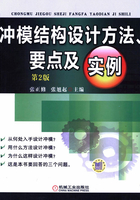
2.7 冲模的排样化快速设计
在完成成套冲模企业标准的编制工作后,应逐步推行冲模“三化”,并在实际设计、制模及修模工作中,进一步完善冲模企业标准。有了冲模“三化”工作基础,便可进行冲模排样化快速设计。
2.7.1 排样化快速设计的实质
冲模的排样化快速设计就是在冲模“三化”后,充分利用成套冲模企业标准,用冲压零件及其冲压工艺工步排样图,取代冲模总装配图,仍然要配齐冲模非标准工作零件(如凸模、凹模、凸凹模成形侧刃、凸模与凹模镶拼组合零件、凹模框等零件)加工图,构成整套模具图,交付制造。
冲模的标准化,只能对模芯即模具工作部分(包括凸模与凹模、凸凹模及其直接连接、配合等相关零部件)以外的安装、支持、夹紧、定位、推卸以及送料等系统与装置的构成零部件,进行品种类型、系列、规格的标准化及半标准化,对规则形状的圆形、方形冲裁凸、凹模进行标准化,对冲模的常用结构形式进行典型化、标准化。模具工作部分随冲压零件及其冲压工艺变化,只能因件而异,进行专门的设计。
冲模排样化设计,是在给定冲模标准类型与结构的基础上,省去结构设计,选用标准定型的典型结构与限定规格,只设计和绘制模芯部分非标准工作零件图,从而节省设计工时,压缩设计周期。
2.7.2 排样化快速设计的一般程序
作为一种简捷的冲模设计方法,通常都只能因件而异,根据冲压零件的不同类型及其不同的冲压工艺过程、冲压排样图等,往往采取不同的设计步骤,以达到尽量压缩设计周期的目的。
1.标准通用的冲压零件用冲模
这类冲压零件通常所用原材料种类、料厚及其供应状态与力学性能都是已知和不变的;其冲压工艺过程及排样图,以及所有冲模的类型与结构,都依然如故,实际上相当于复制以前冲模的备份,制造同样冲模的第二套或第几套,只是用户不同。
有一种情况是冲压零件相同,但是料厚减小或增大,材质改变或技术要求提高,如尺寸精度提高或要求毛刺小等。这对冲模整体结构无影响,主要是改变冲裁间隙,提高冲模制造精度,配用高精度模架。
另一种情况是冲压零件形状、材质及技术要求一样,但其平面尺寸不同,甚至相差较大。这种情况对采用相同的冲模结构也只是改变尺寸规格,选更合适标准规格而已。
不论是上述哪种情况,只要在《冲模典型结构组合》与《冲模典型结构图册》企业标准中,以及计算机图形库、模具底图档案中,可以找到相同或近似的已生产过的冲模,便可依照欲冲压零件或其展开毛坯排样图,参照旧冲模设计新冲模。而且只用绘制出详细的排样化快速设计总图,提供参照冲模编号或典型组合标准号,即可投入制造。
2.选用典型结构组合企业标准进行排样化设计
《冲模典型结构组合》企业标准,一般更细、更深、更广泛。所谓更细是指配套用零部件品种、类型更多。例如:根据冲裁料厚、冲压零件尺寸精度,规定配用不同精度的模架;模座有铸铁、钢的及相同规格而厚薄不同的,可按需要选用;侧刃不仅种类多,而且切边长度超过JB/T 7648.1—2008《冲模侧刃和导向装置 第1部分:侧刃》规定,其切边长度仅为5.2~40.2mm,企业标准可达3.5~60mm,而且中间间隔不限,还可更长一些。所谓更深是指典型结构组合进一步细化到每种类型冲模结构,都有单工序落料模、冲孔模、各种成形模和多工位连续冲裁模的典型结构示例。所谓更广泛是指企业增补了大量常用标准零部件、典型结构组合,并配有企业标准规定与推荐使用的冲压零件等使用实例。因此,无论设计、制造还是修理,可操性很强。
有了上述《冲模典型结构组合》企业标准及“三化”基础,进行排样化设计就很简便了。其步骤如下:
1)依据冲压零件图及其冲压工艺和排样图,确认欲设计冲模种类、类型及套数。
2)计算冲模的凹模周界L×B,并依此选择已定冲模类型的标准规格。
3)确定冲模定位方式及定位系统构成的标准零部件。
4)按标准给定闭模高度范围及要求送料方向、导向精度配用模架。
5)计算模具压力中心,核定模架尺寸与工艺,选定冲压设备类型、吨位及装模空间。
6)绘制排样化模具设计总图,计算并写出冲模技术规格与制造技术要求。
7)填写选用典型结构组合标准号及构成零部件标准明细表。
8)设计并绘制非标准工作零件(如凸模、凹模、凸凹模等)加工图。
9)进入校对、审核、标准检查及批准等质量管理程序。
10)成品冲模图入库。
2.7.3 冲模排样化快速设计实例
1.导柱模架固定卸料结构多工位连续模排样化设计
这类结构冲模可以配用各种滑动导向或滚动导向模架,有纵向送料与横向送料两种典型结构组合标准各33个,共66个标准规格可供设计选用(见原JB/T 8065.3、4—1995)。
实例1
图2-33所示为使用上述典型组合标准进行排样化快速设计的模具总装配图。
该冲压零件是一个平板冲裁件。对于这类零件的冲模结构设计,当采用排样化快速设计时,应特别注意以下几点:
(1)冲孔后落料两个工位凹模的相互尺寸连接与相对位置
1)先计算出冲模的压力中心O。此例压力中心在落料凹模刃口O点中心线上。
2)搭边a是1.5mm,送料进距为S=58mm+1.5mm=59.5mm。
3)第Ⅰ工位冲孔与第Ⅱ工位落料的两工位中心距L=S+0.10。
(2)每根条料入模首件定位 采用始用挡料装置1,让其挡料边与落料刃口差0.3mm,即条料首件送入冲孔后其端头沿边a1≈(1.5-0.3)mm=1.2mm。第Ⅱ工位落料用固定挡料块2,设计其挡料边距刃口为:L1=a1+(0.2~0.3)mm=1.7~1.8mm。正常情况下,首件落料仍可保证1.4~1.5mm端头沿边。
(3)导料槽结构设计及改进 两个导料板12构成的导料槽,其宽度按送进条料宽度最大值Bmax并适当加大。本例中条料宽B=630-0.2mm,最大条料宽度Bmax=63mm。导料槽入料口宽度B导=Bmax+(0.1~0.5)mm=63.1~63.5mm。鉴于料厚t=1.5mm,取B导=63.1mm,同时考虑制造公差为0.1mm,得B导=63.1+0.10mm。
图2-33 底板连续冲裁模排样化设计冲模总图
1—始用挡料装置 2—固定挡料块 3、11—凹模板 4—挡销 5—弹簧 6—卸料板 7—落料凸模 8—导正销 9、10—冲孔凸模 12—导料板 13—承料板
在第Ⅱ工位落料后,搭边框两边沿边宽仅为1.5mm,受到落料凸模的挤压,必然向导料板方向展宽并卡紧,加大了送料阻力,有时会出现卡模。对于t≤1mm的薄料,可使导料板的导料面向外斜30°角,贴近凹模表面可保留2mm左右为直壁,这样减小搭边框推送阻力,便可保证送料顺畅。当t>1mm时,为了在导料槽入料口一段能让条料贴紧导料板送进而不会歪斜,仅在导料槽出料口一段按图示形状与尺寸加工。
(4)始用挡料装置 始用挡料装置为非标准的,故在图中示出,见A—A剖视图件3~6。
(5)合理标注尺寸 多工位连续模设计中,尤其采用排样化快速设计应注意其尺寸的合理标注,图2-34所示为一个典型实例,可供参考。
图2-34 多工位连续模排样化快速设计的尺寸标注方法
2.弹压卸料导板式连续模排样化设计
实例2
图2-35所示为连接片弹压卸料导板式连续冲裁模的排样化快速设计模具装配图。
3.复合冲裁模排样化快速设计
实例3
图2-36所示为变压器硅钢片倒装式圆形薄凹模复合冲裁模排样化快速设计模具装配图。
图2-35 连接片弹压卸料导板式连续冲裁模的排样化快速设计模具装配图
图2-36 变压器硅钢片倒装式圆形薄凹模复合冲裁模的排样化快速设计模具装配图