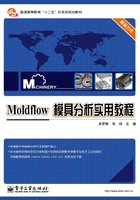
1.2 注塑模CAE的发展趋势
随着科学技术的迅速发展,互联网技术的普及和全球信息化,注塑模CAE技术功能进一步扩充,性能也进一步提高,呈现出如下的发展趋势。
1)用三维实体模型取代中心层模型
3D分析(实体流技术)正在被应用到多次注射成型、气体辅助成型、组合模腔成型和叠模成型。仿真软件分析三维的纤维取向和翘曲,3D技术(实体流技术)非常重要。因为2.5D (双面流技术)只能表明纤维在一个平面上的取向,而3D可以表明纤维在各个角度的取向。3D分析提供的信息是2.5D所无法比拟的,像湍流与层流的辨识,熔融物料中的气泡,喷射和重力的影响等。3D模拟还可以了解模具本身的情况。在2.5D模拟中,在模具中嵌入一个镶件后,需要生成相应网格,然后计算热量是怎样穿过这个镶件的。但是在3D模拟中,当进入模型,就可以观察到温度变化。台湾的Moldex 3D和德国的Sigmasoft,这些软件几乎都无一例外地专注于3D(实体流技术)领域。Moldflow为其最新的Moldflow Plastics Insight分析软件包开发了几种新模块,包括预测纤维取向、翘曲和厚壁制件中的热-机械性能分析的MPI3D模块。Moldflow在其3D软件中扩展了创建热固性塑料制品模型的能力。Moldflow Plastics Insight分析软件包支持64位计算机,可以较快地创建大的模型。如图1-4所示,Moldflow提供三种有限单元模型。

图1-4 Moldflow的三种有限单元模型
2)有限元、有限差分、控制体积方法的综合运用
注塑制品是薄壁制品,制品厚度方向的尺寸远小于其他两个方向的尺寸,温度等物理量在厚度方向的变化又非常大,若采用单纯的有限元或有限差分方法,势必造成分析时间过长,无法满足模具设计与制造的实际需要。在流动平面采用有限元法,厚度方向采用有限差分法,分别建立与流动平面和厚度方向尺寸相适应的网格并进行耦合求解,在保证计算精度的前提下使得计算速度满足工程的需要,并采用控制体积法解决了成型中的移动边界问题。对于内外对应表面存在差异的制品,可划分为两部分体积,并各自形成控制方程,通过在交接处进行插值对比,保证这两部分的协调。
3)数值计算与人工智能技术的结合
优选注塑成型工艺参数一直是广大模具设计人员关注的问题,传统的CAE软件虽然可以在计算机上仿真出指定工艺条件下的注塑成型情况,但无法自动对工艺参数进行优化。使用人员必须设置不同的工艺条件,进行多次CAE分析,并结合实际经验在各方案之间进行比较,才能得出较满意的工艺方案。同时,在对零件进行CAE分析后,系统会产生有关该方案的大量信息(制品、工艺条件、分析结果等),其中分析结果往往以各种数据场的形式出现,要求用户必须具备分析和理解CAE分析结果的能力,所以传统的CAE软件是一种被动式的计算工具,无法提供给用户直观、有效的工程化结论,对软件使用者的要求过高,影响了CAE系统在更大范围内的应用和普及。
4)制品与流道系统的三维流动保压集成分析
流道系统一般采用圆柱体单元,而制品采用的是三角形单元,注塑模CAE系统可以采用半解析法解决混合单元的集成求解问题,这样,不仅能分析一模一腔大型复杂的制品,而且能够分析一模多腔小型精密制品,大大拓宽了系统的使用范围。
5)塑料制品熔合纹预测的高效算法
熔合纹对制品的强度、外观等有重要影响,准确预测熔合纹位置是仿真软件的难题。注塑模CAE系统通过节点特征模型方法大大提高了熔合纹预测的准确性和效率,并利用神经网络方法对熔合纹的影响程度作出定性评价,为用户对成型质量的评估提供了直接的判断依据。
注塑模CAE技术的发展,给模具行业带来了一场技术革命。但因为塑料熔体是非牛顿黏弹性流体,制品结构复杂,成型充模流动过程的非稳态、非等温性,使充模过程的数值模拟相当复杂,所以在程序实现时进行了一些假设,建模过程进行了适当简化,这样计算结果精度与实际结果会有偏差,然而总体趋势与实际结果是一致的。由于进行CAE分析时还要重新建模,不能充分利用产品设计的三维模型,造成重复劳动。国外注射模软件商已开始着手于集成化的CAD/ CAE技术研究,并有商品化软件形成。虽然这些软件能识别CAD的三维图形,但集成的CAD/CAE软件本身不具备建立浇注系统、冷却管网等的功能,使分析应用范围大大减小。