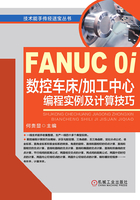
例1-2 小轴的加工(长棒料加工成小件,下料时的计算)。
小轴零件如图1-2所示。该零件的毛坯是ϕ40mm、长度为几米的棒料,材料为45钢,试编写其加工程序。

图1-2 小轴零件
工艺及数学分析:
毛坯是ϕ40mm、长度为几米的棒料,无法夹持。用切割机或带锯下料时要注意,下料的长度为:(精加工尺寸长度+切断刀刃宽+0.5~1mm的两端平面余量)的整数倍+最后一个工件在卡爪端面内的夹持长度+4~6mm,这样才能不浪费材料。装夹时以主轴孔末端伸出卡盘不长为宜,如有需要,可以在主轴孔末端塞紧一个木制或尼龙制塞子,中间有孔刚好能让棒料顺利通过。装夹时工件伸出卡盘端面73~75mm长,夹紧、加工完一个工件之后,松开卡爪,用钢直尺或左端在0位剪齐的钢卷尺段对照着去装夹工件,在夹紧时需要再次测量一下,以避免在工件倾斜于主轴孔的情况下,夹紧时工件位移带来误差。伸出卡盘的长度要和下个班交接好,以免碰撞或欠切。
这个小轴加工起来是很简单的,参考程序如下:
O0010;
G99 G97 M3 S800 T101;采用旋转进给,恒转速为800r/min,1号刀为93°外圆车刀
G0 X45.Z2.M8;定位到工件外且距离较近的中间点,开切削液
Z0;定位到平端面的起点
G1 X-2.F0.15;平端面
G0 X40.Z1.;定位到G71指令循环的起点
G71 U2.R0.5 F0.22;粗车背吃刀量2mm,退刀量0.5mm,进给量0.22mm/r
G71 P1 Q2 U0.8 W0.1; N1~N2之间的程序段群属于这个循环,精加工余量为:X轴直径值0.8mm,Z轴0.1mm
N1 G0 X10.8;移动到倒角的延长线上
G1 X15.8 Z-1.5 S1200 F0.15;延长线倒角,此时X轴移动了15.8mm-10.8mm=5mm,Z轴移动了-1.5mm-1mm=-2.5mm,X轴直径值的变化量是Z轴变化量的-2倍,恰好是45°倒角;倒角值为1.5mm,略大于螺纹牙高1.3mm即可;给定精加工的转速、进给量
Z-16.;
X20.;
X21.99 W-1.;切削到轴的尺寸公差带的中间值或略大,倒角1mm
Z-40.;
X28.;
X29.99 W-1.;切削到轴的尺寸公差带的中间值或略大,倒角1mm
Z-55.;
X36.;
X37.97 W-1.;切削到轴的尺寸公差带的中间值或略大,倒角1mm
N2 Z-70.;多加工5mm,给切断刀留下较好的作业面,不容易打刀
G0 X100.Z150.;退刀到安全点
M3 S1200 T202;换上精车刀
G0 X40.Z1.;精车刀要定位到G71指令之前的定位点,否则轨迹就会平移
G70 P1 Q2;精加工时执行N1~N2程序段之间指定的“S1200 F0.15”
T303 M3 S550;换上车槽刀,切削刃宽3mm
G0 X18.Z2.;定位到工件外且距离较近的中间点
Z-15.;移动到退刀槽右侧的上方
G1 X12.8 F0.1;车退刀槽,图样中“4×1.5”是“槽宽×槽深”,槽深略大于螺纹牙高即可
G0 X23.;车到槽底后,直接退X轴到安全点
Z-16.;再移动Z轴,到退刀槽左侧的上方
G1 X12.8 F0.1;车退刀槽第二刀,切槽时进给量较小
G0 X32.;退刀
Z-40.;定位到第二个槽上
G1 X17.F0.1;车到槽底
G0 X23.;退刀
Z-38.8;移动到倒角的延长线上
G1 X20.8 Z-39.9 F0.1;倒角1.1mm,槽口向右侧扩大了0.1mm
X17.;切到槽底
G0 X100.;先沿X轴退刀
Z150.;再退Z轴
T404 M3 S900;在安全位置换上螺纹车刀
G0 X20.Z5.;定位到螺纹切削起点,Z轴定位点在2倍导程外
G92 X14.8 Z-13.5 F2.;螺纹切削第一刀,背吃刀量0.5mm
X14.2;螺纹切削第二刀,背吃刀量0.3mm
X13.7;螺纹切削第三刀,背吃刀量0.25mm
X13.4;螺纹切削第四刀,背吃刀量0.15mm
X13.4;螺纹切削第五刀,背吃刀量为0,光一刀
G0 X100.Z120.;从螺纹切削起点X20.Z5.退刀到安全位置X100.Z120.
T303 M3 S500;再次换上车槽刀
G0 X40.Z2.;定位到工件外且距离较近的中间点
Z-69.;定位到工件左侧1mm,为便于排屑,以下刀路采用交错进刀
G1 X30.F0.1;切削
G0 X40.;退刀
Z-65.7;定位到倒角的延长线上
G1 X35.Z-68.2 F0.1;倒角1.5mm,给工件左侧平端面时留了0.2mm的余量
X20.;切削
G0 X32.;退刀
W-0.6;定位,和上次切削的Z坐标值错开0.2mm
G1 X10.F0.08;切削,降低进给量
G0 X22.;退刀
W0.4;定位,和上次切削的Z坐标值错开0.2mm
G1 X3.F0.08;切削,留一点量,用手掰断
G0 X50.M9;刀具沿X轴退刀,脱离工件,关闭切削液
M5;主轴停
G0 X100.Z200.;两轴联动定位到安全位置
T101;换上程序中的第一把刀,也可以编写为T100
M30;程序结束,复位
批量加工后,再批量倒角、平端面即可。