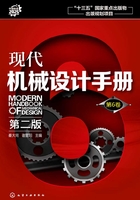
第7章 轴系的临界转速
7.1 概述
轴系由轴、联轴器、安装在轴上的传动件、转动件、紧固件等各种零件以及轴的支承组成。激起轴系共振的转速称为临界转速。当转子的转速接近临界转速时,轴系将引起剧烈的振动,严重时造成轴、轴承及轴上零件破坏,而当转速在临界转速的一定范围之外时,运转趋于平稳。若不考虑陀螺效应和工作环境等因素,轴系的临界转速在数值上等于轴系不转动而仅作横向弯曲振动的固有频率:
(27-7-1)
式中 nc——临界转速,r/min;
fn——固有频率,Hz;
ωn——固有角频率,rad/s。
由于转子是弹性体,理论上应有无穷多阶固有频率和相应的临界转速,按数值从小到大排列为nc1、nc2、…、nck、…,分别称为一阶、二阶、…、k阶临界转速。在工程中有实际意义的只是前几阶,特别是一阶临界转速。
为了保证机器安全运行和正常工作,在机械设计时,应使各转子的工作转速n离开其各阶临界转速一定的范围。一般的要求是,对工作转速n低于其一阶临界转速的轴系,n<0.75nc1;对工作转速高于其一阶临界转速的轴系,1.4nck<n<0.7nck+1。
临界转速的大小与轴的材料、几何形状、尺寸、结构形式、支承情况、工作环境以及安装在轴上的零件等因素有关。要同时考虑全部影响因素,准确计算临界转速是很困难的,也是不必要的。实际上,常按不同设计要求,只考虑主要影响因素,建立简化计算模型,求得临界转速的近似值。
7.2 简单转子的临界速度
7.2.1 力学模型
表27-7-1 力学模型


7.2.2 两支承轴的临界转速
转轴k阶临界转速:
(27-7-2)
式中 m0——轴质量,kg;
L——轴长,m;
E——材料弹性模量,Pa;
J——轴的截面惯性矩,m4;
λk——计算k阶临界转速的支承形式系数,见表27-7-2。
表27-7-2 等直径轴支承形式系数λk

注:1. μ1、μ2为外伸端轴长与轴总长L的比例系数,μ1和μ2之中有一值为零,即为一端外伸。
2.表中只给出μ2=0左端外伸时一阶支承形式系数λ1,见标记*值,当μ1=0右端外伸只是把表中μ1当成μ2,仍查标记*值。
7.2.3 两支承单盘转子的临界转速
表27-7-3 两支承单盘转子的临界转速

注:m1——圆盘质量,kg;m0——轴的质量,kg;E——轴材料弹性模量,Pa;J——轴的截面惯性矩,m4;λ1——支座形式系数,见表27-7-2;β——集中质量m1转换为分布质量的折算系数;μ——轴段长与轴全长L之比的比例系数。
7.3 两支承多盘转子临界转速的近似计算
7.3.1 带多个圆盘轴的一阶临界转速
带多个圆盘并需计及轴的自重时,按如下公式可以计算一阶的临界转速nc1:
(27-7-3)
式中 n0——只有轴自重时轴的一阶临界转速;
n01,n02,…,n0n——分别表示只装一个圆盘(盘1,2,…,n)且不考虑轴自重时的一阶临界转速。
应用表27-7-2及表27-7-3可以分别计算n0及n01,n02,…,n0n值,代入即可求得nc1。
对阶梯轴及复杂转子的轴则用下面的方法计算。
7.3.2 力学模型
将实际转子按轴径和载荷(轴段和轴段上安装零件的重力)的不同,简化成为如图27-7-1所示m段受均布载荷作用的阶梯轴。各段的均布载荷(N/m),mi为i段轴和装在该段轴上零件的质量,kg;li为该轴段长度,m;g为重力加速度,g=9.8m/s2。支承为刚性支承,各种形式支承的位置按表27-7-1中支承图选取。

图27-7-1 轴系的计算模型
7.3.3 临界转速计算公式
对于钢轴E=2.1×1011N/m2,则
(27-7-4)
式中 k——临界转速阶次,通常只计算一、二阶临界转速,用于计算高于三阶临界转速时误差较大;
L——转子两支承跨距,m;
qi——第i段轴的均布载荷,qi=mig/li,N/m;
Ji——第i段轴截面惯性矩,,m4;
Jmax/Ji——最大截面惯性矩与第i段轴截面惯性矩之比;
di——第i段轴的直径,m;
Δi——第i段轴的位置函数,,λi=kxi/L,
,也可由表27-7-4查出。
7.3.4 计算示例
某转子系统简化成为如图27-7-1所示的11段阶梯轴均布载荷计算模型,已知条件、计算过程和按式(27-7-3)计算的nc1和nc2列于表27-7-5。
表27-7-4 函数ϕ(λ)数值表


注:当λ>1时,ϕ 的整数部分与λ的整数部分相等,小数部分由表中查得。
表27-7-5 临界转速近似计算表


7.4 阶梯轴的临界转速计算
可将阶梯轴简化为多质量集中参数的计算模型,使用本章介绍的传递矩阵法,做较准确的计算。
如果只需作近似的估算,则可用式(27-7-2)。但计算轴的截面惯性矩需用当量直径Dm,阶梯轴的当量直径Dm可按式(27-7-5)作粗略计算。
(27-7-5)
式中 di——阶梯轴各阶的直径,m;
Δli——对应于di段的轴段长度,m;
α——经验修正系数。
若阶梯轴最粗一段(或几段)的轴长度超过全长的50%时,可取α=1,小于15%时,此段当作轴环,另按次粗段来考虑。在一般情况下,最好按照同系列机器的计算对象,选取有准确解的轴试算几例,从中找出α值。例如,一般的压缩机、离心机、鼓风机可取α=1.094。
7.5 轴系的模型与参数
7.5.1 力学模型
表27-7-6 力学模型

7.5.2 滚动轴承支承刚度
表27-7-7 滚动轴承支承刚度


图27-7-2 弹性位移系数

图27-7-3 接触变形系数曲线
表27-7-8 滚动轴承径向弹性位移

注:F——轴承的径向负荷,N;i——滚动体列数;z——每列滚动体数;dδ——滚动体直径,mm;d——轴承孔径,mm;α——轴承的接触角,(°);lα——滚动体有效长度,mm,lα=l-2r;l——滚子长度,mm;r——滚子倒圆角半径,mm。
[例] 某机器的支承中装有一个双列圆柱滚子轴承3182120(d=100mm,D=150mm,b=37mm,i=2,z=30,dδ=11mm,l=11mm,r=0.8mm)。轴承的预紧量为5μm(即g=-5μm),外圆与箱体孔的配合过盈量为5μm(即Δ=5μm),F=4900N。求支承的刚度。
解 (1)求间隙为零时轴承的径向弹性位移δ0
根据表27-7-8
(2)求轴承有5μm预紧量时的径向弹性位移δ1
计算相对间隙:g/δ0=-5/2.89=-1.73
从图27-7-2查得:β=0.47,于是得
(3)求轴承外圈与箱体孔的接触变形δ2
计算Δ/D:Δ/D=5/15=0.333,从图27-7-3(b)查得H2=0.2,于是
(4)求轴承内圈与轴颈的接触变形δ3
(5)求支承刚度
将δ1、δ2、δ3代入刚度公式得
7.5.3 滑动轴承支承刚度
滑动轴承力学模型如图27-7-4所示。沿各方向的刚度:
(27-7-6)
式中 W——轴颈上受的稳定静载荷,N;
c——轴承半径间隙,m;
——量纲一刚度系数,可根据轴瓦形式、S、L/D和δ值由表27-7-9查得。

图27-7-4 滑动轴承力学模型
表27-7-9 几种常用轴瓦的参数值




S值的确定方法,一般是先预估轴瓦中油的温度,并确定润滑油的动力黏度η,再算出Sommerfeld数,即S值:
式中 η——润滑油动力黏度,N·s/m2;
D——轴颈直径,m;
R——轴颈半径,m;
N——轴颈转速,r/s;
L——轴颈长,m。
查表用到的量值:
L/D——轴颈的长径比;
δ——量纲一预载,δ=d/c;
d——轴瓦各段曲面圆心至轴瓦中心距离,不同形式轴瓦的预载详见表27-7-9的表头图。
根据轴瓦形式、L/D、δ和预估油温条件下的S值,可由表27-7-9查出该轴瓦的量纲一值、
、
。若假定80%的摩擦热为润滑油吸收,利用热平衡关系就能得到轴承工作温度:
(27-7-7)
式中 ——量纲一边流,
,查表27-7-9;
——量纲一摩擦功耗,
,查表27-7-9;
——轴瓦量纲一温升,
,查表27-7-9;
cV——单位体积润滑油的比热容,J/(m3·℃);
ω——轴颈的转动角速度,rad/s;
P——每秒消耗的摩擦功,N·m/s。
油膜中的最高温度
(27-7-8)
所以,可用Tmax作为确定润滑油黏度的温度。如果Tmax与最初估计的温度值不同,就需要重新估计温度再按上述过程计算,直到两温度值基本一致为止,最后确定了正确的S值,按该S值从表27-7-9查得量纲一刚度系数、
、
、
,这些值虽有差别,但差别不大,所以,在计算轴系临界转速时,只考虑
。
7.5.4 支承阻尼
各类支承的阻尼值,一般通过试验求得,目前尚无准确的计算公式,表27-7-10列出了各类轴承阻尼比的概略值。
表27-7-10 各类轴承阻尼比的概略值

注:滑动轴承阻尼系数也可从表27-7-9查得量纲一阻尼系数、
、
、
值,换算成有单位的阻尼系数,
、
、
。
7.6 轴系的临界转速计算
7.6.1 轴系的特征值问题
通常轴系支承在同一水平线上,由于转子的重力作用,未转动时,转轴发生了弯曲静变形,转动时,这种弯曲有可能加大。实际上当转子以ω的角速度回转时,由于不平衡质量激励,轴系只能做同步正向涡动,即圆盘相对于轴线弯曲平面的角速度(Ω-ω)为零,这种状态下,转轴不承受交变力矩,轴材料内阻不起作用,轴系的运动微分方程就是轴系的弯曲振动微分方程,轴系的临界转速问题即为轴系弯曲振动的特征值问题。
为计算轴系的临界转速,首先应将轴系按前节方法转化为质量离散化的有限元单元模型。将各质量单元(圆盘)和梁(转轴)单元自左向右编号,则有mi、Ii、Ipi(i=1,2,…,n)和li、EJi、αiGAi(i=1,2,…,n-1);各支座自左至右编号,则有Kpj、mbj、Kbj(j=1,2,…,l);支座轴颈中心编号用数组S(j)表示,对于l<n系统,轴颈中心编号同有支座作用的质点编号是一致的,它是联系i和j的桥梁。现对第i个轴段进行分析,单元两端面的挠度γ和转角θ与图27-7-5所示弯矩M和剪力Q存在下列关系:
(27-7-9)
式中
αi为与截面形状有关的因子,对于实心圆轴αi=0.886,Ai为截面积,G切变模量。
再对第i个圆盘进行分析,当轴以ω的角速度作同步正向涡动时,由图27-7-5所示的第i个圆盘得:
(27-7-10)
Kpj为第j个支座的油膜刚度,γbj为第j个支座质量mj的位移。为使符号统一,将ω改为ωn,第i个单元的特征值方程为:
(27-7-11)
式中 (27-7-12)
(27-7-13)
(27-7-14)

图27-7-5 单元受力分析
式中
(27-7-15)
如果第i个圆盘没有支承,则γbj、Kpj、Kbj、mbj均可去掉,此时KMi为6×1阶列阵,mi和Ki为2×6阶矩阵。此处υi定义参阅式(27-7-9)及说明。
以上只是对i单元的分析,对其他各单元的分析可得到类似的式(27-7-11)及其相应的式(27-7-12)~式(27-7-15)。将各单元的公式进行组合,就可以得到轴系的(2n+1)个自由度的特征方程,求解之,就可得到的(2n+1)个解。特征值
并不完全为正实数,除去负数,只有
为正实数的特征值的平方根才是各阶同步正向涡动的临界角速度。由式(27-7-1)换算为临界转速。
以上只可能运用矩阵迭代法、QR法等在计算上求解(已有现成软件)。
7.6.2 特征值数值计算实例
[例] 图27-7-6所示发电机转子简化模型,两支承参数相同,KP=2.45×106kN/m,Kb=3.92×106kN/m,Mb=17.64t,转子数据见表27-7-11。按上述原始数据以及某些数据做15%的调整,根据参数的不同情况分别形成质量矩阵M、刚度矩阵K,用QR法计算该转子系统的一、二阶临界转速和振型。

图27-7-6 发电机转子简化模型
nc1、nc2的计算结果列于表27-7-12。其振型矢量由于过于复杂,计算结果未列出。
表27-7-11 转子各轴段和集中质量数据

表27-7-12 调整部分参数值后轴系一、二阶临界转速计算结果

①灵敏度公式见表27-7-17。
7.6.3 传递矩阵法计算临界转速
传递矩阵法适用于单跨或多跨、弹性支承或刚性支承、有外伸端或无外伸端等各种轴系,而且便于使用计算对轴系的临界转速进行较精确的运算。
把轴系分割成如图27-7-7所示的若干单元,每个单元可以是分布质量的轴段、无质量的轴段、集中质量和无质量轴段的组合、弹性支承等。各单元之间的特性也能够矩阵表示,即传递矩阵,再把这些矩阵相乘,求出整个轴系的传递矩阵,利用边界条件得到轴系的临界转速。

图27-7-7 传递矩阵法计算模型
每个单元左右两端的状态用挠度y、倾角θ、弯矩M和剪力Q表示,简记为{Z}=[y、θ、M、Q]T,每个单元的传递关系为
(27-7-16)
式中 [T]i——各单元的传递矩阵。
整个轴系的传递方程为
(27-7-17)
①单元的传递矩阵 根据各种单元的特性推导出的传递矩阵见表27-7-13。
②频率方程 根据各单元的传递矩阵,按式(27-7-17)求出整个轴系的传递方程为
(27-7-18)
轴两端的支承形式不同,其边界条件不同,根据边界条件求出频率方程式,见表27-7-14。求解频率方程得轴系的固有频率,再按式(27-7-1)求得轴系的临界转速。
表27-7-13 单元的传递矩阵


表27-7-14 频率方程式


7.6.4 传递矩阵法计算实例
某转子可以简化为图27-7-8所示集总质量系统,数据如下:
m1=m13=2.94t mi=5.88t (i=2,3,…,12)
li=1.3m (i=1,2,…,12)

图27-7-8 机组转子的振型
支承相应参数为:
Kpj=1.9600×106kN·m-1,Kbj=2.7048×106kN·m-1,Mbj=3.577t j=1,2,…,5
取第i个部件来分析,对mi取分离体,由表27-7-13得
对轴段li取分离体,如果轴重不计,由表27-7-13可得
两矩阵合并,即可建立第i点与第i-1点状态向量之间的关系
则系统的传递矩阵可写为
若边界条件为=
=
=0,由表27-7-14可得满足此边界条件的频率方程为
t31t42-t32t41=0
由上式可得转子的临界转速如表27-7-15所示,振型如表27-7-16所示。
表27-7-15 传递矩阵法计算转子临界转速的结果

表27-7-16 系统第二阶振型

7.7 轴系临界转速设计
7.7.1 轴系临界转速修改设计
当按初步设计图纸提出简化临界转速力学模型,用特征值计算方法求出各阶临界转速及对应的振型矢量以后,如发现某阶临界转速nci与轴系的工作转速接近,立即将计算得到的第i阶振型矢量进行正规化处理,求得正规化因子μi,用μi去除振型矢量的各个值。然后利用轴系同步正向涡动的特征方程导出的第i阶临界转速对参数Sj的敏感度公式(见表27-7-17),并给出参数微小变化量ΔSj(通常<20%),计算出引起临界转速的变化量。通过对各种参数改变计算结果的比较,优化组合,选出最佳参数修改组合,对轴系临界转速进行修改设计。如果轴系有n个参数Sj同时有微小变化(j=1,2,…,n),改变量分别为ΔSj,轴系第i阶临界转速的相对改变量:
(27-7-19)
参数修改后轴系的第i阶临界转速:
(27-7-20)
结合图27-7-6所示系统实例,按三种不同参数变化组合,用敏感度公式计算轴系的一、二阶临界转速,计算结果列于表27-7-12中。将计算结果与用QR法计算结果的比较,可以看出用该方法进行修改设计的可靠性。
表27-7-17 临界转速对各种参数的敏感度计算公式

7.7.2 轴系临界转速组合设计
转子系统经常是由多个转子组合而成。组合转子系统和各单个转子的临界转速间既有区别又有联系,其间存在一定的规律。这种联系就是各轴系具有相同形式的特征方程。设A、B为两个不同转子,如图27-7-9(a)所示,各转子分别有r及s个圆盘,为简单起见,设各支承为等刚度支承,这一组合系统的特征值方程:
(27-7-21)
式中
KA、KB、MA、MB分别为A、B两个转子的刚度矩阵和质量矩阵。

图27-7-9 轴系组合模型
当对系统坐标进行如下线性变换:
式中 q=[q1,q2,…,q2(r+s)]T
系统的频率方程:
(27-7-22)
线性变化不改变系统的特征值。现将A、B两个转子端部铰接成如图27-7-9(b)所示的系统C,由连续性条件γAr=γB1决定q2r+1=0,系统C的频率方程实际上就是式(27-7-22)划去2r+1行和2r+1列的行列式。由频率方程根的可分离定理知,系统C的临界角速度应介于原系统A和B各临界角速度之间,这是组合系统与各单个转子临界角速度间的一条重要规律。同理再将系统C的铰接改为图27-7-9(c)所示的刚性连接系统D作同样变换,又会得出D系统的临界角速度介于C系统各临界角速度之间。综合以上结果,这一重要规律可概括为:如果将组合前各系统的所有阶临界角速度混在一起由大到小排列:
则按C系统组合后第i阶临界转速与组合前临界转速之间的关系为
按D系统组合后临界转速与组合前临界转速关系为
所以 (27-7-23)
现以200MW汽轮发电机组为例,组合前后都用数值计算方法计算系统低于3600r/min的各阶固有频率及振型矢量,临界转速的计算结果列于表27-7-15,组合后的各阶振型如图27-7-10所示。计算结果也验证了机组的临界转速介于各单机临界转速间,这就使得在设计中,有可能根据各个转子的临界转速去估计机组的临界转速的分布情况,也有助于判断机组临界转速计算是否合理,有无遗漏等。由图27-7-10中各阶主振型可以看出,机组的一阶主振型,发动机振动显著,其他转子振动相对较小,所以称一阶主振型为发电机转子型,这一结果对现场测试布点具有重要意义。

图27-7-10 机组转子的振型
7.8 影响轴系临界转速的因素
7.8.1 支撑刚度对临界转速的影响
在常用的临界转速计算公式和近似计算方法中,都假定支承为绝对刚性的。实际上,轴承座、地基和滑动轴承中的油膜都是弹性体,其刚度不可能无穷大,支承刚度越小,临界转速越低。对于支承刚度比本身刚度大得多的情况,可以忽略支承刚度的影响,按刚性支座计算临界转速。反之,则应按弹性支座计算临界转速。对于传递矩阵法,把表27-7-13中列出的弹性支承的传递矩阵加入式(27-7-17)中,就计及支承刚度对临界转速的影响。
7.8.2 回转力矩对临界转速的影响
在常用的临界转速的计算公式及计算方法中,都把圆盘简化为集中质量点,即只计重量不计尺寸,只考虑圆盘的离心力。若圆盘处于轴中央部位,如图27-7-11(a)所示,这种简化是适当的,此时,圆盘只在自身的平面内作振动或弓状回旋,圆盘的转动轴线在空间描绘出一个圆柱面,没有回转力矩的影响。而当圆盘不在轴的中央部位时,如图27-7-11(b)所示,圆盘的转动轴线在空间描绘出一个圆锥面,圆盘的自身平面将不断地偏转。因此,应考虑由于圆盘的角运动而引起的惯性力矩,此力矩常称为回转力矩。当轴的转速较高,圆盘位置偏离中部或在悬伸端时,回转力矩较大。一般回转力矩是使转轴的轴线倾角减小,即增加了轴的刚度,提高了临界转速。对于多圆盘转轴,外伸臂式转轴,圆盘尺寸较大以及计算高阶临界转速时应考虑回转力矩的影响。

图27-7-11 回转效应示意图
7.8.3 联轴器对临界转速的影响
在用联轴器把各轴联成轴线时,有时由于联轴器的位移约束作用,轴系比单轴的临界转速要高;有时由于联轴器的重量作用,轴系比单轴的临界转速低。因此,在计算有联轴器的临界转速时,应考虑联轴器的影响。应把联轴器作为一个单元,其左端到右端的传递矩阵见表27-7-13,把相应的传递矩阵代入轴系的传递矩阵方程,计算出受联轴器影响的轴系临界转速。
7.8.4 其他因素的影响
影响临界转速的因素很多,例如,轴向力、横向力、温度场、阻尼、多支承轴中各支承不同心、转轴的特殊结构形式等。另外,由于转轴水平安装时受重力的影响,还会产生1/2的第一阶临界转速的振动。这些影响因素一般可忽略不计,在特殊情况下,应予考虑。可参考相应的振动理论进行处理。最终以实物测试来修正与确定其实在的临界转速。
7.8.5 改变临界转速的措施
当转轴的工作转速与其临界转速比较接近而工作转速又不能变动时,应采取措施改变轴的临界转速。
设计时,一般可采取以下措施:改变轴的刚度和质量分布;合理选取轴承和设计轴承支座。此外,对高速转轴的油膜振荡,对大型机组的基础刚度也要考虑它们对临界转速的影响。
机器运行中发生强烈振动时,首先要检查轴的弯曲变形、动平衡和装配质量等情况。当判别清楚强烈振动是因工作转速和临界转速接近而引起时,一般可采取以下措施:在结构允许的条件下附加质量;改变油膜刚度和轴瓦结构;改变轴承座刚度;采用阻尼减振、动力减振或其他减振措施。