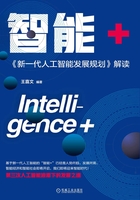
第一节 大规模推动企业智能化升级
《新一代人工智能发展规划》要求,支持和引导企业在设计、生产、管理、物流和营销等核心业务环节应用人工智能新技术,构建新型企业组织结构和运营方式,形成制造与服务、金融智能化融合的业态模式,发展个性化定制,扩大智能产品供给。鼓励大型互联网企业建设云制造平台和服务平台,面向制造企业在线提供关键工业软件和模型库,开展制造能力外包服务,推动中小型企业智能化发展(图1-41)。

图1-41 企业核心业务环节应用人工智能新技术
“智能制造”概念刚提出时,其预期目标是比较狭义的,即“使智能机器在没有人工干预的情况下进行小批量生产”,随着智能制造内涵的扩大,智能制造的目标已变得非常宏大。比如,“工业4.0”指出了8个方面的建设目标,即满足用户个性化需求,提高生产的灵活性,实现决策优化,提高资源生产率和利用效率,通过新的服务创造价值机会,应对工作场所人口的变化,实现工作和生活的平衡,确保在高薪资水平下仍然具有竞争力。我国工业和信息化部曾经指出实施智能制造可给制造业带来“两提升、三降低”,“两提升”是指生产效率的大幅度提升和资源综合利用率的大幅度提升。“三降低”是指研制周期的大幅度缩短,运营成本的大幅度下降,产品不良品率的大幅度下降(图1-42)。

图1-42 各环节的企业智能化
在家电、3C(计算机、通信和消费类电子产品)等行业,产品的个性化来源于客户多样化与动态变化的定制需求,企业必须具备提供个性化产品的能力,才能在激烈的市场竞争中生存下来。智能制造技术可以从多方面为个性化产品的快速推出提供支持,比如,通过智能设计手段缩短产品的研制周期,通过智能制造装备(比如智能柔性生产线、机器人、3D打印设备)提高生产的柔性,从而适应单件或小批量生产模式等。这样,企业在一次性生产且产量很低的情况下也能获利。通过先进的分析和建模技术,帮助决策者更好地分析极其复杂多变的风险和制约因素,以评估各种备选方案,甚至自动决策,从而减少人工干预,提高响应速度。
广泛采用工业机器人,实现“减员、增效、提质、保安全”的目的。工业机器人是典型的数字化、网络化、智能化制造装备,是新工业革命的重要内容。工业机器人不但能够适应恶劣的条件与苛刻的生产环境,而且能够有效提高产品的精度和质量,显著提高劳动生产率。目前,工业机器人技术正在向智能化、模块化和系统化的方向发展。更重要的是,随着技术的成熟和成本的下降,工业机器人即将迎来爆发式增长,在工业生产各领域得到广泛应用,极大推动工业生产方式向定制化、柔性化和对市场快速响应的方向发展。例如宝马沈阳工厂,作为宝马汽车全球生产体系中最新建成的一座工厂,诠释了当今最先进的生产技术和最新的环保生产理念,具有极高的灵活性,引领着个性化定制生产的潮流。
当前许多制造企业通常优先考虑效率、成本和质量,对降低能耗认识不够。然而实际情况是,不仅化工、钢铁、锻造等流程行业亟须降低能耗,汽车、电力装备等离散制造行业对节能降耗也有迫切的需求。以离散机械加工行业为例,我国机床保有量世界第一,约800多万台。按每台机床额定功率平均为5千瓦至10千瓦计算,我国机床装备总的额定功率为4000万千瓦至8000万千瓦,相当于三峡水电站总装机容量2250万千瓦的1.8至3.6倍。智能制造技术能够有力地支持高效可持续制造,首先,通过传感器等手段可以实时掌握能源利用情况;其次,通过能耗和效率的综合智能优化,可以获得最佳的生产方案并进行能源的综合调度,提高能源的利用效率;再次,通过制造生态环境的一些改变,比如改变生产的地域和组织方式,与电网开展深度合作等,可以进一步从大系统层面实现节能降耗。通过工业互联网实现供应链全面互联互通,可链接普通客户、供应商和IT系统,以及各部件、产品和其他用于监控供应链的智能工具。通过持续改进,建立智能化的物流管理体系和畅通的物流信息链,可有效地对资源进行监督和配置,实现物流资源的使用、物流工作的效果与物流目标的优化间的协调和配合。如此能使全球供应链网络实现协同规划和决策。
产品设计是产品形成的创造性过程,是带有创新特性的个体或群体性活动,智能技术在设计链的各个环节使设计创新得到质的提升。通过智能数据分析手段获取设计需求,进而通过智能创成方法进行概念生成,通过智能仿真和优化策略实现产品的性能提升,辅之以智能并行协同策略来实现设计制造信息的有效反馈,从而大幅缩短产品研发周期,提高产品设计品质。采用面向产品全生命周期、具有丰富设计知识库和模拟仿真技术支持的数字化、智能化设计系统,在虚拟现实、计算机网络、大数据等技术支持下,可在虚拟的数字环境里并行、协同地实现产品的全数字化设计,结构、性能、功能的模拟与仿真优化,极大地提高产品设计质量和一次研发成功率。
例如:波音新型客机采用全数字化设计、测试和装配,采用并行工程方法协同工作,采用虚拟现实技术进行模拟试飞,实现了机身和机翼一次对接成功和飞机上天一次成功。我国的大型运输机研制也全面采用了数字化、智能化设计技术,大大提高了设计质量,缩短了研发周期。
产品的价值体现在“研发—制造—服务”的产品全生命周期的每一个环节,根据“微笑曲线”理论,制造过程的利润通常较低,而研发与服务的利润往往更高,通过智能制造技术,有助于企业拓展价值空间。其一,通过产品智能化升级和产品智能设计技术,实现产品创新,提升产品价值;其二,通过产品个性化定制、产品使用过程的在线实时监测、远程故障诊断等智能服务手段,创造产品新价值,拓展价值链。
数字化、网络化、智能化技术的应用将使制造企业向数字化、网络化、智能化企业管控模式发展,可实现产品全生命周期各环节、各业务、各要素的协同规划与决策优化管理,不仅可有效提高企业的市场反应速度,同时可大幅度提高制造效益,降低产品成本和资源消耗,有效提高企业竞争力。
例如:波音公司通过建设数字化工厂,对各个制造环节进行了全方位、全周期的管理,取得了显著的经济效益:显著提高了生产效率,降低了质量缺陷率,减少了因供应商原因导致的生产延期,波音787研制周期缩短了1/3,研制成本降低50%。
在航天、船舶、汽车等行业,存在许多结构复杂、加工质量要求非常高的零件。以航空发动机的机匣为例,它是典型的薄壳环形复杂零件,直径可达3m,其外表面分布有用于安装发动机附件的凸台、加强筋、减重型槽及花边等复杂结构,壁厚变化剧烈。用传统方法加工时,加工变形难以控制,质量一致性难以保证,变形量的超差将导致发动机在服役时发生振动,严重时甚至会造成灾难性的事故。对于这类复杂零件,采用智能制造技术,在线检测加工过程中力—热—变形场的分布特点,实时掌握加工中工况的时变规律,并针对工况变化即时决策,使制造装备自律运行,可以显著地提升零件产品的质量。
人工智能在云计算、物联网和大数据等基础设施的支撑下,促进了企业的智能化。
(1)云计算:在一些有固定数学优化模型,需要大量计算,但无须进行知识推理的地方,比如,设计结果的工程分析、高级计划排产、模式识别等,通过云计算技术,可以更快地给出更优的方案,有助于提高设计与生产效率,降低成本,并提高能源利用率。
(2)物联网:以数控加工过程为例,“机床-工件-刀具”系统的振动、温度变化对产品质量有重要影响,需要自适应调整工艺参数,在这方面,物联网传感器对制造工况的主动感知和自动控制能力明显高于工人。因此,应用物联网传感器,实现“感知—分析—决策—执行”的闭环控制,能够显著提高生产制造的质量和效率。同样,一个企业的制造过程中,存在很多动态的、变化的环境,制造系统中的某些要素(设备、检测机构、物料输送和存储系统等)必须能动态地、自动地响应系统变化,这也依赖于制造系统的智能化。
(3)大数据:随着大数据技术的普及应用,企业竞争力的核心要素正在由资源要素驱动向信息数据驱动转变。大数据的典型应用包括产品创新、产品故障诊断与预测、企业供需链优化和产品精准营销等诸多方面。企业能拥有的产品全生命周期数据可能是非常丰富的,通过基于大数据的智能分析方法,将有助于创新或优化企业的研发、生产、运营、营销和管理过程,为企业带来更快的响应速度、更高的效率和更深远的洞察力(图1-43)。

图1-43 企业智能化带来的升级
由此可见,无论是在微观层面,还是宏观层面,智能化升级都能给企业带来切实的好处。