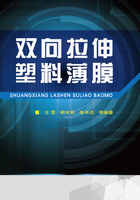
第四节 原料结晶和干燥设备
一般聚合物分子链被分裂成较小部分的反应过程。根据聚合物降解时所受的作用及反应机理不同,通常分为热降解、氧化降解、机械降解、化学降解和生物降解等类型。研究聚合物降解反应有着很重要的意义。如在聚合物成型过程中防止热降解的发生,可提高产品质量和使用寿命。该过程也可用来制取有价值的小分子物质,如天然聚合物在生物酶作用下,从蛋白质分解成氨基酸;从纤维素或淀粉等制取葡萄糖。在合成聚合物方面,也利用降解过程回收单体、制取新型聚合物,如嵌段及端基聚合物等。此外,制备出可以自然降解的聚合物,对于解决高分子材料公害、保持生态平衡也起着重要作用。
通常,聚合物降解是发生在碳-杂链(C-N、C-O、C-Si等)处。因为,碳-杂链的键能较弱,稳定性较差,而碳-碳键的键能相对较强,稳定性较好,除非在强烈的条件和有降低主链强度的侧链时才可能发生降解。
聚合物水解后,分子量产生明显下降,下降的程度与水分含量有关,与加热温度与加热时间有关。表2-1显示不同含水量PET切片降解情况。
表2-1 不同含水量PET切片降解情况

对于塑料切片这类的干燥处理,聚合物加工前必须将树脂进行严格的除湿处理。
比如对于有吸湿倾向的高聚物(例如PET、PA、PC等),在进行双向拉伸之前,须先进行预结晶和干燥处理。这样做的目的是:进一步提高聚合物的软化点,避免其在干燥和熔融挤出过程中树脂粒子互相粘连或结块;往除树脂中的水分,防止含有酯基的聚合物在熔融挤出过程中发生水解或产生气泡。
一般PET的预结晶和干燥设备采用带有结晶床的填充塔,同时配有干空气制备装置,包括空压机、分子筛除湿器、加热器等。预结晶和干燥温度为150~170℃,干燥时间约3.5~4h,干燥后的PET切片湿含量要求控制在(30~50)×10-6。
另外,聚丙烯、聚苯乙烯类聚合物,其主链是碳-碳键相连,侧基为甲基或苯环。因此,这些聚合物稳定性较好,加工前如果原材料中水分含量较低,就不需要专门进行干燥处理。然而,多数薄膜生产线为了确保加工的稳定性、提高产品质量,一般都要配备一台简单的干燥处理器或采取其他措施减小降解。
一、干燥过程的影响因素
原料的干燥处理的过程实质是用加热的方法使原料含水率降低的过程,对于结晶聚合物来说,干燥过程除了降低含水率外,也是充分结晶的过程。
1.分阶段干燥原理
塑料切片的干燥处理是在高于树脂玻璃转化温度(Tg)以上的温度下进行的。在此温度下结晶聚合物会很快结晶,并且在外部加热(及结晶放热)的作用下,切片中未结晶的部分会被软化,或者结晶较细,较不完整的部分会发生熔化。因此,切片在干燥的初期,如果没有及时地搅动,就会出现切片相互粘连,甚至结成大块(已结晶的切片则无此现象)。
2.影响干燥速度的因素
(1)降速干燥阶段 一般为物料干燥降速阶段。此时,切片的空穴内与氢键结合微量水分向表面气化的速率低于切片表面水分气化速率;干燥过程是湿切片表面逐渐变干、气化表面不断向内移动、内部温度也不断升高、内部水分逐渐减少的过程。因此,水分由内部向表面扩散率是逐渐下降的,干燥速率越来越低。这个阶段干燥时间就需要很长。
(2)恒速干燥阶段 一般切片干燥效果(切片含水率下降)明显,吸附于切片表面及细孔中的机械结合水很容易排除。实验表明,干燥10min水分含量就可由0.29%下降到0.16%。
3.切片干燥工艺要求与工艺条件
根据切片干燥原理可以看出,强化干燥效果必须具备以下条件。①选定适当的预干燥-干燥处理时间。②减小干燥介质的水汽分压,即减小进入干燥器的空气湿含量与进入预干燥器(结晶器)加热气体的湿含量。热空气的湿含量越低,与切片的湿含量差值越大,切片中的水分越容易被空气带走。③要选择适当的加热温度与加热程序。④防止切片粘连,促使切片均匀受热。⑤在选择物料及设备时,尽量增大干燥面积。
一般切片干燥的工艺条件是与使用的干燥设备有密切关系。这里,我们以易水解的聚酯为例,当它们采用气流干燥与真空干燥两种不同干燥设备时,干燥的工艺条件有很大区别,具体数据见表2-2。
表2-2 PET切片干燥工艺条件

一般从表2-2可以看出:在预干燥阶段,应该采用略低的加热温度,并要施加外力(气流或机械)使切片充分搅动,及时排出蒸发的水分,此阶段所用的时间比较短;在干燥阶段则需要采用较高加热温度,使用较长的干燥时间,并要求干燥介质含水率尽量小;在真空干燥时,由于传热效率低,所用干燥时间长,但干燥效果好。
二、干燥方式及各种干燥器性能的比较
尽管塑料切片干燥方式种类繁多,但是,归纳起来主要有气流干燥与真空干燥两大类。为了便于使用者选择干燥装置,这里,对几种典型的干燥装置作一简单介绍。
1.气流干燥
这种干燥方法是流态化原理在干燥中的应用,大多数工业用的气流干燥装置都是连续生产装置,其特点是传热、传质速率高,干燥能力强,设备结构简单,设备投资较低。但是也存在能量消耗大的问题。目前,这类设备在国内外得到广泛应用。我国近20年引进的BOPET、BOPA、BOPP、BOPS薄膜生产线及涤纶纺丝生产线,普遍采用这种方法。
在气流干燥方法中,按物料的流动方向来分可以分为立式、卧式两种。
(1)立式气流干燥器 古老的单层圆筒式干燥器(图2-9),目前在工业生产中已被淘汰。工作时,干燥热空气从筒底进入,穿过多孔板,把从顶部加入的切片吹起,物料在筒体内呈沸腾状态,切片上下翻动,彼此碰撞,进行传热、传质。当使用这种方法时,必须严格地控制气流速度,严格控制进出料量。否则,在生产过程中容易出现切片反混和短路,引起切片干燥不均匀。此外,这种方法能量消耗很大,干燥效率低。所以,只能用在小型挤出机、注塑机上。

图2-9 单层圆筒沸腾床干燥器
1—沸腾室;2—加料器;3—多孔板;4—加热器;5—风机;6—旋风分离器
近几年来,在纺织、制膜工业中,立式连续干燥设备用得比较多,其种类也多种多样,各种立式干燥器之间的主要区别在于干燥系统中是否使用预干燥器、预干燥器的形式、干燥器的内部结构、干燥空气的来源。
通常,对于最终含水率较低的干燥系统(PET、PA)都是由预干燥器和干燥器两部分组成的。图2-10为多层圆筒沸腾床干燥器。图2-11为一种组合立式预干燥器-干燥装置的工艺流程图。对于最终含水率比较高的聚合物(PP、PS),可以只用一个立式干燥器。

图2-10 多层圆筒沸腾床干燥器

图2-11 组合立式预干燥器-干燥装置的工艺流程
1—干燥器;2—预干燥器;3,9,14—风机;4—振动加料器;5—旋转阀;6,15—加热器;7—过滤器;8—排气阀;10—旋风分离器;11,16—阀门:12—预除湿器;13—除湿器
国内锥形流化床按操作分有两种型式:一种是浓相溢流出料,近年来国内较多在流化造粒方面使用;另一种即喷动床干燥,是由床顶出料,产品在旋风分离器内收集或间歇操作床底出料。这种结构比流化床结构简单,设备小,产量大,干燥强度高、床层等温性强、不发生局部过热。过去仅适用于大颗粒物料(聚氯乙烯),近年来已发展至能应用于细粒物料的干燥。目前在塑料、谷物、制药等部门使用。但因动力消耗较大,使用受到一定限制。
当使用预干燥器-干燥装置的干燥系统时,其预干燥器可以使用以下几种类型。
①热传导式搅拌干燥器 在一个带有夹套的卧式槽形干燥室内设置多种形状的中空或实心的搅拌桨叶,在夹套或中空的搅拌桨叶内充以热介质,湿物料在搅拌桨叶的翻炒下呈机械流化状态,与传热壁面或热气流充分接触而达到干燥的目的,此类干燥器统称为热传导式搅拌干燥器。
②带搅拌的预干燥器 干燥热空气从容器底部进入,从顶部排出,物料在预干燥器内受到搅拌器的搅动免于结块、加速表面水分蒸发。
③较短的卧式沸腾床预干燥器 如图2-11。
④振动式预干燥器 经过结晶、预干燥的物料然后进入立式干燥器。在干燥器内通过干燥气流表面扩散及较长的停留时间,强化了减速干燥能力。目前,用得最多的立式干燥器是沉降式干燥器,即塔内的物料靠自重自然沉降,不断与底部上升的干燥热气流进行热交换。
个别的薄膜生产线也有采用带有翻板的塔式干燥器。这种干燥器内部有多层带孔的翻板,顶部加入的物料可以在每层板上按照规定的时间作短暂地停留,并能均匀地与干燥热空气进行热交换,然后打开翻板,使物料落入下一层。这种结构的干燥器传热好,有助于物料的混合。但翻板的传动系统较复杂,机械故障多,故应用并不广泛。
在组合立式干燥器中,气流的循环过程是:室内洁净空气→用冷冻水表冷器进行预除湿+化学除湿器→加热器+干燥器→预干燥器内循环、部分排入大气。也可以省掉预除湿和化学除湿器,直接选用压缩空气。
(2)卧式沸腾床干燥器(图2-12) 又称流化床,这种干燥器也是一种连续式干燥器,它是由空气过滤器、加热器、沸腾床主机、旋风分离器、布袋除尘器、高压离心风机、操作台组成,由于干燥物料的性质不同,配套除尘设备时,可按需要考虑,可同时选择旋风分离器、布袋除尘器,也可选择其中一种,一般密度较大的如冲剂及颗粒料干燥只需选择旋风分离器,密度较轻的小颗粒状和粉状物料需配套布袋除尘器,并备有气力送料装置及皮带输送机供选择。它是一个狭长的加热箱,内有许多垂直的挡板,把干燥器分成许多室。物料经过一个旋转阀,从干燥器的一端加入,从另一端放出。热空气从各室的底部经过筛孔向上吹动,并从出料口顶部的排气口排除。物料在各室内被热风吹起,呈沸腾状态,并逐次越过内部的隔板向出口端流动。物料在沸腾床内的流动速度与挡板高度、多孔板斜度与加热气流的风量、风压有关。各室加热空气的温度、湿度、流量均可以调节。

图2-12 卧式多室沸腾床干燥器
1—摇摆式颗粒进料器;2—干燥器;3—卸料器;4—加热器;5—空气过滤器;6—旋风分离器;7—袋滤器;8—风机
这种干燥器的进气速度在整个沸腾床的各部分是不同的。进料区为重流态化区。在这个区域里,气流的速度较高,电机带动旋转风门生成的脉冲的气流使物料预干燥(结晶)、防止物料结块,带走切片表面大量的水分。以后的区域流态化程度逐渐减小,在这些区域里,热风主要是起输送物料与加热、脱水的作用。从干燥器排出的热空气,部分经旋风分离器、空气热交换器排入大气,大部分经加热器再返回干燥器。
一般来说卧式沸腾床干燥设备热效率较低,操作稳定性差,对于易水解的原料,干燥设备需要很长。因此,应用范围受到一定的限制,只适用于中小型薄膜生产厂或最终水分含量可以较高的物料。对于大型薄膜生产线,如果物料又属于易水解的材料,通常这种干燥装置只作为一台预干燥器(结晶器),然后再与立式干燥器组合起来使用。
这种干燥设备的优点是流体阻力比较小,有利于热空气与物料进行热交换;只要加料量不过大,又有足够大的气流,可以有效地避免物料结块。在上述设备的基础上,近几年来为了充分利用热能、增大物料干燥时间,又出现了逆流卧式干燥器。这类干燥器有的设计成带内抄板的转筒式干燥器;有的设计成双螺杆卧式干燥器。由于加强了与内壁热传导作用,使用了强制机械输送物料装置,因此降低了能量消耗,提高了干燥能力。
(3)振动式干燥器 振动式干燥机是一种新型、高效、节能的干燥装置。它是依靠容器外部的机械振动力,使切片达到流化状态,流化的切片与底部吹上的热气流不断接触,使切片加热、水分蒸发。汽化的水分可以由热空气带出,也可以用真空泵抽出。
常用振动式干燥器也有卧式及立式两种。
①多层圆盘振动干燥机(图2-13) 图2-13所示为一种具有多层带孔塔板的圆盘振动干燥机。工作时,湿物料是从上部的进料口加入机内,在外加激振力的作用下,物料在具有一定斜度的圆盘上作圆周运动,每旋转一周便落到下一层塔板上,热风则从机器最底部向上流动,穿过各盘上的物料,与物料形成错流、逆流。含湿量大的气体由顶部排气口排出,其中一部分排入大气,大部分经过旋风分离器、过滤器、加热器再循环使用。干燥后的物料则由底部排料口连续卸下。多层圆盘振动式干燥设备的优点是可以连续化生产,操作简单,清理方便,易更换产品品种,可以防止物料结块,使用空气量较少,粉尘带出量少,机械效率高,节能效果好(可节能30%~60%)。但是由于工作时整机是处于不停的振动中,也就存在弹簧容易疲劳损坏及噪声较大的弊病。

图2-13 多层圆盘振动干燥机
1—空气过滤器;2—鼓风机;3—空气加热器;4—床体;5—旋风分离器;6—袋式除尘器;7—抽风机
②单层振动流化床干燥器 这类设备类似卧式沸腾床干燥器,区别在于使机器内物料浮动、流移的主要作用力不是干燥的空气,而是外加的振动力。设备内无竖直隔板,湿料从一端加入,在多孔板上水平振移,并与底部吹上的热空气进行热交换,排除切片中的水分。由于这种设备的长度有限,物料停留时间不能过长。因此只适用于小型薄膜生产线或作为预干燥器使用。振动式干燥器多用于中型生产工厂,有一些小型工厂也使用真空振动式干燥器(图2-14)。

图2-14 真空振动式干燥器
2.真空干燥器
在干燥含水量较低的易水解的物料时,真空干燥器也是一种常见的干燥装置。真空干燥器的优点是机械化程度高,生产能力大,流动阻力小,容易控制,产品质量均匀。此外,真空干燥器对物料的适应性较强,不仅适用于处理散粒状物料,当处理黏性膏状物料或含水量较高的物料时,可向其中掺入部分干料以降低黏性。真空干燥器的缺点是设备笨重,金属材料耗量多,热效率低(约为50%),结构复杂,占地面积大,传动部件需经常维修等。目前国内采用的真空干燥器直径为0.6~2.5m,长度为2~27m,处理物料的含水量为3%~50%,产品含水量可降到0.5%,甚至低到0.1%(均为湿基)。物料在转筒内的停留时间为几分钟到2h,或更高。
根据物料在设备内搅动的方式,真空干燥器分为以下几种类型。
(1)偏心卧式真空转鼓(图2-15) 偏心卧式真空转鼓类似圆柱形的旋转筒体,它的旋转支撑轴是在筒体的对角线上,轴与筒体的中心线夹角>25°,其外部设有油或蒸汽加热套,筒体内物料的装料量一般小于简体容积的70%,工作时,由于筒体是低速旋转的,物料在重力与离心力的合力作用下,不停搅动,并与筒壁不断进行热交换,从物料中蒸发出的水分随时被真空泵抽出。这类设备在聚酯、尼龙薄膜厂及纤维厂均有广泛地应用。它更是用固相聚合法生产增黏聚酯切片必不可少的设备。

图2-15 偏心卧式真空转鼓
1—疏水阀;2—右支座;3—真空转鼓;4—左支座;5—缓冲罐;6—冷凝器;7—真空泵
此类设备的内层材料均为不锈钢。根据设备的容量的大小来分,最常见的规格有4m3、6m3、8m3、20m3、24m3、36m3。
(2)带内搅拌器的真空干燥器 图2-16是带内搅拌真空干燥器的一种形式——真空螺旋干燥器。筒体的外部设有油或蒸气加热套,筒内装有旋转的搅拌器。由于搅拌器不断地转动,改进了干燥器的传热、传质效果。这类装置是一种节能、高效型真空干燥器,生产能力高,如果搅拌器设计合理,可以实现既防止物料产生化学降解、减小机械磨损,又能保证物料最终含水率达10mg/kg,并具有良好混合的作用。这种装置的缺点是难以清理与维修,设备较复杂,成本较高。

图2-16 带内搅拌器的真空干燥
1—树脂;2—驱动电动机;3—机械密封;4—抽真空;5—旋转板;6—出料;7—蒸汽管
所有的真空干燥器都是靠夹套内传热介质(油、蒸汽)进行加热,工作时转鼓内需要抽真空,故这类设备是属于受压容器。对于蒸汽加热的设备,蒸汽压力有时高达0.4~0.6MPa。如果使用循环油进行加热,压力可以适当降低。
在设计真空系统时,需要考虑抽出空气的温度较高,含水率较大,抽出空气中可能含有部分聚合物粉尘。因此,真空系统中应该安装缓冲器,并且应该选用水环泵与机械泵的组合泵或水喷射泵、蒸汽喷射泵等,避免真空泵油乳化。
3.各种干燥设备性能的对比
在选择聚合物干燥设备时,要考虑物料干燥能力、干燥质量、设备操作性能、能耗、投资费用等多种因素。表2-3显示各种干燥设备的对比情况。
表2-3 塑料切片干燥设备性能对比

注:○代表好;△代表可以;×代表较差。
4.铸片系统
铸片系统主要包括模头、急冷辊和静电吸附装置等。
①模头 是流延铸片的关键,它直接决定铸片的外形和厚度的均匀性。PET常采用衣架型长缝模头,模头开度通过若干个带有加热线圈的推/拉式差动螺栓进行初调,并通过在线测厚仪的自动测厚、反馈给模头的加热螺栓进行模唇开度的微调。模头温度控制在275℃左右。
②急冷辊(铸片辊、俗称冷鼓) 是将流出模头呈黏流态的PET熔体在匀速转动的急冷辊上快速冷却至其玻璃化温度以下而形成玻璃态的厚度均匀的铸片。急冷的目的是使厚片成无定型结构,尽量减少其结晶,以免对下道拉伸工序产生不良影响。为此,对铸片辊要求:一是其表面温度要均匀、冷却效果要好;二是要求急冷辊转速均匀而稳定。铸片辊内通30℃左右的冷却水,以保证铸片冷至60℃以下。
③静电吸附装置 其作用是使铸片与急冷辊能紧密接触,防止急冷辊转动时卷入空气,以保证传热-冷却效果。静电吸附装置由金属丝电极、高压发生器及电极收放力矩电机等组成。其工作原理是利用高压发生器产生的数千伏的直流电压,使电极丝、铸片辊分别变成负极和正极(铸片辊接地),铸片在此高压静电场中因静电感应而带上与铸片辊极性相反的静电荷,在异性相吸的作用下,铸片与急冷辊表面紧密吸附在一起,达到排除空气和良好传热的目的。对非极性高聚物如PP,采用静电吸附的效果不及具有极性的PET,故BOPP双拉生产线铸片时,通常采用气刀法贴附。
④纵向拉伸(MDO) 纵向拉伸是将来自铸片机的厚片在加热状态下进行一定倍数的纵向拉伸。纵向拉伸机由预热辊、拉伸辊、冷却辊、张力辊和橡胶压辊、红外加热管、加热机组及驱动装置等组成。
预热辊:一般有8只,辊筒表面镀铬,一字形排列,温度60~80℃。
拉伸辊:如是单点拉伸,有一只慢拉辊、一只快拉辊,表面镀铬。慢拉辊温度80~85℃,快拉辊温度30℃。
冷却辊:一般有4只,辊筒表面镀铬,一字形排列,温度30℃、50℃。
张力辊:二只,分别位于第一个预热辊和第四个冷却辊的上方。
纵拉比:一般在3~3.5倍,它是通过慢拉辊与快拉辊之间的速度差而产生的。
横向拉伸(TDO)如下所述。
横向拉伸机结构比较复杂,它由烘箱、链夹和导轨、静压箱、链条张紧器、导轨宽度调节装置、开闭夹器、热风循环系统、润滑系统及EPC等组成。横拉机构有进膜、预热、拉幅、缓冲、定型和冷却等功能段。
横拉机的作用是将经过纵向拉伸的薄膜在横拉机内分别通过预热、拉幅、热定型和冷却而完成薄膜的双向拉伸。
横向拉伸的主要工艺参数有:拉伸温度:因经过纵向拉伸的薄膜已有一定的结晶取向度,故横向拉伸温度要比纵拉高15~25℃,具体温度取决于薄膜的厚度和拉伸速度。
拉伸倍数:对于平衡膜,横向拉伸倍数与纵向拉伸倍数基本相同或接近;对于强化膜,纵向拉伸倍数要大于横向拉伸倍数。
热定型温度与时间:在生产非收缩性薄膜时,横向拉伸后必须进行热定型处理,目的是完善其结晶取向过程,消除内应力,增加尺寸稳定性。热定型温度应选择PET结晶速率最大的温度段,即190~210℃,热定型时间约需3~6s。冷却温度:热定型后的PET薄膜还要进行热松弛处理,最后进入冷却段风冷至100℃以下。