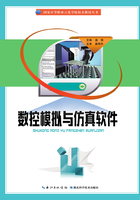
第一篇 机床基础知识简介
1 概述
一、数控机床的发展史
第二次世界大战结束以后,美、苏两国的军备竞赛日益激烈,制空权更是竞争的焦点,而那时飞机零部件的加工均是依靠样板来实现的,效率低、效果差。1948年美国空军向吉斯汀·路易斯公司提出了研制直升飞机螺旋桨轮廓检查样板的加工设备任务,1949年经美国空军的批准,该公司与美国麻省理工学院联合研制数控铣床,经过三年研究,于1952年成功研制出了世界上第一台电子管数控铣床。
第一台数控铣床问世以后引起了世界各国的关注,认为它的出现不仅解决了复杂曲线曲面的加工问题,而且指出了今后数控机床自动化的发展方向,因此纷纷投入研制数控机床。经过50多年的研究和发展,现在的数控机床已是集超大规模集成电路技术、计算机硬软件技术、现代机械制造技术、通信技术、管理控制技术、网络技术、液压气动技术和光电技术为一体的,具有高精度、高效率、高智能、高自动化和高柔性等特点的机械自动化设备(甚至是机械加工机器人)。其产品不仅覆盖了全部传统的切削加工机床,而且推广到锻压、电加工、焊接、激光切割、测量和抄写机等各方面,打开了机械自动化加工的新篇章。
数控系统的发展直接决定了数控机床的发展水平,数控装置的发展一共经历了五个发展阶段:
(1)第一代数控装置是采用电子管元件,其体积大、可靠性差、制造成本高,因此主要用于军工部门,没有得到推广应用,产量比较小。
(2)第二代是1958年出现的晶体管和印刷电路板组成的数控装置,虽然其可靠性有所提高,体积大为缩小,但其可靠性还是低,所以产量虽然有所提高,但不是很明显。
(3)第三代是1965年商品化的集成电路数控装置问世以后,大大缩小了数控装置的体积,由于功耗小,可靠性也得到了实质性的提高,从而成为一般用户所能接受的设备装置,因此数控机床的产量和品种均得到了较大的发展。
(4)第四代:1970年小型计算机在数控装置中得到了应用(数控装置NC因此改称为CNC-COMPUTER NUMBERICAL CONTROLOR),超大规模集成电路也已飞速发展,大大提高了数控机床的智能化程度。
(5)第五代是随着微处理器的发展和计算机软件技术的飞跃发展,数控功能日益强大,体积不断缩小,价格大幅下降,可靠性进一步提高,网络远程控制远程诊断和数控机器人也已开始应用。
数控伺服驱动装置也经历了几阶段的发展:
(1)开环控制的步进电机,精度差;
(2)半闭环控制的直流伺服电机,由于驱动电源为大功率直流,所以大功率变换元件成本高,精度好,稳定性差;
(3)半闭环交流伺服电机,成本相对降低,精度高,稳定性好;
(4)交流伺服加上磁栅尺、光栅尺形成全闭环控制,能将最终传动误差反馈并得以纠正,所以传动精度得到了进一步提高。
1958年北京第一机床厂与清华大学合作试制成功我国第一台数控铣床,但由于相关工业基础较差(尤其是电子工业),致使发展速度缓慢。
直到1970年北京第一机床厂XK5040型升降台数控铣床才开始作为商品。1975年沈阳第一机床厂的CSK6163型数控车床才真正作为商品推向市场。1974~1976年间,虽然开发了加工中心、数控镗床、数控磨床和数控钻床,但因为数控系统不过关,多数机床没有在生产中发挥作用。
20世纪80年代前期,即“六五”期间,进口日本FANUC数控系统后,我国的数控机床才真正进入小批量生产的商品化时代。
通过“七五”、“八五”期间的数控技术攻关,大大推动了我国数控机床的发展。目前我国已经有自主版权的数控系统,但产品品质和功能档次跟国外相比差距很远,国内绝大多数数控机床还是采用国外CNC数控系统。由于长期以来以美国为首的资本主义国家一直在这方面对我国进行严密封锁,国内数控机床无论是可靠性、精度、生产效率和自动化程度,与国外相比,还存在着不小的差距。
20世纪90年代,进口数控系统纷纷进入中国市场,如:日本FANUC、德国SIEMENS、日本MITSUBISHI、西班牙FAGOR、德国MARHO、法国NUM、日本安川、日本TOSHIBA、日本大森等,使中国数控机床真正进入了批量商品化时代,也就是说进口数控系统还是占据中国大部分市场,国内数控系统尚未成气候。
中国数控技术的普及工作起步也很晚,1999年以前中国没有一所院校开设数控专业,在发达城市的模具工业的拉动下,加上各大媒体的强烈宣传,1999年后全国各地大、中专院校纷纷开始强占热门专业市场,两年时间,全国上千首学校立即开设了这种专业,相当一部分学校是将有编制有职称的非专业教师送到机床制造工厂去培训一星期后回来教学,有的中等专业学校的老师甚至照本宣读,自己都没见过数控机床,这就是说目前我国数控专业师资力量奇缺,办学秩序混乱,毕业学生专业素质差,从某种程度上也制约了我国数控技术普及事业的发展。
二、数控机床的发展方向
数控机床的发展跟其他机械、电子行业一样,呈加速度发展,今后的数控机床朝着高效率、高精度、高自动化、高复合化的方向发展,随着单机自动化程度的不断提高,出现了由多台数控机床组成的自动化程度更高的生产系统:
(1)计算机直接数字控制系统(DNC),这种系统是用一台通用计算机直接控制多台数控机床进行多品种、多工序的自动加工。这种方式解决了CNC系统存储量不足的问题,同时也使从计算机辅助设计、计算机辅助工艺编制、自动程序编制到数控机床之间信息的直接传递成为可能,减少了生产准备时间。
(2)柔性制造系统(FMS),柔性制造系统是由多台加工设备、物流系统和信息流系统三部分组成的高度自动化和高度柔性化的制造系统,即全自动生产线。它可以实现几种、几十种甚至上百种零件的自动混流加工,是生产自动化的重要设备。
加工设备是柔性制造系统的主体,负责工件的加工。它可由相同或不同的若干台数控机床和一些辅助设备,如清洗机、测量机、简易机器人等。
信息流系统由中央控制器和各级控制器组成。中央控制器根据作业计划,通过各级控制器控制加工设备和物流系统自动协调作业,同时还要对在线测量和状态监控反馈回来的信息和数据流进行处理,出了问题能自动修改作业计划。
(3)自动化工厂(FA),所谓自动化工厂,实际上是制造车间的自动化。它由一台通用计算机控制车间内的几条柔性制造系统(FMS),车间内只需几个工人负责工件的装卸就可以了。

图1-1 数控车床数控控制简易逻辑
(4)计算机集成制造系统(CIMS)计算机集成制造系统是指用最新的计算机技术控制从定货、设计、采购、工艺、仓储、管理、制造到销售的全部过程,以实现信息系统一体化的高效率的柔性集成制造系统。它是在生产过程自动化(如计算机辅助设计、计算机辅助工艺设计、计算机辅助制造、柔性制造系统(FMS)、自动化车间(FA)等)的基础之上,加上其他管理信息系统的发展和逐步完善的计算机分析与控制能力,这就能把全厂的生产活动、管理行为、信息指令传达等合理高效的统揽,最终实现全厂的综合自动化(俗称智能工厂,如我国宁夏小巨人机床有限公司)。
三、数控车床的结构
数控车床的床身与普通车床相似,数控车床加了一套以数控控制系统为主的电气控制系统(下图作简单示意),实现了自动化控制,操作编程人员通过操作面板或计算机输入程序指令到数控系统CNC,数控系统内的CPU。
处理器进行运算和判断,并按处理结果进行控制,系统内插补器进行运动控制信号的发生和运算,并将驱动脉冲传送给各轴伺服驱动器,驱动器将运动脉冲进行功率放大,并用放大后的信号驱动伺服电机旋转,伺服电机带动机床丝杠旋转,通过丝杠的旋转带动丝杠螺母移动就将电机的旋转运动变换为直线运动,丝杠、丝杠螺母安装在车床拖板下面,丝杠螺母与拖板固定连接,刀架固定在拖板上,所以就实现了刀架纵横方向的直线运动,而电机的运动是否绝对符合插补器的控制呢?有了误差怎么办?所以在电机的后面加装了旋转编码器,编码器与伺服电机一起旋转,并且编码器每转一个微小的角度,就会感应到一个信号,同时将这个信号发送给数控系统,数控系统就根据这一反馈信号与插补器信号相比较,并将其差值发送给伺服驱动器,再去控制伺服电机进行纠偏工作,实现一个由跟踪—反馈—比较—纠正—跟踪的循环,而这一循环在一秒钟以内会进行几万到几十万次,在这几十万分之一秒的时间内,伺服电机可能出现的误差是很小很小的,可以近似的认为没有误差。近似到底是近似,近似是相对的,误差是绝对的,虽然小得惊人,但总是有的(误差大小还与电机的运动加减速设置有关),所以在数控系统的系统参数里还会设置允许的最大误差,当出现不恰当的加减速或其他意外冲击而导致误差超出设定值时,系统会立即截断伺服驱动器的电源,停止工作,并报警提示。这就为数控车床实现较高精度提供了较好保证。
另外,数控车床除了伺服轴控制以外,还有一些如水泵、油泵、液压部分的电磁阀、电磁离合器、刀架电机、刀架定位等控制(即外围控制),这统统由可编程序控制器(PLC)控制,在数控机床上又叫PMC(即可编程机床控制器), PMC内的梯形图程序控制各继电器和交流接触器,再由交流接触器控制各终端部件。所以机床除了配备系统操作面板和显示器外,还得配置如下图的下半部所示的机床控制面板。

图1-2 机床控制面板
上述将编码器连接在伺服电机后的反馈控制方式叫半闭环控制,这种控制方式能有效保证电机的旋转精度,但在电机以后的传动中还会出现如丝杠间隙、丝杠螺距误差、丝杠的轴向窜动、丝杠螺母到刀架的几个连接松开等等的故障误差,这部分的误差没有反馈和纠偏,所以这种反馈传动中间环节的反馈方式只能叫做半闭环。如果要想最大程度的提高控制精度,那就得反馈并纠正传动终端的误差,这种控制方式被称为全闭环,在车床上体现为用直线光栅尺或磁栅尺安装在车床拖板下面,直接跟踪拖板的运动精度,在外圆磨床等高精度机床上则通过探头监测工件直径来反馈和纠偏。
干过普通车床的读者都知道,旋转体的工件大多数有精度要求的都是直径方向(外圆、内孔或子口),所以中拖板运动(径向X方向)精度比横向(轴向Z方向)更为重要,所以全机能的数控车床都采用三副六导轨,尾座采用一副水平导轨,使尾座与主轴轴心线同轴,大拖板支撑采用一副倾斜安装的导轨与主轴轴心线平行(在主轴轴心线的里侧,远离操作者的一侧,X轴(径向)正方向与平导轨的经济型数控车床方向相反,坐标结构如图1-3),使中拖板与水平面夹角45°或30°(形成斜床身),倾斜的目的是借助刀架的自重来克服机床间隙造成的误差,让每一次反向运动不会受到间隙的影响而少运动间隙量。

图1-3 全机能斜导轨数控车床坐标系
全机能数控车床的主轴一般采用大功率主轴电机或伺服主轴,与机床主轴直连实现无间隙传动和无级变速,所以全机能数控车床能实现恒定线速度切削,即使在车工件端面时也通过变速保持刀尖与工件的相对摩擦速度恒定,确保最理想的刀具寿命。
全机能数控车床一般都配备液压卡盘或电动卡盘用脚踏开关程序双重控制,配备下料机和工件推进器或上料机械手就可以实现自动装夹,还配备液压尾座,除程序指令控制外一般还配有脚踏开关或旋钮控制,实现自动伸缩尾座套筒,高档的机床还会配备可编程移动尾座,或改尾座为第二主轴,配置双刀架、双液压卡盘,实现调头车一次完成。(如图1-4所示)有的机床在刀架上配置旋转动力铣头,主轴电机用伺服电机与X、Z轴联动形成第三联动轴(旋转轴),可以实现车、钻、铣、镗等切削功能,所以这种机床又被称为数控车铣中心。
一般这种机床的数控系统配置都比较高,一般配置FANUC0TC、FANUC0i-TA/B、FANUC0i-Mate、FANUC18i-T、FANUC21iT等全功能数控系统,这类机床一般配有软卡爪(可自车后装夹,实现较好的装夹精度)和活络顶尖(顶尖顶住工件时和工件一起旋转,不容易烧损)。

图1-4
所以当机床配置较高(如配置了机械手、第二主轴、自动对刀仪等)时,具体相关控制指令要看机床制造商的设计(可以查看机床说明书),特别是一些单动作的M指令,都是由PMC梯形图设计确定的,具体国际标准并不全面,另外各机床商的贯标情况并不好,同一个功能在不同机床上不一定用同一个M指令,所以只能以机床商的说明书为准,因而熟悉机床也非常重要。