分送到每个喷油器,并借助于集成在每个喷油器上的高速电磁阀的开启与闭合,定时定量地控制喷射至柴油机燃烧室的油量,从而保证柴油机达到最佳的燃烧速率和良好的柴油雾化,以及最佳的着火时间、足够的着火能量和最少的污染排放。
高压共轨系统主要由电控单元、油泵、共轨管、电控喷油器以及各种传感器等组成,见图5-31。低压燃油泵将燃油输入高压供油泵,高压供油泵将燃油加压送入高压共油轨,高压共油轨中的压力由电控单元根据共油轨压力传感器测量的共油轨压力以及需要进行调节,高压共油轨内的燃油经过高压油管,根据柴油机的运行状态,由电控单元从预设的MAP图中确定合适的喷油定时、喷油持续期,由电-液控制的电子喷油器将燃油喷入汽缸。

图5-31 高压共轨电控柴油喷射系统的组成
1-柴油箱;2-柴油滤清器;3-供油泵;4-高压油管;5-燃油压力传感器;6-共轨;7-限压阀;8-回油管;9-喷油器;10-EDU(电子驱动单元);11-ECU;12-供油量控制阀
(2)高压共轨式电控柴油喷射系统主要部件的结构和工作原理
① 高压供油泵。
高压供油泵的作用是产生高压油,其常见的结构是由凸轮轴驱动的带有多个分泵的直列柱塞式油泵或径向柱塞式油泵。驱动高压输油泵的凸轮轴上可布置一个或几个凸轮,按每个凸轮上的凸起数可分为单作用型、双作用型、三作用型和四作用型等多种形式。
图5-32所示为三作用型高压供油泵的结构示意图。其中,三个径向布置的柱塞泵油元件相互错开120°,由偏心凸轮驱动,出油量大,受载均匀。
工作时,从输油泵来的柴油流过安全阀,一部分经节流孔流向偏心凸轮室供润滑冷却用,另一部分经低压油路进入柱塞室。凸轮转动,柱塞下行时,进油阀开启,低压燃油经进油阀流入柱塞腔。柱塞上行时,进油阀中尚未通电,处于开启状态,低压燃油经进油阀流回低压腔。在达到供油量时,进油阀通电,使之关闭,回流油路被切断,柱塞腔中的燃油被压缩,燃油经出油阀进入高压油轨。利用进油阀关闭时间的不同,控制进入高压油轨油量的多少,从而达到控制高压油轨压力的目的。凸轮经过最大升程后,柱塞进入下降行程,柱塞腔内的压力降低,出油阀关闭,停止供油,这时进油阀停止供电,处于开启状态,低压燃油进入柱塞腔进入下一个循环。
② 调压阀。
调压阀的结构见图5-33。它一般被安装在输油泵出口或共轨上。其功用是根据ECU的指令实现对共轨压力的闭环控制。

图5-32 高压供油泵结构示意图
1-共轨;2-进油管口;3-燃油压力传感器;4-限压阀;5-回油管口;6-流量限制器;7-喷油器供油口

图5-33 调压阀
1-球阀;2-电枢;3-电磁线圈;4-弹簧;5-电气接头
调压阀不工作时,电磁线圈不带电,高压泵出口压力大于弹簧的弹力,球阀被顶开。根据输油量的不同,调节打开的程度。当需要提高共轨管中的压力时,电磁线圈带电,给电枢一个附加作用力,压紧球阀,使共轨管中的压力升高到与其平衡为止;然后调节阀门使其停留在一定的开启位置,保持压力不变。调压阀可在宽广的范围内按ECU指令调节油压,且响应速度快。
③ 共轨组件。
共轨管将供油泵提供的高压燃油分配到各喷油器中,起蓄压器的作用;此外,共轨应能抑制高压油泵供油和喷油器喷油时引起的压力波动,以保持共轨中压力的稳定,其结构见图5-34。

图5-34 共轨管的结构
1-出油阀;2-密封件;3-调压阀;4-球阀;5-安全阀;6-低压油路;7-驱动轴;8-偏心凸轮;9-柱塞泵油元件;10-柱塞腔;11-进油阀;12-柱塞单向阀
高压共轨管上还安装了压力传感器、限压阀和流量限制器。
流量限制器的功用是在非常情况下防止喷油器常开并持续喷油,即一旦某喷油器常开并持续喷油,导致共轨输出的油量超过一定限值,流量限制器则会关闭该喷油器的供油通道,其结构见图5-35。

图5-35 流量限制阀
1-进油孔;2-堵头;3-限制阀;4-弹簧;5-壳体;6-出油孔;7-阀座;8-节流孔
由于弹簧和节流孔的作用,使限制阀向下移动的量随喷油速率增加而增大。喷油器异常泄漏使喷油速率和喷油量超过正常喷油最大值时,限制阀完全关闭,停止给喷油器供油。
限压阀一般安装在输油泵内或共轨上,其结构见图5-36。其功用是限制共轨中的最高压力。弹簧的预紧力根据规定的共轨最高压力调定。阀左侧承受的共轨压力超过右侧的弹簧力时,阀头右移离开阀座,共轨中的燃油经限压阀流回油箱或输油泵进油侧,使共轨压力下降。

图5-36 限压阀
1-共轨侧进油口;2-阀头;3-油孔;4-阀;5-弹簧;6-空心螺塞;7-阀体;8-回油口
④ 电控喷油器。
电控喷油器是共轨式燃油系统中最关键和最复杂的部件,它的作用是根据ECU发出的控制信号,通过控制电磁阀的开启和关闭,将高压油轨中的燃油以最佳的喷油定时、喷油量和喷油率喷入柴油机的燃烧室。
博世公司的CR系统和ECD-U2的电控喷油器的结构基本相似,都是由与传统喷油器相似的喷油嘴、液压控制活塞、控制量孔、控制电磁阀等组成。下面仅以ECD-U2的电控喷油器为例加以说明,其结构原理见图5-37。
当线圈没有通电时,外阀在弹簧力作用下落座,内阀在油道①的油压作用下上升,此时密封内锥座A开启,油道①、②相通,高压油从①进入液压活塞上腔中。
当线圈通电时,外阀在电磁力的吸引下向上运动,关闭密封内锥座A,此时内阀仍停留在上方,外锥座B开启,油道②、③相通,活塞上腔向回油室放油,这时喷油器喷油。线圈通电时间即喷油脉宽,决定喷油量。油道①、②也称为控制量孔,液压活塞上部的空间称为控制室的容积。

图5-37 电控喷油器的工作原理图
1-内阀;2-外阀;3-阀体;4-液压活塞;5-喷嘴