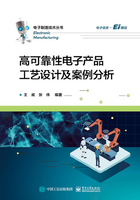
3.3 电子元器件工艺选型要求
目前,普遍使用的电子元器件从结构上可以分为有引线电子元器件和无引线电子元器件两种,安装方式多为表面贴装、通孔插装、压接安装、螺纹连接和胶接。选用元器件时,应结合产品的结构特点,综合考虑元器件的装联方式、布局密度、组装厂的工艺和设备、元器件的可测试性、可更换性、可获得性、电磁兼容性等。此外,元器件本身的封装特点,包括引线间距、引线可焊性、耐受温度和压力的能力等也是工艺选型时应当注意的因素。
3.3.1 尺寸要求
元器件的尺寸要求与所选用的安装方式和工艺能力有关,同样的元器件尺寸,在不同安装方式与工艺能力下的可接受标准可能差距很大。
元器件尺寸的工艺选型要求主要包括以下几个方面。
(1)设备能力对尺寸的要求
应尽量考虑选用与组装厂的工艺和设备相适应的元器件,例如:
① 0.3mm引线间距的QFP须用高精度贴片机和丝网印刷机,而1.27mm引线间距的QFP则只需选择中等精度贴片机即能完成。
② 目前市面上常见的高速贴片机基本可以满足贴装0201元件的需求(尺寸为0.6mm×0.3mm×0.2mm),部分可以满足贴装01005元件的需求(尺寸为0.3mm×0.15mm×0.1mm)。
③ 尺寸较大元器件的贴装一般由多功能贴片机完成,大多数多功能贴片机通常可以满足60mm×60mm×30mm的元器件贴装,某些支持多次照相定位的机型可以满足最长150mm的元器件贴装。
(2)尺寸的公差要求
元器件必须在规格书中注明引脚中心距、引脚直径(包括方形引脚的倒角直径)、封装体外形等尺寸的公差并符合标准要求。对于规格书中未注明公差的部分,一般应符合表3-1中对应的尺寸的极限偏差要求。
表3-1 尺寸的极限偏差要求

(3)共面度的尺寸要求
元器件焊接面(焊盘/引脚/锡珠)的共面度要求如表3-2所示。
表3-2 元器件焊接面(焊盘/引脚/锡珠)的共面度要求

注:无引线陶瓷芯片载体封装(LCCC)共面度指的是底面和焊端的共面度。
表面贴装连接器引脚形式是“Solder Ball”和“Solder Charge”时只可接受0.12mm的共面度。
对于采用焊料球或焊料柱作为引脚的栅格阵列元器件,根据其是否熔化,共面度要求略有不同,主要是因为焊接过程中,熔化的焊料球会发生沉降,在一定程度上可以弥补共面性缺陷。BGA共面度要求如表3-3所示。
表3-3 BGA共面度要求

(4)组装工艺对尺寸的要求
元器件的尺寸精度、引线间距、与安装孔/焊盘的匹配性对组装工艺的影响很大,因此为提高产品的可制造性和焊接质量,应对元器件尺寸严格把控。
① SMT制程对元器件尺寸的要求:目前贴片机的工艺能力,原则上基本可以满足01005级别元器件焊接,但实际选用时,还应考虑良品率的限制。
对于元器件的引脚间距选择,SMT制程元器件选用工艺要求建议参照表3-4执行。
表3-4 SMT制程元器件选用工艺要求

② 手工焊接工艺对元器件尺寸的要求:手工焊接相比设备焊接,操作的一致性较差,对人的依赖较高,不同技术能力的操作者对元器件选用的可接受性差异也较大,应根据大多数人的平均能力情况进行考虑。
手工焊接元器件选用工艺要求如表3-5所示,该表给出了手工焊接中存在一些组装问题,以及为解决这些问题而对元器件选型提出的特殊要求。
表3-5 手工焊接元器件选用工艺要求

3.3.2 可焊性镀层要求
1.镀层选型的目的
焊接,就是用加热的方式使两件金属物体结合起来。如果在焊接的过程中需要熔入第三种物质,则称为“钎焊”,所熔入的第三种物质称为“焊料”。电子产品组装中的“焊接”通常采用“软钎焊”,即用锡、铅等低熔点合金作为钎焊的焊料,因此俗称“锡焊”。
从物理学的角度来看,焊接是一个“扩散”的过程,是一个在高温下两个或两个以上物体表面分子相互渗透的过程。锡焊,就是让熔化的焊料渗透到两个被焊物体(如元器件引脚与印制电路板焊盘)的表面分子中,然后冷凝而使之结合。
从焊接机理可以看出,要获得良好的焊接效果,需要具备以下五个基本条件。
① 被焊金属材料必须具有可焊性;
② 被焊金属表面应洁净;
③ 正确选用助焊剂;
④ 正确选用焊料;
⑤ 控制好焊接温度和时间。
在上述五个基本条件中,后四个条件可以通过优化工艺予以满足,而可焊性作为金属材料的固有属性一经选定就被认为是不可改变的,因此,为获得良好的焊接效果,在元器件选型时,要注意镀层的选用。
可焊性在IPC标准中的定义是“金属被焊料润湿的能力”。而润湿的广义定义为:在基材上形成一层相对均匀、平滑、连续附着的焊料薄膜。这种润湿是通过在规定的助焊剂和温度条件下,测定熔融焊料在其上的实际润湿面积和润湿的最小时间来评估的。图3-1为焊料在母材上润湿情况示意图,润湿程度可以大致分为润湿良好、部分润湿和不润湿三种情况,如图3-1所示。

图3-1 焊料在母材上润湿情况示意图
可焊性的评估主要看以下三个方面的内容。
① 熔融焊料对基体金属的润湿性;
② 焊料和基体金属的结合性;
③ 结合部位的可靠性。
对可焊性的测试,国际上各大标准组织如IEC、IPC、DIN、JIS等推荐了各种方法,但是从试验的重复性和结果的易于解读性来衡量,润湿平衡法(Wetting Balance)是目前公认的进行定性和定量分析的可焊性测试方法。
润湿平衡法又叫表面张力法,是利用专用测量装置将试件从一垂直安装的高灵敏度的力学传感器上悬吊下来,以规定的速度浸渍到规定温度的熔融焊料槽中,当试件底部的焊端浸渍至规定的深度时,作用于试件上的浮力和表面张力在垂直方向上的合力即为润湿力,使用该润湿力与时间的关系来定量表征试件的可焊性。润湿平衡法测量装置示意图如图3-2所示。

图3-2 润湿平衡法测量装置示意图
通过可焊性测试,可以定量地评估电子元器件镀层的可焊性,大幅消除焊接缺陷,保证焊接可靠性,降低产品的返修率,提高生产效率、降低制造成本、提高产品质量。可见,对于元器件焊接而言,引脚的可焊性与焊接的可靠性之间有着密切的关系,只有选用具有良好可焊性镀层引脚的元器件,才能在合适的焊料、助焊剂、焊接条件下获得可靠的焊接。因此,对电子元器件的可焊性镀层进行工艺选型十分必要。
2.电子元器件常用可焊性镀层介绍
焊接过程是熔化的焊料和被焊接基体金属结晶组织之间通过合金反应,将金属和金属结合在一起的过程。许多单金属或合金均可以和SnPb、SnAgCu等发生冶金反应生成IMC,从理论上讲,它们均可以作为元器件引脚的可焊性镀层。
实际应用中,可焊性镀层可分为以下三类。
① 可熔镀层:焊接过程中,镀层金属熔化,如纯Sn镀层或SnPb、SnAgCu、SnCu、SnBi等Sn基镀层等。
② 可溶镀层:焊接过程中,镀层金属不熔化,但金属镀层可以溶解于焊料合金中,如Au、Ag、Cu、Pd等。
③ 不熔也不溶解镀层:焊接过程中,镀层既不熔化也不溶解于焊料中,如Ni、Fe、Sn-Ni等镀层。
表3-6给出了电子元器件引脚常用的镀层类型及特点。
表3-6 电子元器件引脚常用的镀层类型及特点

3.可焊性镀层选用要求
(1)镀层外观要求
要求引脚表面镀层外观清洁,镀层覆盖均匀饱满,无任何可见污染物和锈蚀、裂纹、露底、黑斑、针孔、划痕、烧焦、剥落、变色等缺陷。
(2)镀层的材料及厚度要求
元器件供应商应提供元器件引脚/端子表面镀层说明和相关测试报告。
有铅元器件镀层要求如表3-7所示。
表3-7 有铅元器件镀层要求

注:Ag焊料一般不推荐使用,如果必须选用,则应采用真空包装,且使用含银焊料;AgPt在贴片电阻、电容元器件中禁止使用。
无铅元器件镀层要求如表3-8所示。
表3-8 无铅元器件镀层要求

(3)可焊性要求
通孔插装元器件,其引出端的可焊性应符合GB 2423.28和GB 2423.32要求。表面贴装元器件的引线或电极的可焊性镀层如果为SnPb合金,其镀层厚度为5~7µm,镀层中锡含量应在60%~63%,片式元器件电极表面上的缺陷面积应小于电极总面积的5%。
3.3.3 耐热性能要求
1.温度对电子元器件的影响
数据表明,电子元器件的故障率随温度的升高呈指数增加,而电子产品的工作性能和可靠性则与温度的变化成反比。为了提高电子产品的可靠性,合理的热设计是必不可少的。在合理的热设计中,除散热结构设计外,选用耐热性能良好的电子元器件也是十分关键的。电子元器件的耐热性能包括耐工作温度和耐焊接温度两个方面。
① 温度对真空元器件的影响。
过高的温度对真空元器件玻璃壳和内部结构均有不良的影响。温度过高会使玻璃壳因热应力而损坏,同时也能使管内的气体电离,电离后的离子将轰击阴极,破坏其镀层,导致发射率下降,加速老化,缩短其工作寿命。因此,真空元器件的玻璃壳温度不得超过150~200℃。
② 温度对功率器件的影响。
功率器件的结温是由功率器件的耗散功率、环境温度及散热情况决定的,而功率器件结温对其工作参数及可靠性有很大的影响:
●功率器件的电流放大倍数随结温的升高而增大,这将引起工作点的漂移,增益不稳定,可能造成多级放大器自激或振荡器频率不稳定等不良后果。
●当功率器件的结温升高时,会使穿透电流和电流放大倍数迅速增加,集电极电流的增大促使结温进一步升高,而结温升高又使电流进一步增大,最终导致元器件被“热击穿”。为了防止热击穿,功率器件的结温不宜过高。
③ 温度对电阻的影响。
温度的升高会导致电阻的使用功率下降。如RTX型碳膜电阻,当环境温度由40℃增至100℃时,允许使用的实际功率将降为标称值的20%;又如RJ-0.125W金属电阻,当环境温度由70℃增至125℃时,允许使用功率为标称值的20%。此外,温度的变化对阻值大小有一定的影响,温度每升高或降低10℃,电阻大约要变化1%。
④ 温度对电容器的影响。
温度对电容器的影响主要体现为降低其使用时间。通常认为,当在超过规定使用温度下工作时,每提高10℃,使用时间就要减少一半。此外,温度的变化也会引起电容、功率因素等参数的变化。因此,对各种电容器的允许工作温度也进行了规定。
⑤ 温度对电感类器件(变压器、扼流圈)的影响。
温度对变压器、扼流圈等元器件的影响:除减少其使用时间外,还会使材料的绝缘性能下降。一般变压器、扼流圈的允许温度要低于90℃。
2.电子元器件工作温度的选用要求
对于元器件的工作温度选择,一般只需根据产品本身特点确定元器件的质量等级即可。不同质量等级的电子元器件的工作温度范围是:
① 商业级元器件的工作温度范围是0~+70℃。
② 工业级元器件的工作温度范围是−40~+85℃。
③ 军品级元器件的工作温度范围是−55~+150℃。
④ 汽车工业级元器件的工作温度范围是−40~+125℃。
3.电子元器件耐焊接温度的选用要求
(1)焊接工艺对元器件耐温的要求
电子元器件的耐热性能还包括耐焊接温度。而对于元器件耐焊接温度的要求,则需根据产品的组装工艺来确定,因为不同的焊接工艺对元器件的耐热能力要求是不同的。
不同焊接工艺对元器件的耐热能力要求如下:
① 热风回流焊工艺:要求能在215~230℃温度下,承受至少10个焊接周期的加热。
② 波峰焊工艺:要求能在260℃温度下持续10s。
③ 气相焊工艺:要求能在215℃下温度持续60s。
④ 红外回流焊工艺:要求能在230℃温度下持续20s。
因此在选用元器件时,应遵循与生产单位焊接设备相适应的原则。
(2)元器件封装及内部连接工艺要求
元器件耐高温性能,除与封装材料有关外,还与其内部连接方式有关。IC的内部连接方法有金丝球焊、超声压焊,还有倒装焊等方法,特别是BGA、CSP和组合式复合元器件、模块等新型元器件,其内部连接用材料通常采用表面组装用的相同焊料,连接工艺也是回流焊工艺,因此也要符合回流焊铅焊接的要求。
(3)组装工艺对元器件的特殊耐温要求
在电子元器件选用过程中,由于工艺制程原因,对元器件有特殊温度要求时,工艺人员应在选型之初提前与厂家沟通,达成一致意见,并将协商结果加入规格书。
设备焊接条件对元器件的耐温要求如表3-9所示。
表3-9 设备焊接条件对元器件的耐温要求

注:
• 数据来源:IPC/JEDEC J-STD-020D;
• 所有封装元器件能承受5次焊接者为优选元器件;
• 所有支持波峰焊接的元器件必须能支持2次正常波峰焊接;
• 所有支持回流焊接的元器件必须能支持3次正常波峰焊接;
• 元器件支持手工返修的能力为:350℃,持续5s。
手工焊接对元器件的耐温要求如表3-10所示(仅供参考)。
表3-10 手工焊接对元器件的耐温要求

注:实际焊接过程中,由于焊盘设计和印制板散热情况的不同,参数略有调整。
3.3.4 耐潮湿性能要求
1.湿度对电子元器件的危害
据统计,全球每年有1/4以上的工业制造不良品与潮湿的危害有关。对于电子工业,潮湿的危害已经成为影响产品质量的主要因素之一。电子元器件看起来是密封和防潮的,但实际情况恰恰相反,随着时间的推移,元器件会不断吸收空气中的潮气,吸潮程度与构成元器件的材料成分和制造工艺、运输及使用条件密切相关。大气中的水分会通过扩散渗透到湿度敏感元器件的封装材料内部。
在组装过程中,元器件将经历温度迅速变化的过程。以回流焊为例,在回流区,整个元器件要在183℃以上持续60~90s,最高温度可能在210~235℃(SnPb共晶)。无铅焊接的峰值会更高(245℃左右),在高温作用下,元器件内部的水分会快速转变为热蒸汽,气压的突变将导致封装体快速膨胀,膨胀的程度与封装材料成分、实际吸收的湿气量、加热温度、加热速度及封装体厚度等因素有关。当膨胀压力引起的变形达到一定程度后,构成元器件的不同材料之间的配合会失去调节,各种连接会产生不良变化,进而导致元器件剥离分层或爆裂(通常称作“爆米花”现象),元器件的电气性能受到影响或破坏。
与静电敏感器件ESD的失效一样,大多数情况下,对于湿度敏感元器件MSD的失效,通过肉眼是很难察觉的,有时甚至在测试过程中也不能完全发现。这种失效会作为可靠性隐患长期存在于电子产品中,一旦遇到外部条件变化,随时可能爆发。事实上,湿度因素对电子组装生产直通率和产品可靠性的影响不亚于静电因素和温度因素。
为减小潮湿影响,电子产品的生产和存储环境湿度都应该在40%以下,有些品种还要求湿度更低。
表3-11给出了不同阶段,潮湿对不同类型元器件的影响(推荐)。
表3-11 潮湿对不同类型元器件的影响(推荐)

2.湿度敏感元器件的概念和分级
湿度敏感元器件(MSD)是指因吸收空中的水汽而导致功能丧失或可靠性降低的元器件。根据标准,MSD主要指非气密性(Non-Hermetic)SMD器件,包括塑料封装器件、其他透水性聚合物封装(环氧、有机硅树脂等)器件。一般IC、芯片、电解电容、LED等都属于非气密性SMD器件。
J-STD-020给出了元器件潮湿敏感等级(Moisture Sensitivity Level,MSL)划分,IPC-M190J-STD-033则针对潮湿敏感元器件(MSD)问题提出了传输、包装、运送及应用方面的建议和要求。
元器件湿度敏感等级如表3-12所示。
表3-12 元器件湿度敏感等级

表3-12中部分名词含义:
① MBB:Moisture Barrier Bag,即防潮真空包装袋,该袋同时要考虑ESD保护。
② HIC:Humidity Indicator Card,即湿度显示卡,显示包装袋内的潮湿程度,一般有若干圆圈,分别代表相对湿度10%、20%、30%等,各圆圈内原色为蓝色,当某圆圈内由蓝色变为紫红色时,则表明袋内已达到该圆圈对应的相对湿度;当某圆圈内再由紫红色完全变为淡红色时,则表明袋内已超过该圆圈对应的相对湿度。若湿度显示超过30%,即30%的圆圈内HIC卡颜色完全变成了淡红色,表明生产前需要进行烘烤。
③ 警告标签:Warning Label,即防潮包装袋外的含MSIL(Moisture Sensitive Identification Label)符号、芯片的潮湿敏感等级(或含密封存储条件和拆封后存放最长时间及受潮后烘烤条件)和包装袋本身密封日期的标签。若标签上没有注明湿度敏感等级,可以参考条形码上的说明。
对于湿度敏感等级为2a~5a的元器件,在一盘原包装需拆开部分使用时,剩余材料必须立即做真空包装,并贴上时间控制标签;打开包装后的元器件,应根据湿度敏感等级,在规定的时间内完成焊接,若打开包装的元器件累计暴露时间超规定时间未使用,需对元器件进行烘烤,之后才能再使用。
SMT湿度敏感元器件烘烤条件对照表如表3-13所示。
表3-13 SMT湿度敏感元器件烘烤条件对照表

3.湿度敏感元器件的选用要求
湿度敏感元器件(MSD)对SMT生产直通率和产品可靠性的影响不亚于ESD,做好湿度敏感元器件的工艺选型,对于提高电子产品的良品率、提高产品的可靠性具有重要作用。
湿度敏感元器件工艺选型的一般原则是:
① 优选防潮等级≤4级的物料。
② 对于等级为5级、5a级和6级的物料的选用要严格限制,在工艺能力不能支持的情况下,禁止选用5级以上的防潮物料。
除了工艺选型的一般原则,还应考虑物料状态对湿度敏感等级和处理要求的影响,例如:
① 与IC托盘封装相比,卷带封装可以延长元器件的暴露时间,相当于提升了1或2个等级。
② 无铅焊接的高温环境则会使MSD的湿度敏感性至少下降1或2个等级。
③ 此外,实际生产过程中,生产线的频繁切换会使许多已经装到贴片机上的元器件不得不拆下来。这就意味着,大量没有用完的托盘元器件和卷带器件暂时需要储存起来以备后用。这些封装在托盘和卷带里的没有用完的湿度敏感元器件,很可能在重返生产线并进行最后的焊接以前,超过了其最大湿度容量。
3.3.5 防静电性能要求
1.静电对电子元器件的危害
静电的基本物理特性为:吸引或排斥,与大地有电位差,会产生放电电流。这三种特性会对电子元器件产生四种影响:
① 静电吸附灰尘、改变线路间的阻抗,影响产品的功能与寿命。
② 静电放电(Electro Static Discharge,ESD)破坏,造成电子元器件损伤(或完全破坏;或仍能工作,寿命受损)。
③ 静电放电产生的电磁场幅度很大(达到几百V/m)、频谱极宽(从几兆Hz到几千兆Hz),对电子产品造成干扰甚至损坏(电磁干扰)。
④ 静电放电时所产生的电场或电流发出的热量也会使元器件受伤(潜在损伤)。
其中,ESD是指带电体周围的场强超过周围介质的绝缘击穿场强时,因介质产生电离而使带电体上的静电荷部分或全部消失的现象。静电放电是高电位、强电场、瞬时大电流的过程,与此同时,静电放电会产生强烈的电磁辐射,形成电磁脉冲。ESD是引发电子元器件失效的主要因素。
随着集成电路、MOS电路和表面贴装元器件(SMD)的广泛应用和工艺技术的发展,元器件对静电放电的敏感性增加。虽然静电放电的能量对分立元器件的影响较小,但是对MOS器件的损害是致命性的。除致使元器件失效外,它产生的静电场会造成元器件的“软击穿”,从而给电子产品造成隐患或潜在的故障,直接影响电子产品的质量及可靠性。
静电放电可造成静电敏感元器件的功能失效和参数退化。失效的主要机理有热二次击穿、金属镀层融熔、介质击穿、气弧放电、表面击穿、体击穿等。静电对元器件造成的损伤可能是永久性的,也可能是暂时性的;既可能是突发失效,也可能是潜在失效。如果元器件彻底失效,在生产及品质管理中能够及时察觉并排除,则影响较小,而如果元器件只是轻微受损,在正常测试下则不易发现。另外,在运输途中,摩擦、碰撞、接触带有静电的物体也会产生静电,从而导致元器件受损,这种潜在的和突发的失效更难预防,其损失亦难以预测。
静电失效对电子产品的可靠性影响十分普遍,电子产品在设计与使用过程中必须做好静电防护措施。对电子元器件的选用也要考虑防静电要求。
2.静电敏感元器件的概念和分级
静电敏感元器件(Static Sensitive Devices,SSD)是对容易因静电放电而引起损伤的元器件的统称。为避免物料因不正当操作而导致静电损坏,需要在来料验收、储存、配送、预加工、焊接、组装过程中采用静电防护措施。
静电敏感等级分级如表3-14所示。
表3-14 静电敏感等级分级

注:静电敏感度≥16000V以上的元器件、组件被认为是非静电敏感产品。
常见静电敏感元器件的静电敏感等级分级,如表3-15所示。
表3-15 常见静电敏感元器件的静电敏感等级分级

3.静电敏感元器件选用要求
静电敏感元器件的选用与产品设计需要及工艺制程能力有关,不同制造单位对静电的控制能力不同,对电子元器件的静电敏感等级要求也不同。
① 一般情况下,选用元器件时,优选元器件静电敏感度等级在HBM Class 1B(500~1000 V)及以上级。
② 不推荐选用静电敏感度HBM Class 1A(250~500 V)的静电敏感元器件。
③ 限制选用静电敏感度HBM Class 0(0~250 V)的静电敏感元器件。
值得注意的是:对于所有静电敏感元器件的使用,产品设计过程中均应提供ESD保护,其中单板组件的静电防护能力应>2000V,整机产品的静电防护能力应>4000 V。具体要求见《GJB 1649电子产品防静电放电控制大纲》。
3.3.6 元器件包装要求
1.贴片元器件的包装要求
(1)一般片式阻容类元器件
优选编带包装元器件,可选托盘包装元器件,不推荐选用管装和散装元器件。
(2)IC芯片类元器件
优选编带包装元器件,可选托盘包装元器件,不推荐选用管装和散装元器件。
(3)存储器类IC元器件
优选托盘包装元器件,不推荐管装和编带包装元器件。
(4)军品航天散料
片式表面贴装元器件应放入防静电袋中,IC芯片应放入独立的托盘或专用的带有减振防护功能的防静电盒中。
(5)覆盖带
① 应确保其密封良好,覆盖带不能存在任何空洞和裂纹。
② 覆盖带应居于卷带中央位置,不能发生明显移位,严禁覆盖带因为位置偏移或尺寸过大而遮住圆形齿轮孔的任何部分。
③ 覆盖带应保证自身具有足够的抗拉强度,对于8mm卷带宽度的覆盖带,抗拉强度应不小于700g,对于12~32mm卷带宽度的覆盖带,抗拉强度应不小于1000g,对于44mm卷带宽度的覆盖带,抗拉强度应不小于1300g。
④ 覆盖带与卷带应保持合适的剥离强度,任何情况下覆盖带与卷带的最小剥离力不能小于10g,以保证在正常的运输、存储及生产过程中元器件不会脱离卷带。
(6)卷带
① 对于8mm的卷带,最大剥离力应小于100g,对于12~56mm的卷带,最大剥离力应小于130g,对于72mm及以上的卷带,最大剥离力应小于150g。
② 对于卷带,圆形齿轮孔必须位于进料方向的左边且不能存在错位。
③ 腔体与元器件之间应保证合适的间隙,不能因腔体过小导致取料困难,也不能因腔体过大导致元器件位置偏移过大或导致元器件翻转。
④ 腔体应具有足够强度,以保证在运输、存储和生产过程中不发生变形和破裂,进而避免元器件引脚变形和损伤。
⑤ 圆形齿轮孔尺寸的详细要求见EIA-418-C中的相关规定,腔体与元器件间间隙的要求为:8~12mm(0.5mm);16~200mm(1mm)。
(7)其他要求
① 覆盖带、载带应保证干净整洁、无污染、无纸屑等多余物。
② 包装标识应清晰可见,规格书中必须注明存储条件和存储时间。
③ 温度敏感、湿度敏感、静电敏感元器件应注明等级和使用要求。
2.插装及压接元器件的包装要求
① 包装应兼具防静电、防撞坏、方便取用的特点,优选管装或盘装形式。
② 包装与元器件间应保持合理间隙,必要时,采用防静电泡棉填充,以确保元器件在包装中不会晃动,且元器件引脚悬空。
③ 静电敏感元器件/潮湿敏感元器件的外包装上应贴有静电敏感标识/潮湿敏感标识。
④ 对于编带型插装元器件,应确保元器件引脚全部固定在编带上,以利于批量成型操作。
⑤ 所有外包装不应有严重的变形或压伤痕迹,否则拒收,外包装有轻微划伤但内包装不受损时可以接收。
3.3.7 其他工艺选型要求
电子元器件焊接完成后,还要进行清洗、检验。对于部分高可靠产品,还需进行三防涂覆和灌封、粘固操作,在选用电子元器件时,也应考虑相关要求。