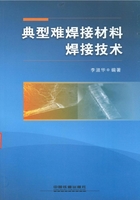
十三、如何进行6061铝合金薄板的超声波点焊?
6061铝合金具有中等强度、耐腐蚀、加工性能好、可焊接性强等优点,已广泛用于功能材料和结构材料。国内外常采用传统的焊接方法(如MIG、TIG等)对此类合金进行焊接,但所焊接的接头强度不能满足要求,且焊缝容易产生气体、夹渣、裂纹等缺陷。超声波焊接技术具有节能、环保、操作简便等突出优点,引起了各国学者极大的研究兴趣。该技术能够实现传统焊接方法难以焊接的镁合金、铝合金等低熔点材料的连接。鉴于此,国内也广泛开展了超声波焊接技术的研究。如某高校的研究者以6061铝合金为试验材料,通过优化6061铝合金超声波焊接工艺参数,研究了超声波焊接后接头的显微组织、表面形貌和力学性能,并分析铝合金表面处理对其焊接性能的影响,以期促进超声波焊接技术在轻质合金连接方面的应用。
研究者试验选用0.3mm厚的6061铝合金,试件尺寸为160mm×18mm×0.3mm,采用超声波金属点焊机对裁剪好的两片铝薄片进行焊接,如图1-28所示。选用的超声波工作频率为20kHz,振幅为35μm,焊头尺寸为8mm×8mm,焊接时间为40~140ms,气缸压强为0.1~0.6MPa,焊接压力和焊接时间均可调。气缸压强与焊接压力的关系为:焊接压力=(气缸面积/焊点面积)×气缸压强。试验设备中,焊点面积为88mm2,气缸直径为53mm,经换算得到焊接压力为气缸压强的35倍,所以焊接压力在3.5~21MPa之间变化。焊接试样剥离测试如图1-29所示。

图1-28 超声波金属点焊装置示意图
为考察表面处理状态对金属材料焊接性能的影响,研究者焊前对试件表面分别采取了四种处理方式,以分析不同表面处理状态对超声波焊接铝合金的最大剥离力的影响。四种表面处理方式为:
(1)试样A:表面无任何处理;
(2)试样B:在试件表面上滴加乙醇;
(3)试样C:用细砂纸打磨;
(4)试样D:将试件表面制备成与焊头一样的纹理。
在相同的焊接压力和焊接时间下,不同表面处理方式与最大剥离力的关系,如图1-30所示。由图可见,试样B的剥离强度最大,试样D的剥离强度最小,而试样C的剥离强度与试样A相当。试样B的剥离强度最大而试样D的剥离强度最小的原因是由于滴加乙醇会减小焊接区域的软化效应。同时,焊接面的接触点多了,即焊接面积增大了,这无疑提高了铝合金的剥离强度。表面成纹理状态的试件因为试件在焊接时表面的凸凹位置不一致,导致接触点不均匀,这无疑会对剥离强度产生一定的影响。

图1-29 焊接试样剥离测试示意图

图1-30 表面处理方式与最大剥离力之间的关系
(焊接压力为17.5MPa,焊接时间为120ms)
试样B在焊接压力分别为12.25MPa、17.5MPa和21MPa下的最大剥离力与焊接时间的关系如图1-31所示。由图可看出,三个不同焊接压力下的最大剥离力随着焊接时间的增大而增大;但当焊接时间为120ms时,最大剥离力均达到最大值,焊接时间继续增大时,最大剥离力反而下降;焊接时间为20ms时,剥离力为零。这是因为焊接时间太短,焊头对材料表面的摩擦以及超声振动不足,以至于没有足够的热量和超声能量使材料发生塑性变形而彼此结合在一起;但焊接时间过长,焊头对材料表面进行过长时间的摩擦而产生较高的热量,导致材料变形量过大,所以最大剥离力反而下降。
试样B在焊接时间为120ms条件下的最大剥离力与焊接压力的关系如图1-32所示。由图可见,最大剥离力随着焊接压力的增大而增大,但当焊接压力达到17.5MPa时,最大剥离力达到最大值,为136.478N;随着焊接压力的继续增大,最大剥离力反而下降。在试验中发现,当焊接压力为3.5MPa时焊接效果很差,几乎用手都能撕裂开。这主要是因为焊接压力过小时,焊头施加在材料上的成型力不够,许多振动能量都损失在材料与上声级之间的表面摩擦上,这严重影响了焊接的质量,甚至还会造成焊接不上的结果。当焊接压力过大时,焊头施加在材料上的成型力太大,使得两铝薄片之间的相对滑动和焊头对铝薄片的表面摩擦受到抑制,严重的会造成焊头微齿压溃铝薄片,使得焊头和底座上的铁砧上粘上铝金属,从而降低焊点的强度,故最大剥离力也会随之下降。

图1-31 焊接时间与最大剥离力之间的关系

图1-32 焊接时间120ms条件下焊接压力与最大剥离力之间关系
焊接时间120ms、焊接压力17.5MPa条件下,不同试样焊接后的接头硬度分布如图1-33所示。由图可看出,焊接接头的硬度从表面到焊缝位置处依次增大,其中试样B的硬度值最大为53.9HV,相比基体材料提高了1.31倍,试样D的硬度值最小。这可能是因为滴加乙醇后,材料抵抗超声软化的能力增强,这点在上述的强度分析中已经论述过;表面成纹理处理后,铝合金表面的凸凹位置有可能不一致,会影响铝合金的摩擦相对滑动,摩擦产生的热量也就减少了,塑性变形没有其他处理方式的剧烈,所以硬度会比较低。

图1-33 不同表面处理方式对焊接接头硬度的影响
焊接时间120ms、焊接压力17.5MPa条件下,不同试样的超声波焊接接头的显微组织如图1-34所示。由图可以看出,试样A焊缝较平整,较狭小;而试样C的焊缝区域有些结合的不好;试样D的焊缝较大;试样B的焊缝区域结合良好,并且平整规则,只有一小部分区域有些未连接好,这可能是因为破碎的氧化物分散在焊缝区域所致,但总体来看不影响焊接质量。对于以上焊缝区域出现的各种情况,可能是因为表面无任何处理时,超声波焊接使得试件表面的氧化物破碎而分布于焊缝周围,表面打磨粗糙后使得两片铝之间的凹痕位置不一致,那么当焊头在试件表面做纵向摩擦时,可能就会出现有些地方结合得很好,有些地方结合得不好。由于焊头的纹理凹痕较深且密集,所以试样D与试样C相比,焊缝较大且焊接效果差,这一点通过力学性能测试也得到证实。试样B的焊缝界面结合很好,是因为加乙醇处理后使材料焊接区域的温度和超声软化效应都高于其他两种表面处理方式,导致结合面上的塑性变形增大,从而焊缝面结合良好。

图1-34 不同试样超声波焊接接头的显微组织
焊接时间为120ms、焊接压力为17.5MPa条件下,不同试样的焊接接头的SEM照片如图1-35所示。由图可见,试样A焊缝结合面较宽且焊缝中间夹杂着白色的物体,这是因为超声波焊接后试件表面破碎的氧化物分散在焊缝周围;试样B焊缝平整规则,界面结合很紧密,焊缝处只有小部分氧化物,这说明表面加乙醇处理的试样发生了剧烈的塑性变形。

图1-35 不同试样超声波焊接接头的SEM照片
由研究者的研究与分析可见,超声波焊接0.3mm的6061铝合金的最佳工艺参数为:焊接时间120ms,焊接压力17.5MPa。焊接前,对焊接接头表面加乙醇处理,焊接接头的力学性能可以达到较优水平。所以,建议操作者焊接前最好将试件进行超声波处理,以达到最好的接头力学性能。