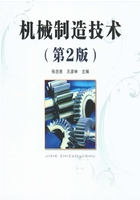
2.4 钻削、铰削与镗削加工
1.钻削加工
1)钻削加工特点
钻削加工属于孔加工方法的一种,与外圆表面加工相比,加工孔要比加工外圆困难,其原因是孔加工所用的刀具的尺寸受被加工孔尺寸的限制,刚性差,容易产生弯曲变形和振动;用定尺寸刀具加工孔时,孔加工的尺寸往往直接取决于刀具的相应尺寸,刀具的制造误差和磨损将直接影响孔的加工精度;加工孔时,切削区在工件的内部,排屑及散热条件差,加工精度和表面质量都不容易控制。
钻孔是在实心材料上加工孔的第一道工序,钻孔直径一般小于80mm。钻孔加工方式有两种:一种是钻头旋转,例如在钻床、镗床上钻孔,如图2-52(a)所示;另一种是工件旋转,例如在车床上钻孔,如图2-52(b)所示。上述两种钻孔方式产生的误差是不相同的。在钻头旋转的钻孔方式中,由于切削刃不对称和钻头刚性不足而使钻头引偏时,被加工孔的中心线会发生偏斜或不直,但孔径基本不变;而在工件旋转的钻孔方式中则相反,钻头引偏会引起孔径的变化,而孔中心线仍然是直的。

图2-52 两种钻孔方式
常用的钻孔刀具有麻花钻、中心钻、深孔钻等。
2)麻花钻
钻削加工中最常用的刀具为麻花钻,它是一种粗加工用刀具,由工具厂大量生产,供应市场。其常备规格为ф0.1~ф80mm。按柄部形状分为直柄麻花钻和锥柄麻花钻。按制造材料分为高速钢麻花钻与硬质合金麻花钻。硬质合金麻花钻一般制成镶片焊接式,直径5mm以下的硬质合金麻花钻制成整体的。
(1)麻花钻的结构要素。图2-53所示为麻花钻的结构图。它是由工作部分、颈部和柄部组成。工作部分担负切削与导向工作;颈部是柄部与工作部分的过渡部分,通常用作砂轮退刀和打印标记的部位;柄部是钻头的夹持部分,用于与机床连接并传递动力。小直径钻头可采用圆柱柄,钻头直径在12mm以上时采用圆锥柄。
麻花钻有两条主切削刃、两条副切削刃和一条横刃。两条螺旋槽形成前面,用于排屑和导入切削液,两个主后面在钻头端面上,钻头外缘上两小段窄棱边形成的刃带是副后面,在钻孔时刃带起导向作用,为减小与孔壁的摩擦,刃带向柄部方向有较小的倒锥量,从而形成副偏角。在钻心处的切削刃叫横刃,两条主切削刃通过横刃相连。

图2-53 麻花钻结构组成
(2)麻花钻的主要角度。麻花钻的主要角度有前角γom、侧后角αfm、顶角2ф、横刃斜角ψ和螺旋角β等,如图2-54所示。
①前角γom,是在正交平面中测量的前面与基面间的夹角。由于前面是螺旋面,故主切削刃上个点的前角是变化的,且变化值很大,从钻头外缘到钻心,前角由+30°减到-30°。
②后角αfm,是在平行于进给方向上的假定工作平面(以钻头为轴心,过切削刃上的选定点的圆柱面)中测量的后面与切削平面间的夹角。主切削刃上各点的后角也是变化的。由钻头外缘向中心过渡,后角逐渐增大,外缘处后角为4°~8°,近横刃处为20°~25°。

图2-54 麻花钻的几何角度
③顶角2ф,是两条主切削刃在与之平行的中心截面上投影的夹角。顶角越小,且主切削刃越长,切削宽度增加,单位切削刃上的负荷减轻,轴向力减小,这对钻头轴向稳定性有利。且外圆处的刀尖角增大,有利于散热和刀具耐用度提高;但顶角增大会使钻尖强度减弱,切削变形增大,导致扭矩增加。一般在钢和铸铁材料上钻孔时,顶角取116°~120°。标准麻花钻的顶角2ф约为118°。
④横刃斜角ψ,是主切削刃与横刃在钻头端面上投影的夹角。它是刃磨钻头时自然形成的,顶角、后角刃磨正常的标准麻花钻ψ=47°~55°,后角越大,ψ角越小,ψ角减小会使横刃的长度增大。
⑤螺旋角β,是螺旋槽最外缘螺旋线的切线与钻头轴线之间的夹角。麻花钻螺旋角一般为25°~32°。增大螺旋角有利于排屑,能获得较大前角,使切削轻快,但钻头刚性变差。小直径钻头,为提高钻头刚性,螺旋角β可取小些。钻软材料、铝合金时,为改善排屑效果,β角可取大些。螺旋角β的方向一般为右旋。
⑥主偏角κrm。主切削刃选定点的切线在基面上的投影与进给方向的夹角称为主偏角。麻花钻的基面是过主切削刃选定点包含麻花钻轴线的平面。由于麻花钻主切削刃不通过轴线,因此主切削刃上各点基面不同,各点主偏角也不相同。当顶角磨出后,各点主偏角也就确定了。
⑦横刃角度。横刃是麻花钻端面上一段与轴线垂直的切削刃,它是由两个后面相交而形成的。该切削刃的角度除横刃斜角ψ以外,还有横刃前角γoψ、横刃后角αoψ。
●横刃前角γoψ。由于的基面位于刀具的实体内,故横刃前角γoψ为负值。
●横刃后角αoψ。横刃后角αoψ≠90°∣αoψ∣。
对于标准麻花钻,roψ=-(50°~60°),αoψ=30°~36°。故钻削时横刃处金属挤刮变形严重,轴向力很大。实验表明,用标准麻花钻加工时,约有50%的轴向力由横刃产生。
(3)麻花钻切削部分结构的分析与改进。
标准麻花钻虽经多年使用,结构不断改进,但在切削部分仍存在如下问题:
①主切削刃上各点前角值差别悬殊(+30°~-30°),切削性能相差较大。
②横刃较长,又为负前角,钻削时会造成严重挤压,轴向力很大,切削条件较差。
③棱边近似为圆柱面的一部分(有小倒锥),副后角接近零度,摩擦严重。
④在主、副切削刃相交处,切削速度最大,散热条件较差,因此磨损很快。
⑤两条主切削刃很长,切屑宽,各点切屑流出速度相差很大,切屑呈宽螺旋卷状,排屑不畅,切削液难以注入切削区。
针对上述麻花钻存在的问题,使用时根据具体加工情况,对麻花钻切削部分加以修磨改进,可显著改善钻头的切削性能,提高钻削生产率。一般常采用以下措施:
①修磨横刃。可采用磨短横刃、加大横刃前角、磨短横刃的同时加大横刃前角等修磨形式改善麻花钻的切削性能。
②修磨前面。加工较硬材料时,可将主切削刃外缘处的前面磨去一部分,适当减小该处前角,以保证足够强度。当加工较软材料时,在前面上磨出卷屑槽,加大前角,减小切屑变形,降低温度,改善工件表面加工质量。
③修磨棱边。标准高速钢麻花钻的副后角为零度,在加工无硬皮的工件时,为了减小棱边与孔壁的摩擦,减小钻头磨损,对于直径大于12mm的钻头,需要磨出副后角,并留有宽度为0.1~0.2mm的窄棱边。
④修磨切削刃。为了改善散热条件,在主副切削刃交接处磨出过渡刃,形成双重顶角或三重顶角,后者用于大直径钻头。生产中还常采用一种圆弧刃钻头,就是将标准麻花钻的主切削刃外缘处修磨成圆弧。
(4)钻削用量包括钻削深度、进给量和每齿进给量、钻削速度三大部分内容。
①钻削深度ap:钻孔时钻削深度是钻头直径的一半,即ap=d/2。钻头直径由工艺尺寸决定,尽可能一次钻出所要求的孔。当机床性能不足时,才采用先钻孔再扩孔的工艺。需要扩孔时,钻孔直径取孔径的50%~70%。
②进给量f和每齿进给量af:钻削时钻头每转一转沿自身轴线方向的移动距离,单位为mm/r。麻花钻为多齿刀具,它有两条切削刃,即z=2,其每齿进给量af(mm/z)为进给量的一半,即af=f/2(mm/z)。
一般钻头进给量受钻头的刚性与强度限制,而大直径钻头受机床进给机构动力与工艺系统刚性限制。普通钻头进给量可按以下经验公式估算:f=(0.01~0.02)d。直径小于3~5mm的小钻头,一般用手动进给。
③钻削速度vc:指麻花钻外缘处的线速度,单位为m/min,其表达式为

式中:d——麻花钻直径(mm);
n——麻花钻转速(r/min)。
3)扩孔
扩孔是用扩孔钻对已经钻出、铸出或锻出的孔做近一步加工,以扩大孔径并提高孔的加工质量,如图2-55所示。扩孔加工既可以作为精加工前的预加工,也可以作为要求不高的孔最终加工。扩孔钻与麻花钻相似,但刀齿较多,没有横刃。扩孔钻按结构可分为整体式和套式两种,如图2-56所示。锥柄扩孔钻的直径为10~32mm,套式扩孔钻的直径为25~80mm。

图2-55 扩孔

图2-56 扩孔钻
与钻孔相比,扩孔具有下列特点:
(1)扩孔钻齿数多(3~8个齿),导向性好,切削比较稳定;
(2)扩孔钻没有横刃,切削条件好;
(3)加工余量小,容屑槽可以做得浅些,钻芯可以做得粗些,刀体强度和刚性较好。
扩孔加工的精度一般为IT11~IT10,表面粗糙度为Ra6.3~12.5µm。扩孔常于直径小于ф100mm的孔。在钻直径较大的孔时(D≥30mm),常先用小钻头(直径为孔径的50%~70%),然后再用相应尺寸的扩孔钻扩孔,这样可以提高孔的加工质量和生产效率。
扩孔除了可以加工圆柱孔之外,还可以加工各种特殊形状的扩孔钻(也称锪钻)来加工各种沉头座孔和锪平端面,如图2-57所示。锪钻的前端常带有导向柱,用已加工孔导向。

图2-57 锪钻
4)钻床
(1)钻床的功用。
钻床是孔加工的主要机床,在钻床上主要用钻头加工尺寸较小、精度要求不高的孔,也可以通过钻孔-扩孔-铰孔的工艺手段加工精度要求较高的孔,还可以利用夹具加工有一定位置要求的孔系。另外,钻床还可用于锪平面、锪孔、攻螺纹等工作,如图2-58所示。
钻床在加工时,一般工件不动,刀具一面旋转做主运动,一面做轴向进给运动。故钻床适用于加工没有对称回转轴线的工件上的孔,尤其是多孔加工,如箱体、机架等零件上的孔。

图2-58 钻床的加工方法
(2)钻床的主要类型
钻床根据用途和结构不同,主要有台式钻床、立式钻床、摇臂钻床、深孔钻床等类型。
①立式钻床。图2-59所示为最大钻孔直径为35mm的Z5135型立式钻床。在立式钻床上钻不同位置的孔时,需要移动工件,因此,立式钻床仅适用于中、小零件的单件、小批生产。
②摇臂钻床。在大型零件上钻孔时,因工件移动不便,想使工件保持不动,而钻床主轴能在空间调整到任意位置,这就产生了摇臂钻床。图2-60所示为摇臂钻床的外形图,摇臂3可绕立柱2回转和升降,主轴箱7又可在摇臂3上做水平移动。因此,主轴8的位置可在空间任意地调整。被加工工件可安装在工作台上,如工件较大,还可以卸掉工作台,直接安装在底座1上,或直接放在周围的地面上,这就为在各种批量的生产中,加工大而重的工件上的孔带来了很大的方便。
③其他钻床。台式钻床是放置在台桌上使用的小型钻床,其主轴垂直布置,用于钻削中小型工件上的小孔,按最大钻孔直径划分有2mm,6mm,12mm,16mm,20mm等多种规格。台式钻床小巧灵活,使用方便,主轴通过变换V带在塔形带轮上的位置来实现变速,钻削时只能手动进给,多用于单件、小批量生产。
深孔钻床是用特制的深孔钻头,专门加工深孔的钻床,如加工炮筒、枪管和机床主轴等零件中的深孔。为避免机床过高和便于排除切屑,深孔钻床一般采用卧式布局。为保证获得很好的冷却效果,在深孔钻床上配有周期退刀排屑装置及切削液输送装置,使切削液由刀具内部输入至切削部位。

图2-59 Z5135型立式钻床
1—底座;2—工作台;3—主轴;4—进给箱;5—主轴箱;6—电动机;7—立柱

图2-60 摇臂钻床外形图
1—底座;2—立柱;3—摇臂;4—摇臂升降丝杠;5、6—电动机;7—主轴箱;8—主轴
2.铰削加工
铰削是对中小直径孔进行半精加工和精加工的方法。铰削时用铰刀从工件的孔壁上切除微量的金属层,使被加工孔的精度和表面质量得到提高。在铰孔之前,被加工孔一般需经过钻孔或钻、扩孔加工。与钻孔、扩孔一样,只要工件与刀具之间有相对旋转运动和轴向进给运动,就可进行铰削加工。根据铰刀的结构不同,铰削可以加工圆柱孔、圆锥孔,可以用手操作,也可在车床、钻床、镗床、数控机床等多种机床上进行。
(1)铰刀的类型。铰刀主要用于对孔进行半精加工和精加工。加工精度可达IT9~IT7级,粗糙度可达Ra0.4~1.6µm。铰刀有多种类型(见图2-61),根据使用方法,可以分为手用铰刀和机用铰刀。
①手用铰刀一般多为直柄,直径范围为1~50mm,如图2-61(c)所示。其工作部分较长,锥角较小,导向作用好,可防止铰刀歪斜。修配及单件生产铰通孔时,常采用可调节式铰刀,当调节两端螺母使楔形刀片在刀体斜槽内移动时,可改变铰刀尺寸,调节范围为0.5~10mm,这样就实现了用一把铰刀可加工不同直径和公差要求的孔。
②机用铰刀用在机床上铰孔,常用高速钢制造,有锥柄和直柄两种,如图2-61(a)所示。大尺寸铰刀为节约材料做成套装式的。为提高加工质量、生产率和铰刀耐用度,硬质合金铰刀的应用也日渐增多。

图2-61 铰刀的种类
(2)铰刀的结构。铰刀由柄部、颈部和工作部分组成,如图2-62所示。工作部分包括导锥、切削部分和校准部分。切削部分担任主要的切削工作;校准部分起导向、校准和修光作用。为减小校准部分刀齿与已加工孔壁的摩擦,并防止孔径扩大,校准部分的后端为倒锥形状。

图2-62 机用铰刀结构
(3)直径和公差。
铰刀是定尺寸刀具,直径及其公差的选取主要取决于被加工孔的直径及其精度。同时,也要考虑铰刀的使用寿命和制造成本。铰刀的公称直径是指校准部分的圆柱部分直径,它应等于被加工孔的基本尺寸d,而其公差则与被铰削孔的公差、铰刀的制造公差G、铰刀磨耗备量N和铰削过程中孔径的变形性质有关。
①加工后孔径扩大。铰孔时,由于机床主轴间隙产生的径向圆跳动、铰刀刀齿的径向圆跳动、铰孔余量不均匀而引起的颤动、铰刀的安装偏差、切削液和积屑瘤等因素的影响,会使铰出的孔径大于铰刀校准部分的外径,即产生孔径扩张。这时,铰刀的直径就应减小一些。其极限尺寸可由下式计算
domax=Dmax-Pmax (2-11)
domin=Dmax-Pmax-G (2-12)
式中:domax——铰刀的上极限尺寸;
domin——铰刀的下极限尺寸;
Dmax——孔的上极限尺寸;
Pmax——铰孔时孔的直径最大扩张量。
②加工后孔缩小。铰削力较大或工件孔壁较薄时,由于工件的弹性变形或热变形的恢复,铰孔后孔径常会缩小。这时,选用的铰刀的直径应增大一些。可用下式表示为
domax=DmaxPmin (2-13)
domin=DmaxPmin-G (2-14)
式中:Pmin——铰孔时孔的直径最小收缩量。
(4)齿数z和槽形。
铰刀齿数一般为4~12个齿。齿数多,则导向性好,刀齿负荷轻,铰孔质量高。但齿数过多,会降低铰刀刀齿强度并减小容屑空间,故通常根据直径和工件材料性质选取铰刀齿数。大直径铰刀取较多齿数;加工韧性材料取较小齿数;加工脆性材料取较多齿数。为便于测量直径,铰刀齿数一般取偶数。刀齿在圆周上一般为等齿距分布,在某些情况下,为避免周期性切削负荷对孔表面的影响,也可选用不等齿距结构。
铰刀的齿槽形式有直线型、折线型和圆弧型三种。直线型齿槽制造容易,一般用于do=1~20mm的铰刀;圆弧型齿槽具有较大的容屑空间和较好的刀齿强度,一般用于do>20mm的铰刀;折线齿槽常用于硬质合金铰刀,以保证硬质合金刀片有足够的刚性支撑面和刀齿强度。
铰刀齿槽方向有直槽和螺旋槽两种。直槽铰刀刃磨、检验方便,生产中常用;螺旋槽铰刀切削过程平稳。螺旋槽铰刀的螺旋角根据被加工材料选取:加工铸铁等取β=7°~8°;加工钢件取β=12°~20°;加工铝等轻金属取β=35°~45°。
(5)铰刀的几何角度。
①前角γo和后角αo。铰削时由于切削厚度小,切屑与前面只有在切削刃附近接触,前角对切削变形的影响不显著。为了便于制造.一般取γo=0°。粗铰塑性材料时,为了减少变形及抑制积屑瘤的产生,可取γo=5°~10°,硬质合金铰刀为防止崩刃,取γo=0°~5°。为使铰刀重磨后直径尺寸变化小些,取较小的后角。
切削部分的刀齿刃磨后应锋利,不留刃带,校准部分刀齿则必须留有0.05~0.3mm宽的刃带,以起修光和导向作用,也便于铰刀制造和检验。
②切削锥角2ф。切削锥角主要影响进给抗力的大小、孔的加工精度和表面粗糙度以及刀具耐用度。2ф取得小时,进给力小,切入时的导向性好,但由于切削厚度过小产生较大的切削变形。同时切削宽度增大使卷、排屑产生困难,并且切入切出时间增长。手用铰刀为了减轻劳动强度,减小进给力及改善切入时的导向性,取较小的2ф值,通常ф=1°~3°。对于机用铰刀,工作时的导向由机床及夹具来保证,故可选较大ф值,以减小切削刃长度和机动时间。加工钢料时ф=30°,加工铸铁等脆性材料时ф=6°~10°。,加工盲孔时ф=90°。
③刃倾角λs。在铰削塑性材料时,高速钢直槽铰刀切削部分的切削刃沿轴线倾斜15°~20°形成刃倾角λs,它适用于加工余量较大的通孔。为便于制造硬质合金铰刀,一般取λs=0°。铰削盲孔时,使用带刃倾角的铰刀,需在铰刀端部开一沉头孔以容纳切屑,(见图2-63中虚线部分)。

图2-63 铰刀的刃倾角
(6)铰削工艺特点。
①铰削的加工余量一般小于0.1mm,铰刀的主偏角κr一般都小于45°,因此铰削时切削厚度ac很小,为0.01~0.03mm。图2-64所示为铰刀的工作情况示意图。除主切削刃正常的切削作用外,在主切削刃与校准部分之间的过渡部分上,形成一段切削厚度极薄的区域。当切削厚度小于刃口钝圆半径时,起作用的前角为负值,切削层没有被切除,而是产生弹、塑性变形后被压在已加工表面上,这时刀具对工件的作用是挤刮作用。这个极薄切削厚度区域的变形情况决定铰孔的加工精度和表面粗糙度。由于已加工表面的弹性恢复,校准部分也对已加工表面进行挤压。当铰刀磨损后,刃口钝圆半径增大,切削刃也会有挤刮的现象存在。由此可见,铰削过程是个复杂的切削和挤压摩擦过程。
②铰削过程所采用的切削速度一般都较低,因而切削变形较大。当加工塑性金属材料时会产生积屑瘤。使用切削液可以避免积屑瘤并使切削力矩减小。但由于切削厚度较小,受到切削液润滑作用的切削刃无法切入工件,只能在加工表面上滑动,使加工表面受到严重挤压和摩擦,从而显著地增加了挤压摩擦力矩。因此总的转矩反而增加。

图2-64 铰刀的工作情况
③在切削液润滑作用下,切削刃的钝圆部分只在加工表面上滑动,使工件表面受到熨压作用,熨压后已加工表面弹性恢复。熨压作用越大,其加工表面粗糙度就越小,弹性恢复越大,其加工后的入径就越小。此时,铰刀钝化也越快。
④铰削不能校正底孔的轴线偏斜。因此,机铰时可以采用浮动连接。
⑤铰刀是定直径刀具的精加工刀具,铰削的生产效率比其他精加工方法高,但是其适应性较差,一种铰刀只能用于加工一种尺寸的孔、台阶孔和盲孔。此外,铰削对孔径也有所限制,一般应小于80mm。
⑥铰孔时,应根据工件材料、结构和铰削余量的大小,综合分析决定切削液的使用。
3.镗削加工
1)镗削加工适用场合
镗削是一种用镗刀对已有孔进一步加工的精加工方法。可以加工机座、箱体、支架等外形复杂的大型零件上的直径较大的孔,特别是有位置精度要求的孔和孔系。在镗床上利用坐标装置和镗模较容易保证加工精度。镗削加工有如下特点:
(1)镗削加工灵活性大,适应性强。在镗床上除加工孔和孔系外,还可以车外圆、车端面、铣平面。加工尺寸可大亦可小,对于不同的生产类型和精度要求的孔都可以采用这种加工方法。
(2)镗削加工操作技术要求高,生产率低。要保证工件的尺寸精度和表面粗糙度,除取决于所用的设备外,更主要的是与工人的技术水平有关,同时机床、刀具调整时间较多。镗削加工时参加工作的切削刃少,所以一般情况下,镗削加工生产效率较低。使用镗模可以提高生产率,使成本增加,一般用于大批量生产。
2)镗刀
根据加工对象的不同,镗床上使用的镗刀也有所不同,其分类也是多种多样。按切削刀数量可分为单刃镗刀、双刃镗刀和多刃镗刀;按工件的加工表面可分为通孔镗刀、盲孔镗刀、阶梯孔镗刀和端面镗刀;按刀具结构可分为整体式、装配式和可调式。
(1)单刃镗刀。单刃镗刀切削部位与普通车刀相似,刀体较小,结构简单,使用方便,适用于孔的粗、精加工。用单刃镗刀镗孔时,可以校正孔轴线的偏斜或位置误差。单刃镗刀分为整体式和机夹式两种类型,如图2-65所示。整体式常用于加工小直径孔;大直径孔一般采用机夹式。在镗盲孔或阶梯孔时,为使镗刀头在镗杆内有较大的安装长度,并具有足够的位置安置压紧螺钉2和调节螺钉1,常将镗刀头在镗杆内倾斜安装,如图2-65(d)所示。镗通孔时,镗刀头安装如图2-65(b)、(c)所示。

图2-65 单刃镗刀类型
1—调节螺钉;2—压紧螺钉
(2)微调镗刀。机夹式单刃镗刀尺寸调节费时,调节精度不易控制。图2-66所示为一种坐标镗床和数控机床上常用的微调镗刀。它具有调节尺寸容易,尺寸精度高的优点,主要用于精加工。

图2-66 微调镗刀
1—镗刀头;2—微调螺母;3—螺钉;4—波形垫圈;5—调节螺母;6—固定座套
微调镗刀是先用调节螺母5、波形垫圈4将微调螺母2连同镗刀头1一起固定在固定座套6上,再用螺钉3将固定座套6固定在镗杆上。调节时,转动带刻度的微调螺母2,使镗刀头径向移动达到预定尺寸。旋转调节螺母5,使波形垫圈4和微调螺母2产生变形,以产生预紧力削除螺纹副的轴向间隙。
(3)双刃镗刀与浮动镗刀。双刃镗刀是定尺寸的镗孔刀具,通过改变两刀刃之间距离,实现对不同直径孔的加工。常用的双刃镗刀有固定式镗刀块和浮动镗刀两种。
①固定式镗刀。固定式镗刀工作时,镗刀块可通过斜楔或者在两个方向倾斜的螺钉等夹紧在镗杆上,如图2-67所示。镗刀块相对轴线的位置误差会造成孔径的误差。所以,镗刀块与镗杆上方孔的配合要求较高。刀块安装方孔对轴线的垂直度与对称度误差不大于0.01mm。固定式镗刀块用于粗镗或半精镗直径大于40mm的孔。

图2-67 固定镗刀
②可调式双刃镗刀。采用一定的机械结构可以调整两刀片之间的距离,从而使一把刀具可以加工不同直径的孔,并可以补偿刀具磨损的影响。
③浮动镗刀。浮动镗刀的特点是镗刀块可自由地装入镗杆的方孔中,不需要夹紧,通过作用在两个切削刃上的切削力来自动平衡其切削位置,因此它能自动补偿由刀具安装误差、机床主轴偏差而造成的加工误差,能获得孔的较高的直径尺寸精度(IT7~IT6)。但它无法纠正孔的直线度误差和位置误差,因而要求预加工孔的直线性好,表面粗糙度不大于Ra3.2µm。浮动镗刀主要适用于单件、小批生产,加工直径较大的孔,特别适用于精镗孔径大(d>200mm)而深(L/d>5)的筒件和管件孔。
3)镗削的工艺特点
镗孔和钻-扩-铰工艺相比,孔径尺寸不受刀具尺寸的限制,而且能使所镗孔与定位表面保持较高的位置精度。镗孔与车外圆相比,由于刀杆系统的刚性差、变形大,散热排屑条件不好,工件和刀具的热变形比较大,因此,镗孔的加工质量与生产效率不如车外圆高。
镗孔的加工范围广,可以加工不同尺寸和不同精度要求的孔。对于孔径较大、尺寸和位置精度要求较高的孔和孔系,镗孔几乎是唯一的加工方法。
镗孔可以在镗床、车床、铣床等机床上进行,具有机动灵活的优点,生产中应用十分广泛。在大批量生产中,为提高镗孔效率,常使用镗模。
4)镗床
镗床是一种主要用镗刀在工件上加工孔的机床,通常用于加工尺寸较大、精度要求较高的孔,特别是分布在不同表面上、孔距和位置精度要求较高的孔,如各种箱体、汽车发动机缸体等零件上的孔。一般镗刀的旋转运动为主运动,镗刀或工件的移动为进给运动。常用的镗床有立式镗床、卧式铣镗床、坐标镗床及金刚镗床等。
(1)卧式镗床。卧式镗床因其工艺范围非常广泛和加工精度高而得到普通应用。卧式镗床除了镗孔外,还可以铣平面及各种形状的沟槽,进行钻孔、扩孔和铰孔,车削端面和短外圆柱面,车槽和车螺纹等。零件可在一次安装中完成大量的加工工序,而且其加工精度比钻床和一般的车床、铣床高,因此特别适合加工大型、复杂的箱体类零件上精度要求较高的孔系及端面。卧式镗床的外形如图2-68所示。

图2-68 卧式镗床外形图
1—主轴箱;2—主立柱;3—主轴;4—平旋盘;5—工作台;6—上滑座;7—下滑座;8—床身;9—镗刀杆支承座;10—尾立柱
机床工作时,刀具安装在主轴箱1的主轴3或平旋盘4上。主轴箱1可沿主立柱2的导轨上下移动。工件安装在工作台5上,可与工作台一起随下滑座7或上滑座6做纵向或横向移动。工作台还可沿滑座的圆导轨绕垂直轴线转位。镗刀可随主轴一起做轴向移动。当镗杆伸出较长时,可用尾立柱10上的支承架来支承左端。当刀具装在平旋盘4的径向刀架时,可随径向刀架做径向运动。
卧式镗床的工作过程如图2-69所示。

图2-69 卧式镗床的工作过程
(2)坐标镗床。坐标镗床是一种高精度机床,主要用于加工精密的孔(IT5级或更高)和位置精度要求很高的孔系,如钻模、镗模等精密孔。它具有测量坐标位置的精密测量装置,而且这种机床的主要零部件的制造和装配精度很高,并有良好的刚性和抗振性。
坐标镗床的工艺范围很广,除镗孔、钻孔、扩孔、铰孔、精铣平面和沟槽外,还可进行精密划线,以及孔距和直线尺寸的精密测量等工作。
5)镗削加工方法
由上述可知,镗削加工既可以加工平面,也可以加工孔,但最主要的功能还是精加工孔。镗孔既可以在车床上进行,也可以在镗床上进行,但最主要的还是在镗床上进行加工。
(1)镗孔的方式。镗孔有三种不同的加工方式。
①工件旋转,刀具做进给运动。在车床上镗孔大都属于这类镗孔方式,如图2-70所示。工艺特点:加工后孔的轴心线与工件的回转轴线一致,孔的圆度主要取决于机床主轴的回转精度,孔的轴向几何形状误差主要取决于刀具进给方向相对于工件回转轴线的位置精度。这种镗孔方式适于加工与外圆表面有同轴度要求的孔。

图2-70 工件旋转、刀具进给的镗孔方式
②刀具旋转,工件做进给运动。图2-71(a)所示为在镗床上镗孔的情况,镗床主轴带动镗刀旋转,工作台带动工件做进给运动。采用这种镗孔的方式镗杆的悬伸长度L一定,镗杆的变形对孔的轴向形状精度无影响。但工作台进给方向的偏斜会使孔中心线产生位置误差。镗深孔或离主轴端面较远孔时,为提高镗杆的刚度和镗孔质量。镗杆由主轴前端锥孔和镗床后立柱上的尾座孔支承。
图2-71(b)所示为用专用镗模镗孔的情况,镗杆与机床主轴采用浮动连接,镗杆支承在镗模的两个导向套中,刚性较好。当工件随同镗模一起向右进给时,镗刀离左支承的距离由L变为L´;如果用普通镗刀来镗孔,则镗杆的变形会使工件孔产生纵向形状误差;若改用双刃浮动镗刀镗孔,因两切削刃的背向力可以相互抵消,因而可以避免产生纵向形状误差。在这种镗孔方式中,进给方向相对主轴轴线的平行度误差对所加工孔的位置精度无影响,此项精度由镗模精度直接保证。

图2-71 刀具旋转、工件进给的镗孔方式
③工件不动、刀具旋转并做进给运动。采用这种镗孔方式镗孔时,镗杆的悬伸长度是变化的,镗杆的受力变形也是变化的,镗出来的孔必然会产生形状误差,靠近主轴箱处的孔径大,远离主轴箱处的孔径小,形成锥孔。此外,镗杆悬伸长度增大,主轴因自重引起的弯曲变形也增大,孔轴线将产生相应的弯曲。这种镗孔方式只适合于加工较短的孔,如图2-72所示。

图2-72 刀具既回转又进给的镗孔方式
(2)高速细镗(金刚镗)。
与一般镗孔相比,高速细镗的特点是背吃刀量小、进给量小、切削速度高,它可以获得很高的加工精度(IT7~IT6)和很光洁的表面(Ra0.4~0.5µm)。由于高速细镗最初是用金刚石镗刀加工,故又称金刚镗,现在普遍采用硬质合金、CBN和人造金刚石刀具进行高速细镗。高速细镗最初用于加工有色金属,现在也广泛用于加工铸铁件和钢件。
高速细镗常用的切削用量如下。
①背吃刀量:预镗为0.2~0.6mm,终镗为0.1mm;
②进给量为0.01~0.14mm/r;
③切削速度:加工铸铁时为100~250m/min,加工钢件时为150~300m/min,加工有色金属时为300~2000m/min。
为了保证高速细镗能达到较高的加工精度和表面质量,所用机床(金刚镗床)需具有较高的几何精度和刚度,机床主轴支承常用精密的角接触球轴承或静压滑动轴承,高度旋转零件须经精确平衡。此外,进给机构的运动必须十分平稳,保证工作台能做平稳低速进给运动。
高速细镗加工质量好,生产效率高,在大批大量生产中它被广泛用于精密孔的最终加工。