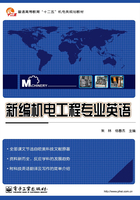
Lesson 3 Kinematic Synthesis
Part A Text
Mechanisms form the basic geometrical elements of many mechanical devices including automatic packaging machinery, typewriters, mechanical toys, textile machinery, and others. A mechanism typically is designed to create a desired motion of a rigid body relative to a reference member. Kinematic design, or kinematic syntheses, of mechanisms often is the first step in the design of a complete machine. When forces are considered, the additional problems of dynamics, bearing loads, stresses, and lubrication are introduced, and the larger problem becomes one of machine design.
A kinematician defined kinematics as “the study of the motion of mechanisms and methods of creating them”. The first part of this definition deals with kinematics analysis. Given a certain mechanism, the motion characteristics of its components will be determined by kinematic analysis. The statement of the task of analysis contains all principal dimensions of the mechanism, the interconnections of its links, and the specification of the input motion or method of actuation. The objective is to find the displacements, velocities, accelerations, shock or jerk (second acceleration), and perhaps higher accelerations of the various members, as well as the paths described and motions performed by certain elements. In short, in kinematic analysis we determine the performance of a given mechanism. The second part of definition may be paraphrased in two ways:
(1) The study of methods of creating a given motion by means of mechanisms.
(2) The study of methods of creating mechanisms having a given motion.
In either version, the motion is given and the mechanism is to be found. This is the essence of kinematic synthesis. Thus kinematic synthesis deals with the systematic design of mechanisms for a given performance. The area of synthesis may be grouped into two categories.
(1) Type synthesis. Given the required performance, what type of mechanism will be suitable? (Gear trains? Linkages? Cam mechanisms?) Also, how many links should the mechanism have? How many degrees of freedom are required? What configuration is desirable? And so on, Deliberations involving the number of links and degrees of freedom are often referred to as the province of subcategory of type synthesis called number synthesis.[1]
(2) Dimensional synthesis. The second major category of kinematic synthesis is best defined by way of its objective: Dimensional synthesis seeks to determine the significant dimensions and the starting position of a mechanism of a preconceived type for a specified task and prescribed performance.
Significant dimensions mean link lengths or distances on binary, ternary, and so on, links, angles between axis, cam-contour dimensions and cam-follower diameters, eccentricities, gear rations, and so forth. A mechanism of preconceived type may be a slider-crank linkage, a four-bar linkage, a cam with flat follower, or a more complex linkage of a certain configuration defined topologically but not dimensionally. There are three customary tasks for kinematic synthesis:function generation, path generation and motion generation.
In function generation mechanisms,[2] rotation or sliding motions of input and output links must be correlated. For an arbitrary function y=f(x), a kinematic synthesis task may be to design a linkage to correlate input and output such that the input moves by x, the output moves by y=f(x)for the range x0<x<xn+1[3].In the case of rotary input and output,the angles of rotation ϕand φare the linear analogs of x and y respectively. When the input link is rotated to a value of the independent x, the mechanism in a “black box” causes the output link to turn to the corresponding value of the dependent variable y=f(x). This may be regarded as a simple case of a mechanical analog computer. A variety of different mechanisms could be contained within the“black box”. However, the four-bar linkage is not capable of error-free generation of an arbitrary function and can match the function at only a limited number of precision points. It is widely used in industry because the four-bar linkage is simple to construct and maintain.
In path generation mechanism a point on a “floating link” is to trace a path defined with respect to a fixed frame of reference [4]. If the path points are to be correlated with either time or input-link positions, the task is called path generation with prescribed timing. An example of path generation mechanisms is a four-bar linkage designed to pitch a baseball or tennis ball. In this case the trajectory of point p would be such as to pick up a ball at a prescribed location and to deliver the ball along a prescribed path with prescribed timing for researching a suitable throw-velocity and direction.
There are many situations in the design of mechanical devises in which it is necessary either to guide a rigid body through a series of specified, finitely separated positions or to impose constrains on the velocity and/or acceleration of the moving body at a reduced number of finitely separated positions. Motion-generation or rigid-body guidance mechanism[5] requires that an entire body be guided through a prescribed motion sequence. The body to be guided usually is a part of a floating link, of which not only is the path of a point p prescribed, but also the rotation of a line passing through the point and embedded in the body. For instance, the line might represent a carrier link in automatic machinery where a point located on the carrier link has a prescribed path while the carrier has a prescribed angular orientation. Prescribing the movement of the bucket for a bucket loader is another example of motion generation mechanism. The path of tip of the bucket is critical since the tip must perform a scooping trajectory followed by a lifting and a dumping trajectory. The angular orientation of the bucket is equally important to ensure that the load is dumped from the correct position.
Words and Expressions
packaging machinery 包装机械
bearing[ˈbεəriŋ] n. 轴承
stress[stres] n. 应力
lubrication[ˌluːbriˈkeiʃən] n. 润滑
specification[ˌspesifiˈkeiʃən] n. 技术要求
actuation[æktfuˈeʃən] n. 驱动
jerk[dʒəːk] n. 振动,冲击
axis n.(pl.axes) 轴[线,心],中心线
contour[ˈkɔntuə] n. 外形,轮廓线
eccentricity[ˌeksenˈtrisitiː] n. 偏心[度,率]
gear ration 齿轮[速,齿数]比
topologically[tɔpɔˈlɔdʒikli] adv. 根据拓扑学
customary adj. 通常的,习惯的
correlate[ˈkɔrileit] v. 使互相关联,联系
analog[ˈænəlɔːg] n. 等同于analogue类似(物),模拟
linear[ˈliniə]analog 线性模拟
second acceleration 二阶加速度
higher acceleration 高阶加速度
paraphrase[ˈpærəˌfreiz] v. 释义,意译
category[ˈkætəgəri] n. 种类,类别
deliberation[diˌlibəˈreiʃən] n. 慎重考虑
province n. 省份,领域
preconceive[priːkənˈsiːv] v. 预想,事先想好
analog computer 模拟计算机
trace v. 追踪,描画
timing n. 定时,计时,配时
pitch v. 投掷
trajectory[trəˈdʒektəriː] n. 轨迹
embed[imˈbed] v. 嵌入,夹在层间
orientation[ˌɔːrienˈteiʃən] n.(定)方位,(取)方向
scoop[skuːp] n. 勺子,铲斗;v. 挖,掘,铲
Notes
[1] Deliberations involving the number of links and degrees of freedom are often referred to as the province of subcategory of type synthesis called number synthesis.
全句翻译:在确定机构杆件数和自由度数目时,人们通常将其看成机构构型综合的一个分支,该构型综合被称为数综合。
type synthesis:机构的构型综合。
number synthesis:机构的数综合。
[2] function generation mechanisms实现函数机构。
[3] For an arbitrary function y=f(x), a kinematic synthesis task may be to design a linkage to correlate input and output such that the input moves by x, the output moves by y=f(x) for the range x0<x<xn+1。
全句翻译:对于一个任意函数y=f(x),机构运动合成的任务是设计一个能将输入运动与输出运动相联系的连杆机构,使得输出运动范围能够界定在输入运动范围x0<x<xn+1所确定的函数y=f(x)内。
[4] In path generation mechanism a point on a “floating link” is to trace a path defined with respect to a fixed frame of reference.
全句翻译:在导轨机构中,“移动构件”上的任意一点将相对于一个固定坐标系沿着指定的轨迹运动。
[5] Motion-generation or rigid-body guidance mechanism.
全句翻译:运动生成或刚体导向机构。
Part B Reading Materials
Standard roller chains are available in single strands or in multiple strands, In the latter type, two or more chains are joined by common pins that keep the rollers in the separate strands in proper alignment. The speed ratio for a single drive should be limited to about 10∶1; the preferred shaft center distance is from 30 to 35 times the distance between the rollers and chain speeds greater than about 2500 feet (800 meters) per minute are not recommended. Where several parallel shafts are to be driven without slip from a single shaft, roller chains are particularly well suited.