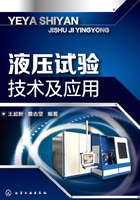
1.2 液压试验的主要作用
(1)验证设计要求与装配质量
在设计液压元件时首先设定性能要求,如压力、流量、寿命、动态特性等,根据这些性能选择材料,确定配合间隙、加工精度、油口大小、摩擦力等,当液压元件制造成功后,还需通过试验来检验其性能是否达到要求。
按照图纸对加工精度、光洁程度、表面处理、装配要求通过试验获取的结果进行检验,也能反映加工、装配的质量。
(2)为研发新的液压元件提供支持
研发新的液压元件,一般是从理论分析、建立数学模型、进行仿真分析提出液压元件结构,通过设计计算设计出加工图,进而通过加工、装配组成新的液压元件。此外,必须通过试验,测定其性能是否达到研发时提出的性能要求,若未达到,必须修改原研发方案,经过不断改进,方可实现研发新元件的目的。
(3)检验维修后液压元件的性能
液压元件维修后,其性能恢复到什么程度,不通过试验是很难确定的,这将决定该液压元件能否重返原液压系统工作。一般情况下,维修后的液压元件的性能均有所降低,但降低到什么程度,是否仍可以继续使用,应通过试验来判定,切不能依靠想象来决定。
(4)对在用液压元件进行故障诊断
在使用一段时间后,系统的液压元件必然有不同程度的损坏,个别元件损坏比较严重时,直接影响液压系统正常工作。一般情况下,取出已损坏的液压元件,在试验台对其性能进行检测,检测中可以发现损坏的部位,进而对其进行修复,不能修复的元件作报废处理。
(5)检验新购或库存液压元件的性能
对新购或库存液压元件需进行性能检测。新购液体元件由于出厂、运输等原因对其性能会造成影响;库存液压元件由于仓库条件差、存放时间长、搬动等原因,也会对其性能造成影响。为了使更换上线的液压元件可靠性高,使生产线能顺利投入运行,对新更换的液压元件进行性能检测也是必要的。总之,对新购或库存液压元件进行性能试验是为了验证该元件是否达到产品样本要求,为液压系统正常工作提供保障。
(6)液压系统调试
液压元件组装到主机上之后,要检验在各种实际应用工况中的表现是否符合设计时的预想,要进行测试试验。
(7)液压系统状况实时监测
重大设备在运行时,都需要进行实时监测,包括液压参数。例如,远洋舰船舵机液压系统的压力都是持续监测记录的,即使没有突发性故障,在返回母港后,也会读取分析。如果设备处于不便接近的位置,如风力发电机,则利用无线通信网络和因特网远程传输数据,以便及时了解系统状况,在发生严重事故前,尽早发现问题,预防故障。
(8)液压课程教学
在机电类专业液压课程教学中,一般安排理论课、实验课和课程设计等环节,液压试验是不可或缺的中间环节。学生在理论课的基础上,由此更加深入具体地掌握液压技术的工作原理及设计应用方法,后续的液压课程设计才能顺利进行。