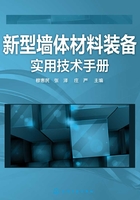
第二节 锤式粉碎机
一、概述
锤式粉碎机是1895年由M.F.Bedmson发明的,距今已有100多年的历史了。在这100多年的时间里,它的应用范围不断扩大。目前,锤式粉碎机的使用已遍及冶金、建材、化工、电力、交通等各个部门,应用非常广泛,主要用于中细碎石灰石、煤、煤矸石、焦炭、页岩、白垩、石膏、炉渣、原矿石、水泥熟料等中低硬度的物料。随着科学技术的不断发展,锤式破碎机的种类也越来越多。反击式粉碎机就是在锤式粉碎机的基础上发展起来的一种新型高效粉碎机。反击式破碎机为锤式粉碎机的一种,目前它已成为锤式粉碎机中的主流产品。近几年来,粉碎机行业发展很快,国际上的一些前沿技术在粉碎机行业得到了充分的利用。同时,随着工业自动化程度的快速发展,对粉碎机的使用性能提出了更高的要求。从国际上整体的发展趋势看,锤式粉碎机正朝着高产量、大破碎比、高耐磨性发展。我国冀东水泥厂引进德国O&K公司制造的反击式锤式粉碎机,它的规格为2300mm×3570mm,能将2000mm物料一次性破碎至25mm以下,其生产能力可达2000t/d,国内生产的锤式粉碎机很难达到这一水平,即使在某些方面达到国际水平,但整体技术水平不高,与国际先进水平还有一段距离,还有很大的提升空间。市场需求量的不断扩大,是推动这一行业发展的巨大动力。未来几年,粉碎机行业将会保持一个稳定、持续、较快的发展速度。
二、结构及工作原理
(一)锤式粉碎机型号的表示方法
PCK-1010也可以表示为PCK-1000×1000。
随着破碎机应用范围的不断扩大,生产厂家不断增多,一些生产厂家根据自己产品的不同特点,自己命名本公司产品。如山东矿机迈科公司生产的YKP系列和MB系列细碎粉碎机都充分体现了自己公司的特点和与众不同的使用性能。
(二)锤式粉碎机的分类
(1)按转子数目可分为单转子和双转子(见图2-2-1、图2-2-2)。

图2-2-1 单转子

图2-2-2 双转子
(2)按转子的回转方向可分为可逆式和不可逆式(见图2-2-3、图2-2-4)。

图2-2-3 可逆式

图2-2-4 不可逆式
(3)按锤头的排列方式可分为单排式和双排式。锤头安装在同一回转平面上,和锤头安装在几个不同的平面上。
(4)按锤头在转子上的连接方式可分为固定锤式和活动锤式(见图2-2-5、图2-2-6)。

图2-2-5 固定锤式
1—机架;2—前盖板;3—上侧架;4—上盖板;5—冲击板Ⅰ;6—冲击板Ⅱ;7—锤头;8—转子;9—后板;10—可调衬板;11—篦板

图2-2-6 活动锤式
1—上机体;2—下机体;3—筛板;4—衬板;5—锤头;6—转子
(三)锤式粉碎机的基本结构
锤式粉碎机的种类虽然很多,但它的整体结构差别不大。下面以固定锤式反击式粉碎机和活动锤式可逆式粉碎机为例,具体介绍锤式粉碎机的基本构造(见图2-2-5、图2-2-6)。
锤式粉碎机主要由以下几部分组成:上箱体部分、下箱体部分、转子部分、筛子部分、传动部分等。
(1)上箱体部分 主要包括机体、方形防护条、防护条等。
(2)下箱体部分 主要包括底座箱体、底座上板、轴承架、堵板等。
(3)转子部分 主要包括皮带轮、主轴、转盘、轴承座、锤头轴、锤头等。转子部分是设备的核心部分。
(4)筛子部分 主要包括筛条、筛条座、弧形双头螺杆、托板等。
(5)传动部分 主要包括电动机、电机皮带轮、电机底座等。
反击式粉碎机又增加了可调衬板部分,它主要包括衬板、方头螺栓、弹簧等。
(四)锤式粉碎机的工作原理
锤式粉碎机由电动机通过三角皮带传动带动主轴旋转而工作。
(1)锤式粉碎机工作原理 物料从上料口落入破碎室后,被高速旋转的锤头打击而破碎,破碎后的物料在锤头冲击的过程中又获得动能,以很高的速度冲向方形防护条、衬板和其他物料,形成物料与衬板、反击板,物料和物料之间的高速碰撞而使物料破碎。
(2)反击式锤式粉碎机工作原理 物料从上料口进入破碎机后,经旋转的锤头打击后与冲击板Ⅰ进行碰撞实现物料的第一次破碎;一次破碎后的物料在冲击板的反弹与物料自重的作用下下落,与锤头进行第二次接触,在旋转锤头的二次打击下与冲击板Ⅱ进行碰撞,实现物料的第二次破碎;破碎后的物料在冲击板的反弹与自重的作用下下落进入由高速旋转的锤头与可调衬板(可实现与锤头的距离的调节)组成的研磨区进行挤压研磨,使大部分物料满足粒度要求从篦板孔落下;极少数物料在篦板与锤头形成的空腔内打击碰撞,最终满足粒度要求从篦板孔落下。
(五)锤式粉碎机的基本参数
锤式粉碎机的基本参数是生产厂家设计、制造的主要依据,也是使用单位进行工艺流程设计能力配套选择的重要的依据。锤式粉碎机的基本参数主要包括锤头转子直径、进料粒度、出料粒度、生产能力、主轴转速、锤头的排数及每排锤头的数量、电动机功率及设备重量等。
下面以三台具体的粉碎机参数为例进行介绍。
1.基本参数(见表2-2-1~表2-2-3)
表2-2-1 粗碎锤式粉碎机的基本参数

表2-2-2 细碎锤式粉碎机的基本参数

表2-2-3 反击式细粉碎机的基本参数

2.锤式粉碎机主要参数的确定原则
锤式粉碎机的主要参数项目与一般粉碎机的参数项目基本相同,这些参数的确定都必须遵循一定的原则,现分别说明如下。
(1)锤式粉碎机的规格 锤式粉碎机的规格是以转子直径的大小尺寸表示的,转子直径尺寸是锤式粉碎机的主要参数。转子直径尺寸越大,锤式粉碎机机体横截面积也越大,在单位时间内可以通过的物料则越多,产量也越高。一般是要求锤式粉碎机的生产能力愈大时,转子直径尺寸也愈大。
(2)进料粒度 锤式粉碎机的进料粒度是根据物料中碎时采用粗碎锤式粉碎机不同产量时粒度不同的原则进行配用的。如MB800型细碎锤式粉碎机与CP900×800粗碎锤式粉碎机的配用。
(3)出料粒度 出料粒度是锤式粉碎机的一项重要性能参数。出料粒度的大小将直接影响到空心砖的质量好坏。国内各种类型的锤式粉碎机都日益趋向细碎化,以期达到大幅度提高产量和节省电耗的目的。
锤式粉碎机的出料粒度是根据进料粒度、生产能力和破碎比来确定的。实践表明,在维持一定的生产能力下,进料粒度越大时则出料粒度也越大。出料粒度的大小,又与锤头排数的多少和每排锤头的数量有着密切的关系。一般情况是锤头排数和每排锤头数量越多时,物料被打击的次数将越多,则出料粒度将越细。
(4)主轴转速 锤式粉碎机的主轴转速是一个重要的工艺参数,它对产品的粒度和破碎比起着决定性作用,同时,对锤式粉碎机的生产能力也有很大的影响。确定主轴转速时,往往是先假定锤头的圆周速度,以锤头旋转时所产生的动能和冲击能能够击碎所确定的物料进行选择。因此,主轴转速选择的原则是:既要使锤头旋转时的冲击动能满足破碎中硬物时所需要的能量,又要使物料的出料粒度达到设计要求的条件下,选择较低的转速。
锤式破碎机是以锤间的冲击作用进行工作的。其动能和冲击能首先要满足物料的破碎要求,因为每一种物料都需要合适的圆周速度以获得在最优粒度下的最大产量。
当锤间的圆周速度过低时,冲击动能就小,则不能破碎物料,或能破碎物料但出料粒度过粗;反之,圆周速度高时,锤头的冲击动能就大,则容易击碎物料,出料粒度也较细。破碎比也增大,生产能力也相应提高。主轴转速是不是可以无限制地提高呢?不是的,因为,转速达到一定的速度时,会严重影响物料的下料速度,反而降低生产效率,且功率消耗也显著增加。同时还将引起锤头和衬板的剧烈磨损、寿命缩短,造成更换锤头、衬板而停机的次数大大增加和生产时间的缩短,成本反而增高,生产效率下降。
多年的实践证明,锤式粉碎机破碎中等硬度物料时,在综合平衡各种因素后,锤头的线速度一般在20~30m/s的范围内选择为宜。
(5)电机功率 锤式粉碎机的功率和很多因素有关,但主要取决于物料的性质、破碎比、生产能力和锤头的圆周速度。
锤式粉碎机电机功率的选择的原则是:一方面要保证机器正常运转时所需的额定负荷,另一方面也要考虑工作时误入大块或铁件等特殊情况下,电流突然增大时不至于烧毁电机的一定安全值。
(6)生产能力 影响锤式粉碎机实际生产能力的因素有很多,比如主轴转速、转子直径、进料粒度、破碎比及进料均匀程度等。目前,我国还没有一套完整的计算锤式破碎机生产能力的理论公式,仅可以根据制造厂家多年实践归纳出来的经验公式进行估算。
生产能力=(1.8~2.2)转子直径×主轴转速的平方×进料粒度/出料粒度×锤头与衬板间隙的平方
(7)锤头排数及个数 物料自进料口自由下落时,将依次受到机内高速旋转的各排锤头的连续打击而破碎成小颗粒。锤头的排数与物料的排数粒度有密切的关系。排数越多物料被打击的次数将越多,排料粒度则越细,但所需的电机功率也就越大,且机体也将升高,重心随之提高,则机械的稳定性就越差。而且,锤头排数过多时,也越容易产生过粉碎现象。
三、主要零部件要求
①主轴材料的力学性能应不低于JB/T 6379—2007中第2章45或50号钢的规定。
②耐磨件材料的力学性能应不低于JC/T 401.1—2011中第4章ZGMn13的规定。
③主轴应经超声波探伤检验,并应符合JB/T 5000.15—2007中Ⅳ级的规定。
④转子体(不含锤类件)应进行平衡试验,其平衡品质等级值应符合GB/T 9239.1—2006中G16的规定。
⑤外购件应不低于相关国家标准、行业标准,并具有合格证。
⑥切削加工件未注尺寸和角度公差、形位公差均应符合JB/T 5000.9的规定。
⑦焊接件应符合JC/T 532—2007的规定。
⑧主要零件材料的力学性能,应不低于表2-2-4所列材料的规定。
表2-2-4 主要零件材料的力学性能

四、制造过程及技术工艺
技术要求是设计、制造锤式粉碎的依据,是为了满足机械设备的使用要求而必须具备的技术性能指标。
(一)主要零件的技术要求
1.锤式粉碎机主轴
(1)主轴材料 主轴是承受扭、弯、压应力的主要零件,处在各种负荷下工作,受力情况比较复杂,要求其应具有良好的综合机械性能,保证有足够的抗扭、抗弯、抗疲劳、耐冲击等能力。因此,要求主轴必须用45#钢,综合机械性能比较好,材料来源广,成本较低廉,又具有良好的热处理性能,所以是制造锤式粉碎机主轴的主要材料。
为保证主轴能长期安全运行,主轴在精加工后应进行探伤检查,不允许有夹渣、裂纹等影响质量的缺陷。
(2)主轴的热处理要求 为进一步提高主轴的韧性和机械强度,延长使用寿命,要求主轴必须经过调制处理,表面硬度不能低于HB217~HB255。
(3)主轴精度 在主轴上安装有数排锤头,两端装轴承,顶端装皮带轮,它们都随主轴高速旋转。因此,严格规定主轴各段轴径的精度具有头等重要的意义,是保证机器运行平稳的首要条件。
主轴各配合轴径应符合以下要求。
①各段轴径的同轴度公差为8级,这是根据在不影响产品使用性能的条件下,选择较低精度的原则确定的。由于主轴较长,如果同轴度要求过低,又会影响机械的使用性能,使主轴运行不平稳,机器振动过大等。长期的实际使用证明,主轴同轴度公差规定为8级是最合适的,能满足实际使用的要求。
②与轴承配合处的表面粗糙度的最大允许值为1.6μm,与密封件配合处的表面粗糙度的最大允许值为3.2μm,这两处的表面粗糙度规定,是与主轴相应轴径的公差等级相适应的。
③与轴承配合处的轴径圆柱度公差为8级。要保证轴径与轴承配合良好,接触可靠,同时考虑易于加工、降低成本,且从实际使用来看,规定轴径的圆柱度公差为8级较为合理和经济。
2.锤式粉碎机锤头和衬板
锤头和衬板是锤式粉碎机的主要易损件,要求具有良好的耐磨性能,一般用高锰钢或高铬铸铁来制造。考虑到成本等方面的原因,目前许多中小型企业仍采用高锰钢锤头和衬板。而新型的耐磨材料高铬铸铁,耐磨性能比高锰钢要优越得多,现已在砖瓦行业中逐步得到应用。
衬板是紧贴在筒体内壁上的。为贴合紧密,利于装配,保证衬板与锤头之间的间隙符合设计要求,一般都是衬板装配面不允许有倾斜,并要求应光洁规整。
(二)装配技术要求
锤式粉碎机的结构虽然较为简单,但由于零件是做高速旋转,在装配时必须严格遵守下列技术要求。
主轴轴承装配后,上轴承的轴向间隙应保证在0.15~0.25mm之间,下轴承的轴向间隙应该在0.1~0.2mm之间。
规定一定的轴向间隙,主要是为了避免工作时因温度升高,主轴轴向伸长而引起不必要的附加应力,造成机器的损坏。
①衬板不允许用火焰切割,这是为了避免零件产生不应有的变形。
②锤头应称重,同一排锤头的重量差值不得大于0.2kg。且在装配时,应将重量差值最小的一对,成对对称装入同一排中,锤头装配后应转动灵活。
上述规定主要是为确保主轴运转平稳,努力减小机器运转时的振动。实践证明,当同一排锤头差值不大于0.2kg时,能达到机器振动小和运转平稳的要求。
③电机皮带轮上端面应与主轴皮带轮上端面在同一平面内,其偏移误差不得大于两皮带轮中心距的2‰。
要求保证了主轴和电机轴中心线的平行,使皮带受力均匀,减轻对主轴的附加应力。
④在外观质量方面,所有零件结合部分边缘应整齐匀称,不应有明显的错位,机器外表面要求光滑、美观。
(三)运转技术要求
锤式粉碎机所有零件加工、组装完毕后,应对整机进行空负荷试车和负荷试车,以检验机器的设计、零件的加工和装配质量。
1.空运转技术要求
①电气控制准确可靠;
②润滑正常,无漏油现象;
③运转中无金属碰击声及其他异常声响;
④轴承温差应小于30℃;
⑤噪声应不大于80dB(A);
⑥上盖处的径向振幅不大于0.5mm。
2.负荷运转要求
①运转中轴承温差不大于50℃;
②噪声应不大于85dB(A);
③上盖处的径向振幅不大于0.5mm;
④进料粒度、出料粒度和生产能力应符合相应机型的性能参数。
五、装配及安装要求
①空负荷运行时,在主轴承座上测量的水平和垂直振幅不得大于0.12mm。
②转子轴的水平度不大于0.2mm/1000mm。
③锤头外缘运动轨迹与冲击板和篦板之间的间隙应不小于10mm。在烘干锤式破碎机中,该间隙应不小于20mm。
④对称位置的两排锤头,其总重量差不得大于总重量的0.25%。
六、安装及调试工艺
全面掌握锤式粉碎机的正确安装和使用方法,是保证机器正常运转和优质高产的前提条件。有了制造质量精良、合理配套的机器后,如果安装不好,或者使用不当,也不能保证安全高效地运行,甚至会损坏机器或者降低机器的使用寿命,造成不应有的经济损失。本章仅对锤式粉碎机的安装与使用做简单介绍。
(一)锤式粉碎机的安装
1.基础
不论何种锤式粉碎机,对基础的要求总的来说是:能承受机器的重量而不沉陷;在运转时,各部分间的相互位置保持不变;并能承受机器高速运转时的震动。
锤式粉碎机的基础,一般都是用混凝土浇注而成。根据经验,混凝土基础的重量应是机组重量的1.5~2.5倍。基础的大小与厚度一般要求比机组高度大500~700mm,其面积应比机组底座每边大出100~150mm。
浇注混凝土的方法,多采用二次浇注法。
浇注基础前,要先挖好基坑,基础底部用灰土夯实,然后浇注碎石混凝土。在浇注时,应按照锤式粉碎机底座螺孔位置留出200mm×200mm的长方形孔。等基础凝固后,再按照机器底座螺孔位置,将地脚螺栓浇注到长方形中去,与基础固定在一起。
基础平面应仔细校平,以免锤式粉碎机安装后发生倾斜或在紧固时地脚螺栓引起底座变形,影响机器正常工作和使用年限。
2.安装与调整
①锤式粉碎机安装前,应清洗机器外部的一切污物。
②测量地脚螺栓尺寸是否符合机器地脚螺栓尺寸的要求,如不符合时,应及时校正。
③将主机吊装在基础上,以主轴皮带断面为基准,加垫调整机器与基础平面垂直。
④将电机组件吊装在基础上,加垫调整电机皮带轮上断面与主轴皮带轮上端面同水平面;调整电机底座调节螺栓,使两轮中心距在规定范围内。
⑤调整进料斗的位置,使其满足工艺安排的需求。
⑥进行二次灌浆,待水泥凝固后,精调两皮带轮的上端面同水平;调整中心距,使三角皮带张紧,但用手能转动其皮带轮。
(二)锤式粉碎机的使用
锤式粉碎机是一种高速运转的破碎机械,为确保其正常运转,操作人员必须预先熟读产品使用说明书,掌握正确的使用方法,严格按照规程操作。在使用过程中,应着重强调以下几点。
开机前,应与有关岗位取得联系,未经取得联系,不得随便开车或停车,以防堵塞或其他意外事故的发生。
机器启动后,待电机及粉碎机运转平稳后,方可加料。
要严格遵守空车启动、卸空停车的原则,严禁带负荷启动。
生产过程中,出料口不得有阻塞现象,以免影响排料。
喂料要均匀,防止喂入过硬的物料或铁件,以免损坏机器。
当发现主轴转速降低,破碎声异常时,应立即停止加料并停车,待查出原因并排除故障后方可开车。
经常检查、紧固地脚螺栓,防止松动。
停机时,应开门检查锤头、衬板等易损件的磨损情况,发现问题应及时处理。
用高压黄油枪经常对轴承加注润滑脂,以保证轴承具有良好的润滑。
经常检查轴承温度,一般应保持在70℃以下,最高不得超过90℃。如发现超过温度时,应立即停车检查,待排除故障后,方可重新开车。
经常检查卸料粒度,如发现不符合要求时,应停车检查锤头与衬板的磨损情况和皮带的张紧情况。如发现锤头、衬板磨损严重,则应调整锤头与衬板间的间隙,或者更换锤头、衬板。
七、维护与修理
锤式粉碎机的使用性和可靠性,取决于许多因素,如结构、材料、制造质量及保养使用状况等,即使这些条件基本上都得到满足,锤式粉碎机在使用中偶尔还是要发生一些故障的。当故障出现后,能及时发现并找出原因,采取有效措施加以排除,对充分发挥锤式粉碎机的效能并长期可靠地工作是十分重要的。否则,会由于小毛病得不到及时处理而造成重大事故。
(一)锤式粉碎机常见的故障及处理方法(见表2-2-5)
表2-2-5 锤式粉碎机常见的故障及处理方法

(二)锤式粉碎机故障产生的原因分析
分析产生故障的原因,无论对用户还是对生产商来说都非常重要,它可避免类似错误的重复发生。
1.故障的分析方法
①观察——查看仪表读数,机器运转状况,进、排料情况及润滑油泄漏情况等。
②触摸——用手检查机体与轴承部位的温度、零件的固定和机器的振动情况等。
③听诊——倾听机器运动声音的变化,有无敲击声或其他异常声音。
2.锤式粉碎机故障产生的原因
违章操作、使用不当,常犯的操作错误如下。
新锤式粉碎机或刚更换过轴承等的锤式破碎机,不经过充分地磨合而直接带高负荷使用,造成零件严重磨损。
直接带负荷启动,造成零件严重磨损,而引起一系列故障。
润滑油量不足,使润滑条件恶化,造成轴承发热、烧损。
长期超负荷运行,造成零件严重磨损或损坏。
带负荷停车,受热零件因冷却过快而引起骤冷裂纹。
3.维护保养不良出现的错误
①不及时地添加润滑油和定期更换润滑油,造成润滑油量不足,或润滑油污染、变质而丧失润滑性能,造成轴承发热而磨损。
②不经常检查和疏通加油管道,造成堵塞,使润滑油条件恶化,引起轴承发热磨损。
③不按期检查和调整主轴轴承的轴向间隙,造成因间隙过小,主轴受热伸长而轴承座磨损加剧或轴承盖顶裂。
④不经常检查衬板紧固螺栓和销轴的磨损情况,造成因衬板松动,锤头与衬板碰撞的严重事故。
4.装配和调整错误
①主轴承轴向间隙不符合规定,间隙过小或无间隙,引起轴承座严重磨损。
②锤头与衬板间隙过小,或因衬板受火焰切割而变形,引起锤头与衬板撞击事故。
③装配锤头不按重量进行级配,引起机器剧烈振动。
5.零件不合格出现的错误
由于零件的材质、加工精度不符合设计要求,使用时没有进行严格的检查而装配。或由于零件内部缺陷,检查时难于发现,而在使用过程中暴露出来,造成故障。常见问题如下。
①主要铸件(如锤头、衬板、轴承座、上盖及底座等)存在着缩松、砂眼、细小裂纹等铸造缺陷,这些问题往往在检查时不易发现,装在锤式粉碎机上初期也不容易暴露,而经过一个长期的使用,上述缺陷逐渐扩大,造成零件损坏。
②零件在加工制造时,没有很好地消除内应力,引起零件变形,丧失原来的加工精度和配合关系,如衬板、上盖翘曲变形。
③零件加工精度不合格,如主轴各段轴径的同轴度公差不符合标准规定,工作时产生剧烈跳动,造成机器振动过大等。