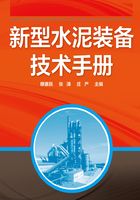
第二节 圆锥式破碎机
一、概述
圆锥破碎机是目前应用最为广泛的硬物料中碎、细碎的一种典型装备,尤其是在产量要求大的矿山、建材、水利等行业,应用十分广泛。圆锥破碎机是利用正立和倒立的两个圆锥之间的间隙进行物料破碎。由于整个运行过程中,其破碎力是脉动的,并且在破碎中有时还混有不可破碎物,如铁块等,故圆锥破碎机必须设计有保险装置,以供排除不可破碎物,起到保护机器的作用。而根据保险装置性质的不同,可分为装有机械弹簧装置和液压弹簧装置(即保险缸装置)两种。长期以来液压圆锥发展缓慢,随着计算机技术和自动化控制技术的迅猛发展,以及液压技术的更新发展,从20世纪80年代末期开始,液压圆锥破碎机发展也加快了速度,世界各国都竞相研制了相关产品。目前,液压圆锥破碎机根据排料口调整方式不同和主轴安装方式的不同,可分为主轴固定式和主轴活动式两类。主轴固定式液压圆锥破碎机是通过定锥螺旋旋动而致使定锥轧臼壁上下移动来调整排料口,其主轴短而粗,固定地插在机架中,其承载能力大。主轴活动式的排料调整有两种方式:一种是主轴上下浮动来调整破碎圆锥部,使破碎壁上下移动,从而调整排料口,这种形式的破碎机被称为单缸液压圆锥破碎机;另一种也是通过定锥螺旋旋动而致使定锥轧臼壁上下移动来调整排料口,其主轴是插在偏心套衬套中,即主轴活动的多缸液压圆锥破碎机。
目前圆锥破碎机由于其操作简单、运行成本低、维修率低,故受到广大用户的欢迎,尤其近几年来,其需要量日益增加,市场不断扩大。据不完全统计,目前能制造圆锥的厂家已达十几家,在销量不断增加的同时,其产品性能和质量也在不断得到改进和提高。
圆锥破碎机今后必定是向着高能、多腔型、大型化发展,在设计中,贯彻如下思想:
(1)采用高能化设计原则,即较高的输入功率/体积(质量)比,即在相同体积或质量下输入功率和处理能力大幅度提高。
(2)在腔型设计中尽可能采用层压破碎和恒定腔型,特别是细碎领域,使处理能力和给料粒度受到的影响减到最小。
(3)采用计算机控制和现代液压技术。
(4)运用虚拟设计,模块化设计,一台装备由基本模块加特定模块组成,针对特定用户,采用特定腔型的菜单式选择和供货,使其性能最优,目前大型先进的圆锥破碎机对我国来说还是一个空白,尤其在装备的运动和动力学分析还停留在定性分析上,在虚拟样机及优化设计仅停留在感性认识上,阻碍了其发展,今后要在这方面深入做一些研究,生产厂家可互相组成研究团体,或与科研机构、高等院校联合,研究攻关,使我国在圆锥设计和制造水平上有一个飞跃,并逐步占据世界领先地位。
一台先进的圆锥与自动控制系统相配合,采用自动控制系统,其排料口调整速度快,精度高,排料口控制误差甚至可达0.1mm,且随着给料粒度、含水量和功能指数等参数的变化,系统能很快将排料口调整到最佳位置,且由于自动控制系统的发展,甚至可用自动控制系统而不是筛分来保证最终产品粒度的要求。
二、主要零部件材料要求
主要零部件材料的力学性能,应不低于表2-2-1所列材料的规定。
表2-2-1 主要零部件材料的力学性能

三、装配及安装要求
(1)传动轴的轴向游动间隙为0.8~1.6mm。
(2)碗型轴承架装配后,其下端与偏心套上端面的间隙应符合表2-2-2的规定。
表2-2-2 碗型轴承架装配后下端与偏心套上端面间隙

(3)圆形齿轮大端的啮合间隙及顶隙,应符合标2-2-3的规定。
表2-2-3 圆形齿轮大端啮合间隙及顶隙

(4)装配后,当排料口调至最小时,动锥与定锥在整个圆周的排料间隙偏差不大于排料口的25%。
(5)装配后,应在制造厂用相同转速的电机和性能相似的润滑站连续进行2h空负荷试车。
(6)空负荷试车时,动锥的自转转速不应大于15r/min。
(7)空负荷试车的供油压力应在0.06~0.10MPa范围内,其回油的油温最高不得超过50℃。
(8)应有保护装置,当非破碎物混入破碎腔内时,产品的主要零部件不被损坏。
四、安装及调试工艺
圆锥破碎机是一种结构较为复杂的破碎机,故必须要正确使用,才能保证机器的正常运转,否则即使有了制造精良、配套合理的机器,如安装不好或者使用不当,都不能保证安全高效地运行,甚至会损坏机器,造成不应有的经济损失。
(一)圆锥破碎机机构设计功能调试应注意的事项
圆锥破碎机的设计涉及很多知识,但有几个要点是共同要注意的。
1.破碎力的计算
(1)单缸液压圆锥破碎机的破碎力计算。在设计中,应注意的是把旋转部件的转动惯量尽量减小,以免在其过铁时损坏机件,一般而言,正常的破碎力F作用在B处,也就是整个破碎腔的2/3长处,破碎力的作用点距A点的距离(见图2-2-1)。

图2-2-1 破碎受力
L=b+0.66(d-b)
破碎力F可分解成垂直分力
Fy=Fsinα
和水平分力
Fx=Fcosα
垂直分力Fy与动锥自重G、液压缸的油压力P平衡,水平分力由主轴上下轴承的支持力Fi与Ft平衡。
由于液压缸的油压液压缸活塞直径可知,故也就能方便地求出正常破碎力F值,而最大破碎力是正常破碎力的3~7倍,以此为依据可计算主轴的强度、机架的强度。
(2)弹簧圆锥破碎机破碎力的计算(见图2-2-2)

图2-2-2 弹簧圆锥破碎机破碎示意图
式中 Lp——F对A点力臂,m(A为弹簧支点);
LF——摩擦力f对A点力臂,m;
np——弹簧预紧力,N;
G——动锥自重,kg;
R——np对A点力臂,m;
f——摩擦系数f=0.25~0.35。
F的作用点,在平行区始点。
2.偏心度γ0与偏心距e的确定
当偏心距一定时,若γ0值小,则破碎腔上部行程有较大值,这有利于提高处理量,有利于降低产品粒度,但球面半径R值增大,球面磨损较重;若γ0值大,则破碎腔上部行程有较小值,由此球面半径R值减小,球面磨损相对较轻。而偏心距e值是决定冲程S值大小的关键,由于要采用层压破碎,其S值必然要比传统的破碎机大,但又必须和动锥的冲击次数相匹配,才能实现层压破碎,经综合考虑,认为γ0值取小一些为宜,一般均为0.7°~1.5°,而球面半径R值一般以(0.45~0.6)H为宜。
3.破碎腔的设计
破碎腔的形状对物料的破碎过程起着决定性的作用,如果用于二段破碎,其啮角α可选用大值,因啮角的增大对降低机器高度,减轻装备重量,降低机器成本有很大影响,对于中、细碎破碎啮角一般均在22°之内。一般二段破碎,采用直线形腔型能满足破碎腔剖面变化的要求,而中、细碎破碎一般采用曲线形腔型,它允许有较窄的排料口,采用曲线形腔型的优点是,功耗相对小,且产品粒度较为均匀,处理量也高且不易堵塞。破碎腔实际设计时,可采用理想破碎过程的方法,把整个破碎腔高度分为n等份,从入料口至排料口依次编号1到n,1为入料口,n为排料口,这样可知道各截面体积向排料口方向是逐渐减小的,如果破碎时不存在间隙,则物料下落就会停止而造成堵塞,为了避免堵塞,每两个相邻环状体应采取一定的渐缩比例,而此比例与偏心距、物料间间隙等有关,一般而言环状体积的渐缩比为1:1.5左右。
4.动载荷的计算
单缸液压圆锥破碎机是靠偏心挤压为主的破碎方法,其质心不在其回转中心线上,加上物料不均等原因,运转中必然会产生惯性力及惯性力矩,这种力作用在机架上,则为一种周期性的动载荷,引起机架振动和偏心套偏斜,其力和力矩方向呈周期性变化,其振动形式为水平振动、垂直振动和摆动,且由于破碎锥沿料层滚压时伴有强制冲击和振动,又对破碎机产生了附加振动,但总的来说,是以水平圆振动为其主要振动,在空载时,有明显的简谐运动规律,但在重载时,特别在破碎大物料时,由于动锥在瞬间转速降低,这时伴有很大的冲击分量,故在负荷运行时的动载荷和空载时的动载荷是不相同的,但常规分析时还是以空载动载荷值为分析依据,其水平动载荷计算公式为:
P1=m1e1w2sinwt
P2=m2e2w2sinwt
P=P1-P2=(m1e1-m2e2)w2sinwt
式中 P1——动锥和偏心套引起的惯性力,kg;
P2——配重引起的惯性力,kg;
P——破碎机在X方向水平动载荷,N;
m1——动锥和偏心套质量,kg;
m2——配重质量,kg;
e1——破碎机中心线到动锥与偏心套质心的距离,m;
e2——破碎机中心线到配重质心的距离,m;
w——偏心套圆频率。
5.润滑油站的计算
单缸液压圆锥破碎机采用压力循环润滑方式进行润滑,但一般油站的冷却方式采用水冷,需要大量水资源,考虑到许多地区缺水也可采用最先进的电制冷方式,其发热量计算如下:
Q=fPu/ΣF
式中 Q——摩擦副单位面积在单位时间内的发热量,J;
P——摩擦副之间压力,N;
u——摩擦副之间的相对滑动速度,m/s;
ΣF——摩擦副之间的接触面积,m2;
f——由润滑状态确定的滑动摩擦系数。
从上述公式可看出,摩擦副的发热量与上述4个因素有关,即载荷轻重、转速高低、接触面积大小、油压力及流量,现分别讨论如下:
(1)载荷轻重。圆锥破碎机工作时,破碎物料的挤压力通过零部件传递到各滑动摩擦副之间,形成压力P,载荷大就意味着压力大,当转速和润滑状态一定时,摩擦副生成热量与载荷成正比关系增加,其发热量的增加将引起摩擦副的表面温度升高,对润滑产生威胁。
(2)转速高低。圆锥破碎机工作时,转速高,与之对应的球面滑动相对速度高,这时在其他条件不变时,摩擦副生成热量会与转速成正比关系增加,由此过高的热量将影响润滑效果。
(3)接触面积大小。摩擦副的接触面积增大,则单位面积上产生热量相对减少,所以摩擦面如有高点,其接触面积大大减小,依然会引起高温,使局部润滑严重恶化,故必须要消灭高点,使之接触面积尽可能大。
(4)压力及流量。润滑作用是在摩擦副表面形成一层油膜,变干摩擦为半干摩擦或液体摩擦,减小滑动摩擦系数,减少发热和磨损,压力循环润滑时,还表现在循环油流能将生成热量带走,不致由于高温致使润滑液黏度降低,使润滑油膜变薄而导致干摩擦或边界摩擦,且油流经摩擦到表面还能带走磨料,因而兼有清洗作用,经过这样分析,再经计算确定,采用内啮合齿轮泵,以减小油站噪声,进油压力视不同种圆锥而不同,润滑油品采用150号齿轮油,冷却方式采用电制冷,电控采用PLC控制。
6.排料曲线的确定
一般用户在选用破碎机时,必定要看排料曲线图,以得出此破碎机是否适合需要,故理论排料曲线的绘制十分重要,我们分析了物料在破碎腔内遭到破碎的物理过程,即破碎发生在动锥和定锥之间,当动锥离开定锥,物料下落,下落到一定距离,动锥向定锥又靠近,物料受到挤压和冲击作用而被破碎,这样经若干次循环后,物料被破碎至要求粒度排出。为了绘制排料曲线,必须先建立数学模型。
任何一个粒度减少过程,都可以用一个矩阵表示,设加入到圆锥破碎机内物料给料粒度分布为:
fn表示第n个粒度区间物料占总物料量的分数。其粒度区间的划分可根据工艺要求,分成若干个。
当动锥向定锥作一次摆动后,破碎腔内物料受到动锥一次挤压,在这一过程中,不同大小物料得到破碎的概率,即破碎的选择性不同,也可用一个函数表示:
此函数为一个对角矩阵,是一个选择函数。
其中Sn表示n粒级物料在破碎腔内得到粉碎的概率,下脚标表示物料所在粒级,其粒度区间划分可根据工艺要求分成若干个,经过一次破碎,已经得到了被破碎的物料,这时,物料粒度组成发生了变化,变化后的物料粒度分布可用一个新的函数表示:
这是一个下三角矩阵,也就是破碎函数。
双下脚标意义:第1个下脚标为物料所在粒度区间,第二个下脚标为该物料原来所在粒度区间,其元素表示该粒级物料占总物料量的分数,如b21表示经过一次粉碎后由第1粒度区间进入到第2粒度区间物料的分数,而b22则表示经一次粉碎后第2区间物料仍留在该区间的物料分数。
这样经一次粉碎后,已经破碎的物料向用户要求的粉碎产品贡献量为BSF,经一次粉碎后,未得到破碎的物料向产品的贡献量为(I-S)F,其中I为单位矩阵,则经一次粉碎后产品的粒度组成为:
P1=[BS+(I-S)]F
这是物料在经一次破碎后在第一破碎区域内破碎的产品粒度分布,该粒度分布也是进入到第二破碎区域的物料粒度分布,由于破碎函数与选择函数与物料性质和装备有关,同一物料在同一装备破碎其值基本不变,这两个函数值可由实验确定。
由此推理出经过第二破碎区域破碎后的物料粒度分布为:
P2=[BS+(I-S)]P1=[BS+(I-S)]2F
类似经n次破碎后,产品粒度组成为:
Pn=[BS+(I-S)]nF
这个公式就是理论上的排料粒度分布。
经过如此推导,把进料粒度划分成几个粒级区域,定出破碎函数和选择函数值,后可确定产品粒度分布。
7.弧齿锥齿轮的采用及其调整计算
弧齿锥齿轮的齿线是一段圆弧,故承载能力高,运转平稳,噪声也低,且由于齿面呈局部接触,故装配误差对偏载能力影响不大,由于重合度大,故强度大大增高,模数相对可取的小一些,这样,相应件尺寸也可减小,有利于整机重量的减轻,但由于弧齿锥齿轮齿轮副侧隙,对齿轮传动的平稳性、冲击、振动都有很大的影响,因此其侧隙调整很重要,间隙大,会产生噪声、振动,间隙太小,会加剧轮齿磨损,可能出现齿轮咬死,甚至断齿,为此,其间隙必须调整合适,我们采用调整垫片,即通过改变齿轮的轴向位移来改变侧隙,实际上是采用厚薄不一的调整垫片来调整,但调整垫片究竟取多厚,或者放置的调整垫片,经测量齿侧隙不合适,要修磨多少,无现成公式可查,于是我们进行了推导和计算,现就图2-2-3~图2-2-5做推导说明:

图2-2-3 调整垫片位置图

图2-2-4 轴向位移和分解

图2-2-5 法向位移分解
假定一个锥齿轮不动,当一个锥齿轮作轴向位移(图2-2-3),齿宽中点从A移到A1(图2-2-4、图2-2-5),则该点处法向位移Sn和切向位移St为:
切向分量直接影响断面高度变化,而法向位移Sn可再次分解为接触区域法向分量Sa和切向分量Sf
Sa=Snsinα
而齿轮副侧隙根据定义就是工作面接触时非工作面间的最小距离,这最小距离方向就是压力角α的方向,因此位移Sa就是侧隙变化量。
这样对于大小锥齿轮,位移引起的侧隙变化量就分别为:
一般调整垫片放在大锥齿轮下方,故在小锥齿轮位置不变,只要调整大锥齿轮即可,另外齿轮的切向位移St也会影响端面高度的变化,但一般可以不计。
这是因为一般弧齿锥齿轮多用于两轴互相垂直的场合,其侧隙变化量以大锥齿轮调整为主。
故可用下列公式计算:
Sa1=S1sinδ1sinα
S1=Sa1/sinδ1sinα
具体方法为测得齿轮副法向侧隙Sn后,与标准值比较,其差值为Sa1,代入上式计算即可。
8.几种单缸液压圆锥破碎机性能比较(见表2-2-4)
表2-2-4 几种单缸液压圆锥破碎机性能比较

从上表中可看出,破碎单位质量物料时的装备质量类似,而按GB/T 26965圆锥破碎机的能耗指标,以排放口为20mm计时,CPYQ-1216能耗为1.0,GP-300为1.198,CH440-M为1.338,AF45为0.846。在小于20mm粒度下能耗,CPYQ-1216为1.428,GP-300为1.71,CH440-M为1.761,AF45为1.571。
由此看来,在能耗上CPYQ-1216为最优,按上述计算结果,如按普通型单缸液压圆锥破碎机计,CPYQ-1216、AF45能耗为1级,而GP-300(MF)与CH440-M能耗为2级。按强力圆锥破计,CPYQ-1216、AF45能耗为2级,而GP-300(MF)与CH440-M能耗为3级。当然这是一个理论比较,是有欠缺的,实际上要以实测平均功率为依据。
(二)安装
在大多数情况下,提供的基础图给出了破碎机的安装数据,但是该基础图不可作为基础施工图,仅可作为用户设计基础施工图的主要参考资料,一个具有相当大小而又经久耐用的坚固基础,对于破碎机成功运转是极其重要的,破碎机空间尺寸是基础结构主要考虑的问题之一,在破碎机上方,要留有足够的空间,以便拆卸主轴和调整套部。在基础的一侧,应留有足够的空间,以便拆卸传动轴部,同时亦应考虑给料装置等所需空间。另外排料室、排料运输机等也应考虑留有足够的空间。
(1)装备基础的位置、几何尺寸和质量要求,应符合相应国家标准。
(2)装备基础表面和地脚螺栓预留孔中油污、碎石、泥土、积水等均应清除干净,预埋地脚螺栓的螺纹和螺母应保护完好,放置垫铁的表面应凿平。
(3)装备找平、找正,调平测量位置。当无规定时,在装备主要工作面或加工精度较高的表面取其安装水平不应大于0.20/1000。
(4)传动轴采用滑动轴承时,传动轴轴向游隙宜为0.2~1.6mm。
(5)圆锥齿轮的啮合间隙应符合相关标准规定。
(6)装配给料槽时,其方向和位置应使物料先落在给料箱内,不应使其直落入破碎机内。
(7)液压系统管路应进行严密性试验,实验压力应缓慢升高至工作压力的1.4倍,保压10min,再降至工作压力进行检査,不得有渗漏现象。
(8)在圆锥破碎机运转过程中,润滑的作用是第一位的。机器安装就位后应立即着手润滑管路的安装。润滑管路的安装主要是保证管路连接正确。为此,应先确认进油口和回油口:一般在机器底部和传动轴架侧各有一个进油口,回油口在传动轴架下的主机架侧。回油管的安装要确保倾斜度,一般要求不小于1:12,因为机器回油是靠自流,倾斜度不够,回油不畅,容易诱发机器漏油和回油温度增加。
润滑油的黏度:使用国标L-CKC一等品,弹簧圆锥破碎机用100#,多缸液压圆锥破碎机用150#闭式工业齿轮油。千万注意用正品油,如壳牌、海牌、长城牌等。
(9)液压系统各管路连接一定要对口。因为保险、锁紧、调整各自要求的液压力不同,联锁要求也不同。
液压系统充压前要先将蓄能器充好氮气。注意:只能是氮气,因为氮气不会造成蓄能器橡胶囊氧化而降低蓄能器胶囊使用寿命。高性能多缸液压圆锥破碎机蓄能器充气压力一般为9.5~10MPa。
各管路连接无误后可进行系统充压试验:充压前先将保险锁紧,调整各胶管最高接头松开1~1.5扣,充油时,松开的接头处首先会向外排出管路中的空气,待该处流出清澈的液压油时再拧紧该处接头。液压系统中混入大量空气,将导致液压系统无法正常工作。液压系统中混入大量空气后,最常见的现象是液压系统打不上压。液压系统中残留少量空气,经数次充压和向液压油箱排油可逐渐排出。
(10)润滑站与主机
①油温低于16℃,主机不能启动;
②油温低于21℃,不能给负荷;
③油温低于27℃,润滑站加热器自动投入工作;
④油温高于27℃,润滑站加热器自动停止工作;
⑤油温高于46℃,润滑站冷却器自动投入工作;
⑥油温低于38℃,润滑站冷却器自动停止工作;
⑦油温高于54℃,报警;
⑧油温高于60℃,切断主电机电源,停止主机运转。
(11)液压站与主机
①液压力低于最低限值时,破碎机主电动机不能得电。
②液压站处于自动工作状态时,液压力低于最低限值时,液压泵自动启动往系统补压;
③液压力高于上限值时,液压泵自动停止供油。
④对高性能多缸液压圆锥破碎机来说,液压站处于自动工作状态时,上述要求可自动实现。
⑤带液压锁紧、液压调整装置时,锁紧缸处于锁紧状态时,液压调整系统不能得电,否则会导致支承套、调整套螺纹损伤,液压系统也可能因输出过大的液压力而损坏液压泵和液压阀。
(三)常见故障
1.弹簧圆锥破碎机(见表2-2-5)
表2-2-5 弹簧圆锥破碎机故障原因与说明/处理

2.单缸液压圆锥破碎机(见表2-2-6)
表2-2-6 单缸液压圆锥破碎机故障原因与说明/处理

3.多缸液压圆锥破碎机(见表2-2-7)
表2-2-7 多缸液压圆锥破碎机故障、原因与说明/处理

五、试运转
(一)启动前的检査如下
(1)检查排料口尺寸;
(2)检查皮带的张紧程度;
(3)检査传动轴的轴向游隙;
(4)检査是否有足够的卸料空间;
(5)检查润滑系统;
(6)检査液压系统。
(二)空负荷试车
按说明书试车前的检查表逐项检查破碎机安装情况,全部合格后才可进行下步试车程序。
1.弹簧圆锥破碎机空负荷试车应检査内容
破碎锥(或称动锥)每分钟自转速:<15r/min;
供油压力:0.05~0.1MPa,就是我们常说0.5~1个压(kgf/cm2);
供油压力过高将导致机器漏油和浮起偏心套引发烧套与飞车;
供油温度:≥27℃;
回油温度:进出油温升≤3℃,稳定在54℃以下。
主电动机电流空负荷试车时大约是额定电流的1/4,如1300弹簧圆锥破碎机的空负荷运转电流在60A左右,如果空负荷试车电流过高,要及时找出原因,排除故障。
2.多缸液压圆锥破碎机空负荷试车应检查内容
破碎锥(或称动锥)每分钟自转速:100~120r/min;这种破碎机由于自转速度高,躯体上衬套与碗形轴承架间相对运动速度很大,而这里的润滑条件又不好,因此破碎机不宜长时间空转。躯体上衬套只在空转时起阻止飞车的作用,负荷时与碗形轴承架间会有间隙,就不起作用了。
供油压力:0.14~0.22MPa,就是我们常说的1.4~2.2kgf/cm2;供油压力稍高影响不大;低了,供油不足容易引发烧套。
供油温度:≥27℃。
回油温度:进出油温升≤5℃,稳定在54℃以下。
主电动机电流空负荷试车时大约是额定电流的1/4(如1100多缸液压圆锥破碎机空负荷运转电流在110A左右),如果空负荷试车电流过高,要及时找出原因,排除故障。
(三)半负荷试车
空负荷试车合格后一定要进行半负荷试车跑合。半负荷试车的目的主要是为了跑合,就连最精密的机床、汽车都需要跑合,破碎机必须经过跑合。
跑合的时间:弹簧圆锥破碎机为72h;多缸液压圆锥破碎机由于偏心套旋转速度高,跑合时间应超过150h。
半负荷试车的控制:
(1)给料少,破碎机负荷较小。
(2)排矿口大对应的破碎机负荷较小。
(3)主电动机工作电流控制在50%~60%额定电流。
(4)液压破碎机还要关注液压力的情况,观察液压系统管路有无渗漏、降压情况发生。半负荷试车期间不能保证产量和变形。
半负荷试车期间要密切关注润滑油供油压力、回油温度,控制范围与空负荷试车相同;还应时刻关注主电动机工作电流,主电动机工作电流突然增大有可能是烧套造成,要及时停车,检査原因,排除故障后再开车。
(四)负荷试车
(1)主电动机工作电流控制在80%~85%额定电流以下。偶尔跳到额定电流以上也没有问题,但大部分时间须在80%~85%额定电流以下;如果主电动机工作电流突然增大且持续时间超过2min,有可能是给料过多,还可能是烧套造成,要及时减少给料或停车,检査原因,排除故障后再开车。
(2)负荷试车期间,必须密切注意润滑油供油压力、回油温度,控制范围与空负荷试车相同;回油温度超过46℃时一定要开冷却,低于38℃时一定要停冷却,润滑油最佳工作温度是38~46℃。
液压破碎机还要关注液压力的情况,观察液压系统管路有无渗漏、降压情况发生。