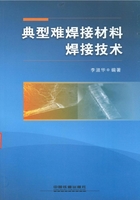
五、采用CO2激光焊焊接AZ61和AZ31镁合金各有什么特点?
激光焊接是一种比较先进的焊接镁合金的方法,具有速度快、热输入量低、焊接变形小、容易实现自动化生产等优点,比传统的弧焊方法更加适合于镁合金结构件的焊接生产。目前应用较多的两种镁合金是AZ61和AZ31,那么CO2激光焊接AZ61和AZ31这两种镁合金各有什么工艺特点呢?在不同厚度的镁合金板材激光焊接中,某院校的科研人员研究了焊接工艺参数对焊缝正面和背面熔宽以及焊缝成型的影响,并对获得的典型焊接接头性能进行了分析。
试验材料为AZ61和AZ31两种镁合金板材,板材厚度分别为1.5mm、2.0mm和2.6mm,两种材料的成分见表2-10。首先将板材切成80mm×245mm的试件,激光焊接前要将样品用丙酮清洗干净,以去除材料表面的油脂和污物。试验在CO2激光焊接试验系统上进行,如图2-22所示,此试验系统包括一个最大输出功率为2.0kW的CO2激光器、具有特殊保护功能的焊枪、特制的焊接夹具和机械自动行走机构等。焊接过程中,为了保护焊接区域正反面的熔池,氩气从焊枪和焊接夹具两面同时加入。正面的氩气从焊枪两侧加入,以旁轴形式吹出;背面的氩气从夹具背面加入到焊接夹具的气室中,可直接保护焊缝背面。
表2-10 AZ61和AZ31镁合金的化学成分


图2-22 CO2激光焊接试验系统
焊接形式采用平板对接,焊接过程不填充金属。试验过程中研究了激光功率、焊接速度、正面和背面的保护气流量等四个工艺参数变化对镁合金焊接效果的影响。
虽然激光的聚焦点也是比较重要的参数,但试验发现,当激光的聚焦点聚焦到工件表面时,镁合金才能获得较高的熔化效率。因此,焊接时始终将激光的聚焦点固定在工件表面。试验工艺条件根据不同的板材厚度进行了相应的调整,激光功率在0.8~1.5kW之间变化,采用连续方式输出。焊接速度变化范围为400~1000mm/min,正反面保护气流量在5~25L/min之间变化。
根据研究者的试验,首先让我们观察不同激光功率情况下焊缝熔宽的变化情况。焊接时,研究者采用的激光功率从0.8kW增加到1.5kW,测量了焊缝正面和背面的熔化宽度。对于不同厚度的AZ61和AZ31镁合金薄板,采用不同的焊接速度。三种厚度(1.5mm、2.0mm和2.6mm)的镁合金板采用的焊接速度分别为1400mm/min、1000mm/min和600mm/min,其主要目的是为了在所研究的激光功率范围内能获得较好的焊缝成型,防止出现烧穿或焊不透的情况。试验过程中正面和背面的保护气流量保持不变,分别为25L/min和20L/min,以保证熔池正面和背面获得良好的保护。图2-23给出了试验获得的焊缝正面熔宽随激光功率的变化关系。从图中可见,对不同厚度和不同材料的镁合金,随着激光功率的增加,正面熔宽都增大。这是因为激光功率增大,热输入增加,使得熔化的金属量增加,正面熔宽也就相应增大。不同厚度的镁合金薄板所获得的正面熔宽变化规律基本相同。
对比相同厚度的两种镁合金材料获得的正面熔宽发现,在相同的焊接条件下,对1.5mm的厚度,AZ61和AZ31获得的正面熔宽相差不大;但对2.0mm、2.6mm的板厚,AZ61获得的正面熔宽明显大于AZ31。这可能与两种镁合金的合金成分不同有关,AZ61的合金成分(主要是Al)明显高于AZ31。对镁合金来说,随着合金成分的增加,镁合金的熔点降低,焊接过程熔化的金属量和范围增加,从而使熔化宽度增加。对1.5mm的厚度,由于焊接时用的焊接速度很快,单位长度的热输入本身较小,所以对两种不同镁合金材料表现不明显,熔宽相差不大。由于所有试验的焊缝都完全熔透,所以焊后从测量的焊缝背面熔化区的宽度(如图2-24所示)可见,背面熔宽随激光功率的变化规律与正面熔宽的规律基本相同,随着功率的增大,背面熔宽增大。因此,激光功率的变化可以明显改变焊缝的尺寸。

图2-23 焊缝正面熔宽随激光功率的变化曲线

图2-24 焊缝背面熔宽随激光功率的变化曲线
焊接速度的变化对焊缝熔宽的影响如图2-25所示。为获得好的焊缝成型和保证焊接熔透,研究者焊接不同厚度的镁合金板时采用了不同的激光功率,对1.5mm、2.0mm和2.6mm的镁合金板采用的激光功率分别为1000W、1200W和1400W。保护气体流量与前面的试验相同。从图2-25中可见,焊接速度增大,正面熔宽明显减小。对比两种镁合金材料的熔池熔宽发现:在相同的焊接参数情况下,AZ61的熔宽大于AZ31的熔宽。

图2-25 焊缝正面熔宽随焊接速度的变化曲线
不同焊接速度情况下获得的焊缝背面熔宽如图2-26所示。从图中可以看出,随着焊接速度增大,背面熔宽也减小,这与正面熔宽的变化规律是一致的。焊接速度增大,单位长度的热输入减小,导致熔化金属减少,使得焊缝尺寸减小,说明焊接速度是影响焊缝尺寸和成型的又一个主要因素。从图中还可以看出,在焊接速度较低时,对1.5mm和2.0mm厚的AZ61镁合金板,存在一个背面熔宽显著变化的奇异区间;在焊接速度较小(如400mm/min)时,背面熔宽很大,然后随焊接速度的增大,背面熔宽才回到正常的曲线范围。这是因为在AZ61母材较薄时,采用的激光功率相对较大,而焊接速度又很小,使得母材大量熔化,背面熔化金属和熔池下塌都较多,从而使背面熔宽较大。同样的焊接条件下,在材料AZ31上未发现背面熔宽增大现象,这也与两者的合金成分相差较大有关。

图2-26 焊缝背面熔宽随焊接速度的变化曲线
焊接中,保护气体的加入是为了保护焊缝的正面和背面防止其氧化。焊接2.6mm厚镁合金板时,采用激光功率和焊接速度分别为1200W和800mm/min,背面保护气流量固定在20L/min,试验结果如图2-27所示。从图中可见,正面气体流量对正面和背面的焊缝熔宽影响都比较小。对AZ61材料而言,在气体流量较小时,随气体流量增大,正面焊缝宽度略有增加;但气体流量增加较大时,正面熔宽略有减小。对AZ31材料,情况则有所不同,特别是气体流量较大时,正面熔宽下降较多,这可能是因为气体流量太大时,气体带走的热量增加,使得散热明显加快,致使熔宽下降。正面气体流量对背面熔宽影响不大,随气流增大,背面熔宽略有增大。此外,还试验了背面保护气体流量(从夹具加入)大小对焊接质量的影响,采用气流量也在5~30L/min之间变化。此试验用的镁合金板厚度为2.0mm,激光功率和焊接速度分别为1200W和800mm/min,正面保护气流量固定在25L/min,试验结果如图2-28所示。从图2-28中可见,背面保护气体流量对焊缝正面和背面熔宽的大小基本没有影响。
对比图2-27和图2-28可以发现,图2-27中正面和背面熔宽相差较大,而图2-28中正面和背面熔宽相差很小。这主要是因为两个试验采用了相同的激光功率和焊接速度,但板材厚度不同,板材越厚,穿透到背面越少,形成的背面熔宽越小,这样造成了正面和背面的熔宽相差更大。虽然正面和背面保护气体流量对熔宽影响不大,但它们主要影响到正面和背面焊缝的保护效果。如果流量太小,则熔化金属表面不能获得很好的保护,表面氧化严重,呈现黑色的外观。试验发现,正面和背面的保护气体流量都应当大于20L/min才能获得好的保护效果。

图2-27 正面保护气体流量对焊缝熔宽的影响

图2-28 背面保护气体流量对焊缝熔宽的影响
后来,研究者又选择了两个典型的镁合金焊缝进行分析,典型焊缝的焊接试验条件以及正面和背面熔宽见表2-11。试样A和B分别是不同材料的2.6mm镁合金薄板对接焊缝,其焊缝正面外观形貌如图2-29所示。从图中可见,激光焊接的焊缝表观连续均匀、成型美观、无表面缺陷、焊缝狭窄、热影响区较小。两个典型焊缝的横断面形貌如图2-30所示。从图中可见,在不填充金属的情况下焊缝有一定的下塌量。同样的参数情况下,AZ61获得的熔化区面积比AZ31稍大。
表2-11 典型焊缝的工艺条件和熔宽


图2-29 典型镁合金激光焊接焊缝的表面形貌

图2-30 典型镁合金激光焊接焊缝的横断面形貌
两个典型焊缝的显微硬度测试结果见表2-12。从表中可见,熔合区和热影响区的硬度均高于母材,说明焊缝区域的硬度优于母材。拉伸试验结果发现,AZ61接头试样是在约3.18kN的拉力情况下,在母材金属区域被拉断,计算出的抗拉强度约为265MPa;而AZ31试样是在约3.03kN的拉力情况下,也是在母材金属区域被拉断,其抗拉强度约为250MPa。这表明AZ61和AZ31焊接接头的抗拉强度均高于母材的抗拉强度。因此,采用激光焊接方法焊接镁合金获得的焊接接头具有很好的力学性能。
表2-12 镁合金焊缝的显微硬度测试结果(单位:HRS)
