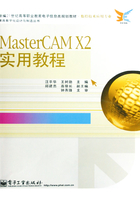
1.6 MasterCAM X从设计到制造的基本流程
使用MasterCAM X进行刀具路径及加工程序生成的基本步骤如下:
图形的产生(根据加工图纸绘制出二维或三维图形、扫描后的数据进行编辑得到的图形、其他的文档交换格式得到的图形)→选择合适的加工方式→编辑加工工艺与选用切削用量(共同参数与特定参数)→生成刀具路径(NCI文件)→刀具路径模拟→NC程序的生成→传给CNC机床进行加工。
下面就一个简单的实例(如图1-22所示)来讲解从设计到制造的基本流程。

图1-22
1.首先,需要创建模型(即项目的CAD部分)
(1)新建一个文件。
(2)作两条辅助线。单击常用工具栏的命令,出现绘线命令操作栏,如图1-23所示。单击
→单击
按钮进行垂直线命令绘制,在坐标输入及捕捉栏的X坐标输入0,然后回车,最后在屏幕上任意两点单击,绘出一条垂直线,用相同的方法绘制出水平线如图1-24所示。

图1-23 绘线命令操作栏

图1-24
(3)绘制圆弧。单击常用工具栏的上的三角按钮,选择
命令,出现绘平行线操作栏,在操作栏的
输入距离15,然后回车,用鼠标单击图1-24所示水平线,再在水平线上方任意位置单击,即绘制出平行线,如图1-25所示。接着单击常用工具栏上
命令进行圆心点半径圆的绘制,先捕捉平行线和垂直线的交点作为圆心。在出现的操作栏
输入半径8.5,然后回车,圆即绘制完成,如图1-25所示。单击常用工具栏上的
旋转命令图标,首先用鼠标单击图1-25所示圆,在键盘上按下回车键,确定被旋转的图素,系统弹出对话框,如图1-26所示,按图中参数进行设定,最后单击
完成圆的旋转复制操作,结果如图1-27所示。

图1-25

图1-26

图1-27
(4)绘制四条直线。单击常用工具栏的上的三角按钮,选择
命令,出现绘平行线操作栏,在操作栏的
输入距离15,然后回车,用鼠标单击图1-24所示垂直线,再在垂直线右方任意位置单击,即绘制出平行线2,如图1-27所示。再单击常用工具栏的
命令,出现绘线命令操作栏,用鼠标捕捉平行线与圆1的交点作为直线第一端点,再捕捉平行线2与圆2的交点作为第二端点,完成线3的绘制,如图1-27所示。
单击常用工具栏上的旋转命令图标,首先用鼠标单击图1-27所示线3,在键盘上按下回车键,确定被旋转的图素,系统弹出对话框,如图1-26所示,按图中参数进行设定,最后单击
完成圆的旋转复制操作,结果如图1-27所示。
(5)进行编辑修改。单击常用工具栏的修剪/打断命令图标,出现修剪/打断命令操作栏,如图1-28所示,单击
分割物体图标和
修剪/延伸图标,接着用鼠标单击图1-29所示圆弧1~8,将不需要的图素进行修剪。最后用鼠标单击不需要的图素,在键盘上按下“Delete”键进行删除,结果如图1-30所示。

图1-28 修剪/打断命令操作栏

图1-29

图1-30
(6)绘制矩形。单击常用工具栏的矩形命令图标,出现矩形命令操作栏,如图1-31所示,在长和宽数据栏中分别输入60、60,然后回车,接着单击
选项图标,将矩形的基准点设为中心点,最后用鼠标捕捉图1-30所示垂直线和水平线的交点作为中心点,完成矩形绘制,如图1-32所示。

图1-31 矩形命令操作栏

图1-32
(7)绘制实体。在界面下方的状态栏中的对话框中输入层别为2,将实体部分绘制在第二图层上。单击常用工具栏的
图标,将视角设为等角视图,在菜单栏依次点选
→
命令,出现选择对话框,如图1-33所示,按图中指示点选选择方式为串连,单击图1-34所示直线,最后完成图形的选取。接着弹出拉伸对话框,如图1-35所示,按图中参数进行设定,要确定绘图区图形出现的拉伸箭头为向下,如相反的话,勾选图1-35所示对话框中的更改方向前方框。最后单击对话框中的
按钮,

图1-33 选择对话框

图1-34

图1-35 拉伸对话框
完成实体绘制,如图1-36所示。

图1-36
(8)绘制实体。在菜单栏依次点选→
命令,出现选择对话框,如图1-33所示,按图中指示点选选择方式为串连,单击图1-36所示直线,最后完成图形的选取。接着弹出拉伸对话框,如图1-37所示,按图中参数进行设定,要确定绘图区图形出现的拉伸箭头为向下,如相反的话,勾选图1-37所示对话框中的更改方向前方框。最后单击对话框中的
按钮,完成实体绘制,如图1-38所示。在键盘上按下“Alt+S”键,可将曲面或实体进行渲染着色,如图1-39所示。

图1-37 拉伸对话框

图1-38

图1-39
2.进行零件的刀具路径规划和后处理(即项目的CAM部分)
(注:毛坯大小:80×80×30(单位:mm),刀具:φ 16立铣刀、φ 8立铣刀)
(9)外形铣削。首先点选菜单栏的→
→
命令进入铣削模块,再点选菜单栏的
→
,弹出名称对话框,如图1-40所示,输入文件名,单击
按钮完成文件名设定。接着弹出外形选择对话框,如图1-41所示,按图中指示选择外形选择方式,用鼠标单击图1-42所示直线,系统自动将四条直线串连,弹出刀具路径对话框,如图1-43所示,首先设定刀具大小及种类,按图1-43所示操作,弹出刀具对话框,如图1-44所示。单击平底铣刀按钮,出现刀具大小对话框,如图1-45所示,按图1-45所示设定,单击
完成刀具种类、大小确定。T.F.S参数按图1-43所示设定。再单击外形加工参数标签,进入外形加工参数对话框,如图1-46所示。单击
按钮,弹出对话框,如图1-47所示,按图中参数设定好,单击
完成平面多次铣削设定。单击
按钮,弹出对话框,如图1-48所示,按图中参数设定好,单击
完成Z轴分层铣削设定。其余参数按图1-46所示设定。最后单击
完成所有参数设定。结果如图1-49所示。

图1-40 名称对话框

图1-41 外形选择对话框

图1-42

图1-43

图1-44 刀具路径对话框

图1-45 刀具大小对话框

图1-46 外形加工参数对话框

图1-47

图1-48

图1-49
(10)挖槽加工。单击菜单栏中的→
命令,接着弹出外形选择对话框,如图1-41所示,按图中指示选择外形选择方式,用鼠标单击图1-49所示直线,系统自动将所示图素串连,弹出刀具路径对话框,如图1-50所示,首先设定刀具大小及种类,按图1-43所示操作,弹出刀具对话框,如图1-44所示。单击平底铣刀按钮,出现刀具大小对话框,如图1-51所示,按图1-51所示设定,单击
完成刀具种类、大小确定。其他参数按图1-50所示设定。再单击2D挖槽参数标签,进入2D挖槽参数对话框,如图1-52所示。单击图1-52中的
按钮,弹出分层铣削对话框,如图1-53所示,按图中参数设定,单击
完成设定。其他参数按图1-52所示参数进行设定。最后单击粗切/精修参数标签,进入粗切/精修参数对话框,如图1-54所示。按图中参数进行设定,单击
完成所有设定。系统自动计算刀路,结果如图1-55所示。

图1-50 刀具路径对话框

图1-51 刀具大小对话框

图1-52 2D挖槽参数对话框

图1-53 分层铣削对话框

图1-54 粗切/精修的参数对话框

图1-55
(11)实体验证。首先设定毛坯的大小,双击刀具路径/实体管理器的,下拉出子菜单,再单击
,弹出材料设置对话框,如图1-56所示,按图中参数设定,单击
完成毛坯设定。接着选取需要验证的刀路,操作如图1-57所示。弹出“实体切削验证”对话框,如图1-58所示,按图中参数进行设定。即可进行实体模拟,结果如图1-59所示。

图1-56 材料设置对话框
(12)生成程序单击图1-57所示的图标按钮,弹出“后处理程序”对话框,如图1-60所示。按图中参数进行设定,最后单击
完成后处理设置,接着弹出保存文件对话框,输入文件名,单击
完成操作。系统经过后处理生成程序,如图1-61所示。

图1-57

图1-58 “实体切削验证”对话框

图1-59

图1-60 “后处理程序”对话框

图1-61