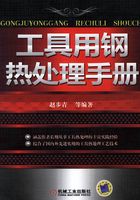
3.1 渗碳及碳氮共渗
渗碳是目前机械工业中应用最广泛的一种化学热处理方法。其工艺特点是将低碳钢或低碳合金钢工件置于能增碳的活性介质(渗碳剂)中加热到渗碳温度,并保持一定的时间,使碳原子渗入工件表面层,继而进行淬火并低温回火,使工件表面与心部具有不同的成分、组织和性能。按渗碳介质的物质状态,渗碳方法可分为气体渗碳、液体渗碳、固体渗碳、离子渗碳、真空渗碳及流态床渗碳等,最常用的方法是气体渗碳。几种渗碳方法的特点及其应用范围如表3-1所示。
表3-1 常用渗碳方法的特点及其应用范围
(续)
工具的碳氮共渗是在工具表面层同时渗入碳和氮的热处理过程,与单一的渗碳相比,碳氮共渗有许多优点。例如,碳氮共渗温度较渗碳温度低,因而渗碳过程奥氏体晶粒小,共渗后一般可直接淬火,因而节能、变形小。
3.1.1 钢的渗碳
1.渗碳工艺参数
1)渗碳介质的化学成分及渗碳气氛特性 渗碳介质的成分与渗碳气氛的碳势、碳传递系数和可用碳等特性有关。其中,碳势是炉中气氛渗碳能力的表征,碳传递系数的大小反映了渗碳气氛的渗碳速度。
2)渗碳温度 常用的渗碳温度为920~940℃。温度越高,渗速越快,渗层越深;但温度过高会引起奥氏体晶粒长大,降低工件的力学性能,增大工件淬火畸变,还会降低渗碳设备的使用寿命。渗碳的温度选择根据要求的渗层深度(δ)来确定:δ=0.3~0.6mm,870~890℃;δ=0.6~0.8mm,890~910℃;δ=0.8~1.2mm,920~930℃。
有的要求深层渗碳或缩短渗碳周期,可采用1030~1050℃快速渗碳,但必须选用细晶粒钢、高温渗碳钢或渗碳后再经循环热处理细化晶粒。
3)渗碳时间 渗层深度确定之后,所需的渗碳时间可根据渗碳介质的碳势、渗碳工艺方式、渗碳温度和渗碳用钢等因素,利用扩散方程来计算。近似计算多采用Harris公式:
式中δ——渗层深度(mm);
t——渗碳时间(h);
T——渗碳温度(K)。
几种常用渗碳温度的渗碳层深度(mm)计算式可以简化为;870℃,;900℃,
;925℃,
。
不同温度下气体渗碳的速度(平均值)见表3-2。
表3-2 不同温度下气体渗碳的速度
渗碳过程总时间亦可按下式估算:
τ=δ/v式中τ——渗碳过程的总时间(h);
δ——要求的渗碳层深度(mm);
v——平均渗碳速度(mm/h)。
2.气体渗碳
采用有机液体或气体碳氢化合物作为渗碳剂,它们在高温炉中形成含CO、H2、CH4、少量CO2、CmHn和水蒸气的气体,使钢在高温下和渗碳介质发生如下渗碳反应:
(1)渗碳气氛特性 通常衡量渗碳的实际效果和质量的指标是渗碳层深度、钢件表面碳含量及碳浓度梯度、渗层及心部的组织等。
渗碳层深度、表面碳含量以及碳浓度梯度都与渗碳气氛的特性有关。这些特性包括碳势、碳传递系数和可用碳等。
碳势是在给定温度下,奥氏体状态的钢件与炉中气氛达到动态平衡时,钢件表面的实际碳含量。碳势是炉内气氛渗碳能力的表征,也是渗碳重要的工艺参数。
碳传递系数是表示碳从渗碳气氛中传入钢表面的传递速度,用β表示。传递速度β值的大小反映了渗碳气氛渗碳速度的快慢;β值随φ(CO)%与φ(H2)%的乘积而变化,乘积大则渗速快。
可用碳是指单位气体可提供碳的质量。
(2)气体渗碳设备 该设备分周期式和连续式两大类。周期式主要有井式、卧式和旋转罐式三种。连续式气体渗碳炉有推杆式、网带输送式、转底式及振动式等。
(3)气体渗碳碳势的自动控制 影响碳势的因素很多,如CO2、H2O、CH4、CO、H2的分压,炉温,炉内总压力,被处理工件中合金元素含量和炉子结构等。在碳势控制系统中,若选取较大的一个自变量作为碳势的控制量,其他次要的影响因素作为恒量来处理,这种控制系统统称为单参数控制系统,所需设备简单,成本低,但控制精度较低。若选用两个或三个较大的自变量作为控制量来控制碳势,则称为双参数或三参数控制系统,设备复杂,控制精度高。渗碳可控气氛常用分析方法及特点见表3-3。
表3-3 气体渗碳可控气氛常用分析方法及特点
通常可用露点仪、CO2红外线或氧探头等作为检测元件组成单参数控制系统。图3-1所示为在RQ3-75-9型炉中滴注式可控气氛渗碳工艺。
图3-1 在RQ3-75-9型炉中滴注式可控气氛渗碳工艺
(4)气体渗碳介质 常用的气体渗碳介质见表3-4。
表3-4 常用气体渗碳剂
(续)
3.滴注式气体渗碳
滴注式气体渗碳一般是把含碳有机液体滴入(或注入)气体渗碳炉内,使之受热裂解,产生渗碳气氛,对工件进行渗碳。
(1)有机液体渗碳剂 有机液体渗碳剂的品种多,在使用时应考虑以下要求:
1)有机液体加热分解后,产生的气体体积应大(即产气量大)。表3-5列出了几种常用有机液体渗碳剂的产气量。
2)有机液体的分子式中,碳与氧的原子数之比应大于1,才可能在渗碳过程界面反应中析出活性碳原子,碳氧比(碳原子数与氧原子数之比)大,析出的活性碳原子就多。
3)产生1g活性碳原子(12g)所需的有机液体的质量称为碳当量。碳当量小,在渗碳时所消耗的有机液体滴量少。几种常用有机液体渗碳剂的产气量与碳当量列于表3-5。从碳当量来看,渗碳能力的顺序是:丙酮>异丙醇>醋酸乙酯>乙醇>甲醇。
4)气氛中CO和H2的含量应稳定,因为在可控气氛渗碳时,无论用CO2红外仪、露点仪或氧探头单参数控制炉气碳势时,都是以炉气中的CO和H2的含量不变为前提。表3-6所示为几种渗碳剂在920℃时炉气组分的变化。
由表3-6可以看出,以炉气中CO与H2不变为依据,丙酮、醋酸乙酯、2#渗碳油及醋酸乙酯+甲醇、2#渗碳油+甲醇等是比较理想的渗碳剂。
5)价格便宜,货源丰富,采购方便。
表3-5 几种常用有机液体渗碳剂的产气量与碳当量
①煤油成分、结构不定,是大分子烷烃混合物CnH2n+2,其中n=6~19。
表3-6 几种渗碳剂在920℃时炉气组分的变化
注:连续时间260~280min。
(2)滴注式气体渗碳气氛的碳势 炉气的碳势直接影响渗碳质量,而炉气的碳势取决于有机液体的组成、分解温度及滴入量。液滴的组成用碳氧比(C/O)表示。调节炉气的碳势,可以通过改变滴量或改变渗剂种类、比例来达到。渗碳温度、渗碳时间对渗层深度有明显的影响,在工艺范围内,渗碳温度越高,渗层越深;渗碳时间越长,渗层越深。但对不同的渗碳用钢,效果有点差异。
(3)滴注式气体渗碳工艺 为了加快渗碳速度,提高渗碳质量,往往采用复合渗碳剂。甲醇+煤油(或丙酮)井式炉滴注式渗碳工艺参数见图3-2和表3-7。
图3-2 20CrMnTi钢工件在RJJ-35井式炉滴注式渗碳和淬火工艺
注:渗碳层深度为0.8~1.2mm。
表3-7 甲醇+煤油井式炉滴注式渗碳工艺
注:1.滴量为每100滴400ml。
2.渗碳温度为930℃。
有的工厂仍用滴煤油进行气体渗碳。图3-3所示为20Cr、20CrMnTiA钢制模具渗碳淬火工艺,渗碳层深度要求1.10~1.30mm。
上述渗碳过程包括:排气、强烈渗碳、扩散及降温淬火四个阶段。
图3-3 井式炉气体渗碳工艺
1)排气。模具入炉后必将引起炉温的下降,同时带入大量空气。排气阶段的作用在于恢复炉温到规定的渗碳温度。在此阶段应尽快排除炉内的空气,通常采用加大渗剂滴量以使炉内氧化性气氛迅速减少。排气时间往往在仪表温度达到渗碳要求的温度后尚需延长30~60min,以使炉气成分达到要求,并使炉内温度均匀及工件透烧;排气不好会造成渗碳速度减慢,质量不合格等缺陷。
2)强烈渗碳。排气阶段结束后,立即进入强烈渗碳阶段。其特点是渗碳剂滴量较多或气氛较浓,使工件表面碳浓度高于最终要求,增大表面的碳浓度梯度以提高渗碳速度。强烈渗碳时间主要取决于模具对渗碳层的要求。
3)扩散。此时炉气渗碳能力降低,表层过剩的碳继续向内部扩散,最后得到要求的深度及合适的碳浓度分布。扩散阶段所需时间由试棒的渗碳层深度确定。
4)降温淬火。渗碳后的冷却,对于直接淬火的零件应随炉冷至适宜的淬火温度(一般为840~860℃),并保温15~30min,使工件内外温度均匀并出炉淬火;对于需要重新加热的模具,可自渗碳温度出炉放入缓冷罐中缓冷。
气体渗碳操作要点:为了保证渗碳质量,工件在进入渗碳炉前应清除表面污垢、铁锈及油脂等。常用热水或Na2CO3水溶液清洗,对锈蚀工件应作喷砂处理。
工件装在料筐或挂具上,彼此间应留5~8mm空隙,以保证渗碳介质与工件充分接触和循环流通。
渗碳炉密封性要好,并保证炉内气氛为正压力(一般为20~60mm水柱高)。风扇应始终运转,以使工件能经常与新鲜气氛接触。排气口要点燃,以免废气污染了空气,还便于观察判定炉内的工作情况。有条件的单位,应经常进行炉气分析。根据生产经验,用煤油渗碳时,炉内气氛(体积分数)应控制在下列范围:CnH2n+2:1%~1.5%;CnH2n≤0.6%;CO:20%~35%;H2:50%~65%;CO2≤0.5%;O2≤0.5%;N2余量。
在这种气氛下对20CrMnTi等钢种渗碳后的表层碳的质量分数为0.80%~1.2%,而且炭黑很少。渗碳件出炉时间根据随炉试样的层深检查结果决定,试样材料应与工件材料相同,最好为同炉号之材。对于不同钢种、渗层深度要求不一者不宜同炉共渗。
另外,对新炉罐、新的工夹具或未用过的炉罐应预先渗碳。在正常生产情况下,停炉再升温时也应进行炉腔渗碳。
渗碳只能改变工件表面的化学成分,而工件表面的最终强化则必须作适当的热处理。经过热处理使工件的高碳表面层获得细小的马氏体、适当的残留奥氏体和弥散的粒状碳化物;而工件的心部由低碳马氏体、托氏体、索氏体等组织组成。渗碳后可采用不同的热处理方法:直接淬火、一次淬火、二次淬火等。
①直接淬火。直接淬火是指工件渗碳后随炉降温或出炉预冷到高于Ar1或Ar3温度(760~850℃),然后直接淬火的方法,淬火后低温回火。
随炉降温或出炉预冷的目的是为了减少淬火应力,从而减少工件的变形。同时,还使高碳的奥氏体中析出一部分碳化物,降低奥氏体中的碳浓度,从而减少淬火后残留奥氏体量,获得较高的表面硬度。
直接淬火的优点是:减少加热和冷却次数,使操作简化,生产效率高,还可以减少淬火变形及表面氧化、脱碳倾向。直接淬火适用于20CrMnTi等本质细晶粒钢,不适用于本质粗晶粒钢及渗碳时表面碳浓度高的零件。
②一次淬火。工模具零件渗碳后立即出炉或降温到860~880°C出炉,置于冷却坑内冷却至室温,然后重新加热淬火。本工艺适用于本质粗晶粒钢工件,以及渗碳后不宜直接淬火的工件。
③两次淬火。对本质粗晶粒钢或使用性能要求很高的工件,要采用两次淬火,或一次正火加一次淬火,以保证工模具心部和渗层都能达到高的性能要求。第一次淬火(或正火),碳钢的加热温度为880~900℃,合金钢为850~870℃,目的是细化心部组织,并消除表面网状碳化物。第二次淬火则根据高碳的表面来决定,一般选择在稍高于Ac1的温度(770~820℃)。
两次淬火有可能出现较大的淬火缺陷,工艺较复杂,生产周期长。故仅用于表面耐磨性和疲劳强度及心部韧性等要求较高的重载荷工件。
4.吸热式气氛渗碳
(1)吸热式渗碳气氛 在连续式炉或密封箱式炉中进行气体渗碳时,常采用吸热式气体加富化气作为渗碳气氛。富化气可以使用甲烷或丙烷。吸热式气氛的组成见表3-8。炉气的主要成分是CO、N2、H2、CO2、H2O、CH4,其中N2是中性气体,起稀释作用。
表3-8 气体渗碳几种吸热式气氛组成
(2)吸热式渗碳气氛的碳势 渗碳层表面碳含量与碳的浓度梯度决定炉气中的碳势、钢表面的界面反应速度、渗碳温度与时间及钢中合金元素等因素。
5.氮基气氛渗碳
以氮气为基体,加入少量的碳氢化合物(如CH4、C3H8)及含氧介质空气(或CO2),直接通入炉内,在高温时,碳氢化合物与空气中的氧或CO2发生反应,生成CO和氢及少量的CO2和水蒸气,即可形成渗碳气氛,氮气为载体气。
氮基气氛渗碳的机理和传统的气体渗碳是一致的。其渗速和渗碳质量也是相当的,然而氮基气氛具有节省能源、气源丰富,安全经济和适用性广的优点。氮基渗碳气氛组成见表3-9。
表3-9 氮基渗碳气氛和吸热式气氛的组成
(续)
氮基渗碳气氛中,氮气的稀释虽然降低了气氛中CO含量,但同时也降低了脱碳性组分CO2和H2O的含量。为了使氮基渗碳气氛具有足够的碳传递系数和可用碳,炉气中CO的体积分数不应低于15%。
用甲醇、乙醇裂解气和氮气制备的氮基渗碳气氛,是一种简单易行的新途径。可采用甲烷(CH4)或丙烷(C3H8)作富化气,也可采用丙酮或醋酸乙酯的裂解气作为富化气制备氮基渗碳气氛代替吸热式气氛,省去吸热式气氛的发生装置,并可使滴注式气体渗碳法推广到连续式渗碳炉的大批量生产中。
为了提高气体渗碳的速度,在渗碳介质中加入稀土元素,可以提高炉气碳势和界面碳传递系数,对碳在渗层奥氏体中的扩散没有明显的影响。氮基气氛含水蒸气少,碳势的控制不宜采用露点仪,当炉气中φ(N2)>70%时,也难用CO2红外仪进行碳势控制,最好用氧探头控制。
气体渗碳的防渗 有些不需强化的部位以前往往采取镀铜,近年来采用防渗涂料,效果尚可。北京、山东、浙江黄岩、杭州等地均有售。理想的涂料应满足以下三点要求:①涂料的工艺性要好,不结块、不变质,容易搅拌,容易涂敷,无毒和不易燃烧;②涂料防渗效果好,来源广泛;③防渗涂料在热处理时容易清除。气体渗碳防渗涂料配方及使用方法见表3-10。
气体渗碳的安全防护 进行气体渗碳时,应采取安全措施。有些气体有毒,且易燃,应知道渗碳气氛中CO、H2和CH4在空气中可以点燃的含量范围[如φ(H2)4%、φ(CO)12.5%]和最低的点燃温度(如H2、CO是595℃)。为了预防发生爆炸的危险,渗碳气体通入炉内时炉温必须高于760℃。没有点燃的炉气或来自发生炉的气体不允许在室内排放,必须严格遵守渗碳炉的操作规程和安全防火规则。
表3-10 气体渗碳防渗涂料配方及使用方法
注:市场还有合成的防渗涂料出售。
6.固体渗碳
将工件放在填充粒状渗碳剂的密封箱中进行渗碳的工艺称为固体渗碳。渗碳剂由供碳剂和催渗剂等组成。常用的固体渗碳剂的配方及使用见表3-11。
表3-11 常用固体渗碳剂的配方及使用
(续)
目前国内固体渗碳剂已经商品化,多制成粒状,按粒度分成6种,按活性分成强、中、弱3种,技术要求见JB/T 9203—2008《固体渗碳剂》。
固体渗碳的典型工艺如图3-4a所示,对于细晶粒钢可采用图3-4b所示工艺。为了缩短生产周期,提高渗碳速度,可采用高温渗碳或强催渗剂渗碳。
图3-4 固体渗碳工艺
a)普通渗碳 b)分级固体渗碳
固体渗碳温度、时间和渗层深度之间的关系见表3-12,不同牌号材料固体渗碳时渗层深度和保温时间的关系见表3-13。
表3-12 固体渗碳温度、时间和渗层深度之间的关系
表3-13 不同牌号材料固体渗碳时渗层深度和保温时间的关系
膏剂渗碳属于固体渗碳,是指工件表面以膏状渗碳剂涂覆进行渗碳的一种工艺方法。此工艺适用于单件生产或修复渗碳和局部渗碳。几种膏剂渗碳的配方及使用效果见表3-14。膏剂渗碳温度、时间与渗层深度的关系见表3-15。
表3-14 几种膏剂渗碳的配方及使用效果
(续)
表3-15 膏剂渗碳温度、时间与渗碳层的关系
7.液体渗碳
在熔融盐浴渗碳剂进行渗碳的工艺称为液体渗碳,又称盐浴渗碳。几种液体渗碳的配方及其使用见表3-16。
表3-16 液体渗碳配方及其使用
(续)
①603渗碳剂成分(质量分数):5%NaCl、10%KCl、15%Na2CO3、20%(CH2)2CO、50%木炭粉(100目)。
渗碳层薄及变形要求严格的工件,采用较低的渗碳温度,反之,则选用较高的渗碳温度。
液体渗碳剂有些含有剧毒氰盐,可能造成严重的环境污染,不符合节能减排大方向,但由于液体渗碳工艺设备简单,操作方便和产品质量稳定等优点,特别是处理温度低,时间短,变形小等长处,因此在有些轻纺机械等工业生产中仍有应用,但对含有大量氰化物的工艺,应尽早淘汰与禁用。
液体渗碳操作要注意安全,未经烘干的工件或工夹具不允许放入高温盐浴中。盐浴“老化”后,要及时调整,补充新盐。新盐必须烘干后才可加入。
8.离子渗碳
在低于一个大气压的渗碳气氛中,利用工件(阴极)和阳极之间产生的辉光放电进行渗碳的工艺,称为离子渗碳。
离子渗碳的原理与离子渗氮相似,工件渗碳时所需的活性碳原子或离子,不仅像常规气体渗碳一样利用热分解反应,而且还利用辉光放电时在阴极(工件)位降区中工作气体的电离而获得。以渗碳介质丙烷为例,它在离子渗碳中的反应过程如下:C3 H8
式中C——表示活性碳原子[C]和碳离子(C+)。
离子渗碳具有一系列优点,比常规气体渗碳乃至真空渗碳都优越。对于承受重载的高精度的重要零件或要求碳含量高的渗碳和深层渗碳,尤为适用。
离子渗碳所用的供碳剂,主要是碳氢化合物气体,如甲烷、丙烷、石油液化气,并通入氢气或氮气稀释;也可采用丙酮、乙醇或丙酮+甲醇等有机液体,用负压方式吸入炉内,但这种供碳方式往往不太稳定,最好将其在炉外气化并经储气罐稳压后再通入炉内。
离子渗碳设备有卧式、立式和连续式三种。大多数采用电阻加热与辉光放电加热的组合加热炉型,即在真空渗碳炉的基础上加一套高压直流辉光放电装置、且带淬火室的双室炉。离子渗碳温度、时间与渗层深度的关系如表3-17所示。
表3-17 离子渗碳温度、时间与渗层深度的关系(单位:mm)
9.真空渗碳
在低于一个大气压的条件下进行高温气体渗碳的工艺称为真空渗碳。和普通气体渗碳相比,真空渗碳有以下特点:
1)可以在较高温度(980~1100℃)下渗碳,真空对工件表面有净化作用,有利于碳原子被工件表面吸附,因而真空渗碳可以加快渗碳过程。
2)真空条件下渗碳,表面不脱碳,不产生晶界氧化,有利于提高工件的疲劳强度。
3)可直接将甲烷、丙烷或天然气通入真空炉中渗碳,无需增加气体制备设备。
4)对于有不通孔、深孔、狭缝的零件,或不锈钢、含硅钢等普通气体渗碳效果欠佳甚至难以渗碳的工件,真空渗碳都可以获得良好的渗碳层。
5)真空渗碳的耗电量仅为普通渗碳的几分之一或十几分之一。
6)对周围环境基本上无污染。
真空渗碳操作过程及具体要求如下:
1)工件的清洗。用专用清洗剂配制的溶液对欲渗碳件进行清洗,去除表面的油污、乳化液及脏物,同时也将工装夹具等清理干净,以防炉膛内吸附过多脏物而影响渗碳效果。
2)工件的摆放和装炉。将洗净的工件摆放在渗碳工装上,不允许多层堆放,布局应合理,以利于炉内渗碳气氛的循环。
3)升温。关闭炉门,开启机械泵和增压泵抽真空,达到要求的真空度后,送电加热工件,同时继续抽真空,使炉内真空度保持在一个稳定的范围内。
4)均温。炉温达到渗碳温度后,要保持一段时间,使炉内工件各部位的温度都均匀一致,以保证渗碳的均匀性。其加热系数按1h/25mm(≤955℃)计算;在955℃以上加热时,均温时间可适当缩短。也可以从炉门口的观测孔观察工件与炉内的颜色是否一致。均温结束前要做好渗碳准备。
5)渗碳与扩散。在渗碳温度下向炉内通入渗碳气体介质,对工件进行渗碳处理。若以CH4为渗碳介质,要求其纯度>96%,否则渗速慢或渗层薄。炉内压力为(26~47)×103Pa;若以丙烷为渗碳介质,其炉压为(13~33)×103 Pa。渗碳一段时间后停止送气,抽真空进行扩散,降低表面碳含量。如此反复脉冲式地进行,直至达到要求的渗层深度。
6)渗碳后的热处理。渗碳结束,停止供应渗碳介质,将炉温降到淬火温度冷却。为了消除网状碳化物可进行正火处理,随后再加热淬火和低温回火。
材料、形状、技术要求不同的工件,应采用不同的渗碳工艺进行渗碳。
真空渗碳工艺有一段式、脉冲式和摆动式三种,大多用脉冲式。脉冲式是利用反复地通入渗碳气体渗碳和抽真空扩散交替进行渗碳处理,可用活化期与扩散期的时间比控制渗层碳含量,具有不用控制碳势、省去碳势控制仪,直接通入渗碳剂、不需要载体气,不需要气体发生器等好处。
为了提高渗碳速度,人们都喜欢选用脉冲式扩散的渗碳方法,一般强渗时间(tc)、扩散时间(td)与总渗碳时间(t)的关系如下:
式中C—技术要求达到的表面碳含量;
Co—强渗期结束后的表面碳含量;
Ci—心部碳含嫩(顾材料)。
10.漉态床渗碳
在悬浮于气流中形成流态化的固体颗粒渗碳介质中进行渗碳的工艺称为流态床洛碳。
流态床洛碳可以使用惰性颗粒,通人碳氢化合物气体和空气进行渗碳,也可用可供碳的颗粒作为供碳源。
(l)流态床渗碳的特点近几年来,流态床瀣碳发J燕很快,受到人们的广泛关注并获得成功应用,与普通气体渗碳相比,具有以下特点:
1)加热速度和渗碳速度都快,生产牢高。
2)由于流动粒子对工件表面的冲刷作用,工件表面不会积炭,可以进行高碳势渗碳。
3)炉温相对均匀(温差≤±5℃),气氛均匀,渗层均匀。
4)操作方便,渗碳后可直接淬火。
5)换气速度快,可以进行多种工艺组合。
(2)常用流态床渗碳类型 大致可分为内燃式、电极式和外热式三种。
1)内燃式流态床渗碳:流动粒子采用Al2O3,流化气一般采用空气+碳氢化合物(如CH4、C3H8)或天然气,除流化作用外同时兼作燃气和渗碳气体。流化气进行不完全燃烧,剩余的CO、CH4可作为渗碳气渗碳。采用空气+丙烷作为流化气时,空气∶丙烷=4∶1~4.5∶1。
2)电极式流态床渗碳:采用电极式(又称石墨式)流态床渗碳,流动粒子采用石墨。石墨为导电物质,可以使流态床导电,当两电极产生的电流通过流态床时,石墨发热而加热工件。流化气采用空气,空气中的氧气在渗碳温度下与石墨反应形成C-CO- CO2渗碳气氛。根据碳势调整温度。
3)外热式流态床渗碳:流动粒子采用0.180mm(80目)的Al2O3,流化气由氮气+富化气组成,这类流态床渗碳工艺可控性较好。
(3)外热式流态床渗碳工艺操作 外热式流态床渗碳采用氮气+富化气作为流化气,如氮气+丙烷、氮气-甲醇、氮气-丙烷-空气等。流化气进入流态床,Al2O3流态化的同时,富化气在高温下裂解,在炉内形成渗碳气氛,通过调整氮气与富化气的比例来调整碳势,气氛的碳势可以用氧探头间接测量。
流态床气氛转换速度非常快,大约几分钟之内就可以完成碳势由零到控制点的转换,而且重复性很好。基于这个特点,渗碳过程往往是由高碳势渗碳-低碳势扩散的多次循环组成,既可获得较理想的碳浓度梯度,又可获得较快的渗速。据有关资料介绍,950℃×1h渗碳,可获得0.8~0.9mm的渗层。对6mm厚的低碳钢板进行1000~1030℃×20min渗碳,渗层为0.5~0.6mm。但采用高温快速渗碳工艺,渗后应对工件进行正火处理,以细化晶粒,然后再淬火回火。
3.1.2 钢的碳氮共渗
碳氮共渗是将工件置于能产生C、N活性原子的介质内,通过加热与保温,使工件表面同时吸附C、N原子并向内部扩散,形成具有一定C、N含量和一定厚度C-N共渗层的化学热处理工艺。碳氮共渗以渗碳为主,其性能与工艺方法等与渗碳基本相似;但是由于氮原子的渗入,碳氮共渗又有其自身的特点。
1.碳氮共渗的特点
(1)碳氮共渗的温度低于渗碳温度 氮的渗入降低了渗层的相变温度(A1点及A3点)。氮和碳一样,都是扩大γ相区的元素,氮和碳共同作用,可使渗层相变温度降低。当氮的质量分数达到0.3%时,Ac1点温度只有697℃。因此,碳氮共渗可以在较低温度下进行,便于渗后直接淬火,且畸变小。
(2)碳氮共渗层的C、N含量高,残留奥氏体较多 氮使γ相区的相变温度A1、A3点下降,γ相区扩大,增加了C、N在奥氏体中的溶解度,从而导致共渗层C、N含量增高。同时,由于氮的渗入,降低了渗层的马氏体相变温度(Ms),减少了奥氏体的转变量,使表层残留奥氏体较多,硬度会有所下降。
(3)碳氮共渗层的淬透性优于渗碳层 氮的渗入不仅扩大了γ相区,而且降低了渗层的临界冷却速度,使奥氏体稳定化。由于临界冷却速度降低,碳氮共渗层中的碳氮奥氏体比单独渗碳奥氏体的稳定性高,因此碳氮共渗工件可以在比渗碳件更低的冷却速度下获得表面硬化层,提高了碳氮共渗层的淬透性。由于共渗层的马氏体相变温度(Ms)低,残留奥氏体量较渗碳多,故有利于碳氮共渗件淬火后在其表面得到较大的残余压应力,提高其疲劳强度和力学性能,并可减小工件共渗后畸变和开裂倾向。
(4)碳氮共渗速度高于渗碳速度 碳、氮的同时渗入加大了碳的扩散系数。在相同的温度和时间条件下,碳氮共渗层厚度远大于渗碳层厚度,即碳氮共渗的渗速较快,可以缩短工艺周期。
(5)碳氮共渗层中可允许一定数量的碳化物 共渗层中碳化物的数量、形态和分布等与钢种及碳氮共渗的工艺参数有关,颗粒状的碳化物可以显著提高工件表面层的耐磨性。已开发出的高含量碳氮共渗层中就含有较多的粒状碳化物。
(6)碳氮共渗层厚度较渗碳层薄 与渗碳相比,碳氮共渗所获得的渗层厚度较薄,承载能力也稍逊一筹。
碳氮共渗层比渗碳层有更高的耐磨性、疲劳强度和耐蚀性;比渗氮有较高的抗压强度和较低的表面脆性,而且生产周期短,渗速快,用材广泛,使用性强,在工具表面强化方面得到广泛应用。
2.碳氮共渗的分类
按使用介质分类,碳氮共渗分为以下三种:
(1)固态碳氮共渗 与固体渗碳相似,常用的渗剂成分(质量分数)为:30%~40%黄血盐、10%Na2CO3和50%~60%木炭。该工艺生产率低,操作繁重,劳动条件差,能耗大,目前生产上已很少用。
(2)液体碳氮共渗 主要渗剂是氰盐,曾兴旺一时,但由于氰盐剧毒,给环保带来危害,使用受到限制,日趋淘汰。
(3)气体碳氮共渗 它是当前应用最广泛的一种,环境污染小,劳动条件好,操作简便,生产率高。
按共渗温度分类,则可分为低温(700~760℃)碳氮共渗、中温(760~860℃)碳氮共渗和高温(860~960)碳氮共渗三种。其中应用最多的是中温碳氮共渗,其主要特点是处理温度比渗碳低,且工艺时间短,渗层性能好,适用面广。
若按渗层厚度不同可分为薄层(<0.2mm)、普通(0.2~0.8mm)、深层(>0.8mm)碳氮共渗。一般应用的渗层厚度为0.2~0.8mm,适用于承受中、低负荷的耐磨件。深层碳氮共渗适用于受载较大的工件。
按渗层含量的不同分为普通含量与高含量碳氮共渗。一般而言,普通含量的碳氮共渗层,碳的质量分数控制在0.8%~0.95%,氮的质量分数为0.2%~0.4%。在高接触应力条件下的部件表面要求有较多的粒状碳化物时,碳的质量分数可提高到1.20%~1.25%,甚至可以更高;但氮的质量分数一般都控制在0.5%以下。
3.碳氮共渗后工件的热处理
碳氮共渗后工件的热处理方式和渗碳后的热处理极为相似,都要进行淬火和低温回火。碳氮共渗常用的共渗温度为820~880℃(低碳钢及低合金钢为840~860℃)。共渗后的热处理有多种工艺方案,大多采用淬火加低温回火处理。
(1)碳氮共渗后直接淬火+低温回火820~860℃共渗后直接淬火,然后160~200℃×2~3h回火。该工艺适用于中、低碳钢及低合金钢,可获得满意的表面及心部组织。由于碳氮共渗层中的碳氮奥氏体比渗碳奥氏体具有更高的稳定性,因此可选用冷却速度较缓慢的淬火冷却介质,如淬火油及合成淬火冷却介质。
(2)碳氮共渗后进行分级淬火+低温回火820~860℃共渗后先在120~200℃热油、硝盐浴或碱浴中分级1~15min(根据工件情况而定),出炉空冷,然后在160~200℃的热浴中回火。经该工艺处理后,工件畸变小,适用于比较精密、尺寸要求严格的合金钢件。
(3)碳氮共渗后一次加热淬火+低温回火 经碳氮共渗后出炉空冷或置于冷却坑中缓冷,然后重新加热淬火+低温回火,适用于共渗后还需机械加工或因各种因素不能直接淬火的工件。淬火加热应在脱氧良好的盐浴炉或带保护气氛的设备中进行。
(4)碳氮共渗后从共渗温度直接淬火、冷处理+低温回火 在820~860℃碳氮共渗后直接淬火,然后在-70~-80℃介质中进行冷处理,随后进行160~200℃低温回火。此工艺适合于含Cr、Ni较多的合金钢工件,如20Cr2Ni4A、18CrNiWA等,以减少表面的残留奥氏体,提高硬度,稳定尺寸。
(5)共渗后缓冷、高温回火、再重新加热淬火+低温回火 工件碳氮共渗后空冷或放到冷却坑中缓冷,然后进行620~650℃×2h(应加强保护)高温回火,再重新加热淬火+低温回火。此工艺适用于含Cr、Ni较多的合金钢以及碳氮共渗后尚需机械加工者。
4.气体碳氮共渗
气体碳氮共渗常采用的渗剂有两大类:一类是渗碳介质+氨;另一类是含有C、N元素的有机化合物。
(1)渗碳介质加氨 渗碳介质可以用丙烷富化的吸热式渗碳气体或煤油、甲苯等液体渗碳剂,氨则作为供氮源。碳氮共渗时,将渗碳剂和氨气同时送入炉罐内,它们除各自发生渗碳反应和渗氮反应生成活性C、N原子外,还会相互反应生成氰氢酸(HCN)。
CH4+NH3→HCN+3H2CO+NH3→HCN+H2O
新生成的HCN在高温下与钢件表面接触时,又分解产生活性C与N原子。
2HCN→H2+2[C]+2[N]
活性C、N原子被工件表面吸收并向内部扩散,形成碳氮共渗层。
采用气体渗碳剂加氨作气体碳氮共渗介质的优点是炉内碳势可以控制,易于保证产品质量,但设备成本较高,操作复杂,只适合于大量生产。
(2)含有C、N的有机溶液 直接向炉内滴入含有C、N的有机化合物,如三乙醇胺、甲酰胺、尿素的甲醇溶液等。该工艺实施方便,目前应用较多。
1)三乙醇胺[(C2H5O)3N]是一种暗黄色黏稠液体,溶于水,活泼性强,共渗速度快,且无毒,在高温下发生下列反应:
900℃分解时,所得的气体成分(体积分数,%):
三乙醇胺的主要缺点是黏度大,流动性差,容易堵塞管道;另外,三乙醇胺氮含量较高,当共渗温度较低时,工件表面易形成较密集的碳氮化物薄层。为降低其氮含量和改善流动性,可用乙醇稀释(三乙醇胺∶乙醇=1∶1)后使用。
2)加尿素的甲醇溶液(最大溶解度为20%)直接滴入炉内,在高温下可分解出CO、H2和[N],其反应为:(NH2)2CO→CO+2H2+2[N]
甲醇在高温下分解产生CO和H2,其反应是:CH3OH→CO+2H2
影响气体氮碳共渗质量的因素比较多,概括起来有如下几点:
1)渗剂供给量对渗层质量影响的规律是:随着供给量的增加,渗层氮、碳含量增高,共渗速度加快;但供给量又不能太多,过多不仅造成浪费,还会形成大量碳氮化物,共渗速度也会降低。渗剂供给太少,不但共渗速度减慢,还会使共渗层C、N含量偏低。因此,正确地选择渗剂的供给量是保证渗层质量的重要的因素之一。
共渗介质的供应量应满足下列工艺要求:供应适量的C、N原子;并使炉内保证正压;保证气氛均匀流动。排气阶段应输入大量的共渗介质,以迅速排除炉内的氧化性气氛,恢复炉气的正常成分。扩散阶段应适当减少渗剂的供应量,以控制渗层的C、N含量,减少淬火后的残留奥氏体量。C、N共渗剂的供给量,一般用换气次数(每小时通入炉内的气体量与炉罐容积的比值)表示。采用气体渗碳剂加氨时,一般以6~10次/h为好;采用煤油作渗碳剂时,可将煤油每小时的滴入量换算成渗碳气(煤油的产气量为0.7~0.83m/L),加上氨气的通入量,一般以3~8次/h为好。应根据炉膛大小决定炉气流量,一般炉子越大,换气次数越少。另外,还要考虑共渗温度、装炉量、工件表面积、工件材料及渗层性能要求等各种因素,适当调整其流量,以获得最佳值。
氨在共渗介质中所占的比例,对共渗层的碳、氮含量、组织状态和共渗速度有很大影响。在一定范围内,氨的加入比例越大,共渗层的C、N含量也越高,而且共渗速度也快。C、N共渗时,氨气所占的渗剂比例应根据共渗温度、表面碳氮含量要求及渗碳介质的种类来合理地选择。当采用煤油和氨进行碳氮共渗时,氨气所占的比例在40%(体积分数);当利用稀释气+富化气+氨气进行碳氮共渗时,氨气只占炉气总体积的2%~10%(体积分数)。
2)共渗温度对渗层质量的影响:一般认为,随着共渗温度的升高,碳原子渗入深度大大增加,而氮原子的渗入深度变化不大。碳原子的渗入深度决定了硬化层厚度的大小。因此,随着温度的提高,渗层深度增加。
共渗温度低于800℃时,工件表面吸收氮原子能力增强,而氮原子向内层扩散的速度减慢,因此在渗层表面易于形成脆性的高氮低碳的ε化合物,使渗层变脆。随着共渗温度的升高,如在800~850℃进行短时间共渗时,一般为ε相和高碳的Fe3(CN)化合物;时间延长或在更高的温度下,在高碳气氛中共渗时为Fe3(CN)化合物及残留奥氏体(淬火后的组织);在低碳气氛中共渗时,为马氏体和残留奥氏体。
共渗温度还影响直接淬火后表面的残留奥氏体量。随着共渗温度的升高,残留奥氏体在渗层中的分布深度增厚。表层的残留奥氏体量随温度的升高先是降低,而后又随温度的升高而增加。每一种钢有一个最低残留奥氏体量的对应温度。这是因为温度较低时,共渗以渗氮为主,随着温度的升高,氮含量降低,使奥氏体稳定性也降低,因此淬火后残留奥氏体量减少;在较高的温度下,共渗以渗碳为主,此时升高温度,碳含量增加,奥氏体稳定性也增加,因此淬火后残留奥氏体量也增加。
综上所述,共渗温度的选择应综合考虑渗层质量、共渗速度及变形量等因素。国内大多数工厂选用820~860℃,只有在特殊情况下才超出此共渗温度范围。
3)共渗时间对质量的影响:气体碳氮共渗保温时间主要取决于共渗温度、工件所要求的渗层深度及钢材的化学成分;另外,渗剂的成分及流量、炉子的大小及装炉量等因素也有一定的影响。当共渗温度和渗剂一定时,共渗时间与共渗层深度的关系式为
式中α——共渗层深度(mm);
τ——共渗时间(h);
K——共渗系数,与共渗温度、渗剂及钢种有关。常用钢种K值见表3-18。
表3-18 几种钢气体碳氮共渗的K值
试验证明:渗层深度在0.5mm以下时,平均共渗速度为0.2~0.3mm/h;渗层深度在0.5~0.9mm时,平均渗速为0.2mm/h。实际生产中,也可根据工件要求的渗层深度计算出共渗时间,并在工件出炉前通过检验试棒的渗层深度来确定准确的出炉时间。
除了气体碳氮共渗外,还有固体碳共渗氮和液体碳氮共渗,它们在大生产中没有气体碳氮共渗应用广泛。