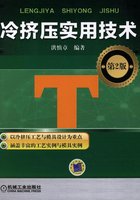
5.2 冷挤压模具结构设计
冷挤压模具总体结构形式的确定,关系到设备选型,模具的制造、使用、寿命和价格,挤压件质量和成本,以及挤压生产工作的稳定性、安全性和可靠性,是模具设计的关键,是开始设计之前必须解决的首要问题。
模具的总体结构形式,必须经过对所使用的设备、产量、制件的形状、尺寸和精度以及加工方法、制造技术等进行综合判断之后,作出决定。
5.2.1 模具结构设计要求及内容
1.模具结构设计的基本要求
(1)总体结构要均衡、协调
1)整个结构的厚度不要过薄。
2)整个结构的凸、凹处要少。
3)整个结构不要过于复杂。
4)外形轮廓尺寸不要相差过大。
(2)具有一定的强度及足够的刚性
1)结构的刚性好,可靠性高。
2)工作部件强度高,韧性好。
3)支承和连接部件具有足够的厚度和较大的接触面积。
4)安装部件牢固、可靠。
5)工作部件选择强度高、韧性好、耐磨性好的模具材料。
(3)结构上要适合受力的需要
1)为了提高模具的承载能力,冷挤压凹模均采用压套组合结构。
2)为了提高凸模的稳定性和抗弯曲性能,其长度应尽可能短。
3)凸模尾部端面、顶杆和凹模的下面,要垫入具有较大接触面积和足够厚度的垫块,以便分散集中载荷,并将模具负荷合理地引导、传递到压力机工作台面和机架上。
4)采用硬质合金模具时,垫板或模座厚度及导柱直径,要比钢模具的相应尺寸增大1倍。
5)为了减小应力集中,防止开裂,在主要工作零件上,尽可能不要制造固定零件的孔或其他孔。
6)为了减少摩擦力,模具工作部件的工作表面应精细抛光,并合理确定其有效接触和结合面积。
7)模座孔口部位,镶装经淬火的中间衬套。
8)必须有精确而可靠的导向装置。在刚度小的压力机上,应采用结实的四导柱结构或模口自身导向方式,以确保凸模和凹模的同轴度,保证挤压时凸模与凹模间隙的均匀性。
(4)通用性强
1)尽量采用通用标准模架。
2)工作部件可以快速更换。
3)易损件拆卸,安装方便。
4)紧固方法可靠。
5)使用调整方便。
6)操作安全、可靠。
(5)结构与选择的压力机相适应
1)冷挤压工艺所需的压力应在压力机所能提供的压力范围内,或压力机的额定压力行程大于模具工作的有效工作行程。
2)模柄尺寸应与压力机滑块中模柄孔尺寸相一致。
3)模具的最大平面尺寸必须能安装在机床工作台或工作垫板上。
4)模具的封闭高度必须在压力机的最大装模高度和最小装模高度之间。
5)模具压力中心与压力机机架重心吻合一致。
6)压力机的工作行程满足挤压工作的需要。
7)当压力机的刚性差、导轨精度低时,模座应设计得相当大,并采用四导柱结构。
8)如果因压力机的装模空间不足,在成形之前凸模不能预先插入凹模时,应在模座上安置可以调整凹模水平位置的微调螺钉。
(6)结构的经济性
1)结构要简单,总体结构尽量简化,零件形状尽量简单。
2)便于加工,制造容易。
3)安装、调整和更换迅速,将辅助作业调整时间减少到最小限度。
4)降低费用,尽量采用廉价材料,在万能、通用设备上加工,使材料消耗和工时费用最低。
2.模具结构设计的主要内容
由于挤压件形状、尺寸及工艺方案和采用设备的不同,冷挤压模具有各种各样的结构。确定模具总体结构形式时,必须解决以下问题。
(1)模具类型的确定 模具类型有:简易敞开模、封闭成形模、导柱模、专用模、标准模、通用模、整体模、镶块模、分割型模具、大批生产精密模、小批生产简单模。
(2)工作部件结构形式 结构形式有整体式、分割式、组合式。
(3)连接部件结构形式 结构形式有模柄、模板、模座、多层垫板结构。
(4)卸料形式 卸料形式有顶杆卸料、环形顶出套卸料、打杆卸料、卸料圈卸料、卸料板卸料。
(5)导向方式 导向方式有导柱导向、凸模导向、模口导向、导向套导向。
(6)紧固方式 紧固方式有螺栓、压板、特形螺母、侧向紧定螺钉紧固。
(7)安全装置 安全装置有护圈装置、挡板装置、光电保护装置。
(8)操作方式 操作方式有手工操作、机械操作、自动化操作。
5.2.2 模具结构形式的种类
在上模板和下模座之间连以导向和卸料等装置的总体称为模架。最简易的冷挤压模架是没有导向装置的敞开式结构。模架是定位连接体,其上部模板或模柄与压力机的滑块连接,下部模座与压力机工作台连接,内部安装全部模具零件,构成模具的总体。
模架是模具的安装基础,又是承受较大载荷、传递压力的重要组件,是冷挤压模具的主要组成部分。模架不仅应该具有一定的强度,还要有足够的刚性和较好的精度。因此,模架的技术条件,还是相当严格的。对模架的主要技术要求有以下三点。
(1)模架的刚性要好 模架(上模板和下模座)要有足够的厚度和重量,具有较大的接触面积,并且能够将作用在模具上的负荷合理地分配到压力机滑块和工作台面上。要求能够承受一定的耐压能力而不变形,使模具工作平稳,始终处于正常的使用状态,以保证挤压件的精度和较高的模具寿命。与其他类型模具明显不同的是下模座大而厚,且应选用优质钢锻件制造。当模具载荷较大时,常采用多层的组合模座垫板,这在其他模具结构中是少见的。
(2)模架应具有一定的强度 模架的强度应满足挤压时承载能力的要求,并确保模具在长期使用条件下,不变形,不损坏。
(3)模架的精度要高 模架的精度必须保证凸、凹模相对位置的精确性和工作中不出现偏心载荷,不产生侧向推力。因此,要求模架的上下面应平行,导柱(导套)对下模座(上模板)的垂直度误差不大于0.01mm,导柱与导套的配合精度不低于7级。
模架的类型主要取决于挤压变形的需要、生产批量和所选用设备的规格。模架按用途、模具结构形式和设备进行分类,见表5-3。
表5-3 模架的分类
专用模架就是为某一种零件,甚至某一道挤压工序所设计的模架,没有通用性。在通用模架上,只要更换工作部件,就可以进行各种形式的冷挤压加工,适用于多种零件的小批量生产。通用模架可大大降低模具的成本,同时也将调整时间减少到最小限度。标准模架的特点是在压力机行程中,凸模的滑动部分在插入凹模之后才开始挤压成形,所以模具的凸、凹模对正中心简单。它适于反挤压、复合挤压等多种作业。
不带导向装置的模架,称为敞开式模架,其精度依靠设备来保证。这种结构只适于精度要求不高、挤压力不大、形状简单零件的小批量生产。一般情况下,冷挤压模具均附有各种形式的导向装置,其中模具自身实行导向,是最理想的导向方式。在不出现严重偏心载荷的情况下,采取导柱导套导向,也可收到较为满意的效果。模架面积不大、受力均匀时,可采用两根导柱导向。当模座面积较大、受力不均匀、有偏心载荷时,应采用四根导柱导向。这种带导向的模架优于敞开式模架,对保证凸、凹模的中心位置及使用寿命都有好处。对于刚性小的压力机,由于成形精度必须靠模架来保证,所以尺寸设计得相当大,且采用结实的四柱导向结构。如果模具的封闭高度不足,在成形前凸模不能预先进入凹模孔口实行导向,应在模架上附加有微调凹模水平位置的螺钉,以使凸、凹模对正中心。
若以模具上的卸料装置进行分类,冷挤压模具又可以分为四种:①无任何卸料装置的敞开式模架;②具有固定卸料板的冲挤模架(见图5-4);③具有单一卸料形式的模架;④具有双级卸料装置特殊结构形式的模架。图5-5所示是结构最简单,在上下模座之间既没有安装导向装置,也没有设计卸料装置的类似一般冲压模具的结构形式。这种结构常用于有色金属材料的贯穿挤压。图5-4所示的挤镦模架常用于有色金属及低碳钢板材的冲挤加工。卸料板的作用是将废料条从凸模上卸下来。
图5-4 带有固定卸料板的冲挤模架
图5-5 敞开式简易模架
图5-6所示六种结构形式的冷挤压模架,其结构的明显特点是具有单一形式的卸料装置。图5-6a是带有弹性卸料板的敞开式模架。这种模架适于有色金属的反向挤压。若挤压件的壁厚精度要求较高,在模架上常安装有导柱和导套,如图5-6b所示。这类模架的特点是卸料板1均安装在下模座上,安装、调整和使用都很方便。图5-6c模架的弹性活动卸料圈2,则安装在模具的上部分,且兼有导向作用,即在凸模没进入凹模之前,卸料圈先进入凹模孔口实行导向。在回程时,卸料圈将抱在凸模上的挤压件卸下来。这种形式的模架结构简单,导向性能好,常用于反挤压和复合挤压。图5-6d是模具上部分具有硬性打料杆3卸料的模架。这种卸料装置具有三种功能:单纯卸料;卸料兼起导向作用;卸料导向兼起封闭挤压作用。图5-6e是常见的具有下顶出装置的模架。一般正挤压时,下部下顶杆或环形顶出套,常与挤压件的顶出端保留有一定的间隔空隙,此时下顶杆或环形顶出套只起顶件作用。反挤压时,下顶杆顶住毛坯,还起封闭挤压作用。图5-6f则是在导柱模架上,安装有下顶出装置的结构形式。在这种模架上,可以挤压较高精度的反挤压、正挤压和复合挤压件。
图5-6 单一卸料形式的冷挤压模架
a)敞开式 b)带导柱的卸料板 c)带卸料圈 d)带打料杆 e)无导柱及下顶杆 f)带导柱及下顶杆
1—卸料板 2—卸料圈 3—打料杆 4—下顶杆
图5-7 双级卸料形式的冷挤压模架
a)卸料板和下顶杆 b)卸料圈和下顶杆 c)打料杆和下顶杆
1—卸料板 2—下顶杆 3—卸料圈 4—打料杆
图5-7所示为在模架上安装有双级卸料的三种典型结构形式。图5-7a在导柱导向模具的下模座上安装了弹性卸料板1和下顶杆2两种卸料装置。这种结构常用于尺寸精度和壁厚偏差要求高的深孔零件的反挤压加工。图5-7b模架的双级卸料装置(卸料圈3和下顶杆2),分别安装在模具的上、下两部分。考虑到卸料圈3可以兼起凸凹模的导向作用,故在这种模架上没安装导柱。图5-7c模架的双级卸料都采取硬性推顶的结构形式。这种结构模架也可利用凸凹模或借助于卸料零件进行导向。在复杂零件的冷挤压模具上,这种双向硬性卸料装置,使用的场合很多,也是常见的一种模架结构形式。
5.2.3 模具结构形式的确定
确定冷挤压模具总体结构形式时,主要考虑挤压件的特点(形状、尺寸、精度)、生产批量和设备类型三个基本因素,以及设计、制造和使用三大技术环节,见表5-4。
表5-4 模具结构形式的选择
一般来说,根据挤压件的形状复杂程度、挤压材料的变形性能和精度要求及生产批量的大小,考虑现有设备状况,便可大致确定模具的总体结构形式。当模具工作部件的结构和相关位置以及各零件之间的配合关系确定之后,模具的轮廓形状和尺寸便大致确定下来了。
在构思模具总体结构时,除满足上述结构设计的基本要求外,还应进一步协调、理顺挤压件图、工序图和挤压工艺路线。调整好工艺、模具和设备三者之间的关系,使模具总体结构设计成为挤压件的质量控制与保证体系。