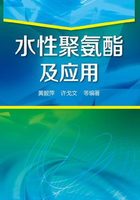
第2章 水性聚氨酯木器漆
2.1 概 述
木器漆对木质家具等不仅有装饰美化作用,而且起着很好的保护作用。但目前使用的木器漆大多为溶剂型,包括大量使用的聚氨酯漆,都含有大量并且往往具有毒性的有机挥发性化合物(VOC),严重危害生产、施工和使用人员的身体健康,对大气环境有着不可逆转的危害。自20世纪60年代以来,世界各国开始重视VOC对大气的污染,西方发达国家还成立了专门的管理机构,制定了各种法规对涂装时的溶剂挥发量加以严格的限制。如1966—66法规(加利福尼亚/美国),目标是减少涂料(油漆)中的溶剂量;1984年德国油漆生产商协会公约,目标是降低溶剂刺激性;1991年清洁空气运动(美国),目标是VOC低于规定限量;1999年有关工业有机挥发物限制的欧洲导向,目标是从1990年至2007年有机挥发物的刺激性要降低70%。因此,各种环境友好型涂料应运而生。作为涂料工业的重要组成部分的木器漆,同样也随之经历了一个重大的变革。20世纪40年代,P.Schlack制备出了阳离子水性聚氨酯,标志着水性聚氨酯涂料的开端。20世纪70年代,阴离子型水性聚氨酯成功开发。1980年,水性丙烯酸-聚氨酯共混体系在瑞典等北欧国家迅速推广并商品化。1987年,开发出水性聚氨酯-丙烯酸共聚树脂,并开始在欧洲商品化。到20世纪90年代,双组分体系、水性UV固化树脂体系开始出现,特别是双组分体系,使得水性聚氨酯木器漆在性能上接近溶剂型的指标,从而得到广泛应用。
水性聚氨酯木器漆具有施工性好,附着性、坚韧度高,高度耐撞击性等优点。其成膜物水性聚氨酯树脂从电荷上分类,主要有阴离子型、阳离子型和非离子型三大类,其中使用比较多的是阴离子型水性聚氨酯树脂。以水性聚氨酯树脂为主要成膜物质的涂料在多种性能上优于水性丙烯酸树脂,如水性聚氨酯木器漆的光泽较高,较好的可以达到90°以上,而丙烯酸树脂或PUA/APU一般都只能达到80°~90°。但是,水性聚氨酯木器漆成本较高,结合保光、保色性、耐候性,往往水性聚氨酯和丙烯酸乳液按不同比例物理混合使用以平衡涂膜的性能及成本。
目前市售的水性聚氨酯木器漆用树脂主要有三种。
(1)单组分水性聚氨酯树脂 聚氨酯树脂分子结构是由硬链段和软链段组成的,硬段和软段有两个Tg,使水性聚氨酯具有优异的低温成膜性和柔韧性,而且耐磨性好、硬度高、光亮度大、抗热回黏性好,并且通过调节软、硬链段的种类和组成比,可以得到不同性能的水性聚氨酯产品,非常适用于配制各种高档的水性木器面漆,如家具漆和地板漆[1]。
为了进一步提高水性聚氨酯木器漆的物理性能及耐化学品性,目前人们在制备过程中选用不饱和油(如亚麻油、蓖麻油等),以引入不饱和键,制得自交联型水性聚氨酯,不仅提高涂膜的物理性能及耐化学品性,还可以提高干燥速率,降低成本。由于水性聚氨酯中引入了亲水基团,会导致其耐水性下降,可用含有羟基硅氧烷基团的有机硅化合物或含氟化合物进行封端,制备含硅/氟水性聚氨酯分散体,得到具有优异的耐水性、抗划伤性及耐候性等性能的单组分水性聚氨酯木器漆[2]。
(2)水性聚氨酯-丙烯酸共聚树脂 综合水性聚氨酯的物理性能、耐化学品性、抗热回黏性和水性丙烯酸树脂的润湿性、颜料的分散性、成本、含量等特点,可以通过化学接枝改性的方法,制备出了水性聚氨酯-丙烯酸共聚树脂[3]。在控制成本的同时,大大改善了涂膜的耐化学品、耐溶剂性及耐沾污性。但目前市售的多为水性聚氨酯-丙烯酸共混树脂,性能上接近共聚树脂,但水性聚氨酯和丙烯酸乳液为两种不同的体系,存在着相容性的问题,这不是简单的pH值问题,还存在热力学稳定性问题,所以在配漆前一定要注意以下几点。
①相容性。液态混合放置一段时间,可以观察混合溶液的外观,如黏度有无变化、有无沉淀析出、有无成胶甚至分层等现象发生来判断其相容性,更好的办法是在玻璃板上涂覆干燥后,观察涂膜的透明性及表面状态等来判断其相容性。
②一定要掌握两种树脂的离子型态。相同离子型的混合后稳定性相对较好,但即使相同离子型还要注意离子强度和离子的电荷作用,有无自由离子存在(像丙烯酸树脂中乳化剂)也是在实际混拼过程中要特别注意的。
③要注意树脂极性的过渡性。比如选一个高极性的和一个相对低极性树脂相拼,相容不好,可以再选一个极性介于两者之间的第三种树脂来平衡两者的极性。
(3)双组分水性聚氨酯树脂 与单组分水性木器漆相比,双组分水性木器漆采取外加交联剂的办法来提高漆膜的综合性能,常见的交联剂有聚氮丙啶、碳化二亚胺,更多的是用水分散多异氰酸酯[4,5]。双组分水性聚氨酯树脂在硬度、光泽、耐水性、耐化学品和耐候性方面与溶剂型双组分聚氨酯木器漆相近,然而水性双组分聚氨酯木器漆的VOC含量很低,可减少70%~90%,且干燥速率快,光泽、物化性能及使用期能满足水性木器漆的要求。但水分散多异氰酸酯中异氰酸酯基不仅与羟基反应,同时也与水发生反应,生成CO2,这些气体如果在成膜前不能及时排出,很容易造成涂膜起泡现象,这在实际应用中特别容易出现问题。
水性聚氨酯木器漆除了上述三种树脂以外,目前还有水性光固化聚氨酯树脂,它的光固化机理是丙烯酸聚氨酯树脂中的丙烯酸双键在光催化下断键而固化,与传统的光固化树脂相比,在耐化学性、抗沾污性以及打磨性方面性能相近,在环保、有毒有害物质含量以及价格特别是再涂覆性方面明显优于传统的光固化树脂[6]。
我国是家具大国,但人均年家具消费程度却很低。据统计,我国人均家具消费程度仅仅是欧美等发达国家和地区的5%。特别是乡村市场家具的占有率更低。中国是木器漆生产和消费大国,年产量在25万吨以上,但水性漆所占比例很少。目前欧美市场水性木器漆在不同领域有5%~80%的使用率,且每年以接近9%的比例增长。
水性聚氨酯木器漆在我国先后经历了十几年的曲折发展历程,真正进入市场还是近几年的事,目前从事水性木器漆研究的高等院校、科研院所和生产企业据报道超过200家。水性木器漆产品已渐渐应用于一些高档宾馆、酒店、医院等公共场所。品种上,儿童家具用漆发展速度很快,已经成为单独的品种。水性聚氨酯尽管综合性能好,但由于价格高,某些性能如丰满度、硬度等还满足不了市场需求,所以市场反映不是很积极,客观上造成了真正从事水性木器漆生产和推广的企业寥寥无几,大部分涂料生产企业都持观望态度。所以在“十二五”涂料行业产业规划中,提出的“清洁生产、循环经济、环境友好、节能减排”四方面规划,为我国水性聚氨酯木器漆的发展提供了良好的契机。
在过去的几年中,水性聚氨酯技术在木器漆领域得到了快速的发展,但水性聚氨酯木器漆的全面推广还需要行政的干预及消费者在理念上的认同。尽管发展前景一片光明,但需要整个行业的努力和呵护。从技术而言,目前国内还处在发展阶段,特别是漆膜厚度及光泽度等性能不如溶剂型,施工性能也不如溶剂型发展得成熟,但这并不妨碍水性聚氨酯木器漆最基本和最重要的保护功能。对涂料产品既强调环保性能又苛求物理性能,在目前全球范围内都不是明智的要求。而木器漆的水平在一定程度上体现了一个国家的涂料工业发展的水平。我国木器漆主要应用于两大领域,一是用于家具制造厂,二是用于室内装修装饰,即家具漆和家装漆;而根据木制品不同的使用场所,水性聚氨酯木器漆可分为以下几个品种。
①木制家具:是目前水性聚氨酯木器漆的主要应用领域,以工厂化生产家具为主,特别是儿童家具制品的涂饰。
②室内装修:以手工刷涂为主要施工手段的家庭装修和公共场所装修,如木门、窗、橱柜、家具等涂饰。
③木地板:是工厂化生产木地板用,目前以水性光固化丙烯酸聚氨酯漆为主。
④木制玩具:以不透明涂饰为主,重金属含量不能超标是其主要的质量指标。
⑤铅笔涂料:是一类不透明涂饰的专用木器漆,除要求快干外,重金属含量也不能超标。
⑥户外用木制品:木制亭阁、休闲木制品、室外木饰。其要求是有一定的耐候性。
随着水性聚氨酯木器漆的应用领域的不断扩大,除了性能的提高外,其环保级别还将不断发展和升级[7]。目前的无甲醛、无苯概念已经远远不能满足人们的需要。水性聚氨酯木器漆还在向着低VOC(挥发性有机化合物)、低或无APEO(烷基酚聚氧乙烯醚)、无重金属的方向不断发展,不但要满足木器装饰、保护的需要,更要保护好人类健康和生存环境。