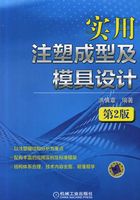
3.2 注塑成型工艺条件
注塑成型具有三大工艺条件,即温度、压力和时间,此外,还有用料量与合模力等条件。
3.2.1 温度
注塑成型过程中需要控制的温度有机筒温度、喷嘴温度和模具温度等。塑化物料的温度(塑化温度)和从喷嘴注射出来的熔体温度(注射温度)主要取决于机筒和喷嘴两部分的温度。热塑性塑料在受热时的变化曲线如图3-4所示,图中A、B、C、D四区分别对应于塑料的玻璃态、高弹性态、可塑态和分解态,机筒温度应参照C区的流动温度tb和分解温度tc来确定。喷嘴温度通常略低于机筒的最高温度,以防止熔料在直通式喷嘴口发生流延现象。模具温度一般通过冷却系统来控制。各种塑料适用的机筒和喷嘴温度范围见表3-3。各种塑料的注射温度与模具温度见表3-4。为了保证制件有较高的形状和尺寸精度,应避免制件脱模后发生较大的翘曲变形,模具温度必须低于塑料的热变形温度,见表3-5。
图3-4 恒压下热塑性塑料的温度-变形曲线
表3-3 部分塑料适用的机筒和喷嘴温度 (单位:℃)
表3-4 部分塑料的注射温度与模具温度 (单位:℃)
表3-5 常用热塑性塑料的热变形温度 (单位:℃)
3.2.2 压力
注射成型过程中的压力包括注射压力、保压力和背压力。
1.注射压力
注射压力用以克服熔体从机筒向型腔流动的阻力,提供充模速度及对熔料进行压实等。它是螺杆(或柱塞)轴向移动时其头部对塑料熔体施加的压力。若忽略熔体流动阻力,注射压力可用下式表示:
式中 pi——注射压力(MPa);
F——注射力(N);
D——螺杆基本直径(mm)。
注射压力的大小与塑料品种、注塑机类型、制件复杂程度、模具结构以及其他工艺条件等有关,通常取40~200MPa。部分塑料的注射压力见表3-6。
表3-6 部分塑料的注射压力 (单位:MPa)
注射压力还与制件的流动比有关。所谓流动比,是指熔体自喷嘴出口处开始能够在模具中流至最远的距离与制件厚度之比值。不同塑料具有不同的流动比范围,并受注射压力大小的影响,见表3-7。
表3-7 部分塑料的注射压力与流动比
注射压力pi与注射速度vi相辅相成。其他工艺条件和塑料制件一定时,注射压力越大,注射速度也越快。表达式为
式中 D——螺杆基本直径(cm);
qV——体积流量(cm3/s);
vi——注射速度(cm/s)。
式中 pi——注射压力(Pa);
pM——型腔压力(Pa),一般pM=kpi,k=0.2~0.4;
b——流道截面的最大尺寸(宽度)(cm);
h——流道截面的最小尺寸(高度)(cm);
L——流道长度(cm);
η——熔体在工作温度和许用切变速率下的动力黏度(Pa·s);
c——体积流量系数,无量纲,其数值按图3-5选取。
2.保压力和保压时间
保压力的大小取决于模具对熔体的静水压力,与制件的形状、壁厚有关。一般来说,形状复杂和薄壁制件,由于采用的注射压力大,保压力可略低于注射压力。对于厚壁制件的保压力的选择比较复杂,保压力大时容易加大分子取向,使制件出现较为明显的各向异性。在保压力与注射力相等时,制件的收缩率可降低,批量产品中的尺寸波动小,但会使制件出现较大的应力。
保压时间一般为20~120s,与物料温度、模具温度、制件壁厚、模具的流道和浇口大小有关。保压力或保压时间选择的原则是保证成型质量(其具体数据可参考表3-13)。
图3-5 体积流量系数与料流通道截面尺寸比的关系
3.背压力与螺杆转速
背压力是指注塑机螺杆顶部的熔体在螺杆转动后退时所受到的压力,简称为背压。背压主要体现对物料的塑化效果及其塑化能力,故也称为塑化压力。增大背压除了可驱除物料中的空气,提高熔体密实程度之外,还可使熔体内压力增大,螺杆后退速度减小,塑化时的剪切作用增强,摩擦热量增大,塑化效果提高。但是,背压增大后若不提高螺杆转速,熔体在螺杆槽中将会产生较大的逆流和漏流,使塑化能力降低。在实际生产中需将背压的大小与螺杆转速综合考虑。根据生产经验,背压的使用范围约为3.4~27.5MPa,其中下限值适用于大多数塑料,特别是热敏性塑料。表3-8列出了部分塑料使用的背压与螺杆转速的关系。表3-9列出了五种常用热塑性塑料的成型条件。
表3-8 部分塑料的背压和螺杆转速
注:△表示通用型喷嘴。
①数值随塑料品级发生变化。
表3-9 五种常用热塑性塑料的成型条件
(续)
3.2.3 时间
完成一次注塑成型过程所需的时间称为成型周期。它包括以下几个部分:
在保证塑料制件质量的前提下,应尽量缩短成型周期中的各段时间,以提高生产率。其中,最重要的是注射时间和冷却时间,它们对产品的质量有着决定性的影响。在生产中,充模时间一般约为3~5s,压实时间一般约为20~120s,冷却时间一般约为30~120s。可参考表3-10或表3-13,确定注射时间、保压时间。
表3-10 部分塑料的注射时间 (单位:s)
根据生产经验,注塑成型周期与制件平均壁厚有关,表3-11列出的经验方法可在生产中参考使用。
表3-11 确定成型周期的经验方法