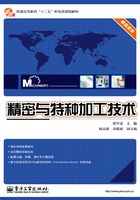
第2章 超精密切削加工技术
2.1 概述
当代超精密加工技术(SPDT)是美国在20世纪60年代初用单刃金刚石车刀镜面切削铝合金和无氧铜开始的。利用金刚石刀具进行超精密切削,在符合条件的机床和环境条件下,可以得到超光滑表面,表面粗糙度可达Ra0.02~0.005μm,精度小于0.1μm。目前,采用金刚石切削技术可以加工的材料主要有:塑性材料,如有色金属(铜、铝合金等)、金、银、无电镍、有机玻璃、各种塑料制品(照相机的塑料镜片、隐形眼镜镜片)等;脆性材料,如硅、锗、红外光学晶体(碲镉汞、锑化镉、多晶硅、硫化锌、硒化锌、氯化钠、氯化钾、氯化锶、氟化镁、氟化钙、铌酸锂、KDP晶体等)。上述材料经过金刚石超精密切削加工均可直接达到光学表面质量要求。
金刚石超精密切削技术,包括金刚石超精密车削技术和金刚石超精密铣削(飞切)技术,是超精密加工技术的重要分支,也是超精密加工技术发展最早的、应用最为广泛的技术之一。金刚石超精密切削技术是在超精密数控车床上,采用具有纳米级锋利度的天然单晶金刚石刀具,在对机床和加工环境进行精确控制条件下,直接利用金刚石刀具单点切削加工出符合光学质量要求的光学零件。金刚石刀具具有较高的耐磨性及形状再现性。金刚石超精密加工的切削深度一般在微米量级,可加工出微米及亚微米级的形状精度及纳米级表面粗糙度的精密工件。
根据加工表面及加工刀具的特点,精密与超精密切削加工可分为四类,见表2-1。
表2-1 精密与超精密切削方法

精密切削研究是从金刚石车削开始的。应用天然单晶金刚石车刀对铝、铜和其他软金属及其合金进行切削加工,可以得到极高的加工精度和极低的表面粗糙度,从而产生了金刚石精密车削加工方法。在此基础上,又发展了金刚石精密铣削和镗削的加工方法,它们分别用于加工平面、型面和内孔,也可以得到极高的加工精度和表面质量。金刚石刀具精密切削是当前加工软金属材料最主要的精密加工方法。除金刚石刀具材料外,还有立方氮化硼、复方氮化硅和复合陶瓷等新型超硬刀具材料,它们主要用于黑色金属的精密加工。