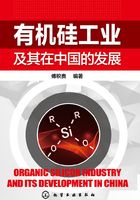
第四章 硅橡胶
一般硅橡胶都有优越的电气性能并能在-55~200℃宽广的温度范围内工作而不丧失其卓越的电气性能,此外尚有耐燃油的氟硅橡胶和能在-110℃工作的苯基硅橡胶等,这些都是航空航天部门和国民经济各部门极为需要的关键材料。从硫化机理上分硅橡胶有用过氧化物硫化的热硫化硅橡胶,有缩合型的双组分室温硫化硅橡胶,湿气硫化的单组分室温硫化硅橡胶和铂催化的加成型硫化硅橡胶以及比较新的紫外线或射线硫化硅橡胶等。早在20世纪50年代末我国就有多个单位开始研发各种硅橡胶及其应用。
第一节 最基本的热硫化硅橡胶
中国开始探索硅橡胶的起步在世界上并不算很晚,如中国是从20世纪50年代末期开始研究制造热硫化(也称热熟化)硅橡胶生胶的。由于开发工作需要大量、高纯度的二甲基二氯硅烷的水解物(从中获得八甲基环四硅氧烷,即D4或DMC),而此前由于没有大量的甲基氯硅烷,就难以得到大量纯净的二甲基二氯硅烷,也就无法有足够量试制硅橡胶生胶的基本原料八甲基环四硅氧烷;还有在开环聚合时要有的合适催化剂国内找不到。这些在开发初期是大难题,特别是甲基氯硅烷的工业性生产难度很大,因此中国有关单位的技术人员为此付出过大量的劳动,花费过很多时间。
最早从自制的二甲基二氯硅烷出发制得硅橡胶样品,向国庆10周年献礼的是沈阳化工研究院杨大海等。中国科学院化学研究所林一、江英彦研究员等也很早就开展甲基硅橡胶的研制。进入20世纪60年代,开发硅橡胶的单位就更多了。
自从搅拌床直接法合成甲基氯硅烷成功后才初步具备合成硅生胶所需原料的条件。由于硅橡胶的需求很紧迫,所以国内在上海地区和北方地区都有单位着手研发,如上海地区的上海化工研究院研究甲基氯硅烷单体的合成和硅橡胶的探索试验,上海信诚化工厂、上海树脂厂则从生产的角度考虑硅橡胶的合成。
在北方,我国第一个化工基地吉化公司,其研究院是以研发合成橡胶为主业的单位。后来该研究院增加以朱宝英为首的硅橡胶研发工作。在吉化公司内部还有设计院、生产厂,有较好的开发从甲基氯硅烷单体开始到合成硅橡胶的全套工艺的一条龙协作条件。
1958年沈阳化工研究院的有机硅部分搬迁到新成立的北京化工研究院后,60年代初沈阳化工研究院又成立了以张尔慈、叶青萱为主任的有机硅研究室,开发有机硅单体和硅橡胶。根据化工部二局的意见,沈阳化工研究院参与吉化公司研究院的硅橡胶开发。由于硅橡胶的合成还需要乙烯基环体等,所以沈阳化工研究院为之合成过甲基氢二氯硅烷等多种配套所需的有机硅单体。
第二节 上海地区首先用“迂回战术”批量生产出硅橡胶
1960年上海市化工局塑料公司下达给信诚化工厂一项研制军工急需硅橡胶的任务,因该厂有生产有机硅原料的农药副产物氯甲烷,有条件合成硅橡胶的原料甲基氯硅烷。信诚化工厂是一个公私合营小厂,只有郑善忠、徐明珊两位工程技术人员。他们认定硅橡胶研究项目的关键技术问题有两项,一是二甲基二氯硅烷的提纯,二是聚合工艺的研究和催化剂的选择。当时国外有机硅单体和中间体对我国禁运和封锁,国内搅拌床合成甲基氯硅烷单体中二甲基二氯硅烷含量低,高效的精馏技术尚未实施,无法获取大量高纯度的二甲基二氯硅烷单体作为硅橡胶原料。他们只能用当时能获得的纯度不很高的二甲基二氯硅烷先行乙醇醇解,生成乙氧基衍生物。其中含有的一甲基三氯硅烷醇解后生成的一甲基三乙氧基硅烷的沸点(151℃)与生成的二甲基二乙氧基硅烷沸点(111℃)相差比较大,沸点差有40℃之多,容易分离,故能得到纯度很高的二甲基二乙氧基硅烷。然后将二甲基二乙氧基硅烷水解转化成八甲基环四硅氧烷(甲基D4)。再经分馏,制取高纯度的D4,解决了硅橡胶原料问题。他们将通过醇解的间接手段获得D4的方法称为“迂回战术”。
在我国研发硅橡胶的初期,对西方国家的硅橡胶合成工艺缺乏了解,有的单位曾试用过比较原始的开环催化剂诸如硫酸、三氯化铁、硫酸铝等。然后再将数十万分子量硅生胶中所含的残余催化剂在双辊筒上用蒸馏水将催化剂洗净,所以使用这种开环催化剂是很不可取的工艺。
郑善忠、徐明珊两位了解到独特性质的暂时性催化剂,认为有它的合理性和先进性,不但可以提高硅橡胶的质量,而且可以大大简化后处理工作,当时国外尚未用于工业化生产。他们决定自行合成四甲基氢氧化铵及四丁基氢氧化,并进行了对比,认为前者较为满意,这样聚合的工艺路线也就得到了肯定。接着,经过自行设计、制造中试设备,试生产了透明清晰的硅橡胶数百公斤。1961年6月化工部二局杨光启处长到厂检查工作,看到了质量合格的硅橡胶产品时,很是高兴。虽然这种方法生产的胶价格较高,但是能批量生产的硅橡胶缓解了当时燃眉之急。
上海市化工局领导的上海树脂厂在中国首先建起了400mm直径的搅拌床生产甲基氯硅烷单体,是当时唯一能批量提供甲基氯硅烷单体的企业。后上海化工局为了加速上海有机硅工业的发展,调整有机硅力量将信诚化工厂与上海树脂厂合并,继续开展高温硫化硅橡胶连续合成工艺装置等的试验。
上海市化工局在壮大后的上海树脂厂建立专门的硅油、硅橡胶生产车间。上海树脂厂先后试制成功了国外禁运的高真空扩散泵油、双组分室温硫化硅橡胶、苯基甲基硅油等,使上海树脂厂成为国内能生产很多类型有机硅产品的、比较全能的工厂。虽然在1992年因上海市工业布局的调整,上海树脂厂不得不退出甲基氯硅烷等单体的生产,改为购入单体和中间体生产下游产品,但上海树脂厂在中国有机硅单体及有机硅高分子材料发展的历史上有着不可磨灭的贡献。
第三节 吉化公司为开发硅橡胶做了大量工作
20世纪60年代初,化工部给吉化公司下达了硅橡胶的研发任务后,吉化公司以该公司电石厂实验室为基础,由朱宝英组建了“361”小组,根据当时军工口对产品的需求和有机硅发展的需要开始了有机硅单体和高温硫化硅橡胶的研发。
为了试制硅橡胶首先要建立一定规模的甲基氯硅烷单体合成装置,再就是将获得的甲基氯硅烷精馏得到高纯度二甲基二氯硅烷,之后再进行水解,水解物裂解制取高纯度的D4,再将D4聚合成胶。吉化公司研究院1962~1967年重点解决以下问题:二甲基二氯硅烷单体连续水解、水解物连续裂解和D4的连续聚合中间试验。
吉化公司研究院建立了连续水解、连续裂解、连续聚合的30吨/年高温胶(现称热硫化硅橡胶)中试装置,并组织了大批技术人员,由朱宝英、谢巧华、徐一冰负责,技术人员有吕绍良、阎世城、周玉琛、姜景勋等。另外还有三位分配到地处四川的晨光二厂的1965年大学毕业生王伟良、冯锡澄、邱瑞芝,因晨光二厂尚未完全建成,他们暂时在吉化研究院有机硅课题组实习,也短期参加了这些工作。
当时为30吨/年高温胶所采用的水解、裂解工艺不在此细说了,要说的第一点是吉化公司研究院按化工部的要求开始有机硅的研发,重点是高温胶聚合小试和高温胶聚合用的暂时性催化剂。吉化公司研究院探索的暂时性催化剂有两种:四甲基氢氧化铵和四丁基氢氧化。1963年确定了工业用的高温胶聚合催化剂为四甲基氢氧化铵。
第二点要说的是十分关键的连续聚合工艺。吉化公司研究院吕绍良、阎世城、姜景勋等于1963年开始在上海树脂厂工艺的基础上开发该工艺:用暂时性催化剂四甲基氢氧化铵作开环聚合的催化剂;用两个脱水釜切换脱掉D4环体中的水和加入催化剂,脱完水、加好催化剂的环体,经齿轮泵定量加入到在慢速间断带式搅拌器的立式聚合釜中正压连续聚合,密封壳内装双滚筒炼胶机,真空脱低分子同时分解催化剂,下接真空接料罐,罐满,间歇常压出料。此工艺1964年4月通过化工部鉴定。
1965年吉化公司研究院成功地开发出间歇脱水连续聚合、连续脱低分子的连续法工艺,规模为年产生胶5t,使中国的硅生胶的合成工艺有了质的飞跃。
上述中试装置中的连续脱低分子和出胶,在工艺上,还不是太理想。1967年吉化公司研究院采用利用闪蒸的原理来脱除低分子的装置。成功将脱低分子器和出胶改为筛孔式空腔,真空分解催化剂和脱低分子。出胶改为变螺距的螺旋挤出机,连续地将生胶由真空挤至常压出胶。对新的脱低分子器和螺旋连续出胶机有贡献的是岳进、姜景勋和王世斗。
吉化公司研究院开发的连续水解、连续裂解、连续聚合的工艺在当时是相当先进和完善的。吉化公司研究院早期的有机硅橡胶的全套工艺工程开发,为多个厂家所借鉴,应该说吉化公司研究院为中国的有机硅橡胶的发展有很大贡献。
上海树脂厂在该厂小试的基础上,学习了吉化公司的经验,于1966年建了一套中试装置,也是类似的连续法,用四甲基氢氧化铵为催化剂,用一对真空室内的辊筒来分解催化剂并脱除低分子量聚合物,规模为年产5t生胶。
1966年晨光二厂由上海医药工业研究院设计,仿照吉化公司研究院的技术,建了一条年产10t的生胶生产线,这在当时是产能最大的生产装置。
第四节 甲基乙烯基硅橡胶攻关成功
由于纯二甲基硅橡胶没有活性交联点,分子间的交联是借助过氧化物氧化掉硅氧分子主链上与硅原子相连接的部分甲基进行的。硫化温度高,硫化后的制品压缩永久变形差,不受用户欢迎。
1963年根据化工部一局陶涛副局长的安排,中国要开发出带活性乙烯基的甲基乙烯基硅橡胶。随即组成了以吉化公司研究院朱宝英、谢巧华等和沈阳化工研究院有机硅研究室叶青萱、韩振山等组成的第一协作组和上海树脂厂章基凯、张慧珍等与中科院化学所孙纯中等组成的第二协作组分别进行攻关,攻关目的是要获得带乙烯基的中间体。第一协作组是用热缩法合成甲基乙烯基二氯硅烷,第二协作组是用钠缩合法合成甲基乙烯基二乙氧基硅烷。两个协作组各自取得突破后,分别通过化工部和上海市化工局的技术鉴定。
在热缩法合成甲基乙烯基二氯硅烷和甲基苯基二氯硅烷试制成功鉴定后,吉化公司研究院的30吨/年装置就发展成了甲基乙烯基硅橡胶、甲基苯基硅橡胶和甲基乙烯基苯基硅橡胶的连续水解、裂解、聚合装置。后来,吉化公司研究院姜景勋等设计了年产100t硅橡胶连续化工艺流程,被北京化工二厂及蚌埠有机硅化工厂等多个工厂所采用。
20世纪70年代中期,晨光二分厂曾派人到吉化公司研究院学习他们开发的闪蒸原理来脱低分子的装置,及单螺杆连续出料等装置。在学习吉化公司研究院技术的基础上,晨光二分厂自行设计了一套年产50t生胶的装置,并通过不断的改进,很快将生产能力提高到150吨/年。
第五节 提高有机硅生胶生产效率的静态混合技术
1990年,深圳新能源公司和江苏扬中塑性材料厂购买了晨光化工研究院(以下简称晨光院)的有机硅生胶的生产技术,各建了一套150吨/年的装置。由于市场对硅橡胶的需要量激增,两家都立刻要求扩大生产能力。考虑到现有装置的局限性,简单放大设备尺寸并不能明显提高产能。1991年晨光院的王伟良决定把一种化工新技术——静态混合技术引入到生胶的聚合装置中,并在扬中塑性材料厂进行了技术改造,在简单地把原有的熟化筒换成一节静态混合器后,扬中厂装置的产能立刻从150吨/年增加到300吨/年。
此后,简单的静态混合器被不断改进成不同水力直径、不同筒径的静态混合器组。单套装置的生产能力也从单一的300吨/年发展成500吨/年、1000吨/年、1500吨/年、3000吨/年系列。静态混合器组在硅橡胶生胶中的应用也申请了专利,并获得了授权,专利号为CN1154974。
在静态混合器组不断被改进的同时,王伟良也在不断地改进脱低分子器的结构与生胶排出装置的结构,甚至真空泵的结构。他们在脱低分子器中的列管内加装了自己发明的一种静态混合器,使脱低分子器的传热效果得到提高,并且基本上防止了以前在操作不当时常会发生的贯通现象。中国台湾的同行用了以后非常赞赏。生胶排出装置的改进导致了一种新型结构的单螺杆——逆向单螺杆的发明,并取得了专利权,专利号为CN2347744。
真空泵的改进导致了一种新结构的真空泵——双级单作用往复式真空泵的诞生,这种真空泵不仅适用性广,而且真空度较高,满足了硅橡胶生产工艺的要求。
为减少中间成分,中国的技术人员在国内外前人工作的基础上,将原来的间歇生产工艺进行了改进,创造了一种新的间歇聚合生产工艺,即在第一个反应釜里间歇脱水,在第二个反应釜里间歇聚合,然后采用连续法的脱低分子设备和排料设备进行脱低分子和出料。两个聚合釜轮换聚合或排料,也就是说,前面的聚合是间歇的,后面的脱低分子是连续的。这种间歇的聚合与国外的间歇聚合略有不同,后者的搅拌是全过程的,因此需要功率极大、动辄几百马力的电机,而国内的间歇聚合只进行半程的搅拌,到高聚物快形成时就停止搅拌了,然后在静止的状态下使聚合过程逐渐达到平衡。这种方法的优点是节约了动力,降低了对设备的要求,但因为聚合釜中心与近壁处的温度差异,所得聚合物的分子量分布较宽。目前,经王伟良的改进,间歇法分子量分布较宽的缺点已经彻底消失了。近年来新建的生产线都已经采用了间歇法工艺,规模已达到单套装置产能4000吨/年。间歇聚合的操作弹性大,因此比较适合使用聚合活性略差的环体,很快在国内得到了发展。
1990年,中国的硅橡胶生胶产能约为600吨/年,由于新的生胶制造技术的开发,以及市场需求的推动,中国的硅橡胶生产线如雨后春笋般地建立起来了,到2002年生胶产能已达到6万吨/年,并且仍在不断地增加之中。
第六节 向国内外转让硅橡胶生胶合成技术
晨光化工研究院的硅生胶生产技术备受各大公司的注意。先后曾有韩国的一友、海龙、KCC(高丽金刚),波兰国家工业研究院,台湾厚生公司,香港坚成控股公司等向晨光化工研究院购买生胶(及混炼胶)合成技术。
晨光院的静态混合器生胶技术在这20多年中进行了12次技术转让,见表4-1。
表4-1 静态混合器生胶技术受让单位

美国道康宁公司也曾决定向晨光化工研究院购买生胶制造技术,最后由于价格原因使交易没有成功。
总之,中国的热硫化硅橡胶工业性合成从吉化公司研究院间歇脱水连续聚合、连续脱低分子的连续法工艺开始,到晨光化工研究院的静态混合器成功应用,再到间歇聚合工艺的改进,在十几年中取得了巨大的进步。生胶生产技术达到了世界先进水平,引起了业界的注意。为此,中国政府于2001年授予连续法硅橡胶生胶生产技术的发明人王伟良国家科技进步二等奖。以上情况足以说明我国在热硫化甲基乙烯基硅橡胶的生产工艺和产品质量上并不逊于跨国公司。
第七节 碱热裂解工艺
在试制硅橡胶时,特别在初期,由于很多企业精馏二甲基二氯硅烷的效率不是十分高,所以一直存在八甲基环四硅氧烷的纯度不够高的问题。由于其中含有微量的三官能杂质会使生胶发生交联,从而影响到八甲基环四硅氧烷的纯度和硅生胶的质量,此问题曾较长时间困扰生胶的合成。20世纪60年代初笔者向国内同行介绍了所知道的国外采取的碱热解措施后,各单位都在流程中加入此操作,困扰很久的硅橡胶合成中的瓶颈得以解决。如果单体精馏能保证所得的二甲基二氯硅烷达到一定纯度,此工艺是可以省略的。