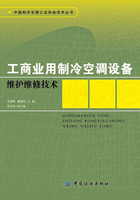
第二节 制冷原理
在长期的日常生活、科学研究和生产实践中,人们所从事的各种活动和现象均与温度密切相关。人在冬天感到寒冷而需要加热环境空气,在炎热的夏天需要把室内空气温度降低而感到凉爽;对于潮湿的空间,人们需要将水分除掉,对干燥的环境又需要加湿,这些都需要应用空调制冷技术。为了保持食品长时间的新鲜度,需要低温环境来抑制食品中霉菌的增殖;医学界保持血浆的质量和人类器官;生物科学保持各类疫苗的特性,均需要冷藏冷冻技术。这一切称为制冷(Refrigeration)技术。
制冷技术是研究和处理低温工程问题、满足人们对低于环境温度的空间或低温条件的需要而产生和发展起来的一门学科。制冷原理是制冷技术的理论基础。
制冷是指用人工的方法在一定时间和一定空间内将某物体或流体降温,使其温度降到环境温度以下,并保持这个低温。
制冷含义中须弄清楚以下问题:
(1)制冷是把被冷却物体温度降低到环境温度以下的过程。将一块灼热发红的铁放在空气中,通过辐射和对流向环境散热,逐渐冷却到环境温度,这种将高于环境温度的物体降低到环境温度的过程是自发降温,属于自然冷却,不是制冷。
(2)制冷是热量转移过程。制冷是通过某种装置或设备,从被冷却空间或流体中吸取热量,并将该热量排放到环境介质中去,使该空间或流体的温度低于环境温度。
(3)制冷过程是消耗能量的过程。根据热力学定律,制冷过程中,所选用的制冷装置或设备必须消耗能量才能完成将热量从低温向高温的传递功能。所消耗能量的形式可以是机械能、电能、热能、太阳能或其他形式的能量。
一、制冷循环
图2-2 制冷过程能流图
制冷过程通过制冷装置来实现。制冷过程中所需机器和设备的总和称为制冷机。例如,蒸气压缩式制冷机中使用的工作介质称为制冷剂(Refrigerant)。制冷机工作时,制冷剂在制冷机中进行状态变化和循环流动,同时不断地从低温热源吸取热量,向高温热源排放热量,完成热量转移,达到制冷效果。制冷剂一系列状态变化的综合称为制冷循环。图2-2为制冷过程能量消耗和热量传递示意图。
1.制冷技术区域定位 按照制冷所得到的温度范围,制冷技术区域定位如下:
(1)普通制冷:制冷温度在120K以上;
(2)深度制冷:制冷温度在120~20K;
(3)低温制冷:制冷温度在20~0.3K;
(4)超低温制冷:制冷温度在 0.3K以下。
2.制冷方法 制冷技术的主要功能是将热量从低温向高温的传递和转移。可以完成这一功能的制冷方法有多种:机械式通过制冷剂循环的制冷方法有蒸气压缩式、吸收式、吸附式、蒸气喷射式和空气膨胀式制冷;通过流体分子能量相互作用的制冷方法有脉管式和涡流管式制冷;通过电效应、磁效应和声效应等的制冷方法有热电制冷、磁制冷、热声制冷和磁流体循环制冷等。本书主要介绍蒸气压缩式制冷方法。
蒸气压缩式制冷是以压缩制冷剂蒸气来实现制冷效果的。一是利用制冷剂来转移热量,二是机械式压缩制冷剂而完成相变制冷。由制冷机械设备和制冷剂相互结合而成,如图2-3 所示。一方面,高压制冷剂在低压的密闭容器(蒸发器)中由液体汽化变为蒸气,吸收的汽化潜热来自被冷却对象,使被冷却对象(低温热源)的温度降低到环境温度以下,产生制冷效果。另一方面,利用气体升压设备(压缩机),将从低温热源吸收热量而汽化的制冷剂压力提高,在环境介质(空气或冷却水)的冷却下,在高压容器(冷凝器)中由气体液化成为高压液体,并释放液化潜热,向高温热源放热;由高压容器(冷凝器)出来的高压液体经过节流装置降为低压饱和液体与部分饱和蒸气而流向低压容器(蒸发器)。由此可见,蒸气压缩式制冷循环是由制冷剂液体在低压下汽化、蒸气被压缩升压、高压制冷剂气体液化和高压液体降压四个基本过程组成的;制冷效应是由液体制冷剂变为气体,再由气体变为液体的相变过程转移热量来达到的。
图2-3中方框表示制冷剂的状态,实线箭头一侧的名称表示制冷剂状态变化而所需要的制冷机械,箭头表示制冷剂循环方向。
图2-3 蒸气压缩式制冷循环机械设备与制冷剂结合示意图
二、制冷循环性能系数
1.制冷性能系数COP 在制冷循环中,用制冷性能系数COP(Coefficient of Performance)来评价各种循环的经济性,它是制冷循环的一个重要的热力学性能参数,定义为单位消耗能量所获得的制冷量。即:
(1)制冷系数。对于消耗电能或机械能等二次能源的制冷循环,如蒸气压缩式、热电式和空气膨胀式等制冷循环的性能系数叫做制冷系数,其值是指名义工况下,制冷机组的制冷量Q0与同一工况下制冷机组的输入功率W之比值,即:
式中:εc——制冷系数;
Q0——制冷机组的制冷量,kW;
W——制冷机组的输入功率,kW。
(2)热力系数。对于消耗热能的一次能源的制冷循环,如吸收式和蒸气喷射式等制冷循环的性能系数叫做热力系数,即:
式中:εη——热力系数;
Qcon——制冷机组所消耗的热量,kW。
(3)制热系数。热泵循环的性能系数称为制热系数,即:
式中:εh——制热系数;
Qk——热泵机组的制热量,kW。
比较上述公式可知,制冷机械的制冷系数εc的值可以大于1、小于1或等于1,而制热系数εη的值则恒大于1。
COP除了用来评价制冷机组的性能以外,还可以用来衡量制冷压缩机的性能。开启式压缩机的COP是指某一工况下,压缩机的制冷量与同一工况下压缩机轴功率之比值。封闭式压缩机的COP(也称作制冷压缩机的能效比EER)是指某一工况下,制冷压缩机的制冷量与同一工况下制冷压缩机电动机的输入功率之比值。
2.部分负荷综合性能系数IPLV 对于冷热水机组来说,绝大部分运行时间是处于部分负荷工况,在衡量机组的能效时,不只应比较名义工况下的性能,还应比较部分负荷工况下的性能。因此,采用IPLV(部分负荷综合性能系数)更能反映机组运行的经济性。IPLV计算公式如下:
IPLV=2.3%×A+41.5%×B+46.1%×C+10.1%×D
式中:A——机组100%负荷时的性能系数COP;
B——机组75%负荷时的性能系数COP;
C——机组50%负荷时的性能系数COP;
D——机组25%负荷时的性能系数COP。
3.温室效应指数GWP和TEWI 在制冷剂替代过程中,除了要求制冷剂的ODP值等于零以外,还有一个GWP值。GWP值是制冷剂的温室效应指数,是指制冷剂本身对大气的温室效应影响的程度。当前,在世界制冷空调领域,特别是在欧洲,专家们提出用TEWI(Total Equivalent Warming Impact)评价制冷剂的温室效应程度。TEWI是指在整个使用周期t中,除了制冷剂本身的GWP外,还应该把制冷装置使用该种制冷剂后所造成的温室效应也考虑进去。比如,某一种制冷剂使用后,制冷装置的耗电量明显上升,如果电来自火力发电厂,多消耗电就意味着火力发电厂要多发电,从而多产生二氧化碳等温室效应气体,间接地起到温室效应作用。因此,TEWI是制冷剂本身的作用(直接作用)和使用它的(间接作用)温室效应的总和。即:
TEWI(t)=x·GWP(t)制冷剂+y·GWP(t)发泡剂+z
式中:TEWI(t)——时间t周期内,制冷装置总的温室效应指标;
x——时间t周期内,制冷装置使用的制冷剂质量,kg;
GWP(t)制冷剂——制冷装置使用的制冷剂的温室效应指标;
y——时间t周期内,制冷装置使用的发泡剂质量,kg;
GWP(t)发泡剂——制冷装置使用的发泡剂的温室效应指标;
z——时间t周期内,制冷装置能源消耗折算成z质量的CO2(如果消耗的电来自水利或原子能,则z=0),kg。
4.生命周期特性LCCP 美国的Arthur D. Little公司提出用生命周期特性LCCP(Life Cycle Climate Performance) 来评价温室效应更趋于完善。LCCP与TEWI指标基本相同,但对TEWI进行了两项修正,一是考虑了制造制冷剂、发泡剂及其原料的能耗(如电和各种燃料)所伴随的温室效应的影响,叫做蕴含能量;二是考虑了生产制冷剂和发泡剂过程中所排放的作为温室气体的任何副产品所产生的影响,成为不易收集的排放。LCCP的计算如下:
LCCP=x·GWP(t)制冷剂+y·GWP(t)发泡剂+z+E+F
式中:LCCP——生命周期特性;
E——蕴含能量;
F——生产过程排放的作为温室气体的任何副产品所产生的影响,即不易收集的排放。
三、单级蒸气压缩式制冷理论循环
蒸气压缩式制冷循环有单级、双级和复叠式等多种形式。所谓单级蒸气压缩式制冷循环是指制冷剂在一个循环中只经过一次压缩的制冷过程。
在制冷过程中,通常使用制冷剂的压—焓图(p—h图)来描述制冷循环。
1.压—焓图 制冷循环中,不仅需要描述各个工作过程,而且需要计算各个部件和整个循环的能量变化。压—焓图的主要特点是用线段的长度来表示能量变化值,即由任意两个状态点作垂直线,两条垂线间的距离为该两点的焓差(能量变化),既精确又便捷。因此,压—焓图在制冷循环的热力计算中得到更广泛的应用。
图2-4 制冷剂的p—h图
压—焓图的结构如图2-4所示。它以绝对压力为纵坐标(为了使低压区域的热力参数表示清楚和避免压比高时由于纵、横坐标比例不当而影响数据查取精度,通常对压力取对数作为纵坐标,即lgp),单位为MPa;以焓值为横作为纵坐标,单位为kJ/kg。图上用不同的等值线簇将制冷剂在不同状态下的温度、比体积、比熵、比焓、干度等状态参数表示出来。
压—焓图由一个点、两条线、三个区域、五种状态、六类等参数线簇组成。
(1)一个点——制冷剂的临界点C。
(2)两条线——以临界点C为焦点,左边的实线为饱和液体线,线上的点代表饱和液体状态;右边的实线为饱和蒸气线,线上的点代表饱和蒸气状态。
(3)三个区域——两条饱和状态线将压—焓图分为三个区域。饱和液体线的左边是过冷液体区,过冷液体的温度低于相同压力下饱和液体的温度,该区域内的液体称为过冷液体;饱和蒸气线的右边是过热蒸气区,该区域内的蒸气称为过热蒸气,它的温度高于同一压力下饱和蒸气的温度;两条线之间的区域为气液两相区,制冷剂在该区域内处于气、液混合状态,又称湿蒸气区。
(4)五种状态——制冷剂的状态,在过冷区称为过冷状态、在饱和液体线上称为饱和液态、在两相区称为湿蒸气态、在饱和蒸气线上称为干饱和蒸气态、在过热蒸气区称为过热态。
(5)六类等参数线簇:
①等压线——水平线簇;
②等焓线——垂直线簇;
③等温线——在过冷区几乎为垂直线簇;在两相区内,等温线与等压线重合,呈现水平线簇;在过热蒸气区为向右下方弯曲的倾斜线簇;
④等熵线——向右上方倾斜的线簇,呈辐射状;
⑤等容线——向右上方倾斜的线簇,其斜率比等熵线小;
⑥等干度线——表示饱和线上和两相区内饱和气体和液体比例成分的一个参数,在两相区域内,线簇形状和方向大致与饱和液体线或饱和蒸气线相近。在饱和液体线上,x=0;在饱和蒸气线上,x=1;在两相区域内,0<x<1。
图2-5 单级蒸气压缩式制冷系统图
2.单级蒸气压缩式制冷循环系统 如第一章所述,蒸气压缩式制冷原理基于制冷剂在低压状态汽化吸收热量、在高压状态下冷凝放出热量的相变过程,将热量从低温物体转移到高温环境,达到制冷效应。完成制冷效应必须使制冷剂相变与系统硬件相结合。如图2-5所示,蒸气压缩式制冷系统由压缩机、冷凝器、节流装置、蒸发器四个基本部件组成,通过管道将它们连接成一个密封系统。
其工作过程如下:
(1)制冷剂液体在蒸发器内以低温与被冷却对象发生热交换,吸收被冷却对象的热量并汽化。
(2)产生的低压蒸气被压缩机吸入,经压缩后以高压排出。
(3)压缩机排出的高压气态制冷剂进入冷凝器,放出热量传给冷却介质(一般是常温的水或空气),凝结成高压液体。
(4)高压液体经过节流装置(膨胀阀、毛细管)节流,变成低压低温的气、液两相混合物,进入蒸发器,其中的液态制冷剂在蒸发器中蒸发制冷,产生的低压蒸气再次被压缩机吸入。如此周而复始,形成循环,完成制冷过程。
3.单级蒸气压缩式制冷理论循环及其在压—焓图上的表示 单级蒸气压缩式制冷理论循环由两个等压过程、一个等熵过程和一个等焓过程组成,是建立在以下假设基础之上的:
(1)无传热温差,即制冷剂在冷凝器中的冷凝温度等于冷却介质的温度,在蒸发器中的蒸发温度等于被冷却介质的温度,且冷凝温度和蒸发温度都是恒定的。
(2)制冷剂除了在压缩机和节流装置中发生的压力变化外,在其他设备和管道内流动时,没有流动阻力损失。
(3)制冷剂除了在换热器中发生的热量传递外,在其他设备和管道内流动时,没有任何热交换。
(4)制冷剂在冷凝器的出口为饱和液体,在蒸发器的出口为饱和蒸气。
(5)在压缩过程中不存在任何不可逆损失,即压缩过程为等熵过程。
理论循环可使分析制冷循环特性的问题得以简化,如图2-6所示。
图2-6 理论循环在T—s图和p—h图上的表示
点1表示制冷剂进入压缩机的状态。它是对应于蒸发温度T0的饱和蒸气,可由T0找到对应的p0,再由p0的等压线与x=1的饱和蒸气线相交来确定。
点2表示过热蒸气,即制冷剂出压缩机时的状态,也是进冷凝器时的状态。过程线1—2表示制冷剂蒸气在压缩机中的等熵压缩过程(s1=s2),压力由蒸发压力p0升高到冷凝压力pk。1—2绝热压缩过程要消耗机械功。由点1沿等熵线(s=c,c为常数)向上与pk的等压线相交便可求得点2。
点4表示制冷剂出冷凝器时的状态。它是对应于冷凝温度Tk的饱和液体,可由pk的等压线与饱和液体线(x=0)相交求得。过程线2—3—4表示制冷剂在冷凝器内等压地进行冷却(2—3)和冷凝(3—4)的过程。该过程中,制冷剂向冷却介质(冷却水或空气)放出热量。
点5表示制冷剂出节流装置时的状态,也就是进入蒸发器时的状态。过程线4—5表示制冷剂在通过节流装置时的节流过程。在此过程中,制冷剂的压力由pk降到p0,温度由Tk降到T0,并进入两相区,这说明制冷剂液体节流后产生少量的闪发气体。节流前后制冷剂的焓值不变,即h4=h5。节流过程是一个不可逆过程,所以用一条虚线表示4—5过程。点5可由点4沿等焓线与p0等压线相交求得。
过程线5—1表示制冷剂在蒸发器中汽化的过程。该过程是在等温、等压下进行的,液体制冷剂吸取被冷却介质的热量(即制冷)而不断汽化,制冷剂的状态沿等压线p0向干度增大方向变化,直到全部变为饱和蒸气(x=1)为止。因此,制冷剂的状态又重新回到进入压缩机前的状态点1。
制冷剂经过1—2—3—4—5—1过程后,就完成了一个理论制冷循环。
四、单级蒸气压缩式制冷实际循环
上述理论循环是为了分析热力循环而假设的,而在实际制冷循环中:
(1)冷凝和蒸发过程均为有温差传热。即冷凝器中制冷剂冷凝温度高于冷却介质温度,蒸发器中制冷剂蒸发温度低于被冷却介质温度。
(2)制冷剂通过设备和管道时,具有流动阻力损失和热量损失。
图2-7 制冷理论循环和实际循环的p—h图
(3)制冷剂在冷凝器出口为非饱和液体,产生一定程度的过冷度。
(4)制冷剂在蒸发器出口为非饱和蒸气,产生一定程度的过热度。
(5)压缩过程为非等熵过程,压缩时制冷剂与压缩机产生热交换。
(6)有空气泄漏进入制冷系统,使制冷系统存有不凝结气体。
单级制冷理论循环和实际循环见图2-7。
图2-7中,1—2—3—4—1表示理论制冷循环,4′—1表示制冷剂在蒸发器中的蒸发和压降过程,1—1′表示蒸气在回热器及吸气管道中的加热和压降过程,1′—1″表示蒸气经过压缩机吸气阀的加热和压降过程,1″—2s表示压缩机内实际的多变压缩过程,2s—2s′表示排气经过压缩机排气阀时的压降过程,2s′—3表示蒸气经排气管道进入冷凝器的冷却、冷凝及压降过程,3—3′表示液体在回热器及管道中的降温、降压过程,3′—4′表示节流过程。
1.制冷剂液体过冷制冷循环 图2-8为具有液体过冷的循环和理论循环的对比图,1—2—3—4—1为理论循环,1—2—3′—4′—1表示过冷循环。制冷剂液体的温度低于该压力下的饱和温度时称为过冷液体(点3′),过冷液体的过冷度Δtr,c=t3-t3′。
图2-8 制冷理论循环和实际循环的p—h图
从图2-8中比较具有液体过冷和非过冷制冷循环,两个循环所消耗的功率相同,即W=h2-h1,但过冷循环中单位制冷量增加Δq0=h4-h4′,因此过冷循环的制冷系数增加。可见,液体过冷对制冷循环是有利的。实际循环中通常采用节流前制冷剂液体过冷的方法,以提高制冷效果。另外,节流前制冷剂的过冷也有利于膨胀阀的稳定工作。
实际循环中通常采用过冷器、回热器(汽液热交换器)实现节流前的制冷剂液体的过冷。
图2-9 制冷系统制冷剂蒸气过热循环p—h图
2.制冷剂蒸气过热制冷循环 实际制冷循环中,为了不将液滴带入压缩机,通常制冷剂液体在蒸发器中完全蒸发后仍然要继续吸收一部分热量,因此,压缩机吸入的通常为过热蒸气。图2-9中,1—2—3—4—1表示理论循环,1′—2′—3—4—1′表示具有制冷剂过热蒸气的循环。蒸气在某压力下的温度高于该压力下的饱和温度时称为过热蒸气(状态1′)。过热蒸气的过热度Δtr=t1′-t1。
制冷剂蒸气过热循环对制冷循环的影响取决于过热过程中吸收的热量是否来自被冷却对象,以及制冷剂的性质是否产生对循环性能有利的结果。热量来自被冷却对象的过热循环叫做有效过热,热量来自其他热源的过热循环称为无效过热或有害过热。
(1)有效过热。如果过热发生在蒸发器中,或者产生在安装于被冷却对象的吸气管道上,由于过热而吸收的热量来自被冷却对象,因而产生了有用的制冷效果,这种过热称为有效过热。有效过热时,蒸发器中制冷剂的吸热过程为4—1′。相对于理论循环,有效过热时其单位质量制冷量增加值为Δq0=h1′-h1,但单位理论功也增加了,加之过热对某些制冷剂有利,而对某些制冷剂不利,因此无法直接判断制冷系数的变化。
对某一些制冷剂来讲,制冷剂蒸气过热将使循环的制冷系数增加,这类制冷剂称为过热有利的制冷剂,如CFC-12、R502;而对于某些制冷剂,过热将使循环的制冷系数降低,这类制冷剂称为过热有害的制冷剂,如HCFC-22、R717。
吸气过热虽可避免湿压缩现象的发生,但会使压缩机的排气温度升高,对于过热无利的制冷剂,其排气温度升高更大,严重时会影响压缩机的正常润滑,因此采用过热无利制冷剂时应控制其过热度。
(2)无效过热。若过热发生在蒸发器出口与压缩机吸入口之间的连接管段时,由于蒸发器出来的低温制冷剂蒸气从周围环境中吸取热量而过热,并未对被冷却物质产生任何制冷效应,这种过热称为无效过热。
无效过热时,尽管蒸发器中制冷剂的吸热过程为4—1′,但是单位质量制冷量仍为q0=h1-h4,并未增加,而蒸气比体积的增加使单位容积制冷量减少,压缩机消耗的功率增加,导致循环制冷系数降低。可见,无效过热时,制冷循环的制冷系数总是降低的,对制冷循环不利。无效过热又称为有害过热。实际循环中为避免有害过热的影响,应尽量缩短蒸发器和制冷压缩机间吸气管道的长度或对管道进行保温,以减少有害过热对系统的影响。
3.带气、液回热器的制冷循环 在系统中增加一个气—液热交换器,利用蒸发器出口低温制冷剂蒸气冷却冷凝器出口的制冷剂液体,使高压制冷剂液体过冷,同时使低压低温蒸气的有效过热。这种循环称为回热循环,如图2-10所示。
图2-10 带有回热器的制冷循环示意图
回热循环中,制冷剂在蒸发器中的吸热过程为4′—1。1—1′为回热器中的过热过程,3—3′是液体过冷过程,因此相当于有效过热循环。假若回热器与外界绝热,热交换仅发生在内部气、液之间,则回热器中能量是守恒的,蒸气过热过程吸收的热量等于液体过冷过程中放出的热量,称为回热器热负荷,即qh=h1′-h1=h3-h3′。相较理论循环,其单位质量制冷量q0=h1-h4′或 q0=h1′-h4,增加值为Δq0=h4-h4′。同有效过热循环一样,回热循环时制冷系数的影响仍与制冷剂的种类有关。
对于制冷系统产生过冷和过热现象,可以由系统内部回热引起,也可以由系统外界条件变化引起,两者对系统循环效率的影响不同。对于系统内部回热器引起的过热和过冷,因为冷凝液体过冷失去的热量使饱和蒸气过热了,从而使系统内部达到热平衡,真正转移的热量值在p—h图上仅是Δq0=h4-h4′或Δq0=h1′-h1,所以系统采用回热器后,制冷循环制冷量增长为q0=h1-h4′或 q0=h1′-h4,而非q0=h1′-h4′。但是,对于由系统外界条件变化,例如冷却水温度降低引起冷凝液体过冷、蒸发器面积增加或放置在被冷却对象中的蒸发器和压缩机间连接管道加长而引起蒸气过热,此时制冷系统的制冷量为q0=h1′-h4′,而h1′-h1不一定等于h4-h4′。
4.系统带有不凝性气体的制冷循环 系统中除气态制冷剂外,由于抽真空不彻底或外界空气往系统内泄漏的原因,系统内部存在不凝性气体。由于不凝性气体不能通过冷凝器的液封,因此积存在冷凝器上部,使冷凝器内的压力增加,从而导致压缩机排气压力提高,压缩功率增加而制冷系数下降,对循环产生负面影响。因此,应该及时排除系统中的不凝性气体。
五、单级蒸气压缩式制冷机变工况特性分析
制冷机工况指制冷机运行时的温度条件及其他附加条件,目的是为了对不同制冷机进行性能测试和使用者对不同产品的容量及其他性能指标做出对比与评价而建立的比较基准。
对一个制冷循环系统而言,它的工况条件主要包括冷凝温度、蒸发温度、节流前制冷剂液体的温度和压缩机的吸气温度等。四个工况参数中,冷凝温度和蒸发温度对制冷系统性能的影响最大,因此制冷机变工况是指在蒸发温度和冷凝温度变化时制冷循环热力学参数的变化。
制冷机在铭牌上的制冷量是在名义工况下测得的制冷量。不同制冷机的名义工况由国家标准给出。实际运行中,如果工况发生改变,制冷机的性能可以直接从制造厂提供的变工况性能曲线中查取。
1.蒸发温度对制冷循环性能的影响 如图2-11所示,冷凝温度保持不变,蒸发温度由t0降低到t′0时,循环由原来的1—2—3—4—1变为1′—2′—3—4′—1′。对制冷循环的热力学性能参数的影响如下:
(1)制冷剂的蒸发压力由p0降低到p′0。
(2)单位质量制冷量由q0减小到q′0。单位理论耗功由W0增加到W′0,从而引起循环的制冷系数必然降低。
(3)单位容积制冷量为qv=q0/v1,由于压缩机的吸气比体积v1增大为v′1,单位质量制冷量由q0减小到q′0,因此,qv随着蒸发温度的降低而迅速下降。
2.冷凝温度对制冷循环性能的影响 在图2-12中,当蒸发温度保持不变,冷凝温度由tk升高到t′k时,循环由原来的1—2—3—4—1变为1—2′—3′—4′—1。对制冷循环的热力学性能参数的影响如下:
图2-11 蒸发温度变化时制冷循环性能的变化情况
图2-12 冷凝温度变化时制冷循环性能的变化情况
(1)制冷剂的冷凝压力由pk升高到p′k。
(2)单位质量制冷量由q0减小到q′0,单位理论耗功由W0增加到W′0,从而引起循环的制冷系数必然降低。
(3)单位容积制冷量为qv=q0/v1,尽管压缩机的吸气比体积v1未变,但单位质量制冷量减小,导致qv会随着冷凝温度的增大而减小。
综上所述,降低蒸发温度,可得到较低的温度,但是循环的制冷量及制冷系数明显下降,反之亦然。因此,制冷系统运行时,在满足被冷却对象温度要求的前提下,尽量使制冷机保持较高的蒸发温度,以获得较大的制冷量和较好的经济性。冷凝温度的升高会使循环的制冷量及制冷系数下降,反之亦然。所以系统在运行中要尽量降低冷凝温度,以提高制冷循环效率。
六、单级蒸气压缩式混合工质制冷循环
混合工质制冷循环就是单级蒸气压缩式制冷循环中采用混合制冷剂作为工质。混合制冷剂包括共沸混合物(共沸制冷剂)和非共沸混合物(非共沸制冷剂)。
1.共沸混合物 对于共沸混合物,如图2-13(a)所示,指两种制冷剂以ξB的组分浓度混合时,产生一个共同沸点,在定压下相变时温度保持不变,可以作为纯制冷剂应用,所以共沸混合物的制冷循环与纯制冷剂相同。
图2-13 二元混合制冷剂相变图
2.非共沸混合物 对于非共沸混合物,如图2-13(b)所示,定压下相变时温度将发生变化。在压力恒定的条件下,制冷剂的凝结放热过程(C—B—A)中温度降低,组分X2在气相中浓度变化为C″—B″—A″,在液相中浓度变化为C′—B′—A′;吸热沸腾过程(A—B—C)中温度升高,组分X2在气相中浓度变化为A″—B″—C″,在液相中浓度变化为A′—B′—C′。由此可见,非共沸混合制冷剂在蒸发器和冷凝器中的热交换过程不是等温过程,而是一个变温过程,饱和液相线和饱和气相线间的两相区产生温度差异,称为滑移温度。混合制冷剂的混合种类不同,产生的滑移温度不同。
上述说明,非共沸混合制冷剂在单级蒸气压缩理论制冷循环中,在冷凝器和蒸发器中换热时是等压非等温的相变过程,在饱和状态下进、出口温度不同,因此,在进行热力学计算时要适当确定参数值。图2-14是非共沸混合制冷剂R407C的p—h图。
在非共沸二元混合制冷剂实际循环的定压相变过程中,混合制冷剂的气相成分和液相成分均发生变化,这种相变特征导致循环流动中的制冷剂成分与充入系统的制冷剂成分不相同。
实际运行中,下述因素将导致混合制冷剂的成分偏离规定的浓度:
(1)制冷机的生产工艺与充灌工艺过程的差异。
(2)运行工况改变造成气相成分与液相成分之间的差异。
(3)润滑油对混合物组分的不相同互溶性。
由于上述独特因素的影响,使非共沸混合制冷剂的实际制冷循环特性不同于使用纯制冷剂。当充灌混合制冷剂的制冷机运行时,由于不像使用纯制冷剂的循环系统中温度与压力之间存在明确的对应关系,所以必须测量制冷剂的压力值和气液相成分等的热力学参数,再通过相变图来确定相变温度。精确地进行非共沸混合制冷剂的制冷循环模拟和测量与计算制冷量都是比较复杂的过程。
图2-14 摇非共沸混合制冷剂R407C的p—h图
七、热泵
热泵就是为了满足人们生活和生产工艺高温的要求,人工地将热量从低温环境传送到被加热的对象中去,并维持被加热对象温度不变的泵热设备。热泵的工作过程也叫做制热过程。热泵循环和制冷循环在热力学上是相同的。同一个制冷循环系统可以兼顾热泵系统。
图2-15 制冷机和热泵热力循环比较
1.热泵循环与制冷循环的区别
(1)使用目的不同。对于制冷循环系统,目的是在消耗外界能量后将被冷却对象的热量转移到大气环境中,并保持被冷却对象的温度低于大气环境温度。对于热泵循环系统,目的是在消耗能量后将从大气环境中获得的热量转移到温度高于大气环境温度的被加热对象中,并保持这个高温条件。两者的热力循环见图2-15。
(2)工作温度区间不同。图2-15中,制冷循环为1—2—3—4—1,热泵循环为 ①—②—③—④—①,分别由两个等温过程和两个等熵过程组成。制冷循环将大气环境作为高温热源而放热,其工作温度范围在大气环境和被冷却对象温度(低温热源)之间。热泵循环把大气环境作为低温热源而吸取热量,其工作温度范围在大气环境和被加热对象温度(高温热源)之间。如果一个制冷循环的低温热源被用作冷却低于环境温度的对象而吸取热量,而它的高温热源被用作加热高于环境温度的对象而排出热量,则这个循环即担负着制冷和制热两种功能,该装置是制冷机和热泵的综合。
总之,热泵循环与制冷循环相似,共同使用同一个机械系统。主要区别在于循环系统服务对象的温度不同,热泵循环系统提供给服务对象的是高温热量,制冷系统提供给服务对象是低温冷量。
2.热泵的分类
(1)按工作原理分类。可分为气体压缩式热泵、蒸气压缩式热泵、蒸气喷射式热泵、吸收式热泵、吸附式热泵、热电式热泵、化学热泵等。
(2)按低温热源分类。可分为空气、地表水(江河、湖泊)、地下水、城市自来水、土壤、太阳能、生活或生产废热(水、气)等。
(3)按供热温度分类。可分为低温热泵(供热温度低于100℃)、高温热泵(供热温度高于100℃)。
(4)按驱动方式分类。可分为机械能、电能驱动(二次能源)和热能驱动。
(5)按热泵机组的安装形式分类。可分为单元式热泵机组、分体式热泵机组、现场安装式热泵机组。
3.蒸气压缩式空气源热泵机组 图2-16展示了一个蒸气压缩式空气源热泵机组工作流程图,这个系统兼顾制冷和制热两种功能。
图2-16 蒸气压缩式空气源热泵机组工作流程图
1—空气侧换热器2—压缩机3—四通换向阀4—板式换热器5—止回阀
6—回热型气液分离器7—单项膨胀阀 8—干燥过滤器 9—截止阀 10—储液器 11—视液镜 12—电磁阀
在实际中应用的空调装置是具有制热(热泵)和制冷(制冷机)双重功能的。夏天作为制冷机而提供冷量,冬天用作热泵来供给热量。由图2-16可知,蒸气压缩式空气热源热泵机组进行制冷循环和制热循环工作时,制冷剂的流动方向分别如图中的实线箭头和虚线箭头所示。
在这个蒸气压缩式空气源热泵系统中,当制冷循环时,空气侧换热器1被作为风冷冷凝器排出热量,板式换热器4作为蒸发器来吸取载冷剂的热量而制冷;当制热循环时,空气侧换热器和板式换热器的功能相反。如果将空气侧换热器1更换为土壤热源热交换器或地下水热源、江河水热源热交换器,就构成土壤热源热泵系统和水热源热泵系统,此时该系统的热交换器当制冷循环时,向土壤或地下水、江河水放出热量;当制热循环时,从土壤或地下水、江河水中吸取热量。板式换热器中进出的载冷剂在夏季制冷循环时提供冷媒水,在冬季制热循环时提供供热水。
在该循环系统中四通换向阀3的作用是通过交替转换四根管道的断和通,从而始终保持在制冷或制热循环时压缩机吸气端与低压连通,排气端与高压相连。如图2-16所示,制冷循环时,四通换向阀的①、②端口,③、④端口接通,而①、④端口,②、③端口断开;制热循环时,①、②端口,③、④端口断开,而①、④端口,②、③端口连通。
该空气源热泵机组设置了储液器10,其目的是存放制冷循环时从空气侧换热器1冷凝的和制热循环时从板式换热器4冷凝的液体制冷剂。除此之外,还存放制热过程中融霜期间空气侧换热器1内冷凝的制冷剂。对于系统中回热型气液分离器6,一则将吸入压缩机前的低压制冷剂蒸气进行气液分离,避免气体带液压缩而产生液击现象;二则由储液器10来的高温高压制冷剂将分离出的少量低压液体制冷剂加热汽化,同时高压制冷剂降温,起到回热作用,提高系统循环效率。
如果将图2-16中空气侧换热器1替换成为壳管式换热器,则在冬天可以利用液体媒介将浅表水、地下水、废气(水)以及土壤等热源中的热量,完成热泵循环;在夏天将系统运行的热量排入这些热源,完成制冷循环。这种功能通常由冷热水机组承担。在这种热泵循环系统中,无须考虑融霜。
八、多级蒸气压缩式制冷循环
1.采用多级蒸气压缩制冷循环的原因 对于一个单级蒸气压缩式制冷系统,当使用的制冷剂确定后,制冷循环的冷凝温度和蒸发温度就会确定一个有利于循环效率的变化范围。冷凝温度受制于外界冷却介质,变化不大。如果要想利用单级蒸气压缩式制冷系统制取更低的温度,通常采取降低蒸发压力的方式。蒸发温度越低,蒸发压力就越小,压力比(冷凝压力与蒸发压力之比)就越大。对于单级蒸气压缩式制冷循环来说,压力比增大会带来下述问题:
(1)压力比增大,制冷压缩机余隙容积内积存的制冷剂蒸气质量增大,导致压缩机的输气系数λ下降,实际输气量减少,制冷量下降。压力比过大,甚至使压缩机输气为零。
(2)压力比增大,会使制冷压缩机的排气温度升高。排气温度过高时,润滑油黏度下降,压缩机的润滑条件恶化。当排气温度超过润滑油的闪点时,会使润滑油炭化,从而堵塞油路,发生故障。排气温度过高,还易使润滑油在高温下挥发而随制冷剂一起进入换热设备,并在换热设备中积聚而形成油膜,增大传热热阻,降低传热效果。
(3)压力比增大,会使制冷机压缩过程偏离等熵程度增大;压缩机的效率下降,实际耗功增大;高压制冷剂液体节流后干度增大,制冷系数下降。
(4)蒸发压力过低,无法克服吸气阀片的预紧力,致使阀片颤抖震荡,启闭无常,影响压缩机正常工作。
(5)蒸发压力过低,制冷剂蒸气比体积增大,欲获得的相同制冷量,压缩机的几何尺寸需要增大,运行经济性差。
在实际制冷工程中,单级制冷压缩机的压力比是有限制的。即对于氨制冷剂,压力比不超过8,对于卤代烃,压力比不超过10。因此,要想达到更低的蒸发温度和高的制冷循环性能系数,就需采用双级或多级蒸气压缩式制冷循环或复叠式制冷循环。
2.两级蒸气压缩制冷循环 采用两级或多级蒸气压缩式制冷循环可降低每一级压力比,减少制冷压缩机的余隙影响,提高制冷压缩机的输气系数,提高实际输气量;可提高制冷压缩机的效率,在有中间冷却的多级压缩中,节省循环耗功,降低每一级的排气温度,提高运行的可靠性。但压缩级数过多,使系统复杂,设备费用增加,技术复杂性提高。工程中常采用两级或三级压缩循环形式。
两级蒸气压缩制冷循环是工业制冷中常用的循环形式,基本形式有一次节流中间完全冷却两级蒸气压缩制冷循环和一次节流中间不完全冷却两级蒸气压缩制冷循环。
一次节流是指向蒸发器供液的制冷剂液体直接由冷凝压力pk节流至蒸发压力p0的节流过程。中间完全冷却是指在中间冷却过程中,将低压级排出的过热蒸气等压冷却到中间压力下干饱和蒸气的冷却过程。中间不完全冷却是指在中间冷却过程中,将低压级排出的过热蒸气等压冷却降温而未达到饱和状态的冷却过程。不同中间冷却方式的采用与制冷剂的特性有关,对那些吸气过热有利的制冷剂可采用中间不完全冷却方式;对那些吸气过热不利的制冷剂,可采用中间完全冷却方式。
(1) 一次节流中间完全冷却两级蒸气压缩制冷循环,其原理如图2-17所示。
图2-17 一次节流中间完全冷却两级蒸气压缩制冷循环原理图
一次节流中间完全冷却两级蒸气压缩制冷理论循环的工作过程如图2-18所示。
图2-18 一次节流中间完全冷却两级蒸气压缩制冷理论循环热力状态图
1—2:低压级等熵压缩过程,消耗功率PO.L.(低压级理论功率)。
2—3:低压级排气在中间冷却器内的等压冷却过程,低压级排气被完全冷却成中间压力pm下的干饱和蒸气,即中间完全冷却过程。其放热为Qm1。
3—4:高压级等熵压缩过程,消耗功率PO.H. (高压级理论功率)。
4—5:制冷剂蒸气在冷凝压力pk下的等压冷却冷凝过程,向冷却介质放热Qk。
5—6:制冷剂液体经节流阀Ⅰ由pk节流至pm的过程,并向中间冷却器供液Mr2。
5—7:制冷剂饱和液体Mr1在中间冷却器盘管中的过冷过程,盘管内的制冷剂液体向盘管外的制冷剂放热Qm2。
7—8:制冷剂过冷液体经节流阀Ⅱ由pk节流至p0的过程,即一次节流过程。
8—1:制冷剂Mr1在蒸发器内等压汽化吸热过程,从被冷却对象获取冷量Q0。
6—3:中间冷却器内,制冷剂Mr2在pm下蒸发吸热过程,吸热为Qm= Qm1+Qm2。
由图2-18可以看出,一次节流中间完全冷却两级蒸气压缩制冷理论循环比单级蒸气压缩理论循环节约的绝热压缩功为T—s图中面积3—2—4′—4—3;高压液体节流前过冷,单位质量制冷量增加为p—h图中的h5-h7。
(2)一次节流中间不完全冷却两级蒸气压缩制冷循环,其原理如图2-19所示。
图2-19 一次节流中间不完全冷却两级蒸气压缩制冷循环原理图
一次节流中间不完全冷却循环和一次节流中间完全冷却循环的主要区别是高压级制冷压缩机吸入的制冷剂不是中间压力pm下的干饱和蒸气,而是具有一定过热度的过热蒸气(图2-20中的状态3),所以称作中间不完全冷却。
图2-20 一次节流中间不完全冷却两级蒸气压缩制冷理论循环热力状态图
一次节流中间不完全冷却两级蒸气压缩制冷理论循环的工作过程类似于一次节流中间完全冷却两级蒸气压缩制冷理论循环,不同之处在于,低压级的压缩过热制冷剂气体与来自中间冷却器的部分饱和蒸气在高压级吸气管道混合后进行二级压缩。
比较图2-18和图2-20可以看到,由于一次节流中间不完全冷却两级蒸气压缩制冷循环的低压级排气冷却效果差,因此它比一次节流中间完全冷却两级蒸气压缩制冷循环的压缩功消耗得多,制冷系数低。
3.带闪发蒸气分离器的多级压缩制冷循环 从冷凝器来的高压液态制冷剂节流降压至某中间压力时,在闪发蒸气分离器中气液分离,闪发蒸气通入压缩机进行压缩,液体再经节流降压至蒸发器吸热制冷。由于有了闪发蒸气分离器,达到了节约压缩机功耗的目的,故一般也把闪发蒸气分离器称为经济器或节能器。目前采用经济器的循环主要有:
(1)带经济器的螺杆式压缩机的二次吸气制冷循环。如图2-21(a)所示,在螺杆式压缩机冷热水机组中可以设立吸气口和经济器。经济器有过冷及无过冷两种形式,螺杆式压缩机组常用过冷型,其流程和制冷循环p—h图如图2-21(b)所示。
图2-21 带经济器的二次吸气制冷循环(螺杆式压缩机)
由图2-21可见,由冷凝器出来的高压液体一部分mR2经过节流到pm压力后进入经济器,在其内蒸发吸收热量将另一部分高压液体mR1过冷,使其在蒸发器内增加了Δq的制冷量。经济器内蒸发的温度较低,制冷剂mR2与压缩机第一级出来的mR1高温气体混合降温,经过二级压缩到高压p2进行冷凝,节约能耗ΔP。因此,带经济器的二次吸气制冷循环,其冷量增加,功耗减少,性能系数COP明显提高。
(2)带经济器的多级离心式压缩制冷循环。离心式压缩机属于速度型压缩机,每一级压缩比较小,需要多级压缩。离心式压缩机可以采用两个、三个或多个叶轮,实现对制冷剂气体的多级压缩,同时可以在叶轮之间设立吸气口和经济器。吸气口数目一般比压缩级数(即叶轮数)少一个,经济器数目和吸气口数目相等。
这种带经济器的多级压缩制冷循环的优点有:
①可减少压缩过程中的过热损失和节流过程中的节流损失,能耗少,性能系数高。据有关文献报道,带经济器的三级离心式制冷机组名义工况下的性能系数COP比单级机组高5%~20%,部分负荷下的COP可提高20%。
②可以制取较低的蒸发温度,适用范围大。
③可降低离心机工作转速或省去增速装置,噪声低,振动小,从而提高机组运行的可靠性。国内外均有这种离心式冷水机组及热泵机组产品。
④改善调节特性,扩大压缩机的稳定工作范围。
在多级离心式压缩制冷循环中,带有经济器的压缩级数越多,压缩就越接近等温过程,功耗就越少,循环效率就越高。但压缩级数过多,使系统庞杂,设备增大。对使用卤代烃类制冷剂的多级离心式压缩机,工程中常采用三级压缩三次节流带经济器的循环形式。多次节流是指向蒸发器供液的制冷剂液体先由中间冷却器前的节流器从冷凝压力pK节流至中间压力pm,再由蒸发器前的节流器将中间压力pm下的制冷剂液体节流至蒸发压力p0的过程。
以卤代烃为制冷剂的三级压缩三次节流带经济器的离心式制冷机工作原理如图2-22所示。
图2-22 三级压缩三次节流带经济器的离心式蒸气压缩制冷循环
A—低压级压缩机B—蒸发器C—三级节流阀D—低压级经济器E—二级节流阀
F—高压级经济器G—一级节流阀H—冷凝器J—高压级压缩机
K—中压级压缩机
如图2-22所示,在蒸发器B中,吸热后的低压制冷剂蒸气Ⅲ经离心压缩机的第Ⅰ级(低压级)A压缩使其压力由蒸发压力p0升压至中间压力pm.Ⅱ.。升压后的制冷剂蒸气与经第Ⅰ次补气的
Ⅱ混合后被冷却至中间压力pm.Ⅱ.下的过热蒸气,并进入第Ⅱ级压缩。离心压缩机的第Ⅱ级(中压级)K将制冷剂蒸气
Ⅲ+
Ⅱ从中间压力pm.Ⅱ.升压至中间压力pm.Ⅰ.,然后与经第Ⅱ次补气的
Ⅰ混合后被冷却至中间压力pm.Ⅰ.下的过热蒸气,再一次输入第Ⅲ级压缩。离心压缩机的第Ⅲ级(高压级)J将制冷剂蒸气
Ⅲ+
Ⅱ+
Ⅰ从中间压力pm.Ⅰ.升压至冷凝压力pK,排入冷凝器H中等压冷却冷凝成饱和液体。制冷剂饱和液体
经一级节流阀G节流至中间压力pm.Ⅰ.,并被全部送入高压级经济器F,其中一部分压力为pm.Ⅰ.的液体被用于冷却第Ⅱ级(中压级)排出的过热蒸气。被冷却的第Ⅱ级过热蒸气和一级节流时产生的饱和蒸气
Ⅰ混合成为状态点5′的过热蒸气,并进入高压级压缩机J进行压缩。高压级经济器F底部未汽化的压力为pm.Ⅰ.的饱和液体经二级节流阀E节流至中间压力pm.Ⅱ.后被送入低压级经济器D。同样,一部分压力为pm.Ⅱ.的液体蒸发为饱和蒸气
Ⅱ与来自第Ⅰ级离心压缩机A的过热蒸气混合成为状态点3′的过热蒸气,并进入中压级压缩机K进行压缩。低压级经济器D底部未汽化的压力为pm.Ⅱ.的饱和液体经三级节流阀C节流至蒸发压力p0后被送入蒸发器吸热制取冷量Q0。出蒸发器的制冷剂低压蒸气被低压级压缩机A吸入后继续进行压缩。
三级压缩三次节流带经济器的离心式蒸气压缩制冷循环的热力状态见图2-23。
图2-23 三级压缩三次节流带经济器的离心式蒸气压缩制冷循环热力状态图
由图2-23可见,三次节流前的制冷剂液体均处于饱和液体状态,因此节流级数越多,每一级的等焓节流线越短,节流后各级的干度越小,有利于增加制冷量;还可以看出,三级压缩过程中带有两个经济器,每经过一个带经济器的压缩,功耗就减少一部分,因此压缩级数越多,压缩过程越省功。
九、复叠式蒸气压缩式制冷循环
1.采用复叠式蒸气压缩制冷循环的原因 对于采用氨、HFC-134a或HCFC-22作为制冷剂的蒸气压缩式制冷装置,尽管采用多级压缩比采用单级压缩可以获得较低的温度,而且可以降低压缩机的排气温度、减少压缩机的总耗功量。但是为了获得更低的蒸发温度,多级制冷循环采用中温制冷剂时却受到高凝固点的限制,采用低温制冷剂时却受到低临界点的限制,因此必须采用复叠式制冷循环。其原因如下:
(1)蒸发温度必须高于制冷剂的凝固点,否则制冷剂无法进行制冷循环。如氨的凝固点为-77.7℃,不能制取更低的温度。
(2)制冷剂的蒸发温度过低时,其相应的蒸发压力也非常低。如氨在t0=-65℃时,p0=1.565×104Pa(0.1565bar);HFC-134a在t0=-62℃时,p0=1.44×104Pa(0.144bar)。但是,当蒸发压力低于1×104~1.5×104Pa(0.1~0.15bar)时,空气容易渗入系统,严重影响制冷循环的正常运行,因此须采用沸点更低的制冷剂。
(3)蒸发压力很低时,气态制冷剂的比体积很大,单位容积制冷能力大为降低,势必要求压缩机的体积流量增大。
所以,为获得-60~-90℃的低温,就不宜采用氨等中温制冷剂,而需要采用低温制冷剂,如HFC-23。低温制冷剂的特点是凝固点低,且沸点低。这时,它们在低温条件下的饱和压力高于大气压力,但是,这类制冷剂的临界温度很低,临界压力很高,如HFC-23,临界温度为25.9℃,临界压力为4.83×106Pa(48.3bar)。若采用一般冷却水,由于水温接近临界温度,使气态制冷剂难以冷凝,即使被冷凝,也接近临界点,不但冷凝压力高,而且比潜热很小,制冷效率很低。因此为了降低冷凝压力,就必须对这种采用低温制冷剂的循环附设人造冷源,使这种制冷剂冷凝。也就是说,采用这种制冷剂的制冷装置虽然可以制取更低的温度,但它不能单独工作,需要另一台制冷装置与之匹配运行,即所谓复叠式蒸气压缩制冷。
2.复叠式蒸气压缩制冷循环的工作流程 如图2-24(a)所示,复叠式蒸气压缩制冷循环由两个独立的制冷循环组成,左端为高温级制冷循环,制冷剂为HCFC-22;右端为低温级制冷循环,制冷剂采用HFC-23。蒸发冷凝器既是高温级制冷循环的蒸发器,又是低温级制冷循环的冷凝器,也就是说,高温级制冷循环为低温级制冷循环附设了一个冷源,依靠高温级制冷剂的蒸发,吸收低温级制冷剂的冷凝热,从而保障低温级的正常运行,制取低的温度。
图2-24(b)是HCFC-22和HFC-23组成的复叠式蒸气压缩制冷循环的温—熵图。由于两种制冷剂物理性质不同,所以,同一幅温—熵图绘有两套饱和液线和饱和蒸气线,HCFC-22的饱和线在上部,HFC-23的饱和线在下部;两种制冷剂除等温线和等比熵线相同外,其他各参数线均不一致。图中低温级HFC-23制冷循环的蒸发温度为-82.3℃,相应的蒸发压力为1×105Pa(1.0bar);冷凝温度为-25℃,相应的冷凝压力为1.196×106Pa(11.96bar)。为了保证HFC-23的冷凝温度,则要求高温级HCFC-22制冷循环的蒸发温度低于低温级的冷凝温度,一般低3~5℃。如果取5℃,则图2-24(b)中的高温级HCFC-22制冷循环的蒸发温度应为-30℃,相应的蒸发压力为1.64×105Pa(1.64bar);如果HCFC-22的冷凝温度为30℃,冷凝压力为1.188×106Pa(11.88bar),压缩比等于7.24,则采用单级压缩即可。从这里可以看出,复叠式制冷循环发挥了HCFC-22和HFC-23各自的优点,又克服了它们的不足,使得制取很低的温度成为可能。
图2-24 复叠式蒸气压缩制冷循环
由三个单级压缩系统组成的三元复叠式制冷循环由高温、中温、低温三部分组成,高温部分可采用HCFC-22或R502等制冷剂,中温部分可采用HFC-23等制冷剂,低温部分可采用R14等制冷剂,最低蒸发温度可达-130~-120℃。如果要制取更低的温度,可采用多级复叠形式。
十、 制冷系统的热交换设备
制冷系统的热交换器通常采用间壁式换热器,即传热时冷、热两种流体处于固体壁面的两侧,例如在卤代烃卧式冷凝器中,冷却水在管内流动,卤代烃蒸气在管外凝结,蒸气凝结时放出的热量通过管壁传递给冷却水。这种热量由壁面一侧的流体穿过壁面传给另一侧流体的过程,称为传热过程。制冷系统中,间壁式传热设备主要有蒸发器、冷凝器、回热器及板式热交换器等。制冷系统热交换器所涉及的传热过程包括通过平壁传热、通过圆管的传热和通过肋壁的传热。
图2-25 平壁传热方式
tf1—热流体温度tf2—冷流体温度
tw1—热流体侧壁面温度
tw2—冷流体侧壁面温度
—单位时间通过平壁的传热量
1.热交换设备中的传热学基本知识
(1)平壁传热。通过平壁的传热方式如图2-25所示。
由传热学可知,平壁传热过程所传递的热量正比于冷、热流体的温差及传热面积,即傅里叶公式:
式中:——单位时间通过平壁的传热量,W;
K——传热系数,是热交换设备的一个重要指标,表示温差为1℃,面积为1m2时的传热率,W/(m2·℃);
A——传热面积,m2;
Δtm——冷、热流体间的传热温差,℃。
单位面积热流密度为:
式中:——平板单位面积热流密度,W/m2。
传热学指出,单层平壁的平壁传热系数为:
式中:R0——单层平壁传热总热阻,m2·℃/W;
Rw——热流体与平壁间的放热热阻,m2·℃/W;
R—— 平壁导热热阻,m2·℃/W;
Rn—— 冷流体与平壁间的放热热阻,m2·℃/W;
αw——热流体与平壁间的放热系数,W/(m2·℃);
δ—— 平壁层壁厚,m;
λ—— 平壁层导热系数,W/(m·℃);
αn——冷流体与平壁间的放热系数,W/(m2·℃)。
对于n层平壁,传热系数为:
图2-26 圆管传热方式
ri—圆管内径ro—圆管外径
(2)圆管传热。通过圆管的传热方式如图2-26所示。
制冷系统热交换器常采用壳管式热交换设备。当圆管长度为l,圆管内、外径分别为di、do(相应半径为ri、ro)时,以圆管外表面积Ao为计算基准的单层圆管稳定传热量为:
p=Ko·Ao·(ti-to)=Ko·πdol·(ti-to)
式中:p——单位时间通过单层圆管的传热量,W;
Ko——以圆管外表面积为计算基准的传热系数,W/(m2·℃);
Ao——圆管外表面积,m2;
do——圆管外直径,m;
l——圆管长,m;
ti、to——圆管内、外侧流体温度,℃。
单位长度热流密度为:
式中:ql——圆管单位长度热流密度,W/m2。
传热学指出,单层圆管的传热热阻是高温侧流体放热热阻、圆管传热热阻、低温侧流体放热热阻之和。单位长度单层圆管传热系数为:
以圆管外表面积为计算基准的传热系数为:
工程计算中,当圆管的内、外径之比<2时,上式可写成:
式中:dm——圆管内、外径的算术平均值,m。
热交换器在投入使用后,流体中的润滑油、冷媒水和冷却水会在传热表面形成污垢,增加了传热热阻。因此,实际计算时应考虑污垢系数的传热系数,即:
式中:γi,γo——换热器换热面内、外壁污垢系数。
2.蒸发器 制冷系统的热交换设备主要有蒸发器、冷凝器、回热器、中间冷却器、板式热交换器等。
蒸发器是制冷系统中用于制冷剂与被冷却介质间进行热交换的设备,制冷剂在内部蒸发,吸收载冷剂的热量,达到制冷的目的。按被冷却介质种类的不同,蒸发器可分为冷却液体、冷却空气等类型。
(1)冷却液体蒸发器。冷却液体的蒸发器主要用于冷却水、盐水及其他溶液的载冷剂,主要有卧式壳管式和沉浸式。
①卧式壳管式蒸发器。卧式壳管式蒸发器一般用于闭式的载冷剂系统,有满液式和干式两类。
a.满液式。其工作过程是,制冷剂沿壳程流动,载冷剂沿管程流动。制冷剂液体节流后进入蒸发器的壳程,吸收载冷剂热量。吸热汽化后的制冷剂蒸气上升至回气包中进行气液分离,干饱和蒸气通过回气管进入制冷压缩机,饱和液体流回蒸发器筒体内继续吸热汽化。卤代烃类制冷剂用满液式蒸发器中的润滑油较难排出蒸发器。载冷剂在管程内的流速为1.0~2.5m/s。
满液式蒸发器的结构紧凑,传热性能好,制造工艺简单;为了强化卤代烃类制冷剂侧的沸腾换热,用于卤代烃类制冷剂的卧式壳管蒸发器采用低肋铜管。冷却普通淡水时,其出水温度应控制在2℃以上,以免冻裂传热管。满液式蒸发器制冷剂充注量大,且有回油问题,所以原来多用于价格较低廉且难溶于润滑油的氨制冷剂中。近年来,由于提高性能系数的需要,HCFC-22冷水机组采用满液卧式壳管蒸发器逐渐增多。
氨用满液式蒸发器,其结构如图2-27所示。
图2-27 氨用满液式壳管蒸发器
蒸发器的筒体由钢板焊制而成,筒体两端焊有管板,板间焊接或胀接许多根水平传热管。两端管板外侧装有带隔板的封盖,靠隔板将水平管束分为几个管组(流程),使被冷却液体顺序流过各管组,以提高管中液体流速,增强传热效果。液态制冷剂经膨胀阀降压后,从筒体下半部进入,充满管外空间,受热后形成的气泡不断浮升至液面,这样,传热表面基本均与液态制冷剂接触。在满液式蒸发器中,由于制冷剂汽化形成大量气泡,使其液面高于静止时的液面,因此,为了避免液态制冷剂被带出蒸发器,充注的液量不应浸没全部传热面。一般的,氨充液高度为筒径的70%~80%,卤代烃类制冷剂产生泡沫现象比较严重,充液高度为筒径的55%~65%。吸热后形成的气态制冷剂经筒体顶部液体分离器流出,被吸入压缩机。氨用卧式壳管蒸发器筒体底部焊有集油罐,随制冷剂被带入的润滑油因密度较大而沉于其中,以便定期排放。
卤代烃类制冷剂用满液式蒸发器,其基本结构与氨用相似,如图2-28所示。
图2-28 卤代烃类制冷剂用满液式蒸发器
1—端盖2—筒体3—回气包4—管板5—橡胶垫圈6—换热管束
卤代烃类制冷剂用满液式蒸发器的基本结构与氨用满液式蒸发器的主要区别在于,卤代烃类制冷剂用满液式蒸发器壳体内的换热管可采用直径20mm以下的滚压成薄壁低肋的紫铜管或黄铜管,以增强传热效果。
b.干式。构造与满液式壳管蒸发器相似,主要不同点在于,载冷剂沿壳程流动,制冷剂液体沿管程流动,制冷剂的充灌量少,通常在蒸发器出口处制冷剂全部蒸发完,成为饱和或过热状态,故称为干式,主要用于卤代烃类制冷剂制冷系统。工程中常用的有直管式和U形管式。
干式蒸发器的充液量一般占管内容积的40%左右,明显比满液式蒸发器少,因此制冷剂液体静压力的影响较小,排油方便,载冷剂结冰也不会胀裂换热管;同时还具有结构紧凑,传热系数高等优点。缺点是管组内供液不均匀,折流板外周与壳体间容易产生载冷剂泄漏旁流,影响其传热效果。干式蒸发器属低温设备,筒体外需设置隔热层。
卤代烃类制冷剂用直管式干式蒸发器,其结构如图2-29所示。
图2-29 直管式干式蒸发器
1—前端盖2—圆缺形折流板3—后端盖4—支座5—螺塞6—换热管束7—筒体
制冷剂液体经节流后从蒸发器前端盖的下方进口进入管程内,经2~4个流程吸热后由同侧端盖上方出口引出。直管式蒸发器的水平光滑铜管束上套有多块相互颠倒排列的切去弓形面积的圆缺形折流板,载冷剂在壳程圆缺形折流板的引导下沿管间流动,在筒身的另一端上方(或侧面)流出。由于换热管内外的制冷剂与载冷剂的放热系数相差悬殊,常采用各种形式的肋化来增强蒸发器的传热。
U形管式干式蒸发器,其结构如图2-30所示。
图2-30 U形管式干式蒸发器
1—端盖2—圆缺形折流板3—筒体4—换热管束
由多根半径不等的U形管组成,这些U形管的开口端胀接在同一块管板上,其他结构与直管式相似。制冷剂液体节流后由端盖下部进入,经过两个流程吸热汽化后从端盖上方出口引出。其优点是不会因不同材料的膨胀率的差异而产生内应力以及U形管束可以比较方便地抽出来清洗。
②沉浸式蒸发器。沉浸式蒸发器一般用于开式载冷剂系统,有立管式、蛇管式、螺旋管式和V形管式等形式,并按一定的排列方式沉浸于载冷剂池中。
a.立管式蒸发器,其结构如图2-31所示。
图2-31 立管式蒸发器
1—过滤器2—节流阀3—截止阀4—气液分离器5—上集管
6—电动机7—搅拌器8—换热立管束9—下集管10—浮球阀11—集油包12—液面位置
立管式蒸发器全部由无缝钢管焊制而成。每一组列管上各有上下两根水平集管,即上面的蒸气集管与下面的液体集管。沿集管的轴向焊接有四排直径较小、两头稍有弯曲的立管,与上下集管接通;沿集管的轴向每隔一定间距设有直径稍大的粗立管。节流后的制冷剂液体从中间的进液管进入蒸发器,在下集管和立管中汽化吸热后的制冷剂蒸气上升至上集管。上集管的一端设置气液分离器,并通过下液管使分离后的液体回到下集管。
立管式蒸发器工作时,细立管中制冷剂的汽化强度大,促使氨液上升,相应地使在粗立管中的氨液下降,形成循环对流。汽化的制冷剂沿上集管进入气液分离器。润滑油积存在底部的集油包中,需定期放出。
b.蛇管式蒸发器,其结构如图2-32所示,常用于小型卤代烃类制冷剂制冷装置。
图2-32 蛇管式蒸发器
1—换热蛇管束2—换热管束支架3—搅拌器4—电动机
蛇管式蒸发器通常由一组或几组铜管弯成的蛇形盘管组成。为保证盘管供液均匀,采用液体分配器从上部向多组蛇形盘管供液。
(2)冷却空气的蒸发器。在冷却空气的蒸发器中,制冷剂沿管内流动,并与管外的空气进行热交换。冷却空气的蒸发器主要有冷却自然对流空气的冷却排管和冷却强迫对流空气的冷风机。
a.冷却自然对流空气的冷却排管。自然对流形式常用于冰箱、冷藏柜、冷藏车、冷藏库等处。如图2-33所示,冷藏库多采用安装在顶棚下或墙壁的排管冷却库内空气,排管为光管或片距6~12mm的肋管。由于空气侧为自然对流,故这种冷排管的传热系数很低。
图2-33 光滑管集管式排管
图2-34 卤代烃类制冷剂干式冷风机结构示意图
b.冷却强迫对流空气的冷风机。为了增强传热,在间冷式冰箱的冷冻室、空调机组、冷藏库及除湿机等处多采用强制对流式的直接蒸发式空气冷却器。强制对流式蒸发器与自然对流蒸发器相比,具有传热效果好、结构紧凑等优点,在冷冻、空调设备中得到广泛应用。
卤代烃类制冷剂干式冷风机,其构造示意图如图2-34所示。
来自节流装置的低压制冷剂湿蒸气通过分液器分成多通路,吸热蒸发后为气态制冷剂,汇集到集管中流出;而空气以一定流速从肋片管的肋片间掠过,将热量传给管内流动的制冷剂,温度降低。蒸发温度较低时,考虑到肋片处结露或结霜,应加大肋片间距。
图2-35是五种常见的分液器示意图。图中a是离心式分液器,来自膨胀阀的制冷剂沿切线方向进入一小室,充分扰动后的气液混合物,从小室顶部沿径向出流,至各分液管。b、c是碰撞式分液器,来自膨胀阀的制冷剂以高速进入分液器后,首先与壁面碰撞,形成均匀的气液混合物,然后再进入各路分液管。d、e是降压式分液器,制冷剂流体先流经分液器腔室内的狭窄通道,增加流动速度。
图2-35 分液器结构
a—离心式分液器b、c—碰撞式分液器d、e—降压式分液器
上述分液器使制冷剂首先通过缩孔,增大流速,克服重力影响,达到气液充分混合,并保证制冷剂均匀分配给各路分液管。分液器应垂直使用。
氨用落地式冷风机,其结构示意图如图2-36所示,由箱体上部的风机(轴流式或离心式)、中部淋水—蒸发室和下部的水盘—支架三大部件构成。淋水—蒸发室由长方形箱体内肋片蛇管蒸发器和淋水装置构成,蒸发器上部装有淋水融霜装置。水盘—支架用于支撑箱体和保持足够的回风面积。
图2-36 氨用落地式冷风机
1—风机2—箱体3—融霜淋水管4—制冷剂回气集管5—制冷剂供液集管
6—支架7—承水盘8—回风口9—蒸发器换热管束
氨用落地式冷风机在工作时,制冷剂液体自管束的供液集管进入,吸热汽化后的制冷剂蒸气由回气集管引出。冷风机的供液方式有下进上出或上进下出。冷间空气在轴流风机作用下从下部进风口进入,自下而上地流过蒸发器管束,空气的热量被管内氨液吸收,降温后的空气经箱体顶部送风道均匀地送往冷间各处,达到冷间降温的目的。
3.冷凝器 冷凝器的作用是将制冷压缩机排出的高温高压气态制冷剂予以冷却、使之液化,以便制冷剂在系统中循环使用。根据冷却介质种类的不同,冷凝器可分为水冷式、空气冷却式、蒸发式冷凝器等类型。
(1)水冷式冷凝器。水冷式冷凝器是用水冷却高压气态制冷剂而使之冷凝的设备。水冷式冷凝器的冷却水可采用地表水或地下水。冷却水有一次用水、循环用水及混合用水等形式。采用水冷式冷凝器可以得到较低的冷凝温度,对制冷系统的制冷能力和运行经济性均有利。常用的水冷式冷凝器有壳管式、套管式和焊接板式等。
①壳管式冷凝器,分为卧式和立式两大类。
a.卧式壳管冷凝器,其结构如图2-37所示。卧式壳管冷凝器须水平方向装设,筒体两端焊有管板,板上焊接或胀接若干根传热管,此外,筒体上还设有进气管、出液管、平衡管和安全阀。氨用卧式壳管冷凝器下部还设有集油罐和放油管。高温高压气态制冷剂由上部进入管束外部空间,冷凝后的液体由下部排出。
图2-37 卧式壳管冷凝器
1—泄水管2—放空气管3—进气管4—均压管5—传热管6—安全阀接头
7—压力表接头8—放气管9—冷却水出口10—冷却水入口
11—放油管12—出液管
卧式壳管冷凝器筒体两端管板的外面用带有隔室板的封盖封闭,隔室板把全部管束分隔成几个管组(流程),冷却水从一端封盖的下部进入,顺序通过每个管组,最后从同一端封盖的上部流出。这样,可以提高管内冷却水的流动速度,增加冷却水侧的对流换热系数,同时,由于冷却水的行程较长,可以提高冷却水进出口温差,减少冷却水用量。氨用卧式壳管冷凝器的管束多采用外径为25~32mm的钢管,卤代烃类制冷剂用卧式壳管冷凝器多采用管束外径为16~25mm的外肋铜管。
图2-38为卤代烃类制冷剂用卧式壳管式冷凝器。
图2-38 卤代烃类制冷剂用卧式壳管式冷凝器
1—端盖2—管板3—制冷剂进气管4—筒体5—橡皮垫圈6—换热管束7—制冷剂液管
卧式壳管式冷凝器具有传热系数高、冷却水用量少、结构紧凑、占空间高度小、便于机组化设计等优点,较普遍地应用于大、中、小型的氨、卤代烃类制冷剂制冷系统中,尤其在船舶制冷和冷水机组中应用广泛。不足之处是,卧式壳管式冷凝器具有制冷剂泄漏不易发现、冷却水水质要求高、不易清洗,造价较高等缺点。卧式壳管式冷凝器多用于水源丰富和水质较好的场合。
b.立式壳管冷凝器,其结构如图2-39所示。立式壳管式冷凝器的外壳是由钢板焊成的圆筒体,筒体两端焊有多孔管板,在两端管板间用扩胀法或焊接法将无缝钢管束固定严密。在立式冷凝器壳体上部有进气管、安全阀,中部有均压管和压力表,下部有出液管和放油管;壳体最上端设有配水箱,把冷却水均匀地分配到各个管口。在配水箱中可设置金属丝水过滤网,水过滤网下每根管口设置一个扁圆形铸铁分水环,也可在每根管口上安装一个带斜槽的由铸铁或陶瓷制成的导流管。冷却水通过斜槽切线方向流入管中,以螺旋线状沿管内壁流下,在管内壁形成一层水膜,可提高换热效率和节约用水。
图2-39 立式壳管式冷凝器
1—放气管2—均压管3—安全阀4—配水箱5—管板6—进气管7—传热管
8—压力表9—出液管10—放油管11—导流管嘴
高压气态制冷剂从冷凝器外壳的中部进入管束外部空间,冷凝后的液体沿管外壁流下,积于冷凝器的底部,并从出液管流出。由于气态制冷剂从中部进入,其方向垂直于管束,能很好地冲刷钢管外表面,故传热系数较高。
立式壳管冷凝器应垂直安装,其优点是占地面积小,无冻结危险,可安装在室外;冷却水自上而下直通流动,便于清除铁锈和污垢,对冷却水的水质要求不高。它的缺点是冷却水用量大,体形比较笨重。多用于大中型氨用制冷系统。
②套管式冷凝器。如图2-40所示,套管式冷凝器是由不同直径的管子套在一起,并弯制成螺旋形或蛇形的一种水冷换热器。该冷凝器的外管一般为无缝钢管,管内套有一根或数根铜管。
图2-40 卤代烃类制冷剂用套管式冷凝器
冷却水在内管流动,流向为下进上出;高压气态卤代烃类制冷剂则在外套管自上向下流动,冷凝后的液体从下部流出,比较理想地实现逆流式换热。套管式冷凝器的盘管总长度不宜太长,否则不仅传热管内流体的流动阻力较大,而且盘管下部还会积聚较多冷凝液,减小传热管的传热面积。
套管式冷凝器多用于卤代烃类制冷剂。套管式冷凝器的传热管多采用铜制高效冷凝管,且制冷剂蒸气同时受传热管内冷却水和无缝钢管外的空气冷却,加上卤代烃类制冷剂和冷却水的纯逆向流动,故传热效果较好。套管式冷凝器具有结构紧凑、制造简单、价格便宜、冷凝液体再冷度较大、冷却水耗量较少等优点;但两侧流体的流动阻力均较大,且清除水垢较困难。多用于小型单机制冷机组。
(2)空气冷却式冷凝器。以空气为冷却介质的冷凝器称为空气冷却式冷凝器,又称为风冷式冷凝器,其基本结构如图2-41所示。风冷式冷凝器完全不需要冷却水,而是利用空气使气态制冷剂冷凝。制冷剂在风冷式冷凝器中的传热过程和水冷式冷凝器相似,分降低过热、冷凝和再冷三个阶段。风冷式冷凝器有自然对流式和强迫对流式之分,图2-41为强迫对流风冷式冷凝器。工作时,制冷剂蒸气从冷凝器上端的进气集管进入蛇形盘管束内,自上而下的通过管壁与管外肋片间流动的空气进行热量交换,冷凝后的制冷剂液体从管束下端流出。借助轴流风机或离心风机,使空气横掠肋管管束,吸收管内制冷剂放出的热量。
图2-41 空气冷却式冷凝器
1—肋片2—传热管3—上封板4—左端板5—进气集管6—弯头7—出液集管
8—下封板9—前封板10—通风机
由于空气侧的对流换热系数远小于管内制冷剂冷凝时的对流换热系数,所以在空气侧采用肋管强化空气侧的传热。肋管通常采用铜管铝片,也有采用钢管钢片或铜管铜片的。风冷式冷凝器的管簇可以顺排,也可以叉排。空气流过叉排管簇时,所受到的扰动大于顺排管簇。试验表明,空气流过叉排管簇时的传热系数,比顺排管簇高10%以上。沿空气流动方向的管排数以取2~6排为好。风冷式冷凝器的迎面风速一般取2~3m/s。由于空气冷却式冷凝器以空气为冷却介质,冷凝器的冷凝温度和冷凝压力都比水冷式冷凝器高,因此它适用于冷凝温度较高,而冷凝压力较低的制冷剂系统,以及供水困难或者可移动的制冷装置中。
(3)蒸发式冷凝器。蒸发式冷凝器的结构如图2-42所示,来自制冷压缩机的高压气态制冷剂,从上部被送入换热盘管,冷凝后的液态制冷剂从盘管下部流出。蛇形盘管可用铜管或无缝钢管弯曲制成。冷却水由盘管上部的喷淋机构喷出,淋洒在换热盘管外表面上,水吸收气态制冷剂放出的热量,一部分蒸发变成水蒸气,其余则落入下部水槽中,供循环使用。室外空气自下向上流经盘管,与喷淋冷却水形成逆向流动。不仅强化盘管外表面的换热,而且及时带走蒸发形成的水蒸气,以加速水的蒸发,提高冷凝效果。空气流经盘管的迎面速度不超过2.5m/s。为了防止空气带走水滴,喷水管上部装有挡水板。
图2-42 蒸发式冷凝器
1—风机2—挡水板3—冷却水喷淋机构4—换热盘管5—冷却水泵6—补水浮球
7—制冷剂出液管8—制冷剂进气管
风机可设在盘管上部,称为吸风式;也有设在盘管下部者,称为鼓风式。这两种形式的蒸发式冷凝器各有优缺点,吸入式由于气流均匀地通过冷凝盘管,所以传热效果好,但通风机在高温高湿下运行,易发生故障,降低可靠性;鼓风式则与之相反。
图2-43 氨中间冷却器
1—安全阀2—低压级排气进口管
3—中间压力氨液进口管4—排液阀
5—高压氨液出口管6—高压氨液进口管
7—放油阀8—氨气出口管
蒸发式冷凝器主要是利用水的汽化以带走制冷剂蒸气冷凝过程中放出的凝结潜热,因此,蒸发式冷凝器所消耗的冷却水只是补给散失的水量,与水冷式冷凝器相比,可节约大量冷却水。蒸发式冷凝器进口空气湿球温度对换热量影响很大,进口空气相对湿度越小,冷却水蒸发量则越大,冷凝效果越好。蒸发式冷凝器适用于缺水和气候干燥的地区。
4.其他换热设备
在制冷系统中常用的其他换热设备有中间冷却器、回热器与板式热交换器等。
(1)中间冷却器。中间冷却器用于两级压缩制冷装置,位于制冷循环的高、低压级之间,主要作用是:冷却低压级制冷压缩机排出的过热蒸气;冷却中间冷却器盘管中进入蒸发器的制冷剂液体,使其过冷。中间冷却器有氨用和卤代烃类制冷剂用两类。
①氨用中间冷却器,其结构见图2-43。低压级压缩机排气经顶部的进气管直接通入氨液中,冷却后所蒸发的氨气由上侧氨气出口管流出,进入高压级压缩机的吸气侧。用于冷却高压氨液的盘管置于中间冷却器的氨液中,高压液体由下端进口流入盘管中,经过冷却由下端出口伸到壳外。筒内进气管的外侧设有两个多孔的伞形挡板,以阻挡氨气中夹带的液滴进入高压级压缩机。在进气管伞形挡板以上部位有一个5mm的平衡孔,以平衡中冷器内与进气管中的氨蒸气压力,避免停机时,氨液从进气管倒流回低压级而造成事故。氨用中间冷却器中蒸气流速一般取0.5m/s,盘管内的高压氨液流速取0.4~0.7m/s。
②卤代烃类制冷剂用中间冷却器。卤代烃类制冷剂用双级压缩制冷装置大都采用一次节流中间不完全冷却双级压缩循环形式,中间冷却器只用来冷却高压制冷剂液体。卤代烃类制冷剂用中间冷却器结构常采用盘管式(图2-44)。
图2-44 卤代烃类制冷剂用中间冷却器
1—筒体2—挡板3—螺旋式换热管
卤代烃类制冷剂用中间冷却器主要由筒体和螺旋式换热管等组成。其筒体上设有进液管、出液管、节流后的供液管、出气管等。由冷凝器(或高压储液器)来的液态卤代烃类制冷剂分两路流动:一部分制冷剂液体(pk)经热力膨胀阀节流后(pm)由供液管供入中间冷却器;大部分液体(pk)经中间冷却器内的螺旋盘管流动。盘管内的制冷剂液体经过过冷后流出中间冷却器并送往蒸发器;管外制冷剂吸热汽化后成为中压下的饱和蒸气,并在高压级的吸气管路中与低压级排出的过热蒸气混合后进入高压级。
(2)回热器。回热器是指卤代烃类制冷剂制冷装置中使节流装置前制冷剂液体与蒸发器出口制冷剂蒸气进行换热的气液热交换器。其作用是,对于CFC-12、HFC-134a和R502,通过回热提高制冷循环效率;使得节流装置前制冷剂液体过冷,提高制冷量;使蒸发器出口制冷剂蒸气中夹带的液体汽化,防止压缩机液击。
盘管式回热器的结构(图2-45)与卤代烃类制冷剂用中间冷却器相似,其外壳是用钢板卷焊成圆筒形或用较大直径的无缝钢管,两端加封头焊制的密闭容器。回热器内装有一组用铜管或钢管绕成的螺旋盘管。壳体上有进气管、出气管、供液管、出液管。盘管式回热器在工作时,制冷剂液体沿管程流动,制冷剂蒸气沿壳程流动。为了防止润滑油沉积在回热器的壳体内,制冷剂蒸气在回热器最窄截面上的流速取8~10m/s,制冷剂液体在管内的流速可取0.8~1.0m/s。
图2-45 盘管式回热器
(3)板式热交换器。组合式板式换热器的结构如图2-46所示。板式换热器根据换热量的大小选定多片换热板,并组合而安装在换热器的导杆上。安装在导杆上的板片组两端均装有压紧板,其中一个为固定压紧板,另一个为活动压紧板。板片组与两压紧板用一组加压支架固定在一起。
图2-46 板式热交换器结构图
1—固定压紧板2—前端板3—换热板片4—后端板5—活动压紧板
6—上导杆7—下导杆8—后立柱9—夹紧螺栓
图2-47是板式换热器的结构分解图,是由一组不锈钢波纹金属板压紧而成的;板上的四孔分别为冷、热两种流体的进、出口;在板和板之间形成传热板两侧的冷、热流体通道,在流动过程中通过板壁进行热交换。两种流体在流道内呈逆流流动;而板片表面制成的点支撑形、波纹形、人字形等各种形状,会破坏流体的层流边界层,在低流速下产生漩涡和旺盛紊流,强化了传热。图2-47所示的三种板片形状中,点支撑形板片是在板上冲压出交错排列的一些半球形或平头形凸状,流体在板间流道内呈网状流动,流动阻力较小;水平平直波纹形板片,其断面呈梯形,传热系数较高;人字形板片属于典型网状流板片,它将波纹布置成人字形,不仅刚性好,且传热性能良好。
图2-47 板式热交换器分解图
板式换热器具有体积小、重量轻、传热效率高、可靠性好、加工过程简单等优点。但是板式换热器也存在内容积小、难以清洗、内部渗漏不易修复等缺点。
十一、制冷系统的节流装置
节流装置是制冷循环系统四大部件之一,位于冷凝器与蒸发器之间,其作用是使从冷凝器出来的高压制冷剂液体进行等焓节流,使其压力降低,然后进入蒸发器,在低压下蒸发吸热,从而达到制冷的目的。节流装置除了对制冷剂起节流作用外,还对进入蒸发器的制冷剂流量起调节作用,以适应蒸发器热负荷的变化。通过节流装置的调节,使制冷剂离开蒸发器时保持一定的过热度,进而保证液态的制冷剂不会进入压缩机,以避免“走湿车”现象发生。
节流机构的形式很多,结构也各不相同,常用的节流机构有热力膨胀阀、电子膨胀阀和其他节流装置(如手动膨胀阀、浮球膨胀阀、毛细管)等。
1.热力膨胀阀 热力膨胀阀是一种借助制冷系统热力学参数(如压力)来控制液体制冷剂流量的节流装置,主要靠控制蒸发器出口处制冷剂蒸气的过热度来自动调节蒸发器的供液量,同时起到节流降压作用。热力膨胀阀用于卤代烃类制冷剂系统(非满液式蒸发器)中组成。
(1)热力膨胀阀的分类。热力膨胀阀根据膜片下部的气体压力不同可分为内平衡式热力膨胀阀和外平衡式热力膨胀阀。若膜片下部的气体压力为膨胀阀节流后的制冷剂压力,则称为内平衡式热力膨胀阀;若膜片下部的气体压力为蒸发器出口的制冷剂压力,则称为外平衡式热力膨胀阀。
①内平衡式热力膨胀阀。图2-48是内平衡式热力膨胀阀的工作原理图。从图中可以看出,它是由阀芯、弹簧金属膜片、弹簧、感温包和调整螺钉等组成。阀体安装在蒸发器的供液管路上,感温包紧扎在蒸发器的回气管路上,感温包内充有与制冷系统相同的液态制冷剂。
图2-48 内平衡式热膨胀阀
1—阀芯2—弹簧金属膜片3—弹簧4—调整螺钉5—感温包
由图2-48可以看出,作用在弹簧金属膜片上的力主要有三个:p1为阀后制冷剂的蒸发压力,作用在膜片下部,其作用方向向上,使阀门向关闭方向移动;p2为弹簧力,它也作用在膜片下部,其作用方向向上,使阀门向关闭方向移动,其大小可以通过调整螺钉予以调整;p3为感温包内制冷剂的压力,它随蒸发器出口回气过热度的变化而变化,作用在膜片的上部,其作用方向向下,其趋势是使阀门开大,它的大小取决于感温包内充注制冷剂的性质以及感受温度的高低。
当膨胀阀保持一定的开启度稳定工作时,作用在膜片上、下部的三个力处于平衡状态,即p3=p1+p2,这时膜片不动,即阀门的开启度不变。而当其中一个力发生变化时,原有的平衡被破坏,此时p3≠pl+p2,膜片开始位移,阀门开启度也随之变化,直到建立新的平衡为止。当蒸发器负荷增加时,蒸发器内制冷剂汽化量增加,显得供液量不足,蒸发器出口的制冷剂蒸气过热度增大,感温包内制冷剂温度升高,这时感温包的压力p3>p1+p2,阀针向下移动,阀门开大,供液量增加。当蒸发器负荷减小时,显得供液量过大,过热度减小,这时p3<p1+p2,弹簧力推动传动杆向上移动,阀门关小,减小供液量。
现举例说明:假定感温包内充注与制冷系统相同的制冷剂HFC-134a,若进入蒸发器的液态制冷剂为5℃,其相应的在A处的压力p1=349.6kPa,液体在非满液式蒸发器中吸热汽化,如果不考虑制冷剂在蒸发器内的压力损失,则蒸发器各部位的压力均为349.6kPa,直到B点液体全部汽化为饱和蒸气。从B点开始再向前流动,制冷剂继续蒸发吸热变成过热蒸气,气体温度升高了,压力却仍然保持不变。假定由B点至装设感温包的C点(蒸发器出口处),气态温度升高5℃,即达到10℃,由于感温包紧贴管壁,包内液态制冷剂温度也接近10℃,即t5=10℃,其相应的饱和压力p5=414.5kPa,这个压力经过毛细管作用于膜片上部,则膜片上部的压力p3=414.5kPa。若将弹簧力p2通过调节螺钉调到64.9kPa,则使膜片向上移动的力为p1+p2=(349.6+64.9)kPa=414.5kPa。显然,此时p1+p2=p3,膜片上下压力相等,膜片不动,处于平衡状态,相应阀门有一定的开启度,保持一定的制冷剂流量。这时,蒸发器出口处气态制冷剂的过热度为tC-t0=(10-5)℃=5℃,相应于这个过热度的压力恰好等于弹簧力p2。
当外界条件改变,蒸发器的负荷减小时(即用冷减少时),蒸发器内的液态制冷剂汽化量减弱。这时,蒸发器的供液量显得过剩,于是蒸发器的液态制冷剂达到全部汽化的终点不是B点,而是B′点。蒸发器出口C点的温度将低于10℃,即过热度也小于5℃,致使感温包内制冷剂的压力低于414.5kPa,则p1+p2>p3,使阀门稍微关小,供液量减小,从而达到另一平衡状态。反之,蒸发器的负荷增加,吸热量增大,则蒸发器出口C点气态制冷剂的过热度增加,大于5℃,感温包内的压力也将大于414.5kPa,即p1+p2<p3,则阀门稍微开大,加大供液量,使膜片达到另一平衡状态。
内平衡式热力膨胀阀适用于蒸发器内部阻力较小的小型制冷机和空调机。对于大型的制冷装置及蒸发器阻力较大的场合,蒸发器出口处的压力比进口处下降较大,相对应的蒸发器出口处的制冷剂饱和温度低于入口处的饱和温度,若使用内平衡式热力膨胀阀,则将增加阀门的静装配过热度,相应地减少了阀门的工作过热度,导致蒸发器过热气体换热面积过大而换热效果下降、热力膨胀阀供液不足或根本不能开启,影响蒸发器的工作。因此,对于蒸发器管路较长,或是多组蒸发器装有分液器时,通常采用外平衡式热力膨胀阀。
②外平衡式热力膨胀阀。外平衡式热力膨胀阀有一根外部连接管,将膜片下部的空间与蒸发器出口相连接,这样膨胀阀膜片下部的压力就不再是蒸发器的进口压力,而是蒸发器的出口压力,从而可消除由于制冷剂在蒸发器中的流动阻力所引起的附加过热度。下面以图2-49为例说明其工作过程:假如制冷系统和感温包内均充注HFC-134a,在蒸发器入口A处的压力同样是tA=5℃,pA=349.6kPa,但是,膜片下部制冷剂的压力p1不等于pA,而是等于蒸发器的出口压力,即p1=pC,这样,热力膨胀阀的工作不受蒸发排管流动阻力的影响。当蒸发器流动阻力Δp=64.9kPa时,蒸发器出口的压力pC=pA-Δp=(349.6-64.9)kPa=284.7kPa,再加上相当于5℃工作过热度的弹簧力p2=64.9kPa,这时膜片下部的压力为p=p1+p2=(284.7+64.9)kPa=349.6kPa,而膜片上部(即感温包内)的压力p3=349.6kPa,此时膜片处于平衡状态,阀门的开启度不变。若供液量多时,蒸发器出口处C点的温度降低,感温包内的温度也降低,感温包内压力p3减小,而膜片下部压力p=pl+p2不变,就会推动阀杆向上移动,阀门关小,减小其供液量。相反,供液量不足时(即蒸发器负荷增大时),蒸发器出口C点的过热度增大,感温包内温度升高,p3增大,而p=pl+p2不变,阀门开大,增大其供液量。所以说阀门的开启度可使蒸发器出口的温度基本上等于5℃,即保持5℃的过热度,从而消除了蒸发器流动阻力的影响。外平衡式热力膨胀阀可以改善蒸发器的工作条件,但其结构比较复杂,安装与调试比较麻烦,因此,只有蒸发器的压力损失较大时才采用此种膨胀阀。
图2-49 外平衡式热力膨胀阀
1—阀芯2—弹簧金属膜片3—弹簧4—调节螺钉5—感温包6—平衡管
(2)热力膨胀阀的安装。在卤代烃类制冷剂制冷系统中,热力膨胀阀安装在蒸发器入口处的供液管路上,阀体应垂直安装,不能倾斜,更不能倒装。蒸发器配有分液器时,气液分液器应直接安装在膨胀阀的出口侧。热力膨胀阀的感温包应装设在蒸发器出口处的吸气管路上,要远离压缩机吸气口1.5m以上。感温包的布置、安装是否合理,关系到热力膨胀阀的灵敏度。因为膨胀阀的温度传感系统是借助于压力进行传递的,灵敏度比较低,传递信号时会产生一个滞后时间,引起膨胀阀启用频繁,从而使系统的供液量波动,因此,感温包的安装对热力膨胀阀影响很大。实际工程中,感温包被包扎在吸气管道上,如图2-50所示。
图2-50 感温包的安装方法
安装的具体做法:首先将包扎感温包的吸气管段上的氧化皮清除干净,以露出金属本色为宜,并涂上一层铝漆作为保护层,以防生锈;然后用两块厚度为0.5mm的铜片将吸气管和感温包紧紧包住,并用螺钉拧紧,以增强传热效果。当吸气管外径小于22mm时,将感温包包扎在吸气管上面;当吸气管外径大于22mm时,将感温包绑扎在吸气管水平轴线以下与水平线呈30°角的位置上,以免吸气管内积液(或积油)而使感温包的传感温度不正确。为防止感温包受外界空气温度的影响,外面需包扎隔热层。
在安装感温包(图2-51)时,务必不能把感温包安装在有积存液体的吸气管处。因为积存在管道内的液体制冷剂继续蒸发,会使感温包感受不到过热度(或过热度很小),从而使阀门关闭,停止向蒸发器供液,直到管路中所积存的液态制冷剂全部蒸发,感温包重新感受到过热度时,膨胀阀方才会开启而正常供液。为了防止膨胀阀误操作,蒸发器出口处吸气管需要垂直安装时,吸气管垂直安装处应有存液管,否则,只能将感温包装在出口处的立管上。
图2-51 感温包的安装位置
(3)热力膨胀阀的调试。热力膨胀阀安装完毕后需要与制冷装置同时调试,使它在实际工况下进行自动调节。所谓调试,实际上就是调整阀芯下方的弹簧的预紧力。拧下底部的帽罩,用扳手顺旋(由下往上看为顺时针方向)调节杆,使弹簧压紧而关小阀门,蒸发压力会下降;反旋调节杆,使弹簧放松,阀门开大,则蒸发压力会上升。调整热力膨胀阀时,让制冷装置正常运转,在压缩机的吸气截止阀处装一块压力表,通过观察压力表来判断调整量是否适度。如果蒸发器离压缩机较远,也可根据回气管的结霜(中低温制冷)或结露(空调用制冷)情况进行判别。对于中低温制冷装置,如果挂霜后用手摸上去有一种将手粘住的阴凉感觉,则表明此时膨胀阀的开度适宜。在空调制冷装置中,蒸发温度一般在0℃以上,回气管应该结露滴水。若结露直至压缩机附近,则说明阀口过大,则应调小一些;相反,蒸发器出口处如果不结露,则说明阀口过小,供液不足,应调大一些。在装有回热器的系统中,回热器的回气管出口处不应结露。
调试工作要细致认真,一般分粗调和细调两段进行。粗调每次可旋转调节螺钉(即调节螺杆)一周左右,当接近需要的调整状态时,再进行细调。细调时每次旋转1/4周,调整一次后观察20min左右,直到符合要求为止。据经验,调节螺杆转动一周,过热度变化1~2℃。
(4)热力膨胀阀的缺点。热力膨胀阀是一种利用制冷剂热力学参数来自动调节流量的节流控制元器件,被广泛应用。但是有其不足之处:
①蒸发器处的高温气体首先要加热感温包外壳,感温包外壳有较大的热惯性,导致反应滞后;而感温包外壳对感温包内工质的加热又引起进一步的滞后。这种信号反馈的滞后会导致被调参数的周期性振荡。
②感温包内的压力通过薄膜传递给阀针。因薄膜的加工精度及安装均会影响它受压产生的变形以及灵敏度,故难以实现高精度控制。
③因薄膜的变形量有限,使阀针开度的变化范围较小,故流量的调节范围较小,不能满足使用变频压缩机时大流量的调节。
2.电子膨胀阀 热力膨胀阀的缺点,限制了其应用范围。随着无级变容量制冷系统制冷剂供液量调节范围变宽和调节反应快的要求,电子膨胀阀应运而生,并为制冷装置的智能化提供了条件。电子膨胀阀利用被调节参数产生的电信号,控制施加于膨胀阀上的电压或电流,进而控制阀针的运动,达到调节供液量的目的。热力膨胀阀及电子膨胀阀的特点比较见表2-2。
表2-2 热力膨胀阀及电子膨胀阀特点比较
按照驱动方式的不同,电子膨胀阀可分为电磁式和电动式两类。
(1)电磁式电子膨胀阀。电磁式电子膨胀阀的结构如图2-52(a)所示,它是依靠电磁线圈的磁力来驱动阀针的。电磁线圈通电前,阀针处于全开位置。通电后,受磁力作用,阀针的开度减小,开度减小的程度取决于施加在线圈上的控制电压。电压越高,开度越小【阀开度随控制电压的变化情况如图2-52(b)所示】,流经膨胀阀的制冷剂流量越小。电磁式膨胀阀的结构简单,动作响应快,但是在制冷系统工作时,需要提供控制电压。
图2-52 电磁式电子膨胀阀
1—柱塞弹簧2—线圈3—柱塞4—阀座5—弹簧6—阀针7—阀杆
(2)电动式电子膨胀阀。电动式电子膨胀阀是依靠步进电动机驱动阀针的,分直动型和减速型两种。
a.直动型电动式电子膨胀阀,其结构如图2-53(a)所示。该膨胀阀是用脉冲步进电动机直接驱动阀针的。当控制电路的脉冲电压按照一定的逻辑关系作用到电动机定子的线圈上时,永久磁铁制成的电动机转子受磁力矩作用产生旋转运动,通过螺纹的传递,使阀针上升或下降,调节阀间制冷剂的供液量。直动型电动式电子膨胀阀的工作特性(流量和电子脉冲数关系)如图2-53(b)所示。直动型电动式电子膨胀阀驱动阀针的力矩直接来自定子线圈的磁力矩,故这个力矩较小,应用受到一定的局限性。
图2-53 直动型电动式电子膨胀阀
1—转子2—线圈3—阀针4—阀杆
b.减速型电动式电子膨胀阀。为了克服直动型电动式电子膨胀阀力矩小的缺点,开发了减速型电动式电子膨胀阀。该膨胀阀的结构见图2-54(a),内装有减速齿轮组,步进电动机通过减速齿轮组将其磁力矩传递给阀针。减速齿轮组放大了磁力矩的作用,因而该步进电动机易与不同规格的阀体配合,满足不同调节范围的需要。图2-54(b)是减速型电动式电子膨胀阀的工作特性(液体流量—脉冲数关系)。
图2-54 减速型电动式电子膨胀阀
1—转子2—线圈3—阀杆4—阀针5—减速齿轮组
(3)电子膨胀阀的工作原理。电子膨胀阀对蒸发器出口制冷剂的过热度调节,是通过设置在蒸发器出口和中部的两只温度传感器来采集过热度信号的,并采用反馈调节来控制膨胀阀的开度。下面以调节蒸发器出口处制冷剂的过热度为例,说明电子膨胀阀的工作原理。
如图2-55所示,为了获得调节信号,在蒸发器的两相区管段外和蒸发器出口的管段外各贴一个热敏电阻。图中的θ1w表示蒸发器出口处的管壁温度,θ2w表示蒸发器两相区段管壁的温度,(θ1w-θ2w)表示蒸发器出口处制冷剂的过热度。由于管壁的热阻很小,故认为热敏电阻感受的温度即为该两处管壁内制冷剂的温度,两电阻片反映的温度之差即为制冷剂的过热度。这种测定过热度的方法,远比热力膨胀阀测得的过热度准确。图中两片热敏电阻测得的制冷剂过热度信号被输入控制电路中,通过程序的转换产生脉冲信号,控制阀针的运动。
图2-55 利用蒸发器过热度的电子膨胀阀调节系统
1—蒸发器2—压缩机3—冷凝器4—电子膨胀阀
制冷系统同时使用变频压缩机及电子膨胀阀时,因变频压缩机的运转受到主计算机指令的控制,电子膨胀阀的开度也随之受该指令的控制。一般情况下,阀的开度与变频器的频率成一定的比例关系,但由于制冷系统的蒸发器和冷凝器一定,其传热面积成为定值,这就难以使阀的开度与频率保持完全固定的比例。实验表明,在不同频率下存在一个能效比最佳的流量,因而在膨胀阀开度的控制指令中,应包含压缩机频率、蒸发温度和功耗等因素。
3.其他节流装置
(1)手动膨胀阀。手动膨胀阀又称节流阀或调节阀。其结构与普通截止阀相似,如图2-56所示,阀杆采用细牙螺纹,便于微量启闭阀芯。当转动阀杆时,就能保证阀门的开启度缓慢地增大或关小,以适应制冷量的调节变化。手动膨胀阀与截止阀的主要区别是阀芯为针形锥体或带V形缺口的锥形(图2-57),以提高调节的精确度。手动膨胀阀要求管理人员根据蒸发器负荷变化随时调节阀门的开启度,管理麻烦,而且凭经验操作,因此近年来大多数被自动膨胀阀所替代,只将手动膨胀阀装在旁通管道上,以备应急或检修自动膨胀阀时使用。手动膨胀阀的开启度为手轮旋转的1/8~l/4周,不能超过一周。如果开启过大,则起不到节流降压的作用。
图2-56 手动膨胀阀
1—出口2—阀针3—阀体4—阀杆5—入口
图2-57 手动膨胀阀阀芯
(2)浮球膨胀阀。浮球膨胀阀是一种自动膨胀阀,它的作用是根据满液式蒸发器液面的高低来控制蒸发器的供液量,同时进行节流降压。浮球膨胀阀根据节流后的液体制冷剂是否通过浮球室而分为直通式和非直通式两种,如图2-58所示。
图2-58 浮球膨胀阀结构
1—液体进口2—阀针3—支点4—浮球5—液体连通管6—气体连通管7—节流后的液体出口
这两种浮球膨胀阀的工作原理都是依靠浮球室中的浮球受液面的作用而降低或升高,通过杠杆原理去控制阀门阀针的开启度。浮球室置于满液式蒸发器一侧,上、下用均压管与蒸发器相通,所以浮球室的液面与蒸发器的液面高度是一致的。当蒸发器的负荷增加时,蒸发量增加,液面下降,浮球室中的液面也相应下降,于是浮球下降,依靠杠杆作用使阀门开启度增加,加大供液量;当蒸发器负荷减小时,制冷剂蒸发量减少,其蒸发器液面与浮球室内液面同时升高,浮球升高,阀门的开启度减小,使制冷剂供液量减少。
直通式浮球阀节流后的制冷剂液体通过浮球室,由液体平衡管进入蒸发器。其优点是构造简单;缺点是浮球室液面波动和冲击很大,容易使浮球阀失灵,其次需较大口径的平衡管。非直通式浮球阀节流后的制冷剂液体不通过浮球室,而是通过管道直接进入蒸发器。其优点是浮球室液面平稳,但构造和安装比较复杂。
浮球膨胀阀一般安装在蒸发器、气液分离器、中间冷却器前的液体管路上。
(3)毛细管。毛细管是应用在制冷装置上的又一种节流元件,其结构是在直径很小的金属管内让液体制冷剂流过,利用液体沿管程阻力损失进行降压节流。它被广泛应用于小型卤代烃制冷装置中,如家用冰箱、冰柜、空气调节器等,是一种便宜、有效的节流机构。由于其直径小,通路易被固体物粒或“冰堵”现象阻塞,所以在毛细管前面应固定性能良好的过滤器和干燥器。毛细管通常采用直径为0.7~2.5mm、长度为0.6~6m,细而长的纯紫铜管,连接在蒸发器与冷凝器之间(图2-59)。
图2-59 毛细管在制冷装置中的应用
毛细管节流装置一旦确定,其流量和降压特性便由两端的高、低压差决定,因此应用时应注意:
①制冷系统的制冷剂充注量要准确,若充注量过多,则在停机时留在蒸发器内的液体制冷剂过多,导致启动负荷大和引发湿压缩;反之,充液量过少,会难以形成正常的液封,而导致制冷量下降,甚至降不到所需的温度。
②毛细管的孔径和长度是根据某一机组的特性和一定工况变化范围而配置的,不能随意更改规格,否则会影响制冷装置的正常工作。
③当几根毛细管并联使用时,应安装分液器以使流量均匀。
十二、制冷系统的安全控制
压缩机作为制冷装置的主机,它的安全可靠性对系统的安全可靠性起着决定性作用,因而压缩机的安全保护控制在压缩机的控制系统中占有相当重要的地位,是保证压缩机安全运行的必要条件。压缩机保护方法是当工作参数出现异常将危及压缩机安全时,立即或者延时中止其运行,待故障排除后,设备方可再次投入运行。制冷系统安全控制主要有以下几个方面。
1.压缩机高低压力保护
(1)高压保护。高压保护即排气压力保护,其目的是为了防止排气压力过高而对压缩机及设备的安全运行产生危害。引起压缩机排气压力过高的原因可能是:操作失误,开机后排气管阀仍未打开;初充灌量过多,冷凝器大量积液;冷凝器断水或水量严重不足;冷凝器风扇电动机出现故障;系统中不凝性气体含量过多等。
其保护控制的方法是在压缩机排气阀前引一根导管,接到高压控制器上,当排气压力超过给定值时,控制器立即动作,切断压缩机电源,使压缩机停机,同时发出声光警报信号。
(2)低压保护。即吸气压力过低保护,吸气压力过低,一方面会造成蒸发压力过低,导致冷藏物的温度过低,加大食品干耗,容易引起食品变质;另一方面会因低压侧压力过低,会引起大量空气渗入系统,将不凝性气体和湿分带入,使排气温度、压力提高,影响系统的安全运行及经济性;水分还会造成膨胀阀冰堵;对于氨机,系统中混入空气甚至有爆炸的危险。
其保护控制的方法是在压缩机吸气阀前引出一根导压管,接到低压控制器上,当吸气压力低于给定值时,控制器立即动作,切断压缩机电源,停机。
高低压力控制器种类较多,图2-60所示为KD型高低压力控制器原理图。其传动机构直接采用弹簧传动,所以结构简单。KD型高低压力控制器主要由低压部分、高压部分和微动开关组成。当高于低压给定值的气体进入低压波纹管10时,使低压波纹管受力产生压缩形变,然后通过传动棒芯9、传动杆4使微动开关1的接点动作,电路接通,压缩机正常运行。若吸气压力低于给定值,在调节弹簧3的反力作用下,使传动杆4抬起,解除对微动开关的压力,微动开关电路断开,使压缩机停止运行。当压力高于高压给定值的气体进入高压波纹管11时,波纹管在高压压力下被压缩,克服高压调节弹簧17的反力,把传动螺丝12压下,按下微动开关19的按钮,电路断开,压缩机停止运行。若低于高压给定值的气体进入时,则可使电路接通,压缩机正常运行。
图2-60 KD型高低压力控制器原理图
1,19—微动开关2—低压调节盘3—低压调节弹簧4—传动杆5—调节螺丝6—低压压差调节盘7
,14—蝶形弹簧8—垫片9—传动棒芯10—低压波纹管11—高压波纹管12—传动螺丝13—垫片
15—高压压差调节盘16—传动杠杆17—高压调节弹簧18—高压调节盘
高压及低压的断开压力值,可通过高压调节盘18或低压调节盘2进行调节,若加大调节弹簧预紧力,则切换压力值就相应增大;反之,则减小。高压或低压的差动压力值,即接通或断开时的压力差,可以通过高压压差调节盘15或低压压差调节盘6进行调节,若转动压差调节盘使碟形弹簧预紧力增大,则差动值相应增大。
另外,有些型号的控制器带有自锁装置,比如当高压超过给定值停车后,即使压力下降到给定值以下,也不能自动复位,需待查明原因排除故障后,按动复位按钮,压缩机才能继续运行。
2.油压保护 制冷系统中,为了使压缩机各运动摩擦件能得到良好的润滑和冷却,必须保持润滑系统有一定的油压。为防止油压过低,引起在压缩机正常运转或启动时间内因失油而造成咬轴或咬缸等事故,必须对油压进行控制。因为油循环的动力是液压泵出口压力与压缩机曲轴箱压力(即吸气压力)之差,所以压缩机运转时油压表所反映的压力,并非是真正的润滑油压力,真正的润滑油压力应该是油压表指示的压力与压缩机吸气压力的差值,所以油压控制器实质上是一个压差控制器。压差控制器接受润滑液压泵排出压力和压缩机吸入压力两个压力信号的作用,并使这两个压力之间保持一定的差值范围。当压力差小于给定值时,控制器开关动作,自动切断压缩机电路,使压缩机停车。
考虑到油压差总是在压缩机启动后才逐渐建立起来,所以,因欠压令压缩机停止的动作必须延时执行。这样在开机前,油压差尚未建立起来时并不影响启动运转;运转后,短期缺油也不会危及压缩机的安全。如果持续到指定的延时时间仍建立不起油压,才表明有故障,这时再令压缩机停车。因此,油压差控制器本身应具有延时机构。若选择不带延时机构的压差控制器,则必须外接延时继电器才能使用。
图2-61为JC3.5型油压差控制器的工作原理。它的延迟时间是(60±20)s。控制器由压差继电器和延时继电器两部分组成。延时继电器的电接触点串接在压缩机启动控制回路中,基本控制过程为:压差继电器根据压差信号使延时继电器的电加热器接通或者断开;延时开关在其电加热器接通后经过一定的时间断开,压缩机启动控制电路。
图2-61 JC3.5型压差控制器原理图
1—杠杆2—主弹簧3—顶杆4—压差调节螺丝5—低压波纹管6—试验按钮7—电加热器
8—手动复位按钮9—降压电阻10—压缩机电源开关11—高低压控制器12—热继电器
13—事故信号灯14—交流接触器开关15—正常工作信号灯16—压缩机电动机
17—延时开关18—双金属片19—压力差开关20—高压波纹管
用压差调节螺丝4调整油压差给定值。高压、低压包分别引接液压泵出口压力和曲轴箱压力,获得这两者的压差信号,与主弹簧2的给定压力比较后,使顶杆3向上移动,拨动直角杠杆1偏转,扳动开关19。图中1、19、17在压差正常时处于实线位置。按接点状态分析电路,可以看出这时压缩机的运行状态,事故信号灯13给出运行状态显示。
当油压差低于给定值时,顶杆3下移,杠杆1处于虚线所示位置,将开关19扳到虚线位置,正常工作信号灯15熄灭,立即给出油欠压的信号,同时接通电加热器7,对双金属片18持续加热一段时间,即延时时间,使双金属片变形(向右翘曲),把延时开关17扳到虚线位置,断开压缩机启动控制回路,使压缩机保护性停机。同时,事故信号灯13接通,给出故障显示信号。
启动前,双金属片18处于冷态位置,延时开关17处于实线位置,启动控制回路接通。这时,尽管没有油压差也不妨碍启动。启动后,油压差在建立过程中,尽管开关处于虚线位置,使电加热器通电,但通电尚未持续到足以使双金属片动作时,油压就已达到正常,将开关17扳回到实线位置,电加热器断电。至此启动完成,投入正常工作,正常工作信号灯亮。
使用油压差控制器时应注意:
(1)压差控制器的高、低压信号接口切勿接反。
(2)机器仪表盘上的油压表指示为液压泵出口的表压力值,不要误以为是油压差。油压差=油压表读数-吸气压力表读数。
(3)油压差的控制值一般取0.15MPa。
(4)注意电气接线说明,按规定正确连接。
(5)延时机构动作过后,要等5min使双金属片完全冷却下来,再按动复位按钮使延时开关复位后才能再次启动压缩机。
3.温度保护
(1)排气温度保护。压缩机排气温度过高会影响机器寿命,使润滑油炭化,严重时可引起制冷剂蒸气分解,发生爆炸,因此必须设置排气温度保护。一般可采用压力式温度控制器作为保护控制。温度控制器的感温包应在紧靠排气口处安装,感温包内充注饱和液体,受热后产生的压力通过毛细管传到波纹管上,波纹管产生的形变力作用到微动开关,以控制压缩机。当排气温度超过给定值时,温度控制器动作,使压缩机停车。当然,由于热气旁通引起的排气温度过高也不允许,但这种情况不是靠压缩机停车解决的,而是应采用喷液冷却。
(2)油温保护。在压缩机运转过程中,有时尽管油压正常,但由于油温过高,润滑性能下降,会导致压缩机运动部件磨损加剧、烧坏轴瓦。一般可采用压力式温度控制器在油温过高时控制停机。曲轴箱内油的温度规定比环境温度高20~40℃,最高不得超过70℃。曲轴箱内有油冷却盘管的压缩机不必设油温保护。对于氟机,若曲轴箱中有大量制冷剂混入,启动时会影响油压的建立,为此须在曲轴箱内设电加热器,启动前通电加热使制冷剂蒸发,在这种情况下也要控制油温。油温的控制也可以由压力式温度控制器实现。
(3)轴温保护。对高速运行的离心式机组,轴承温度是保证系统安全运行的重要监测项目,轴承温度监视法多采用热电耦温度巡检仪,当检测出某一轴承温度超过90℃时,即停车报警。
4.冷却水断流保护 氨压缩机气缸头设冷却水套,若运行中水套断水也会使排气温度升高,严重时引起气缸变形。一般采用晶体管水流继电器作为断水保护,在水套出水管路安装一对电接点,有水流通过时,电接点被水接通,继电器发出信号使压缩机可以启动或者维持正常运行;没有水流过时,接点不通,禁止压缩机启动或令其故障性停机。水流中常有气泡造成接点偶尔断开,会引起误动作,而且水套断水不会立即引起故障,所以停机要延时执行,一般延时15~30s。
5.电动机保护 压缩机电动机的保护主要是短路保护和长期过载保护。常用的保护装置有过流继电器和热继电器,前者是短路保护用,后者是长期过载用。也可以采用自动空气断路器,它既有开关作用,又有自动保护功能,在电路发生短路、严重过载、过压或欠压时,能自动地切断电路,有效地保护所控电动机。
除了前述各项装置的保护控制内容以外,尚有液位保护控制、中压保护控制(防止双级压缩系统低压级排气压力过高)等,这些保护措施在实际工程中以满足安全运行为原则。