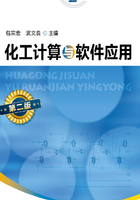
2.5 含循环流过程
真实的化工过程往往都含有循环流。根据循环流的性质,可分为组分循环流与能量循环流。在萃取精馏、共沸精馏、液液萃取、气液吸收过程中,往往要把萃取溶剂、共沸剂、吸收剂等从产物物流中分离出来循环使用。在化学反应过程中,因为反应转化率的限制,反应物不能在反应器中一次全部反应,往往要从反应器出口物流中分离出未反应的组分再返回反应器入口进行二次反应。所有这些工艺设置或操作会在化工过程中产生组分循环流。
为回收利用产品物流的能量,往往要将高温物流与低温物流换热,这就有可能形成热量循环流。另外,在化工过程模拟过程中,进行反馈计算、灵敏度分析计算、最优化计算等,都会产生循环流的求解问题。根据工艺流程中循环流的复杂程度,又可分成独立循环、嵌套循环、交叉循环等不同的循环回路。循环流的出现,使得计算复杂化,产生许多大型非线性方程组,手工计算往往难以为继。化工过程模拟的实质是对大型非线性方程组的求解,就模型方法的求解而言,主要有三种方法,即序贯模块法、联立方程法、联立模块法。
序贯模块法从系统入口物流开始,经过接收该物流变量单元模块的计算得到输出物流变量,这个输出物流变量就是下一个相邻单元的输入物流变量,依次逐个地计算过程系统中的各个单元,最终计算出系统的输出物流。该方法的优点是与实际过程的直观联系较强,模拟系统软件的建立、维护和扩充都比较方便,易于通用化,当计算出错时易于诊断出错位置。主要缺点是对存在多股循环物流的复杂流程,需要采用多层嵌套迭代,求解计算效率低下,尤其在解决设计和过程优化问题时需要反复迭代求解,耗时较多。
联立方程法又称为面向方程法,是将描述整个过程系统的所有方程组成一个大型非线性代数方程组,同时求解此方程组得出模拟计算结果。联立方程法可以根据问题的要求灵活地确定输入输出变量,而不受实际物流和流程的影响。由于所有的方程同时求解、同步收敛,不存在嵌套迭代的问题,因此该方法计算效率较高,尤其计算优化问题具有明显优势。但该方法需要较大存储量和较复杂计算,计算出错诊断比较困难。
联立模块法可以看成是综合序贯模块法和联立方程法的优点而出现的一种折中方法,将过程系统的近似模型方程与单元模块交替求解,在每次迭代中都要求解过程的简化方程,以产生新的初值作为严格模型单元模块的输入,通过严格模型的计算产生简化模型的可调参数。联立模块法兼具序贯模块法和联立方程法的优点,既能使用序贯模块法开发的大量模块,又能将过程收敛和设计规定收敛等迭代循环合并处理,通过联立求解达到同时收敛的目的。
Aspen Plus软件将序贯模块法和联立方程法两种算法同时包含在一个模拟工具中。序贯模块法提供了过程收敛计算的初值,联立方程法大大提高了流程模拟计算的收敛速度,使收敛困难的过程计算成为可能,并可节省计算时间。
Aspen Plus软件包含的数值计算方法有韦格斯坦法(WEGSTEIN)、直接迭代法(DIRECT)、正割法(SECANT)、拟牛顿法(BROYDE)、牛顿法(NEWTON)、序列二次规划法(SQP)等。软件默认的数值计算方法是韦格斯坦法,当此方法不收敛时,可改用其他数值计算方法,以使含循环物流的流程模拟迅速收敛。
采用序贯模块法进行流程模拟计算时,要求所有进料物流的数据已知后才能进行计算,每个单元操作模块按流程顺序执行,每个模块计算出来的输出流股被作为下一个模块的进料使用。如果流程中没有循环物流,计算简单快捷。带有循环回路的过程计算必须循环求解,流程的执行要求选择撕裂流股,也就是具有所有由循环确定的组分流、总摩尔流、压力和焓的循环流股,可以是一个回路中的任意一股流股。若只有简单的一两股物流循环,软件会自己判断选择撕裂流股,对循环物流赋值。每个撕裂流股都有一个相关的收敛模块,由Aspen Plus 生成收敛模块的名字,以字符$开始。但是如果流程较复杂,为加快收敛,人为对撕裂流股赋值会较容易得到收敛结果。
对于复杂的多循环回路的过程,有效地加速收敛方法:一是将流程分段或分节后运算,二是将循环回路撕裂,给循环物流的下一次计算赋一个初值(温度,压力,流量,组成),然后计算。根据计算结果,再把计算结果作为下次赋值填入,反复迭代,直至循环物流相差很小时,再把撕裂流股接入循环物流的流程计算,这样会很快收敛。
2.5.1 萃取精馏
在相对挥发度接近1或等于1的原料中加入高沸点萃取溶剂,使原料中组分的相对挥发度增大,从而使难以精馏分离的原料得以分离,这种分离方法称为萃取精馏。通常在萃取精馏塔的后面要设置溶剂再生塔,并使回收的萃取溶剂循环利用。
例2-13 萃取精馏与溶剂回收组合流程——Calculator功能应用。
甲苯和正庚烷都是含7个碳原子的烃类化合物,沸点相近,普通精馏分离困难。选择苯酚为萃取溶剂,用萃取精馏方法分离甲苯正庚烷混合物。根据小试研究结果,规定摩尔溶剂比2.7,操作回流比5,饱和蒸汽进料,进料流率100kmol/h,平均操作压力1.24bar。要求两塔塔顶产品中甲苯、正庚烷的摩尔分数不少于0.98。求:(1)萃取精馏塔和溶剂再生塔的理论塔板数、进料位置;(2)两股产品的流率与组成;(3)若把回收溶剂返回到萃取精馏塔循环使用,求正常生产时需要补充的萃取溶剂流率。
解 解题思路:(1)用Aspen Plus 软件中的“RadFrac”模块串联操作,模拟萃取精馏塔和溶剂再生塔;(2)组合流程稳态运行时需要补充的萃取溶剂量等于两塔顶物流带出的萃取溶剂量之和。模拟过程分两步进行:①模拟两塔串联运行,溶剂不循环,求两塔运行参数;②模拟溶剂循环,求溶剂补充量。
(1)模拟两塔串联运行
① 全局性参数设置 计算类型“Flowsheet”,选择SI-CBAR计量单位集,输入甲苯、正庚烷和苯酚。因两塔内的液相都是均相体系,平均操作压力1.24bar,汽相可看作理想气体,选择“WILSON”性质方法。
② 画流程图 先模拟萃取精馏塔,选择“RadFrac”模块拖放到工艺流程图窗口,用物流线连接精馏塔的进出口,对模块、物流进行改名,如图2-92所示。

图2-92 萃取精馏塔流程图
③ 设置流股信息 双击进料物流号,把题目给定的进料物流信息填入对应栏目中。进料物流入塔压力应该大于塔底压力,取1.5bar。溶剂入塔温度应该与溶剂进料板上的温度接近,取105℃;由题给溶剂比计算,溶剂入塔流率270kmol/h。
④ 设置“B1”模块信息 对于一股进料两股出料的简单精馏塔,可以应用“DSTWU”模块估算精馏塔完成分离任务需要的理论塔板数和进料位置。但萃取精馏塔有两股进料,属于复杂塔,不能用“DSTWU”模块估算理论塔板数、进料位置和需要的操作回流比。理论上可以假设溶剂的浓度和焓沿塔高变化较小,在求取苯酚作用下甲苯、正庚烷的相对挥发度后,按二元精馏计算方法计算分离任务需要的理论塔板数、进料位置和操作回流比,最后设置若干溶剂回收塔板完成萃取精馏塔的设计计算,然后再把简捷计算结果输入软件中进行严格计算,但这一过程繁复且缓慢。“RadFrac”模块是操作型计算,一开始就要输入理论塔板数和进料位置。变通的办法是开始先填入理论塔板数和进料位置的估计值,然后根据分离要求,依据能耗最小的原则,采用软件的优化功能确定理论塔板数和进料位置的准确值。本例中,取萃取精馏塔理论塔板数22,溶剂进料位置7,混合物进料位置13。根据混合物进料组成和塔顶流出物质量要求,估计塔顶出料量50.7kmol/h。塔顶压力设为1.05bar,每塔板压降0.01bar。把这些信息填入“B1”模块“Setup”文件夹的三个页面,其中“Configuration”页面填写见图2-93,模拟结果见图2-94,馏出液中正庚烷的摩尔分数0.985,脱溶剂浓度>0.99,达到分离要求。由“B1|Profiles”页面可见第7板温度103.4℃,说明溶剂入塔温度设置为105℃是合适的。

图2-93 萃取精馏塔参数设置

图2-94 萃取精馏塔模拟计算结果
由B1塔“Profiles”页面数据可绘制各种参数分布图。B1塔汽相组成分布见图2-95(a),第13塔板甲苯、正庚烷的汽相组成在0.5左右,与汽相进料组成相当,原料在此板入塔是合适的。B1塔液相组成分布见图2-95(b),第7~21板上溶剂苯酚浓度0.55左右,可近似看作恒定溶剂浓度,这是萃取精馏塔的操作特性之一。

图2-95 萃取精馏塔内组成分布
溶剂作用下B1塔内正庚烷与甲苯相对挥发度分布见图2-96,溶剂苯酚从第7板入塔后,精馏段与提馏段各块塔板上正庚烷与甲苯的相对挥发度均提高到2以上,使得正庚烷与甲苯的分离变得容易与可行,说明选择苯酚作为萃取溶剂是合适的。

图2-96 正庚烷与甲苯的相对挥发度分布
⑤ 溶剂再生塔的模拟计算 仍然用“RadFrac”模块模拟计算,为了预先估算溶剂再生塔的设置参数,先把B1塔釜液连接到一个流股复制器模块“DUPLICAT”,再把简捷计算模块“DSTWU”连接到“DUPLICAT”上。用“DSTWU”模块简捷计算溶剂再生塔需要的设置参数,如回流比、理论塔板数和进料位置。在“DSTWU”模块的“Input| Specifications”页面,设置操作回流比为最小回流比的1.1倍,塔顶甲苯回收率0.99,苯酚0.002,塔顶压力1.05bar,塔底压力1.2bar。经计算,“DSTWU” 模块给出溶剂再生塔需要的理论塔板数为17,回流比1.1,进料位置11,塔顶出料量50.1kmol/h。
在B1塔后面串联一个“RadFrac”模块“B2”,进行溶剂再生塔的模拟计算。B2塔的进料从流股复制器模块“DUPLICAT”上引入B1塔釜液,再把“DSTWU”模块计算结果输入到“B2”模块,模拟计算结果见图2-97,溶剂再生塔塔顶馏出液中甲苯摩尔分数>0.985,脱溶剂浓度摩尔分数>0.99,达到纯度分离要求。进料总流率是370kmol/h,三股出料流率总和也是370kmol/h,两塔串联系统达到物料平衡。

图2-97 两塔串联系统的物料平衡
(2)模拟溶剂循环 对模拟过程进行修改,删除“DUPLICAT”和“DSTWU”模块,添加混合器、冷却器、增压泵模块,用物流线连接各模块,添加补充萃取溶剂物流“MAKEUP”,构成溶剂循环流程,如图2-98所示。

图2-98 萃取精馏系统溶剂循环流程图
补充萃取溶剂模拟方法:采用软件的“Calculator”功能,计算两塔塔顶物流带出的萃取溶剂量之和,再赋值给补充萃取溶剂物流“MAKEUP”。
① 新增模块参数设置 增压泵出口压力设置为2bar,混合器不必设置,溶剂冷却温度设置为105℃。
② 定义物流名称 在“Flowsheeting Options|Calculator”文件夹中创建一个“MAKEUP”补充萃取溶剂的计算文件,然后在该文件夹“Input|Define”页面定义两塔塔顶带出的萃取溶剂流率变量名称“FTOP1”、“FTOP2”和补充的萃取溶剂流率变量名称“MAUP”,如图2-99所示。其中“FTOP1”和“FTOP2”是输入变量(Import variable),“MAUP”是输出变量(Export variable),补充萃取溶剂流率“MAUP”的定义如图2-100所示。

图2-99 创建计算器文件

图2-100 定义补充萃取溶剂流率变量
③ 计算器设置 在“MAKEUP”文件夹的“Calculate”页面,说明三个变量之间的关系,如图2-101所示,Fortran语言编程规定运算语句从第7列开始编写。

图2-101 定义三个变量运算关系
④ 模拟计算 计算结果见图2-102,萃取精馏塔塔顶正庚烷含量(摩尔分数)0.985,脱溶剂浓度(摩尔分数)49.918/(49.918+0.119)=0.9976,达到分离要求。正庚烷收率49.918/ 50=0.998;溶剂再生塔塔顶甲苯摩尔分数0.996,脱溶剂浓度(摩尔分数)49.881/ (49.881+0.082)=0.9984,达到分离要求,甲苯收率49.881/50= 0.998;正常生产时需要补充的萃取溶剂流率0.8kmol/h。

图2-102 带循环回路的萃取精馏系统计算结果
由模拟过程可知,萃取精馏系统稳定运行时,进入系统的两股物流总量是100.8kmol/h,流出系统的两股物流总量50.7+50.1=100.8kmol/h,进出系统的物流总量相等。由图2-102可看出,各个组分进出系统的量也是相等的。萃取精馏系统运行时的能量从两塔的再沸器输入,消耗的蒸汽能量值分别是2.697MW和1.330MW。另外,增压泵耗能0.001MW,换热器移除热量1.340MW。
2.5.2 变压精馏
一般来说,若压力变化明显影响共沸组成,则可采用两个不同压力操作的双塔流程,不添加共沸剂,可实现二元混合物的完全分离。变压精馏是通过改变系统压力来改变体系共沸组成的特殊精馏方法,常用来分离均相共沸物。变压精馏与其他几种精馏方式相比,其优点在于避免引入和回收共沸剂。对于具有正偏差共沸物的稳态过程,变压精馏流程包括加压精馏塔和低压精馏塔,两塔塔顶的正偏差共沸物互相引入对方塔内进行分离,形成循环流,从两塔的塔底得到目标产物。
例2-14 变压精馏——分离乙醇和苯。
已知乙醇和苯生成均相共沸物,因其共沸组成受压力影响明显,可以不添加共沸剂,采用常压和1333kPa双压精馏方法进行分离。若进料流率为100kmol/h,含乙醇0.35(摩尔分数),压力1450kPa,温度165℃。分离后乙醇产品纯度为0.99(摩尔分数)和苯产品纯度0.99(摩尔分数)。要求:(1)设计双压精馏流程实现该物系的分离;(2)确定各产品的流率和循环物料的流率。
解 解题思路:应用软件的相图绘制功能,绘制两个压力下的汽液平衡相图,根据不同压力下的共沸点数据以及进料组成,设计双压精馏流程。选用“RadFrac”模块进行精馏模拟,两塔的理论塔板数和进料位置可由经验初步确定,然后根据分离要求,依据能耗最小的原则,采用软件的优化功能确定理论塔板数和进料位置的准确值。
① 全局性参数设置 计算类型“Flowsheet”,输入乙醇与苯。乙醇与苯是互溶的,可以选用WILSON方程计算液相的非理想性;又因加压操作,可选择Radlish-Kwong方程计算汽相的非理想性,故最终选择“WILS-RK”性质方法,确认WILSON方程的二元交互作用参数。
② 绘制相图 点击“Tools|Analysis|Property|Binary”工具条,打开绘制相图窗口,在“Analysis type”栏目下选择“T-xy”,表示绘制温度-组成图。在“Pressure”栏目下选择“List of values”,在空格内填写两个压力值,点击“Go”按钮,软件绘制出乙醇与苯在两个压力下的温度-组成图,把进料和两个共沸点名称标绘到图上,如图2-103所示。依据相图分析和均相共沸精馏原理,只能在高压塔输入原料,高压塔塔顶共沸物D1作为低压塔的进料,低压塔塔顶共沸物D2返回到高压塔,由此构成循环。在高压塔塔釜得到纯苯,在低压塔塔釜得到纯乙醇。这样,不添加共沸剂,采用双塔双压精馏,可以实现乙醇与苯均相共沸物的分离。

图2-103 乙醇与苯温度-组成图
D1—高压塔塔顶共沸物;D2—低压塔塔顶共沸物
③ 绘制流程图 根据相图分析,设计双塔双压精馏分离乙醇与苯共沸物的流程,如图2-104所示。因为两塔压差太大,操作温度相差亦很大。低压塔塔顶共沸物进入高压塔之前需要升压升温,高压塔塔顶共沸物进入低压塔之前需要降温,因此在流程图上增设了两个换热器和一台增压泵。
为使两塔模块参数设置准确性好一些,可以用题目数据、相图数据及分离要求进行初步的物料衡算。

图2-104 双压共沸精馏分离乙醇与苯流程
对两塔作物料衡算:F=B+E
对乙醇作物料衡算:0.35F=0.01B+0.99E
合并两式解出:E=34.69kmol/h;B=65.31kmol/h
对低压塔作总物料衡算:D1=D2+E
对低压塔乙醇作物料衡算:0.7244D1=0.4537D2+0.99E
合并两式解出:D2=34.04kmol/h;D1=68.73kmol/h。
以上物料衡算求得的E、B、D1、D2四个物流点流率数据,可用于图2-104分离过程的参数设置与调整。
④ 设置流股信息 把题目给定的进料物流信息填入对应栏目中。进料物流压力应该高于高压塔的操作压力,设为1450kPa,液相进料。
⑤ 设置模块信息 “B1”模块:在“Setup”文件夹中,有3个页面需要填写。设理论板数30,全凝器,收敛模式选择共沸精馏“Azeotropic”。暂定摩尔回流比为2,后用“Sensitivity”功能确定。暂定摩尔蒸发比为4,后用“Design Specs”功能确定。B2塔顶共沸物与原料混合后从第26板进入,合适的进料位置用“Sensitivity”功能确定。塔顶压力1333kPa,设每块塔板压降1kPa。“B1”模块“Configuration” 页面的填写如图2-105所示。

图2-105 高压塔“Configuration”页面参数填写
为保证塔釜物流中苯的摩尔分数达到0.99,可以使用软件的反馈计算功能“Design Specs”调整塔釜的摩尔蒸发比。在“B1”模块的“Design Specs”文件夹中建立一个反馈计算指标控制文件“1”;在其“Specifications”页面填写塔釜物流中苯的浓度控制指标,在“Components”页面填写苯的组分代号,在“Feed/Product Streams”页面填写苯的物流代号。在“Specifications”页面的填写方式如图2-106(a)所示。然后,在“B1”模块的“Vary”文件夹中建立一个操作参数变化文件“1”;在其“Specifications”页面填写满足塔釜物流中苯浓度控制指标的塔釜摩尔蒸发比的变化范围,如图2-106(b)所示。

图2-106 调整塔釜摩尔蒸发比控制塔釜物流中苯浓
为选择合适的进料位置,在控制塔釜物流中苯浓度0.99(摩尔分数)时,用“Sensitivity”功能计算不同进料位置所需要的塔釜热负荷。在“Model Analysis Tools|Sensitivity”页面,建立一个灵敏度分析文件“S-1”;在“S-1|Input|Define”页面,定义“B1”模块塔釜热负荷为QN1,见图2-107(a);在“S-1|Input|Vary”页面,设置进料塔板位置范围和考察步长,见图2-107(b);在“S-1|Input|Tabulate”页面,设置输出不同进料位置的塔釜热负荷数据。

图2-107 考察不同进料位置的塔釜热负荷
由全系统物料衡算,D1流率为68.73kmol/h。在控制塔釜物流中苯浓度0.99(摩尔分数)条件下,不同的回流比会导致不同的塔顶共沸物浓度和不同的共沸物流率。合适的回流比应该使得“B1”模块的塔顶共沸物浓度和流率接近相图值和物料衡算值,这可以用“Sensitivity”功能筛选获得。
在“Model Analysis Tools|Sensitivity”页面,建立一个灵敏度分析文件“S-2”;在“Input |Define”页面,定义“XD1”为“B1”模块塔顶共沸物D1中的乙醇摩尔分数,见图2-108(a);定义“WD1”为“B1”模块塔顶共沸物D1的摩尔流率,见图2-108(b);在“Input|Vary”页面,设置回流比考察范围和考察步长,见图2-108(c)。

图2-108 筛选“B1”模块的回流比
“B2”模块:在“Setup”文件夹中,有3个页面需要填写。设理论板数20,全凝器,收敛模式选择共沸精馏“Azeotropic”。暂定摩尔回流比为1,然后用“Sensitivity”功能确定。暂定摩尔蒸发比为2,然后用“Design Specs”功能确定。B1塔顶共沸物冷凝冷却到72℃后从第14板进入,合适的进料位置用“Sensitivity”功能确定。塔顶压力101.3kPa,设每块塔板压降1kPa。“B2”模块“Configuration”页面的填写如图2-109所示。“B2”模块塔釜物流中乙醇浓度控制和回流比筛选方法与“B1”模块相同,此处不再赘述。

图2-109 低压塔“Configuration” 页面参数填写
“B3”混合器模块:选择液相混合“Liquid-only”。
“B4”冷却器模块:设置出口温度72℃,与B2塔进料塔板温度相当;设置冷却器估计压降50kPa,有效相态是液相。
“B5”加热器模块:设置出口温度165℃,与B1塔进料塔板温度相当;设置加热器估计压降50kPa,有效相态是液相。
“PUMP”模块:设置出口压力1500kPa。
为加快流程模拟收敛,在“Convergence|Tear”页面,把流程中的循环物流“RECYC”设置为撕裂流。
⑥ 模拟计算 计算收敛后观察模拟结果。首先选择两塔合适的回流比。在用“Design Specs”功能控制两塔塔釜产品纯度一定的前提下,合适的回流比应该使得两塔塔顶共沸物浓度和流率接近相图共沸点值和全系统的物料衡算值。由“Sensitivity”功能计算的不同回流比下塔顶共沸物浓度分布见图2-110。由图可见,高压塔和低压塔合适的回流比分别为2.05和0.8,此时两塔塔顶乙醇浓度与相图共沸点D1和D2值接近。其次确定两塔合适的进料位置。由“Sensitivity”功能计算出的两塔进料位置与塔釜热负荷的关系见图2-111,可见“B1”模块和“B2”模块合适的进料位置分别是26和14,此时的两塔塔釜热负荷最小。

图2-110 不同回流比下的塔顶共沸物浓度

图2-111 不同进料位置对应的塔釜热负荷
最后确定两塔的蒸发比。把两塔回流比分别修改为2.05和0.8,两塔进料位置修改为26和14,由“Design Specs”功能计算得到两塔的蒸发比分别为3.91和1.58。全流程计算结果见图2-112,可见高压塔塔釜苯摩尔分数0.99,低压塔塔釜乙醇摩尔分数0.99,均达到分离要求,两塔塔釜出料流率与全系统物料衡算结果相符。

图2-112 双塔双压精馏系统模拟结果
2.5.3 非均相共沸精馏
分离非均相共沸物只需把汽相共沸物冷凝即可分成两个液相,从而越过了y-x相图上平衡线与对角线的交点,不必加入共沸剂即可把混合物完全分离。故非均相共沸精馏过程最少包含两个塔,分别处理液液分相器的两个液相回流。
例2-15 非均相共沸精馏分离正丁醇水溶液。
用双塔非均相共沸精馏方法实现含水正丁醇的脱水。原料含水0.28(摩尔分数),流率5000kmol/h,压力1.1atm,进料汽相分率0.3。要求产品正丁醇中含正丁醇0.96(摩尔分数),外排水相中含水0.995(摩尔分数)。常压操作,饱和液体回流,两塔均采用再沸器加热,丁醇塔理论塔板数9,水塔理论塔板数4。求:(1)产品流率;(2)丁醇塔最佳进料位置;(3)两塔再沸器能耗。
解 解题思路:利用软件的相图绘制功能,绘制常压下正丁醇-水汽液平衡相图,根据共沸点数据以及进料组成,设计双塔精馏流程。两塔的进料位置可依据经验初步确定,然后依据能耗最小原则,采用软件的优化功能确定准确值。
① 全局性参数设置 计算类型“Flowsheet”,输入正丁醇与水。正丁醇与水是部分互溶,选用“NRTL”性质方法,确认NRTL方程的二元交互作用参数。
② 绘制相图 点击“Tools|Analysis|Property|Binary”工具条,打开绘制相图窗口,在“Analysis type”栏目下选择“T-xy”,在“Vlid phases”栏目下选择“Vapor-liquid-liquid”,表示绘制温度-汽液液组成相图。单击“Go”按钮,软件绘制相图见图2-113(a),在常压下,正丁醇与水是部分互溶,三相平衡温度为92.5℃。共沸点把汽液平衡包络线分成两个区域,左侧是水相蒸馏区域,右侧是正丁醇相蒸馏区域,可设计两塔分离流程完成正丁醇脱水任务。在正丁醇塔加入原料,塔顶共沸物冷凝后分相,有机相含正丁醇0.56(摩尔分数),回流到正丁醇塔塔顶;水相含正丁醇0.025(摩尔分数),作为水塔进料回流到水塔塔顶。两塔均无冷凝器,合用一个外置冷凝器为两塔汽相冷凝,合用一个外置分相器为两塔汽相冷凝液分相。由正丁醇塔塔釜得到提纯的正丁醇,由水塔塔釜得到废水外排。这样,不加共沸剂,采用双塔精馏,实现非均相共沸物的分离。

图2-113 正丁醇脱水分离流程分析
③ 绘制模拟流程图 根据相图分析,设计双塔精馏分离正丁醇与水的模拟流程,见图2-11(b),液液分相器的水相入水塔第1塔板,有机相入正丁醇塔第1塔板。为了给两塔模拟结果的判断提供参考,可以用题给数据及分离要求进行初步的物料衡算。
对两塔作总物料衡算:FEED = BUT + WAT
对两塔的水作物料衡算:0.28FEED = 0.04BUT + 0.995WAT
合并两式解出:BUT=3743.5kmol/h(B1塔釜出料);WAT=1256.5kmol/h(B2塔釜出料)
④ 设置流股信息 把题目给定的物流信息填入对应栏目中。
⑤ 设置模块信息 “B1”模块:在“Setup”文件夹中,有3个页面需要填写。理论板数9,无冷凝器,共沸精馏方式收敛,其中“Configuration” 页面参数填写如图2-114(a)所示。暂定摩尔蒸发比为0.5,然后用“Design Specs”功能根据塔釜产品中丁醇含量0.96(摩尔分数)确定塔釜摩尔蒸发比准确值,页面参数填写如图2-114(b),“Vary”页面参数填写如图2-114(c)。由于没有冷凝器,分相器有机相回流从第1板进入,原料暂时从第2板进入,塔顶压力1atm,设全塔压降9kPa。在“Estimates|Temperature”页面,设置塔顶、塔底的温度估计值分别为95℃和115℃。

图2-114 丁醇塔部分页面参数填写
“B2”模块:在“Setup”文件夹中,有3个页面需要填写。理论板数4,无冷凝器,共沸精馏方式收敛,其中“Configuration”页面填写如图2-115所示。暂定摩尔蒸发比为0.05,然后用“Design Specs”功能根据塔釜物流中水含量0.995(摩尔分数)确定塔釜摩尔蒸发比准确值。由于没有冷凝器,分相器水相回流从第1板进入。塔顶压力1atm,设全塔压降4kPa。在“Estimates|Temperature”页面,设置塔顶塔底的温度估计值分别为95℃和100℃。

图2-115 水塔“Configuration”页面填写
“HEATER”模块:在“Input|Specification”页面,设置汽相冷凝,压力1atm。
“DECANTER”模块:在“Input|Specification”页面,设置压力1atm,绝热分相,指定返回丁醇塔顶液相的关键组分为正丁醇。在“Block Options|Properties”页面,选择分相器物流的性质方法为“NRTL-2”,见图2-116(a);选择源于LLE的NRTL方程二元交互作用参数,见图2-116(b)。为加快收敛,在“Convergence|Tear”页面,把模拟流程中的循环物流“REF1”和“REF2”设置为撕裂流。

图2-116 设置分相器性质方法
⑥ 模拟计算 结果见图2-117,丁醇塔釜液中正丁醇摩尔分数0.96,水塔釜液中水摩尔分数0.995,均达到分离要求,两塔塔釜出料流率与全系统物料衡算结果相符。由计算结果还可看到,丁醇塔塔釜蒸发比为0.586,塔釜热负荷为27.4MW,水塔塔釜蒸发比为0.073,塔釜热负荷为1.21MW。

图2-117 正丁醇脱水双塔精馏系统模拟计算结果
⑦ 求B1塔最佳进料位置 图2-117的计算结果是基于丁醇塔暂时指定的进料位置而得到的,准确的进料位置应该是满足分离要求前提下使塔釜热负荷最小,可通过“Sensitivity”功能确定。
在“Model Analysis Tools|Sensitivity”页面,建立一个灵敏度分析文件“S-1”,定义B1塔的塔釜热负荷为“Q”,见图2-118(a),设置进料位置搜索范围为1~7塔板,步长1,见图2-118(b),在“Tabulate”页面设置“Q”输出,计算结果见图2-118(c),可见在第5塔板进料,塔釜热负荷最小,为19.06MW,与第2塔板进料比较,塔釜热负荷降低30.5%。

图2-118

图2-118 丁醇塔最佳进料位置
2.5.4 反应器与精馏塔的组合流程
在化工流程中经常看到反应器与精馏塔的组合流程,反应混合物经精馏塔分离后,未反应的原料返回反应器入口,形成循环流。
在以二氯乙烷裂解制氯乙烯的工艺中,二氯乙烷热裂解生成氯乙烯反应是强烈的吸热反应,反应式为:ClCH2CH2Cl → CH2=CHCl+HCl。裂解产物进入淬冷器,以避免继续发生副反应。产物温度冷却到50~150℃后,进入脱氯化氢塔。塔底为氯乙烯和二氯乙烷的混合物,通过氯乙烯精馏塔精馏,由塔顶获得高纯度氯乙烯,塔底重组分主要为未反应的粗二氯乙烷,经精馏除去不纯物后,仍作热裂解原料返回二氯乙烷热裂解反应器继续反应。
例2-16 二氯乙烷裂解制氯乙烯组合流程——循环流Fortran语言应用。
已知某装置二氯乙烷进料流率2000kmol/h,21.1℃,压力2.7MPa。裂解温度500℃,压力2.7MPa。淬冷器压降0.35bar,过冷5℃。脱氯化氢塔操作压力2.53MPa,氯乙烯精馏塔操作压力0.793MPa,要求精馏产物氯化氢和氯乙烯的摩尔分数均大于0.998。当二氯乙烷单程转化率在0.50~0.55范围内变化时,求裂解反应器、淬冷器、精馏塔设备热负荷(Q)的变化。
解 ① 全局性参数设置 计算类型“Flowsheet”,输入二氯乙烷、氯化氢、氯乙烯三个组分。本例涉及高温高压气相反应,选择“RK-SOVAE”性质方法。
② 画流程图 按题目信息绘制模拟流程,如图2-119所示,两塔采用“RadFrac”模块,把进料物流信息填入对应栏目中。

图2-119 带循环的二氯乙烷裂解流程
③ 设置模块信息 规定二氯乙烷单程转化率0.55,脱氯化氢塔(TOWER1)理论塔板数17,进料位置8,回流比1.082,塔顶摩尔出料比0.354。氯乙烯精馏塔(TOWER2)理论塔板数12,进料位置7,回流比0.969,塔顶摩尔出料比0.55。
④ 模拟计算 计算结果见图2-120,二氯乙烷单程转化率0.55时,二氯乙烷裂解流程产物氯化氢、氯乙烯的摩尔分数均大于0.998,达到分离要求,氯化氢的摩尔收率0.998,氯乙烯的摩尔收率1.0。

图2-120 带循环的二氯乙烷裂解计算结果
⑤ 考察转化率在0.50~0.55范围内变化时设备热负荷的变化 在“Model Analysis Tools|Sensitivity”页面,建立一个灵敏度分析文件“S-1”,定义四个因变量分别为“DUTY1”、“DUTY2”、“DUTY3”、“DUTY4”,分别代表反应器、淬冷器、精馏塔1、精馏塔2的热负荷,如图2-121所示。自变量为反应转化率,在“Vary”页面填写,见图2-122,设置转化率的变化范围0.50~0.55,计算步长为0.01。

图2-121 建立灵敏度分析文件

图2-122 定义自变量转化率的变化范围及计算步长
在“Tabulate” 页面填写灵敏度分析结果的输出格式。在“Fortran”页面编写一句Fortran语言,计算四台设备总热负荷,如图2-123所示,因为淬冷器的热负荷是负值,故在求和时用绝对值参与计算,模拟计算结果见图2-124。

图2-123 计算四台设备总热负荷

图2-124 二氯乙烷裂解流程灵敏度分析计算结果
由图2-124(a)可以看出,当二氯乙烷转化率从0.50提高到0.55时,反应器、淬冷器的热负荷增加,两精馏塔的热负荷降低;各设备总热负荷随二氯乙烷转化率的变化趋势见图2-124(b),可见总热负荷随二氯乙烷转化率提高而增加。
2.5.5 吸收塔、解吸塔与换热器的组合流程
在化工过程中,吸收塔与解吸塔往往成对出现。吸收塔在加压、相对低温下操作,解吸塔在常压或低压、加热或蒸汽汽提状态下操作。为降低解吸塔能耗,通常用解吸塔塔釜再生后的吸收剂预热解吸塔进料,这样就产生了物料循环与换热的组合流程。
例2-17 轻烃气体吸收、解吸与换热组合流程——Calculator+Sensitivity综合应用。
拟用正十二烷为吸收溶剂,对原料气中的烃类组分进行吸收分离,原料气组成见例2-17附表,吸收和解吸组合流程如图2-125所示。吸收塔塔顶压力1.013MPa,解吸塔塔顶常压,溶剂进塔温度25℃,吸收塔和解吸塔均为10块理论板。要求异丁烷的吸收率为0.9。求:(1)两塔塔顶汽相流率与组成;(2)循环溶剂量和补充溶剂量;(3)解吸塔再沸器、换热器和冷却器热负荷。
例2-17附表 吸收塔原料气组成 单位:kmol/h


图2-125 轻烃气体吸收和解吸组合流程
解 ① 全局性参数设置 计算类型“Flowsheet”,输入例2-17附表中原料气组分和吸收溶剂正十二烷,本例均为烃类组分,选择“CHAO-SEA”性质方法。
② 吸收塔模拟 吸收塔C1选用“RadFrac”模块,进料气体组成按例2-17附表数据输入,吸收溶剂暂时按40kmol/h输入,后由软件的设计规定功能修正。在C1塔的“Setup”文件夹,有3个页面需要填写。在“Configuration”页面,填写理论级数10,无冷凝器无再沸器;在“Convergence”栏目选择“Custom”;在“Streams”页面,填写溶剂从第1板进,气体从第11板进;在“Pressures” 页面,填写塔顶1.013MPa,全塔压降7kPa。在“Convergence|Advanced”页面的“Absober”栏目内选择“Yes”,说明C1塔是吸收塔。为协助软件迭代计算收敛,在“Estimates|Temperature”页面,填写塔顶的温度估计值25℃,塔底的温度估计值50℃。
进料气体中异丁烷的流率2.5kmol/h,要求吸收率0.9,塔顶吸收尾气V1物流中异丁烷的流率应该不高于0.25kmol/h。在“Flowsheeting Options|Design Specs”子目录,建立一个反馈计算文件“DS-1”。给考察变量(塔顶吸收尾气V1物流中异丁烷的流率) 取名“WC4”,见图2-126(a)。对因变量设置收敛要求和容许误差,即V1物流中异丁烷的流率0.25kmol/h,允许误差1×10−4kmol/h,如图2-126(b)所示;设定吸收溶剂添加量范围40~60kmol/h,见图2-126(c);单塔计算结果如图2-126(d)所示。当吸收溶剂添加量为46.9kmol/h时,由图2-126(d)可知,塔顶吸收尾气V1中异丁烷的流率为0.25kmol/h,吸收率达到0.9,满足分离要求。为了减少后续计算量,把进料溶剂流率改为46.9kmol/h,同时把反馈计算文件“DS-1”隐藏。

图2-126 轻烃气体吸收塔计算结果
③ 解吸塔模拟 解吸塔C2选用带再沸器的“RadFrac”模块,在C2塔的“Setup| Configuration”页面,填写理论级数10,无冷凝器,有再沸器;在“Convergence”栏目,收敛方法选择“Petroleum/Wide-boiling”,说明解吸塔是宽沸程体系,软件将采用流率加和法(Sum-Rates)进行收敛计算;在“Operating Specifications”栏目,填写塔釜热负荷估计值1MW,见图2-127(a),其准确值用软件的设计规定功能计算。在“Streams”页面,填写物料从第1板进;在“Pressures”页面,填写塔顶0.1013MPa,全塔压降7kPa。在“Convergence|Basic”页面,把流率加和法最大迭代次数从默认的25次修改为50次。为协助软件迭代计算收敛,在“Estimates| Temperature”页面,填写塔顶的温度估计值120℃,塔底的温度估计值220℃。

图2-127 解吸塔模拟结果
C2塔的任务是把吸收液中的轻烃组分尽量解吸出来,其中最难解吸的是分子量最大的正己烷,其解吸率与塔釜热负荷有关,可以用软件的设计规定功能确定。在C2塔的“Design Specs”子目录,建立一个反馈计算文件“1”,在“Specifications”页面,规定C2塔釜液中正己烷的浓度0.001(摩尔分数),在“Components”页面,选择考察组分正己烷;在“Feed/Product Streams”页面,指定考察物流是“BOT2”。在“Vary”子目录,建立一个反馈计算文件“1”,在“Specifications”页面,规定调节变量是塔釜热负荷,变化范围1~10MW。单塔反馈计算结果见图2-127(b),C2塔釜液中正己烷浓度已降低到0.001(摩尔分数)。
④ 补充溶剂损耗 由于两塔塔顶都有一定数量的溶剂损耗,在建立溶剂循环流程时,需要对两塔塔顶物流带出的溶剂进行补充,这可由软件的计算器功能“Calculator”完成。在“Flowsheeting Options|Calculator”子目录,点击“New”按钮,建立一个计算器对象文件“C-1”,在“Input|Define”页面,定义3个全局性计算变量,见图2-128(a),其中“FMAKE”表示需要补充的吸收溶剂流率,“FV1”和“FV2”分别表示两塔塔顶物流带出的溶剂流率,“FV1”和“FV2”是输入变量,“FMAKE”是输出变量,“FMAKE”的定义方法见图2-128(b),“FV1”与“FV2”定义方法类似。“FMAKE”是“FV1”与“FV2”之和,计算语句见图2-128(c)。

图2-128 建立溶剂循环流程
⑤ 冷却器与增压泵设置 设置循环吸收溶剂冷却器出口温度25℃,压降30kPa;增压泵出口压力1.02MPa。
⑥ 换热器设置 为了节省能耗,把C2塔釜高温循环溶剂物流BOT2与C1塔釜物流BOT1换热,以提高BOT1的进塔温度,降低C2塔再沸器加热能耗。换热器“HEAT”采用简捷计算,在“Setup|Specifications”页面,设置冷流体的出口温度135℃,压降30kPa。
为了协助软件运算收敛,在“Convergence|Tear”页面,把循环溶剂物流“RECYC”设置为撕裂流;在“Convergence|Conv Options|Defaults|Default Methods”页面,把撕裂流的收敛方法改为“Broyden”;在“Convergence|Conv Options|Methods|Broyden”页面,把最大迭代次数改为100。
⑦ 模拟计算 全循环流程计算结果见图2-129,吸收塔塔顶尾气V1物流中异丁烷流率0.248kmol/h,吸收率≥0.9。因BOT1物流在C2塔顶进料,进料温度提高会增加溶剂的损耗,吸收溶剂损耗从换热之前的0.076kmol/h增加到1.222kmol/h。解吸塔再沸器热负荷从换热之前的1.10MW下降到0.60MW,降低了45.5%。换热器“HEAT”热负荷为0.54MW,此即为回收的热量。冷却器“COOL”热负荷从换热之前的1.11MW减少到0.55MW,减少了50.5%。

图2-129 含冷热流股换热的吸收和解吸组合流程计算结果