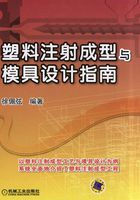
4.2 分型面和排气设计
注射模设计过程中,首先是合理确定分型面,往往是在模具结构设计的最后设置排气槽。排气系统主要利用分型面,排气槽大都开设在分型面上。在不能利用分型面排气时,必须熟知其他途径的排气设计。
4.2.1 分型面设计
在注射模具中,用于取出注塑件或浇注系统凝料的面通称为分型面。常见的取出注塑件的主分型面与开模方向垂直。主分型面将注射模分成定模和动模两部分,也有从主分型面取出并放回活动型芯,或放置嵌件。注射模有一个或多个分型面,还有采用与开模方向一致的侧向分型面。采用点浇口的双分型面的注射模,注塑件与浇道凝料分别从两个分型面中取出。分型面大都是平面,也有倾斜面、曲面或台阶面。
分型面的选择不仅关系到注塑件的正常成型和脱模,而且涉及模具结构与制造成本。在选择分型面时,应遵守以下原则。
(1)分型面应选择在注塑件的最大截面处 如图4-13a、图4-13c所示,否则,如图4-13b所示,无法脱模和加工型腔。无论注塑件以何方位布置型腔,都应将此作为首要原则。
(2)尽可能地将注塑件留在动模一侧 因为在动模一侧设置和制造脱模机构简便易行。为了让注塑件留在动模一侧,图4-14a将型芯设在动模的型芯上,薄壁注塑件对型芯产生有足够的包紧力;但是遇到厚壁塑件或者没有型芯,如图4-14b所示,可将注塑件型腔设在动模一侧的型腔里。
图4-13 分型面应选在注塑件的最大截面处
a)分型面在注塑件的最大截面处 b)最大截面在型腔内 c)箭头所指为分型面
(3)有利于保证塑件的尺寸精度 图4-15a为保证双联齿轮的齿廓与孔的同轴度,两齿轮型腔和型芯都设在动模一侧;若分设在动模与定模两侧,见图4-15b。会受到导柱与导套配合精度及它们磨损的影响。又如图4-16a所示,为了保证注塑件两台阶间距尺寸L的精度,应将两台阶面置于模具同一侧;否则如图4-16b布置,尺寸L精度受到分型面制造精度和锁模力的影响,会引起较大误差。
图4-14 注塑件应尽可能留在动模一侧
a)注塑件留在动模的型芯上 b)注塑件留在动模的型腔里
图4-15 有利于保证注塑件的同轴度
a)两齿轮都设在动模同一侧 b)两齿轮分别设在动模和定模两侧
(4)有利于保证注塑件的外观质量 分型面上型腔壁面稍有间隙,熔体就会在注塑件上产生飞边。飞边影响注塑件的外观质量。因此在光滑平整表面或圆弧曲面上,应尽量避免选择分型面,如图4-17a所示。而图4-17b的选择显然不当。
(5)考虑满足注塑件的使用要求 注塑件在模塑过程中,有一些很难避免的工艺缺陷,例如脱模斜度、分型面上的飞边以及顶杆与浇口痕迹等。在分型面设计时,应从使用角度避免这些工艺缺陷影响塑件功能。如图4-18b所示,塑件完全在动模一侧脱出,会使脱模斜度过大。图4-18a分别在动模、定模安排型腔,可减小脱模斜度。又如图4-19b上的注塑件轴需与圆孔支撑,或轴上传动零件的孔有配合要求,但分型面飞边痕迹会影响运转功能;若如图4-19a在有飞边两侧,留有与圆孔的单边间隙0.15~0.25mm,便不会影响其转动。
图4-16 有利于保证注塑件尺寸精度
a)两台阶置于动模一侧成型 b)两台阶由动模和定模分别成型
图4-17 有利于保证注塑件外观质量
a)圆弧曲面由型腔成型 b)圆弧曲面上设置分型面
图4-18 有利于减小注塑件的脱模斜度
a)分别在动模和定模脱模,脱模斜度小 b)在动模一侧脱出,脱模斜度大
图4-19 有利于保证塑料轴的转动功能
a)飞边处在有间隙孔中 b)转轴柱面上会有飞边
(6)注塑件在主分型面上的投影面积应小于所用注射机的成型面积 减小注塑件在合模平面上的投影面积,可减小所需锁模力。如图4-20所示的弯角板块类注塑件,图a的选择比图b为好。但是按图a布置后模具的闭合高度较大。
(7)长型芯应置于开模方向 当注塑件在相互垂直方向都需设置型芯时,如图4-21a所示,将较短型芯置于侧抽芯方向,有利于减小抽拔距,因为侧向分型抽芯机构的抽拔距较小;若按图4-21b布置,需要尺寸很大的斜导柱抽芯机构。
(8)有利于排气 应将分型面置于熔体充模流动的末端,如图4-22a所示;而图4-22b所示熔体溢料面与分型面垂直,熔体不能从分型面溢出。注塑件在压缩中成型,虽然翻边壁厚的尺寸精度高,但不能利用分型面排气。又如图4-23a所示,料流的末端气体可利用分型面排气;而图4-23b所示,气体会在型腔中积聚。
图4-20 有利于减小注塑件在合模平面上的投影面积
a)注塑件在分型面上的投影面积小 b)成型注塑件需较大的锁模力
图4-21 较长型芯应置于开模方向
a)长型芯设在开模方向 b)长型芯设在侧抽方向
图4-22 分型面应有利于排气
a)利用分型面排气 b)不能利用分型面排气
图4-23 料流的末端排气
a)利用分型面排气 b)气体在型腔中积聚
(9)应有利于简化模具结构 为此在安排制件在型腔中方位时,尽可能避免侧向分型或抽芯。特别是避免在定模部分侧向抽芯,如图4-24所示。图4-24a布置方位可避免侧向抽芯,模具结构比图4-24b简单。
(10)非平面分型面的选择,应有利于型腔加工和方便脱模 图4-25、图4-26和图4-27中的倾斜面、曲面和阶梯面分型面,用磨削加工使动模与定模密配是不可能的,常采用电火花对合加工。
图4-24 应有利于简化模具结构
a)模具简单 b)需侧向抽芯
图4-25a所示斜面分型时型腔加工方便。图4-26所示曲面分型时,孔的成型和壳体的脱模方便。图4-27a所示平面分型需侧向抽芯。图4-27b阶梯面分型需异形型芯成型孔,阶梯分型面加工困难。
图4-25 斜面分型
a)斜面分型使型腔加工方便 b)分型面加工方便
图4-26 曲面分型
图4-27 阶梯面分型
a)平面分型需侧向抽芯 b)阶梯面分型需异形型芯
设计非平面分型面时,应注意模具侧向的力平衡,如图4-27a那样。如图4-28b所示,由于型腔布置对开模方向的不对称,注射时动模与定模间存在侧向作用力,不利于开模和脱模。若由于注塑件的几何尺寸限制不能作图4-28a那样的平衡设计,则应设有粗壮的导柱并加装锥面斜面定位机构。
图4-28 非平面分型时模具侧向的力平衡
a)侧向作用力被平衡 b)动模与定模受到侧向作用力
注射模有些模板之间的分离运动,并没有注塑件或流道凝料取出。例如:动模上的推件板被脱模推杆顶离动模;定模上的脱卸板将主流道和分流道凝料推离定模。但都没有对注塑件或流道分型。对于一些特殊注塑件,分型面设计是困难的技术问题。由于涉及制品的几何尺寸精度和质量,分型面选择后应得到注塑件设计人员的认可。
4.2.2 排气设计
从某种角度而言,注射模也是一种置换装置。即塑料熔体注入模腔同时,必须置换出型腔内空气和从物料中逸出的挥发性气体。排气系统是注射模设计的重要组成部分。本节详细讨论该计算式的推导过程和物理条件,可供实用计算时参考。
1.排气设计
(1)排气不良的危害 排气和排气槽设计不合理,将会产生下述的弊病:
1)增加熔体充模流动的阻力,使型腔不能充满,会使注塑件棱边不清。
2)在制品上呈现明显可见的流动痕和熔合缝,其力学性能降低。
3)滞留气体使注塑件产生银纹、气孔、剥层等表面质量缺陷。
4)型腔内气体受到压缩后产生瞬时局部高温,使塑料熔体分解变色,甚至碳化烧焦。
5)由于排气不良,降低了充模速度,增长了注射成型周期。
越是薄壁制品、越是远离浇口的部位,排气槽的开设越重要。对于小型精密制品的注射成型也要重视排气设计,因为除了能避免制品的注射量不足和表面灼伤外,还可以消除各种缺陷。对于几何形状复杂的制件,模具上排气槽的开设在试射后确定。
(2)排气系统设计方法
1)利用分型面排气是最简便的方法,排气效果与分型面的接触精度有关。减少实际锁模面有利排气。利用模块结构,可减小锁模接触面,但锁模接触面的宽度不能低于15mm。
2)利用顶杆与孔的配合间隙排气,必要时对顶杆作些排气的结构措施,如图4-29所示。对于型腔的封闭死角,可增设推杆作排气用。推杆排气隙的长度为2~3mm,开设排气槽和沟。推杆与孔的配合长度不小于10mm,或为推杆直径的2~3倍。顶端利用推管同样也能排气,其排气结构如图4-30所示。型芯也被利用排气,其排气结构如图4-31所示。以上三图中图示单向间隙δ可为表4-1所列的常用排气槽高度h的一半。排气通道表面顺气流方向抛光,无锐角。
3)利用球状合金颗粒烧结块渗导排气,如图4-32所示。透气钢块应有足够的承压能力,设置在注塑件隐蔽处,并须开设排气通道。透气钢的透气效果与厚度成反比,钢块的排气方向厚度30~50mm。但透气钢块的强度和刚度较低,既要有足够截面的排气坑,又要有较好支承。图4-33a所示透气钢块的刚性差,透气途径长。改用图4-33b的高强度钢支承又作大面积透气。透气钢块的成型面和出气底面的精加工,只能用电火花成型。透气钢硬度为35~38HRC,可以机械切削加工。用脱模剂之类的液体涂在透气钢块的工作面上,从底面吹入压缩空气,检查气泡涌起。如果透气钢块阻塞,可以清洗后再用。将透气钢块加热至500℃,保持1h,冷却后浸入丙酮至少15min,然后用压缩空气吹出残渣。如效果不好,重复加热、溶渣和吹气。
4)在熔合缝位置开设冷料井,在贮留冷料前也滞留了少量气体。也有在锁模分型面上,挖贮气小坑,引留少量气体。
图4-29 兼排气的顶杆
图4-30 兼排气的推管
图4-31 兼排气的型芯
图4-32 烧结金属块渗导排气
图4-33 透气钢块的排气设计
a)排气效果差 b)排气坑效果好
5)可靠有效的方法,是在分型面上开设专用排气槽,如图4-34所示,尤其大型注射模必须如此。排气槽通常设在分型面的动模一侧,应开设在熔体最后充满的部位。图4-34为单个侧浇口的型腔,排气槽大致设在浇口对面。排气槽截面尺寸,既要有利于排气,又要不溢料。因此,对于黏度较低的塑料熔体应有较小的排气槽高度h,见表4-1。高压塑料熔体冲着排气隙口,熔体容易溢进排气槽。因而,熔料在排气槽隙口垂直流过时,排气槽高度h和排气隙δ容许稍大些。
排气槽流通截面S,应按所需排气量由式(4-26)确定,然后计算得排气槽宽度W和槽的数目。槽宽度W取2~6mm,优选了3.2~5mm。气流方向的排气槽长度L取1~2mm,一般不超过2mm。排气槽表面应顺气流方向进行抛光。排气槽后续的导气沟应适当增大,以减小排气阻力。其高度h′=0.8~1.6mm,单个宽度W′≥W=3.2~5mm。分型面上排气沟为梯形或半圆截面,优选梯形截面,以便于清除溢进的塑料。圆筒形注塑件,在采用中央浇口时,应在分型面的型腔周围均匀布置排气槽,并设置环形的导气沟。
6)对于大型模具,可利用镶拼的成型零件的缝隙排气。图4-35所示为点浇口设计的浇口套镶件排气间隙和环形导气沟。
图4-34 开设专用排气槽和导气沟
图4-35 绕口套镶件排气间隙和环形导气沟
1—浇口镶件 2—型腔板 3—推板 4—动模型芯 5—环形导气沟
表4-1 常用的排气槽高度
排气槽的表面、推杆和镶块的排气间隙,在注射生产时会留下塑料的残余物。污垢会堵塞排气截面。压缩空气可在每次开模时吹去污物。可动零件上的排气槽和排气隙有一定的自我清理能力。紧固型芯和镶块上的排气间隙上污物清理困难,要设计清理的通道,后续的排气沟的截面要足够大。
2.排气槽的截面尺寸计算
塑料熔体注射充模时,型腔内气体被压缩成气室,然后经排气口喷出。
(1)气体压缩 注射模排气过程的第一阶段,是充模的高温塑料熔体将型腔内气体驱赶压缩至死角,形成一个高温高压的气室。此阶段既不是等温过程,也不是绝热过程,而是气体动力学的多方过程理想气体的多方过程中,压力p和体积V的关系满足下式:
p·Vn=恒量 (4-10)
n称多方指数,n=1时为等温过程,n=γ=1.4时为绝热过程。此气室的状态是第二阶段排气槽喷排气体时的初始条件。许多设计理论,均按照临界的有效排气来计算排气槽的截面积。此气室的温度和压力,应根据注射工艺确定。此气室处于熔体料流的末端,压力p=20MPa,被压后气体温度T升高至300℃左右。此时气室中气体可能分解和烧焦塑料物料。有危害状态的多方指数为
式中 V0——包括浇注系统在内的型腔总体积;
p0——原型腔内具有的标准大气压(p0=0.1MPa);
V——被压缩气室的体积,拟定为V0的1%。
被压气室的温度,由多方过程
得到
模内气体从20℃经压缩升温达311℃。若按系统不与外界交换热量的绝热过程计算,则被压气室温度还要高得多。介于等温和绝热过程之间的多方过程是符合注射充模实际的。这里存在误差,在形成气室前,模具中的排气槽是开放的。但由于气压低、充模快,先期被排出的气体不多,由上述假定推算的气室温度和压力比实际要偏大些。
(2)排气槽的喷射 推导的第二阶段,把排气槽视为喷气管。由于排气过程迅速,来不及与外界有明显的热量交换,因此作为绝热过程处理。有参量比热容比
γ=cp/cv (4-14)
式中,cp为定压比热容,cv是定容比热容,对于空气γ=1.4。根据气体动力学的流量函数所述,喷管的质量流量称为密流m′,单位截面积A的密流有
m′/A=ρv (4-15)
式中,v为喷管的排气流速,气体密度
ρ=ρ′/(RT′) (4-16)
又有喷管排气的音速公式,音速为
以上式(4-16)和式(4-17)中,气体常数R=287.04J/(kg·K);T′为喷管中气体的热力学温度;p为喷管中气体的压力,代入式(4-15)后得
其中ν/a=M称为马赫数。前述T和p为第一阶段所生成气室的滞止温度和压力。此时气体的动能完全转化为热焓的滞止状态。根据能量守恒关系,它们与喷管中气体的温度T′和压力p′有以下关系
代入式(4-18)后,可得
在M给定的情况下,气体密流m′与滞止压力p成正比,与滞止温度T的平方根成反比。如果滞止的压力p给定,密流m′只是M数和γ、R的函数。
如果气流的M数达到1,出现临界密流,对应着喷管的临界面积A,有
用γ=1.4,R=287J/(kg·K)代入后,得排气槽截面积的计算式
密流m′用常温常压下型腔体积V0和空气密度ρ=1.16kg/m3代入,用注射充模时间t计算:
m′=m/t=ρV0/t (4-24)
再用气室的高温T=584K和高压p=20MPa=20×106 N/m2,代入式(4-22),得到排气槽截面积的设计计算式:
上式中A(m2或cm2)与V0(m3或cm3)的单位一致。为计算方便,型腔体积V0用cm3代入,截面A单位是mm2,于是有
式中 A——排气槽的截面积(mm2);
V0——包括浇注系统的型腔体积(cm3);
t——注射充模时间(s)。
式(4-26)计算关键是充模时间的正确估测。建议按第8章的表8-1注射机公称注射量与注射时间,根据模具实际型腔体积VO来确定t。
(3)计算修正 考虑到有些塑料品种的热分解温度高于或低于前假定TK=584K,可对式(4-25)进行气体温度的修正
于是物料分解温度TK修正的排气槽截面积的计算式为
当某种物料的热分解温度较低,TK小于584K时,则计算得到截面积A会略大些,以避免熔体被烧焦。同样,式(4-27)中的V0和A量纲是一致的。
对式(4-26)和式(4-27)的计算结果,常见的修正意见有:
1)当注射模有顶杆、分型面等其他排气通道时,截面积A可斟酌减小;
2)排气槽长期使用后有积垢,会减小有效截面积,A可略大些。
[例]有型腔体积V0=100cm3的模具开设排气槽。参考表8-1,取充模时间t=1.5s。求排气槽截面尺寸。
[解]由式(4-26)得排气槽面积
再由表4-1,按塑料物料取排气槽高度h=0.02mm,高度h的制造公差为±0.005mm。排气槽总宽度11.5mm,单个排气槽宽度4mm,需三个排气槽,排气方向的长度取1.5mm。
随着高速注射的发展,真空排气系统将被采用。在如图4-32所示的烧结金属块后侧,配以真空抽气。以上陈述的是热塑性塑料注射模的排气系统。热固性塑料注射模的排气系统更为重要。排出气体质量中需计入化学反应产生的气体质量。