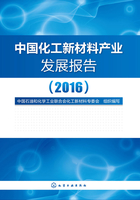
第二节 我国化工新材料产业发展现状
一、总体情况
“十一五”以来,我国化工新材料在工艺技术方面取得了重要突破,氟硅材料、聚氨酯材料、工程塑料、高性能橡胶等行业装置能力快速增长。2015年,我国化工新材料产业规模达到2600亿元,市场总消费规模约为4700亿元,化工新材料进口额约320亿美元,占化工产品总进口额的20%(化工产品进口额达1600亿美元),自给率为55%。按产量统计,2015年国内产量约为1681万吨,消费量达2622万吨,自给率仅为63%,其中,工程塑料产量209万吨,自给率仅为52%,高端聚烯烃产量为371万吨,自给率为39%。高性能合成橡胶产量221万吨,自给率约66%;电子化学品按重量和销售额计的国内自给率分别为53%和40%。
从产业发展水平看,我国在氟硅树脂和橡胶、聚氨酯材料、储能材料领域有很高的发展水平,但产品品种有待进一步丰富并拓展下游应用领域;在高性能分离膜材料、高性能纤维、工程塑料与特种工程塑料、高性能橡胶、新型特种涂料、新型特种胶黏剂、电子化学品领域具备一定发展水平,但存在较多技术空白,如PA66原料己二腈、乙丙橡胶、超大规模半导体集成电路用化学品等;在高端聚烯烃树脂领域发展水平很低,处于大范围技术空白,详见表1-10。
表1-10 2015年中国化工新材料分行业情况

二、消费情况
近年来很多产品的消费量年均增长都在20%以上,2015年,我国化工新材料产业形成约上亿元以上产值的生产体系。但由于受技术水平的制约,化工新材料又是我国化学工业体系中国内自给率最低、最急需发展的领域,高性能产品主要依赖进口。
在我国化工新材料产业中,市场需求量较大、自给率较低、最急需发展的领域是工程塑料、高端聚烯烃塑料、高性能橡胶、功能性膜材料和电子化学品。我国化工新材料产品的供需变化情况如表1-11所示。
表1-11 我国化工新材料总体情况

三、分领域发展情况
2015年,我国主要化工新材料的供需情况见表1-12。其中,高端聚烯烃树脂、高性能橡胶自给率不到40%;高性能纤维、工程塑料与特种工程塑料自给率为60%左右;氟硅树脂和橡胶供略大于需。
(一)工程塑料与特种工程塑料
2015年我国工程塑料产量209万吨,表观消费量为405万吨,自给率仅为52%,其中消费量最大的聚碳酸酯国内自给率仅为27%(见表1-12),而且主要由外资企业生产。我国工程塑料领域主要问题是产能过度集中于低端产品,而高端产品的产能受制于技术等因素而导致对进口的依赖严重。随着塑料工业的发展,对工程塑料的要求也会越来越高,迫切要求工程塑料的高性能化与国产化的技术要求,从而使得工程塑料的合成和加工改性变得尤为重要。
表1-12 2015年中国工程塑料与特种工程塑料供需情况

(1)聚碳酸酯
截至2015年,我国PC产能为68.9万吨/年,产量约为45多万吨,集中在外资和合资企业。近年来我国聚碳酸酯的进口量快速增长,我国聚碳酸酯进口量呈逐年上升态势,进口量由2007年75万吨上升至2015年142.7万吨,2015年消费量达166万吨,自给率仅为27%。
聚碳酸酯生产工艺具有较高的技术壁垒,目前世界聚碳酸酯生产主要集中在美国、西欧和日本。其中,美国通用电气(GE)、德国拜耳(BAYER)、美国陶氏化学(DOW)、日本帝人(TEIJIN)和三菱瓦斯/三菱化学公司(MITSUBISHI)是世界5大聚碳酸酯生产企业,其生产能力合计占世界总能力的90%左右。
(2)聚甲醛
截至2015年年底,中国境内的聚甲醛年生产能力已近50万吨/年,产量28万吨,进口量25.8万吨,出口量3.8万吨,表观消费量为50万吨,自给率为56%。
随着生产工艺包的引进和自主知识产权的开发,我国的聚甲醛生产行业经历了一个井喷式的发展时期。2001年云南云天化股份有限公司从波兰化工集团(ZAT)引进国内第一套1万吨/年聚甲醛生产装置,并于当年投产。2008年以来,上海蓝星新材料公司、中海石油天野化工、天津碱厂、开封龙宇化工和神华宁煤集团相继通过引进香港富艺技术投资建成POM装置。另外,开滦中浩和兖矿鲁南化工有限公司引进韩国P&ID公司技术。
聚甲醛生产工艺有共聚和均聚两条路线。仅杜邦和日本旭化成两家公司可以生产均聚甲醛,其市场占有量在20%以下。均聚甲醛的力学性能比共聚甲醛有一定的优势,但是由于均聚甲醛对材料的加工工艺要求较高,只有一些高端产品使用均聚甲醛产品。目前国内只有杜邦和旭化成公司合资建设的年产2万吨的旭化成聚甲醛(张家港)有限公司生产聚甲醛,其他国内企业尚未涉足。
(3)聚酰胺
我国聚酰胺产业从20世纪50年代起步,整体上发展较为缓慢。自20世纪90年代,中国聚酰胺产业的发展才慢慢步入正轨,但是同时也伴随出现了产能过剩、高性能产品比重较低、产业链较短、环境污染等问题。我国生产的聚酰胺中,PA6约占90%,PA66约占10%。
2015年我国聚酰胺6切片生产能力为339.2万吨/年,产量为237.4万吨,进口量为44.9万吨,出口量5.7万吨,表观消费量为276.6万吨。2015年我国聚酰胺66切片生产能力为31.6万吨/年,产量为22.1万吨,进口量为28.6万吨,出口量4.7万吨,表观消费量为46万吨。
PA6得益于石油价格下降,上游原料苯和己内酰胺价格下降,在浙江、福建等地产能温和扩大,但我国己二腈主要依赖进口,成本较高,制约了中国己二胺及PA66产业的发展。己二腈生产工艺分丁二烯法和丙烯腈电解法。丁二烯法约占总产能的70%,反应过程的路线短、能耗低,被杜邦(英威达)、罗地亚(罗纳普朗克)、巴斯夫等少数几个公司高度垄断。山东润兴化工科技有限公司年产10万吨己二腈项目系国内首套工艺,填补了国内生产空白。此外,重庆紫光己二腈中试项目,包括丁二烯法500吨/年己二腈装置(试生产阶段)和250吨/年丙烯腈电解制己二腈装置(试生产阶段)。
(4)热塑性聚酯
热塑性聚酯在工程塑料中占有重要地位,其中已经得到广泛应用和大规模工业化生产的是PET和PBT。
我国已成为世界上最大瓶级PET切片生产国,2015年中国瓶级PET切片需求约400万吨,而产能达到了近900万吨/年,受产能严重过剩影响,2015年中国PET生产装置的平均开工率仅为65%。2015年,我国PBT主要生产企业的总产能达到98万吨/年,平均开工率仅为50%,产量约45万吨,进口量为13万吨,出口量约18万吨。表观消费量为40万吨。
(5)聚苯硫醚树脂
2015年,我国聚苯硫醚树脂产能达到4.6万吨/年,其中中国旭光高新材料3万吨/年、浙江新和成0.5万吨/年、张家港新盛新材料0.5万吨/年、敦煌西域特种新材0.4万吨/年、中国化工0.2万吨/年。产量约1万吨,进口量为2.7万吨,表观消费量3.7万吨,自给率为27%。主要以低分子量注塑级PPS产品为主,绝大部分聚苯硫醚材料尚须从国外进口,尤其是挤出级和薄膜级技术难度更高,还无法生产。即使是在中低端市场,我国聚苯硫醚的实际生产规模也远小于国内的需求总量。更重要的是,高品级的聚苯硫醚树脂在国内还没有形成有规模的产品,纤维级PPS树脂的生产能力不足1万吨/年。
(6)液晶高分子材料
液晶高分子材料分为溶致液晶高分子(LLCP)和热致液晶高分子(TLCP)。全球TLCP市场是一个高度集中的市场,美国Celanese公司,比利时的Solvay,日本的宝理塑料和住友化学等4家公司占据全球TLCP市场份额的75%以上。我国目前仅上市公司普利特一家,2000吨/年TLCP试生产,产能严重跟不上需求。较高的技术壁垒,限制了企业进入。TLCP市场对外依赖度高:随着全球IT、电子工业产能向我国转移,我国已成为TLCP使用量最多的地区,每年需进口约2~3万吨,对外依赖度极高。
(二)高端聚烯烃塑料
2015年我国高端聚烯烃塑料的国内自给率仅为38%,其中己烯共聚聚乙烯约占高端聚烯烃塑料总消费量的75%,自给率仅为44%,己烯、辛烯等高碳α-烯烃依赖进口是制约高碳α-烯烃共聚聚乙烯发展的重要原因之一。在高端聚烯烃树脂领域,EVOH树脂完全依赖进口;POE、mPE和mPP自给率严重不足,仅为10%左右;EVA树脂自给率也不到50%,详见表1-13。
表1-13 2015年中国高端聚烯烃树脂供需情况

(1)乙烯-醋酸乙烯共聚树脂(EVA)
国内EVA树脂产能达到60万吨/年(其中燕山石化20万吨/年产能为LDPE/EVA树脂切换生产,以生产LDPE为主)。EVA树脂生产企业主要有中石化旗下的北方东方、扬巴公司、北京华美聚合物、燕山石化和联想旗下的山东昊达化学5家企业。此外,大庆石化20万吨/年LDPE装置及上海石化LDPE装置均可兼产EVA树脂,但由于切换生产EVA难度较大,自建成以来从未排产EVA树脂。2015年,国内EVA全年产量初步估算在34万吨左右,基本与2014年持平。据统计,2015年国内初级形态的EVA树脂进口量89.2万吨,出口量5.2万吨,净进口量高达84.0万吨,表观消费量达到118万吨,2015年进口依存度达到71.2%。
(2)乙烯-乙烯醇共聚树脂(EVOH,亦称EVAL)
目前,国内EVOH工业化生产尚处于空白,国内所需产品全部依靠进口,制约了下游应用产业的发展。“十二五”期间,中石化四川维尼纶厂组织研发力量,自主开发出用于EVOH生产的高压间歇聚合、间歇醇解、连续聚合、连续醇解和后处理小试装置,小试产品各项指标达到国外同类产品先进水平,2014年EVOH树脂小试研制项目技术通过中石化集团公司评议组评议,并于重庆长寿正式启动500吨/年中试项目,预计将在2016年建成。若该中试项目取得成功,将为未来进一步实现工业化放大奠定基础,有望推动我国EVOH树脂产业实现突破。
(3)茂金属聚乙烯(mPE)
截至2015年年底,国内共有中石化齐鲁石化、中石油大庆石化、中石油独山子石化、中国化工沈阳化工四家企业工业化生产mPE产品,总产量在10万吨左右。中石化齐鲁石化是国内最早开始进行mPE工业化试生产的企业,也是目前国内mPE生产规模最大的企业,2015年产量接近8万吨,主要有4个mPE产品牌号,均采用1-己烯为共聚单体,产品用于PE-RT管材、薄膜、滚塑制品等领域。中石油大庆石化/中石油独山子石化和中国化工旗下沈阳化工引进UNIVATION公司茂金属催化剂技术的mPE生产企业,以1-己烯为共聚单体,但受国内市场开发等问题影响,产量规模一直在未能显著提升,维持在数千吨的水平。Total公司正在筹划与中电投公司合资建设80万吨/年煤制聚烯烃项目,其31万吨/年HDPE装置产品定位即以生产茂金属薄膜料、高性能吹塑料、高规格双峰管材料以及高端注塑料(含茂金属牌号瓶盖专用料)等高端产品为主。
2015年国内mPE总消费量约50万吨,自给率仅20%左右。目前国内mPE主要用于包装领域,占到总消费量的70%。其次是PE-RT管材领域,占到25%左右,此外还用于滚塑油箱、注塑瓶盖等其他领域。
(4)茂金属聚丙烯(mPP)
茂金属聚丙烯(mPP)产品的起步时间和发展规模均远落后于茂金属聚乙烯,目前其在世界聚丙烯市场中所占比例仅1%左右,总体市场规模在50~100万吨之间。mPP生产技术是生产工艺与催化剂体系的综合体系,目前LyondellBasell、ExxonMobil、Braskem(收购陶氏化学聚丙烯业务)、Total(原Fina)、三井石化、JPP(原窒素)、Novolen等聚丙烯专利商/生产企业都开发(合作开发)出用于生产聚丙烯的茂金属催化剂。对中国聚丙烯生产企业而言,虽然世界主流的先进聚丙烯生产工艺均有引进,但采用的催化剂体系均为传统的Z-N催化剂,国内的茂金属催化剂体系尚处于实验室研究阶段。因此,目前我国mPP生产尚处于空白,高端应用领域所需产品全部依靠进口。初步估算,2015年消费的mPP数量约6~7万吨,主要用于高透明聚丙烯制品,特别是微波炉用具及医疗用品、纺粘无纺布、超细旦丙纶纤维和食品包装膜等领域的高端产品生产,主要进口产品有埃克森美孚Achieve系列牌号、巴塞尔Metocene系列牌号、道达尔MR系列牌号、日本三井Tafmer XM系列牌号等产品。
随着聚丙烯中低端产品市场竞争日益激烈,寻求差异化、高端化发展成为行业共识,mPP等高端牌号产品的市场潜力和发展前景已引起高度关注,部分企业正在积极探索布局中国市场。如Total公司正与中电投公司合资建设80万吨/年煤制聚烯烃项目,其50万吨/年聚丙烯装置产品定位即以生产双峰膜料、茂金属纤维料以及高端注塑料(含茂金属牌号)等高端产品为主。预计在“十三五”期间,国内mPP生产有望突破空白,并推动下游高端应用制品行业健康、快速发展。
(5)超高分子量聚乙烯
2015年,我国UHMWPE的总产能约5.2万吨/年。产量约4万吨,消费量约7万吨,自给率为57%。我国UHMWPE生产规模较小,无法满足国内市场需求,近两年我国UHMWPE净进口量在3万吨/年左右,进口产品主要来自美国和日本生产企业。
其他高性能树脂主要是高吸水性树脂、聚乳酸、聚丁二酸丁二醇酯(PBS)和可降解塑料,2015年消费量达63万吨,可基本自给。随着我国进入老龄化社会和对二胎生育限制的放松,我国高吸水性树脂正在进入加速发展期;我国可降解塑料正处在起步发展期,未来在环保政策的推动下发展潜力巨大。
(三)高性能橡胶
高性能橡胶指除乳聚丁苯橡胶和通用型顺丁橡胶外的其他合成橡胶,包括溶聚丁苯橡胶和稀土顺丁橡胶,也包括各类热塑性弹性体。
据统计,2015年我国特种合成橡胶装置总能力达244万吨,消费量为187万吨,其中净进口量61.2万吨,国内产品市场占有率约67.3%。2015年我国高性能合成橡胶产品供应状况见表1-14。
在高性能橡胶领域,乙丙橡胶、丙烯酸酯橡胶自给率严重不足,约10%左右;丁基橡胶、异戊橡胶自给率也仅为30%左右,详见表1-14。
表1-14 2015年中国高性能橡胶供需情况

从表1-14供应状况可以看出,SBS是国内市场占有率最高的品种,其原因应归结于近年中国石化集团公司下属企业竞争力强,加上在大陆的台资企业保障了台商鞋用料供应而降低对进口材料的依赖;2015年,我国丁基橡胶和乙丙橡胶的装置能力已经大于消费量,但是因天然橡胶价格冲击,国内装置开工低,市场消费大量依靠进口产品。
(1)丁基橡胶
2015年我国丁基橡胶装置总能力达36万吨/年,产量9.5万吨,净进口量23.2万吨,消费量为32.7万吨,自给率为29%。
中石化燕山石化丁基橡胶装置建成,打破了丁基橡胶市场长期为少数国外公司垄断的局面,投产后缓解了国内供应紧张局面,经济效益较好,吸引了国内多家企业引进技术投资丁基橡胶装置建设。但国际一流公司仍坚持不转让丁基橡胶生产技术以维持技术和市场垄断地位,意大利CONSER公司丁基橡胶技术成为国内进入合成橡胶产业的多家新投资者的技术来源。
我国丁基橡胶工业生产比跨国公司晚了半个多世纪,技术和经营经验上存在明显差距,引进的意大利或俄罗斯技术建成的生产装置也只是世界上的二流技术水平。因此,我国的丁基橡胶生产要达到世界先进水平还要做很多工作。首先要将卤化丁基装置建设好,稳定生产,开拓市场,替代进口,为我国轮胎工业技术进步提供质量稳定、供应充足的优质材料;其次要在技术层面上进一步完善与提高,降低能耗物耗,缩小与国际先进水平技术差距,提高产品竞争能力;第三,扩展丁基橡胶的产品谱,扩大橡胶工业制品中的丁基橡胶市场份额。
(2)异戊橡胶
2010年,采用国内技术建设异戊橡胶工业装置先后在茂名鲁华化工有限公司和青岛伊科思公司建成投产,从此我国合成橡胶七大基本胶种全部实现工业化。后来又在各地大型乙烯装置的化工区域内,建成多套碳五分离生产异戊二烯并联产异戊橡胶生产装置。2015年我国已经建成异戊橡胶生产装置总能力27万吨/年。但由于近几年国际天然橡胶供应过剩价格极低,异戊橡胶市场价格与生产成本倒挂,使已建装置长期处于停产状态,全国异戊橡胶的生产总量仍很低。青岛第派新材料公司建成世界上第一套反式异戊橡胶工业生产装置,反式异戊橡胶属于热塑性橡胶,市场开发的应用前景很广。
(3)氯丁橡胶
我国氯丁橡胶是依靠国内自己开发技术发展起来的。目前国内生产装置能力共5.8万吨/年。山西大同某企业在合资过程中开发大聚合釜技术,3万吨/年装置可生产的产品牌号达数十个,极大提升了国内氯丁橡胶供应能力。最近几年全国氯丁橡胶年生产量在3万~5万吨,除供应国内市场外还有部分产品出口国际市场,最高年份出口量曾达0.95万吨,进口量在近10年的较长时间内保持在2万吨左右。国内氯丁橡胶年消费量在6万~7万吨,2015年国内产品的市场占有率为67%。
国内氯丁橡胶市场消费量增长缓慢,传统市场受其他高分子聚合物替代。氯丁橡胶应用在一些特定场合,目前国内市场份额的33%左右被进口产品占据。国内企业需要进一步稳定产品质量,提高市场开拓和用户精细服务,替代进口。
(4)丁腈橡胶
国内丁腈橡胶生产装置能力从2010年8.3万吨/年提升到2015年22.7万吨/年。2015年国内消费量为21.9万吨,国产胶市场占有率65%。主要生产企业有中国石油兰化公司、中国石油吉化公司、台湾南帝化学公司、宁波顺泽、朗盛台橡(南通)化学工业有限公司、南京金浦英萨合成橡胶有限公司。
(5)乙丙橡胶
2015年年底国内乙丙橡胶装置总能力达37万吨/年。主要生产企业有中国石油吉化公司、上海中石化三井化工有限公司、朗盛(常州)有限公司、宁波爱思开合成橡胶有限公司。
随着汽车为代表的国民经济快速发展,乙丙橡胶市场需求量不断增长,而国内扩建装置一直未能及时补充市场需要,我国乙丙橡胶进口量持续上升到2014年的高峰值25.3万吨,2014年国内对进口乙丙橡胶依存度达90%。
(6)热塑性丁苯橡胶
我国已成为世界热塑性丁苯橡胶最大生产和消费市场。2015年产量达80万吨,消费量达84.5万吨,国产市场占有率94.4%,是国内合成橡胶品种内自给率最高的产品。由于国内热塑性丁苯橡胶生产能力发展较快,进口量已从2006年峰值17.8万吨回落到2015年6.4万吨。2015年出口1.6万吨,是目前国内合成橡胶出口量万吨以上的四大品种之一。SBS的生产技术还分别向意大利EniChem公司和台湾合成橡胶公司转让。
2015年年底高性能合成橡胶品种的国内装置能力均高于相应国内消费量,其中热塑性丁苯橡胶、丁腈橡胶和氯丁橡胶这三个品种的国内产品市场占有率达到60%以上,需要进一步增加高档适销产品;而丁基橡胶、乙丙橡胶和异戊橡胶三个品种因装置建成时间不长,目前国内产品市场占有率还很低,需要进一步稳定产品质量,开发市场,尽快达到正常生产,满足国内市场需要。
(四)聚氨酯
聚氨酯材料生产以异氰酸脂和多元醇为起始原料,产品种类包括聚氨酯发泡材料、聚氨酯涂料、聚氨酯胶黏剂等聚氨酯制品。2015年我国聚氨酯消耗量约1000万吨,各类聚氨酯制品产量达962万吨,折合聚氨酯树脂产量743万吨。聚氨酯制品如发泡材料等大多不便运输,一般在市场所在地进行生产,因此除个别特种聚氨酯制品外,基本国内自给。我国聚氨酯行业的发展长期受到异氰酸酯和多元醇等关键原料的制约,“十二五”期间原料供应情况大为改善,目前大宗品种的原料MDI、TDI,脂肪族异氰酸酯和聚醚多元醇均已实现或基本实现国内自给。
(1)异氰酸酯
改革开放以来,经过30多年的引进、消化吸收、自主创新开发,特别是近10年来快速创新发展,我国异氰酸酯形成了以MDI、TDI为主体品种的坚实产业基础,已成为全球异氰酸酯主要生产和消费国。
①MDI 2015年我国MDI总产能306万吨/年,产量197万吨。生产全部分布在华东地区,尤其是以上海为中心的长三角地区。主要生产企业有3家,分别为万华化学有限公司、拜耳(上海)聚氨酯股份有限公司、上海联恒异氰酸酯有限公司。
2008~2015年我国MDI缺口不断减小,国内产量不断提高,进口量逐渐减少,出口量逐渐增加。国内生产完全能满足国内消费,并大量出口,2015年进口37.37万吨,出口44.43万吨。
②TDI 2015年中国TDI总产能达到89万吨/年。2014年新增产能为福建省东南电化股份有限公司的10万吨/年TDI项目。我国TDI主要集中在华东地区,尤其是上海地区。我国TDI生产企业有6家,分别为拜耳(上海)聚氨酯股份有限公司、上海巴斯夫聚氨酯有限公司、沧州大化股份有限公司、甘肃银光化学工业公司、烟台巨力异氰酸酯有限公司和福建东南电化。
2015年我国TDI消费量约为65万吨,其中聚氨酯软质泡沫消费约占67%;聚氨酯涂料消费约占17.5%;弹性体消费约占6%,密封剂、胶黏剂消费约占8.8%。2015年我国TDI进口3.68万吨,出口6.33万吨,聚氨酯软泡以及涂料等持续低迷,导致TDI需求不旺,加上新增产能的开工,使得我国TDI产能过剩局面加剧。在需求和产能过剩的双重压力之下, TDI产业长期处于成本线下方运行,开工率偏低。预计随着万华化学的30万吨/年TDI装置建成投产,TDI市场产能严重过剩局面持续。
③HDI HDI主要应用领域于汽车面漆固化剂。2015年我国HDI总产能4.5万吨/年,产量4万吨,净进口量为近1万吨,表观消费量为5万吨左右,自给率为80%。主要生产商有拜耳材料科技(中国)有限公司和万华化学有限公司、日本旭化成(南通,装置产能扩大1万吨/年)。
④聚醚多元醇 2000年以来,随着中国聚氨酯工业的迅速发展,我国聚醚多元醇工厂大量新建、扩建,产能也在不断增长。2015年,我国聚醚多元醇产能约450万吨/年,其中还不包括2016年将建成投产的吉林神华集团的聚源化学工业股份有限公司的40万吨/年装置、万华化学的24万吨/年装置,产能过剩凸显。
聚醚多元醇生产的技术壁垒不高,中国生产企业较多,主要供应商有句容宁武化工、上海高桥石化、中海壳牌、山东东大、淄博德信联邦、佳化化学、南京红宝丽、河北亚东等。
(2)聚氨酯制品
聚氨酯制品按照其形态和应用,可分为聚氨酯泡沫、弹性体、鞋底原液、氨纶、合成革浆料、涂料和胶黏剂/密封剂等。随着我国经济增速放缓,消费低迷,直接影响了聚氨酯材料的消费增速,据统计,2015年我国聚氨酯制品的消费量约为1009万吨(含溶剂),增速约5%,低于我国GDP的增速。2015年我国聚氨酯制品的供需情况见表1-15。
表1-15 2015年我国聚氨酯制品的供需情况

①含溶剂。
①泡沫塑料 聚氨酯泡沫分软质、硬质、半硬质三大类。2015年中国聚氨酯软、硬质泡沫总消费量406万吨。聚氨酯软泡生产企业主要有新乡鑫源化工实业有限公司、乔福泡棉股份有限公司、圣诺盟控股集团、联大实业有限公司和南通馨源海绵公司,产能均在2~3万吨/年。
2012~2015年,硬泡聚氨酯复合板的生产企业爆发式增加到250多家,主要硬泡聚氨酯复合保温材料生产企业有万华节能科技集团股份有限公司、北京茂华聚氨酯建材有限公司、上海华峰普恩聚氨酯有限公司、浙江科达新型建材有限公司、江苏绿源新材料有限公司等。GB50016—2014《建筑设计防火规范》于2015年5月1日起开始实施后,我国聚氨酯复合板材生产企业举步维艰,大多处于停工状态。
②聚氨酯弹性体 2015年中国聚氨酯弹性体消费量86万吨,其中TPU由于原料价格的下降和优良的力学及加工性能,成为增速最快的聚氨酯产品。浇注型、混炼型产品规模较小而分散,厂家100~200家,主要有山西化工研究院、南京金三力橡塑公司、江苏泰来东方聚氨酯有限公司等。热塑型万吨级厂家约8家,主要企业有烟台万华聚氨酯公司、路博润特种化工制造(上海)有限公司、巴斯夫聚氨酯特种产品(中国)有限公司、东莞宏德化学工业有限公司、拜耳热塑性聚氨酯(深圳)有限公司等。
聚氨酯铺装材料主要用于塑胶田径跑道,篮、排球各运动场地等。约有300余个聚氨酯铺装材料生产、施工厂家,主要集中在北京、河北、山东、江苏、上海、浙江、广东等区域,占全国总量的80% 左右。铺装材料主要生产厂家有山东一诺威聚氨酯股份有限公司、青岛神鹿塑胶铺装有限公司、山东东海塑胶有限公司、北京蓝星科技有限公司、北京新世纪纳米塑胶材料有限公司。
③革鞋树脂 我国不仅是世界第一聚氨酯革用树脂生产和消费国,而且也是聚氨酯合成革制品(鞋类、服装、箱包等)最重要的出口国。2015年我国聚氨酯革用树脂产能400多万吨/年,主要集中在浙江、江苏和福建地区,约占全国总产能的70%。中国聚氨酯革用树脂产能在5万吨/年以上的生产企业有60余家,其中,华峰集团、旭川化学、华大树脂、上海汇得、嘉兴禾欣等5家企业所占市场份额较大,总计约50%,由于合成革产业前几年新增产能的集中释放,导致合成革企业同质化竞争异常激烈,绝大多数合成革企业均处于保本或亏损状态。再加上合成革生产工艺的环境污染问题已纳入政府重点管控范围,合成革企业的整体环境不容乐观。
④聚氨酯纤维(氨纶) 我国已成为全球聚氨酯纤维(氨纶)最大的生产、消费和出口大国,产能约占全球产能的70%。中国氨纶生产企业30余家,产能1万吨/年以上的企业有17家,主要生产企业有浙江华峰氨纶股份有限公司、诸暨华海氨纶有限公司、烟台泰和新材料股份有限公司、江苏双良氨纶有限公司和浙江薛永兴氨纶有限公司等。2015年我国消费量约48万吨,已完全实现自给。
⑤聚氨酯涂料 2015年使用异氰酸酯固化剂固化的各类涂料产量约165万吨。聚氨酯涂料企业主要集中在长江三角洲和珠江三角洲地区,聚氨酯涂料品种已达60多种。聚氨酯涂料主要生产企业有广东华润涂料有限公司、中华制漆(深圳)有限公司、东莞秉顺制漆有限公司、东莞大宝、维新制漆(深圳)、广东美涂士化工、广东鸿昌化工、深圳大中化工、广东嘉宝莉化工有限公司等。
(五)有机氟硅材料
氟硅材料是化工新材料领域我国最具资源和原料优势的领域,但目前萤石、工业硅等稀缺资源和高耗能基础原料高比例出口,而氟硅树脂等深加工产品出口量相对较少。
(1)有机氟材料
有机氟材料主要包括氟氯烷烃、氟硅橡胶、氟硅油、氟硅树脂、含氟烷烃等。
“十二五”期间,我国含氟聚合物通过加强自主创新、加快产业结构调整,技术装备水平明显提高,产品品种不断增加,质量稳步提升,已形成以氟氯烷烃为配套原料支撑的从氟单体合成到聚合物制造的较为完整的体系,主要产品产能、产量、出口规模已处于世界前列。含氟聚合物材料产业经历了2011年的暴利高点后,由于严重的同质化重复建设,2012年下半年开始出现过山车式的下滑,总体出现结构性产能过剩。
2015年,HCFCs产能达到100.45万吨/年,总产量78.05万吨;HFCs的产能74.6万吨/年,总产量达到43.95万吨。以HFOs为代表的新一代低GWP值的ODS替代品将实现快速增长。国内含氟聚合物总生产能力19.4万吨/年左右,产量12.9万吨左右。通用型氟树脂产品已有部分出口,但高性能产品仍依赖进口,其中氟树脂为净出口,我国氟橡胶生产能力达2万吨/年,通用型产品存在差能过剩问题,装置开工率低。表1-16是2015年中国氟硅树脂和橡胶供需情况。
表1-16 2015年有机氟材料供需平衡情况表

国内含氟聚合物产业与国际先进水平相比,主要差距体现在:产品低端,缺少高性能品种;产品单一,缺乏满足各种不同用途加工需求的专用化、系列化产品;产品稳定性不够,给下游加工带来不便。因此结构性短缺现象比较突出。
①聚四氟乙烯(PTFE) 具有抗酸抗碱、抗各种有机溶剂的特性,几乎不溶于所有溶剂,同时还具有强密封性、高润滑不粘性、电绝缘性和良好的抗老化能力、耐温优异(能在-180~+250℃的温度下长期工作),被称为“塑料王”。各类塑料王制品已在化工、机械、电子、电器、军工、航天、环保和桥梁等国民经济领域中起到了举足轻重的作用,聚四氟乙烯已成为市场需求最大的含氟聚合物产品。
目前国内聚四氟乙烯主要生产企业有山东东岳、四川晨光、浙江巨化、江苏梅兰和上海三爱富等。国内聚四氟乙烯生产主要集中在通用牌号。产能的重复扩张使国内聚四氟乙烯价格急速下滑,出现产能过剩,装置开工率下降,部分厂家甚至出现了长时间停产的情况。
虽然2015年国内PTFE价格急剧下跌,但进口PTFE价格相对稳定在高位,甚至有所上升,这也反映了我国PTFE结构性短缺的矛盾。
②聚偏氟乙烯(PVDF) 目前国内聚偏氟乙烯主要生产企业有三爱富万豪、山东东岳、浙江巨化等,近几年虽然PVDF国内年均消费增长率达到了46.90%,但产能扩张的速度更快,涌现了一批新进入企业,国外厂家也纷纷在中国投资建厂,进一步加剧了产能过剩。国内PVDF生产牌号主要集中在涂料级,注塑/挤出级色泽不稳定,加工之后容易出现发黄现象,不能完全替代进口,锂电池黏结剂和水处理膜领域还处于研究开发和市场推广阶段,主要依靠进口。
③聚全氟乙丙烯(FEP) 目前国内聚全氟乙丙烯主要生产企业有山东东岳、浙江巨化等,和其他含氟聚合物一样,近几年新进入厂家多,产能迅速扩张,产能也已经严重过剩。
④氟橡胶(FKM) 是指主链或侧链的碳原子上含有氟原子的高分子弹性体,国内多数生产的产品是偏氟乙烯与六氟丙烯的二元共聚物(FKM-26)或者偏氟乙烯、六氟丙烯与四氟乙烯的三元共聚物(FKM-246)。氟原子的引入,赋予橡胶优异的耐热性、抗氧化性、耐油性、耐腐蚀性和耐大气老化性,在航天、航空、汽车、石油和家用电器等领域得到了广泛应用,氟橡胶通常用于耐高温、耐燃料油、润滑油和强氧化剂的场合,是国防尖端工业中无法替代的关键材料。
随着氟橡胶的优异特性被逐步认识,国内氟橡胶的应用领域也越来越广泛,随之而来的则是社会需求量的迅速增加。国内总消费约12000~13000吨。此外国内军工、航空航天、水利设施等领域对氟橡胶需求也在快速增长。目前,氟橡胶国内市场需求稳中有升,国内氟橡胶企业仅能满足低端的生胶生产,部分氟橡胶加工企业仍大量选择进口国外氟橡胶产品。
⑤其他含氟聚合物
除了上述的四种聚合物以外,目前市场上用量相对较大的品种还有FEVE、ETFE、PFA等。
a. FEVE FEVE是指氟烯烃和乙烯基醚的共聚树脂FEVE。采用三氟氯乙烯或四氟乙烯为主要共聚单体,乙烯基醚或乙烯酯为共聚体,由自由基共聚反应可以制备FEVE树脂。FEVE树脂由氟乙烯单体和乙烯基乙醚(或酯)单体交替连接构成,氟乙烯单体把乙烯基醚单体从两侧包围起来,形成交替共聚物。FEVE树脂用于涂料领域,制得的含氟涂料不仅耐候性优异,而且耐酸碱及耐溶剂性优良,可以常温固化,大大拓宽了含氟涂料的应用领域。国内FEVE厂家主要集中在常熟中昊、大连振邦等厂家,国外生产厂家主要集中在日本旭硝子和日本大金公司,国内公司生产的FEVE产品质量不够稳定,只能应用在低端领域。
b. ETFE ETFE为乙烯-四氟乙烯共聚物,ETFE是最强韧的氟塑料,它在保持了PTFE良好的耐热、耐化学性能和电绝缘性能的同时,耐辐射和力学性能有很大程度的改善,拉伸强度可达到50MPa,接近聚四氟乙烯的2倍,乙烯-四氟乙烯共聚物膜有较高的机械强度。国内ETFE还没有厂家有成熟的产品投入市场,目前浙江巨化、山东东岳、江苏华奥等厂家在进行试验研究,国外公司日本旭硝子、日本大金和美国杜邦公司有成熟产品应用市场。
c. PFA PFA是四氟乙烯-全氟烷氧基乙烯基醚共聚物,熔融黏结性增强,熔体黏度下降,而性能与聚四氟乙烯相比无变化。PFA树脂可以直接采用普通热塑性塑料成型方法加工成制品,有与FEP相同的热熔流动性和用途,而PFA的内热性和耐开裂性更优于FEP,扩宽了使用领域。国内PFA还没有生产装置,浙江巨化、山东东岳、上海三爱富等主要含氟聚合物生产厂家都在进行试验,也有试验产品投放市场,但还不稳定,国外公司美国杜邦、日本大金、日本旭硝子、比利时苏威等主要含氟聚合物生产厂家都有PFA产品在市场上应用。
d. PCTFE PCTFE是三氟氯乙烯的均聚物,也是最早开发的热塑性氟塑料,PCTFE的耐热性虽不及PTFE,但它的压缩强度大,更宜作设备的耐高压防腐垫片,PCTFE具有优异的耐低温性能,可用作液氮、液氧、液态燃料的密封材料。国内PCTFE还没有生产装置,青岛宏丰、常熟中昊有试验,产品还很不稳定,国外主要是日本大金公司在生产。
e. PVF PVF是氟乙烯的均聚物,也是一种较晚开发的含氟树脂,是氟含量较低的含氟塑料,它的化学稳定性和使用温度虽不及PTFE、FEP等含氟聚合物,但PVF优良的耐候性、耐腐蚀和耐污染性,使它有一定的使用范围,PVF复合膜及分散液涂层用作保护和表面装饰材料。国内PVF只有中化蓝天有一套小生产装置,但没有成熟产品投放市场,国外公司主要是美国杜邦公司在生产。
(2)有机硅材料
2015年,中国有机硅单体生产企业共13家,甲基单体总产能达267万吨/年(折硅氧烷134万吨/年),2015年甲基单体实际产量约193万吨(折硅氧烷产量为96.5万吨),装置利用率约72%。
聚硅氧烷下游产品主要分为硅橡胶、硅油及硅树脂。其中硅橡胶按硫化方式可分为高温胶(HTV)、液体胶(LSR)、室温胶(RTV)等品种;硅油可分为甲基硅油、苯基硅油、氨基硅油、含氢硅油、羟基硅油等。中国硅橡胶发展的最为成熟,市场需求量较大,发展速度也较快。而硅油一直保持较为稳定的发展速度,生产量和消费量均逐年增加,纺织行业增速的放缓某些程度上影响了硅油的消费速度。硅树脂产品特别是高品质硅树脂产品却出现供不应求的情况,其应用不断开拓中。2015年中国主要聚硅氧烷产品生产统计见表1-17。
表1-17 2015年主要聚硅氧烷产品生产统计(实物量)

注:按实物量统计。
(六)高性能纤维
国内高性能纤维产量约9万吨,自给率为84%。目前国内碳纤维装置开工率仅约为20%,同时国内自给率仅为27%,主要原因是国内通用型碳纤维的生产成本高于进口产品价格,急需完善工程技术,降低生产成本。我国间位芳纶已能基本自给,但是对位芳纶仍严重依赖进口。聚对苯二甲酸丙二醇酯纤维长期受原料1,3-丙二醇供应不足的制约,2014年1,3-丙二醇实现大规模工业化生产,聚对苯二甲酸丙二醇酯纤维正在进入快速发展期。
在高性能纤维领域,碳纤维自给率严重不足,不到30%,详见表1-18。
表1-18 2015年中国高性能纤维供需情况

(1)碳纤维
我国碳纤维工业的起步可以追溯到20世纪60年代,基本上与日本同时期展开。但是之后相关研究和产业化工作进展缓慢,2015年,我国碳纤维产能约1.7万吨/年。我国已经培育出山东威海拓展碳纤维有限公司、江苏恒神碳纤维有限公司、中复神鹰碳纤维有限公司等龙头企业。在产品方面,目前国内已能稳定生产T300碳纤维,T700、T800等高规格产品也突破了制备技术瓶颈,部分碳纤维生产企业还在进行工程化技术研究。而日本企业已经能够生产包括T700、T800、T1000、T1100在内的系列产品。
国内碳纤维企业单线最高产能是1000吨/年,规格在12K以下、24K及以上的碳纤维产品质量不稳定,生产运行速度慢、运行工位少、装备保障能力弱、实际产量低、产品均匀性和稳定性差,导致国内产品生产成本高,市场竞争力差。
(2)芳纶
2015年中国芳纶总产能为1.9万吨/年,总产量1.2万吨,平均开工率60%,其中间位芳纶产能1.7万吨/年,产量9300吨,平均开工率56%;对位芳纶产能2500吨/年,产量2200吨,平均开工率88%。
2015年中国芳纶消费量约1.8万吨,其中对位芳纶消费量8500万吨左右,间位芳纶9500吨左右。2015年中国对对位芳纶依存度较高,2015年对位芳纶进口量为6979吨,出口量为667吨;间位芳纶的进出口数据基本保持平衡,进口量2264吨,出口量2040吨。
中国芳纶主要生产企业有烟台泰和新材、江苏圣欧、广州彩艳、杭州九隆和蓝星晨光等,另外河南神马、仪征化纤、苏州兆达、河北硅谷等企业处于工程化研发和建设阶段。
(3)PTT纤维
20世纪90年代后期,国内有多家生产企业正在进行有关PTT的合成、PTT纤维的制造及应用等方面技术的开发,如上海石化股份有限公司、仪征化纤股份有限公司、中国纺织大学等,并取得了一些进展。因PTT工艺技术的绝对垄断和PDO单体未能大规模工业化生产,导致国内PTT工业化进程缓慢。2000年8月,上海华源股份有限公司与壳牌化学公司达成协议,合作开发PTT纤维及纺织品,2004年,泉州海天轻纺集团经杜邦公司正式授权使用材邦Sorona聚合物开发、生产和销售PTT短纤维、纱线及其织物。2009年12月,由石狮文兴集团、泉州海天集团与美国杜邦公司合资2万吨/年PTT柔性短纤生产线,采用美国杜邦的玉米Sorona聚合物技术,生产PTT短纤维、功能性纤维、细旦纤维、中空纤维等系列产品。
2008年7月,盛虹集团旗下的江苏中鲈科技发展股份有限公司一期年产8000吨的PTT纺丝项目正式投产,引进Oerlikon Barmag(欧瑞康巴马格)设计生产的国际先进的PTT专用纺丝设备技术,改进工艺,该公司已试制出了PTT记忆纤维和超细纤维。
2015年国内PTT纤维产量约为6万吨,进口量约0.2万吨,表观消费量6.2万吨,基本能实现自给。
PTT纤维面料及其各种混纺、交织面料市场将迎来超速发展的黄金时期,PTT代替尼龙,用于生产短纤维和长丝产品,有很强的市场竞争能力,未来将有较大的需求。
(4)UHMWPE纤维
国内最初的生产厂家有3家:浙江宁波大成新材料股份有限公司、湖南中泰特种装备有限责任公司和北京同益中特种纤维技术开发有限公司。目前,我国的UHMWPE纤维生产厂家已发展至30家左右,形成了较为完善的规模化生产能力。目前国内市场产能约为2.8万吨/年左右,若在建产能完全释放可达3.5万吨/年以上。我国UHMWPE应用较多的是绳索类产品,其次是应用于轻质防弹衣、防刺服、防弹头盔等产品。业内人士估计目前国内对UHMWPE纤维的年需求量在1.5万吨左右,我国UHMWPE年产量已达8000余吨,不仅可以部分替代从国外进口,而且可以出口创汇,每年出口收入超过20亿元。
高强高模聚乙烯纤维作为一种重要的战略性高新技术材料,对我国进行技术封锁项目,按规定其生产工艺技术不予转让,产品禁止销往其他国家作为军需用品。中国成为世界上第三个掌握UHMWPE纤维生产技术并能产业化生产的国家,国内UHMWPE纤维性能已经达到国际水平并各具特色,也结束了我国警用防弹材料较长时间依赖进口的历史。
超高分子量聚乙烯纤维是我国唯一具有国际竞争力的高性能纤维,也是获得专利最多的品种。我国单套生产线最大产能为400吨/年,相当于国外的1/2,如果采用国产树脂和设备,目前达到2500吨/年总产能的产品成本估计为100元/kg左右,这是国外产品难以达到的。据调查,国内部分厂家相关产品的单丝强度可达到45cN/dtex,产品均匀性好,纤度不匀率可控制在2%左右,总体技术已经基本达到国际先进水平。随着生产工艺的进一步优化,UHMWPE纤维的生产成本将逐步下降,特别是有些企业实现千吨级规模生产后,总体成本进一步降低,从而刺激需求的增长。
(七)高性能膜材料
高性能膜材料主要包括水处理用膜、特种分离膜、离子交换膜、锂电池和太阳能电池用特种膜、光学膜等。2015年年底,我国膜工业产值已突破千亿大关,其中膜材料产值约450亿元,消费的功能性膜材料重量约43万吨,面积约为27亿平方米,市场销售额约为450亿元,其中高端产品主要依靠进口,按重量、面积和销售额计的国内自给率分别为54%、51%和43%。国内高性能膜材料消费情况见表1-19。
表1-19 国内高性能膜材料消费情况

注:数据来源于石油和化学工业规划院。
目前全球高性能膜材料的发展呈现以下特点:膜材料产业向高性能、低成本及绿色化方向发展;膜材料市场快速发展,与上下游产业结合日趋紧密;膜技术对节能减排、产业结构升级的推动作用日趋明显;膜技术对保障饮水安全,减少环境污染的作用显著增强。长远来看,我国特种膜技术的发展仍需紧密围绕国家重大需求,加强基础理论与原创技术的研究,继续推动我国膜领域的“三个提升”:通过膜材料设计与制备的基础研究,提升学术水平;通过高性能分离膜材料的工程技术研究,提升产业竞争力。
(1)水处理用膜
目前全球水处理用膜组件、膜工程的市场规模约分别达110亿美元、400亿美元。国内随着排水及供水标准的不断提高,膜法水处理技术在给排水处理设施升级改造中得到了大规模应用,“十二五”期间市场空间超过1200亿。
今后预计膜市场的增长率会很高,《中国膜行业“十三五”战略发展规划》对重点产品的要求是:RO膜技术完全达到国际先进水平,海水淡化RO膜国内市场占有率实现30%~50%,微滤膜及超滤膜质量实现新突破,国内市场占有率达60%~80%。至今为止,我国RO膜仍主要依赖进口,微滤膜、超滤膜的国产率也仅有50%。国内高性能水处理膜材料上市公司主要有以下几家:膜材料板块的上市公司包括裕兴股份、康得新、沧州明珠、东材科技、碧水源、万邦达、中电环保、维尔利、巴安水务、津膜科技等。其中,从事膜生产的企业主要是碧水源(MBR抗污染膜)、津膜科技(深度处理、及海水淡化),此外,还有南方汇通下属的时代沃顿公司(苦咸水淡化)。
超滤膜作为目前最有效的水预处理方法,在国内市场开始迅速增长。相对于反渗透膜强大的市场占有率,目前超滤膜还没有形成较大的占有局面,但近几年超滤膜开始翻倍增长,进入发展关键期。现在越来越多的企业选择超滤膜来做预处理,不仅是因为超滤膜是目前水预处理最有效的方法,还因为反渗透系统要想得到良好的运行,最好的方法就是用超滤膜来做预处理。
天津膜天膜科技股份有限公司已突破国外公司在TIPS法生产聚偏氟乙烯中空纤维膜的技术封锁,开发了具有完全技术知识产权的TIPS法聚偏氟乙烯中空纤维膜制备工艺,已建设一条TIPS法高性能PVDF中空纤维膜生产线(135万平方米)。北京赛诺膜技术有限公司(赛诺膜)率先在国内采用热致相分离(TIPS)技术大规模工业化生产PVDF中空纤维膜及系列化膜组件,已建成了国内首条年产200万平方米的TIPS法PVDF中空纤维膜生产线,产品性能达到国际先进水平,成功替代了国际著名品牌产品,环境及经济效益非常显著。
新加坡美能材料科技有限公司的热致相分离法(TIPS)制备PVDF超滤膜生产线于2009年在广州和绵阳投产。美能(MEMSTAR)应用自主的PVDFTIPS法的制造设备和独特的配方,经过一年多的时间完成基础研究、中试和产业化的全过程。开发TIPS法高性能PVDF中空纤维超/微滤膜制备技术,实现高强度和高通量,高过滤精度,低成本的PVDF中空纤维超/微滤膜工业化生产。
历经20余年的研究开发及应用示范,我国已在膜法海水淡化工艺装备和系统集成等方面取得了重大突破,先后研制出了具有自主知识产权的反渗透膜元件、压力容器、高压泵、能量回收装置等核心部件和关键设备,反渗透海水淡化单机产能突破万吨级关口,并建立了12500吨/日的示范装置,以及规模为日产5万吨示范工程,系统制水能耗、运行成本等关键技术指标与世界先进水平同步,国产化膜法海水淡化技术与装备已成功参与国际市场竞争。
(2)离子交换膜
当前,我国对高性能离子交换膜材料需求强劲,特别在燃料电池、液流电池、电渗析、氯碱等方面。我国每年都要花费巨额资金进口,尤其是全氟磺酸离子交换膜及磺化芳香族聚合物等材料。然而,由于国内均相离子交换膜工业化产品的空白,以日本为首的国家对我国进行相关技术封锁和价格垄断,使得国外均相离子交换膜价格在国内不仅价格高昂(1500~2000元/m2),而且供货周期长、附加条件多,大大阻碍了电膜技术的应用推广。目前我国氯碱行业对全氟离子交换膜的年需求量在(30~40)万平方米,但几乎全部依赖进口。据统计2010年氯碱工艺用膜的54%使用旭化成膜。
我国离子交换膜的研究是从20世纪50年代后期开始的,也是我国最早开发研究的膜品种,当时北京和上海的科研单位最早是将离子交换树脂磨成粉再加压成异相离子交换膜。以此技术为基础,形成了现在我国市场上离子膜的主导产品,年产量达5×105m2左右。国内的一些单位(包括山东东岳集团、上海交通大学、中科院上海有机所、中科院大连化学物理所、中国科技大学、大连理工大学、山东省海洋化工科学研究院、中科院宁波材料所等)除在含氟的离子交换膜取得进展外,也在经济型的离子膜方面开展了大量的基础研究工作。研究的思路大部分还是在含有苯环的各种高分子体系,包括聚苯醚、聚醚砜、聚酰亚胺、聚醚醚酮等的体系中引入功能基团。虽然部分研究成果已形成了中试规模的生产,但还没能形成规模化的应用及产品的系列开发。2011~2014年,科技部及有关部委大力实施膜技术攻关及产业化,全氟离子膜、酸碱回收膜、双极膜等膜产品的技术研究已达世界先进水平。
(3)特种膜
①渗透汽化膜
世界上已相继建成了400多套渗透汽化膜工业装置。在膜组件方面,已经开发成功了板框式、管式和中空纤维膜组件。其中,板框式组件是最早开发成功的膜组件。我国渗透汽化膜分离技术的研究始于20世纪80年代初期,清华大学膜技术工程研究中心自1984年以来,一直从事膜技术研究,是我国最早从事渗透汽化膜技术研究开发的单位之一。随后渗透汽化因高效、节能、环保、不引入第三组分等优点,逐渐成为有机溶剂分离领域的后起之秀。依靠其自身独特的优势,逐渐被应用到工业生产中。其中以山东蓝景膜技术工程有限公司为代表的专业从事渗透汽化膜开发生产的企业也逐渐兴起,主要解决一些企业单位有机溶剂分离等问题,它符合国家节能减排和循环经济的产业政策,能帮助企业解决实际问题。作为一种新型的分离技术,渗透汽化膜分离技术需要克服汽化膜开发应用等技术问题,从而使渗透汽化膜分离技术更好地应用于各个领域。随着渗透汽化膜分离技术的发展,在石油化工方面的应用也将更加成熟,渗透汽化膜分离技术应用于石油化工能够降低生产过程中的能源消耗,保护环境,同时能够提高生产过程中的经济效益。
②无机陶瓷膜
陶瓷膜是高性能膜材料的重要组成部分,属于国家重点大力发展的战略新兴产业。陶瓷膜是由金属氧化物制备而成的具有高效分离功能的薄膜材料,具有耐高温、耐化学侵蚀、机械强度好、抗微生物能力强、渗透通量大、可清洗性强、孔径分布窄、使用寿命长等特点,在多个领域有着很好的应用前景,市场发展迅猛。
陶瓷膜作为特种分离膜材料,在多个领域中应用广泛,新型陶瓷膜材料及成套装备技术不断发展。陶瓷膜材料的发展趋势主要有两个:一是更高分离精度的陶瓷材料的开发与应用,目前仅有个别外国公司具有生产陶瓷纳滤膜的技术和实力,二是低成本高装填密度的陶瓷膜元件的开发,南京工业大学也已开发出适合于水处理的低成本蜂窝状陶瓷膜。若实现产业化,应用成本将有较大下降空间。
近年来陶瓷膜市场发展虽受国际国内经济形势较为严峻的影响而增速下降,但仍保持稳步增长。到2015年,中国无机膜市场需求超过200亿元,占到世界总量的10%~15%。陶瓷膜在新领域获得了显著拓展,在许多新兴应用方向实现了工业化应用,开发出了多种工艺技术与成套装备,为陶瓷膜应用的持续发展储备了市场空间,随着面向应用过程的陶瓷膜设计与制备的理论体系的进一步完善,陶瓷膜应用技术的进一步提高,预期在今后数年将形成百亿元以上的市场规模。
(八)电子化学品
电子化学品的应用领域主要是集成电路、平板显示器、新能源电池和印制电路板。2015年我国电子化学品消费量约为69万吨,国内市场销售额为460亿元,按重量和销售额计的国内自给率分别为53%和40%,为新一代信息产品配套的电子化学品主要依靠进口,无法满足信息产品快速更新换代的配套需求。由于进入门槛高,目前国产电子化学品和材料在国内市场占有率低,且多在中低端市场,高端市场仍由日本、欧美、韩国及中国台湾地区的厂商垄断,部分产品进口依存度高达90%。
四、存在的问题
(一)化工新材料国内产业化程度还比较低
部分化工新材料产品目前国内仍未实现大规模工业化生产。在高性能树脂领域,国内目前尚属空白的产品主要有茂金属聚丙烯等高端聚烯烃、聚醚醚腈等特种工程塑料、可熔性聚四氟乙烯等特种氟树脂;在特种合成橡胶领域,SEPS、聚酰胺型热塑性弹性体和聚酯型热塑性弹性体等新型热塑性弹性体仍未实现工业化生产;在功能性膜材料领域,PVF太阳能背板膜等高端产品还没有实现大规模产业化。部分化工新材料产品,例如通用级碳纤维处于产业化的起步阶段,虽然已建成工业化生产装置,但是技术尚不成熟,生产成品率低,成本高于进口产品价格,急需完善工业化技术,降低生产成本,实现正常生产。
另外部分化工新材料产品虽然国内已有生产,但是主要由外资企业生产,例如我国消费量最大的工程塑料聚碳酸酯主要依靠进口,而国内产量主要来自外资企业。
(二)化工新材料产品结构还不能满足国内需求
部分化工新材料产品虽已国产化但产品质量与进口产品差距很大,只能满足中低端需求。在高性能树脂领域,此类产品主要有茂金属催化聚乙烯等高端聚烯烃、聚甲醛和聚苯醚等工程塑料、聚偏氟乙烯和聚全氟乙丙烯等新型含氟材料及氟硅树脂等;在特种合成橡胶领域,主要有乙丙橡胶、丙烯酸酯橡胶等石油基高性能橡胶和聚氨酯弹性体等热塑性弹性体;在功能性膜材料领域,主要有PVDF太阳能背板膜和液晶显示器用TAC膜。
部分化工新材料产品虽然已实现国内自给,但是高端产品基本由外资企业生产,内资企业产品质量差距较大,局限于中低档市场,例如高吸水性树脂虽然已经国内自给,但内资企业只能生产中低端产品。
针对不同的细分市场,需要对不同类型的化工新材料进行改性,以达到最佳性价比,目前国内部分化工新材料的特种改性产品如发动机进气歧管用特种改性尼龙主要依靠进口。
另外,某些特殊用途的化工新材料制品国内基本也属空白,例如页岩气钻头桥塞等油气开采用特种氟材料制品和耐中高温的食品包装用无溶剂聚氨酯胶黏剂。
(三)化工新材料关键配套原料产业化程度还有待提高
部分化工新材料的关键配套单体国内尚未工业化生产,严重制约化工新材料的发展。在高性能树脂领域,八碳及其以上的高碳α-烯烃尚未国产化,制约高碳α-烯烃共聚聚乙烯的发展;己二腈完全依靠进口,制约聚酰胺工程塑料的发展;异丁烯法MMA尚未产业化,制约PMMA的发展;CHDM供应困难制约PCT和PETG等特种聚酯的发展;1,3-丙二醇依赖进口,制约PTT的发展;IPDI和H12MDI等特种异氰酸酯国内空白,制约高端聚氨酯材料的发展;在高性能合成橡胶领域,异戊二烯的供应仅限于乙烯联产,从数量和成本上都无法保障异戊橡胶的发展,急需发展异丁烯合成异戊二烯。在功能性膜材料领域,分离膜用的PVDF树脂国内尚未实现大规模生产,目前国内PVDF树脂主要是涂料级产品。
(四)部分化工新材料具有很大的发展潜力
部分化工新材料有望大范围推广应用,成为新的大宗材料,但是需要进行应用示范,解决加工和应用技术问题,进行应用验证。例如异戊橡胶在俄罗斯已经全面替代天然橡胶用作轮胎,天然橡胶占我国橡胶消费量45%以上,但80%以上依靠进口,急需推广应用异戊橡胶弥补天然橡胶的供应不足,因此应当完善优化异戊橡胶的加工成型技术,进行各类异戊橡胶轮胎的应用验证,加快异戊橡胶在轮胎领域的推广应用。
五、发展方向及趋势
我国化工新材料发展的重点领域包括:有机硅单体及下游应用材料,新型高档聚四氟乙烯和氟橡胶、聚偏氟乙烯、聚全氟乙丙烯等新型含氟聚合物,缺口较大的工程塑料与特种工程塑料,树脂改性、共混、合金化、加工技术,淀粉塑料、聚乳酸、PBS等可降解类产品,高性能纤维(碳纤维、芳纶、PTT纤维和超高分子量聚乙烯纤维等)、复合材料和功能高分子材料。
未来化工新材料行业的发展重点如下。
(一)大力实施技术改造,提高国内装置的开工率
围绕优化原料结构、提高产品质量、降低消耗排放、促进本质安全,利用清洁生产、综合利用、智能控制等先进技术装备对现有生产装置进行改造提升,与国外先进工艺技术水平进行对标,进行准确的定位,确定差距,对症下药,推动化工新材料产业降本增效,提高综合竞争能力,提高国内装置的开工率,实现进口替代。提升化工新材料自身的发展水平,降低能源和物料消耗以及污染物排放,提高产品的国际竞争能力,重点提高国内已有品种的质量水平,实现产品差异化、高端化。
(二)加大科研和产业化投入,突破产业瓶颈
追踪和对标国际领先和前沿技术,组织和支持研究开发团队和企业技术中心以及用户进行科技联合攻关,切实有效突破产业瓶颈,实现良性健康发展。充分利用好国家已有的科研专项基金和产业化助推基金和政策,力争有效突破。
(三)积极推进重大工程项目建设
围绕满足国家重大工程及国计民生重大需求,以《中国工业制造2025》为导向,以满足国内高端市场需求为重点,以产业联盟的方式,加快延伸发展下游高端制品并加快化工新材料在新应用领域的推广。
针对高端产品制造、生物化工、节能环保产业培育等重点领域,突破一批共性技术、关键工艺、成套装备。有序推进汽车轻量化化工新材料工程、高性能膜工程和电子化学品自给率提升工程。
(四)优化调整化工新材料产业布局
按照全国主体功能区规划、区域产业布局规划、城市发展规划以及园区产业定位要求,优化化工新材料产业园区布局,依托园区已有的化工基础原料产业和现有的化工新材料产业特色,重点打造20个左右以分领域为特色的化工新材料产业园区,引导产业资本集中投资,避免化工新材料园区遍地开花,产业松散,缺乏综合竞争力。
(五)加强国际产能合作
继续发挥外资在引进资金、先进技术、管理经验和高素质人才方面的作用。鼓励外资投向化工新材料产业,在我国设立全球研发机构。鼓励外资参与国内企业兼并重组,与国内企业在全球范围开展合资合作。
通过全球资源优化、业务流程再造、产业深度整合、资本市场运作等方式,打造一批具有国际竞争力的跨国企业,在境外开展并购和股权投资、创业投资,建立研发中心、实验基地和全球营销及服务体系。发挥骨干企业的技术和资金优势,推进上下游产业链融合和集群发展。
(六)强化知识产权意识,提升行业知识产权创造、运用、保护和管理能力
积极贯彻实施《国家知识产权战略纲要》,强化知识产权的创造、运用、保护和管理。加强对外科技和产业交流与合作,注重引进技术的消化吸收再创新,全面赶超国际先进水平。强化企业知识产权意识,加强知识产权保护,建立健全技术资料、商业秘密、对外合作知识产权管理等法律法规,保障知识产权所有人的合法权益,促进自主创新成果的知识产权化、商品化、产业化,提升行业知识产权创造、运用、保护和管理能力。