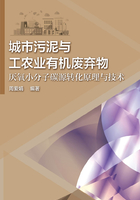
1.2 城市污泥预处理研究现状
剩余污泥中微生物细胞壁属于生物难降解物质,呈半刚性结构,严重阻碍了胞内有机物的溶出和水解,进一步影响了污泥厌氧消化的降解速率,因此,高效的预处理技术是污泥资源化利用的前提。
1.2.1 物理预处理
1.2.1.1 热处理
热处理早在1970年便被用于提高污泥的脱水性能。热处理一般是指将污泥温度加热到150~200℃,与之相对应的压力通常为600~2500kPa。经过热处理后的污泥,其胶体结构被破坏并释放出污泥絮体内部和细胞内部的间隙水[36],与此同时,细胞内的有机物也随之被释放出来。
近年来,对污泥进行热处理以获得大量溶解性的易降解有机物,从而补充污水处理过程中不足的碳源成为了研究热点。同时,基于热预处理的一些商业化污泥处理工艺逐渐开发,并用于污泥的处理。例如,挪威Cambi公司开发了一套热水解系统,在180℃处理30min条件下,处理后的污泥溶胞率可达30%,相应的产气量提高150%。Veolia公司的水务子公司Krüger公司亦开发出相似的热处理装置,以BioThelys®系列出售。另外,很多研究者在采用热预处理提高污泥厌氧消化性能方面做过很多研究,采用的处理条件和主要的结果见表1-3。
表1-3 热预处理综述

污泥的热处理不应仅仅被看作是促进污泥溶解的一种方法。在微生物细胞溶解的同时,污泥的脱水性能也得到了提高,此外还达到了污泥灭菌的目的。污泥在脱水后,其热水解过程所产生的易于生物降解的有机物都溶解在水解液中,因此热处理也可以被认为是污泥稳定的一种方法。
1.2.1.2 超声预处理
利用超声波在液体中传播时产生的空化作用破解污泥絮凝体、菌胶团和细胞体。该方法可认为是多种作用效果的综合。
Tiehm和Neis等人利用3lkHz、3.6kW的超声波处理污泥64s,污泥中SCOD由63mg/L增加到2270mg/L,而且使后续厌氧消化的SRT(固体停留时间)由22d缩短至8d,生物气产量明显增大[46]。F. Wang等人研究了超声破解污泥释放进入液相的组分,发现超声破解后,污泥的SCOD增加较多,溶液中的蛋白质、DNA、Ca2+和Mg2+浓度都相应增加[47]。Q. Wang等人研究超声波预处理污泥对厌氧消化的影响,结果发现利用9kHz、200W超声波处理污泥10~40min,破解时间在10~30min内,污泥的COD浓度、蛋白质浓度和碳水化合物浓度都随着破解时间的延长增大较快,而破解时间为40min时,污泥中各物质浓度增大趋缓;破解时间在10~30min内,厌氧消化时累计产气量增大明显,而40min时,累计产气量增大较小[48]。Tiehm和Zeilhorn等人的研究结果也证明超声破解后的污泥厌氧消化时,VS降解率由21.5%增加到33.7%,生物气产量增加了41.6%。C. P. Chu和D. J. Lee等人的研究也得到了相似的结论[49]。其他超声预处理研究见表1-4。
表1-4 超声预处理综述

1.2.1.3 机械预处理
机械预处理污泥的原理是利用剪切力来破碎微生物的细胞壁。研究表明,将污泥在87℃下剪切预处理6~10min后,其厌氧消化性能大大提高,有机物组分中的88%~90%转化为生物易降解物质。
Harrison采用高速混合球磨机破碎污泥。据报道这种球磨机可以有效地破碎污泥中的高分子有机物,但能耗较高,破碎单位质量的干污泥需要60MJ的能量[54]。高压均质器是一种应用较广的机械处理方法。在高压均质器内,污泥首先在60MPa的压力下被压缩,然后以较高的速率通过阀门,细胞被压紧环粉碎。在此过程中,微生物细胞受到了紊流作用、气穴作用和剪切作用,从而导致了细胞的解体。在能耗为30~50MJ/m3的情况下,就可以使85%的污泥破碎。
Lin等采用了化学/机械的方法来促进污泥解体。首先使CO2在25~35MPa的压力和55℃下穿透细胞壁,渗透到细胞内部,当压力下降时,CO2气泡会膨胀并充斥着整个细胞,随着气泡的破碎,微生物细胞也会破裂。这种方法可以使污泥中80%的微生物细胞解体。其他机械预处理研究见表1-5。
表1-5 机械预处理综述

注:1bar=105Pa。
尽管各种机械处理方法对污泥中颗粒有机物的破碎很有效,但这些方法都需要较高的能耗,因此它们的应用受到了限制。
1.2.2 化学预处理
1.2.2.1 酸碱调节
酸碱调节处理是向污泥中加入酸或碱来促进污泥的水解,通过水解、皂化细胞壁和细胞膜上的蛋白质和脂多糖,破坏污泥的絮体结构和微生物细胞结构,使胞内物质向浓度较低的胞外环境释放,使不可溶的物质通过化学分解作用转化为可溶物质。与热处理方法需要采用的高温条件相比,酸碱调节处理只要求在常温或中温条件下进行。具体酸碱调节预处理研究见表1-6。
表1-6 酸碱调节预处理综述

因为需要的pH值条件比较极端,尽管酸碱调节方法对污泥溶胞比较有效,但是在后续进一步处理时却需要中和反应,因此其应用较受限。
1.2.2.2 氧化剂
传统的氧化法是利用氧气来破碎微生物细胞,为了提高效率和反应速率,传统的氧化法常常在高温(260℃)和高压(10MPa)的条件下进行[60],污泥中的一部分有机物会被彻底氧化为CO2和H2O。氧化作用会导致污泥中的颗粒性有机物溶解到液相中,因此被氧化的污泥的上清液中有机物负荷会升高。但是,腐蚀设备、高能耗和散发臭气等问题限制了传统氧化法的实际应用。20世纪90年代,湿式氧化成为了污泥氧化处理的主要手段。在荷兰建成了一座200m深的中空井,这样的深度可以保证系统内的压力。新鲜的污泥从井的内层流入,处理后的污泥则由井的外层流出,通过这样的对流方式使得热量由处理后的污泥传递给新鲜的污泥,从而实现了热交换。这样的处理方式可以获得较高的污泥溶解率和去除效率(20%的颗粒固体溶解,75%的溶解态有机物被完全氧化)。
最常用的氧化剂是过氧化物类氧化剂,氧化机理是释放出新生态原子氧,氧化菌体中的活性基团,氧化特点是作用快而强,能杀死所有微生物。常用的过氧化物类氧化剂有臭氧(O3)、过氧化氢(H2O2)、过氧乙酸等(氧化电位2.8V)。由于本身的高氧化能力,有毒副产物未检测到[61]。具体过氧化物类氧化剂预处理研究见表1-7。
表1-7 氧化剂预处理综述

氧化法对污泥中有机物的去除十分有效,但是氧化法往往需要复杂的操作和极端的反应条件,如高温高压,因此对这一方法的广泛应用和反应条件的优化仍需要进一步的研究。
1.2.2.3 表面活性剂
表面活性剂的应用领域很广,比如洗涤剂、化妆品、食品、造纸、制革、石油、印染、医药、农药、胶片、金属加工、选矿等各个工业部门。近年来,关于表面活性剂在环境领域中的应用有较大的突破,而且其应用范围还在不断地拓展[71]。
表面活性剂用于剩余污泥处理的研究在国内外不多。同济大学陈银广教授[72]发现加入表面活性剂后明显改善污泥的脱水性能,并认为其机理在于表面活性剂能加快污泥的沉降速度、减少污泥颗粒间的间隙水,同时促进污泥所含的蛋白质和DNA释放到水相中。随着表面活性剂量的增加,更多的有机质从污泥表面释放到外界环境中;在一定时间范围内,释放的蛋白质和DNA的浓度随时间的延长而增大。这一机理就在于表面活性剂具有独特的性质:不但具有“两亲”即亲水亲油的性质,而且还有“增溶”作用。“两亲”作用是指表面活性剂连接于污泥表面的大分子(具有亲油性)与水分子之间,在外界搅拌力的作用下,污泥表面(胞外聚合物中)的大分子物质(如蛋白质和DNA)能够脱离污泥颗粒。增溶作用指表面活性剂使一些溶解度不大或难溶物质的溶解度增加的现象。具体表面活性剂预处理研究见表1-8。
表1-8 表面活性剂预处理综述

虽然很多研究者在试验中发现,化学表面活性剂(主要是SDBS和SDS)加入到剩余污泥体系中,能够促进剩余污泥中颗粒态有机物的溶解、溶解态大分子有机物(蛋白质和碳水化合物)的水解以及水解后小分子有机物(氨基酸和单糖)的降解和酸化过程,降低了产甲烷菌的活性。从而使得剩余污泥厌氧发酵过程的中间产物SCFAs得以大量积累。
但是化学表面活性剂对微生物细胞具有一定程度的毒性,主要是因为它们能够溶解细胞酶、细胞受体和蛋白,导致细胞膜的生理功能紊乱或者细胞膜损伤,从而改变细胞膜的透过性能,对微生物的生长与繁殖造成危害。且化学表面活性剂本身难降解,沉积在处理后的污泥系统中,易引起二次污染。
1.2.3 生物预处理
在传统的污泥厌氧消化过程中,污泥中的颗粒态有机物先要水解为小分子有机物释放到液相后,才能被进一步转化为甲烷气体。这一颗粒态有机物转化为溶解态小分子有机物的过程就是生物水解的作用。一般说来,生物水解过程操作简单,是向污水中原位补充生物易降解碳源的最简单、最经济的方法。然而,由于生物水解污泥颗粒有机物的速率较慢,要获得满意的水解效果,常常需要较长的固体停留时间,这样造成反应池内的污泥负荷偏低。
一些学者通过加入纯菌种或相应的酶制剂来提高传统生物法水解污泥的速率。文献中报道有研究者分离出7株厌氧的高效产酸菌(Clostridium bifermentans DYF),并考察了它们对厌氧消化池内污泥水解和发酵的影响[77]。结果表明,这些菌株可以将污泥中50%以上的挥发性固体溶解到液相中,并将溶解态的有机物转化为有机酸(其中大部分为乙酸)。批试试验的结果显示,接种这些菌株的厌氧消化池在连续运行30d内,初始阶段的厌氧消化速率提高了20%以上,甲烷产量增加了10%。Luo等[78]考察了在污泥中投加酶制剂对污泥中颗粒态有机物的水解速率的促进作用,研究发现,由于污泥的成分复杂和酶的专一性(即一种酶只能作用于一种物质或一类物质),若要获得较高的水解效率,需要投加多种不同的酶,这样造成了操作费用的大幅度提高。
上述几种用于提高污泥中颗粒态有机物水解速率的处理方法,与传统的生物法相比具有水解效率高、水解速率快、提高污泥厌氧消化的甲烷产量等优点,然而,由于能耗高、操作费用高、腐蚀设备和极端的操作条件(如高温高压)等问题,而没有得到广泛的应用。