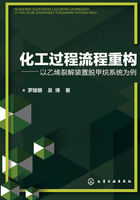
前言
在化工生产过程中,为实现精细的分离任务,往往需要多种不同类型单元设备的协同配合,且随着设备的运行,部分设备的结构和性能会发生改变,并直接影响到整个系统关键产品的分离及能量的高效利用,成为制约系统节能减排的瓶颈。以化工过程的分离装置为例,核心操作单元精馏塔随着设备的长期运行,塔内结垢或者进料组成及流量等发生改变,可能会导致精馏塔内部塔板的传热/传质异常,塔板利用率下降。传统的装置内部塔板结构改造措施,操作复杂且成本较高。本书围绕进料位置不合适引起的塔内部传热/传质异常的问题展开,研究精馏塔系统进料瓶颈的识别方法,探讨消除进料瓶颈进料位置调整的流程重构策略,并设计出重构后系统的再优化及关键过程设备的控制策略。以乙烯裂解过程多股进料脱甲烷装置为例,提出了化工过程流程重构的设计、识别及操作条件再优化的系统理论和实践方法。
①对于实际装置上开展理论研究工作的难题,可以通过建立相似功能的仿真系统来实现。针对复杂系统中的循环物流的问题,提出基于寄存器思想的数学模型,进而实现对整个脱甲烷塔装置建模,同时能为化工系统中循环系统的建模提供解决策略。
②通过精馏塔内部的传热/传质组合曲线的图示法,有效识别出精馏塔内部的传热/传质的瓶颈位置,并指出系统中进料瓶颈的位置。通过在乙烯裂解过程中的关键过程——多股进料脱甲烷塔装置上的仿真应用研究,针对原始设计,采用进料瓶颈识别的方法能够有效找到多股进料脱甲烷塔装置中脱甲烷塔的进料瓶颈。
③通过对进料瓶颈处进料位置的调整,对于塔内部的传热/传质的影响进行分析,采用脱甲烷塔装置瓶颈进料位置调整的流程重构方法,被证明对于系统的节能及降低内部的传热/传质的瓶颈具有显著的作用。对产品质量改变和处理量调整两个方面的研究证实,流程重构方法均能有效降低多股进料脱甲烷塔系统的能量消耗,是一种可以采用的精馏塔的节能降耗改造策略。
④流程重构后多股进料脱甲烷塔装置的操作条件未必处于最优状态,需要重新优化操作条件。本书提出的脱甲烷塔装置核心流程的单塔优化与扩展装置的复合塔优化的实施方法,主要是从装置仿真级的角度出发,分别采用了单塔优化和复合塔优化的策略来解决能量优化的问题。关于操作优化所产生的经济及节能效益,建议采用考虑进料操作的复合塔优化策略,但单塔优化也能得到系统的次优操作条件且容易实现优化。
⑤多股进料脱甲烷塔的控制直接关系到产品的分离和系统的能耗,过程控制与协同优化策略能同时实现系统的关键指标的控制及系统能耗的最优化,即通过主要变量的目标指标控制,次要变量的协同优化以得到系统能耗最低的控制策略。通过脱甲烷塔的塔顶和塔底的控制及协同优化的实施,能够有效降低原始操作条件下的系统能耗。另外,在进料位置切换条件下,需要考虑生产指标控制的问题。根据塔顶和塔底指标在进料位置切换时的动态分析,针对小范围切换,采用常规控制策略即可满足对塔顶和塔底指标的控制。指标控制与进料位置切换在需要的时候也能够同步进行。对多股进料脱甲烷塔的仿真结果表明,同步切换比分步切换的控制效果更好。
由于笔者水平有限,编写过程中不足之处在所难免,希望广大读者批评指正。
著者