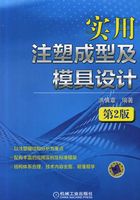
5.2 分型面选择
塑料在模具型腔凝固形成塑件,为了将塑件取出来,必须将模具型腔打开,也就是必须将模具分成两部分,即定模和动模两大部分。简单地说,分型面就是动模和定模或瓣合模的接触面,模具分开后由此可取出塑件或浇注系统。
1.分型面与型腔的相对位置
分型面与成型塑件型腔的相对位置一般有四种基本形式,如图5-1所示。
图5-1 分型面与型腔的相对位置
1—动模 2—塑件 3—定模 4—瓣合模
1)塑件全部在动模内成型(见图5-1a)。
2)塑件全部在定模内成型(见图5-1b)。
3)塑件在动、定模内同时成型(见图5-1c)。
4)塑件在多个瓣合模内成型(见图5-1d)。
具体采用哪种形式要根据塑件的几何形状、浇注系统的合理安排,是否便于推出、是否利于排气,以及对塑件同轴度和外观质量要求的高低等因素综合加以考虑。
2.分型面的选择
常见的分型面形状有平面、斜面、阶梯面、曲面,如图5-2所示。
图5-2 分型面的形状
a)平面 b)斜面 c)阶梯面 d)曲面
分型面的选择好坏对塑件质量、操作难易、模具结构及制造都有很大的影响,通常遵循以下原则:
(1)有利于脱模
1)分型面应取在塑件尺寸最大处。如图5-3所示,在A—A处设置分型面可顺利脱模,若将分型面设在B—B处则取不出塑件。
2)分型面应使塑件留在动模部分。由于推出机构通常设置在动模一侧,将型芯设置在动模部分,塑件冷却收缩后包紧型芯,使塑件留在动模,这样有利于脱模,如图5-4所示。如果塑件的壁厚较大、内孔较小或者有嵌件时,为使塑件留在动模,一般应将凹模(型腔)也设在动模一侧,如图5-5所示。
图5-3 分型面取在尺寸最大处
图5-4 分型面应使塑件留在动模
1—型芯 2—动模 3—定模
图5-5 有嵌件或小孔的分型面
a)有嵌件 b)有小孔
1—动模 2—嵌件 3—定模
3)脱模斜度小或塑件较高时,为了便于脱模,可将分型面选在塑件的中间部位,如图5-6所示,但此时塑件外形有分型的痕迹。
(2)有利于保证塑件的外观质量和精度要求如图5-7a所示的分型面方案较合理,如果用图5-7b的形式在圆弧处分型会影响外观,应尽量避免。
塑件有同轴度要求时,为防止两部分错型,一般将型腔放在模具的同一侧,如图5-7c所示。图5-7d的形式不妥。
图5-6 脱模斜度小、塑件较高的分型面
1—定模 2—动模
图5-7 分型面应保证塑件的外观质量和精度要求
(3)有利于成型零件的加工制造 如图5-8a所示的斜分型面,凸模与凹模的倾斜角度一致,加工成型零件较方便,而图5-8b的形式较难加工。
图5-8 分型面应有利于成型零件加工
(4)有利于侧向抽芯 塑件有侧凹或侧孔时,侧向滑块型芯宜放在动模一侧,这样模具结构较简单。由于侧向抽芯机构的抽拔距离都较小(除液压抽芯机构外),选择分型面时应将抽芯距离小的方向放在侧向,如图5-9a所示。图5-9b所示的分型面不妥。但是,对于投影面积较大而又需侧向分型抽芯时,由于侧向滑块合模时的锁紧力较小,这时应将投影面积较大的分型面设在垂直于合模方向上,如图5-9c所示。如采用图5-9d的形式会由于侧滑块锁不紧而产生溢料。
图5-9 分型面应有利侧向抽芯
(5)有利于排气 分型面应尽量与最后才能充填熔体的型腔表壁重合,这样对注塑成型过程中的排气有利。如图5-10a、c所示的分型欠妥,图5-10b、d所示的分型面较合理。
图5-10 分型面对排气的影响
a)、c)排气较差 b)、d)排气性好