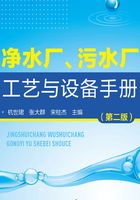
3.2 单元构筑物及设备
3.2.1 预沉
原水泥砂颗粒较大或浓度较高时,采用一次混凝沉淀和加大投药量仍难以满足沉淀出水要求,此时应设置预沉池。可根据原水含砂量、粒经、沉降性能、砂峰持续时间、排泥要求和条件、处理水量水质要求,结合地形、现有条件选择预沉方式。
预沉池常用的有沉砂、沉淀(自然沉淀、絮凝沉淀)、澄清等。原水中悬浮物多为砂性大颗粒时应采用沉砂池,原水含有较多黏土性颗粒时采用混凝沉淀、澄清等凝聚沉淀方式。
沉淀池有:沉砂池(旋流絮凝沉砂池、平流沉砂池、辐流式沉砂池、斜管沉砂池);预处理沉淀池;预处理澄清池等。
3.2.1.1 旋流絮凝沉砂池
经过投加絮凝剂的原水,通过池上部进水管的喷嘴快速混合,并旋转向下流动,穿过固定网板和导流板,由絮凝室下端流入分离室,进行泥水分离,分离出来的清水向上汇集于环行集水槽内流出池外;分离出来的泥渣依自身重力向下进入池下部浓缩室进行浓缩;浓缩后的泥渣由池上部刮泥传动装置带动池底刮泥板,将泥渣刮入池中心集泥斗内;斗内泥渣借助与池内水的静压力,由池底所设的排泥管排出池外。
(1)设计要点 采用絮凝沉淀时,原水的最大含砂量不超过60kg/m3,混合絮凝时间为5~15min,进水管喷嘴流速为2~3m/s,喷嘴距水面的距离(或淹没水深)为0.2~0.3m。絮凝室出口流速≤0.02m/s。泥渣浓缩时间一般取1.5~2.0h,泥渣浓缩室截锥体斜壁与水平面夹角一般为50°~60°。
(2)基本设计公式
1)絮凝室
① 絮凝室面积:
A0=Q/V
式中,Q为单池设计进水量,m3/min;V为絮凝室流速,m/min。
② 絮凝室直径:
③ 絮凝室容积:
W=Qt
式中,W为絮凝室容积,m3;t为絮凝时间,min。
④ 絮凝室高度:
h3=W/A0
2)分离室
① 分离室面积:
A1=αQ1/v1
式中,A1为分离室面积,m2;Q1为单池设计进水量,m3/min;v1为絮凝室流速,m/min;α为系数,一般取1.3~1.5。
② 沉淀池总面积:
A=A0+A1
式中,A0为絮凝室面积,m2;A为沉淀池总面积,m2。
③ 沉淀池直径:
3)浓缩室
浓缩室容积:
h1=vmT
式中,W1为浓缩室容积,m3;h1为泥渣浓缩室高度,m;vm为泥渣层增长速度,m/s;T为泥渣浓缩时间,s;F1为泥渣浓缩室上端锥体截面积,m2;F2为泥渣浓缩室下端锥体截面积,m2。
4)沉淀池高度
① 沉淀池中心高度:
H=h1+h2+h3+h4
式中,H为沉淀池中心高度,m;h1为泥渣浓缩室高度,m;h2为水流由浓缩室下沿流入分离室所需高度,m;h3为絮凝室有效高度,m;h4为絮凝室安全高度,m;Q为进水量,m3/s;d为絮凝室直径,m;v为絮凝室出口流速,m/s。
② 沉淀池周边高度:
H1=h1+h5+h6+h7
式中,H1为沉淀池高度,m;h1为泥渣浓缩室高度,m;h5为泥渣悬浮层高度,m;h6为泥渣分离区高度,m;h7为沉淀池安全高度,m。
5)排泥含砂量
式中,Cm为排泥含砂量,kg/m3;C为设计进水含砂量,kg/m3。
主要设备有排泥阀、搅拌器等。
3.2.1.2 平流沉砂池
平流沉砂池截留砂粒效果较好、构造简单、排砂较方便,其主要缺点是沉砂中夹杂有约15%的有机物,使沉砂的后续处理较困难。平流除砂池沉淀效果除受絮凝效果的影响外,与池中水平流速、沉淀时间、原水凝聚颗粒的沉降速度、进出口布置形式及排泥效果等因素有关,其主要设计参数为水平流速、沉淀时间、池深、池宽、长宽比、长深比等。
(1)设计要点 平流沉砂池的进口端要采取缓慢的扩散渐变形式,其扩散角不宜超过20°,进口段的长度一般取15~30m,进水栏与池体底一般采用(1∶2.5)~(1∶1.3)的陡坡连接。采用定期水力冲砂的池宽不大于6m,池深一般采用4~6m。
(2)基本设计公式
① 沉淀池长度:
式中,v为池子首端流速,m/s;Hρ为沉淀池首端工作水深,m;ω为计算粒径的泥沙的沉降速度,m/s。
Hρ=H-hy
式中,H为水力冲砂时的沉淀池深度,m;hy为冲砂的设计泥砂淤积高度,一般为首端总深度的25%~30%。
② 沉淀池的深度:
H+ilp≤Z+q/v
式中,i为池底纵坡;lp为沉淀池工作长度,m;Z为沉淀池池上游水位和冲洗排泥管、沟下游水位之间的落差,m;q为沉淀池单宽冲洗水量,m3/(s·m),取(1.1~1.25)vhR;v为冲砂流速,m/s,一般取2~2.5m/s;hR为冲砂时的平均水深,m。
主要设备:排泥阀、吸排砂机等。
3.2.1.3 斜管(板)沉砂池
在池内设置斜管(板),泥砂沿斜管(板)滑下。特点是沉淀效率高、池子容积小和占地面积少,但维护管理较复杂,斜管(板)需要定期清理和更换。
主要设备:快开排泥阀、潜水式刮砂机。
3.2.1.4 辐流式沉砂池
辐流式沉砂池多为池深较浅(周边水深2.4~2.7m)的圆形构筑物。原水自池中心进入,沿径向以逐渐变小的速度流向周边,在池内完成沉淀过程后,通过周边集水装置流出。沉降在池底部的泥砂靠机械排除。
主要设备:周边传动刮泥机、排泥阀、进水阀等。
3.2.1.5 沉淀池和澄清池
沉淀池和澄清池描述及设计要点见2.2.5和2.2.6部分相关内容。需要注意的是在选择投药量、上升流速、水力负荷、进水方式和排泥方式等时要考虑原水水质高含砂量和高浊的特点。
3.2.2 生物预处理
生物预处理的主要作用是去除原水中氨氮、异臭、有机微污染物、藻类等,减少对后续工艺滤池的堵塞,达到生活饮用水水质标准。
生物预处理是利用依附在填料上的微生物自身生命代谢活动(氧化、还原、合成等过程),微生物的生物絮凝、吸附、氧化、生物降解和硝化等综合作用使水中氨氮、有机物等逐渐有效去除。生物预处理主要包括生物滤池和生物接触氧化两种方式。
生物预处理的形式和参数应通过试验或参照相似原水条件的净水厂运行经验确定。应注意水温、气温对生物活性的影响,一般水温应不低于5℃。
主要设备有阀门、蝶阀、止回阀、排气阀、搅拌器、水泵、鼓风机、空压机等。
3.2.2.1 曝气生物滤池
曝气生物滤池(biological aerated filter,BAF)工艺是近年来国际上较为流行的一种新型水处理技术,该技术对氨氮的去除率达到80%以上,对耗氧量、浊度、色度、铁、锰等污染物均有较好的去除效果。
根据所使用的滤料不同,BAF的工艺形式主要有两种:一种使用陶粒等密度大于水的物质作为滤料,类似于Degrement公司推出BIOFOR滤池,目前使用较多的是页岩陶粒;另一种则使用密度小于水的悬浮型轻质滤料,类似于OTV公司推出的BIOSTYR滤池(滤料主要成分为聚苯乙烯)。由于所采用的滤料的不同,两种滤池在运行方式上各有特点。
主要设计参数:填料粒径 2~5mm;填料高度 1.5~2m;水力负荷 3~8m3/(m2·h);气水比(0.5∶1)~(1∶1.5);反冲洗周期 7~10d;反冲洗方式为气水联合反冲;反冲强度 气、水均为10~15L/(m2·s);反冲时间 5~10min。
3.2.2.2 生物接触氧化池
生物接触氧化也叫浸没式生物膜法,是一种介于活性污泥法和生物滤池之间的生物膜法工艺,主要由池体、填料、布水装置和曝气系统4 部分组成。生物接触氧化的优点是处理能力大,处理时间短,容积负荷高,水头损失小,对冲击负荷有较强的适应性,耐停运,出水水质较稳定,污泥产率低,投资和运行费较低,运行灵活,操作管理方便等。存在问题:生物膜增厚后不能仅靠自然脱落,要采取加大气量等措施控制其厚度,当池面积大时布水布气不易达到均匀,填料上较易生长水生动物。
生物接触氧化工艺水质净化效果取决于生物膜上的生物量及其活性,影响生物接触氧化工艺水质净化效果的主要环境因素有水源水质、水温、pH值、有机物浓度、悬浮物、溶解氧、水力停留时间、气水比等。此外,曝气方式、填料类型、结构特点和填料比表面积等也对处理效果产生影响。
主要设计参数:水力停留时间宜为1~2h;有效水深在3.5~6.0m;曝气气水比宜为(0.8∶1)~(2∶1);氨氮负荷0.05~0.08kg/(m3·d);曝气强度范围4.0~5.5m3/(m2·h),一般不宜小于4.0 m3/(m2·h)。
3.2.3 化学预氧化
在混凝工序前投加氧化剂可以去除微量有机污染物、除藻、除嗅味、控制氯化消毒副产物、去除铁锰等,并可起到助凝作用。在预氧化过程中,氧化剂与水中多种成分作用,能够提高对有害成分的去除效率,但在一定条件下也会产生某些副产物。目前给水处理预氧化药剂主要有臭氧、高锰酸钾(及高锰酸钾复合剂PPC)、氯、二氧化氯等。由于二氧化氯的副产物对人体有害,其投量不宜过高,因此二氧化氯一般主要作为后续的消毒剂使用;高铁酸盐制备难度大、成本高、易分解,实际工程中使用的较少。下面主要针对水厂中常用的3种化学预氧化技术进行介绍。
3.2.3.1 预氯氧化
用预氯氧化工艺能够杀菌、杀藻,降低藻类和有机物对后续混凝沉淀的干扰,并防止藻类在沉淀池和滤池中滋生,保证构筑物的卫生环境和正常运行,效果明显、投资和成本低,但会生成氯化消毒副产物,氯氨生成的消毒副产物比氯要低得多。
主要设备有加氯机、加氨机、二氧化氯发生器、次氯酸钠发生、液氯蒸发器、液压称、氯吸收设备等。
3.2.3.2 预臭氧氧化
预臭氧氧化是在混凝沉淀前投加臭氧,作用是氧化铁、锰,去除色度和臭味,改善絮凝和过滤效果,取代前加氯,减少氯消毒副产物、氧化无机物以及促进有机物的氧化降解。
臭氧是一种强氧化剂,能够与水中易被氧化的还原性无机物质或小分子有机物例如亚硝酸盐、氰化物、甲醛和酚等发生反应,也会与一些大分子有机物反应,使其得到不同程度的降解,变成简单的有机物,随后去除。
臭氧和水中溴离子反应生成溴酸盐致癌物,臭氧投加浓度和接触时间应合理,预臭氧氧化应设置在混凝沉淀前。
主要设备:气源系统、臭氧发生器、增压泵、输送系统、臭氧投加设备、控制系统、尾气处理装置、臭氧破坏装置等。
气源系统:臭氧的制备系统需要较高纯度的氧气(92%以上)作为气源。氧气气源提供方式有空气现场制氧和现场液氧直接气化制氧两种。空气现场制氧又包括真空变压吸附现场制氧(VPSA)和变压吸附现场制氧(PSA)两种。
臭氧发生器国外厂家有奥宗尼亚(Ozonia)、威德高(Wedeco)、三菱(Mitsubishi)、富士(Fuji)等。
臭氧的输送应采用不锈钢材质。
臭氧的投加方式有水射器投加和曝气扩散器。预臭氧的投加多采用水射器扩散装置。
臭氧投加的控制有流量配比和余臭氧控制两种方式,预臭氧的投加多采用流量配比控制方式。
臭氧尾气消除方式有电加热分解、催化剂接触分解和活性炭吸附分解消除等。
3.2.3.3 高锰酸钾氧化
高锰酸钾属于过渡金属化合物,是水处理中常用的强氧化剂。
高锰酸钾尚未发现能生成对人体有毒害的氧化副产物,是较为安全的预氧化剂。高锰酸钾杀藻,藻内容物不外泄,也是较安全的。如在预处理中同时使用活性炭,比加氯更有优势。高锰酸钾作为有效的预氧化剂主要有以下几方面的作用:a.去除二价铁、锰离子;b.去除水中有机物;c.降低三卤甲烷和其他氯化有机物的生成量;d.控制饮用水中的嗅味;e.氧化除藻。
高锰酸钾预氧化可以投加在取水口,如在净水厂内投加,需先于其他药剂的投加时间不少于3min。后处理必须有过滤单元,以减少不溶性二氧化锰造成的水体颜色。高锰酸钾投加量应根据烧杯试验确定。
主要设备:高锰酸钾的投加设备可采取干粉或溶液两种方式。
3.2.3.4 预氧化药剂的选择
可以根据原水水质特点、设计要求和后续处理工艺,选择合适的氧化剂进行化学预氧化处理(见表1-3-1)。
表1-3-1 化学预氧化药剂对水质的综合影响

3.2.4 粉末活性炭吸附(应急)
粉末活性炭吸附是完善常规处理工艺,去除水中有机污染物的有效方法之一。
当原水短时间内含较高浓度溶解性有机物、色嗅味异常时,采用投加粉末炭,主要作用是吸附溶解性物质和改善色、臭、味等感官性指标。由于连续大量投加粉末活性炭成本较高,因此只在应对突发水源事件时使用。
粉末炭一般投加在原水中,经过充分混合接触后(10~15min),再投加其他药剂。
粉末活性炭的投加方法有干式投加和湿式投加两种。目前常用于给水处理工艺中的是湿式投加法,即将粉末活性炭配置成悬浮液定量投加。悬浮液的质量百分比浓度采用5%为宜。
主要设备:粉末活性炭压缩空气进料系统、贮料仓、除尘过滤器、输送料斗、投加罐、进料器、螺旋投加器、计量泵等。
(1)设计要点 炭浆的输送可采用塑料水泵或普通离心泵,管道采用聚丙烯管道或ABS管道,管道内浆液流速一般在1.5~2.0m/s为宜,搅拌设备的功率按1~1.5kW/m3设计,所有炭浆制备和投加池均要求密封且通气系统要设置空气过滤器,以防止粉末活性炭污染环境和空气中灰尘进入炭浆池,降低炭浆的吸附效率。
(2)计算公式
① 粉末活性炭干粉量及调配水量计算:
日常粉末活性炭干粉量=已知处理数量×日常粉末活性炭的投加量
最大粉末活性炭干粉量=已知处理数量×最大粉末活性炭的投加量
② 调配池容积和投加池容积:
投加池容积=日常粉末活性炭的投加量×4h
调配池容积=投加池容积/2
3.2.5 磁分离预处理技术MIEX®
磁分离预处理技术MIEX®是由澳大利亚(ORICA)研究人员及企业合作研发的一种专利技术,在澳大利亚、新西兰、欧洲和美国被用于有效降低原水中的DOC;有效去除原水中的硝酸盐、磷酸盐、硫酸盐、砷化物,控制溴酸盐的产生;能减少后续混凝剂的用量从而减少饮用水中铁和铝的含量;能降低嗅味,并达到对消毒副产物的控制作用。
MIEX颗粒充满Cl-,是可重复使用的聚合物,粒径约180μm,在MIEX-DOC离子交换工艺中,MIEX颗粒被置于搅拌的电流接触池中,在磁场的作用下颗粒快速吸附水中溶解性DOC,从而降低水中DOC,处理水中Cl-略有增高。MIEX颗粒具有可再生性,再生过程中带有DOC的MIEX颗粒与水中Cl-进行反方向置换,以提供最大的表面积,便于再次吸附水中DOC。
在MIEX-DOC离子交换工艺中,MIEX颗粒选择性地去除水中溶解性DOC,且具有可再生性,通过再生可以使MIEX颗粒反复使用,环保、经济。
MIEX工艺主要去除指标包括:浊度(NTU)35%,TOC(mg/L)22%,UV25433%,色度(度)36%。
主要设备:搅拌器、砂循环泵、再生设备等。