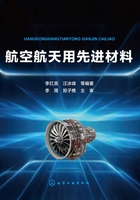
1.4 航空航天材料的应用
1.4.1 航空航天材料的服役环境
除了经受高应力、惯性力外,航空飞行器还要经受起飞和降落、发动机振动、转动件的高速旋转、机动飞行、突风等因素导致的冲击载荷和交变载荷。发动机燃气以及太阳辐照导致航空器处于高温环境,随着飞行速度提高,气动加热效应凸显,产生“热障”。此外,还要经受交变温度,在同温层以亚音速飞行时,表面温度会降到-50℃左右,极圈以内地域的严冬环境温度会低于-40℃,金属构件或橡胶轮胎容易产生脆化现象。汽油、煤油等燃料和各种润滑剂、液压油,多数对金属材料产生腐蚀作用、对非金属材料产生溶胀作用,而太阳辐照、风雨侵蚀、地下潮湿环境长期储存产生的霉菌会加速高分子材料的老化过程。
宇宙的严酷环境对人类提出了严峻挑战。随着离地距离增加,大气压、大气密度、地球引力逐渐下降,强宇宙射线辐射逐渐增强,在高真空环境,互相接触的金属材料会出现“冷焊”现象,在高真空和宇宙射线辐照下,非金属材料会加速挥发和老化。对于航天器,低温推进剂、发动机燃气、空气动力加热、太阳辐照导致表面温度出现大范围的交变。液体火箭发动机使用液氧和液氢作为推进剂,其沸点很低,部分金属材料和绝大多数高分子材料在如此低的温度环境都会变脆。航天器进入太空或者返回大气层时会产生气动加热,其表面会产生上千摄氏度乃至上万摄氏度的高温,返回舱、弹道导弹弹头再入大气层时会出现热障现象,到达离地面60~70km时,速度仍然保持在声速的20多倍,处于严重的气动加热环境中,温度急剧升高至10000℃以上,必须采取特别措施来克服气动加热导致的“热障”。火箭发动机燃气温度达3000℃以上,喷射速度达10余个马赫数,固体火箭燃气中还夹杂有固体粒子,飞行器要经受高温高速气流和粒子冲刷。四氧化二氮、肼类等火箭推进剂以及各种润滑剂、液压油,多数对金属有强烈的腐蚀作用,对非金属材料有溶胀作用。
1.4.2 航空航天材料的失效分析
在极端环境(超高温,超低温,高真空,高应力,强腐蚀介质)、交变载荷和交变温度联合作用下,航空航天材料容易出现磨损、变形、开裂、腐蚀、疲劳、蠕变和应力松弛等行为,导致零件、构件、仪器、装置、系统等出现功能衰退或失效,使飞行器失去可靠性和安全性。
1.4.2.1 磨损
相互接触的一对表面发生相对运动(滑动和/或滚动)时,接触表面微小部分分离出来,导致质量不断损耗和接触面尺寸不断变化,这种现象称为磨损。磨损可分为黏着磨损、磨料磨损、表面疲劳磨损、冲刷磨损、腐蚀磨损等基本类型,实际服役中往往存在多种磨损类型的复合状态,产生复合磨损失效。在局部高压下,两个金属表面的微凸部分产生局部黏着,称为黏着磨损,主要特征是材料从一个表面转移到另一个表面,或撕下作为磨料留在表面之间,严重时产生“咬合”现象,完全丧失滑动能力。因外来硬颗粒或表面微凸体的作用,导致相对运动的配合表面损伤,称为磨粒(料)磨损,主要特征是表面被犁削形成沟漕。滚动或滚动滑动复合摩擦的接触表面,在交变接触压力作用下,因材料表面疲劳而产生的磨损,称为表面疲劳磨损,主要特征是表面小片脱落而形成麻坑。含有固态粒子的流体冲刷表面而导致的磨损为冲刷磨损,固体粒子的运动方向与被冲刷表面平行时为研磨冲刷,固体粒子的运动方向与被冲刷表面近似垂直时为碰撞冲刷。金属在摩擦过程中与周围介质发生化学或电化学反应,产生表层金属的损失或迁移,称为腐蚀磨损,化学反应增加了磨损。
磨损为动态过程,相互作用的耦合件表面形貌、成分、结构和性能都随时间推移而发生变化,与此同时,磨损亚表层(表面下相当厚度的一层金属)也会因磨损发生变化,产生变形和加工硬化及软化,形成绝热剪切层、超细晶层、非晶态层等。磨损失效分析主要包括磨损表面形貌分析、磨损亚表层分析、磨损产物(磨屑)分析,根据磨损表面的宏观形貌可初步判断磨损类型、磨损程度及原因;根据磨损微观形貌分析可以了解磨损过程及工况条件对磨损过程的影响,分析磨损机理;通过磨屑形貌观察,配合磨损表面形貌及亚表层特征分析,可判断磨屑的类型(切削屑,变形屑,脆断屑)。为了深入了解磨损失效的细节,可根据磨损件的运行规律和工况条件进行磨损的强化模拟试验,分析各种类型材料的磨损特性。
1.4.2.2 变形
结构件在外力作用下会发生变形,外力较小时发生弹性变形,卸载后变形恢复,外力较大时发生塑性变形,为不可逆和永久性的变形,当承受的载荷过大时就会发生断裂。
晶体材料的弹性变形是因原子在力作用下偏离其平衡位置而产生微小位移所致,高分子材料的弹性变形是因分子链沿受力方向伸展所致,外力去除后原子和分子链回归到原来的位置,弹性变形消失。金属、陶瓷、结晶态高分子材料的弹性变形量较小,应力应变保持线性关系,橡胶态高分子材料的弹性变形量较大,应力应变不遵循线性关系。
金属材料的塑性变形主要是因应力迫使晶粒内部及晶粒间产生滑移和转动所致,滑移是晶体的一部分沿一定晶面(原子密排晶面)和晶向(原子密排晶向)相对于另一部分产生位移,滑移前后晶体结构和晶格位向均未改变。晶体还可能以孪生方式产生塑性畸变,晶体的一部分沿着一定晶面(孪生面)相对于另一部分产生一定角度的切变,发生切变的部分称为孪生带,简称孪晶,孪晶的晶格位向已发生改变,但晶体结构没有变化。陶瓷材料的塑性变形通常是晶相滑移所致,只有少数具有简单晶体结构的陶瓷在室温下产生塑性畸变,非晶态陶瓷材料的塑性畸变是分子位置交换所致,属于黏性流动变形机制,在一定剪切应力作用下,材料以一定变形速度流动而产生不能恢复的变形。结晶态高分子材料的塑性畸变是因薄晶体转变成沿应力方向排列的微纤维束所致;非晶态高分子材料的塑性畸变,一是在正应力作用下形成银纹,二是无取向分子链在切应力作用下转变为规则排列的纤维束。
弹性变形主要受工件形状尺寸、材料的弹性模量、服役环境和载荷大小影响,与强度无关。除了导致弹性变形的因素外,导致塑性变形的因素还有材质缺陷、使用不当、设计失误等。材质缺陷包括冶金缺陷和热加工缺陷,较为常见的是热处理不良造成的缺陷,热处理未能使工件达到所需的硬度和屈服强度。实际上,在制造和装配过程中会产生机械应力、热应力、组织应力、装配应力,造成不均匀塑性变形而导致残余应力,应力集中和残余拉应力会导致早期疲劳断裂、应力腐蚀断裂和低应力脆断,残余应力的重新分布会导致工件发生变形。
1.4.2.3 断裂
断裂是结构件最危险的失效形式。材料内部缺陷引起的微裂纹,在外力或外力与环境(腐蚀、温度、辐照等)联合作用下,扩展到大于临界尺寸后失稳而快速扩展,导致结构件断裂,被分成两个或几个部分。
(1)裂纹分析
按形成的先后次序,裂纹可分为主裂纹和二次裂纹,主裂纹通常扩展较快。按扩展途径,裂纹可分为沿晶裂纹和穿晶裂纹。按产生原因,裂纹可分为使用裂纹和工艺裂纹,疲劳裂纹、应力腐蚀裂纹、氢脆等为使用裂纹,加工过程中产生的裂纹为工艺裂纹。
裂纹源总是在构件承受应力最大(应力集中)处和薄弱环节(材料缺陷)处,通常在裂纹源处都能找到缺陷,在裂纹扩展的转折处也能找到缺陷。微观裂纹扩展的方向可能穿晶、沿晶或二者混合,如图1-25所示。当晶界强度大于晶内强度时,裂纹穿晶扩展;应力腐蚀、氢脆、过烧等的晶界为薄弱环节,裂纹沿晶扩展。

图1-25 裂纹穿晶扩展和沿晶扩展
根据应力场强度因子与断裂韧度的相对大小,可以建立裂纹失稳扩展断裂的K判据,如式(1-8)所示,由于平面应变断裂最危险,通常以KⅠc为临界值。
KⅠ ≥KⅠc (1-8)
裂纹体受力时,如果KⅠ ≥KⅠc ,裂纹扩展发生脆断;如果,即使存在裂纹也不会发生断裂,称为破损安全。材料的KⅠc越高,裂纹体的断裂应力或临界裂纹尺寸越大,因此可以用KⅠc表征材料抵抗断裂的能力。对于高强度脆性材料,利用K判据可以估算裂纹体的最大承载能力σ、允许的裂纹尺寸a,可用于分析评价带伤工件的安全性和寿命,也可用于选材、优化工艺等。
裂纹分析包括裂纹部位的宏观分析、裂纹的微观分析、材质的检验,首先采用X射线、磁粉、超声波、荧光等探伤方法检测裂纹的存在,然后通过观察裂纹的形态、大小、颜色、产生部位及走向确定主裂纹和裂纹源,并在取样前进行宏观形态拍照。
确定主次裂纹主要采用T型法、分叉法、变形法、氧化颜色法、疲劳裂纹长度法等方法。通常,脆性断裂可用T型法或分叉法判别主次裂纹;韧性断裂则可用变形法来判别主次裂纹;环境断裂可根据氧化或腐蚀程度及颜色深浅来区分主次裂纹;疲劳断裂通常利用断口的宏观、微观特征形貌加以区分。当断裂成2块或2块以上碎片时,如图1-26所示,可将其合拢起来,其裂纹如构成T型,则横贯裂纹为主裂纹,其他裂纹为二次裂纹。图1-27为判别主次裂纹的分叉法示意图,通常裂纹的分叉或分支方向为裂纹扩展方向,相反方向为裂纹的起始方向,即分支或分叉裂纹为二次裂纹,汇合裂纹为主裂纹。

图1-26 判别主次裂纹的T型法示意图

图1-27 判别主次裂纹的分叉法示意图
当构件在断裂过程中产生变形并断裂成几块时,可根据各碎块不同方向上的变形量大小来确定主次裂纹,变形量大的部位为主裂纹,其他裂纹为二次裂纹。对于在环境介质与温度作用下的断裂,颜色较深的为主裂纹部位,颜色较浅的为二次裂纹部位。疲劳断裂可根据疲劳裂纹扩展区的长度、疲劳弧线或疲劳条带间距的疏密来判别主次裂纹,疲劳裂纹长、疲劳弧线或条带间距密者为主裂纹,反之为二次裂纹。
(2)断裂分析
根据受力状态,断裂可分为静载断裂(拉伸断裂,扭转断裂,剪切断裂等)、冲击断裂、疲劳断裂。根据断裂面取向,断裂可分为正断型断裂和切断型断裂,塑性变形受到较大约束时发生正断型断裂,塑性变形不受约束或受约束较小时发生切断型断裂。根据断裂前的塑性变形量,断裂可分为韧性断裂和脆性断裂。根据裂纹扩展路径,晶体材料的断裂可分为穿晶断裂和沿晶断裂。根据微观断裂机理,断裂可分为解理断裂和剪切断裂。断裂类型会随环境变化而改变,如低温冷脆断裂、高温蠕变断裂、应力腐蚀断裂和氢脆断裂。
①韧性断裂和脆性断裂 产生了明显塑性变形的断裂称为韧性断裂,一般为缓慢撕裂,断口呈暗灰色、纤维状。没有明显塑性变形的断裂称为脆性断裂,通常规定光滑拉伸试样的断面收缩率小于5%的为脆性断裂,断口齐平光亮,呈放射状或结晶状。室温静载拉伸时,塑性较好的金属材料和聚合物材料发生韧性断裂,陶瓷、玻璃等无机非金属材料通常发生脆性断裂,金属在韧脆转变温度以下发生脆性断裂,聚合物在玻璃化温度以下发生脆性断裂。
②沿晶断裂和穿晶断裂 穿晶断裂的特征是裂纹穿过晶粒内部扩展,可以是韧性断裂或脆性断裂。金属在室温通常产生穿晶韧性断裂或混晶断裂,在其韧脆转变温度以下通常产生穿晶脆性断裂,而离子键晶体以穿晶解理断裂为主。沿晶断裂的特征是裂纹在晶界形成并沿晶界扩展,多为脆性断裂,但是,高温蠕变会产生沿晶韧性断裂。共价键陶瓷和晶界较弱(包括高温导致晶界弱化)的金属材料通常产生沿晶断裂,当晶粒特别粗大时,沿晶断裂形成石块或冰糖状断口;当晶粒较细时,沿晶断裂形成结晶状断口,比解理断裂的结晶状断口的反光能力稍差,颜色黯淡。偏聚于晶界的杂质元素、脆性第二相和夹杂物等会弱化晶界结合力,当晶界受到损伤并形成晶界开裂时,裂纹沿晶界扩展的阻力最小,容易产生沿晶断裂。材料在热加工过程中,因加热温度过高,造成晶界熔化,严重减弱了晶界结合力和晶界处的强度,受载时会产生早期的低应力沿晶断裂。环境因素与晶界相互作用造成的晶界弱化或脆化,如高温蠕变条件下的晶界弱化,应力腐蚀条件下晶界易于优先腐蚀等,均促使沿晶断裂产生。因此,将金属进行提纯、净化晶界、防止杂质原子在晶界偏聚、防止第二相在晶界析出、改善环境因素等,均可降低金属发生沿晶脆性断裂的倾向。
③解理断裂和剪切断裂 在正应力作用或低温条件下,原子间的结合键被破坏,致使材料沿特定晶面以极快速率发生的穿晶断裂,称为解理断裂,属于脆性断裂,但脆性断裂不一定是解理断裂。解理断裂具有明显的结晶学性质,裂纹沿着一定结晶方向<uvw>扩展,断裂面为解理面{hkl},解理面是原子键合力最弱、在正应力下容易开裂的晶面,通常为低指数晶面或表面能最低的晶面。体心立方、密排六方金属及合金处于低温、冲击载荷作用下,通常会发生解理断裂,体心立方的解理面为{100}面,六方晶系的解理面为{0001}。对于面心立方金属,通常不发生解理断裂,但在非常苛刻的环境下也可能发生解理断裂。剪切断裂是材料在切应力作用下沿滑移面分离而造成的断裂,又分为滑断和微孔聚合型断裂。滑断为纯剪切断裂,用肉眼观察断口可以看到很多直线状的滑移痕迹。微孔聚合型断裂是材料韧性断裂的普遍形式,宏观断口一般呈现暗灰色、纤维状,微观断口分布大量韧窝。在外力作用下,在夹杂物、第二相粒子与基体的界面处,或在晶界、孪晶带、相界、大量位错塞积处形成微裂纹,因相邻微裂纹的聚合产生可见的微孔,微孔不断增殖、长大和聚合,沿晶界聚合发生沿晶断裂,在晶内聚合发生穿晶断裂。
(3)断口分析
断口包含很多与断裂有关的信息,通过断口分析可以找到裂纹源、了解裂纹扩展途径和发展过程,分析断裂原因、性质、机理及影响因素。
①宏观断口分析 宏观断口分析是用肉眼、放大镜及100倍以下的显微镜对断口进行观察,具有可全面观察断口形貌的优点。根据断口颜色、形貌特征和变形等信息,可以判断载荷类型、加载方式和断裂类型,可以确定裂纹源的位置和裂纹扩展方向,判断材料的冶金质量和热处理质量,分析材料的强度水平、构件的应力集中情况、工作温度和环境等。解理断裂的断口表面光滑平整、光亮有金属光泽;脆性沿晶断裂的断口为结晶状和反光的小刻面;韧性断裂的断口表面的纤维区粗糙不平、颜色灰暗而无金属光泽;应力腐蚀断裂的断口表面无金属光泽,其裂纹区及亚临界扩展区因介质作用呈黑色或灰黑色;氢脆断裂的断口比较平齐、较光亮、无腐蚀产物。
根据破断面的形貌,大致可以将宏观断口分为三类。第一类为杯锥状断口,破断面与拉伸轴呈90°,即断口垂直试样的轴线,有明显的剪切唇,表明材料抗剪切屈服强度较低,在外加切应力作用下发生塑性变形,表现出较好的塑韧性。第一类拉伸断口的典型形貌由纤维区、辐射区、剪切唇区组成,如图1-28所示,纤维区一般位于试样中部且呈粗糙状,其面积大小和粗糙度反映裂纹形成前材料变形的大小程度,变形越大,纤维区面积越大、越粗糙、越发灰;辐射区有放射状条纹,是中心裂纹达到临界尺寸后发生快速撕裂的痕迹;剪切唇区在最后形成,与拉应力方向呈45°。第二类断口的破断面也与拉伸轴呈90°,基本观察不到剪切唇,没有明显的塑性变形,中部的纤维区很小,断口的放射线汇集于启裂点,表现为脆性断口。第三类断口的破断面与拉伸轴呈45°,且可以观察到剪切唇,表明材料切断抗力较低,失效前先发生塑性变形,且在切应力作用下形成裂纹、断裂。

图1-28 圆柱形样品第一类拉伸断口照片和示意图
与圆柱形样品不同,片状样品在拉伸时处于平面应力状态,对于韧性材料,切断抗力比正断抗力弱很多,通常在最大剪应力作用下撕裂,而最大剪应力与轴线近似呈45°,断口面往往与拉伸轴呈45°,如图1-29所示,断口也分为三个区域,心部的纤维区变为椭圆形,辐射区变为人字形花样,花样的尖端指向裂纹源,最后的破断区仍为剪切唇区。

图1-29 片状样品宏观拉伸断口照片和示意图
当断口粗糙度较低(表面光亮)、辐射区面积较大,而纤维区与剪切唇区面积较少,表明材料强度较高而塑性、韧性较低。脆性断口放射条纹的收敛处、韧性断口纤维区的中央、疲劳断口弧形贝纹线的圆心位置通常为断裂裂纹源。受到轴向拉伸载荷的圆柱形工件,裂纹源如果不在中心区域,表明其材料本身有缺陷、存在附加应力或残余应力。放射条纹的发散方向、疲劳贝纹线弧形的法线方向等为裂纹扩展方向,当裂纹扩展到接近表面时,裂纹尖端由平面应变状态转为平面应力状态,呈现斜断面,最后形成剪切唇区。多数情况下,宏观断口存在放射线,如图1-30(a)、(b)所示,其汇集区便是裂纹源(或起裂点)区,放射线越细韧性越差,如果观察不到放射线,可能为沿晶断裂或解理断裂。图1-30(c)所示断口也存在放射条纹,但在断口找不到明显的汇集区,其左边较平坦区域是应力较小的裂纹开始扩展区域,凹凸不平区域是塑性变形较大的区域,裂纹失稳扩展区域、剪切唇区是最后断裂区域。

图1-30 宏观断口的裂纹源区和辐射线
②微观断口分析 采用扫描电镜、透射电镜和电子探针等分析手段可进行断口的微观分析,高倍观察断口形貌特征和分析微区成分,确定断裂性质、研究断裂机理和断裂原因。微观断口分析必须要有统计学概念,在大面积范围观察的基础上,选择有代表性的断口拍照。
韧性断裂的微观断口通常存在大量韧窝,主要有拉伸型等轴状、剪切型伸长状、拉伸撕裂型伸长状等形状,其形状取决于微区的应力状态和加载方式。当裂纹扩展方向垂直于最大主应力σmax且σmax均匀分布于断裂平面时,产生颈缩的拉伸试样的中心部分呈现拉伸型等轴状韧窝,边缘部分呈现剪切型伸长韧窝,韧窝很大,上下断面的韧窝方向相反。表面有缺口或裂纹的试样,会导致σmax沿截面非均匀分布,在边缘部分应力很大,裂纹由表面逐渐向内部延伸,且扩展快,其断口常呈现拉伸撕裂型伸长韧窝,韧窝小而浅,宏观表现为脆断,因此,不能把微孔聚合型断裂的微观机制都归为韧断。韧窝的大小和密度与第二相质点的大小及密度有关,韧窝深度则与基体的塑性变形能力相关。图1-31为T6(160℃/44h)态和T8(5%+160℃/28h)态的2297合金的拉伸断口的SEM照片,均为沿晶和穿晶混合型断口。图1-31(a)对应T6态,主要为沿晶断裂,少部分穿晶断裂,可以观察到光滑的晶界和少量较浅的小韧窝;图1-31(b)对应T8态,主要为穿晶断裂,韧窝数量相对较多,尺寸也较大和较深。

图1-31 2297铝合金不同时效状态试样的拉伸断口照片
解理裂纹沿着一簇相互平行但高度不同的晶面扩展,不同高度的解理面之间存在台阶,众多台阶汇合成河流状花样并形成扇面形向四周扩展,裂纹源在解理扇的扇柄处,河流上游许多较小的台阶汇合成较大的台阶,河流下游较大台阶又汇合成更大的台阶,根据河流花样的流向,可以判断解理裂纹在微观区域内的扩展方向。解理裂纹与孪晶相遇时可沿孪晶面形成局部裂纹,发展到一定程度后与解理面的裂纹相连通,形成似躺在解理面上的舌状裂面,舌状花样容易在低温高速加载条件下出现。
准解理断裂属于解理和微孔聚合的混合机制。与解理断裂相同,准解理断裂也是穿晶断裂,也有小解理面、台阶或撕裂棱及河流状花样,但是,准解理小刻面不是晶体学解理面,而且准解理裂纹也不是源于晶界,而是源于晶内硬质点,形成从晶内某点发源的放射状河流花样。准解理断裂的另一特征是断裂面显现有较大的塑性变形,断口存在几个地方的小裂纹分别扩展相遇发生塑性撕裂而形成的撕裂岭。图1-32为不同回火程度的高强度钢在不同温度冲击的断口SEM照片,图1-32(a)和图1-32(b)为充分回火试样在韧脆转变点上下温度冲击的断口照片,韧脆转变温度为-37℃;图1-32(c)和图1-32(d)为未充分回火试样在韧脆转变点上下温度冲击的断口照片,韧脆转变温度为-2℃。图1-32(a)对应试样的冲击温度为-20℃,呈现混合型断裂特征,以穿晶断裂为主,基体塑性变形能力强,韧窝深,第二相较少、分布不均匀,韧窝大小和分布不均。图1-32(b)对应试样的冲击温度为-40℃,稍低于韧脆转变点,断口形貌以解理花样为主,由许多与晶粒大小相当的解理刻面集合而成。图1-32(c)对应试样的冲击温度稍高于韧脆转变点,具有较少的韧窝和准解理特征,微观形态类似于解理河流花样,但裂纹不是严格沿着一定晶面扩展,其刻面不是晶体学解理面。图1-32(d)对应试样的冲击温度远低于韧脆转变点,断口呈现解理断裂特征。

图1-32 不同回火程度的高强度钢在不同温度冲击的断口照片(SEM)
此外,应力腐蚀、氢脆、腐蚀疲劳、热疲劳、微动磨损疲劳等断口均有其特有的微观形貌特征。借助图像自动分析仪和定量断口分析软件,可以定量研究导致断裂的因素及各因素之间的关系,诸如韧窝尺寸、深度、形状与第二相质点的数量、形态、分布之间的关系,疲劳条带间距与交变应力幅、应力强度因子之间的关系。
1.4.2.4 疲劳失效
疲劳断裂是航空航天结构件最常见的失效形式,约占断裂失效的80%~90%。直升机的旋翼、发动机的轴和叶片、齿轮、弹簧等在服役中要承受反复交变载荷,经受一定循环周次的交变载荷后,由于累积损伤,即使应力远低于静载下的强度极限也有可能发生突然断裂,称为疲劳失效。疲劳是一种潜在的突发性脆性断裂,不管是脆性材料还是韧性材料,断裂前均不会发生塑性变形或没有明显的形变预兆,因而具有很大的危害性。
疲劳可以分为两个阶段:第一阶段在整个寿命中所占的时间较短,一般为总寿命的10%,材料在交变载荷作用下形成裂纹;第二阶段,裂纹沿着与载荷垂直的方向扩展,又可分为微观扩展(a<0.05mm)和宏观扩展(a>0.05mm)两个阶段。疲劳裂纹扩展行为受材料内部及外界环境的影响,其中显微组织、加载频率、应力比、温度、环境因素等对裂纹扩展速率影响较大。
疲劳对组织缺陷、缺口和裂纹十分敏感,缺陷降低材料的强度,缺口和裂纹因应力集中加大材料的损伤,促进疲劳破坏开始和发展。疲劳裂纹往往萌生于材料表面和内部缺陷处,表面滑移带开裂、第二相及其界面或夹杂物及其界面开裂、晶界或亚晶界开裂等显微裂纹是主要的疲劳源,经过裂纹萌生、亚稳扩展、失稳扩展导致疲劳断裂。典型的疲劳断口由裂纹产生区(疲劳源区)、裂纹扩展区、瞬断区组成。疲劳源区光滑细腻,裂纹扩展区较光滑且分布有贝纹线花样,有时还有裂纹扩展台阶,近疲劳源区贝纹线较细密,表明裂纹扩展较慢,远疲劳源区贝纹线较稀疏粗糙,表明裂纹扩展较快。图1-33为疲劳断口的SEM照片,疲劳辉纹(条纹)是疲劳断口的主要特征,为一系列相互平行又略带弯曲的水波形条纹,垂直于局部裂纹扩展方向,裂纹扩展方向朝向波纹凸出一侧。

图1-33 疲劳断口的SEM照片
疲劳裂纹的形成及扩展与交变载荷的关系密切,如图1-34所示,交变载荷导致不均匀滑移而产生裂纹源,由于裂纹尖端应力集中,尽管施加的应力小于材料的屈服极限,每次循环均会产生局部的塑性变形,只不过裂纹在每次循环扩展的距离很小,与之对应的疲劳条纹很小,随着裂纹不断扩展,剩余的有效面积不断减少,剩余断面的局部应力不断增加,当应力达到一定极限后,裂纹快速扩展产生瞬时断裂。

图1-34 疲劳裂纹的形成及扩展与断裂示意图
通过疲劳断口裂纹扩展区的微观分析可以反推断裂条件和裂纹扩展速率,具有疲劳条纹特征断口对应较慢的裂纹扩展速率,而沿晶断裂断口对应较快的裂纹扩展速率。图1-35为2297合金稳态扩展区(ΔK=18MPa·m1/2)和瞬断区的SEM照片,稳态扩展区分布有大面积带明显疲劳辉纹的裂纹扩展平面,且疲劳辉纹较细密和规则,瞬断区形貌特征与拉伸断口形貌相似。

图1-35 2297合金的稳态扩展区(a)和瞬断区(b)的SEM照片
瞬断区断口比疲劳裂纹扩展区粗糙,脆性材料断口呈结晶状,韧性材料断口呈纤维状,在心部平面应变区呈放射状或人字纹状,边缘平面应力区则有剪切唇区存在。可以根据疲劳裂纹扩展区与瞬断区所占面积的相对比例估计所受应力高低及应力集中程度,所受应力小且无大的应力集中时,疲劳裂纹扩展区大,反之则小。
1.4.2.5 蠕变和松弛
(1)蠕变
蠕变是材料受温度和外力持续作用而发生的缓慢塑性流变,温度和应力的作用方式可以是恒定的,也可以是变动的,常规蠕变通常指静态蠕变,温度和压力恒定。蠕变通常包括滞弹性蠕变、低温(对数)蠕变、扩散蠕变、高温(或回复)蠕变4种类型。外加应力远低于弹性极限时发生滞弹性蠕变或微蠕变;在极低温度下,外加应力大于屈服强度时产生低温(对数)蠕变;在高温极低应力下,应力梯度引起原子定向扩散流动而产生扩散蠕变;在较高温度下发生高温蠕变或回复蠕变,不但产生加工硬化,还发生回复软化,工程材料的蠕变多属此类。
蠕变速度和蠕变量取决于材料性能、服役温度、应力。从极低温度到熔点Tm,材料都有可能产生蠕变,多数蠕变在(0.3~0.7)Tm温度区间发生,温度越高,蠕变越快,蠕变量越大。当温度高于(0.3~0.4)Tm时,金属材料产生明显的蠕变;当温度高于(0.4~0.5)Tm时,陶瓷材料会产生蠕变;聚合物发生蠕变的温度受玻璃化温度Tg影响,许多聚合物在室温就可观察到明显的蠕变。蠕变的应变速率很小(10-10~10-8s-1),应变量不仅与应力有关,还与应力作用的时间有关,当应力超过某一极限值时,随着时间延长,蠕变不断发展,最后导致材料破坏,称为蠕变断裂或静载延滞断裂。蠕变断裂不是因为载荷过大导致,而是因为温度和时间对塑性变形产生了影响,即使应力小于屈服强度,材料也会发生蠕变,在持续的温度和应力作用下,蠕变逐渐累积而导致断裂。
(2)应力松弛
材料或元件在固定载荷长期作用下会发生应力松弛现象,储存的弹性功逐渐转变为热散发出去,导致初始弹性应变逐步向非弹性应变转化,宏观表现为在恒应变条件下应力随时间延续逐渐降低。应力松弛是机械弹簧、精密仪器仪表中弹性元件的主要失效形式,高温环境工作的紧固件特别容易发生应力松弛,其初始紧固应力随着时间延长而不断下降。
应力松弛是在温度和总应变量不变的情况下,由于弹性变形不断转变为塑性变形,应力随时间增长而减小,可看作应力不断降低条件下的蠕变过程,归于广义蠕变。金属材料的应力松弛与位错的热激活有关,施加足以使位错移动的应力就会发生松弛,减少可动位错数目、增加钉扎位错的数目是抑制应力松弛的关键。与回复过程相似,松弛过程中位错重新排列,虽然平均位错密度未变,但可动位错数量减少,使组织结构更为稳定。密封管道的法兰橡胶垫,时间长了产生渗漏现象,是由聚合物大分子链在外力作用下产生位错和构象改变引起应力松弛所致。
1.4.2.6 腐蚀
腐蚀和老化是一种自然现象,是材料受外部因素或环境介质作用而破坏、变质的现象。外部因素主要有化学、生物、物理、机械等方面因素,化学因素包括各种酸、碱、盐及其水溶液、腐蚀性气体等,生物因素包括菌类、昆虫等产生的腐朽和虫蛀等,物理因素包括光、热、电、温度差、湿度差、干湿循环、冻融循环等,机械因素包括冲击、交变载荷、磨损等。工程材料往往同时受到两种以上的外部因素作用,金属材料常因化学和电化学作用而导致腐蚀,无机非金属材料常因化学作用、溶解、冻融、风蚀、温差、湿差、摩擦等因素而导致破坏,有机材料常因生物作用、溶解、化学腐蚀、光、热、电等作用而导致破坏。腐蚀会严重影响航空航天器结构的完整性、可靠性、适航性、安全性、耐久性,处于严酷海洋腐蚀环境的舰载机的寿命不及陆上的20%。
(1)金属腐蚀
金属材料在干燥气体或无电解质存在环境中发生化学反应而导致的腐蚀称为化学腐蚀,腐蚀过程中无电流产生,在氧气、二氧化硫、硫化氢、氯化氢等气体作用下,金属表面形成氧化物、硫化物、氯化物等腐蚀产物,表面致密的氧化膜能降低金属与介质的反应速率,一定程度抑制金属的进一步腐蚀。大多数金属腐蚀为电化学腐蚀,存在电位差的不同金属或金属的不同部位,处于相连通的电解质溶液或潮湿空气中,且不同电位金属间有导体相连时,通常形成原电池或微电池并产生电流,其中较活泼的金属电位较低,不断被溶解,其腐蚀速率比化学腐蚀快得多,量也大得多。
根据腐蚀环境,腐蚀可分为自然环境腐蚀和工业环境腐蚀,前者可细分为大气、土壤、海水、微生物腐蚀等,后者可分为熔融金属、酸、碱、盐介质腐蚀及航空、航天、化工、石油等工业环境腐蚀。在潮湿空气中,水蒸气在金属表面凝聚,金属在极薄的水膜下发生破坏,空气中的二氧化碳、二氧化硫、硫化氢、氯化氢等溶于水膜中形成电解液,加剧金属的腐蚀,水膜越薄,空气中的氧越容易通过,金属越易腐蚀。在干燥气体中的金属也可能产生腐蚀,空气中的二氧化硫会降低临界湿度,当空气相对湿度增加到一临界值时,金属腐蚀急剧加大,大气中的氧、海洋盐雾、尘埃、微粒、工业烟尘等均会加速腐蚀。
根据腐蚀形态,腐蚀可分为全面腐蚀、局部腐蚀、应力腐蚀。当被腐蚀的金属表面具有均匀的化学成分和显微组织,且腐蚀环境均匀而不受限制的包围金属表面时,腐蚀会在整个金属表面均匀发生,称为全面腐蚀或均匀腐蚀,如图1-36(a)所示,主要在大气、液体、土壤里发生。局部腐蚀缘于电化学因素不均匀而形成的局部腐蚀原电池,洁净表面的纯化膜局部受到破坏或局部地方的防蚀剂被破坏、金属材料成分或组织结构不均匀、应力或温度差异都会引起局部腐蚀。局部腐蚀主要有电偶腐蚀、点蚀、晶间腐蚀、剥落腐蚀等类型。异种金属彼此接触或通过其他导体连通并处于同一介质中,由于腐蚀电位不同,造成异种金属接触部位的局部腐蚀,称为电偶腐蚀。金属表面受破坏处和未受破坏处形成“局部电池”,受破坏处为阳极,未受破坏处为阴极,两极的面积差造成相应的电流密度差,具有很小面积的阳极电流密度很大,腐蚀电流从阳极流向周围的阴极,周围部分受到阴极保护,而阳极处很快形成腐蚀坑或小孔,称为点蚀,如图1-36(b)所示,小孔逐渐被腐蚀,呈尖锐小孔向纵深发展成孔穴甚至穿透形成孔蚀。晶界原子排列较为疏松而紊乱,易于富集杂质原子、发生晶界沉淀,导致晶界处化学成分不均匀,形成“局部电池”而产生晶间腐蚀,如图1-36(c)所示,晶间腐蚀发生在晶粒边界及其近旁。剥落腐蚀又称层状腐蚀,一般发生在晶界处,腐蚀产物从金属本体脱离,如图1-36(d)所示,从而产生一种层状外观。多数构件处于应力和环境介质的联合作用下,会发生应力腐蚀、腐蚀疲劳、冲击腐蚀(或湍流腐蚀)、微动(振)腐蚀等,如图1-36(e)~图1-36(h)所示,这些腐蚀导致的破坏均集中在材料局部,通常归于广义局部腐蚀范畴。

图1-36 材料的主要腐蚀破坏形态特征示意图
几乎所有类型的腐蚀损伤在航空航天器上都有发现,最常碰到和危害性最大是电偶腐蚀、缝隙腐蚀、点蚀、晶间腐蚀、剥落腐蚀、应力腐蚀等局部腐蚀,腐蚀的金属量少且相对集中而不易察觉,发生的部位和时间具有随机性而难以预测和防止,对结构危害比全面腐蚀严重得多。
航空航天器由许多部件和构件组装而成,在两种金属或金属与非金属导体相互接触的边缘附近发生电偶腐蚀的可能性很大,图1-37为铝合金与不锈钢连接后的电偶腐蚀,亦称接触腐蚀或双金属腐蚀。在飞行器结构中,小阳极和大阴极的电偶腐蚀是非常危险的,用铝合金铆钉铆接钛合金板就属于此类,如图1-38所示,铝合金铆钉迅速破坏,如果用钛合金铆钉铆接铝合金板,组成大阳极小阴极,铝合金板受到的破坏和危险性较前者小,但是,由于钛合金与铝合金在电偶序中相距较远,飞机结构件要尽量避免这种情况出现,新型飞机结构中采用真空等离子镀铝的钛合金紧固件,力求接触部分电位一致。由于金属存在杂质或其他成分,会引起金属表面电化学不均匀性而导致腐蚀微电池形成,即使未与其他金属相接触也会产生电偶腐蚀,美军F16战斗机曾因发动机油路控制阀门的电子连接器电偶腐蚀造成一个编队7架飞机失效。

图1-37 铝合金与不锈钢连接后的电偶腐蚀

图1-38 铝合金与钛合金接触后的电偶腐蚀
构件间存在很多窄小缝隙,电解质溶液进入并滞留其中,导致构件产生缝隙腐蚀,铝合金特别容易遭受缝隙腐蚀,几乎所有含水介质都会使其发生缝隙腐蚀。点蚀是造成航空航天飞行器腐蚀损伤比例最高的腐蚀类型,对飞行器的安全可靠性威胁最大,腐蚀小孔还经常成为应力腐蚀开裂、腐蚀疲劳和机械疲劳的裂纹源区,使结构提前破坏。剥落腐蚀是铝合金形变材料的一种特殊的晶间腐蚀形式,也是飞机构件腐蚀的主要形式之一,将导致材料强度、塑性以及疲劳性能大幅度下降,从而降低材料的使用寿命。
图1-39为2A97合金在NaCl(4mol/L)+KNO3(0.5mol/L)+HNO3(0.1mol/L)溶液中浸泡不同时间后的点蚀和剥落腐蚀形貌。浸泡7h后,如图1-39(a)所示,有很多细小点蚀坑;浸泡27h后,如图1-39(b)所示,点蚀坑扩大;浸泡96h后,发生了严重的剥落腐蚀,图1-39(c)和图1-39(d)分别为剥落腐蚀表面形貌和横截面形貌。在表面个别点或微小区域内通常出现点蚀向纵深方向发展,产生孔蚀,由于蚀孔很小且孔口常被腐蚀产物覆盖,很难查出,航空航天飞行器的压力容器和管道系统一旦腐蚀穿孔,轻则引起“跑、冒、滴、漏”问题,重则造成失火或爆炸事故。

图1-39 2A97合金的点蚀和剥落腐蚀形貌
晶间腐蚀通常从材料表面开始,沿着晶界向内部发展,是危害性较大的局部腐蚀。图1-40(a) 为2297铝合金的晶间腐蚀形貌,图(b)为未经稳定化处理的304不锈钢的晶间腐蚀形貌,出现了晶粒脱落现象。晶间腐蚀导致晶粒间结合力显著降低,严重时可使力学强度完全丧失,只要轻轻敲打就可破碎,而外观并未发生明显变化,不易发现,常常导致飞机结构和设备突发性的腐蚀破坏。

图1-40 2297铝合金和304不锈钢晶间腐蚀形貌
在应力和腐蚀介质共同作用下,表面的氧化膜容易被腐蚀,破坏的表面和未破坏的表面分别形成阳极、阴极,阳极处的金属成为离子而被溶解,产生电流流向阴极,由于阳极面积比阴极面积小得多,阳极电流密度很大,进一步腐蚀已破坏表面,拉应力促使破坏处形成裂纹、逐渐扩展直到断裂。应力腐蚀分为阳极溶解和氢致开裂,裂纹可以沿着金属晶粒边界发展,还能穿过晶粒发展,往往导致构件在工作应力远小于许用应力、外表并无任何预兆的情况下突然断裂。图1-41为几种航空用材的应力腐蚀(SCC)微观断口形貌。超高强度钢在含Cl-的水溶液中乃至纯水中都能表现出很高的SCC敏感性,其SCC过程以氢脆机制为主,如图1-41(a)所示,断口为冰糖块状沿晶脆性断口。铝合金容易在氯化钠水溶液、海水、水蒸气、含SO2大气、熔融氯化钠、含Br-和I-的水溶液中产生应力腐蚀,拉伸应力分量可能是外加载荷引起的工作应力,或者是加工和装配过程中产生的残余应力,或是温差产生的热应力、相变产生的组织应力,如图1-41(b)所示,断口通常呈现河流状花样或扇形准解理形貌特征。Ti3Al+Nb金属间化合物的SCC断口则出现沿相间开裂的阳极溶解型SCC形态特征,如图1-41(c)所示,既不同于沿晶型开裂,也不同于穿晶型开裂。

图1-41 几种航空用材的应力腐蚀微观断口形貌
图1-42为应力腐蚀开裂的主要影响因素,包括冶金因素、应力因素、环境因素。提高冶金质量和通过加工及热处理改善组织,通过优化结构设计减少局部应力集中、尽量避免缝隙和可能造成腐蚀液残留的死角,这些措施均可降低材料及其结构件的应力腐蚀敏感性。

图1-42 应力腐蚀开裂的主要影响因素
在一定温度范围内,金属及合金在与某些低熔点金属接触且同时承受张应力时,其断裂强度和塑性指标显著降低,这种现象称为低熔点金属致脆(MIE),也是航空航天工程结构的重要破坏隐患。当低熔点金属处于液相时,称为液态金属致脆(LMIE),归于液态金属腐蚀范畴,当低熔点金属处于固相时,称为固态金属致脆(SMIE)。
对于腐蚀的鉴定可以采用目测、专用工具或无损探伤技术。目测可以识别全面腐蚀、点蚀、缝隙腐蚀,用专用检测工具可以识别冲击腐蚀、空泡腐蚀、晶间腐蚀,显微检测可以识别剥落腐蚀、应力腐蚀开裂、腐蚀疲劳。在无损探伤技术中,辐射照相法适于点状腐蚀、腐蚀疲劳的鉴定,超声法适于鉴别晶间腐蚀、应力腐蚀裂纹、氢脆裂纹,涡流电流法适于鉴别点状腐蚀、晶间腐蚀、腐蚀疲劳、应力腐蚀裂纹、氢脆裂纹,磁性微粒和染料渗透法可用于腐蚀疲劳、应力腐蚀裂纹、氢脆裂纹的检测。
采用改善金属表面的化学成分、在金属表面覆盖镀层、阳极保护法等措施可减少或避免腐蚀。此外,还可通过改善工作环境来降低腐蚀,如将周围气体干燥或将工件密封。
(2)非金属的腐蚀
非金属材料也存在由各种环境介质导致的腐蚀失效问题,其腐蚀机理与金属有所不同,通常以化学、物理、生物作用导致材料性能退化为主,聚苯烯等塑料也有应力腐蚀,石墨等非金属材料与金属材料接触会产生电偶腐蚀。
①高聚物的腐蚀 在物理、化学、生物因素作用下,聚合物也会发生腐蚀,其实质是高分子的降解、交联及物理过程引起的次价键破坏等,导致性能逐渐退化,俗称老化。如果老化使分子量下降,会导致聚合物变黏、变软,力学性能大为劣化;如果老化使分子链发生交联,会导致聚合物变硬、变脆、开裂、丧失弹性,其他性能也随之劣化。
高聚物的腐蚀受材料自身因素(配方、化学结构、聚集态结构)和环境因素的影响,环境因素包括物理因素(光、紫外线或其他辐射等)、化学因素(空气中的氧、臭氧、水、酸、碱、盐、有机溶剂等)、生物因素(微生物、海洋生物)及加工成型时的热和机械力。根据其与环境介质的反应过程及反应机理,聚合物的腐蚀可分为溶解腐蚀、化学侵蚀、降解、应力腐蚀(环境应力开裂)、生物腐蚀、辐照腐蚀、热氧化分解、光氧化分解、溶胀溶解等。
图1-43为高聚物在大气及水介质环境中的主要腐蚀破坏形式,主要有物理腐蚀、化学腐蚀、应力腐蚀,导致物理性能、力学性能、介电性能下降。介质向高聚物内部扩散渗透,一方面引起高聚物的溶剂化过程,产生溶胀等物理腐蚀;另一方面,介质与高聚物发生氧化、水解等化学反应,破坏化学键,发生分解等化学腐蚀;存在应力、温度突变时,会产生应力腐蚀。此外,增塑剂、稳定剂等组分会由高聚物内部向外扩散迁移进入介质中,发生材料组分的溶出,有时还生成溶胀性物质,使表面形态和色泽改变。

图1-43 高聚物的主要腐蚀破坏形式
在应力和某些介质(如表面活性介质)共同作用下,不少高聚物会出现银纹(发亮的条纹),由高聚物细丝及贯穿其中的空洞组成,如图1-44所示,大分子链沿应力方向取向,介质向空洞渗透和应力的作用,使银纹进一步发展成裂纹,裂纹不断发展而导致脆性断裂。

图1-44 银纹和裂缝示意图
塑料的耐腐蚀性能优良,但也存在化学侵蚀、溶解、渗透、老化等破坏过程。化学侵蚀导致聚合物分子键的不可逆断开,溶解使塑料性质发生变化,但不会改变聚合物链状结构的化学组成,渗透是因为吸收液体、气体、蒸汽使材料溶胀而导致性能变化。
②无机非金属材料的腐蚀 玻璃和陶瓷在使用过程中会遭受液体介质、气体介质等周围介质的腐蚀破坏,主要有水解、酸侵蚀、碱侵蚀、风化、选择性腐蚀、应力腐蚀。对于陶瓷材料中的晶体相,可能受到的腐蚀性液体环境有熔融玻璃、熔融盐、熔融金属和水介质,而玻璃体或陶瓷中的玻璃相则受水介质腐蚀的情况更为普遍。在空气中,某些无机非金属材料会因为物理和化学作用而发生风化变质,在冻融循环和干湿循环作用下,多孔材料会发生体积变化,导致性能下降。在常压下,气体和液体都可通过扩散渗透浸入硅酸盐玻璃,通过化学反应破坏硅氧骨架,而玻璃组分中的某些阳离子也通过迁移扩散与外界进行交换,导致玻璃的化学腐蚀。当材料的孔隙率(特别是开口孔隙率)较大时,其耐久性往往较差;当材料的组成易与水、其他液体或其他物质发生化学反应时,其耐水性、耐化学腐蚀性较差。
(3)复合材料的腐蚀
复合材料的腐蚀主要表现在环境介质腐蚀、生物腐蚀、雨蚀及复合材料对其他飞机结构材料的电偶腐蚀,其中环境介质的腐蚀包括基体的腐蚀、增强体的腐蚀、界面的腐蚀、应力腐蚀及腐蚀疲劳。
①金属基复合材料的腐蚀 金属基复合材料保持了金属基体的高强度、良好的塑性和韧性、高耐热性、良好的导热和导电性能等。但是,由于存在合金元素在增强体/基体界面处偏析、围绕增强体产生残余应力、在增强体周围基体中位错密度升高、增强体/基体界面处产生空洞、基体与增强体发生反应而导致活性界面层、界面层电偶效应等因素,耐蚀性通常比金属基体差。以铝基复合材料为例,不同类型增强体会使铝基体的腐蚀速率大不相同,如碳纤维在电解质中的电位较高,碳纤维/铝复合材料有明显的电偶腐蚀倾向,耐蚀性比铝基体差很多,而碳化硅/铝复合材料的耐蚀性则与铝基体相差不大。
②非金属基复合材料的腐蚀 聚合物基复合材料在介质作用下的腐蚀主要通过浸蚀基体、增强纤维及其界面等途径表现出来,强碱和硝酸、浓硫酸等强氧化性腐蚀介质对大多数树脂基体都有较严重的腐蚀作用。介质经扩散、渗透、吸附或吸收进入基体内部而导致物理腐蚀,引起聚合物的溶胀与溶解、溶出,介质与基体发生化学反应而导致化学腐蚀,水解及氧化等反应引起断键、降解或生成新的化合物等,从而改变树脂基体的性质。介质与增强体作用会使其与基体界面的黏结劣化,温度越高,基体链段的松弛运动越快,介质中的水分子扩散速率越大,时间越长,基体吸水及渗入界面的水越多,从而使得界面结合力下降越多。应力腐蚀和生物腐蚀也会对聚合物基复合材料的服役性能产生较大影响,拉应力会加速介质和基体中有关组分的相互扩散与渗透,导致基体溶胀、裂纹产生及扩展,引起纤维/树脂脱粘等。
陶瓷基复合材料在耐高温、耐腐蚀、抗氧化方面比金属基复合材料和聚合物基复合材料好得多,导致材料失效往往是高温下的氧化问题。陶瓷基复合材料的腐蚀除受环境影响外,主要受基体、增强体、界面区的结构及成分的影响,基体材料必须与增强材料相容,尤其是基体和增强体的热膨胀系数应基本匹配,避免在界面处产生过高的残余应力和裂纹。
1.4.3 航空航天材料的选择及应用
飞行器长期在大气层或外层空间运行,在极端环境服役还要有极高可靠性和安全性、优良的飞行性和机动性,除了优化结构满足气动需求、工艺性要求和使用维护要求外,更有赖于材料的优异特性和功能。
1.4.3.1 选材原则
结构件在服役中要承受各种形式的外力作用,要求材料在规定期限内不超过允许的变形量和不破断,而航空航天结构还要尽量缩小结构尺寸、降低重量,早期航空航天构件采用静强度设计,不考虑或很少考虑塑韧性,导致出现了灾难性事故。
为了保证结构安全并充分利用材料的性能,航空航天结构件的设计由“强度设计原则”转变为“损伤容限设计原则”,并逐步过渡到“全寿命周期设计原则”,在设计阶段就考虑到产品寿命历程的所有环节,所有相关因素在产品设计阶段就得到综合规划和优化。要求材料不仅具有高的比强度、比刚度,还要有一定的断裂韧性和冲击韧性、抗疲劳性能、耐高温性能、耐低温性能、耐腐蚀性能、耐老化性能和抗霉菌性能,并有针对性地强化一些性能指标。此外,不同等级的载荷区采用不同的选材判据,根据部件的具体要求选择与之匹配的材料,大载荷区采用强度判据,选用高强材料;中载荷区采用刚度判据,选用高弹性模量材料;轻载荷区主要考虑尺寸稳定性,确保构件尺寸大于最小临界尺寸。
选择和评价结构材料时,要根据服役条件和应力状态,选择合适的力学性能(拉伸、压缩、冲击、疲劳、低温系列冲击)测试方法,针对不同的断裂方式(韧断、脆断、应力疲劳、应变疲劳、应力腐蚀、氢脆、中子辐照脆化等),综合考虑材料强度与塑性、韧性的合理配合。承受拉伸载荷的构件,表层及心部应力分布均匀,所选材料应具有均一组织和性能,大型构件应有良好的淬透性。承受弯曲及扭转载荷的构件,表层及心部应力相差较大,可用淬透性较低的材料。承受交变载荷的构件,疲劳极限、缺口敏感性为选材的重要考核指标。在腐蚀介质中服役的构件,抗腐蚀能力、氢脆敏感性、应力腐蚀开裂倾向、腐蚀疲劳强度等为选材的重要考核指标。高温服役材料还要考虑组织稳定性,低温服役材料还要考虑低温性能。
减重对提高飞行器的安全性、增加有效载荷和续航距离、提高机动性能及射程、降低燃料或推进剂消耗和飞行成本具有实际意义,飞行器速度越快,减重意义越大。战斗机重量减轻15%,则可缩短飞机滑跑距离15%,增加航程20%,提高有效载荷30%。对于导弹或运载火箭等短时间一次性使用的飞行器,要以最小体积和质量发挥等效功能,力求把材料性能发挥到极限程度,选取尽可能小的安全余量而达到绝对可靠的安全寿命。
1.4.3.2 主要航空航天材料
对于减轻结构质量,密度降低30%,比强度提高50%的作用还大。铝合金、钛合金、复合材料是主要的航空航天结构材料,具有较高的比强度和比刚度,可提高飞行器的有效载荷、机动性、续航距离,同时降低飞行成本。
超高强度钢(屈服强度>1380MPa)在航空航天工程中的用量不会超过10%。对于超声速歼击机等现代飞行器,超高强度钢用量稳定在5%~10%,其抗拉强度在600~1850MPa,有时高达到1950MPa,断裂韧性KIc=78~91MPa·m1/2。在活性腐蚀介质中使用的机身承力结构件,一般要采用高强度耐蚀钢,装备氢燃料发动机的飞机要选用无碳耐蚀钢作为在液氢和氢气介质中服役的构件材料。
21世纪的飞行器机身结构材料还是以铝合金为主,包括2×××系、7××××及铝锂合金。在铝合金中加入锂,可在提高强度的同时降低密度,实现提高构件的比强度和比刚度的目标。铝锂合金已用于大型运输机、战斗机、战略导弹、航天飞机、运载火箭,主要用于头部壳体、承力构件、液氢液氧储箱、管道、有效载荷转接器等,被誉为极具发展前景的航空航天材料。第三代和正在发展的第四代铝锂合金不再片面追求低密度,有较好的综合性能,在裂纹扩展速率、疲劳性能、腐蚀性能、弹性模量等与第三代铝锂合金相当的条件下,第四代铝锂合金有更高的静强度(尤其屈服强度)和更高的断裂韧性。
钛合金的比强度高于铝合金,已应用于飞机框架、襟翼导轨和支架、发动机底座和起落架构件等,还可用于排气罩和隔火板等受热部分。Ma>2.5的超声速飞机表面温度可达到200~350℃,可采用钛合金作蒙皮。采用快速凝固/粉末冶金方法制备的高纯度高致密度的钛合金,有较好的热稳定性,在700℃的强度与室温相同,开发的高强度高韧性的β型钛合金已被NASA定为SiC/Ti复合材料的基体材料,用来制造飞机的机身和机翼壁板。钛合金在航空器中的应用比例逐渐增加,在民航机身中的使用量将达20%,在军机机身中的使用量将高达50%。
金属基复合材料、高温树脂基复合材料、陶瓷基复合材料、碳/碳复合材料已在航空航天领域扮演越来越重要的角色。碳/碳复合材料综合了碳的难熔性与碳纤维的高强度、高刚性,具有优越的热稳定性和极好的热传导性,在2500℃的高温下仍具有相当高的强度和韧性,且密度只有高温合金的1/4。混合型复合材料得到了越来越多的关注,如在碳纤维复合材料中添加玻璃纤维可以改善其冲击性能,而玻璃纤维增强塑料中加入碳纤维可以增加其刚度。
此外,层状复合材料在航空航天工程中的应用越来越广泛,如A380采用了3%的GLARE,为新型的层压板。层压板是通过压力使两种不同种类的材料层叠在一起的复合材料,通常由上面板、上胶合层、芯材、下胶合层、下面板构成,其强度和刚度要高于单独的面板材料或芯材,已应用于运输机和战斗机。GLARE层压板是通过压力(或热压罐)把多层薄铝板和单向性玻璃纤维预浸料(浸渍环氧黏合剂)叠接热压而成的,如图1-45所示。铝板要经过适当的预处理,使其更容易与纤维预浸料层粘在一起。表1-4为可商业化生产的GLARE层压板类型,可根据需要制成不同厚度的板,纤维可以是2层、3层、4层等,纤维含量和方向符合表中规定即可,每类GLARE层压板可以有不同形式,可根据具体需要进行调整。

图1-45 GLARE层压板示意图
表1-4 可商业化生产的GLARE层压板类型

GLARE层压板的拼接技术解决了铝板宽度有限的问题,如图1-46所示,拼接时,同层铝板间有一条窄缝,不同层铝板间的接缝在不同位置,这些接缝可以通过纤维层和其他层铝板连接起来,使得大型机身壁板或整体蒙皮制造成为可能,并具有出色的抗疲劳、抗腐蚀和阻燃性能,从而消除了铆钉孔及由此引发的应力集中。为了确保载荷的安全传递,可在拼接处增加一个补强层,即增铺一层金属板或一层玻璃纤维预浸料。

图1-46 GLARE层压板的拼接示意图
蜂窝夹层复合材料由夹层和蒙皮(面板)复合而成,蒙皮可以是铝、碳/环氧复合材料等,夹层形似蜂窝,是由金属材料、玻璃纤维或复合材料制成的一系列六边形、四边形及其他形状的孔格,在夹层的上下两面再胶接(或钎焊)上较薄的面板。铝蜂窝夹芯复合材料的芯材由铝箔以不同方式胶接,通过拉伸而制成不同规格的蜂窝,芯材的性能主要通过铝箔的厚度和孔格大小来控制,具有比强度和比刚度高、抗冲击性能好、减振、透微波、可设计性强等优点,与铆接结构相比,结构效率可提高15%~30%。蜂窝夹层结构材料可用来制作各种壁板,用于翼面、舱面、舱盖、地板、发动机护罩、消声板、隔热板、卫星星体外壳、抛物面天线、火箭推进剂储箱箱底等。但是,蜂窝夹层结构复合材料在某些环境中易腐蚀,受冲击时,蜂窝夹层会发生永久变形,使蜂窝夹层与蒙皮发生分离。
1.4.3.3 飞行器用材分析
表1-5为美国军机用结构材料的百分比,总的变化趋势是复合材料和钛合金的用量逐渐增多,铝合金的用量有所下降。
表1-5 美国军机用结构材料的百分比 %

表1-6为典型干线飞机用材比例,B787的复合材料占50%,A350的复合材料占52%,大量应用复合材料将成为航空航天领域的发展趋势。复合材料减重效果好,耐损伤、抗腐蚀、耐久性好,适合机敏结构,但是,复合材料成本很高,抗冲击性能差,无塑性,技术难度增加,可维修性差、再生利用性差。因此,A320neo和B737MAX的复合材料用量并未比A320和B737增加。
表1-6 典型干线飞机用材比例 %

人造地球卫星与空间探测器的结构材料大多采用铝合金,要求高强度的零部件则采用钛合金和不锈钢,要求高比刚度的结构主要采用高模量石墨纤维增强的复合材料,卫星体和仪器设备表面常覆有温控涂层,利用热辐射或热吸收特性来调节温度。卫星体内还使用多层材料、工程塑料、玻璃纤维树脂基复合材料等作为隔热材料,用二硫化钼固体润滑剂等作为运动部件的润滑材料,用硅橡胶等作为舱室的密封材料。大面积太阳翼可采用以石墨纤维复合材料作面板的铝蜂窝夹芯结构,更先进的轻型太阳翼则以石墨纤维复合材料作框架,蒙上聚酰胺薄膜,面积更大的柔性太阳翼全部由薄膜材料制成。大型抛物面天线是现代卫星的重要组成部分,指向精度要求高的天线,要采用热膨胀系数极小的轻质材料,石墨和芳纶在一定的温度范围内具有负膨胀系数,可通过材料的铺层设计制造出膨胀系数接近于零的复合材料。超大型天线需制成可展开的伞状,其骨架由铝合金或复合材料制成,反射面为涂有特殊涂层的聚酯纤维网或镍-铬金属丝网。
载人飞船各舱段的结构材料大多是铝合金、钛合金、复合材料,如航天飞机的轨道器大部分用铝合金制造,支承主发动机的推力结构用钛合金制造,中机身的部分主框采用以硼纤维增强铝合金的金属基复合材料,货舱舱门采用特制纸蜂窝夹层结构,以石墨纤维增强环氧树脂复合材料作面板。导弹头部、航天器再入舱外表面和火箭发动机内表面,要采用烧蚀材料,在热流作用下,烧蚀材料能发生分解、熔化、蒸发、升华、侵蚀等物理和化学变化,材料表面的质量消耗带走大量的热,以达到阻止再入大气层时的热流传入飞行器内部、冷却火箭发动机燃烧室和喷管的目的。为了保持舱内有适宜的工作温度,再入舱段要采取辐射防热措施,外蒙皮为耐高温的镍基合金或铍板,内部结构为耐热钛合金,外蒙皮与内部结构之间填以石英纤维、玻璃纤维复合陶瓷等有良好隔热特性的材料。
随着载人航天、探月及深空探测、高分辨率卫星、高超速飞行器、重复使用运载器、空间机动飞行器等航天工程的实施和不断发展,对材料提出了全新的、更加苛刻的要求,为航天新材料的发展提供了新的契机和动力,材料领域必须尽早在材料体系创新、关键原材料自主保障以及工程应用等方面取得重大突破。