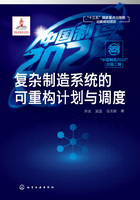
1.2 多重入复杂制造系统运作概述
1.2.1 多重入复杂制造系统概念及特征
多重入复杂制造系统(Multi Re-entrant Lines)主要指离散制造中一类具有结构性多重入特性的复杂制造系统,所谓的“重入”是指在制品WIP(Work in Process)按照其工艺流程,在生产过程中会出现反复多次进入同一个加工区域或设备进行加工的现象。发生重入的加工中心或设备的数量越多、重入的次数越多,制造过程及所需工艺也越复杂。所谓“结构性”重入,是指重入的现象是由工艺流程决定的,与其他制造系统中出现的“返工(Rework)”有本质不同,返工是指不合格品的重新加工,对生产线的负荷影响非常有限。
20世纪90年代初,Kumar等[5]将这类多重入生产系统定义为继作业生产与流水生产之后的第三类生产系统。作业车间与多重入生产的不同点为[6]:每一时刻每台机器只加工一个工件;每个作业不能在同一台机器上加工多次;不考虑作业加工的优先权;作业加工时间事先给定。流水车间每一个任务都有相同的流动次序,与多重入系统的生产方式更加不同。Kumar给出的多重入制造问题的定义如下[5]:
加工中心集合记为{1,2,…,S},加工中心记为σ,σ∈{1,2,…,S},包括Mσ台相同的设备。某类型若干工件进入加工中心σ1的缓冲区b1等待,加工完毕进入加工中心σ2的缓冲区b2等待。以此类推,假设σl是最后一个加工中心。那么σ1,σ2,…,σl就形成了工件的加工路径。对于不同的加工阶段i、j,i≠j,允许σi=σj。
在多重入制造系统中,普遍存在如下情况:不同加工工序的工件在同一设备前同时等待加工。这种情况使得每台设备的加工任务数目急剧增加,同时带来更多不确定性因素,直接导致设备产能即便能够满足加工任务要求,生产线也会出现WIP急剧增加、生产周期很难预测等非常不稳定状态。由于多重入加工流程的存在,使得多重入制造系统在本质上有别于传统的作业生产(Job Shop)与流水生产(Flow Shop),针对Job Shop与Flow Shop的相关研究成果也无法直接在多重入制造系统中得到应用。
1.2.2 典型多重入复杂制造系统——半导体制造
具有上述特征的多重入复杂制造系统有多种,如半导体芯片制造、薄膜胶片生产,其中,以半导体芯片制造为典型代表。进入信息时代以来,半导体制造作为微电子产业的重要基石,尤其受到了学术界和工业界的广泛关注。
半导体制造的主要产品是集成电路芯片,完整的制造过程包括硅片制备、硅片加工、测试/分类、装配与封装、产品终测五大步骤[7]。其中的硅片加工过程,即通称的半导体芯片制造过程,是技术最为复杂、资金最为密集的部分,该阶段的主要任务是将设计好的IC线路逐步制作在硅片制备加工阶段准备好的硅晶圆片上。这是一个步骤复杂且有大量重入现象的过程,往往需要进行成百上千道工序,概括起来主要有五个工艺阶段。
①氧化、淀积、金属化 通过氧化淀积在硅片表面形成一层SiO2薄膜,以隔离和保护硅片内的灵敏器件;通过金属化在绝缘介质薄膜上淀积金属薄膜,为形成电路连接做准备。
②光刻 将光刻胶涂到硅片表面后,经曝光在硅片表面形成所需的图形。这是芯片制造中最复杂也是最关键的操作,又可细分为涂胶、前烘、曝光、曝光后烘、显影、坚膜等步骤。
③刻蚀 用化学或物理方法有选择地从硅片表面去除不需要的材料,刻掉被曝光的部分以最终形成电路。刻蚀方法有干法刻蚀和湿法腐蚀,有图形刻蚀和无图形刻蚀。
④离子注入 选中的离子被植入本征半导体层中,以改变被曝光的部分的电学特性,形成不同导电形式的P型或N型区域。
⑤去胶 去掉残留的光刻胶。
由于半导体元件是层次化的结构,每一层以类似的工序生产,有些工序只是加入的材料或使用的模板有所变化,因此在工艺过程上就表现为不断重复访问某些设备,造成了多重入加工流程的出现。图1-3给出了一个半导体硅片加工的生产过程示意图[7],表1-5是其中的设备功能明细。图1-3中的大多数设备都被多次重入访问,例如完成沉积工艺的设备1的重入次数达到10次,而在实际的半导体生产线上某些设备的重入次数往往更多。

图1-3 半导体硅片加工的生产过程示意图
随着半导体芯片制造技术的不断发展,芯片制造企业之间的竞争势必越来越激烈,为了降低成本、快速收回投资,获得良好的经济效益,针对多重入的复杂半导体芯片制造的生产计划与调度的研究需求越来越强烈,提出了迫切需要解决的一系列决策优化问题。例如,合理的生产计划与调度体系结构、先进的建模方法与优化算法、实时调度与在线优化方法等。这些问题也给管理科学、系统科学和优化控制带来了新的挑战和广阔的研究和发展空间。从应用的角度看,对半导体芯片制造的生产计划与调度进行研究,将为半导体芯片制造企业的生产计划与调度提供决策支持的模型和软件工具,从而大大提高企业的生产管理水平。
表1-5 设备功能明细

1.2.3 制造信息系统
物质、能源和信息是社会赖以生存的三大要素,信息已渗透到社会的各个角落,对促进传统产业特别是制造业的进步发挥着越来越重要的作用。
制造系统的本质是对原材料进行加工处理,使之成为具有一定用途的产品的过程,表现在两个方面:一方面,能源是加工制造的一种驱动源;另一方面,制造过程中各种信息资源的采集和加工处理过程,也是增强产品信息含量的过程。因此,信息是加工制造的另一个驱动源。信息链接了制造系统各个要素,形成一定的生产组织结构的纽带,已经成为制造系统中与设备、能源同等重要的制造资源。建立以信息为导向的生产流程,可以使得产品设计、开发、制造、行销、售后服务等信息快速流动和有效管理,从而减少在制品数量,提升准时交货率,缩短生产周期,保证交货周期,减少不合格品数量,这已经成为企业强化竞争力,实现制造业信息化的基本前提。
制造信息系统是辅助制造企业实施管理和运营的信息化系统,是一个不断与市场、设计、制造等进行信息交换的复杂的开放性系统。根据普渡企业参考体系结构[8](Purdue Enterprise Reference Architecture,PERA),一个完备的制造系统体系架构可以自上而下地分为5个层次22项任务,涉及制造设备体系、信息系统体系、人与组织体系三大方面。其中,仅从制造信息系统的角度考察,可以概括为5个层次,自上而下依次为经营决策、企业管理、生产调度、过程优化、过程控制[9],如图1-4所示。基于PERA的五层结构给出了指导制造信息系统实施的详细路线图,用细分层次将生产过程控制和管理加以区分。

图1-4 基于PERA的制造信息系统模型
根据美国先进制造研究机构(Advanced Manufacturing Research,AMR)提出的制造业三层结构[10],将制造管理信息系统分为以企业决策、财物分析为核心的经营规划系统(BPS),以优化管理、优化运行为核心的制造执行系统(MES),以设备综合控制为核心的过程控制系统(PCS)三个部分(图1-5),为充分体现生产和管理的有机结合,进一步引入了制造执行系统(MES)作为上层决策管理与底层工业控制之间的重要桥梁。本书重点讨论的生产计划与调度作为MES的核心功能,是面向车间层的制造管理信息系统的中枢,旨在实现对车间内部具体生产活动的管理和优化,在制造信息系统中起到了承上启下的作用。

图1-5 基于BPS/MES/PCS三层结构的制造信息系统模型
企业车间层是一个企业物流与信息流的集中交汇点,也是制造价值增值的关键环节。通过对生产现场的透明化感知,实现对执行过程的有序可控,从而达到车间生产的高效优化,是生产计划与调度的根本任务。为此,不仅需要对生产计划与调度系统的结构、方法和集成应用等共性技术加以研究,而且还需要有针对性地对具有特殊需求和特点的制造对象加以特别研究与设计。