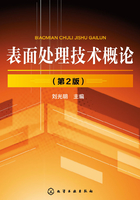
1.1 表面技术的分类和内容
(1)表面技术分类
表面技术有着十分广泛的内容,仅从一个角度进行分类难以概括全面,目前也没有统一的分类方法,我们可以从不同角度进行分类。
①按具体表面技术方法划分。包括表面热处理、化学热处理、物理气相沉积、化学气相沉积、离子注入、电子束强化、激光强化、火焰喷涂、电弧喷涂、等离子喷涂、爆炸喷涂、静电喷涂、流化床涂敷、电泳涂装、堆焊、电镀、电刷镀、自催化沉积(化学镀)、热浸镀、化学转化、溶胶-凝胶技术、自蔓延高温合成、搪瓷等。每一类技术又进一步细分为多种方法,例如火焰喷涂包括粉末火焰喷涂和线材火焰喷涂,粉末喷涂又有金属、陶瓷和塑料粉末喷涂等。
②按表面层的使用目的划分。大致可分为表面强化、表面改性、表面装饰和表面功能化四大类。表面强化又可以分为热处理强化、机械强化、冶金强化、涂层强化和薄膜强化等,着重提高材料的表面硬度、强度和耐磨性;表面改性主要包括物理改性、化学改性、三束(激光、电子束和离子束)改性等,着重改善材料的表面形貌以及提高其表面耐腐蚀性能;表面装饰包括各种涂料涂装和精饰技术等,着重改善材料的视觉效应并赋予其足够的耐候性;表面功能化则是指使表面层具有上述性能以外的其他物理化学性能,如电学性能、磁学性能、光学性能、敏感性能、分离性能、催化性能等。
③按表面层材料的种类划分。一般分为金属(合金)表面层、陶瓷表面层、聚合物表面层和复合材料表面层四大类。许多表面技术都可以在多种基体上制备多种材料表面层。如热喷涂、自催化沉积、激光表面处理、离子注入等;但有些表面技术只能在特定材料的基体上制备特定材料的表面层,如热浸镀。不过,并不能据此判断一种表面技术的优劣。
④从材料科学的角度,按沉积物的尺寸进行,表面工程技术可以分为以下四种基本类型。
a.原子沉积。以原子、离子、分子和粒子集团等原子尺度的粒子形态在基体上凝聚,然后成核、长大,最终形成薄膜。被吸附的粒子处于快冷的非平衡态,沉积层中有大量结构缺陷。沉积层常和基体反应生成复杂的界面层。凝聚成核及长大的模式,决定着涂层的显微结构和晶型。电镀、化学镀、真空蒸镀、溅射、离子镀、物理气相沉积、化学气相沉积、等离子聚合、分子束外延等均属此类。
b.颗粒沉积。以宏观尺度的熔化液滴或细小固体颗粒在外力作用下于基体材料表面凝聚、沉积或烧结。涂层的显微结构取决于颗粒的凝固或烧结情况。热喷涂、搪瓷涂敷等都属此类。
c.整体覆盖。欲涂覆的材料于同一时间施加于基体表面。如包箔、贴片、热浸镀、涂刷、堆焊等。
d.表面改性。用离子处理、热处理、机械处理及化学处理等方法处理表面,改变材料表面的组成及性质。如化学转化镀、喷丸强化、激光表面处理、电子束表面处理、离子注入等。
(2)表面技术的主要内容
表面技术内容种类繁多,随着科技不断发展,新的技术也不断涌现,下面仅就一些常见的表面技术做简单介绍。
①电镀与电刷镀 利用电解作用,使具有导电性能的工件表面作为阴极与电解质溶液接触,通过外电流的作用,在工件表面沉积与基体牢固结合的镀覆层。该镀覆层主要是各种金属和合金。单金属镀层有锌、镉、铜、镍、铬、锡、银、金、钴、铁等数十种;合金镀层有锌-铜、镍-铁、锌-镍等一百多种。电镀方式也有多种,有槽镀如挂镀、吊镀、滚镀、刷镀等。电镀在工业上应用很广泛。电刷镀是电镀的一种特殊方法,又称接触镀、选择镀、涂镀、无槽电镀等。其设备主要由电源、刷镀工具(镀笔)和辅助设备(泵、旋转设备等)组成,是在阳极表面裹上棉花或涤纶棉絮等吸水材料,使其吸饱镀液,然后在作为阴极的零件上往复运动,使镀层牢固沉积在工件表面上。它不需将整个工件浸入电镀溶液中,所以能完成许多槽镀不能完成或不容易完成的电镀工作。
②化学镀 是在无外电流通过的情况下,利用还原剂将电解质溶液中的金属离子化学还原在呈活性催化的工件表面,沉积出与基体牢固结合的镀覆层。工件可以是金属,也可以是非金属。镀覆层主要是金属和合金,最常用的是镍和铜。
③涂装 它是用一定的方法将涂料涂覆于工件表面而形成涂膜的全过程。涂料(俗称漆)为有机混合物,一般由成膜物质、颜料、溶剂和助剂组成,可以涂装在各种金属、陶瓷、塑料、木材、水泥、玻璃等制品上。涂膜具有保护、装饰或特殊性能(如绝缘、防腐标志等),应用十分广泛。
④堆焊和熔结 堆焊是在金属零件表面或边缘熔焊上耐磨、耐蚀或特殊性能的金属层,修复外形不合格的金属零件及产品,提高使用寿命,降低生产成本,或者用它制造双金属零部件。熔结与堆焊相似,也是在材料或工件表面熔敷金属涂层,但用的涂敷金属是一些以铁、镍、钴为基,含有强脱氧元素硼和硅而具有自熔性和熔点低于基体的自熔性合金,所用的工艺是真空熔敷、激光熔敷和喷熔涂敷等。
⑤热喷涂 它是将金属、合金、金属陶瓷材料加热到熔融或部分熔融,以高的动能使其雾化成微粒并喷至工件表面,形成牢固的涂覆层。热喷涂的方法有多种,按热源可分为火焰喷涂、电弧喷涂、等离子喷涂(超音速喷涂)和爆炸喷涂等。经热喷涂的工件具有耐磨、耐热、耐蚀等功能。
⑥电火花涂敷 这是一种直接利用电能的高密度能量对金属表面进行涂敷处理的工艺,即通过电极材料与金属零部件表面间的火花放电作用,把作为火花放电极的导电材料(如WC、TiC)熔渗于零件表面层,从而形成含电极材料的合金化涂层,提高工件表层的性能,而工件内部组织和性能不改变。
⑦热浸镀 它是将工件浸在熔融的液态金属中,使工件表面发生一系列物理和化学反应,取出后表面形成金属镀层。工件金属的熔点必须高于镀层金属的熔点。常用的镀层金属有锡、锌、铝、铅等。热浸镀工艺包括表面预处理、热浸镀和后处理三部分。按表面预处理方法的不同,它可分为熔剂法和保护气体还原法。热浸镀的主要目的是提高工件的防护能力,延长使用寿命。
⑧真空蒸镀 它是将工件放入真空室,并用一定方法加热镀膜材料,使其蒸发或升华,飞至工件表面凝聚成膜。工件材料可以是金属、半导体、绝缘体乃至塑料、纸张、织物等;而镀膜材料也很广泛,包括金属、合金、化合物、半导体和一些有机聚合物等。加热镀膜材料方式有电阻、高频感应、电子束、激光、电弧加热等。
⑨溅射镀 它是将工件放入真空室,并用正离子轰击作为阴极的靶(镀膜材料),使靶材中的原子、分子逸出,飞至工件表面凝聚成膜。溅射粒子的动能约10eV,为热蒸发粒子的100倍。按入射正离子来源不同,可分为直流溅射、射频溅射和离子束溅射。入射正离子的能量还可用电磁场调节,常用值为10eV能量。溅射镀膜的致密性和结合强度较好,基片温度较低,但成本较高。
离子镀 它是将工件放入真空室,并利用气体放电原理将部分气体和蒸发源(镀膜材料)逸出的气相粒子电离,在离子轰击工件的同时,把蒸发物或其反应产物沉积在工件表面成膜。该技术是一种等离子体增强的物理气相沉积,镀膜致密,结合牢固,可在工件温度低于550℃时得到良好的镀层,绕镀性也较好。常用的方法有阴极电弧离子镀、热电子增强电子束离子镀、空心阴极放电离子镀。
化学气相沉积(简称CVD) 它是将工件放入密封室,加热到一定温度,同时通入反应气体,利用室内气相化学反应在工件表面沉积成膜。源物质除气态外,也可以是液态和固态。所采用的化学反应有多种类型,如热分解、氢还原、金属还原、化学输运反应、等离子体激发反应、光激发反应等。工件加热方式有电阻、高频感应、红外线加热等。主要设备有气体的发生、净化、混合、输运装置,以及工件加热、反应室、排气装置。主要方法有热化学气相沉积、低压化学气相沉积、等离子体化学气相沉积、金属有机化合物气相沉积、激光诱导化学气相沉积等。
化学转化膜 化学转化膜的实质是金属处在特定条件下人为控制的腐蚀产物,即金属与特定的腐蚀液接触并在一定条件下发生化学反应,形成能保护金属不易受水和其他腐蚀介质影响的膜层。它是由金属基体直接参与成膜反应而生成的,因而膜与基体的结合力比电镀层要好得多。目前工业上常用的有铝和铝合金的阳极氧化、铝和铝合金的化学氧化、钢铁氧化处理、钢铁磷化处理、铜的化学氧化和电化学氧化、锌的铬酸盐钝化等。
化学热处理 它是将金属或合金工件置于一定温度的活性介质中保温,使一种或几种元素渗入它的表层,以改变其化学成分、组织和性能的热处理工艺。按渗入的元素可分为渗碳、渗氮、碳氮共渗、渗硼、渗金属等。渗入元素介质可以是固体、液体和气体,但都要经过介质中化学反应、外扩散、相界面化学反应(或表面反应)和工件中扩散四个过程。
高能束表面处理 它是主要利用激光、电子束和太阳光束作为能源,对材料表面进行各种处理,显著改善其组织结构和性能。
离子注入表面改性 它是将所需的气体或固体蒸气在真空系统中电离,引出离子束后在数千电子伏至数十万电子伏加速下直接注入材料,达一定深度,从而改变材料表面的成分和结构,达到改善性能之目的。其优点是注入元素不受材料固溶度限制,适用于各种材料,工艺和质量易控制,注入层与基体之间没有不连续界面。它的缺点是注入层不深,对复杂形状的工件注入有困难。
目前,表面技术领域的一个重要趋势是综合运用两种或更多种表面技术的复合表面处理技术。随着材料使用要求的不断提高,单一的表面技术因有一定的局限性而往往不能满足需要。目前已开发的一些复合表面处理,如等离子喷涂与激光辐照复合、热喷涂与喷丸复合、化学热处理与电镀复合、激光淬火与化学热处理复合、化学热处理与气相沉积复合等,已经取得良好效果。
另外,表面加工技术也是表面技术的一个重要组成部分。例如对金属材料而言,有电铸、包覆、抛光、蚀刻等,它们在工业上获得了广泛的应用。