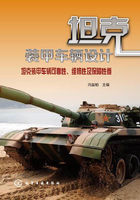
第二节 坦克装甲车辆可靠性与维修性
一、坦克装甲车辆可靠性与维修性的基本概念
可靠性(Reliability)和维修性(Maintainability)是装甲车辆的重要战术技术指标,是构成装甲车辆综合效能的重要因素,是由设计赋予、生产保证,并在使用中体现出来的装甲车辆本身的一种固有质量特性。
1.可靠性
(1)可靠性的定义 国家军用标准GJB 451—90给出的可靠性定义是:产品在规定的条件下和规定的时间内,完成规定功能的能力。可靠性的概率度量亦称可靠度。1991年美军5000.2(DODI)给出的可靠性定义为:系统及其组成部分在无故障、退化或不要保障系统的情况下执行其功能的能力。它更强调了可靠性与保障的关系。
(2)可靠性有关的主要参数
①可靠度 装备的寿命T是一个非负随机变量。装备的可靠度表示装备在指定的时间区间[0,t]内不发生故障的概率,用R(t)表示:
R(t)=P(T>t),t≥0
②故障概率分布函数 又称为寿命T的概率分布函数,即[0,t]内发生故障的概率,用F(t)表示:
F(t)=P(T≤t)=1-R(t),t≥0
装备的寿命分布是连续时,称故障概率分布函数的导数为故障概率分布密度函数,或称故障概率密度函数,记为:

③故障率函数 故障率表示产品在规定的条件下,工作到t时刻后,尚未发生故障的产品在单位时间内发生故障的概率,记为λ(t)。某时刻t的故障率称为瞬时故障率。
设T是规定条件下某产品的寿命,其故障概率分布函数为F(t),故障概率密度函数为f(t),此时事件“产品工作到时刻t后”可表示为“T>t”。事件“产品在(t,t+Δt)内发生故障”可表示为“t<T≤t+Δt”。于是产品工作到时刻t后,在(t,t+Δt)内产品发生故障的概率可以表示为条件概率P(t<T≤t+Δt|T>t),把这个条件概率除以时间间隔Δt以后,就得到在Δt时间内的平均故障率,当Δt→0,就得到在时刻t瞬时故障率:

上式两边积分,可得:

于是


④平均寿命 平均寿命是产品在规定的条件下,持续工作时间的平均值。对于不可修产品(如装甲车辆的一些零部件)指故障前工作时间的平均值,记为MTTF,称为平均故障前时间;对于可修产品(如装甲车辆的大部件、整车)是指相邻故障间隔时间的平均值,记为MTBF,称平均故障间隔时间。
已知产品寿命T的分布密度函数f(t)时,平均寿命记为E(T),定义如下:

当已知产品的寿命分布时,平均寿命是一常量;当不知道产品寿命分布时,平均寿命是一样本的统计量。仅当产品寿命分布服从指数分布时,平均寿命才等于故障率的倒数。
(3)耐久性 坦克装甲车辆这样的以机械产品为主的复杂系统,耐久性指标是必不可少的,有时甚至比可靠性指标更重要。按GJB 451—90的规定,耐久性是指“产品在规定的使用维修条件下,其使用寿命的一种度量。它是可靠性的另一种特殊情况”。对该定义的理解应明确以下几点。
①使用寿命和耐久性损坏 既然耐久性是使用寿命的一种度量,就有必要首先搞清什么是使用寿命。根据GJB 451—90,使用寿命是指“产品从制造完成到出现不修复的故障或不能接受的故障率时的寿命单位数”。从中可以看出,使用寿命是与某种故障直接相关的。
这里讲的“不修复的故障”至少包含三种情况:一是指无法修复的故障,报废故障件用更换新品的方法来恢复功能;二是在部队的基层级和中继级维修单位无力修复的故障,要恢复功能,只能大修;三是从经济效益考虑已不值得修复的故障,也只能报废,用更换新品的方法来恢复功能。至于“不能接受的故障率”,实际上也可归结为从经济效益考虑已不值得修复。
从耐久性的角度出发称这类故障为耐久性损坏,它可定义为无论从技术上考虑,还是从经济上考虑,使产品都不能再继续使用而必须进行更换或大修的一种耗损型故障。这里强调耐久性损坏是一种“耗损型故障”。
②使用寿命的度量和耐久性要求 由于产品的实际使用寿命值是一个随机变量,只能用概率来度量。根据GJB451—90中对耐久性的定义和对使用寿命的定义,耐久性的概率度量可定义为:耐久性是产品能够满意地达到设计使用寿命或大修寿命而不发生耐久性损坏的概率。也可称不发生耐久性损坏的概率为耐久度。耐久性和可靠性只是研究的故障范围不同,规定时间的性质不同,其基本属性是一致的,可靠性一些基本特征同样适用于耐久性。所以耐久度也可以认为是研究耐久性损坏的一种可靠度。
装甲车辆的耐久性要求,一般用两个指标表示:一个指标为规定的使用寿命(或大修寿命);另一个指标是达到规定使用寿命的概率(耐久度)。例如,美国M1坦克动力装置的耐久性要求是:在其规定的使用寿命4000mile行驶中,不发生耐久性损坏的概率要求为0.5(置信度75%时)。中国对可修产品,如发动机的耐久性要求是:在规定的大修寿命500h的使用中,不发生耐久性损坏的概率(耐久度)为0.63(置信度为0.75时);对不可修产品,如负重轮的耐久性要求是:在规定的使用寿命6000km的行驶中,不发生耐久性损坏的概率为0.67(置信度为0.8时)。
目前装甲车辆采用的统计试验方法是:一定数量的样本试验到规定的使用寿命(定时截尾),根据出现耐久性损坏的次数,用非参数法计算概率(耐久度)的单侧置信下限,大于要求值则为达到耐久性要求,计算公式如下:

式中 Dr——不发生耐久性损坏的概率(耐久度);
n——参试样本数;
r——发生耐久性损坏数;
Fα——F分布上侧分位数;
α——置信水平。
也可直接查在一定置信度下由试验样本数和故障数(耐久性损坏数)确定的可靠度(耐久度)表。
2.维修性
(1)维修性的定义 GJB 451—90的维修性定义是:产品在规定的条件下和规定的时间内,按规定的程序和方法进行维修时,保持或恢复到规定状态的能力。维修性的概率度量亦称维修度。
(2)维修性的主要参数
①维修度 是可修复产品在规定的维修条件下和规定的时间内,完成产品修复(使之保持和恢复到规定状态)的概率。维修度是维修时间t的函数,记为M(t),亦称为维修度函数,其值域为[0,1]区间。若用非负随机变量T来描述维修时间时,维修度函数表示指定时间区间[0,t]内产品修复的概率:
M(t)=P(T≤t),t≥0
应该明确,这里指的“修复”包括预防维修和修复性维修(故障维修)两类维修活动,即维修度有各级预防性维修的维修度和各级修复性维修的维修度。像装甲车辆预防维修的维修度可以有一级保养维修度、二级保养维修度、三级保养维修度、小修维修度、中修维修度等。修复性维修的维修度也可以分基层Ⅰ级、基层Ⅱ级和中继级修复性维修的维修度,也可统计计算总的修复性维修的维修度。
②维修度分布密度函数 维修度函数M(t)对时间t的导数称为维修度分布密度函数,记为:

③修复率 也称维修率。一般情况下,修复率是时间t的函数,记为μ(t),表示到时刻t仍处于维修状态的产品,单位时间内被修复的概率,也称瞬时修复率。μ(t)的定义式如下:
μ(t)=m(t)/[1-M(t)]
μ(t)与维修度分布密度函数m(t)有如下关系:

④平均修复时间 现场的维修时间包括预防性维修时间和修复性维修时间,其平均值称为平均维修时间。平均修复时间是修复性维修时间的平均值,记为MTTR。MTTR的度量方法是:在规定的条件下和规定的时间内,产品在某一规定的维修级别上,修复性维修总时间与修复的故障总数之比。
当已知产品修复性维修的维修度分布密度函数m(t)时,MTTR由下式计算:

当修复性维修时间分布密度函数为已知时,MTTR为常量。研制中的产品只考虑平均修复时间,它也是产品的固有特性。仅当修复性维修时间服从指数分布时,平均修复时间MTTR才等于常量修复率μ的倒数。
(3)测试性 装甲车辆的测试性是指车辆本身能提供的及时确定其工作状态(可工作,不可工作或性能下降),并隔离其内部故障的一种设计特性。产品使用阶段的测试工作属于维修范畴,包括预防性维修中的检测和修复性维修的故障检测、隔离(故障诊断)及检验等活动,所以测试性原先是作为维修性的一个组成部分来对待的,随着科学技术的进步,特别是电子技术、计算机技术的广泛应用,坦克装甲车辆的性能越来越先进,结构越来越复杂,电子产品所占的比例越来越大,在维修过程中如何迅速地查找与隔离故障显得越来越重要。单纯依靠维修人员的经验和技术已远不能适应车辆维修发展的需要。因此,测试性的问题越来越突出,鉴于其理论与技术的特殊性,逐步把测试性作为一种独立的质量特性。
测试性主要包括两方面的因素:一是机内测试(BIT),它是指坦克装甲车辆自身提供的为检测、诊断或隔离故障的自动测试能力。完成机内测试功能的装置,就是机内测试设备(BITE),主要包括传感器、激励信号、响应数据处理及测试软件、硬件等。二是坦克装甲车辆自身(主要是硬件)的固有测试性,它是指仅取决于系统或设备的硬件设计,不受测试激励和响应数据处理影响的测试性。或者说,硬件设计要具有支持机内测试(BIT)和外部测试或自动测试设备(ATE)进行测试的特性。包括结构的合理划分、接口设置、与ATE兼容性等。
中国坦克装甲车辆的现役装备,测试性是个薄弱环节。随着中国新型坦克装甲车辆的研制发展,采用的新技术项目越来越多,微电子技术、计算机技术所占比重越来越大(尤其是火控系统),测试性已引起各方面的关注。提高机内测试能力,设置好检测接口,全面考虑主装备本身与外部检测设备的兼容问题,已成为装甲车辆研制发展中应予特别关注的一个技术发展问题。
二、复杂可修系统的可靠性数据统计
装甲车辆是典型的复杂可修系统,在可靠性数据统计中,仅用随机变量来描述在很多情况下已不能满足需要,下面简单介绍复杂可修系统可靠性数据统计的思路。
1.复杂可修系统可靠性数据统计的特点
(1)随机点过程 在研究不可修系统的寿命分布时,涉及故障率λ(t)、可靠度R(t)、故障概率分布函数F(t)、故障分布密度函数f(t)等,前面已介绍了这些参数之间的关系。不可修系统的寿命在数学上是用随机变量及其分布函数来描述的。但是对于装甲车辆这样复杂的可修系统来说,还要研究系统发生的故障随运行时间(这里的时间是指寿命单位,可以是小时、千米、次数、发数等)而变化的规律,由于系统发生故障的时刻Ti(i=1,2,…)是随机的,故可修系统故障发生的时刻可以看成是时间轴上依次出现的随机点。这种按一定的统计规律在时间轴上随机分布的点集就形成了一个随机点过程(简称点过程)。有的称这种时间轴上的点过程为事件流,在可靠性数据统计中称故障流。为研究计算落在时间轴上某区段中的点数(故障数),引入了计数过程的概念,研究时间轴上某区段故障数的随机点过程也称为故障计数过程。这种描述可修系统故障发生规律的随机点过程用故障强度(或称故障强度函数)作为其特征量。设系统在[0,t]中发生的故障数为r(t),则其故障强度为:
λ(t)=dE[r(t)]/dt
故障强度是时间的函数,其物理意义为系统在单位时间内发生故障的次数。它表明系统在时刻t发生故障的强弱程度,有的称其为故障率(与不可修系统的故障率是有区别的)。若已知系统的故障强度,则系统在[0,t]中发生故障次数的数学期望称累积故障强度函数(也有称均值函数的)可用下式计算:

这里说明可修系统与不可修系统在故障分布规律的数学描述上是有区别的,即从不可修系统的随机变量变成了可修系统的随机点过程。对于可修系统的故障分布,认为是时间轴上的一个计数过程。
(2)更新过程 有一些系统发生故障后经过修复又如同新的一样,即修复活动使系统发生故障后的可靠性水平又恢复到该系统刚开始工作时的水平,此时的故障强度又回到了开始工作时的水平。这种情况常见于一些简单的系统,当其关键件经换件修理后,状态如新,称为更新过程。
由修复如新导出的更新过程,其故障间隔时间为Xi=Ti-Ti-1,是一个随机变量并独立分布。此时的故障间隔时间Xi也可以看成是不可修系统多个样本情形时得到的数据,即可把Xi按大小排序,用不可修系统的统计方法来处理。
(3)非时齐泊松过程 对于复杂可修系统发生故障后,经过局部的维修、调整或更换零部件等措施,使系统的可靠性水平恢复到故障前瞬间的水平。此时的故障强度仍保持故障前瞬间的水平,这种情形为修复如旧。这个概念更符合复杂系统的实际情况,因为系统发生故障是由其中个别零部件的故障引起的,维修、调整或更换的是发生故障的个别零部件,而系统的那些没有故障的大部分零部件仍在继续使用,虽然经过修复后的零部件,其可靠性水平与故障前瞬间的可靠性水平相比有所提高,但对由众多零部件组成的整个系统而言,可靠性水平基本没有变化,即系统的复杂程度达到了系统的可靠性水平不会因为其中个别零部件的修复而发生显著的变化。装甲车辆就是这样的复杂系统。这种情况下的故障强度曲线在整个时间轴上是连续的,不会因故障而产生间断。
修复如旧的计数过程可以用非时齐泊松过程(Nonhomogeneous poisson process,简记NHPP)来描述。NHPP的定义如下:
若计数过程{r(t),t≥0}满足:
①独立增量性。即对于任意的n及互不相交的区间(ai,bi],i=1,2,…n,r(bi)-r(ai)互相独立;
②P{r(t+Δt)-r(t)≥2}=0(Δt);
③P{r(0)=0}=1。
若λ(t)非负,在有限区间上可积,则称{r(t),t≥0}为有故障强度λ(t)的非时齐泊松过程;
设{r(t),t≥0}为有故障强度函数λ(t)的非时齐泊松过程,则

N(t)为累积故障强度函数(如前式)。一般NHPP其故障间隔时间Xi既不独立也不同分布,即认为Xi的母体是变化的。
(4)威布尔过程模型 由于NHPP中故障强度λ(t)数学表达式的不同,NHPP可以有多种类型,装甲车辆可靠性数据统计时一般采用威布尔过程模型(AMSAA模型)。威布尔过程模型的故障强度为
λ(t)=abtb-1,(a>0,b>0)
式中,a为强度参数;b为形状参数。b>1时,λ(t)随时间增大;b=1时,λ(t)为常数;b<1时,λ(t)随时间减小。
(5)时齐泊松过程 当非时齐泊松过程的故障强度λ(t)=λ为一常数时,就退化为时齐泊松过程(Homogeneous poisson process,简记为 HPP)。此时其故障间隔时间Xi独立同分布,且服从参数为λ的指数分布。即此时系统处于偶然故障期。时齐泊松过程也可看成是更新过程的一个特例,较适合于电子系统。装甲车辆在预防维修时机合理,维修质量有保证的情况下,可近似用时齐泊松过程来描述。
2.威布尔过程模型的参数估计和检验
(1)参数a和b的点估计:
①用极大似然法求a和b的点估计:

式中,k为试验统计装甲车辆的样本数;n为故障总数;Si为第i个样本统计起始时间(里程);Ti为第i个样本统计截尾时间 (里程);ni为第i个样本在区间(Si,Ti]中发生的故障数;tij为第i个样本的第j次故障发生的时刻。
②若各样本的试验起始时间Si=0,实际操作中统计各样本的一个大修期的试验情况或统计第一小修期、第一中修期时,均属这种Si=0的情况,统计其他修理间隔期时Si≠0,此时可以将Ti和tij都分别减去Si,使其转化为Si=0,这样计算公式可简化为:

实际操作中用这种简化的方法进行计算比较合适。
(2)参数a和b的无偏估计 当n>2时形状参数b的无偏估计为:

强度参数的无偏估计:

(3)拟合优度检验 检验统计数据是否接受威布尔过程模型,检验统计量为:

式中,Zm是Zij的升序排列,而Zij=tij/Ti;当C2m>C2m,α时拒绝威布尔过程模型;C2m≤C2m,α时接受威布尔过程模型;C2m,α为检验临界值,可查GBJ 1407—1992表B2得,α为显著性水平。当n>100时暂仍按n=100表中的数据进行检验。
3.可修系统的可靠性参数
(1)可靠度函数

这说明R(t)的大小不仅与t2—t1的区间大小有关,而且还与区间的起点t1有关。
(2)故障强度函数
λ(t)=abtb-1
①当前值 当统计试验的定时截尾时间为T时,时刻T的故障强度当前值为λ(T)=abTb-1,当n≤20时,用b代替b。
②区间积分平均值 统计试验的定时截尾时间为T,在(0,T]区间内故障强度的平均值

(3)平均故障间隔时间(里程)
①当前值。MTBFt=1/λ(T)
②平均值。统计试验的定时截尾时间为T,在(0,T]区间内的平均值:
积分平均值
算术平均值

三、坦克装甲车辆可靠性与维修性指标确定的约束条件
1.寿命剖面
(1)寿命剖面定义 寿命剖面是指坦克装甲车辆从采购接车开始,到其寿命终结或退出现役为止这段时间内所经历的全部事件和环境的时序描述。坦克装甲车辆在寿命剖面中所经历的主要事件有装卸、运输、贮存、启封、检测、保养、修理、训练、演习、执行作战任务等。寿命剖面还要为这些事件的持续时间、顺序、环境条件和操作方法等加以描述。在设计时,这些事件对坦克装甲车辆可靠性与维修性的影响必须给予通盘的考虑。
(2)寿命剖面一般形式 坦克装甲车辆寿命剖面一般不分后勤阶段和使用阶段,通常由接装部队按计划直接到生产厂接装,并按使用计划,投入战备贮存或教练使用。坦克装甲车辆寿命剖面的一般形式如图1-3所示。

图1-3 坦克装甲车辆寿命剖面
2.任务剖面
(1)任务剖面定义 任务剖面是指坦克装甲车辆在完成规定任务这段时间内所经历的事件和环境的时序描述,是确定其任务可靠性指标的重要依据。
(2)主战坦克典型作战任务剖面 在主战坦克的作战任务中,最主要的任务是进攻和防御,而进攻作战是主战坦克最具有代表性和典型性的任务。因为进攻作战经历的事件最多,时间最长,条件最严酷。一般情况下,能满足进攻作战的可靠性要求,也就能满足其他作战任务的可靠性要求。
在研究主战坦克的作战任务时,以合成集团军编成内的坦克师为主要研究对象。把集团军编成内坦克师对野战防御之敌的进攻作战所经历的事件和环境的时序描述,作为主战坦克典型的任务剖面。主战坦克任务剖面一般应包括:越野行驶300 ~800km,消耗弹药1.5~2个基数,电台工作36~48h,火控工作8~16h(其中连续工作4h)。
(3)训练任务剖面 训练任务剖面主要是针对部队平时的正常训练确定的。通常装甲兵部队平时训练动用坦克贯彻“计划使用,均衡修理”原则,在保证完成平时训练任务的同时,尽可能减少维修人力和保障费用。训练任务剖面是确定坦克装甲车辆基本可靠性指标的主要依据。
装甲兵部队的训练课目主要分驾驶训练、射击训练和通信指挥训练等。以驾驶训练和射击训练为主来确定训练任务剖面。坦克的一个训练剖面定为:行驶里程70~90km,射击炮弹3~9发,火控工作3~6h,电台工作4~6h。
(4)其他装甲车辆的任务剖面 步兵战车和装甲输送车在协同主战坦克作战时,其任务剖面可参照主战坦克的任务剖面。对水陆坦克和有海上行驶性能的步兵战车在执行登陆作战任务时,要充分考虑泛水任务阶段的特殊性。水陆两栖车辆一个登陆作战的任务剖面为:陆上越野行驶300~500km,水上行驶30~50km,消耗弹药1.5~2个基数,火控工作8~12h,电台工作36~48h。在提出任务可靠性要求时,除要有完成一个任务剖面的可靠度要求外,还应有单独的抢滩登陆阶段的可靠度要求。
3.装甲车辆维修方案
装甲车辆维修方案包括维修体制、维修设备和人员编制、维修间隔期划分、维修范围和维修方式等。维修方案是确定装甲车辆可靠性和维修性指标,特别是零部件的耐久性指标的重要约束条件。
4.故障判断准则
故障判断准则对于确定坦克装甲车辆的可靠性维修性指标至关重要,没有故障判断准则的可靠性指标毫无意义。所以故障判断准则是可靠性维修性指标的重要约束条件,也是进行可靠性维修性验证试验的重要依据。GJBz 20448—97《装甲车辆故障判断准则》是提出型号故障判断准则的基本依据,对于装甲车辆的具体型号,必须根据型号的特点,提出更具体的故障判断准则。在验证试验时,还应细化型号的故障判断准则。
5.环境条件
坦克装甲车辆在实际使用中的环境条件非常复杂,可能遇到的地形和气候条件多种多样。经分析归纳得到的坦克装甲车辆在各种条件下的使用概率如下:平原地区使用概率为60%~70%,高原地区为20%~25%,沙漠戈壁地区为10%~15%;常温条件下使用的概率为70%~75%,寒冷条件下为20%~ 25%,严寒或高温条件下各为2%左右;公路行驶概率为15%~ 20%,砂石路为25%~30%,乡村土路为15%~20%,起伏地为 10%~15%,无道路为25%左右。
6.验证试验方案
可靠性和维修性指标应该是可以验证的,指标的量值也受指标的统计性质和检验统计准则的制约,所以在合同(或研制任务书)中应明确可靠性和维修性指标的性质,有关检验的统计准则,以便于验证试验方案的确定。具体的验证试验方法在 GJB 899—90和GJB 2072—94中已有明确的规定,应根据坦克装甲车辆的特点,用上述标准的基本原理,确定试验方案。
(1)可靠性验证
①假设装甲车辆的故障计数过程是时齐泊松过程,或其 MTBF(MTBCF)服从指数分布。
②在合同(或研制任务书)中要明确合同指标是可靠性定量要求的最低可接受值;或合同指标有两个:一个是最低可接受值;另一个是规定值。
③检验的统计准则 在合同(或研制任务书)中应给予明确。
判断风险α和β,一般取α=β≈10%~20%;置信区间的置信度C,一般取C=1-2β;装甲车辆的可靠性鉴定试验一般结合设计定型试验进行,试验样车的数量一般为3~5台,单车试验里程一般为10000km;坦克装甲车辆的MTBF(MTBCF)检验的下限θ1等于合同指标的最低可接受值。
④验证试验方案 根据β、θ1、T,用泊松公式确定判别故障数r;根据α、T、r,用泊松公式确定检验上限θ0,θ0应小于预计值θp,对装甲车辆鉴定试验一般θ0/θ1=d<1.5。
⑤试验结果的计算分析 按GJB 899—90,计算置信度为C的置信区间,其置信下限大于最低可接受值则验证合格,只要实际出现的故障数小于或等于判别故障数r,置信下限也一定会大于最低可接受值;当指标有规定值时,当计算的置信下限大于规定值时,可以认为规定值通过验证,即装甲车辆的MTBF(MTBCF)达到合同要求的规定值;
根据现场统计的故障发生时刻,用威布尔过程模型进行拟合,计算形状参数b,以此来评价分析用时齐泊松过程来进行试验统计的误差。
(2)维修性验证
①一般情况下,坦克装甲车辆各种维修时间服从对数正态分布,预防性修理时间服从正态分布。
②合同(或研制任务书)中应明确合同指标(MTTR等)是维修性定量要求的最低可接受值,或合同指标有两个:一个是最低可接受值;另一个为规定值。
③检验统计准则 在合同(或研制任务书)中应给予明确。
判断风险α和β,一般取α=β≈5%~20%;因装甲车辆的维修性鉴定试验与设计定型试验结合进行,其自然故障数每台车一般可在50个以上,各级修复性维修次数也多大于30次,所以在合同(或研制任务书)中一般不规定维修作业的样本数,只规定α和β值,并应明确用试验统计结果的置信上限作为验证维修性定量要求(MTTR等)最低可接受值的判决标准。
④试验结果的计算和分析 参照GJB 2072—94,一般按对数正态分布计算置信度为C=1-2β的置信区间,其置信上限等于或小于最低可接受值,则判为验证合格。若置信上限还小于规定值,则可判为装甲车辆的维修性定量要求已达到合同要求的规定值。用记录的每一个维修作业时间的观测值,对各类维修时间分别进行分布函数假设检验,如不服从对数正态分布,则应拟合确定服从哪一类分布,并对置信区间计算进行修正。
四、装甲车辆可靠性设计
装甲车辆是以机械产品为主的复杂系统,因此具有机械产品的可靠性设计问题的特点。把规定的可靠性指标设计到产品中去并提高产品可靠性的各种方法,统称为可靠性设计方法,它包括定性分析和定量计算。
1.机械产品可靠性设计的特点
(1)机械产品的可靠性设计比电子产品难度更大 电子元器件可实现设计标准化,因此电子产品通常把系统设计与元器件设计分开,元器件由专门人员设计、制造和筛选,因而系统设计不涉及元器件的设计;而机械零部件大多难于标准化,机械产品设计既要作系统结构设计,又要作零件的具体设计,同时制造设备,生产工艺对可靠性起着重要的作用,因此机械产品的可靠性设计难度比较大。
(2)机械产品的可靠性预计不易准确 电子产品的可靠性预计比较容易,标准化的电子元器件的基本失效率一般可看作常数,一旦获得其基本失效率的数据,再加上环境应力因子等则可进行可靠性预计。机械产品的功能零部件多是非标准件,而且一种零部件常要完成多种功能,使用环境又很复杂,因此,像电子产品一样统计其失效率是很困难的。造成机械产品的可靠性预计难以比较准确。
(3)降额设计、冗余设计等可靠性设计方法对机械产品不太适用 电子产品有比较成熟的降额设计准则,而机械产品设计中的定量降额问题尚未有统一的规范和方法;电子设备中几乎都可使用冗余措施来提高任务可靠性,而机械产品的主体部分很难采用冗余设计。
(4)电子产品使用过程中发生的故障主要是由于偶然因素造成的,而机械产品故障原因主要是疲劳、老化、磨损、腐蚀等,因此耐久性设计在机械产品的可靠性设计中占有重要的地位。
(5)概率设计等可靠性设计方法虽然是一种新的设计理论和方法,它仍然需要传统的设计经验,并且要与其他设计方法和理论一起综合应用,例如有限元分析,实验应力分析等。
(6)由于机械产品可靠性设计计算与分析要考虑的因素非常复杂,难以做得比较完善,所以在研制过程中,从零件、部件到系统都必须强调可靠性增长试验和耐久性考核试验,机械产品研制过程的试验与评价是可靠性设计的重要组成部分。
2.定性分析方法
(1)可靠性模型的建立 可靠性模型包括可靠性方框图和可靠性数学模型两部分,它反映了产品各组成单元之间的可靠性逻辑关系。对于机械产品同样是一项重要的工作。但坦克装甲车辆并联单元的不等效性和某一单元故障后会引起应力的重新分配等问题,对可靠性模型的建立带来一定的困难。
(2)可靠性分配和预计
①可靠性分配 电子产品可靠性分配方法大多适用于机械产品。对于装甲车辆的故障率实际上指的是故障强度,一般是随时间变化的,所以分配的故障率是指规定寿命期(如一个大修期)内的平均故障率。由于坦克装甲车辆主要部件的寿命单位不同(如推进系统以公里、火炮以发数、火控以小时为寿命单位),从整车到各主要部件一般不直接用故障率进行分配,而是用可靠度进行分配。
②可靠性预计 相似产品类比论证法、评分法、修正系数法等都适用于机械产品的可靠性预计。
③耐久性的分配和预计 首先要确定耐久性关键件和重要件,耐久性分配和预计主要针对关键件和重要性。也要建立耐久性框图,然后可用经验分配法或等分配法等进行耐久性分配。用寿命分布法、经验模型法等对关重件进行耐久性预计。
(3)故障模式及分析 故障模式影响及危害性分析(FMECA)和故障模式及影响分析(FMECA)适用于机械产品的所有研制阶段,GJB 1391—92中的FMECA程序是适用于机械产品的。由于机械产品标准化程度差,可靠性数据缺乏,定量可靠性设计分析难以实施,因而FMEA实际上处于可靠性分析的核心位置。危害度分析(CA),也是适用于机械产品的,能否实施主要取决于是否有故障率等数据的支持。
故障树分析(FTA)也适用于机械产品,FTA的定性分析避开了机械产品数据缺乏的问题,在FMEA分析出关键故障模式的基础上进行FTA,是一种较好的方法。
(4)可靠性设计准则 可靠性设计准则是进行可靠性设计的重要依据,是把可靠性设计到产品中去,提高产品可靠性的有效方法。可靠性设计准则是把已有的、相似产品的工程设计经验和教训总结起来,使其条理化、系统化、科学化,成为设计人员进行可靠性设计所遵循的原则。可靠性设计准则一般都是针对某个型号或产品的同时还需制订分系统、部件以及某些典型零部件(如轴、齿轮、轴承、密封、花键等)的设计准则。
3.定量设计方法
(1)概率设计法 概率设计法即是应用概率统计理论进行机械零件及构件设计的方法。概率设计的核心是把应力和强度视为受多种因素影响的随机变量,是属于某种概率分布的统计量,以通用的广义应力强度干涉模型作为基本运算公式,广泛沿用机械零件传统的设计计算模型,求出给定可靠度下的零件尺寸或给定尺寸零件的可靠度及相应的寿命。广义的干涉模型不仅适用于机械强度,而且对刚度、疲劳、磨损、腐蚀等情况均可应用。
由于应力和强度的随机性,概率法设计的基础是设计变量的统计数据,最理想的情况是针对具体对象试验取值,对取得的大量数据进行统计处理,确定分布类型,估计分布参数。然而由于试验的困难或受经济及时间的限制,直接试验并统计处理往往是不可能的,因此常就已有的类似数据或间接资料近似估计所需的数据。目前可用的数据积累很少,很难得到应力和强度的概率密度函数。如果应用不正确的数据和不正确的模型,先进的概率设计也就失去意义。在今后相当长的一段时期内,概率设计方法只是一种发展的趋势,在实际应用中,将可靠性设计的分析技术如FMECA、FTA等定性分析方法引入到传统的设计方法中,利用可靠性分析技术发现产品的薄弱环节和缺陷,采用概率法的概念去完善和改进传统的安全系数法,这将是目前比较可行的方法。
(2)稳健性设计 所谓稳健性设计,就是使得产品的性能对在制造期间的变异或使用环境的变异不敏感,并且使产品在其寿命周期内,不管其参数、结构发生漂移或老化(在一定范围内),都能持续满意地工作的一种设计方法。稳健性设计是寻求低成本、高性能稳定的产品的一套系统的优化设计方法,它不是一种单一的具体方法,而是为达到共同的目标而形成许多方法的集合。这个目标就是使产品具有高度稳定的性能。稳健性设计是以用户需求为牵引,采用三次设计(系统设计、参数设计、容差设计)法、全面质量管理、质量功能展开、FMECA等方法精心优化设计方案,把问题解决在设计阶段,以最小的代价获得高性能稳定性,即高可靠性、高质量的产品,也就是健壮的产品。
稳健性设计形成一套系统的方法历史并不太长,但其理论研究及工程应用都得到很大的发展,把稳健性设计的技术方法引入可靠性工程之中,对于提高产品质量与可靠性是一个有益的补充。
五、中国装甲车辆可靠性与维修性的特点
1.中国装甲车辆的可靠性与维修性水平
与国外装甲车辆的可靠性与维修性水平作比较,虽然由于没有国外可靠性数据的背景条件(如:故障准则、数据的统计性质等)资料,不能作绝对的数据比较,但从收集到的数据作一种宏观的比较,分析其趋势是有参考意义的。中国第一代某坦克的平均故障间隔里程(TBF)为204km,接近美军M48A3的 209.3km,可靠性水平基本相当。美军第二代坦克M60A1的TBF已达到252.8km。中国第二代坦克的可靠性已引起高度的重视,并进行了大量的工作,以缩小与世界先进水平的差距。
2.可靠性数据的统计特性
对某坦克试验的故障数据用威布尔过程模型进行统计分析,基本可靠性的故障强度函数的形状参数b一般为 0.95~1.2;而任务可靠性的b一般为1~2.19。基本可靠性数据统计简化为时齐泊松过程来描述误差不大,而任务可靠性数据统计简化为时齐泊松过程描述大多情况下误差较大,其他装甲车辆的情况基本与此相仿。
3.关于早期故障
各小修期故障强度函数λ(t)的变化规律性较差,在小修质量较差的情况下,小修期故障强度函数λ(t)的形状参数b<1,呈明显的早期故障型。提高部队的修理质量是提高使用可靠性水平的重要环节。
4.维修时间的统计特性
通过对某坦克14种整车的维修时间和7种部件的维修时间统计分析,证明维修时间大多数服从对数正态分布;当维修范围和维修方法相对比较固定时,维修时间比较明显地服从正态分布,如小修、中修、大修的时间分布;当所用维修时间较短的轻度故障较多时,其维修时间服从指数分布,如基层Ⅰ级修复性维修时间。一般情况下用对数正态分布来统计分析维修时间是可以的,不会产生很大的误差。
5.关于预防性维修时间
中国现役装甲车辆的预防性维修时间耗时太多。从某坦克的维修时间统计可以看出,预防性维修时间(不含大修时间)为修复性维修时间的3倍多。坦克可达可用度之所以很低,与预防维修时间耗时太多有关。美国、俄罗斯等发达国家都在努力提高主要部件的耐久性水平,以减少预防维修时间,并有取消中修的趋势。这也是中国发展坦克装甲车辆的努力方向。
6.故障模式
从故障模式看,坦克装甲车辆的螺纹连接松动和渗漏故障占有相当大的比重。以某坦克为例,在统计的534个故障中,有 185个故障属于螺纹连接松动和油液严重渗漏。因此要加强紧固技术和密封技术研究,如果能较好地解决紧固和密封问题,中国坦克装甲车辆的可靠性水平将大幅度提高。