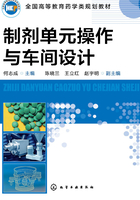
第四节 造粒
一、概述
在制剂生产中,原料药及辅料经粉碎、筛分、混合并制成软材后,还需进一步制成一定粒度的颗粒,即造粒。
一般来说,造粒为下列情况的总称:
①由粒子的聚集、成形或固体粒子表面被覆等导致的粒径增大;
②由粒子的聚集物或成形物的碎解而得到较小的粒状物;
③由熔融物质的分散冷却固化而得到粒状物等。
广义上,诸如结晶、喷雾干燥、粉碎等也属造粒的范畴,但从单元操作的观点出发,造粒的定义范围不包括上述3项操作。
造粒所得粒子的形状、粒度分布、内部构造及硬度等性质会因原料的种类、造粒方法及用途的不同而有所差异。
在制药工业中,片剂的压制,颗粒的制造,丸剂的塑制、泛制以及滴制等,均属于造粒操作。
(一)分类
药品制造所采用的造粒方法大致可分为湿法、干法、喷雾造粒法及熔融液滴制法等。
依据成粒的机制,造粒还可分为强制造粒和非强制造粒。
强制造粒是利用冲模、滚筒、喷嘴等机械,根据物料的性质进行压制、挤出、碎解、喷射等,以达到物料的成形作用。如压片、丸剂成形、制粒、滴丸等。
非强制造粒是依靠材料本身的聚集(被覆)作用,利用造粒设备的旋转、振动、流化、搅拌等,达到物料成形目的。如泛丸、喷雾及转动制粒等。非强制造粒过程中,物料一般在设备内有较长的停留时间。
(二)粉粒间的结合力
粉粒依靠各种聚集因素在造粒时相互结合才能形成一定形状的粒状物。粉粒间的结合力主要有如下几种:
(1)粒子间的结合力 ①分子间引力(范德华力);②静电引力。
(2)自由流动液体的附着、凝集力 ①粒子之间的架桥现象所引起的表面张力;②液体在粒子之间的毛细管吸力。
(3)非流动性物质的附着力 ①黏合剂的黏合力;②一部分物料(如稠浸膏)的黏合力。
(4)固体形成时的结合力 ①固体溶质的再结晶;②粒子间液体被干燥后所形成的固体架桥。
二、湿法强制造粒
湿法强制造粒是指将液体黏合剂与粉状原料混合后通过挤压等外力使其成形的操作方法。
此法既可用于制造较小的颗粒(如颗粒剂、片剂的颗粒等),也可借助切割装置制造较大的粒状物(如丸剂等)。
湿法强制造粒按所用设备可分为压出造粒和摇摆造粒。以下分别对具有代表性的压出造粒设备和摇摆造粒设备进行介绍。
(一)压出造粒
1.螺旋压出造粒机
螺旋压出造粒机利用在圆形壳体内水平旋转的螺旋推进器将湿料加压,由装在壳体前端或侧面的挤出口压出。图1-35(a)所示的是中药蜜丸成形所用的丸条机,图1-35(b)所示的是压丸机中的压辊,图1-35(c)所示的是物料在丸条机内的压力分布。

图1-35 蜜丸成形装置
1—加料口;2—外壳;3—螺旋输送器;4—出料口;5—槽形压辊
丸块由加料口1加入,在螺旋输送器3的推进作用下压力逐渐升高,最后由最前端的出料口4被压成长条并挤出。
丸条到达压丸机上压辊的另一端时,落到槽形压辊5上,利用压辊凹槽上凸起的刃口将丸条压割成丸。
蜜丸的大小与丸条机出料模口尺寸及压辊刃口间距有关,制造不同规格蜜丸时,应调换不同规格的出料模口及压辊。
制药工业还使用一种螺旋式造粒机,如图1-36所示。物料由混合室内双螺杆上部的加料口加入,两个螺杆2分别被齿轮带动相向旋转,借助螺杆上的螺旋推力,物料被挤入右端的造粒室,在造粒室被压出滚筒3搅动,物料通过筛筒4上的筛孔完成成粒。该机生产能力大,压力强,适用于多种颗粒的制造。

图1-36 螺旋式造粒机(俯视图)
1—外壳;2—螺杆;3—压出滚筒;4—筛筒
2.旋转式造粒机及研磨式造粒机
旋转式造粒机如图1-37所示。不锈钢制立式圆筒形造粒室1内有2、3上下两组逆向旋转的叶片。物料由上部加入造粒室,上部的倾料叶片将物料压向下方,下部弯形叶片将物料推向外侧。物料被从造粒室下方的细孔压出成粒,颗粒大小由该细孔直径所定。孔径以0.7~1mm为宜,一般不小于0.5mm,孔径过小会影响造粒效果。本机可将干硬原料研成颗粒,并可用来粉碎已压成药片返工的颗粒。

图1-37 旋转式造粒机
1—造粒室;2—上部叶片;3—下部叶片
研磨式造粒机如图1-38所示。短圆筒形的可旋转筛框内置有一层圆形筛圈,筛圈内有一压出转子,筛圈与压出转子同向旋转。

图1-38 研磨式造粒机
1—筛圈;2—压出转子;3—湿料
湿料投于筛圈内,在同向旋转的筛圈1和压出转子2的挤压下通过筛孔成粒。制粒的压力可通过调整筛圈与压出转子间的距离来调节。颗粒的粒径可通过更换筛圈(筛孔直径)来调节。
研磨式造粒机的特点是处理能力大、运转可靠,因其筛圈与压出转子同向旋转,故因摩擦而产生的热量较少。
(二)摇摆式颗粒机
摇摆式颗粒机如图1-39所示。加漏斗的底部与一个半圆形筛网相连,在筛网内部有一可正反向旋转的七角滚筒,其上固定有若干截面为梯形的“刮刀”(blade)。借助滚筒正反方向旋转时刮刀对湿物料的挤压与剪切作用,物料通过筛网成粒。

图1-39 摇摆式颗粒机
1—电机;2—皮带轮;3—蜗轮;4—蜗杆;5—七角滚筒;6—筛网;7—管夹
摇摆式颗粒机与其他常用颗粒机相比所成的颗粒更加接近球形、表面更为光滑。但是,摇摆式颗粒机也有生产能力较低、对筛网的摩擦力较大、筛网易破损等不足。
三、转动造粒
转动造粒是利用一定量的黏合(或润湿)剂,在转动、振动、摇动或搅动下使固体粉末黏附成球形颗粒的操作。
转动造粒属于湿法非强制造粒。中药水丸或水蜜丸制造中的转动造粒操作称为泛制。
(一)转动造粒原理
转动造粒操作可采用两种方法:
①附聚 物料粉末相互黏结附聚成粒,同时包括母核的生成。
②包层 原料黏附在事先制好的母核上,颗粒体积逐层地增大。包层操作需事先制造母核(起模),然后逐层喷加液体并撒入药粉,以使药粉逐层黏附(泛制)。每次加粉量需适宜,以防止产生新的母核。
包层操作所得球体粒径较附聚法均匀,但原料中的含水量要求较低。水丸泛制的母核制造过程属于附聚操作,成丸过程属于包层操作。
固体粒子黏附长大的机理如图1-40所示。液体将粒子湿润并附于其表面。由于液体的黏合力,固体粒子相互黏附成颗粒。颗粒转动中,自颗粒外侧压出过剩的液体,这些表面液体可继续将另外的粒子黏附,如此逐渐长大成致密的球形粒子。

图1-40 转动造粒机制粒示意图
粒径变化是颗粒间相对运动产生的破坏力与粒子相互结合的黏附力达到平衡的结果。在球形粒子长大的过程中,强度必须足够大,以克服那些破坏力。只有这样,颗粒才不致被磨损并能继续长大。
(二)转动造粒设备
转动造粒设备主要有倾斜回转锅式[图1-41(a)]及回转圆筒式[图1-41(b)]。

图1-41 转动造粒设备
倾斜回转锅式造粒设备也可用包衣锅代替。锅底与水平面的夹角能够调节(一般为45°~55°),以便获最佳操作效果。锅的转速可以是恒定的,也可以是可变的。回转锅的临界转速由下式计算:
(1-29)
式中,Nc——临界转速,r/min;D——锅的直径,m;θ——锅底与水平面的夹角,(°)。
锅的实际转速可取临界转速的40%~75%。
由于球形粒子与锅壁间的摩擦系数比原料粉末间的小,所以转动造粒过程中粒子具有向表层移动的倾向。所产生的自动分级作用,使倾斜锅式造粒设备所造出的粒子比回转圆筒式的粒子粒径均匀,故制药工业多用倾斜锅式造粒设备。该设备可以连续操作,也可以间歇操作,直径范围为250~5000mm。但制药工业主要为间歇操作,设备直径一般在1000mm左右。
物料在造粒锅中的造粒机理模型如图1-42所示。

图1-42 回转锅式造粒机内的粒子分布
造粒锅内物料粒子的分布可分为3个区域:
α区 长成的球形大粒子进行压实的区域;
β区 粒子的主要成长、生成区;
γ区 细粉和未长成粒子的混合共存区域。
特别在β区,颗粒中水分的含量对颗粒的成长具有很大影响。设水分系数f为
据测定,当f=0.75左右时,β区内颗粒的成长速度急剧增加,此种倾向在回转圆筒式造粒设备中也同样存在。
回转锅式造粒机操作容易控制,容易直接观察,价格较低,故对各种物料的转动造粒均具有很好的适应性。
四、滴制造粒
通过分散装置将熔融液体微粒化,再经冷却装置使之固化,以此得到球形颗粒的操作称为滴制造粒(或称喷射选粒)。滴制造粒属于强制造粒。
制药工业中利用滴制法制备软胶囊、喷雾法制备微囊以及滴丸的制备等操作均属于滴制造粒。
滴制造粒设备的设计首先需考虑溶液的性质和该溶液的可喷或滴出性能(如熔点、黏度、表面张力等)。
一定粒径和质量的产品所需要的最适宜温度和喷嘴尺寸,只有通过实验室规模的喷雾(或滴出)试验才可能得到。
(一)滴制造粒操作
典型的制药工业滴制造粒流程见图1-43。

图1-43 滴制造粒流程
1—熔融物料贮槽;2—保温电热器;3—分散装置;4—冷却柱;5—滤槽;6—冷却液贮槽;7—循环泵
熔融物料的熔化、混合等操作通常在另外的设备中进行。熔融物料置于贮槽1中,贮槽周围有保温电热器(电阻或电感加热)2以保持温度,防止料液凝固。料液通过分散装置3喷射或滴制成滴进入冷却柱4的冷却液中冷却、定形、固化,并随冷却液进入滤槽5。圆形颗粒经干燥得到成品。冷却液由滤槽5进入冷却液贮槽6,经冷冻盐水的冷却后可连续使用。
(二)滴制造粒设备
滴制造粒设备主要由分散装置和冷却装置两部分组成。
1.分散装置
分散装置是将熔融液喷制或滴制成一定大小液滴的装置。其中包括熔融液的贮槽、保温或恒温装置等。
最简单的分散装置为滴管,一种由玻璃管拉制的锥形尖口管。适用于黏度较小熔融液的少量滴制,多用于滴丸的制造。
在软胶囊的制造中,熔融液的喷制多采用柱塞泵。最简单的柱塞泵如图1-44所示。

图1-44 柱塞泵
1—柱塞;2—泵体;3—排出阀;4—弹簧;5—出口管
泵体2中有柱塞1可作垂直方向的往复运动,当柱塞上行超过药液吸入口时,将药液吸进泵内。柱塞下行时,通过排出阀3将液体压出至出口管5成液滴喷出。喷出终了时,出口阀的球体在弹簧4的作用下将出口封闭,柱塞重复下一循环。
图1-45所示的是另一种柱塞泵,该泵采用动力机械的油泵原理。当柱塞4上行时,液体经进油孔进入柱塞下方,待柱塞下行时,进油孔被柱塞封闭,室内油压增高,迫使出油阀6克服出油阀弹簧7的压力而开启,此时液体由出口管排出。当柱塞继续下行至柱塞侧面凹槽与进油孔相通时,柱塞下方的油压降低,出油阀在弹簧力的作用下将出口管封闭。喷出的液量通过齿杆5控制柱塞侧面凹槽的斜面及进油孔的相对角度来调节。

图1-45 柱塞式油泵
1—弹簧座;2—柱塞弹簧;3—泵体;4—柱塞;5—齿杆;6—出油阀;7—出油阀弹簧
制备软胶囊常采用的第3种柱塞泵为三柱塞泵,如图1-46所示。泵体中有3个柱塞,中间柱塞主要起吸入与压出的作用,其余两个柱塞相当于吸入、排出阀。3个柱塞运动的先后顺序通过调节推动柱塞运动的凸轮方位来完成,泵的出口可喷出大小一定的液滴。

图1-46 三柱塞泵原理
1—柱塞;2—泵体
在软胶囊制造中,明胶与油状药物的液滴分别经由柱塞泵压出。为将药物包裹到明胶液膜中心以形成球形颗粒,这两种液体应在严格同心的条件下分别通过喷头套管的内外侧,并有序地喷出才能形成正常的胶囊。否则将会产生偏心、破损或拖尾等不合格产品。
喷头结构见图1-47,药液由侧面进入喷头后经套管中心喷出。明胶由上部进入喷头,通过两个通道流至下部,然后在套管的外侧喷出,两种液体在喷头内互不相混。从顺序上看,明胶喷出过程时间较长,而药液喷出过程则应位于明胶喷出过程的中段。

图1-47 喷头结构
软胶囊分散装置包括凸轮、连杆、柱塞泵、喷头、缓冲管等,如图1-48所示。明胶与油状药液分别经由柱塞泵3(参见图1-45)喷出。明胶通过连管由上部进入喷头4,药液则经过缓冲管6由侧面进入。两种液体垂直向下喷到充有稳定流动冷却液(液体石蜡)的视盅5内。如操作得当,经过系统内冷却液的冷却固化,即可得到球形软胶囊。泵内柱塞的往复运动由凸轮1通过推动连杆2完成,两种液体的喷出时间由控制凸轮的方位来调节确定。

图1-48 软胶囊的分散装置
1—凸轮;2—连杆;3—柱塞泵;4—喷头;5—视盅;6—缓冲管
2.冷却装置
冷却装置是利用低温流体将熔融液体定形、固化(或胶凝等)以得到一定形状颗粒的装置。包括上述的流体输送装置、冷冻装置等。
五、干法造粒
向添加固体黏合剂的原料粉末施加压力以形成片状或粒状产物的操作称为干法造粒。干法造粒通常用于不宜湿法造粒的场合(如药品与湿润剂起反应或药品易在干燥过程中分解)。
制药工业中的干法造粒可分为压片法和滚压法。
压片法先利用重型旋转压片机将固体粉末压实至直径为19~25mm的片坯,然后再压碎成所需粒径的固体粒子。
滚压法则是利用两个转速相同、转向相反滚筒之间的缝隙,将粉末滚压成一定形状的压制物。
压制物的形状及大小决定于滚筒表面情况。按照滚筒表面具有的凹槽不同压制物可形成卵形、枕形、滴形或圆形块等。如果滚筒具有光滑表面或瓦楞状沟槽,则压制物可形成大块状。大块状的物料需经粉碎才能造粒制成所需粒径的产物。
固体粉末在滚筒间受到挤压与摩擦力的作用,靠近缝口的粉末被滚筒“咬入”,因受到压缩而聚集,滚筒表面开始对物料施力的部位为“咬入点”,如图1-49所示。

图1-49 滚筒间的压缩模型
“咬入点”处粉末空隙率与成形物空隙率的关系可由式(1-30)表示:
(1-30)
式中,αn——“咬入点”处粉末空隙率, %;αp——成形物空隙率, %;θn——咬入角,(°);DS——滚筒间隙,m;DR——滚筒直径,m。
最简单的干法造粒是用双滚筒将粉末压成长片,然后通过颗粒机粉碎成一定大小的颗粒。
图1-50表示干法造粒流程。将原料粉末投入料斗1中,用加料器2将其送至波形滚筒4进行压缩,如需润滑剂,可通过润滑剂喷散装置3将固体润滑剂喷散到滚筒上。由滚筒压出的固体块坯落入料斗6,并预碎成较小的块状物,然后进入具有确定凹槽的滚碎机7制成预定尺寸的颗粒,最后进入整粒机8经整粒后得到成品。

图1-50 干法造粒流程
1—料斗;2—加料器;3—润滑剂喷散装置;4—波形滚筒;5—液压缸;6—料斗;7—滚碎机;8—整粒机
利用与滚压类似的原理可以制成压制软胶囊的设备,如图1-51所示。两张端部被加热软化的明胶带绕入滚筒,同时随滚筒一起旋转,在即将会聚于一处时,计量泵把一定量的药液注入两带之间,滚筒利用本身的凹槽边缘将胶带封口、切断并成一个完整的胶囊。

图1-51 压制软胶囊中的充填与封合
1—喷头;2—定量药液;3—明胶带;4—明胶带余屑
明胶带的余屑落入化胶锅仍可继续套用制造新的明胶带,胶囊嵌入下滚筒至适当位置被刷,以进行洗涤干燥等操作。胶囊的形状因滚筒上的凹槽而异。一台连续胶囊机的生产能力可达3万粒/h。
依此相同的原理可制造充填固体粉末的软胶囊,但胶囊的成形需靠负压完成。
六、压片与压片机
压片是指药物与赋形剂等辅料经加工后被压制成片剂的操作,属干法造粒。
片剂的压制可采用粉末直接压制及颗粒压制。片剂成品应符合外观、硬度、片重差异及崩解时限等质量要求。
片剂最主要的制造方法是干料压制,有时也采用湿料模制片等方法。
(一)压片机分类及原理
1.分类
压片机的分类有以下方法:
①按结构 单冲压片机、旋转式压片机;
②按片形 圆形片压片机、异形片压片机;
③按加压次数 一次压缩压片机、多次压缩压片机及包衣片压片机等。
2.单冲压片机
单冲压片机构造简单,适用于少量药片的压制。其构造及工作原理如图1-52所示。

图1-52 单冲压片机构造及工作原理
1—偏心轮;2—曲柄;3—上冲;4—下冲凸轮;5—下冲拉杆;6—下冲;7—充填凸轮;8—连杆;9—加料器;10—中模
单冲压片机只有一副冲模,利用偏心轮及凸轮等机构在转轴旋转一周内完成充填、压片及出片等动作。操作中,电机通过皮带轮(或人工旋转飞轮)带动偏心轮1及凸轮4、7旋转。偏心轮1通过曲柄2带动上冲3做上下往复运动;下冲凸轮4通过下冲拉杆5带动下冲6做上下往复运动;充填凸轮7通过连杆8拨动加料器9后部的拨叉,使加料器往复摇摆。中模10固定在上下冲间的中模合板上,片剂在其中被压制而成。为协调压片过程各个动作的顺序,应将偏心轮及凸轮的方位调整适当,并防止使用过程中出现挪动。该机型的动作顺序如表1-10所示。
表1-10 单冲压片机各机构的运动状态与主轴转角的关系

单冲压片机片剂压制过程如图1-53所示。其中图(a)表示在中模充填颗粒前的状态,上冲处于最高位置,下冲正在下降阶段;图(b)表示加料器运动至中模处,正在充填物料;图(c)表示加料器已经复位,在偏心轮的作用下,上冲下行将粉末压缩;图(d)表示上冲上升,下冲凸轮将下冲上拉并将药片顶出中模;图(e)表示下冲下降,加料器回摆至中模加料,同时将片子推出台板。

图1-53 单冲压片机片剂压制过程
单冲压片机的片重调节装置如图1-54所示。下冲4通过锁紧螺帽固定于下冲螺杆5,在下冲螺杆上有2个可调的螺帽6及7,用螺帽7可调节下冲下降的深度(即中模孔内的容积),并借此调节片重;螺帽6可调节下冲螺杆5的上升高度,操作时应调节至下冲的上平面与台板相平,借以顺利出片;下冲拉杆1上的两个螺帽2用以调节推片板3,使之位于螺帽6、7之间并稍留空隙,以便压片时的压力直接通过螺帽7传递给机座8,避免压片时的巨大压力损坏机器。

图1-54 单冲压片机的片重调节装置
1—下冲拉杆;2,6,7—螺帽;3—推片板;4—下冲;5—下冲螺杆;8—机座
单冲压片机最大压片直径12mm,最大充填深度11mm,最大压片压力1500kg,主轴的最大转速100r/min。
3.旋转式压片机
旋转式压片机又称多冲压片机,是一种连续操作的设备。在其旋转时连续完成充填、压片、推片等动作。
旋转式压片机的原理如图1-55所示。具有3层环形凸边的回转盘1在垂直于其回转轴的平面内等速旋转,中模2等距离固定在中层环形凸边(模盘)上,在上、下两层凸边(上、下冲转盘)按与中模相同的圆周等距离布置着相同数目的孔,孔内插有上冲3及下冲4,冲杆可在上、下冲转盘内沿垂直方向移动。上、下冲依靠固定在转盘上、下方的轨导5、6及压轮7、8的作用上升或下降。其升降的规律应满足压片循环周期的要求。

图1-55 旋转式压片机工作原理
1—回转盘;2—中模;3—上冲;4—下冲;5—上轨导;6—下轨导;7—上压轮;8—下压轮;9—加料器
操作时,利用加料器9将药粉充填于中模孔中,在回转盘转动至压片部分时,上、下冲在压轮7、8的作用下将药粉压制成片。压片后,下冲上升,将药片从中模孔内推出,待回转盘运转至加料器处,靠加料器的圆弧形侧边推出转盘。
(二)旋转式压片机的压缩速度及压缩停滞时间
1.压缩速度
压缩速度的定义为:单位时间中模内固体粒层厚度的变化量(待压深度)。片剂压制的质量与固体粒子的压缩速度有关。旋转式压片机的压制部分如图1-56所示。

图1-56 旋转式压片机压制部分
1—模盘;2—上压轮;3—上冲;4—料粉;5—下冲;6—下压轮
图1-56中:N—模盘的转速,r/min;R—模盘半径,mm;ϕ—模盘转角,(°);r—压轮的半径,mm;h—料粉在任意位置的厚度,mm;h0—压制终态料粉的厚度,mm;Δh—待压深度,mm,Δh=h-h0。
按定义,压缩速度表示为
(1-31)
式中,u——压缩速度,mm/s;τ——压制时间,s。
由图1-56所示的几何关系可得
(1-32)
因为、
、
,代入式(1-32)得
(1-33)
代入式(1-31)得
整理得
(1-34)
式中,ω——模盘的角速度,1/s。
由于在压制过程中,ϕ值变化很小,cosϕ≈1、sin2 ϕ≈0,代入式(1-34)化简得
(1-35)
由图1-56所示的几何关系得
整理得
(1-36)
因为Δh≪r,所以,代入式(1-36)有
(1-37)
将式(1-37)及代入式(1-35)有
整理得
(1-38)
或
(1-39)
式中,K——压缩速度系数,mm1/2/s。
由式(1-39)可见,旋转式压片机的压缩速度u与被压制的固体颗粒层厚度变化Δh有关。在压缩终态时(h=h0),压缩速度u=0。压缩速度系数K与压缩速度u成正比。压缩速度随模盘半径R的减小、压轮半径r的增大而减小。
因在片剂压制过程中压缩速度是固体颗粒厚度Δh的函数,所以在考察压缩速度与片剂硬度之关系时,通常以压缩速度系数K为准。
图1-57为乳糖及小麦淀粉颗粒压制时压缩速度系数K与片剂硬度(H)之关系。可见,片剂硬度随K值的增加而下降。压缩速度系数与压片机的构造有关,压轮直径较大、模盘的转速及直径较小的压片机所压制的片子质量较高。

图1-57 K与H的关系
2.压缩停滞时间
设de为冲杆底面的直径。当中模内的压缩处于终态时,冲杆底平面水平移过压轮,冲头在垂直方向处于停滞状态。设τe为压缩停滞时间,在该时间内模盘转动的圆周长度应与冲杆直径de相同,即
整理得
(1-40)
由式(1-40)可见,冲杆底面直径越大,模盘半径及其转速越小,则压缩停滞时间越长。
图1-58所示的结果证明,压缩停滞时间与片剂硬度有关。压片过程中压缩停滞时间越长,所得片子的硬度越高。因此,模盘直径较小、冲杆直径较大的压片机对片剂压制有利。

图1-58 τe与H的关系
3.旋转压片机与单冲压片机压缩速度的比较
旋转压片机与单冲压片机的压缩速度差别很大。两种压片机冲头位移Δhp与压缩时间τ的关系如图1-59所示。曲线的斜率即为冲头压缩速度。

图1-59 压片机压缩速度的比较
1—旋转压片机线;2—单冲压片机线
由图1-59可见,开始压缩时冲头位移速度较大,压缩终了时冲头位移速度为0。压缩初期旋转式压片机的冲头位移速度大于单冲压片机,但在压缩末期,即在最大压力时,旋转式压片机的冲头位移速度小于单冲压片机。说明在压力最大的时段,旋转式压片机内单位时间受压固体的体积变化比单冲压片机缓慢,受力更为均匀。
压制过程中,由于旋转式压片机采用上下冲同时加压,所以固体颗粒内部应力的分布较好。而单冲压片机采用上冲单独加压的方式,故颗粒内部应力的分布也不太均匀。综上所述,旋转式压片机的压片质量优于单冲压片机。
4.压片机故障判断
压制过程中判断压片机机器故障的思路,是根据生产现场有规律的产品破损现象来反推。
由式(1-39)和式(1-40)可知,K值越大、τe值越小,压出的片剂质量越差。造成产品破损的原因无非有3个方面:一是压轮的直径因受冲头尾端长期连续撞击而受损变小;二是冲头尾端因受压轮反复撞击而使底面直径变小;三是因追求产量而将回转盘转速调得过大。从这些角度思考,就会很容易地找出故障。
以33冲旋转压片机为例说明如下:
由压片原理可知,33冲压片机回转盘每转动一周(360°),两侧压制就会各压出33片,共计为66片。每转动一周(360°),如果两侧各有2片破损产品,说明在33对冲头中有两对冲头磨损并需更换;如果在一侧全是破损产品而在另一侧全部合格,说明破损产品侧的压轮已经磨损并需更换;如果两侧全是破损产品,而两侧压轮同时损坏的概率极低则说明回转盘转速过高,需将其调低到所有产品合格为止。
(三)压力与片剂体积的关系
1.固体粉末压制时的位移与变形
固体粉末在受到外力后产生位移和变形,使粉末之间的孔隙度大大降低,片剂内部的比表面积增加,并且强度也有所提高。
(1)粉末的位移 压片中,固体粉末充填于中模前多为松散堆积。由于表面不规则,相互间产生摩擦,颗粒间因拱桥效应而相互架桥,形成很多孔隙。施加压力时,粉末内的拱桥效应遭到破坏,颗粒彼此填充孔隙,重新排列位置,粉末间发生各种形式的位移,如颗粒间的滑动、转动、接近等,如图1-60所示。

图1-60 压制时粉末颗粒的位移
一般,固体颗粒在受压状态可能同时发生数种位移现象,而且,位移总是伴随着变形而发生的。
(2)粉末的变形 固体粉末受到外力后,可发生3种变形:
①弹性变形 外力卸除后粉末可恢复原状;
②塑形变形 压力超过粉末的弹性极限,变形不能复原;
③脆性断裂 压力超过粉末的强度极限后,颗粒发生粉碎性的破坏,脆性较大的固体主要以脆性断裂的方式被破坏。
粉末的变形如图1-61所示。

图1-61 压制时粉末的变形
压力增大时,颗粒由最初的点接触[图1-61(a)]逐渐变成面接触[图1-61(b)、(c)],由球形逐渐变为扁平状,接触面积不断增大。压力继续增加时,颗粒就可碎裂。
2. σ-ΔH曲线
固体颗粒压缩时容积变化状态如图1-62所示。图中ΔH为压缩深度;h0为压制后片剂厚度;H0为压制前粉末的充填厚度。则压制最大深度:

图1-62 固体颗粒压缩时料粉的容积变化(单冲冲压机)
1—中模;2—上冲;3—下冲;4—料粉
设σ为片剂内应力,则压制过程中压缩深度与粉末物料内部应力的关系曲线可由图1-63表示。根据粉末颗粒压制过程中的关系曲线,固体颗粒的集合状态可分为以下4个阶段:

图1-63 内应力与压缩深度的关系
1—滑动段;2—变形段;3—破碎段;4—恒定段
①滑动段 随冲头的压入,固体颗粒相互滑动靠近,填充空隙。所以压力增加不多,体积变化却很大;
②变形段 随冲头施加压力的增加,固体颗粒开始发生弹性或塑性变形,所以体积变化虽一般,但内部应力增幅却很大;
③破碎段 压力继续增加时,粒子发生破碎,新的表面产生。料粉内因粒子破碎而余留的空隙被填充,体积减小幅度有限,内部应力的升幅也不大;
④恒定段 当压力继续增加到一定值后,料粉间的空隙已经填满,此后,尽管继续增加压力,料粉的体积几乎不变。
实际上,在粉末压缩时各阶段的现象可同时出现,且曲线的形状与压缩速度及物料的种类、粒径、含水量等有关。
Higuchi通过测定粉碎中压力与料粉比表面积关系指出,压制初期,比表面积随压力的升高而增大;达到极值后,压制进入末期,比表面积随压力的升高而减小,如图1-64所示。

图1-64 压力与比表面积的关系
(四)压力与片剂体积关系的解析
由于固体颗粒受压时体积变化的影响因素十分复杂,所以迄今尚无经过实践检验的描述压制中压力与片剂体积关系的数学表达式。这些因素包括:固体颗粒的变形、破碎,颗粒之间的摩擦,颗粒与模壁间的摩擦,颗粒的流动性质及压制速度等。
多年来人们对压制理论进行了一系列研究,并提出许多压制理论或者经验公式。其中以Бапьщин、Athy、川北公夫等方程式较为优越。
川北公夫采用受压面积为2cm2的钢压模,粉末粒度75μm左右。粉末装入压模后在油压机上逐步加压(最高压力497MPa),然后测定粉末体的体积变化,并作出各种粉末的压力-体积曲线,得出了经验公式。
川北公夫在研究压制过程中先作了如下假设:
①粉末层内所有各点压力相等;
②粉末层内各点的压力为外力P和粉末内固有内压力P0之和;
③粉末层各断面上的外压力与各断面上实际受到压力的粉末断面积总和保持平衡关系,外压如果有增加,粉末体即被压缩,各断面上粉末颗粒的实际接触断面积增加,重新回到平衡状态;
④每个粉末颗粒仅能承受其固有屈服极限的能力;
⑤粉末层所能承受的负荷和位移概率成反比。粉末压缩时,各颗粒的位移概率和它邻接的孔隙大小成比例,没有孔隙,即使外压再大也不能压缩。
设:P为单位面积粉末所受的外部压力;P0为单位面积粉末固有的内部压力;V为受外压时粉末的体积;V0为无外压时粉末的体积;V∞为全部颗粒的实际体积;A为粉末体的断面积;A0为颗粒的平均断面积;n为各层的粉末颗粒数;n∞为粉末体完全充填时的颗粒数;S为颗粒位移的概率;σ为颗粒的固有屈服极限。则
(1-41)
根据假设,粉末体层各部分承受的负荷为,平衡时各断面层力的平衡关系为
(1-42)
根据几何学得
(1-43)
由式(1-41)~式(1-43)可得
常数 (1-44)
当P=0时,V=V0,代入式(1-44)得
(1-45)
将式(1-44)代入式(1-45)得
或
整理得
或
即
(1-46)
设粉末体积减小率
(1-47)
又设
(1-48)
(1-49)
由式(1-46)~式(1-49)联立可得
(1-50)
川北公夫对10种粉末进行试验,得到粉末体积减小率与压制力的关系如图1-65所示。

图1-65 粉末体积减小率与压制力的关系
1—氧化镁;2—滑石粉;3—硅酸铝;4—氧化锌;5—皂土;6—氯化钾;7—硅酸镁;8—糖;9—碳酸钙;10—糊精
(五)压片过程中的力
固体颗粒在受到外力而成形的过程中,各断面的受力并不是相等的。在同一断面内,中心部位与靠近模壁的部位、颗粒的上部和下部所受的力也并不一致。料粉除去受到外加的正压力外,还有侧压力及摩擦力等。所以,压制成形的片剂密度并不均一。
正压力作用于固体颗粒后,一部分用来使固体颗粒产生位移、变形及克服其内部的摩擦力,称之为净压力;另一部分用以克服颗粒与模壁之间的摩擦压力,这部分称为压力损失。压制时所用的总压力为
P=P1+P2
式中,P1——单位面积的净压力,N/m2;P2——单位面积的摩擦压力,N/m2;P——单位面积的总压力,N/m2。
1.侧压力
固体颗粒在中模内受到冲头的压缩时会向周围膨胀,模壁会给固体物料侧面一个反向作用力,以限制其变形。这个作用力就是侧压力。
图1-66是圆柱固体受压时的受力示意图。当固体在Z轴方向受到正压力PZ的作用时,会在Y轴和X轴方向产生膨胀,同时X轴方向的侧压力PX驱使固体向Y轴方向膨胀、Y轴方向的侧压力PY也会驱使固体向X轴方向膨胀。然而,由于受到模壁在两轴方向的反向侧压力,故其对固体的膨胀趋势产生了限制。

图1-66 圆柱固体受力分析
应用广义虎克定律分析上述诸力对Y轴的作用:
①正压力PZ使固体在Y轴方向产生的膨胀 (1-51)
②侧压力PX使固体在Y轴方向产生的膨胀 (1-52)
③侧压力PY使固体在Y轴方向产生的压缩 (1-53)
式中,μ——固体物料的泊松比;E——固体物料的弹性模量,N/m2。
由于模壁的限制,固体在Y轴方向产生的膨胀总量为零,即
(1-54)
整理得
μPZ+μPX=PY (1-55)
设:Pr为圆柱物料外侧单位面积的径向压力,N/m2。
根据对称性原理有
PX=PY=Pr (1-56)
将式(1-56)代入式(1-55)并整理得
(1-57)
或
Pr=ξPZ (1-58)
式中,ξ——侧压系数。
由式(1-58)可见,侧压力与正压力为线性关系,且随正压力的增高而加大。
同μ类似,侧压系数ξ也与物料种类、粉末特性有关。在片剂压制中,ξ与固体物料的孔隙率有关。可知片剂压制中侧压力的变化十分复杂。
还应指出,上述的侧压力是平均值。由于固体颗粒与模壁摩擦的影响,外加的正压力传递到固体内部后,在不同深度的断面是不同的。所以,在固体内的不同深度上侧压力也是不同的。可以证明,同正压力一样,侧压力随深度的增加而减小。
2.固体颗粒与模壁间的摩擦压力
固体颗粒与模壁间的摩擦压力Pf同侧压力有如下关系:
Pf=kPr (1-59)
式中,k——固体颗粒与模壁之间的摩擦系数。
将式(1-59)代入式(1-58)得
Pf=kξPZ (1-60)
3.轴向压力沿固体颗粒层厚度的变化
图1-67所示为单冲压片机冲模内距上冲底面深度h的被压制固体颗粒层的相对位置及其轴向受力分析图。

图1-67 轴向力沿固体颗粒层厚度h的变化
1—上冲;2—料粉;3—颗粒层;4—下冲;5—中模
当颗粒层处于图1-67(a)所示位置时,由静力学原理得
FZ-Ff-(FZ+dFZ)=0 (1-61)
将,Ff=(πDdh)Pf及Pf=kξPZ代入式(1-61)得
(1-62)
积分并整理得
(1-63)
代入边界条件h=0时PZ=P上冲得
(1-64)
式(1-64)表明单冲压片机压制过程中轴向压力与固体颗粒层厚度和直径成指数变化关系。由式(1-64)可见,直径较大的片子所需的压制压力比直径小的片子要小,这是因为随固体外形尺寸的增加,固体的比表面积相对减小,固体与模壁的相对接触面积减小,因而消耗于外摩擦的压力损失也相应减少。
图1-68所示为单冲压片机和旋转压片机轴向压力沿固体颗粒深度的变化情况。由于旋转压片机在压制过程中上、下冲同时加压,两侧的轴向外压力同时沿固体颗粒两侧表面向内部的中间对称面递减。

图1-68 单冲压片机和旋转压片机轴向压力沿固体颗粒深度变化的比较
【例1-3】 分别用单冲和旋转压片机压片。终态时,测得两压片机上冲压力均为400kgf,压得片厚均为4mm,单冲压片机下冲力300kgf,其他条件一致。
求:两机距片顶3mm处的片剂层所受的压力各为多少千克?(得数取至整数)
解:①对单冲压片机分析如图1-69(a)所示。
根据;代入边界条件h0=4mm时,P上冲=400kgf,P下冲=300kgf;令
,得:
300=400e A × 4
或
将所求A,h=3mm及P上冲=400kgf代入得
②对旋转压片机分析如图1-69(b)所示。

图1-69 [例1-3]附图
由对称原理和图1-69(c)得PZ, h=3=PZ, h=1。将P上冲=400kgf,h=1mm代入得
PZ, h=3=400e A × 1
整理得
结论:单冲机和旋压机距片顶3mm处片剂层的压力分别为322kgf、372kgf。
说明旋转压片机压片时,片剂受力更均匀,压片质量更好。
如上所述,外摩擦力造成了压力损失,使得片剂内部力和密度的分布不均匀,影响了压制质量。为减少因摩擦出现的压力损失,可采取如下措施:
①添加润滑剂;
②提高冲头和中模的光洁度和硬度;
③改进压制方式(如采用双面压制或多次压制等)。
式(1-64)说明:如物料中的某一成分出了问题(如变质或错料使侧压系数增大)或因操作不当(如装料量或冲头位置调节不当造成产品尺寸变化),都可能造成产品因硬度下降而出现无规律破损的现象,这种情况下,只能通过相关的质检手段找出问题并加以解决。
4.固体颗粒内部力的分布
固体颗粒在压制过程中受力是不均匀的。Train曾在直径50mm的圆形中模中充填160g碳酸镁,在水压机上进行7个不同压力的试验。在粉末中的不同层位置有压敏电阻,借以观察固体内部受力的分布状态。试验结果如图1-70所示,图中各曲线为等压线。
将上述实验的成型片子精确切割后分别测定其重量和体积,可得到片子的相对密度分布图,图形与图1-70相似。

图1-70 碳酸镁的压制试验结果
高压或高密度区位于靠近上冲的圆周处,另一高压区位于靠近下冲的轴心处。可见,在与上冲相接触的片子最上层压力和密度从中心到边缘逐步增大;在片子的内部,压力和密度自上而下逐渐降低,但在靠近模壁处,由于外摩擦的作用,压力和密度的降低比片子中心大,以致在片子底部的边缘压力和密度比中心的密度低。因此,片子下层压力和密度的分布状况和上层相反。
实践表明:增加片子的厚度会使压力分布的不均匀性增加,而增大片子直径有利于改善压力分布的不均匀性。采用光洁度很高的中模和冲头,在料粉中加入润滑剂等减小外摩擦系数,可以改善片子内部的压力分布和密度分布。
(六)片剂的出模力与弹性后效
1.固体在压力消除时的弹性膨胀
在压制时由于受到外力的作用,固体颗粒发生弹性及塑性变形,体积发生收缩。
压制终了时,上冲移去,片剂出模。其间的片剂体积会发生弹性膨胀,对片剂出模过程及出模后的形状等均会产生影响。
根据Leigh所作的固体在压力下变形的研究,按固体在受压与压力消除时的性质可将其分为2种类型。
(1)完全弹性体 如前所述,对圆柱物体施以轴向压力,则在径向产生径向压力,其关系如式(1-58):Pr=ξPZ。
若片子是完全弹性体,在轴向力消除后,径向力恢复到零,见图1-71。压片后上冲移去时,物料复原,片子可自由地从中模内移出,压制却无法实现。

图1-71 弹性体的压缩循环
(2)发生塑性变形的固体 如图1-72所示,设所施加的外力超过固体的屈服点A,则该固体发生塑性变形,轴向压力PZ与径向压力Pr的关系与屈服值S有关。屈服值可由线段BA延伸至横坐标得到,过屈服点的线段AB的斜率为1,故可得
Pr=PZ-S (1-65)

图1-72 出现屈服应力的压缩循环
若到点B后减小轴向压力,此时径向压力的降低将比轴向压力的降低小k倍,降压线段BC平行于线段OA。在达到C点时又发生屈服现象,以后按线段CD下降。线段CD与线段AB平行,方程为Pr=PZ+S。可见压缩结束后仍有模壁压力S作用于固体之上。
减小外加压力,B点将会降低,模壁压力也可减小。
2.片剂的出模压力
外加压力去除后,模壁的径向压力仍会作用于成形的片子。使片子从中模脱出仍需一定的力,这个力称为出模力。出模力与压制压力、粉末性能、片子密度、片子尺寸、中模和润滑剂等有关。
如物料为完全弹性体,压制外力去除后片子的出模力为零;如为完全塑性体,则出模力等于压缩终了时固体与模壁的摩擦损失。通常情况下,片子在外力消除后会有弹性膨胀发生,片子沿轴向伸长,侧压力也会减小,出模力介于零和压缩终了时的摩擦损失之间。物料弹性越大,出模力的下降就越大,反之亦然。
3.弹性后效
在压片中,当除去冲头的压力并把片子移出中模之后,由于内应力的作用,片子发生弹性膨胀,这种现象称为弹性后效。
弹性后效计算公式为
(1-66)
式中,δ——沿片子厚度或直径的弹性后效;l0——片子卸压前的厚度或直径;l——片子卸压后的厚度或直径。
固体颗粒在压制中发生弹性或塑性变形,在片子内部聚集很大的内应力(弹性内应力),其方向与颗粒所受的外力方向相反。当外力消除后,弹性内应力释放,颗粒的外形和颗粒间的接触状态会发生改变,片子因此而发生弹性后效。由于片子受力的大小和方向不同,所以弹性内应力也不相同。片子的弹性后效具有方向性,由于轴向力比侧压力大,故轴向的弹性后效比径向的弹性后效大。一般来说,片子从中模脱出后片厚可增大0.5%~3%。片子之所以发生顶裂和裂片,也是弹性膨胀的缘故。
(七)旋转式压片机构造及组成
1.旋转式压片机的分类
旋转式压片机是片剂生产中应用最多的压片机。按转盘上的模孔数可分为16冲、19冲、27冲、33冲等。如按转盘旋转一周充填、压缩、出片等操作的次数,又可分为单压、双压等。
单压指转盘旋转一周只充填、压缩、出片各一次。单压压片机冲数有12冲、14冲、15冲、16冲、19冲、20冲、23冲及24冲等,现已很少见到,目前常用的单压高速压片机的冲数则要更多(如GZP40高速旋转式压片机为40冲)。
双压指转盘旋转一周完成上述操作各两次。双压压片机的冲数有25冲、27冲、31冲、33冲、39冲、41冲、45冲及51冲等。
双压压片机有两套压轮,为避免机体同时承受两倍的冲头压制力,减少振动及噪声,设计时采用两套压轮交替加压的方式,故压片机的冲头数多为奇数。
药厂采用的普通旋双压压片机多为33冲压片机,其中ZP33型旋转压片机的性能见表1-11。
表1-11 ZP33型旋转压片机主要性能参数

该压片机具有操作方便、使用安全可靠等优点,适用于生产各种圆形药片。但不适用于半固体、潮湿的粉末和极细粉末的压制。对于异形片的压制,需采用装有异形冲头的压片机完成。
2.旋转式压片机的组成
旋转式压片机由动力传动、加料、压制及吸粉4部分组成。
(1)动力及传动部分 电机安装在机座内部,机轴固定有无级变速轮,通过三角带带动机座上部的传动轴旋转。传动轴水平装置在轴承托架内,中间装有蜗杆,由此蜗杆带动转盘上的蜗轮运转。
传动轴的前端为试车手轮,另一端为锥形圆盘离合器。离合器靠弹簧压力所产生的摩擦与传动轴上的皮带轮接触。若机器的负荷超过弹簧力时,离合器就发生打滑,保护机器免受损坏。
压片机的调速是靠调节电机轴上的无级变速轮的有效直径来实现的。无级变速轮内部有两片锥形活片,活片端部铣有沟槽。两活片在沟槽处相互啮合,借以调节三角皮带在槽内的有效直径,从而达到无级变速的要求。两片活片各靠6个弹簧两面顶住,产生正压力。调速的方法是移动电动机,以使两活片之间的距离改变,从而改变有效直径。
(2)加料部分 在转盘的模盘上方装有圆形锥底下料斗和月形栅式加料器。加料器底部距模盘0.03~0.1mm,可将料粉颗粒刮入中模孔内,并将模口刮平,以使所压制的片子符合重量差异的要求。颗粒的流量由下料斗出料口距模盘的高度来控制,高度的调节以控制加料器内颗粒无外溢为准。
(3)压制部分 压制部分包括具有3层结构的转盘(上层为上冲转盘、下层为下冲转盘、中层为中模转盘)、冲模、上下轨导、上下压轮及充填调节装置等。
①转盘 转盘为一整体铸件,周围均布着垂直的模孔,见图1-73。转盘垂直套在固定的立轴上,转盘的最下层装有蜗轮。由电机经皮带传至传动轴的动力经蜗杆传给转盘下方的蜗轮,转盘带动冲头及中模转盘绕立轴作顺时针方向旋转。

图1-73 旋转压片机转盘装置
1—转盘;2—蜗轮;3—蜗杆
②冲模 压片机冲模包括上冲、下冲与中模,如图1-74所示。该图为我国最常用的ZP19及ZP33压片机所用的冲摸。

图1-74 冲模
1—上冲杆;2—中模;3—下冲杆
上下冲杆直径22mm,全长115mm,中模外径26mm,高22mm。可压药片直径5.5~12mm,每隔0.5mm为一种规格,共14种。
冲头形状依所压出的片子的形状有浅凹形(圆片)、深凹形(深糖衣片)、平面底角圆弧形(平片)及平形等,如图1-75所示。

图1-75 冲头的形状
因中模在压片过程中承受很大的压力,所以其制造材料应具有较高的强度和硬度。轴承钢强度较高,并具有一定的耐腐蚀性,在制造冲模时较多采用。对较难压制的中草药等物料,常在中模内衬以硬质合金衬套以延长其使用寿命。冲模加工时需经热处理,以达到规定的硬度。中模的硬度一般应高于上、下冲的硬度。冲模应具有较高的精度及光洁度,冲头和中模应有互换性。
为提高生产能力,在小直径片子的压制中,一支冲杆上可以固定 2~3个冲头,中模上也要开相应的模孔。此种情况只在异形片压机上才有。由于在模盘上距转盘中心不一致及离心力的差异,多孔冲模可能会增加片重差异。
异形片压片机的冲杆具有方向性,通常在冲杆的一侧固定有滚轮或凸出滑块,操作时,滚轮或滑块在随转盘一同旋转的垂直滑道内运动,可以避免冲杆自转。
③上下轨导装置 压片机在完成充填、压片、出片等过程中需不断调节上、下冲间的相对位置,冲杆升降的调节由轨导装置完成。上、下轨导均为圆环形,上轨导装置位于转盘的上方,固定在立轴上;下轨导位于转盘的下方,固定于主体的上平面。
上轨导装置由导盘及轨导片组成。轨导盘为圆盘形,中间有轴孔,其固定于立轴上,轨导盘的外缘镶有经过热处理的轨导片,用螺钉紧固在轨导盘上。上冲尾部的凹槽沿着轨导片的凸边运转,完成有规律的升降,如图1-76所示。

图1-76 旋转压片机上、下轨导装置示意图
1—轨导盘;2—轨导片;3—上压轮装置;4—上冲安装活板;5—下轨导;6—下压轮装置;7—充填调节装置;8—下冲安装孔盖板
在上轨导的最低点装有上压轮装置。下轨导被螺钉紧固在主体之上。当下冲在运行时,它的尾部嵌在或顶在轨导槽内,随着轨导槽的坡度完成有规律的升降。在轨导圆周范围内的主体上平面装有下压轮装置、充填调节装置等。
④上压轮装置 如图1-77所示,上压轮套在曲轴上,轴外端有杠杆,其下端被连接的弹簧压住。当上压轮受力过大时,由曲轴的偏心力矩作用使弹簧压缩,增大了上、下压轮间的距离,以保护机器和冲模的安全。

图1-77 上压轮装置
1—上压轮;2—曲轴;3—杠杆;4—弹簧;5—螺杆
⑤下压轮装置 如图1-78所示,下压轮位于主体的槽孔内,轮的上缘凸出于主体的上平面,其凸出的高度可调,借以调整压制力。

图1-78 下压轮装置
1—下压轮;2—下压轮曲轴;3—蜗轮;4—蜗杆
下压轮套在曲轴上,曲轴的外端装有蜗轮,蜗轮与可旋转的调节蜗杆相连。用手转动蜗杆使曲轴的偏心向上时,压轮上升,则压制力增加,反之则压制力减小。以此来控制片剂的厚度和硬度。
⑥充填调节装置 充填调节装置是用来调整模盘上面加料器最后刮粉时下冲位置的,用以调整中模内的药粉量,以达到片重偏差要求。充填调节装置装在主体的内部,主体上平面的有槽孔使月形充填轨凸出其上。它的下部为一螺杆,螺杆外为一螺母,利用螺母外围的蜗轮蜗杆装置可使螺母转动。由于螺母在原位转动,使得与月形充填轨相连的螺杆可以垂直升降,调节月形充填轨凸出主体上平面的高度,从而控制最后刮料时下冲的位置,见图1-79。

图1-79 充填调节装置
1—月形充填轨;2—螺杆;3—螺母(外为蜗轮);4—蜗杆;5—手轮
(4)回收部分 回收部分也称吸粉部分。吸粉装置位于机座内部,其吸粉管自机座侧面伸出,吸入口装在模盘附近。它的作用是将压片过程中冲模上产生的飞粉和下漏的粉末回收,以避免污染环境并保护设备。
机座内部的电动机通过带动鼓风机,通过吸粉管将粉末吸入吸粉箱下部的贮粉室,粉末下坠于贮粉室底部,气体则迂回上升。经过数个重叠的滤粉盘,粉末进一步得到分离,气体由滤粉盘上部的开口进入滤粉室,最后被装在滤粉室内部的鼓风机引出,见图1-80。

图1-80 吸粉装置
1—吸粉管;2—贮粉室;3—滤粉盘;4—滤粉室;5—鼓风机
如粉末很轻不易净制时,可采用湿法净制,即在滤粉盘内放一半清水,以提高净制效果。有的压片机用滤袋代替滤粉盘,因滤袋所占空间较大,鼓风机需置于吸粉箱的外部。
(八)其他压片机简介
1.高速压片机
高速压片机的压片速度并无明确界限,其“高速”也是相对而言。对于湿颗粒法压片高速压片是指出片速度在每秒15片以上(双压式一般可达每秒30片以上)。
中模内充填速度,冲头冲击,机器过载,片子顶裂和裂片等问题限制了高速压片机的应用。
近些年开发的一些技术例如粉末的强制充填、压片的缓冲机构、锥形中模内孔的利用等,突破了上述诸多障碍,结合压片机机构的改革和新型制剂工艺的发展,使高速压片在工业上的应用日趋广泛。
(1)多次压缩压片机 普通旋转式压片机转盘直径较小,冲杆底面积较大,虽有利于片剂的成形,但冲模数量少,单位时间出片数量少。此外,由于冲杆底面积大,与轨导的摩擦还会增加。
如在压片机上安装两套压轮,使每一片剂在成形过程经受两次压缩,不仅可延长压缩时间,且可降低冲杆轨导的损伤。这种重复压缩的方法就称为二次压缩,这种压片机就是二次压缩压片机。同理,也可有三次压缩压片机。
二次压缩压片机可有两种方式:预压方式和双压方式。预压方式采用直径较小的预压压轮(ϕ90mm)将颗粒预压,然后用正常压轮(ϕ180mm)再次压制,二次压缩开发初期多用此法。另一方法是采用直径相同的两套压轮(ϕ180mm)压制。
图1-81为二次压缩压片机的展开略图。固体颗粒充填于中模后,经一次和二次压缩后,下冲上升出片,各次压制力可分别由调节下压轮的升降高度来完成。

图1-81 二次压缩压片机原理
1—料斗;2—加料器;3—压轮;4—模盘;5—下轨导
图1-82为多次压缩的应力-应变曲线,曲线内部所包容的面积代表所消耗的功率。由图1-82可以看出,在多次压缩的情况下,使用较小的应力可以达到较大的应变,可以减少压片的功率消耗。但随反复压缩次数的增加,物料的塑性变形部分减少,最后可接近于弹性变形。可见,多次压缩的次数是有一定限度的。

图1-82 多次压缩的应力-应变曲线
压片机的压缩时间如前所述,包括动压缩时间和压缩停滞时间。
多次压缩的总时间为每次压缩的动压缩时间和压缩停滞时间之和,计算公式为
(1-67)
式中,τ0——多次压缩的总时间,s;Δhi——第i次压缩时的压缩距离,m;ri——第i次压缩时的压缩半径,m;N——回转盘的转速,r/min;n——压缩次数;de——压片的直径;R——回转盘的半径,m。
式中的第1项为动压缩时间,第2项为压缩停滞时间。
若各压轮半径ri相等,且时,动压缩时间与压缩次数的关系如图1-83所示。由图1-83可见,n>4时的曲线斜率较n≤3时的小,时间增加率下降。此外,如n增加则压轮数随之增加,磨盘直径必增加很多。所以,多次压缩的次数限度为3次。

图1-83 动压缩时间与压缩次数关系
片剂在多次压片机中所经受的压缩次数较多,内部密度分布也较均匀,使得其强度提高,顶裂现象下降。
(2)倾斜压轮式压片机 压片机在压制时承受很大的力,为防止机件和冲模损坏,压制普通黏性粉末时,压片机转速一般最高不超过50r/min。异形片压制时冲模的摩擦力较大,最大转速不超过40r/min。
为改善压片机的受力状态,开发了倾斜压轮压片机。
图1-84所示为倾斜压轮压片机原理,压轮为球形台状,其工作面为球面,工作面与冲杆接触点的轨迹为一复杂的曲线,冲杆的运动轨迹为一椭圆形。

图1-84 倾斜压轮压片机工作原理
1—上压轮;2—下压轮
实践证明,倾斜压轮式压片机以比普通压片机高得多的转速操作时,冲头和中模的损伤程度远优于普通压片机。若与3次压缩压片机相比,倾斜压轮式压片机所压制的片剂其顶裂率大致相同,说明该压片机的片剂顶裂率较低,压制质量较好。
2.减压压片机
减压压片机的压片机构密闭在真空容器内,加料与出片均在密闭容器内进行。
减压压片具有下列优点:因固体内空气量少,故粉末容易充填,所需压片压力小,应力分布均匀。对空气中易起变化的药品,可在密闭容器内实施惰性气体保护。
与常压下相同,减压下的片剂强度随压制压力的增加而加大。减压下的片剂强度通常较常压下高,但在高真空(1.33×10-3Pa)条件下,粒子表面附着水分子(极性非常强)消失,影响了固体粉末间的黏合力及成形性,片剂强度却较常压下低。
减压压片机的机构复杂,片剂的顶裂和裂片率也较高,目前在制药工业中用量有限。
3.多层片压片机
双层和三层压片机的结构原理基本相同,可用于压制隔离层片剂(将不宜直接接触的两种药物中间用隔离层遮断而压制成的三层结构片剂)和多层长效片剂(按速释层和缓释层压制成的双层结构片剂)。多层片压制有两种方法:
①一次压制法 将各层药粉按顺序充填于中模后,一次压制成形;
②预压法 底部各层分别充填并经预压后,将上层充填,再以重压压制成形。
预压法是生产中常用的方法。一次压制法因各层药量不易控制,且压制出的片剂分层不明显,故较少使用。
三层压片机的预压法成形过程如图1-85所示。

图1-85 三层压片机的预压法成形过程
多层片层间的结合力与预压力、粉末粒径有关。预压力较大时,层间分层明显,但层间结合力较弱。所以,预压力的大小应以能将压制物取出以供重量检测为准,一般需将预压力控制在较低的水平。
粉末过细会降低层间结合力。所以一般优先考虑较粗的粒径。此外,各层间在压制时不应有过剩的粉末。
多层片压片机主要结构原理与旋转式压片机相似。各层药粉贮于单独的料斗中,机上配有预压压轮和重压压轮。按充填→预压→充填→……→充填→预压→充填→重压→出片的顺序布置。此外,各层均有取样装置,以供片重检测之用。
因各层充填量较少、充填层较薄,所以多层片压片机压出的片子各层厚度不易均匀。多层片压片机的出片速度较慢,大约在每秒8~9片左右。
4.压制包衣压片机
压制包衣是将片芯及作为包衣材料的固体粉末压制成包衣片的方法。包衣片有圆形平片、圆形凸片及异形片等,外观上与一般片剂相同。因包衣是干式操作,所以适用于对热、水不安定药品的包衣。此外,可按用途将药物置于片芯或包衣层中制成多层片(如肠溶片等)。与糖衣片相比较,包衣片的包衣层机械强度较低,而透气性、透湿性较高。压制包衣的过程一般为一次压制成形,如图1-86所示。

图1-86 包衣片的压制成形过程
压制过程中如片芯置偏、置斜或片芯形状与片剂外廓不适合等,压缩后会出现因片芯膨胀而引起的裂片。因此,片芯及包衣层的形状、大小以及物料性质均对压制包衣操作有明显的影响。
对表面粗糙的片芯和粒度较细的包衣粉末来说,因细粒子可充填于片芯粒子间隙的缘故,片芯与包衣层结合的情况较好。
一般的压制包衣压片机是由一根主动轴带动两台压片机组成。第1台专用于片芯的压制,然后通过供片装置送往第2台并埋于外层粉末中压制成包衣片。有时,也采用在其他压片机预先压制片芯然后供给包衣压片机压制包衣片的方法。
此种压片机的关键部分有3处,即将片芯准确置于包衣材料中心部位的控制机构(置芯机构)、将位置不准确的片芯检出的控制机构及将无芯片剔出的控制机构。在完成上述操作时不应影响整机的连续运转。
该种压片机出片速度较慢(操作速度较快时,片芯难以准确置入),实际生产场合的出片速度大约8~9片/s。
本章小结
1.本章所涉及的粉碎、筛选及造粒(重点为干法造粒中的压片),均为制备药物粉体的常用单元操作,各自的机理、原理均需掌握。本章同时介绍了固体粒子粒径及其测量方法、力学性能等,是课程理论讲解中的基础知识,需要了解。
2.熟悉粉碎能量计算、筛效率计算、压片速度及片剂受力计算,对指导生产实际(如操作成本核算、机械故障排除及找出产品质量原因等)具有指导意义。
3.了解粉碎、筛选、压片设备的构造、工作原理、操作流程及适用范围,可以针对不同生产场合作出合理的选择,进而指导实际生产。
4.在制剂生产技术不断发展的今天,新型制剂设备不断涌现,了解其适用范围、工作原理及其演变过程,为实际生产中是否采用、为何采用新设备提供依据。