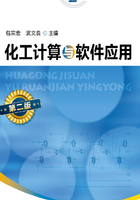
2.2 简单物理过程
2.2.1 混合过程
在化工生产中,固体、液体、气体物质溶解于溶剂的过程是常见的单元操作,涉及溶解度和溶解热的计算。物质溶解于溶剂的过程通常经过两个过程:一种是溶质分子(或离子)在溶剂中的扩散过程,这种过程为物理过程,需要吸收热量;另一种是溶质分子(或离子)和溶剂分子作用,形成溶剂化分子的过程,这是化学过程,放出热量。当放出的热量大于吸收的热量时,溶液温度就会升高,如浓硫酸、氢氧化钠等;当放出的热量小于吸收的热量时,溶液温度就会降低,如硝酸铵等;当放出的热量等于吸收的热量时,溶液温度不变,如盐、蔗糖等。多股物料的混合与一股物料分流成多股物料是化工生产中常见的操作,其物料与能量衡算可以用Aspen Plus 中的混合器与分流器进行模拟。
例2-1 混酸过程——电解质过程数据包应用。
硝基苯是一种有机合成中间体,常用作生产苯胺、染料、香料、炸药等的原料。其生产方法是以苯为原料,以硝酸和硫酸的混合酸为硝化剂进行苯的硝化而制得。现用三种酸 (组成见例2-1附表1) 常压下配制硝化混合酸,要求混合酸含0.27(质量分数)HNO3及0.60(质量分数)H2SO4,混合酸流率2000kg/h。求:(1)三种原料酸的流率;(2)若原料酸的温度均为25℃,混合过程绝热,计算混合酸的温度、密度、黏度、表面张力、恒压热容。
例2-1附表1 三种酸的组成 (质量分数)

解 首先物料衡算求原料用量 设混合过程稳定,无物料损失,根据式(2-1),输入体系的物料质量流率应该等于离开体系的物料质量流率。以x,y,z 分别代表循环酸、浓硫酸、浓硝酸的原料质量流率,列出以下物料衡算方程组:
0.22 x + 0.9 z = 2000×0.27
0.57 x + 0.93 y = 2000×0.6
0.21 x + 0.07 y + 0.1 z = 2000×(1−0.27−0.6)
解出循环酸 x = 768.85kg/h,浓硫酸y = 819.09kg/h,浓硝酸z = 412.06kg/h。下面用Aspen Plus 软件中的混合器模块“Mixer”模拟计算。
① 选择电解质过程数据包 在软件安装位置“GUI”文件夹的“Elecins”子文件夹中,选择水与硫酸电解质过程数据包“eh2so4”,把此文件复制到另一文件夹中打开,默认计算类型“Flowsheet”。对物流的数据格式进行设置,在“Setup| Report Options|Stream”页面的“Fraction basis”栏中选择质量流率和质量分数,在“Stream format”栏中选择“ELEC_E”电解质输出格式。单击“Next”按钮,进入组分输入窗口,原数据包中已包含了水、硫酸体系的所有分子组分与离子组分,只需要在“Component ID”中再加入硝酸组分。
② 再次确定体系的构成 加入硝酸后,溶液中的离子成分需要重新确定,点击“Elec Wizard”按钮,进入电解质体系构建方法向导窗口,见图2-2。单击“Next”按钮,进入基础组分与离子反应选择页面,把混合酸溶液的各个电解质组分选入到“Selected components”栏目中,离子反应类型用默认选择,如图2-3所示。

图2-2 电解质体系构建方法向导

图2-3 基础组分与离子反应类型选择
单击“Next”按钮,进入溶液离子种类和离子反应方程式确认页面。热力学模型选用“ELECNRTL”,如图2-4所示,单击“Next”按钮予以确认。在软件询问电解质溶液组成表达方式时,选择“Apparent component approach”,使计算结果仍然用溶液的表观组成表示,以方便阅读计算结果。连续单击“Next”按钮,确认软件已选择的热力学模型参数、电解质离子对参数。软件“Elec Wizard”功能构建的混合酸溶液电解质体系的实际组分如图2-5所示。

图2-4 溶液体系构成要素确认

图2-5 混合酸溶液的实际组分
③ 画流程图 选择混合器模块“Mixers”,拖放到工艺流程图窗口,用物流线连接混合器的进出口,如图2-6所示。依次双击进料物流号,把三股原料酸的进料物流信息填入对应栏目中。

图2-6 混合流程图
④ 设置混合器参数 在混合器模块“Input|Flash options”页面,填写闪蒸压力1atm、液相混合。
⑤ 设置物性输出 在“Properties|Prop-Sets|Properties”页面,创建一个输出物性集名“PS-1”,选择题目要求输出的物性名称,如图2-7所示。在“Qualifiers”页面,选择物流的相态为“Liquid”。在“Setup|Report Options|Stream”页面,点击“Property-Sets”按钮,在弹出的对话框中选择物性集“PS-1”,使“PS-1”数据能够输出,见图2-8。至此,混合器模拟计算需要的信息已经设置完毕,点击计算。

图2-7 设置输出物性的名称与计量单位

图2-8 选择输出物性集
⑥ 查看计算结果 计算结果如图2-9所示。

图2-9 酸混合过程计算结果
由图2-9可知,混合酸的质量流率2000kg/h,等于三种原料酸的质量流率和,即混合过程总物料平衡。由于采用了电解质溶液的表观组成表示方法,各物流中只显示表观组分含量,混合酸的硫酸质量分数是60%,硝酸的质量分数是27%,达到题目要求。另外,可以看到各物流的物性,其中混合酸的温度为45.1℃,密度1649.6kg/m3,黏度4.2cP(1cP=1×10−3Pa·s),表面张力0.075N/m。
此混合过程也可手工计算,依据是硫酸溶于水的积分溶解热曲线,或依据25℃时1mol硫酸溶解到水中的积分溶解热与水物质的量n的关系[式(2-3)]。因硝酸溶于水的积分溶解热数值相对很小,可忽略不计。引用图2-9对4股物流的物性计算值,由式(2-3)计算得到的各物流的放热量见例-1附表2。
(2-3)
混合过程总的放热量:Q =[−363310−(−176490−108170)] = −78650(kJ/h)
查出混合酸的热容是105.9kJ/(kmol·K)、混合酸的摩尔流率为35.238kmol/h,故混合酸的温升是:
(℃)
则混合酸的温度是25 + 21.1 = 46.1(℃),与模拟计算的混合酸温度近似。
例2-1附表2 混合过程各物流的放热量

2.2.2 汽化过程
汽化热是温度不变时,单位质量液体物质在汽化过程中吸收的热量。化工生产中有很多不同温度等级的高温物流,除了可以进行冷热物流的相互换热外,也可以利用高温物流作为热源来生产水蒸气,使生产过程所需的动力和热能得以全部或部分自给,提高整个工厂的热效率和经济效益。
例2-2 废热锅炉产汽量——“Heatx”模块应用。
某化工厂计划用高温废气生产水蒸气,进入废热锅炉的废气温度450℃,压力300kPa,出口废气的温度260℃,进入锅炉的水温25℃,产生3.0MPa的饱和水蒸气,试计算每100kmol废气可产生的水蒸气量。
解 ① 全局性参数设置 计算类型“Flowsheet”,用氮气代替废气,在组分输入窗口“Component ID”中输入氮气、水,把氮气设置为亨利组分,选用“TEAM-TA”质方法计算水蒸气性质。
② 绘制流程图 废热锅炉采用两股流体换热器“HeeatX”模块计算,热流体可能较脏走管程,冷流体一般比较洁净走壳程,流程见图2-10。

图2-10 废热锅炉流程图
③ 设置流股信息 把题目给定的氮气物流信息填入对应栏目中,水的用量不知,暂时填写200kg/h,由“Design Specs”功能确定准确值。
④ 设置模块信息 在换热器模块的“Setup|Specifications”页面,指定采用换热器的简捷模式计算,指定冷流体出口汽化分率为1.0。在换热器模块的“Block Options|Properties”页面,管程氮气物流的物性计算采用SRK方程,见图2-11。

图2-11 壳程与管程的物性计算选择不同的性质方法
⑤ 反馈计算求进水量 在“Flowsheeting Options|Design Specs|Input|Define”页面,创建一个流程变量“N2OUT”,定义为废热锅炉氮气出口温度;在“|Input|Spec”页面,规定变量“N2OUT”为260℃,设置计算允许误差0.01℃;在“|Input|Vary”页面,设置废热锅炉进水“3H2O”的流率范围为100~300kg/h。
⑥ 模拟计算 结果见图2-12,图2-12(a)给出了冷热流体的始终状态与废热锅炉的热负荷,图2-12(b)给出了冷热流体的流率。可见热流体的出口温度为规定的260℃,冷流体的出口温度为233.9℃,废热锅炉的热负荷为160kW,生产3.0MPa 饱和水蒸气213.9kg/h。

图2-12 废热锅炉计算结果
2.2.3 单级相平衡过程
单级相平衡过程是指两相流体经一次充分混合、相互传质达到平衡后再分离的过程。由于平衡两相的组成不同,因而可起到一个平衡级的分离作用。化工过程中常见到的一些单元操作,如闪蒸罐、蒸发器、分液罐等,其操作原理近似于单级相平衡过程,在进行相关的设计计算时,可归纳为单级相平衡分离计算。这些计算包括汽(气)液平衡、液液平衡、汽(气)液液三相平衡、液固平衡、气固平衡等,对应于Aspen Plus 软件中的Flash2、Decanter、Flash3、Crystallzer、HyCyc等计算模块,可根据需要选择使用。
例2-3 汽-液-液三相平衡计算——Sensitivity功能考察相变点温度。
已知合成苯乙烯固定床反应器出口气体流率如附表,如果将该物料在300kPa下从150℃降温到38℃,问:(1)是否分相;(2)若分相,求各相的流率与组成;(3)分相时的温度。
例2-3附表 混合气体组成

解 因为混合物中含有氢气、水、醇、烃组分,降温后形成汽液液三相平衡的可能性较大,可用Aspen Plus 中的汽液液三相平衡计算模块“Flash3”求解。
① 全局性参数设置 选择公制计量单位模板,计算类型“Flowsheet”,输入混合物中的所有组分,把氮气设置为亨利组分。
② 选择性质方法 考虑到可能会出现部分互溶,应选择“NRTL”性质方法。另外平衡压力为300kPa,应该考虑汽相的非理想性,故可选择NRTL-RK方程。单击“Next”按钮,进入“Properties|Parameters|NRTL-1”页面,要求确认NRTL方程的二元交互作用参数。进料中有6个组分,应该有15对二元交互作用参数。可以看到软件显示的二元交互作用参数不全,只有8对。这时,可以在“Estimate missing parameters by UNIFAC”前面的方框内打钩,由UNIFAC方程计算缺失的二元交互作用参数。
③ 画流程图 选择汽液液三相平衡闪蒸器“Flash3”模块,拖放到工艺流程图窗口,用物流线连接进出口。为方便阅读,对物流编号进行更改,如图2-13所示。

图2-13 三相闪蒸流程图
④ 设置流股信息 双击进料物流号,把物流信息填入对应栏目中。
⑤ 设置闪蒸器操作参数 在闪蒸器模块的“Input|Specifications”页面,填写闪蒸温度38℃,闪蒸压力300kPa。
⑥ 模拟计算 计算结果如图2-14所示。在闪蒸器模块的“Results|Summary”页面,可看到闪蒸后的汽相分率为0.239;闪蒸器的热负荷为-17.5MW,表明为维持38℃的闪蒸温度,需要移除17.5MW的热量;有机相占总液相的分率0.522。

图2-14 三相平衡闪蒸计算结果
在闪蒸器模块的“Results|Balance”页面,可看到进料总流率与三股出料的总流率之和相等,达到物料平衡。在闪蒸器模块的“Results|Phase Equilibrium”页面,可看到闪蒸后的相平衡数据,包括进料、闪蒸后三股物流的组成,汽相中各组分分别与两液相中组分的相平衡常数。在闪蒸器模块的“Streams Results|Material”页面,可看到闪蒸前后物流的详细信息,包括组分流率、摩尔分数、总流率、物流焓与熵、物流密度,平均分子量,如图2-15所示。若希望增加出口物流的其他热力学性质或者传递性质的输出数据,可参照例2-1的方法进行设置。

图2-15 闪蒸前后的物流信息
⑦ 考察相变温度点 为考察反应器出口混合气体在冷凝冷却过程中的相变温度点,可以利用软件的“Sensitivity”分析功能进行进一步的详细模拟计算。在“Model Analysis Tools|Sensitivity”页面,建立一个灵敏度分析文件“S-1”,对闪蒸器的3股产品物流进行定义,对汽相物流的定义方式如图2-16所示。在“S-1”文件的“Input|Vary”页面,对自变量闪蒸温度进行定义,变化范围为150~30℃,步长-1℃,如图2-17所示。在“S-1”文件的“Input|Tabulate”页面,设置计算数据输出格式,如图2-18所示,其中“V/1546”是要求软件输出汽相分率的计算值,以便观察相变点。

图2-16 定义汽相物流

图2-17 定义闪蒸器温度变化

图2-18 定义输出物流
⑧ 模拟计算 计算结果见图2-19。由图2-19(a)可知,当反应器出口混合气体在150~30℃的区间冷凝冷却时,汽相分率从1.0下降到0.234,最终汽相中的主要成分是氢气;不同温度下的汽相分率曲线在143℃和107℃出现转折点,且在转折点的下方汽相分率加速下降,说明在这两个转折点上出现了相变。由图2-19(b)可知,在143℃开始产生第一液相,在107℃开始产生第二液相,同时汽相流率曲线在这两个转折点上出现下降转折点。综合两图信息,可以判断143℃为体系一次露点,开始出现有机相冷凝,107℃为体系二次露点,出现水相冷凝,107℃也是体系泡点。

图2-19 冷凝冷却过程中的相变温度点考察
例2-4 液液相平衡(LLE)计算——Design Specifications功能调整溶剂用量。
以甲基异丁基酮(C6H12O,简记MIBK)为萃取溶剂,从含醋酸质量分数0.08的水溶液中萃取醋酸。萃取温度25℃,进料量13500kg/h。求:(1)若要求萃余液中醋酸质量分数为0.01,问单级萃取时溶剂量为多少;(2)萃取温度0~50℃时,醋酸在MIBK相和水相中的浓度是多少。
解 ① 全局性参数设置 选择SI-CBAR计量单位集,对输出结果的数据格式选择质量分数,输入MIBK、醋酸、水。
② 选择性质方法 因为是LLE计算,选择UNIQUAC方程,确认UNIQUAC方程的二元交互作用参数。进料中有3个组分,应该有3对二元交互作用参数。可以看到软件显示的二元交互作用参数齐全。同一对组分的二元交互作用参数可能有不同的数据库来源,如来源于汽液平衡(VLE),或者来源于LLE。对于LLE计算,应该选择来源于LLE数据库的二元交互作用参数。在“Properties|Parameters|UNIQ-1|Input”页面,点击“Source”栏目,选择来源于LLE数据库的二元交互作用参数,见图2-20(a)。应用软件的相图绘制功能,绘制出MIBK-醋酸-水体系在常压、25℃下的LLE相图,见图2-20(b)。由图可见,萃取溶剂MIBK与醋酸互溶,与水微溶,因此可以从水相中萃取醋酸。

图2-20 性质方法选择与LLE相图
③ 画流程图 把模块库中的“Decanter”模块拖放到工艺流程图窗口,用物流线连接萃取器的进出口,如图2-21所示。双击进料物流号,把题目给定的进料物流信息填入对应栏目中。溶剂MIBK的用量暂时不知道,以估计的140000kg/h填入。

图2-21 液液萃取流程图
④ 设置模块信息 “Decanter”模块参数设置如图2-22所示。运行计算,在“Results Summary|Streams”页面,可看到萃取后的两平衡液相物流信息,如图2-23所示。可见萃余液中醋酸质量分数0.0117>0.01,说明萃取溶剂的流率还不足。

图2-22 设置模块信息

图2-23 初次单级萃取计算后的两平衡液相
⑤ 调整萃取溶剂用量 在“Flowsheeting Options|Design Specs”子目录,点击“New”按钮,建立一个模拟对象文件“DS-1”。给因变量(萃余相醋酸质量分数)取名“XL2”,对“XL2”的定义见图2-24(a),对“XL2”设定收敛要求和容许误差,见图2-24(b),对萃取溶剂用量的设定见图2-24(c)。

图2-24 反馈计算调整萃取溶剂用量
⑥ 模拟计算 结果见图2-25,可见萃取溶剂用量为168540kg/h时,萃余相中醋酸质量分数为0.010,达到分离要求。

图2-25 萃取过程模拟计算结果
在“B1”模块的“Results|Summary”页面,可见为维持25℃的LLE温度,外部环境需要向分相器提供290kW的热量。第一液相(有机相)的质量分数为进入分相器总量的0.795。在“B1”模块的“Results|Balance”页面,可见进口的两液相质量流率之和等于出口的两原料流率之和,总物料达到平衡。在“B1”模块的“Results|Phase equilibrium”页面,可见两液相平衡组成和相平衡常数值。
⑦ 求取不同温度下的溶解度 进一步地,利用软件的“Sensitivity”分析功能,可以计算不同温度下醋酸在MIBK相和水相中的浓度。在“Model Analysis Tools|Sensitivity”子目录,建立一个模拟对象文件“S-1”。在“S-1”文件的“Define”页面,给萃取相的醋酸质量分数取名“XL1”,对“XL1”的定义见图2-26。类似地,定义萃余相的醋酸质量分数“XL2”。在“S-1”文件的“Vary”页面,对萃取温度及其变化范围进行定义,设定温度步长5℃,如图2-27所示。在“S-1”文件的“Tabulate”页面,给出计算数据的输出格式。

图2-26 定义萃取相醋酸质量分数

图2-27 定义萃取温度
把“B1”模块中萃取溶剂物流“MIBK”的流量修改为准确值168540kg/h,隐藏反馈计算文件“DS-1”。运行灵敏度设置文件“S-1”,计算结果见图2-28。可见随着温度上升,水相中的醋酸浓度逐步降低,MIBK相中醋酸浓度逐步增加。在25℃,醋酸在水相中的质量分数是0.01。相平衡问题也可以用“RGibbs”模块模拟计算,模拟流程见图2-29,参数设置见图2-30,溶剂用量140000kg/h时的计算结果与用Decanter模块计算结果相同。

图2-28 不同温度下醋酸在MIBK相和水相中的浓度

图2-29 “RGibbs”模块LLE流程

图2-30 “RGibbs”模块参数设置
例2-5 固液溶解平衡计算——Sensitivity功能调整结晶温度。
质量分数为0.3的硫酸钠水溶液以5000kg/h的流率在50℃下进入冷却型结晶器,首先结晶出来的是十水硫酸钠(GLAUBER),假设常压操作,求开始结晶的温度。
解 ① 选择数据包 在软件安装目录“GUI”文件夹的“Elecins”子文件夹中,选择电解质过程数据包“pitz_3”,把此文件拷贝到另一文件夹中打开使用,计算类型“Flowsheet”。因为数据包“pitz_3”中已包含题目中的所有分子组分与离子组分,已经选择了“PITZER”性质方法,因此“组分输入”与“物性选择”两项操作均可省略,直接进入流程图绘制步骤。另外,在数据包“pitz_3”中的分子组分与离子组分远大于本题所涉及的组分数,不必删除或修改,不影响后续计算。
② 画流程图 选择模块库中的“Crystallizer”模块,拖放到工艺流程图窗口,用物流线连接结晶器的进出口,对模块、物流改名,见图2-31,把题目给定的进料物流信息填入对应栏目中。

图2-31 结晶器流程图
③ 设置模块信息 在“Saturation calculation method”栏目下,有3种结晶饱和度的计算方法供选择:一是输入固液平衡数据(Solubility);二是由电解质化学反应计算电解质盐的溶解度(Chemistry);三是由用户子程序计算固液平衡(User subroutine)。本例选择“Chemistry”,结晶饱和度数据由软件自带的电解质化学反应平衡常数计算得到。在“Salt specifications|Salt component ID”栏目下,指定结晶物质名称为GLAUBER。在“Valid phases”栏目下,选择物流相态“Liquid-Only”。在“Operating mode”栏目下,选择操作模式“Crystallizing”,见图2-32。软件自带的GLAUBER电解质化学反应平衡常数可在“Reaction|Chemiastry|PITZ-3”文件夹中看到。至此,结晶器模拟计算需要的信息已经全部设置完毕。点击软件运行计算,结果报警,提示没有结晶生成,说明结晶温度设置50℃太高。

图2-32 结晶器模块设置
④ 寻找开始结晶温度点 在“Model Analysis|Tools|Sensitivity”页面,建立一个灵敏度分析文件“S-1”,定义因变量“W”代表GLAUBER晶体的质量流率,如图2-33所示。在“S-1”文件夹的“Input|Vary”页面,定义自变量为结晶温度,变化范围32~30℃,步长-0.05℃,如图2-34所示。在“S-1”文件夹的“Input|Tabulate”页面,设置灵敏度计算输出格式。

图2-33 定义晶体质量流率

图2-34 灵敏度分析自变量设置
点击“Next”按钮,软件运行,部分温度点没有结晶生成而报警,如图2-35所示。由灵敏度计算结果可知,结晶开始温度点为31.3℃,产生十水硫酸钠结晶10.783kg/h,当温度升到31.35℃时结晶全部溶解。

图2-35 灵敏度分析计算结果
图2-36是文献中硫酸钠水溶液结晶相图,可以看到,质量分数30%的硫酸钠水溶液起始结晶温度约在31℃,软件计算结果与文献数据吻合。在31.3℃结晶时,进出结晶器物流总质量流率平衡,GLAUBER晶体10.783kg/h,进料中的其余硫酸钠均以离子状态存在。在结晶器模块的“CRYSTALL|Results|Summary”页面,可见在31.3℃结晶时,需要移除结晶热量92.24kW。

图2-36 硫酸钠水溶液结晶相图
例2-6 气固平衡计算——Design Specifications功能调整热空气用量。
用90℃热空气常压下干燥含水0.005(质量分数)的SiO2粉末1000kg/h,湿粉末温度20℃。要求粉末中水分含量降到0.001(质量分数),求热空气需要量。
解 这是气固两相平衡计算问题,可用Aspen Plus 中的固体模块求解,也可用气液模块求解。用气液模块求解时,软件把液体和固体合并为一相处理。下面用“Flash2”模块求解,选择含固体过程的公制计量单位模板“Solids with Metric Units”。
① 全局性参数设置 计算类型“Flowsheet”。因为本例物流中有固体颗粒,在“Setup|Stream class|Flowsheet”页面的“Stream class”栏目中,软件自动选择了物流类型为“MIXCISLD”,说明物流中有常规固体存在,但是没有粒子颗粒分布。在组分输入窗口添加空气、水、SiO2,在“Type”栏目中把SiO2属性改为“Solid”。因为是常压气固平衡计算,选择“IDEAL”性质方法。
② 设置物流的物性输出 在“Properties|Prob-Sets|ALL-SUBS|Properties”页面,为计算结果的物性选择合适的计量单位:混合物体积流率(VOLFLMX),混合物气相质量分率(MASSVFRA),混合物固相质量分率(MASSSFRA),混合物密度(RHOMX),混合物中组分质量流率(MASSFLOW),混合物温度(TEMP),混合物压力(PRES)。
③ 画流程图 选择模块库中的“Flash2”模块,拖放到工艺流程图窗口,用物流线连接干燥器模块的进出口,对模块、物流改名,如图2-37所示。

图2-37 气固平衡计算流程图
④ 设置流股信息 对热空气物流,只需要一个页面提供物流信息,因为用量暂时不知道,以估计的1.0kmol/h 填入,见图2-38。对湿粉末物流需要两个页面提供物流信息,图2-39为设置物流中水分的质量流率,图2-40为设置物流中固体颗粒的质量流率。

图2-38 热空气物流设置

图2-39 水分质量流率设置

图2-40 固体颗粒质量流率设置
⑤ 设置模块信息 干燥器模块的参数填写见图2-41。至此,干燥器模拟计算需要的信息已经全部设置完毕。点击“Next”按钮,软件运行计算。

图2-41 干燥器模拟计算设置
⑥ 查看初步计算结果 在干燥器模块的“Results Summary|Streams”页面,可看到干燥后的两平衡相物流信息,如图2-42所示。题目要求固相干燥后水分降到0.001,即干燥器出口固相中水分为0.995kg/h。而计算结果中固相中水分为4.54kg/h,高于干燥要求,说明热空气的流率还不足。

图2-42 干燥器初步计算结果
⑦ 调整热空气的用量 在“Flowsheeting Options|Design Specs”子目录,点击“New”按钮,建立一个模拟对象文件“DS-1”,干燥器出口固相中水分量定义为“W”,见图2-43;出口固相中颗粒分量定义为“SIO2”,见图2-44。

图2-43 定义干燥器出口固相中水分量

图2-44 定义干燥器出口固相中颗粒分量
⑧ 设定收敛要求和容许误差以及热空气用量 对因变量设定收敛要求和容许误差,如图2-45所示;对热空气用量的设定,如图2-46所示。

图2-45 收敛要求和容许误差设定

图2-46 热空气用量的设定
⑨ 模拟运行与结果 在干燥器模块的“Streams Results”页面,可见当热空气用量准确值为203.531kg/h时,干燥器出口固相含量为0.999,达到分离要求,如图2-47所示,干燥器进、出口总质量流率达到平衡,各组分质量流率也达到平衡。

图2-47 干燥器模拟结果
2.2.4 机械分离过程
机械分离过程的分离对象是由两相或两相以上物流所组成的非均相混合物,目的是简单地将各相加以分离,操作特征是在分离过程中各相之间无质量传递现象。机械分离操作包括过滤、沉降、离心分离、旋风分离、旋液分离和静电除尘等化工过程常见的单元操作。
例2-7 固液机械分离——HYCYC模块应用。
用氢氧化钙与水混合制备碱性水用于酸性气体的吸收。已知氢氧化钙用量740kg/h,水用量5400kg/h,常压混合,温度20℃,石灰乳中固体颗粒的粒径分布见例2-7附表。若用旋液分离器除去固体颗粒,要求对固体颗粒的截留率达到0.99,求:(1)旋液分离器出口物流碱性水和含渣水的流率与组成;(2)旋液分离器的尺寸。
例2-7附表 石灰乳中固体颗粒的粒径分布

解 ① 全局性参数设置 选择含固体过程的公制计量单位模板,计算类型“Flowsheet”,选择SI-CBAR计量单位集,把压力单位改为“atm”。因本例进料物流中含不同粒径分布的固体颗粒,需要在“Setup|Stream class|Flowsheet”页面的“Stream class”栏目中选择“MIXCIPSD”,说明物流中有常规固体粒子的颗粒分布存在。为输入进料物流中固体粒子颗粒分布数据,在“Setup|Substream|PSD|PSD”页面,输入粒径分布范围,如图2-48所示。
② 输入组分 在“Component ID”中输入水和氢氧化钙。点击“Elec Wizard”按钮,进行电解质组分的离子化设置,溶液的真实组分构成见图2-49;采用电解质性质方法ELECNRTL计算石灰乳溶液物性。

图2-48 输入粒径分布范围

图2-49 石灰乳溶液成分
③ 画流程图 选择混合器模块和“HYCYC”旋液器模块拖放到工艺流程图窗口。用物流线连接混合器和旋液器的进出口,构成旋液分离流程,对模块、物流改名,如图2-50所示。

图2-50 旋液分离流程图
④ 设置流股信息 双击进料物流号,把题目给定的进料物流信息填入对应栏目中。对水的物流,只需要一个页面提供物流信息:20℃,1atm,5400kg/h。对氢氧化钙物流有两个输入页面,其中第一页面在子物流 “CIPSD”栏目中填写氢氧化钙的物流信息,第二页面提供氢氧化钙颗粒的粒径分布数据,如图2-51(a)及图2-51(b)所示。

图2-51 设置氢氧化钙物流信息
⑤ 设置模块操作参数 混合器不必设置,直接跳过。在旋液器模块的“Input| Specification”页面,计算模式“Calculation mode”栏目选择“Design”,表明是设计型计算。设计参数“Design parameters”栏目填写分离要求和对旋液器尺寸与运行压降的估计数据,见图2-52。至此,模拟计算需要的信息已经全部设置完毕,进行计算。计算结果见图2-53和图2-54。

图2-52 旋液器模块操作参数设置

图2-53 旋液器设计尺寸

图2-54 旋液器模块物料平衡数据
图2-53给出了旋液器的操作数据与设备规格:操作压降3.8kPa,旋液器长度1.46m,直径0.29m,悬浮液进口管径0.042m,溢流口径0.058m,底流口径0.044m,悬浮液进口流速1.1m/s,旋液器中液体体积流率5.41m3/h。
图2-54给出了旋液分离后的清液物流和浊液物流的物料平衡数据,清液物流中的固体颗粒质量流率是4.54kg/h,浊液物流中的固体颗粒质量流率是735.46kg/h,进出物流中固体颗粒的质量达到平衡,可计算出旋液器颗粒分离效率为735.46/740×100%=99.4%,达到题目规定的分离要求。图2-54还给出了清液物流和浊液物流中颗粒分布数据,可见清液物流中的固体颗粒以100~120μm的细颗粒为主,达到80%,浊液物流中的固体颗粒以140~200μm的粗颗粒为主,100~120μm的细颗粒不到10%。