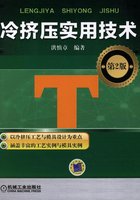
1.6 冷挤压时的外摩擦和润滑
在金属塑性成形过程中,被加工金属与模具之间都有相对运动,因而在接触表面间便产生阻止切向运动的阻力,即外摩擦。外摩擦的存在会使塑性加工所需的力、能量增加;使模具磨损加剧,使工件表面发生粘结、擦伤等现象。所有这些既影响产品质量,又降低模具的使用寿命。
润滑和塑性成形有密切的关系。润滑技术的开发能促进挤压加工的发展。20世纪30年代,钢的冷挤压技术由于研制出了磷化-皂化润滑新工艺,才得以成功地用于工业生产便是一例。随着新材料、新工艺的出现,必将要求人们解决新的摩擦、润滑问题,以适应塑性成形技术不断进步的需要。
1.6.1 冷挤压过程中的摩擦特点及种类
1.摩擦特点
冷挤压变形过程中,模具表面与毛坯直接接触,它们之间存在着滑动摩擦。由于冷挤压变形时的压力可高达2000~2500MPa以上,因此,冷挤压变形过程中的滑动摩擦与机器零件中的滑动摩擦有很大的差别。其主要特点如下所述。
(1)模具与毛坯的接触表面产生局部粘结 在冷挤压加工中,接触表面上的压力很高,故表面之间接合很紧密。在变形过程中,还有内部质点不断地迁移到接触表面上来。这些都使接触表面间的原子吸引力增大,从而使接触表面之间产生粘结的趋势增强。如果金属的粘结强度较高,则剪切变形将发生在变形金属表层下较软的区域内。在一般情况下,当沿接触表面产生滑动时,必然切断粘结面,沿该粘结面的切力就是摩擦力的一部分。
在冷挤压变形区内沿接触表面存在分子吸引力,并产生局部粘结,这可由冷挤压变形时产生死区金属得到证明。
(2)接触表面的机械咬合 由于模具和毛坯表面实际上都具有一定的平面度误差,存在着微观的凸起和凹谷,彼此接触时互相嵌入,形成如图1-53所示的机械咬合。当接触表面产生滑动时,模具表面的凸起必须碾平陷进凹谷内的变形金属。很显然,凸起越高,压入变形金属内的深度大,表面沿切向位移所需的力就越大,也就是摩擦阻力越大。
图1-53 接触表面的机械咬合
(3)中间物质的剪切 在冷挤压加工中,在模具与变形金属的接触表面之间,常有中间物质存在,形成一定厚度的隔离层,部分地或全部地屏蔽着金属的表面。这些中间物质主要为金属表面上的工艺润滑剂、水和灰尘等,对摩擦过程有很大的影响。通常是中间物质的强度大大地低于变形金属。当沿接触表面产生滑动时,将在中间物质的隔离层内发生剪切变形。该剪切力为摩擦阻力的一部分。
2.滑动摩擦种类
冷挤压加工中,为了减少摩擦阻力,应加润滑剂。生产实践证明,润滑剂性能的优劣对于摩擦过程有着很大的影响。现根据润滑剂隔离层的厚度和存在情况,将冷挤压中的滑动摩擦分为如下三种基本类型。
(1)液体润滑摩擦 在模具与变形金属的接触表面之间存在较厚的润滑层,当其厚度大于分子距离的1000倍时,可形成液体润滑摩擦。由于冷挤压加工压力很大,润滑剂将部分地被挤出,因此,在冷挤压过程中,只可能在部分接触表面上形成液体润滑摩擦。
(2)吸附润滑摩擦(边界摩擦) 在模具与变形金属的接触表面之间,仅存在润滑剂吸附层的润滑摩擦,称为吸附润滑摩擦或边界摩擦。由于在吸附层内分子成为定向排列,润滑剂的吸附层不具有液体的基本物理性质——流动性,而相当于固体物质,因此能承受较大的压力,具有较低的层间剪切阻力。如果润滑剂能在接触表面形成紧附于金属表面上的高塑性的吸附层,其润滑效果更好。但是,完全的吸附润滑摩擦,在实际中是难以找到的。这是因为接触表面总不是理想的那么平直和光滑。在冷挤压变形过程中,吸附层一旦在部分接触表面间遭到破坏,便形成半干摩擦。
图1-54 接触表面的实际摩擦状态
a)润滑情况良好 b)润滑情况较差
1—液体润滑摩擦 2—边界摩擦 3—半干摩擦
(3)干摩擦 接触表面之间没有润滑剂薄膜和任何杂质存在,摩擦表面处于直接接触状态的摩擦,称为干摩擦。实际上,真正的干摩擦只能在高真空中实现。在冷挤压中,绝对的干摩擦是不存在的,也是不希望的。如果出现真正的干摩擦,接触表面必产生粘结(粘附),从而伴随接触表面间的相对滑动而产生严重的表面擦伤。
冷挤压中的摩擦皆是上述几种滑动摩擦的混合情况,如图1-54所示。当采用良好的润滑剂时,形成液体润滑摩擦和吸附润滑摩擦的混合摩擦情况;当采用一般的润滑剂时,则形成液体润滑摩擦、吸附润滑摩擦和半干摩擦的混合摩擦情况。
1.6.2 影响摩擦力的因素
从上述分析可知,在冷挤压加工中计算摩擦力的大小,严格说来库仑定律已不适用。这是因为冷挤压中的摩擦力应由两部分组成:一部分为与正压力有关的摩擦力;另一部分为与正压力无关的附着力。但是目前对于冷挤压中摩擦规律的研究还很不够,欲确定与局部粘结、机械咬合、中间物质等有关的摩擦力大小是很困难的。因此,目前计算摩擦力的大小仍采用与库仑定律相同的形式。不过,此时摩擦因数的大小不能采用机器零件中滑动摩擦因数值,其数值应该加大,加大的部分就是考虑了与正压力无关的附着力的影响。
因此,这里主要讨论摩擦因数的大小,容易理解摩擦因数的数值实际上随金属的化学成分、模具表面状态、接触面上压力、接触面积、变形程度、变形速度、变形温度以及润滑条件状况而异。下面将具体分析这些因素的影响。
(1)金属化学成分 外摩擦因数随着金属、化学成分的不同而异。例如,用光洁的钢压头,在常温下对不同材料进行压缩时测得:软钢的摩擦因数为0.17,铝的摩擦因数为0.18,α-黄铜的摩擦因数为0.10,电解铜的摩擦因数为0.17。对于不同的钢种,摩擦因数也不一样。钢中的碳含量增加时,摩擦因数会减小。钢中的合金元素的种类、数量也影响摩擦因数,一般说来,随着合金元素的增加,摩擦因数下降。
图1-55 锡在模具钢上滑动时模具表面粗糙度对摩擦因数的影响
金属的种类、化学成分影响接触面的粘合性。例如,在同样的压力下,室温时铝与钢在干摩擦的粘合性比钢与钢之间的粘合性大得多,接触面的粘合性越强,摩擦因数越大。总的说来,金属材料越硬,摩擦因数越小;反之,软材料的摩擦因数则较大。
(2)模具表面状态 表面状态主要是指表面粗糙度、加工痕迹的方向及硬度等。
模具表面越粗糙,越凹凸不平,真实接触面积率就越大,摩擦因数也就越大。图1-55所示为锡在模具钢上滑动时模具表面粗糙度对摩擦因数的影响。由该图可知,模具表面粗糙度越小,摩擦因数就越低。
模具表面的机械加工痕迹的方向性,使摩擦因数也具有方向性。实验证明,顺着加工方向的摩擦因数比垂直于加工方向的摩擦因数约小20%。
模具表面的硬度越高,受压力作用后,弹性变形越小,使真实接触面积率减小,则摩擦因数也减小;反之,硬度越小,摩擦因数就越大。模具与变形金属的硬度差越大,硬度高的模具表面上的凹谷就越易被金属所充填,使真实接触面积率增大,则摩擦因数也增大。
冷挤压成形中,模具的表面粗糙度在决定摩擦因数大小方面是起主要作用的。但被挤压毛坯表面粗糙也会引起摩擦因数的增加,因此要求毛坯表面应该足够平整和光滑。
(3)接触面上单位压力 计算冷挤压摩擦力的大小仍借用库仑定律,即摩擦力T与正压力P成正比,即
T=fP (1-8)
式中 f——冷挤压变形时的摩擦因数。
冷挤压变形时,在模具与毛坯的接触面上,由于存在摩擦力,从而引起了切应力。这种切应力称为平均摩擦应力,用τ表示,则
式中 A——接触表面的面积。
由T=τA=fP=fσA (1-10)
得
式中 σ——正应力。
由式(1-10)可知,当其他条件相同时,单位面积上的摩擦应力与正应力成正比。但这一正比关系是有限制的,这是因为随着正应力的增大,变形程度增大,被挤毛坯与模具之间的凸起与凹谷互相嵌入程度增大。当互相嵌入达到了最大值时,摩擦力也达到了最大值。在单向应力状态下,当摩擦应力等于临界剪应力τK时达到最大值,此时
τ与σ的正比关系也破坏了。由式(1-11)可知,由于τK为定值,因此摩擦因数f值随正应力σ的增大反而下降。原因在于:随着正应力的增大,在被挤毛坯与模具接触面上出现所谓“磨损生成物”,这些质点起着吸附润滑的作用,单位压力越大,“磨损生成物”越多,吸附润滑作用越大,摩擦因数就越小。
(4)接触面积 冷挤压加工的摩擦应力τ可用下式表示:
τ=τ1β+τ2(1-β) (1-12)
式中 β——真实接触面积率;
τ1——真实接触面积上的摩擦应力;
τ2——充满润滑剂部分的摩擦应力。
接触面上充满润滑剂,可以认为是属于液体润滑。此时τ2=0,那么,式(1-12)变为
τ=τ1β (1-13)
式(1-13)表明摩擦应力与真实接触面积率成正比。冷挤压加工中采用良好的表面处理和润滑处理就是为了减少β,从而减少摩擦应力。近几年发展起来的静液挤压如图1-56所示。由图1-56中的结构可知,毛坯进入凹模锥形部分以前,四周充满高压液体,当进入凹模锥形部分时,带入高压液体,使毛坯始终保持良好的液体润滑状态,大大减小真实接触面积率,即明显减小摩擦阻力。
(5)变形程度 随变形程度增加,真实接触面积率β增大,因而摩擦应力τ也增大,如图1-57所示。由图1-57还可以看出:原始润滑膜越厚,相同变形程度时的真实接触面积率β越小。
图1-56 静液挤压
1—凸模 2—钢圈 3—密封圈 4—液体介质 5—毛坯 6—凹模 7—挤压筒
(6)变形速度 随着变形速度的增加,摩擦因数逐渐减小,如图1-58所示。由图1-58可知,高速变形的摩擦因数比低速变形小。原因在于:由液体润滑状态变成吸附润滑或半干摩擦需要一定的时间,高速变形的时间极短,仍能维持良好的润滑状态和较小的真实接触面积率β,因而摩擦因数也就较小。
图1-57 变形程度与真实接触面积率的关系
图1-58 铝试样压缩加工时变形速度与摩擦因数的关系
(7)变形温度 冷挤压过程中,由于热效应的影响比较显著,使得模具和毛坯材料的变形温度皆有不同程度的提高,这就直接影响到润滑剂的黏度,从而影响到润滑皮膜的厚度和摩擦因数的大小。图1-59所示为摩擦因数与变形温度的关系。由该图可知,不同黏度的润滑剂,随着变形温度的升高,摩擦因数逐渐加大。
(8)润滑条件 良好的润滑条件可以始终保持较厚的润滑皮膜、较小的真实接触面积率β,从而保持较小的摩擦因数。因此,合理选择润滑剂能成倍降低摩擦因数。
(9)其他因素的影响 载荷特性对摩擦也有明显的影响。例如,振动变形能使毛坯的塑性变形力降低1.5~2倍,超声加工条件也能减小摩擦。
关于不同冷挤压条件下的摩擦因数值,建议参考表1-1选取。
图1-59 摩擦因数与变形温度的关系
1—黏度较小的润滑剂 2—黏度较大的润滑剂
表1-1 摩擦因数f值
总之,在大多数情况下,冷挤压中的摩擦和摩擦力是一个不利的因素。它带来了以下几方面的不利影响。
1)由于外摩擦的作用,引起应力和变形不均,使工件内产生附加应力和残余应力,降低产品质量,如图1-60所示零件产生内孔表面环状裂纹。
2)由于外摩擦的作用,增加了克服摩擦力的附加变形功及变形力,使工作应力增加,能量消耗提高。
3)由于外摩擦的作用,使变形力增加,因而加重模具的负荷,此外摩擦力会加快模具的磨损,降低模具的使用寿命。
4)由于外摩擦的作用,引起变形不均匀分布,使挤压件产生附加应力和残余应力,从而降低了产品质量。
图1-60 锡磷青铜冷挤压
a)毛坯 b)挤压件 c)内孔环状裂纹
5)由于外摩擦的作用,有时会产生粘模现象,增加了从模具中取出冷挤压件的困难,影响正常生产工作。
1.6.3 冷挤压中的润滑剂
1.润滑剂的效果
冷挤压时,影响摩擦力的主要因素是模具工作表面状态和润滑情况。因此,在生产中都将模具工作部分加工成很光洁的表面,一般表面粗糙度Ra在0.4μm以下。合适的润滑剂可以有如下的效果。
1)显著降低模具与变形金属之间的摩擦因数。
2)降低变形功及变形力。
3)减少模具的磨损,防止模具损坏及提高模具的使用寿命。
4)防止由于附加应力而引起的各种挤压件废品。
必须指出,润滑剂的用量要适当,否则会产生缺陷。例如反挤薄壁件时,由于润滑剂太多,会造成单向缺口现象。
2.润滑剂的要求
为了减少摩擦对冷挤压成形过程的不良影响,必须选用合适的润滑剂。冷挤压加工中使用的润滑剂一般应符合以下要求。
1)润滑剂应有良好的耐压性能,在高压力作用下,润滑膜仍能吸附在接触表面上,保持润滑效果。
2)应有良好的耐热性。由于冷挤压变形会产生热能,使毛坯温度升高,此时润滑剂应不分解、不变质。
3)润滑剂不应对金属毛坯和模具有腐蚀作用。
4)润滑剂应对人体无毒,不污染环境。
5)润滑剂要求使用、清理方便,来源丰富,价格便宜等。
3.润滑剂的种类
冷挤压加工时,常用的润滑剂有液体润滑剂和固体润滑剂两大类。
(1)液体润滑剂 液体润滑剂包括矿物油、植物油、动物油、乳液等。矿物油多是全损耗系统用油,全损耗系统用油的化学成分稳定,与金属不起化学作用,但摩擦因数比动、植物油大,因此,常把全损耗系统用油作配制润滑油的基油,再加入各种添加剂以制成所需的润滑油。动、植物油主要有猪油、牛油、鲸油、蓖麻油、棕榈油等。动、植物油含有脂肪酸,与金属起反应后在金属表面生成脂肪酸的润滑膜,润滑性能良好。动、植物油与矿物油相比,它的化学成分不稳定,还带有酸性。
(2)固体润滑剂
1)石墨。石墨具有六方晶格的层状结构,同一层内碳原子是以共价键连接的,因此石墨晶格受到剪切力作用时,就容易在层与层之间产生滑移。当金属毛坯与模具间涂有石墨的两接触面发生摩擦时,事实上是石墨层与层之间的摩擦,这样就起到了润滑作用。
石墨具有良好的导热性和热稳定性,滑动速度对它的摩擦特性影响很小,随着压力的增大,石墨的摩擦因数增大。另外,石墨的润滑作用和它吸附气体有关。石墨吸附气体后,摩擦因数减小,因此,它在真空条件下的润滑性能不如在空气中好,因而真空条件下,不采用石墨作润滑剂。石墨的摩擦因数一般在0.05~0.19的范围内。
2)二硫化钼。二硫化钼也是六方晶格结构,在二硫化钼晶体中,每个钼原子被六个硫原子所包围,硫原子处在钼原子的上、下层,形成S—Mo—S层状结构。在表面的硫原子与金属表面有较强的吸附性,因此,二硫化钼容易涂抹在金属表面上。此外,由于原子间距的差异关系,很容易在硫原子层之间发生滑动。当涂有二硫化钼的接触面相对滑动时,就发生二硫化钼分子层面的滑移,因此呈现出良好的润滑性能。二硫化钼的摩擦因数为0.12~0.15。
二硫化钼在真空中的摩擦因数比在大气中的还小,因而可作为真空条件下的润滑剂。
3)肥皂和蜡类润滑剂。常用的肥皂和蜡类润滑剂有:硬脂酸钠、硬脂酸锌以及一般肥皂等。硬脂酸锌用于冷挤压纯铝、铝合金;硬脂酸钠用于钢坯磷化处理后的皂化处理工序,也用于冷挤压有色金属。