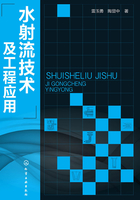
1.3 水射流技术研究动态
水射流作为一门新兴的技术,在过去的数十年间发展十分迅速。各种新型水射流技术,如脉冲水射流(pulsed water jet)、磨料水射流(abrasive water jet)、空化水射流(cavitation water jet)、低温水射流(cryogenic water jet)等相继诞生,并已广泛应用于工业清洗(industrial cleaning)、材料表面处理(surface processing)和物料切割(materials cutting)等方面。
过去人们把注意力主要集中在提高水射流压力来获得更好的水射流性能,因此,水射流压力从70MPa不断提高到如今的420MPa甚至1000MPa。随着机械制造水平的提高,大批高压和超高压发生器应运而生,从而大大推动了水射流技术的进步。但是,受多种技术条件制约,通过提高压力来提高连续水射流出口速度终究受到限制,不可持续。20世纪70年代末期,学者们发现脉冲水射流的打击力大大优于连续水射流,于是脉冲水射流技术迅速发展。脉冲水射流用比普通水射流低得多的压力来完成特定的工作任务。
超高速脉冲水射,又叫水炮(water cannon)的研究成果,使水射流技术跃上一个新的台阶。当脉冲射流速度达到1~2km/s时,射流头部的动压可高达1~3GPa。在如此高压头作用下,几乎任何工程材料都可被穿透。这意味着超高速脉冲水射流可用于材料表面处理和切割加工。其特点在于这种水射流不需要任何添加剂,结构更简单、控制更方便、环境更友好(friendly environment)。超高速脉冲水射流可以完成一些普通水射流无法完成的任务,例如,超高速水弹可以穿透黏土层深达20m(Kolle,1998)。正是由于超高速脉冲水射流的卓越穿透能力,因而引起国际学术界部分学者对超高速脉冲水射流技术的研究兴趣。超高速脉冲水射流具有许多功用,如对特殊材料进行打孔、表面强化处理等。
20世纪,超高速脉冲水射流发生装置的典型代表如IV-5、 MPI-2、 VIS-1 、VBS等面世。21世纪,一些速度更高、性能更优良的超高速脉冲水射流发生装置相继问世。参考文献[7]介绍了一种试验装置,利用自由落体动能驱动并配合聚能喷嘴,可以产生速度高达2000m/s的超高速脉冲水射流;瑞士特拉空间公司(Terraspace Inc.)研制了一种速度达2987m/s的超高速脉冲水射流发生装置,其相应的射流头部动压则高达4.46GPa;瑞士的另一家研究机构——塞拉克研究所(CERAC S.A Institute)设计的一台超高速脉冲水射流发生器,其理论速度可高达3500m/s。这种装置的结构特点是采用了具有指数内轮廓曲线的聚能喷嘴。英国谢菲尔德大学沃森博士(Dr.A.J.Watson,University of Sheffield,England)根据德国著名的纽曼效应(或美国的门罗效应),采用锥形装药的爆炸装置产生了速度高达9500m/s的脉冲水射流,其对应的射流头部动压则高达13.8GPa。
微细加工磨料水射流(micro-machining abrasive water jets,MAWJ)是一种新型、高效水射流形式,由于其射流束径远小于传统磨料水射流,因此,在半导体、微机电系统(micro electro mechanical system,MEMS)以及光学器件领域具有广阔的应用前景。近十年来受到如英国、美国、德国、瑞士、澳大利亚、新加坡以及日本等国的高度重视,开始相关技术及应用研究。美国在微磨料水射流技术方面大量投入,欧盟已将微磨料水射流加工技术列为第五框架项目,澳大利亚也启动微磨料水射流技术前期研究,我国一些学者也开始这方面的研究。
根据目前国际研究文献资料,磨料水射流按高能射束的直径大小可分为三类:传统(普通)磨料水射流(abrasive water jet,AWJ)、精细磨料水射流(fine abrasive water jet,FAWJ)和微细加工磨料水射流(micro-machining abrasive water jets,MAWJ)。传统磨料水射流的切缝宽度一般在500μm以上,精细磨料水射流的切缝宽度为100~300μm,而微细加工磨料水射流的切缝宽度可达50~100μm。由于精细磨料水射流对磨料的要求较微细加工磨料水射流低,而解决精细磨料水射流的相关技术问题对成功开发和应用微细加工磨料水射流具有借鉴作用,因此许多学者将精细磨料水射流看成是传统磨料水射流与微细加工磨料水射流之间的一种技术过渡而得到优先研究。Hashishi(2005)等人利用传统AWJ方法,通过设计新的切割头,产生射束直径在400μm以下的精细磨料水射流(压力375~400MPa,喷嘴直径12μm 、75μm,砂管内径380μm,磨料粒度65μm),并成功应用于各种半导体材料的切割。Miller(2003)采用纳米磨料粒子(氧化铝磨料,平均直径50~300nm)成功开发出射流直径为40μm 的微磨料水射流。Miller(2005)研究认为,微细加工磨料水射流的束径完全可以达到激光加工的数量级。图1-5 是50μm微细加工磨料水射流。

图1-5 微细加工磨料水射流(50μm)
随着微机电系统的发展,对微细加工技术的需求越来越高,科学家们努力研究开发新型微细加工技术和方法。于是,一种称为激光微水射流(laser micro jet,LMJ)的新技术,亦称为水射流导引激光(water jet guided laser)技术诞生了。它是一种将激光注入微水射流束,从而形成一种新的复合射流,兼具激光和水射流的诸多优点。瑞士Synova 公司成功开发出水射流导引激光系统和切割机床,在微电子和超精密加工领域得到应用,如图1-6所示。最初,水射流导引激光加工主要是用于减少切割区域附近的热效应,但事实上用水射流取代传统激光切割中的辅助气体流束,还有很多别的优点。这项技术在很多应用中,特别在微电子和半导体制造行业,被证明是有效且可靠的。

图1-6 水射流导引激光切割
低温射流(cryogenic jet)又叫做冷射流(cold jet),是20世纪末发展起来的一种新型射流之一。20世纪90年代初,Kannol和Szijcs等人提出了用喷射冷冻固体颗粒来处理敏感材料表面的技术。他们通过在高速空气射流中添加制冷剂,如液态氮(N2)、固体二氧化碳(CO2)或氟利昂(freon)等,从而使射流中的液体冷凝形成冰粒射流。此后,国际上对冰粒射流技术的研究和应用表现出极大兴趣。最近几年,冰粒射流技术在冰粒子形成方法、冰粒射流喷嘴、冰粒射流喷射系统及其应用等方面取得重要进展。
低温射流(cryogenic jet)包括液态二氧化碳射流(CO2 jet)、液氮射流(LN2 jet)、固态二氧化碳(干冰)射流以及冰粒射流(ice jet)。同普通水射流相比,低温射流具有独特的优势。
①消除液体残存。液态二氧化碳和液氮这类物质,在常温、常压下即成为气态,因此,低温射流工作后迅速蒸发,无液体残留。这在两种情况下特别有用:一是要求清洁环境或工件;二是工件含有剧毒或放射性物质。对于第一种情况,低温射流可确保工件污染降到最低。对于第二种情况,可大大减少危险的加工废弃物料的处理。
②扩展水射流的潜在应用范围。由于低温射流的液态物质离开喷嘴以后不断扩散和蒸发,从而使低温射流沿轴向的切割功率随靶距的增加而快速衰减。因此,低温射流可用于一些压力敏感材料或易碎材料的切割。
③用可挥发的低温固态粒子(如固态CO2粒子)作为磨料来增强切割(或清洗)能力,从而可大大减少加工废弃物的处理。
④当温度降至材料的韧性/脆性过渡温度以下,从而可能改善工件材料的失效形式。
根据国际研究动态,水射流技术的研究方向可以概括为以下几个方面。
①新型高效射流技术。包括高速和超高速水射流技术的理论;超高速水射流、空化水射流、脉冲水射流、冰粒射流的产生方法和设备。
②水射流切割的智能化控制技术。包括高能水束对各种工程材料的穿透性能、冲蚀机理;高速水射流各参数与加工精度的映射关系;高能水束对工程材料的机械和热影响;高能水束的能量有效利用和优化等。
③水射流集成制造系统与装备。将高速水射流技术与机械、电子、液压、气动、数控、计算机CAD/CAM集成于一体,形成多功能、柔性化和智能化的清洗与制造设备。
④继续拓展水射流技术的工程应用。特别是在材料工程、医疗机械、环保工程和微加工等领域的应用研究。如材料表面处理、医用手术刀、微细加工等。