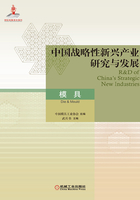
1.2 模具产业是高端装备制造业的重要组成部分
1.2.1 模具技术是精密成形技术的重要组成部分
随着模具成形工艺的不断发展(如自动化冲压、高速多工位级进冲压,智能注射、多料多色注射等工艺),模具被赋予的功能也越来越多(如模内转印、模内装配等技术),致使模具结构越来越复杂,模具制造精度和模具可靠性(性能、寿命等)要求越来越高,这就要求模具的设计、制造及质量控制的技术参数必须与涉及制件(零部件)的材料、成形工艺、成形设备(机床)和控制系统进行协同确定。因此,模具的设计制造技术越来越体现出在制件、制品和零部件精密成形技术中的重要地位和作用。模具技术包括模具的设计和加工技术、装配和检测技术、材料与处理技术、使用维护技术和模具再制造技术等。
模具设计包括功能、结构、性能设计,模具主要零部件加工工艺设计,装配和试模工艺设计等。我国的模具设计技术在20世纪90年代末基本实现计算机辅助设计(CAD)、计算机辅助制造(CAM)和计算机辅助工程(CAE)的数字化设计;进入21世纪,特别是到“十二五”末,我国的模具设计CAD/CAM/CAE一体化技术基本成熟,重点骨干企业应用率达到90%以上,全三维数字设计技术应用率在70%以上。近几年,面向模具制造的服务业发展迅速,模具设计公司、云编程公司、云智造公司利用互联网技术开展网上设计服务。
我国模具零部件的加工自20世纪80年代起,逐步采用NC、CNC加工设备以替代传统的加工设备,到20世纪90年代末,关键工序的数控加工采用率在60%左右;到2010年,关键工序的数控加工采用率达到90%左右,其中三轴以上联动设备占75%左右,高速加工中心开始应用;到目前为止,关键工序的数控加工采用率达到95%左右,四轴、五轴加工的编程技术基本掌握,高速切削技术得到广泛应用。除模架、热流道等模具标准件较早就采用自动化生产线加工外,在“十一五”“十二五”期间也建成了若干模具零件自动化加工单元和生产线,如“电极自动化加工单元”“光学镜片注射模自动化加工单元”“轮胎模具花纹块自动化加工线”等。随着增材制造技术的发展,特别是金属3D打印技术的逐渐成熟,为模具制造提供了一个新的制造方法。我国已有数十家企业正在开展采用增材制造技术制造精密模具的探索并取得了有益的成果,为我国模具行业广泛应用增材制造技术打下了坚实的基础。光加工技术(主要是激光加工技术)正在被广泛用于模具的皮纹加工、极微细孔槽加工、超高强制件切边、模具表面局部强化等制造工序。放电加工、激光加工、高速切削已成为硬质(超硬质)模具加工的系列化加工技术,使得硬化至35~65HRC的模具工作部分可以直接加工到所需精度,提高了加工质量,缩短了加工周期。
三坐标测量机、白光扫描(测量)仪等高精度数字化测量仪器已经成为我国重点模具制造企业的标准配置,不仅为提高我国模具的制造精度和制造质量提供了保证,也为模具企业采用逆向工程进行产品开发和模具设计提供了必要条件。
以计算机仿真和模拟技术为基础的“虚拟试模”技术正在用于复杂模具和多工位级进冲模的设计合理性及装配精度的数字化校验,以提高物理试模的效率并降低其成本。
模具材料已从20世纪的合金钢为主,扩展至目前的钢、铸铁、铝合金、铜合金、陶瓷、石膏、可加工塑料等材料品种。目前我国模具材料年消耗量在160万t左右,其中:合金工模具钢60万t左右,铸铁30万t左右,碳素钢或低合金结构钢50万t左右。模具材料的供应由30年前的粗制毛坯逐步改为精制型材或模块。塑料模中用量最大的P20类模具钢,80%以上由钢厂提供预硬化(35~42HRC)型材或模块,减少了模具厂加工工序和各自热处理带来的质量不稳定风险;钢制模具零件的热处理已普遍采用真空热处理或保护气氛热处理工艺;精密、长寿命模具根据需要已广泛采用PVD(如氮化钛)、CVD(如碳化钛)等涂层技术、渗氮技术(或氮碳共渗技术)、激光强化技术、感应加热技术等表面处理技术,增加模具表面或局部的强度,提高耐磨性或耐(冲)蚀性,改善制件的表面质量和脱模性。
1.2.2 我国模具行业具备承担高端装备制造业的能力
模具是产品制造业生产中的重要工艺装备,是模具成形制造装备的主要组成部分,因此,模具制造属高端装备制造业。
我国的现代模具制造业经过三十多年的发展,已经从改革开放初期作为产品制造业中的辅助性部门发展成为具有研发体系,材料研制、生产、供应体系,模具标准件生产供应体系和门类齐全的模具生产体系的独立的工业部门。我国的模具生产,不但基本满足了我国制造业发展对模具的需求,而且具备了所有门类模具批量出口的能力。
(1)建立起由国家、行业和企业技术创新机构构成的模具技术研发体系 在各级政府的支持下建立起国家级模具技术创新机构,包括国家计委(1995—2000年)利用世界银行贷款建立的“精密成形国家工程研究中心”(依托单位:北京机电研究所)、“模具计算机辅助设计(CAD)国家工程研究中心”(依托单位:上海交通大学)和“橡塑模具国家工程研究中心”(依托单位:郑州大学)。国家在1990年支持建立了“材料成形与模具技术国家重点实验室”(依托单位:华中科技大学)。科技部2011年支持建立了“国家家电模具工程技术研究中心”(依托单位:海尔模具公司)。国家标准化管理委员1983年批准设立了“全国模具标准化技术委员会”(SAC/TC33,秘书处设在桂林电器科学研究院)。国家批准在广东东莞、浙江台州和江苏苏州建立了国家级“模具检测中心”。
在西安交通大学、上海交通大学、大连理工大学、合肥工业大学等著名大学建立有“模具技术研究所”。
一汽模具制造有限公司、天津汽车模具股份有限公司、青岛海尔模具有限公司、群达模具(深圳)有限公司等一大批重点骨干模具企业建立有“(工程)技术中心”,其中不少技术中心已经升级为省市级。
宁海县第一注射模具有限公司、浙江嘉仁模具有限公司等近二十家模具企业建立了“院士工作站”和“博士后工作站”。
(2)面向模具制造的现代制造服务业日趋完善 模具是结构复杂、制造精度高的特种机电产品,专业化生产是现代模具工业的内在规律和基本特征。现代模具工业的专业化生产包含两个方面:一是各种类型模具的专业化生产,如汽车覆盖件冲压模具、多工位级进冲压模具、电机铁心冲模、插接件高速多工位级进冲模、大型注射模具、精密注射模具、汽车车灯模具、轮胎模具、铝型材挤压模具、压铸模具、拉丝模具、塑料挤出模等;二是所有模具制造中材料、标准件、模具零部件的专业化生产。
我国的模具工业在党的改革开放政策指引下,通过技术的引进消化再创新和管理体制改革,到20世纪90年代中期,已彻底改变了改革开放初期国有和外资(合资)为主的单一投资模式,民营企业迅速成为投资主体和经营主力,同时完成了模具生产的专业化,实现了完全的市场化运营。到“十一五”末,我国成为世界模具制造大国和出口大国。
为了实现我国模具由制造大国向模具强国的转变,2010年工信部委托中国模具工业协会编制了《模具行业“十二五”发展规划》提出坚持推动整个行业的转型升级,在保持行业经济增长和稳定出口增长基础上,通过技术创新、发展制造服务业和加速两化融合等措施,为2020年我国模具工业进入世界强国行列打好基础。2015年,中国模具工业协会编制了《模具行业“十三五”发展指引纲要》(见附录C),提出以模具市场和存在问题为导向,以《中国制造2025》国家战略为指引,坚持推动行业发展的动能转换,大力发展知识型制造服务业,积极推进模具成形制造技术的协同创新,为实现《中国制造2025》提出的强国目标夯实基础。
经过“十二五”和“十三五”开局之年的发展,我国模具行业在完善“模具材料研制、生产、供应体系”和“模具标准件生产、供应体系”的同时,面向模具制造的知识密集型制造服务业得到快速发展,其中以北京数码大方科技股份有限公司、武汉益模科技股份有限公司为代表的数字化、信息化技术软件开发和应用的专业化公司,他们的技术起点高,行业服务涵盖面广,已经成为我国模具行业自主品牌软件开发和服务的主力;以信息技术和互联网技术为基础的“模具设计公司”“云智造公司”“云编程公司”“创客平台”和“模具精益研发服务平台”等技术服务专业公司蓬勃发展;以电子商务技术为基础的“模客网”“易模网”“精模网”等信息、交易网络化服务平台纷纷建立。知识密集型制造服务业的发展,创新了模具制造业态、优化了模具制造流程,为推动“互联网+模具制造”落实和加快模具行业的“由大转强”将继续发挥促进作用。
(3)成长起了我国的骨干模具企业队伍 现代模具行业是一个技术密集、资金密集、人才密集的行业,模具制造企业既是承载技术、资金、人才的主体,更是承担创新、运营和发展的主体。
我国的模具企业在20世纪80年代主要进行投资体制、市场化运营和专业化生产改革。20世纪90年代中期,国家对模具行业实行税收优惠政策扶持(如增值税先征后返),进一步促进了模具的专业化生产。到20世纪90年代后期,模具专业生产厂虽近3万家,但规模较小、布局分散,其中规模以上模具企业不到1000家,产业集中度低,主要模具产品为电子、电器、包装、建材、汽车行业服务。进入21世纪,在汽车制造业快速发展的拉动下,我国模具企业在经济规模、技术水平、信息化建设、品牌塑造和国际化程度等方面有了快速提升。
到2016年,我国模具企业中规模以上企业近5000家,其中被认定为高新技术企业的超过500家;由中国模具工业协会评定授牌的“中国重点骨干模具企业”达到178家,涉及汽车覆盖件模具、大型冲压模具、精密冲压模具、精密级进冲压模具、大型注射模具、精密注射模具、塑料挤出模具、铸造模具、压铸模具、电机铁心模具、子午线轮胎模具、钣金折弯模具、模具制造服务业等48类模具类型,涵盖了目前所有常用模具。它们以不到1%的企业数量,实现了全部模具销售额(产值)的20%,使我国模具产业的集中度在“十一五”末基础上提高了1倍。以模具为主业的上市公司达到40家,其中在主板、创业板上市的有近30家。目前世界上有近15类最大的模具制造企业在中国落户(如汽车覆盖件模具、汽车内饰件注射模具、塑料挤出模具、子午线轮胎模具等制造企业)。如图1-51到图1-54。

图1-51 建筑面积15.6万m2的一汽模具制造有限公司及其车身模具试模车间

图1-52 天津汽车模具股份有限公司建筑面积11万m2的龙门加工中心加工车间

图1-53 建筑面积35万m2的山东豪迈科技股份有限公司及其轮胎模具刻字车间

图1-54 无锡微研股份有限公司的精密磨削车间和慢走丝线切割加工车间
目前已有17家模具企业获得“中国机械工业优质产品”称号;30多家模具企业获得“知名商标”“知名商号”等;山东豪迈机械科技股份有限公司获“制造业单项冠军示范企业”称号。
1997—2008年,模具行业有290家企业先后享受“增值税先征后返”优惠政策,总额度17亿元,全部用于企业设备更新和技术改造;2010—2013年,模具行业有19家企业承担发改委“产业振兴、技术改造”项目,总投资超过20亿元,其中国家补贴近2亿元;2014—2016年,4家模具企业承担工信部“强基工程”项目;2011—2015年,3家模具企业承担科技部“智能制造”“云技术开发应用”等项目。
“十二五”期间,模具行业获省部级科技进步(成果)奖励25项,获得专利授权近10万项(其中发明专利9000项),35家企业作为主要起草单位参与模具国家标准和行业标准制修订工作。