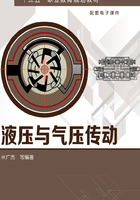
学习情境2 认识液压元件和基本回路
任务1 机床液压系统动力元件的认识
【任务目标】
1.掌握液压泵的结构组成、特点、工作原理,掌握常用液压元件的应用场合和选用原则方法。
2.掌握常用液压泵选用方法,了解常见的故障及维修方法。
【任务描述】
正确拆装机床液压系统典型齿轮泵、叶片泵,观察分析结构组成、特点,掌握液压泵工作原理,能合理选用。
【知识准备】
液压泵是液压系统的动力元件,它由原动机驱动,把输入的机械能转换成为油液的压力能,再以压力、流量的形式输入到系统中去,它是液压系统的动力源。
1.液压泵的工作原理和分类
(1)液压泵的工作原理 液压泵都是依靠密封容积变化的原理来进行工作的,图2-1-1所示的是一单柱塞液压泵的工作原理图,图中柱塞2装在缸体3中形成一个密封容积a,柱塞在弹簧4的作用下始终压紧在偏心轮1上。原动机驱动偏心轮1旋转使柱塞2作往复运动,使密封容积a的大小发生周期性的交替变化。当a由小变大时就形成部分真空,使油箱中油液在大气压作用下,经吸油管顶开单向阀6进入油腔a而实现吸油;反之,当a由大变小时,a腔中吸满的油液将顶开单向阀5流入系统而实现压油。这样液压泵就将原动机输入的机械能转换成液体的压力能,原动机驱动偏心轮不断旋转,液压泵就不断地吸油和压油。

图2-1-1 液压泵工作原理图
1—偏心轮;2—柱塞;3—缸体;4—弹簧;5,6—单向阀
(2)液压泵的特点
①具有若干个密封且又可以周期性变化的空间。液压泵输出流量与此空间的容积变化量和单位时间内的变化次数成正比,与其他因素无关。这是容积式液压泵的一个重要特性。
②油箱内液体的绝对压力必须恒等于或大于大气压力。这是容积式液压泵能够吸入油液的外部条件。因此,为保证液压泵正常吸油,油箱必须与大气相通,或采用密闭的充压油箱。
③具有相应的配流机构,将吸油腔和排油腔隔开,保证液压泵有规律地、连续地吸、排液体。液压泵的结构原理不同,其配油机构也不相同。如图2-1-1中的单向阀5、6就是配流机构。
(3)分类 液压泵按其结构形式不同可分为叶片泵、齿轮泵、柱塞泵、螺杆泵等;按其输出流量能否改变,又可分为定量泵和变量泵;按其工作压力不同还可分为低压泵、中压泵、中高压泵和高压泵等;按输出液流的方向,又有单向泵和双向泵之分。
液压泵的类型很多,其结构不同,但是它们的工作原理相同,都是依靠密闭容积的变化来工作的,因此都称为容积式液压泵。
常用的液压泵的图形符号如图2-1-2所示

图2-1-2 液压泵图形符号
2.液压泵的主要性能参数
(1)液压泵的压力
①工作压力p 液压泵工作时输出油液的实际压力称为工作压力p。其数值取决于负载的大小。
②额定压力pn 液压泵在正常工作条件下,按试验标准规定连续运转的最高压力称为液压泵的额定压力。
③最高允许压力pmax 在超过额定压力的条件下,根据试验标准规定,允许液压泵短暂运行的最高压力值,称为液压泵的最高允许压力。
p、pn、pmax的国际单位为N/m2、Pa,常用单位为MPa。
(2)液压泵的排量和流量
①排量V 在没有泄漏的情况下,液压泵每转一周,由其密封容积几何尺寸变化计算而得到的排出液体的体积叫液压泵的排量。
排量可调节的液压泵称为变量泵;排量为常数的液压泵则称为定量泵。
V的国际单位为m3/r,常用单位为mL/r。
②理论流量qt 理论流量是指在不考虑液压泵的泄漏流量的情况下,在单位时间内所排出的液体体积的平均值。显然,如果液压泵的排量为V,其主轴转速为n,则该液压泵的理论流量qt为
qt=Vn (2-1-1)
③实际流量q 液压泵在某一具体工况下,单位时间内所排出的液体体积称为实际流量,它等于理论流量qt减去泄漏流量Δq,即
q=qt-Δq (2-1-2)
④额定流量qn 液压泵在正常工作条件下,按试验标准规定(如在额定压力和额定转速n下)必须保证的流量。
qt、q、qn的国际单位为m3/s,常用单位为L/min。
n的国际单位为r/s,常用单位为r/min。
(3)液压泵的功率P
①液压功率与压力及流量的关系 功率是指单位时间内所做的功,在液压缸系统中,忽略其他能量损失,当进油腔的压力为p,流量为q,活塞的面积为A,则液体作用在活塞上的推力F=pA,活塞的移动速度v=q/A,所以液压功率为
由上式可见,液压功率P等于液体压力p与液体流量q的乘积。
②泵的输入功率Pi 原动机(如电动机等)对泵的输出功率即为泵的输入功率,它表现为原动机输出转矩T与泵输入轴转速ω(ω=2πn)的乘积。即
Pi=2πnT (2-1-4)
③泵的输出功率PoPo为泵实际输出液体的压力p与实际输出流量q的乘积。即
Po=pq (2-1-5)
Pi、Po的国际单位为W,常用单位为kW。
T的国际单位为N·m。
(4)液压泵的效率η
①液压泵的容积效率ηV ηV为泵的实际流量q与理论流量qt之比。即
②液压泵的机械效率ηm 由于泵在工作中存在机械损耗和油液黏性引起的摩擦损失,所以液压泵的实际输入转矩Ti必然大于理论转矩Tt,其机械效率为ηm为泵的理论转矩Tt与实际输入转矩的Ti比值。即
③液压泵的总效率η η为泵的输出功率Po与输入功率Pi之比。即
不计能量损失时,泵的理论功率Pt=pqt=2πnTt,所以
(5)液压泵所需电动机功率的计算 在液压系统设计时,如果已选定了泵的类型,并计算出了所需泵的输出功率Po,则可用公式Pi=Po/η计算泵所需的输入功率Pi。
以上各计算公式,单位均采用国际单位,使用常用单位的应统一化成国际单位代入计算。
例如,已知某液压系统所需泵输出油的压力为4.5MPa,流量为10L/min,泵的总效率为0.7,则泵所需要的输入功率Pi应为
这样,即可从电动机产品样本中查取功率为1.1kW的电动机。
【任务实施】
1.场地与设备
(1)场地 液压实训室,实训基地。
(2)设备 齿轮泵、叶片泵等液压泵,各类型5台,拆装工具。
2.齿轮泵的认识
齿轮泵是一种常用的液压泵,它的主要特点是结构简单,制造方便,价格低廉,体积小,重量轻,自吸性好,对油液污染不敏感,工作可靠;其主要缺点是流量和压力脉动大,噪声大,排量不可调。齿轮泵被广泛地应用于采矿设备、冶金设备、建筑机械、工程机械、农林机械等各个行业。
齿轮泵按照其啮合形式的不同,有外啮合和内啮合两种,其中外啮合齿轮泵应用较广,而内啮合齿轮泵则多为辅助泵。下面以外啮合CB-B齿轮泵为例来分析齿轮泵。
(1)外啮合齿轮泵的组成 齿轮泵的外形结构如图2-1-3(a)所示,CB-B齿轮泵的内部结构如图2-1-3(b)所示,它是分离三片式结构,三片是指泵盖4、8和泵体7。泵的前后盖和泵体由两个定位销17定位,用六个螺钉固紧。主动齿轮6用键5固定在传动轴12上并由电动机带动旋转。

图2-1-3 CB-B齿轮泵的结构
1—轴承外环;2—堵头;3—滚子;4—后泵盖;5,13—键;6—齿轮;7—泵体;8—前泵盖;9—螺钉;10—压环;11—密封环;12—主动轴;14—泄油孔;15—从动轴;16—泄油槽;17—定位销
(2)CB-B型齿轮泵拆装分析(见图2-1-4)

图2-1-4 CB-B型齿轮泵拆装零件图
①拆卸步骤
a.松开紧固螺钉,分开左、右端盖,取出密封圈;
b.从泵体中取出主动齿轮及轴、从动齿轮及轴;
c.分解端盖与轴承、齿轮与轴、端盖与油封。此步可不做。
②装配要领 装配顺序与拆卸相反。
③拆装注意事项
a.如果有拆装流程示意图,请参考该图进行拆与装;
b.仅有元件结构图或根本没有结构图的,拆装时应记录元件及解体零件的拆卸顺序和方向;
c.拆卸下来的零件,尤其泵体内的零件,要做到不落地,不划伤,不锈蚀等;
d.拆装个别零件需要专用工具,如拆轴承需要用轴承起子,拆卡环需要用内卡钳等;
e.在需要敲打某一零件时,请用铜棒,切忌用铁或钢棒;
f.拆卸(或安装)一组螺钉时,用力要均匀;
g.安装前要给元件去毛刺,用煤油清洗然后晾干,切忌用棉纱擦干;
h.检查密封有无老化现象,如果有,请更换新的;
i.安装时不要将零件装反,注意零件的安装位置,有些零件有定位槽孔,一定要对准;
j.安装完毕,检查现场有无漏装元件。
(3)外啮合齿轮泵的工作原理分析
外啮合齿轮泵的工作原理和结构如图2-1-5所示。外啮合齿轮泵主要由主动齿轮2、从动齿轮3,驱动轴,泵体1及端盖等主要零件构成。泵体内相互啮合的主、从动齿轮2和3与两端盖及泵体一起构成密封工作容积,齿轮的啮合点将左、右两腔隔开,形成了吸、压油腔,当齿轮按图示方向旋转时,右侧吸油腔内的轮齿脱离啮合,密封工作腔容积不断增大,形成部分真空,油液在大气压力作用下从油箱经吸油管进入吸油腔,并被旋转的轮齿带入左侧的压油腔。左侧压油腔内的轮齿不断进入啮合,使密封工作腔容积减小,油液受到挤压被排往系统,这就是齿轮泵的吸油和压油过程。

图2-1-5 外啮合齿轮泵的工作原理和结构
1—泵体;2—主动齿轮;3—从动齿轮
(4)主要结构分析(图2-1-4)
①泵体 泵体的两端面开有压力卸荷槽c,侧面泄漏的油液经此槽与吸油口相通,用来降低泵体与端盖结合面间泄漏油的压力。左端进油口m由孔d进入吸油腔,右端排油口腔由孔e通入排油口n。泵体与齿顶圆的径向间隙为0.13~0.16mm。
②左右端盖 封油槽a、b,此槽与吸油口相通,用来防止泵内油液从泵体与泵盖接合面外泄。端盖内侧开有卸荷槽f、g,用来消除困油。端盖上吸油口大,压油口小,用来减小作用在轴和轴承上的径向不平衡力。
③齿轮 两个齿轮的齿数和模数都相等,齿轮与端盖间轴向间隙为0.03~0.04mm,轴向间隙不可以调节。
(5)内啮合齿轮泵
内啮合齿轮泵的工作原理也是利用齿间密封容积的变化来实现吸油压油的。图2-1-6所示是内啮合齿轮泵的工作原理。

图2-1-6 内啮合齿轮泵的工作原理
它是由配油盘(前、后盖)、外转子(从动轮)和偏心安置在泵体内的内转子(主动轮)等组成。内、外转子相差一齿,图中内转子为六齿,外转子为七齿,由于内外转子是多齿啮合,这就形成了若干密封容积。内转子带动外转子作同向旋转。这时,由内转子齿顶和外转子齿谷间形成的密封容积(图中阴线部分),随着转子的转动密封容积就逐渐扩大,于是就形成局部真空,油液被吸入密封腔,当封闭容积达到最大时吸油完毕。当转子继续旋转时,充满油液的密封容积便逐渐减小,油液受挤压,于是通过另一配油窗口将油排出,压油完毕。内转子每转一周,由内转子齿顶和外转子齿谷所构成的每个密封容积,完成吸、压油各一次,当内转子连续转动时,即完成了液压泵的吸排油工作。
内啮合齿轮泵的外转子齿形是圆弧,内转子齿形为短幅外摆线的等距线,故又称为内啮合摆线齿轮泵,也叫转子泵。
内啮合齿轮泵有许多优点,如结构紧凑,体积小,零件少,转速可高达10000r/min,运动平稳,噪声低,容积效率较高等。缺点是流量脉动大,转子的制造工艺复杂等,目前已采用粉末冶金压制成型。随着工业技术的发展,摆线齿轮泵的应用将会愈来愈广泛;内啮合齿轮泵可正、反转,可作液压马达用。
3.叶片泵的认识
叶片泵的结构较齿轮泵复杂,但其工作压力较高,且流量脉动小,工作平稳,噪声较小,寿命较长。所以它被广泛应用于机械制造中的专用机床、自动线等中低液压系统中,但其结构复杂,吸油特性不太好,对油液的污染也比较敏感。
根据各密封工作容积在转子旋转一周吸、排油液次数的不同,叶片泵分为两类,即完成一次吸、排油液的单作用叶片泵和完成两次吸、排油液的双作用叶片泵。单作用叶片泵多为变量泵,工作压力最大为7.0MPa,双作用叶片泵均为定量泵,一般最大工作压力亦为7.0MPa,结构经改进的高压叶片泵最大的工作压力可达16.0~21.0MPa。
(1)双作用叶片泵 双作用叶片泵的结构如图2-1-7所示。它由前泵体6和后泵体7,左右配油盘1、5,定子4,转子,叶片,传动轴3等组成,右配油盘5的右侧与高压油腔相通,使配油盘与定子端面紧密配合,对转子端面间隙自动补偿。

图2-1-7 双作用叶片泵的典型结构
1,5—配油盘;2,8—轴承;3—传动轴;4—定子;6—前泵体;7—后泵体;9—密封圈;10—盖板;11—叶片;12—转子;13—定位销
①YB1型叶片泵拆装分析(见图2-1-8)

图2-1-8 YB1型叶片泵的零件图
拆卸步骤:
a.卸下固定螺钉,拆开泵体;
b.取出右配油盘;
c.取出转子和叶片;
d.取出定子,再取下左配油盘。
拆卸后清洗、检验、分析。
装配要领:与拆卸顺序相反。
拆装注意事项参考齿轮泵拆装注意事项。
②双作用叶片泵的工作原理分析 如图2-1-9所示,泵由定子1、转子2、叶片3和配油盘(图中未画出)等组成。定子和转子是同心的,定子内表面是由两段长半径圆弧、两段短半径圆弧和四段过渡曲线组成,近似为椭圆柱形。当转子转动时,叶片在离心力和(建压后)根部压力油的作用下,在转子槽内作径向移动而压向定子内表面,由叶片、定子的内表面、转子的外表面和两侧配油盘间形成若干个密封空间,当转子按图示方向旋转时,处在小圆弧上的密封空间经过渡曲线而运动到大圆弧的过程中,叶片外伸,密封空间的容积增大,要吸入油液;再从大圆弧经过渡曲线运动到小圆弧的过程中,叶片被定子内壁逐渐压进槽内,密封空间容积变小,将油液从压油口压出。因而,当转子每转一周,每个工作空间要完成两次吸油和压油,所以称之为双作用叶片泵,这种叶片泵由于有两个吸油腔和两个压油腔,并且各自的中心夹角是对称的,所以作用在转子上的油液压力相互平衡,又称为平衡式叶片泵。为了要使径向力完全平衡,密封空间数(即叶片数)应当是双数。

图2-1-9 双作用叶片泵的工作原理
1—定子;2—转子;3—叶片
③主要零件分析(图2-1-8)
a.定子和转子 定子内表面曲线是由四段圆弧和四段过渡曲线所组成。目前常用的过渡曲线有阿基米德螺旋线,等加速-等减速曲线等。保证叶片贴紧在定子内表面上,使叶片在转子槽中径向运动时速度和加速度的变化均匀,过渡曲线接点处圆滑过渡,以避免冲击、噪声和磨损。定子和转子的外表面是圆柱面。转子中心固定,径向开有12条槽可以安置叶片。
b.叶片 该泵共有12个叶片,流量脉动较小。流量脉动率在叶片数为4的整数倍、且大于8时最小,故双作用叶片泵的叶片数通常取为12或16。叶片相对于转子径向连线前倾13°,防止作用在叶片上的切向力过大引起的叶片折断以及因切向力过大导致的摩擦力过大,使叶片滑动困难甚至卡死的现象出现。转子不允许反转。
c.配流盘 油液从吸油口m经过空腔a,从左右配油盘的吸油窗口b吸入,压力油从压油窗口c经右配油盘中的环形槽d及右泵体中的环形槽e,从压油口n压出。在配油盘端面开有环槽f与叶片底部r相通,右配油盘上的环槽有通过空h与压油窗c相通。这样压力油就可以进入到叶片底部,叶片在压力油和离心力的作用下压向定子表面,保证紧密接触以减少泄漏。在配油盘的压油窗口一边,开一条小三角卸荷槽s(又称眉毛槽),使两叶片之间的封闭油液在未进入压油区之前就通过该三角槽与液压油相通,使其压力逐渐上升,因而减缓了流量和压力脉动,降低了噪声。从转子两侧泄漏的油液,通过传动轴与右配油盘的间隙,从g孔流回吸油腔b。
(2)单作用叶片泵
①单作用叶片泵的工作原理分析 单作用叶片泵的工作原理如图2-1-10所示,单作用叶片泵由转子1、定子2、叶片3和端盖等组成。定子具有圆柱形内表面,定子和转子间有偏心距。叶片装在转子槽中,并可在槽内滑动,当转子回转时,由于离心力的作用,使叶片紧靠在定子内壁,这样在定子、转子、叶片和两侧配油盘间就形成若干个密封的工作空间,当转子按图示的方向回转时,在图的右部,叶片逐渐伸出,叶片间的工作空间逐渐增大,从吸油口吸油,这是吸油腔。在图的左部,叶片被定子内壁逐渐压进槽内,工作空间逐渐缩小,将油液从压油口压出,这是压油腔,在吸油腔和压油腔之间,有一段封油区,把吸油腔和压油腔隔开。

图2-1-10 单作用叶片泵的工作原理
1—转子;2—定子;3—叶片
叶片泵在转子每转一周,每个工作空间完成一次吸油和压油,因此称为单作用叶片泵。转子不停地旋转,泵就不断地吸油和排油。
②单作用叶片泵的结构特点
a.改变定子和转子之间的偏心便可改变流量。偏心反向时,吸油压油方向也相反。
b.处在压油腔的叶片顶部受到压力油的作用,该作用要把叶片推入转子槽内。为了使叶片顶部可靠地和定子内表面相接触,压油腔一侧的叶片底部要通过特殊的沟槽和压油腔相通。吸油腔一侧的叶片底部要和吸油腔相通,这里的叶片仅靠离心力的作用顶在定子内表面上。
c.由于转子受到不平衡的径向液压作用力,所以这种泵一般不宜用于高压。
d.为了更有利于叶片在惯性力作用下向外伸出,而使叶片有一个与旋转方向相反的倾斜角,称后倾角,一般为24°。
(3)限压式变量叶片泵 限压式变量叶片泵是单作用叶片泵,根据前面介绍的单作用叶片泵的工作原理,改变定子和转子间的偏心距e,就能改变泵的输出流量,限压式变量叶片泵能借助输出压力的大小自动改变偏心距e的大小来改变输出流量。当压力低于某一可调节的限定压力时,泵的输出流量最大;压力高于限定压力时,随着压力增加,泵的输出流量线性地减少,其工作原理如图2-1-11所示。泵的出口经通道7与活塞6相通。在泵未运转时,定子2在弹簧9的作用下,紧靠活塞4,并使活塞4靠在螺钉5上。这时,定子和转子有一偏心量e0,调节螺钉5的位置,便可改变e0。当泵的出口压力p较低时,则作用在活塞4上的液压力也较小,若此液压力小于上端的弹簧作用力,当活塞的面积为A、调压弹簧的刚度为ks、预压缩量为x0时,有
pA<ksx0 (2-1-10)

图2-1-11 限压式变量叶片泵的工作原理
1—转子;2—定子;3—压油窗口;4—活塞;5—螺钉;6—活塞腔;7—通道;8—吸油窗口;9—调压弹簧;10—调压螺钉
此时,定子相对于转子的偏心量最大,输出流量最大。随着外负载的增大,液压泵的出口压力p也将随之提高,当压力升至与弹簧力相平衡的控制压力pB时,有
pBA=ksx0 (2-1-11)
当压力进一步升高,使pA>ksx0,这时,若不考虑定子移动时的摩擦力,液压作用力就要克服弹簧力推动定子向左移动,随之泵的偏心量减小,泵的输出流量也减小。pB称为泵的限定压力,即泵处于最大流量时所能达到的最高压力,调节调压螺钉10,可改变弹簧的预压缩量x0即可改变pB的大小。
设定子的最大偏心量为e0,偏心量减小时,弹簧的附加压缩量为x,则定子移动后的偏心量e为
e=e0-x (2-1-12)
这时,定子上的受力平衡方程式为
pA=ks(x0+x) (2-1-13)
将式(2-1-11)代入式(2-1-12)可得
e=e0-A(p-pB)/ksp≥pB (2-1-14)
式(2-1-14)表示了泵的工作压力与偏心量的关系,由式可以看出,泵的工作压力愈高,偏心量就愈小,泵的输出流量也就愈小,且当p=ks(e0+x0)/A时,泵的输出流量为零,控制定子移动的作用力是将液压泵出口的压力油引到柱塞上,然后再加到定子上去,这种控制方式称为外反馈式。
这种泵被广泛用于要求执行元件有快速、慢速和保压阶段的中低压系统中,有利于节能和简化回路。
4.柱塞泵的认识
柱塞泵是靠柱塞在缸体中作往复运动造成密封容积的变化来实现吸油与压油的液压泵,与齿轮泵和叶片泵相比,这种泵有许多优点。首先,构成密封容积的零件为圆柱形的柱塞和缸孔,加工方便,可得到较高的配合精度,密封性能好,在高压工作仍有较高的容积效率;第二,只需改变柱塞的工作行程就能改变流量,易于实现变量;第三,柱塞泵中的主要零件均受压应力作用,材料强度性能可得到充分利用。由于柱塞泵压力高,结构紧凑,效率高,流量调节方便,故在需要高压、大流量、大功率的系统中和流量需要调节的场合,如龙门刨床、拉床、液压机、工程机械、矿山冶金机械、船舶上得到广泛的应用。柱塞泵按柱塞的排列和运动方向不同,可分为径向柱塞泵和轴向柱塞泵两大类。
(1)径向柱塞泵 径向柱塞泵的组成及工作原理如图2-1-12所示,柱塞1径向排列装在缸体2中,缸体由原动机带动连同柱塞1一起旋转,所以缸体2一般称为转子,柱塞1在离心力的(或在低压油)作用下抵紧定子4的内壁,当转子按图示方向回转时,由于定子和转子之间有偏心距e,柱塞绕经上半周时向外伸出,柱塞底部的容积逐渐增大,形成部分真空,因此便经过衬套3上的油孔从配油孔5和吸油口b吸油,衬套3是压紧在转子内,并和转子一起回转;当柱塞转到下半周时,定子内壁将柱塞向里推,柱塞底部的容积逐渐减小,向配油轴的压油口c压油,当转子回转一周时,每个柱塞底部的密封容积完成一次吸压油,转子连续运转,即完成压吸油工作。配油轴固定不动,油液从配油轴上半部的两个孔a流入,从下半部两个油孔d压出,为了进行配油,配油轴和衬套3接触的一段加工出上下两个缺口,形成吸油口b和压油口c,留下的部分形成封油区。封油区的宽度应能封住衬套上的吸压油孔,以防吸油口和压油口相连通,但尺寸也不能大得太多,以免产生困油现象。

图2-1-12 径向柱塞泵
1—柱塞;2—缸体;3—衬套;4—定子;5—配油轴
(2)轴向柱塞泵
①轴向柱塞泵的工作原理 轴向柱塞泵是将多个柱塞配置在一个共同缸体的圆周上,并使柱塞中心线和缸体中心线平行的一种泵。轴向柱塞泵有两种形式,即直轴式(斜盘式)和斜轴式(摆缸式)。
如图2-1-13(a)所示为直轴式轴向柱塞泵的工作原理,这种泵主体由缸体1、配油盘2、柱塞3和斜盘4组成。柱塞沿圆周均匀分布在缸体内。斜盘轴线与缸体轴线倾斜一角度,柱塞靠机械装置或在低压油作用下压紧在斜盘上(图2-1-13中为弹簧),配油盘2和斜盘4固定不转,当原动机通过传动轴使缸体转动时,由于斜盘的作用,迫使柱塞在缸体内作往复运动,并通过配油盘的配油窗口进行吸油和压油。如图2-1-13中所示回转方向,当缸体转角在π~2π范围内,柱塞向外伸出,柱塞底部缸孔的密封工作容积增大,通过配油盘的吸油窗口吸油;在0~π范围内,柱塞被斜盘推入缸体,使缸孔容积减小,通过配油盘的压油窗口压油。缸体每转一周,每个柱塞各完成吸、压油一次,如改变斜盘倾角γ,就能改变柱塞行程的长度,即改变液压泵的排量,改变斜盘倾角方向,就能改变吸油和压油的方向,即成为双向变量泵。图2-1-13(b)所示为直轴式轴向柱塞泵。

图2-1-13 轴向柱塞泵
1—缸体;2—配油盘;3—柱塞;4—斜盘;5—传动轴;6—弹簧
斜轴式轴向柱塞泵的缸体轴线相对传动轴轴线成一倾角,传动轴端部用万向铰链、连杆与缸体中的每个柱塞相联结,当传动轴转动时,通过万向铰链、连杆使柱塞和缸体一起转动,并迫使柱塞在缸体中作往复运动,借助配油盘进行吸油和压油。这类泵的优点是变量范围大,泵的强度较高,但和上述直轴式相比,其结构较复杂,外形尺寸和重量均较大。
轴向柱塞泵的优点是:结构紧凑、径向尺寸小,惯性小,容积效率高,目前最高压力可达40MPa,甚至更高,一般用于工程机械、压力机等高压系统中,但其轴向尺寸较大,轴向作用力也较大,结构比较复杂。
由于柱塞在缸体孔中运动的速度不是恒速的,因而输出流量是有脉动的,当柱塞数为奇数时,脉动较小,且柱塞数多脉动也较小,因而一般常用的柱塞泵的柱塞个数为7、9或11。
②轴向柱塞泵的结构特点
a.缸体端面间隙的自动补偿 由图2-1-13(a)可见,使缸体压紧配流盘端面的作用力,除弹簧6的推力外,还有柱塞孔底部台阶面上所受的液压力,此液压力比弹簧力大得多,而且随泵的工作压力增大而增大。由于缸体始终受力紧贴着配油盘,就使端面间隙得到了自动补偿,提高了泵的容积效率。
b.滑履结构 在斜盘式轴向柱塞泵中,一般都在柱塞头部装一滑履(见图2-1-14),二者之间为球面接触。而滑履与斜面之间又以平面接触,从而改善了柱塞工作的受力状况。并且由于各相对运动表面之间通过小孔引入压力油,实现可靠的润滑,故大大降低了相对运动零件表面的磨损,就有利于泵在高压下工作。

图2-1-14 滑履结构
c.变量机构 在变量轴向柱塞泵中均设有专门的变量机构,用来改变斜盘倾角γ的大小以调节泵的排量。轴向柱塞泵的变量方式有多种,其变量机构形式亦多种多样。
5.液压泵的选用及故障分析
液压泵是液压系统提供一定流量和压力的油液动力元件,它是每个液压系统不可缺少的核心元件,合理地选择液压泵对于降低液压系统的能耗、提高系统的效率、降低噪声、改善工作性能和保证系统的可靠工作都十分重要。
(1)液压泵的选用 选择液压泵的原则是:根据主机工况、功率大小和系统对工作性能的要求,首先确定液压泵的类型,然后按系统所要求的压力、流量大小确定其规格型号。
表2-1-1列出了液压系统中常用液压泵的主要性能。
表2-1-1 各类液压泵的选用

一般来说,由于各类液压泵各自突出的特点,其结构、功用和运转方式各不相同,因此应根据不同的使用场合选择合适的液压泵。一般在机床液压系统中,往往选用双作用叶片泵和限压式变量叶片泵;而在筑路机械、港口机械以及小型工程机械中往往选择抗污染能力较强的齿轮泵;在负载大、功率大的场合往往选择柱塞泵。
(2)液压泵的故障分析 见表2-1-2。
表2-1-2 液压泵的故障分析

【思考与练习】
1.液压传动中常用的液压泵分为哪些类型?
2.什么是容积式液压泵?它的实际工作压力大小取决于什么?
3.容积式液压泵的工作原理是什么?
4.如果与液压泵吸油口相通的油箱是完全封闭的,不与大气相通,液压泵能否正常工作?
5.什么是泵的排量、流量?什么是泵的容积效率、机械效率?
6.外啮合齿轮泵有哪些优缺点?低压齿轮泵、中高压齿轮泵和高压齿轮泵的压力范围各是多少?
7.齿轮泵的困油现象是怎么引起的?对其正常工作有何影响?如何解决?
8.齿轮泵的径向力不平衡是怎样产生的?会带来什么后果?消除径向力不平衡的措施有哪些?
9.说明叶片泵的工作原理。双作用叶片泵和单作用叶片泵各有什么优缺点?
10.叶片泵为什么能得到最广泛的应用?目前所用中压叶片泵、中高压叶片泵和高压叶片泵的额定压力范围各是多少?
11.限压式变量叶片泵适用于什么场合?有何优缺点?
12.径向柱塞泵和轴向柱塞泵各有什么优缺点?各适用于什么场合?
13.各类液压泵中,哪些能实现单向变量或双向变量?画出定量泵和变量泵的符号。
14.已知液压泵转速为1000r/min,排量为160mL/r,额定压力为30MPa,实际输出流量为150L/min,泵的总效率为0.87,求:
(1)泵的理论流量;
(2)泵的容积效率和机械效率;
(3)额定工况下驱动液压泵所需的电动机功率。
15.已知某液压泵的输出压力为5MPa,排量为10mL/r,机械效率为0.95,容积效率为0.9,转速为1200r/min,求:
(1)液压泵的总效率;
(2)液压泵输出功率;
(3)电动机驱动功率。