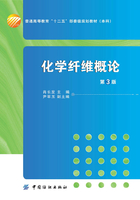
第四节 普通粘胶短纤维
一、凝固浴的组成和作用
1.凝固浴的组成
凝固浴是由硫酸、硫酸钠和硫酸锌按一定比例组成的溶液。单独的硫酸水溶液虽然也能用于粘胶纤维成形,但所得纤维的质量很差,主要是因为纤维素黄原酸酯的分解速度过快,大分子还来不及经受足够的拉伸定向,纤维素已经再生出来,使得纤维的结构疏松,内外层结构不匀,强度低,纤维无实用价值。故一般要用组合凝固浴。纤维品种不同,凝固浴组成及成形温度等也不同。
2.凝固浴的作用
(1)硫酸的作用:在成形过程中硫酸的作用,一是使纤维素黄酸钠分解,再生出纤维素和CS2;二是中和粘胶中的NaOH,使粘胶凝固;三是使黄化时产生的副产物分解。
酸的浓度要根据成形参数的波动而进行适当调整。凝固浴中硫酸的浓度除与生产纤维品种有关外,还与粘胶的熟成度、粘胶的组成、纺丝速度以及喷丝头大小等有关。
(2)硫酸钠的作用:硫酸钠的主要作用是抑制硫酸的离解,从而延缓纤维素黄酸钠的再生速度。硫酸钠是一种强电解质,能促使粘胶脱水而凝固,这些作用能改善纤维的力学性能。
(3)硫酸锌的作用:当凝固浴中只含有硫酸和硫酸钠时,虽能制得强度较高的纤维,但因其刚性太高,不能全面符合纺织加工的要求。硫酸锌的加入,可改进纤维的成形效果,使纤维具有较高的韧性和较优良的耐疲劳性能。
硫酸锌除具有与硫酸钠相同的作用外,还有两个特殊的作用:一是能与纤维素黄原酸钠作用生成稳定的中间产物——纤维素黄原酸锌,这种中间产物的分解速度比纤维素黄原酸钠慢得多,有利于拉伸,从而得到强度较高的纤维;二是纤维素黄原酸锌具有交联结构,能形成结晶中心,生成均匀而细小的结晶,避免大块结晶体的形成,从而使纤维结构均匀,强度、延伸度和钩接强度都可得到适当提高。
二、纺丝成形工艺
1.粘胶短纤维的成形特点
(1)喷丝头的选用:采用直径较大或组合式喷丝头,单头孔数上千乃至数万,合并后的丝束总线密度在百万分特以上,纺丝机的单台生产能力较大。
(2)成形条件:由于喷丝头孔数较多,所以除要求喷丝孔有合理的排列与分布外,还要求酸浴的分配和流向更加均匀合理。短纤维的成形条件比普通长丝要缓和,纺丝浴组成中硫酸含量略低,而硫酸钠含量稍高。因此,在塑性状态下丝条能经受较大的拉伸。
(3)双浴成形:经凝固成形后,丝束还要在专门的塑化槽中进行拉伸,纤维素在此完全再生,即双浴成形。从一浴中纺出的丝束,合并成丝束后,在95~100℃的二浴中进行60%~100%的拉伸,并充分分解成为水化纤维素。
2.成形过程中的化学及物理化学变化
粘胶纤维纺丝是将粘胶溶液通过多孔喷丝头挤出进入凝固浴中,使纤维素黄原酸酯凝固成为丝条,然后再分解成为水化纤维素。凝固和分解两个过程往往是同时发生的,只是前后程度有所不同。
(1)成形过程中的化学变化:
①纤维素黄原酸酯遇酸的分解反应:
2C6H9O4OCS2Na+H2SO42C6H10O5+Na2SO4+2CS2↑
②粘胶中碱与酸的中和反应:
2NaOH+H2SO4Na2SO4+2H2O
③纤维素黄酸钠和硫酸锌的过渡反应:
④粘胶中杂质与酸的各种副反应:
Na2CS3+H2SO4Na2SO4+H2S↑+CS2↑
Na2S+H2SO4Na2SO4+H2S↑
Na2Sx+H2SO4Na2SO4+H2S↑+(x-1)S↓
Na2S2O3+H2SO4Na2SO4+H2O+SO2+S↓
(2)成形过程中的物理化学变化:当粘胶经过喷丝孔道时,在切向力作用下成为各向异性的粘胶细流。粘胶细流和凝固浴各组分的双扩散结果,使纤维素黄原酸酯被分解而析出再生纤维素。细流被离析成双相,即以纤维素网络结构为主的凝胶相和以低分子物质为主的液相。在初生的凝胶纤维中,原来在粘胶中已形成的结晶粒子首先析出。结晶粒子进一步结合其他大分子或缔合体而不断增大,并逐渐形成较大的结晶区域。由于纤维素大分子活动性小,故结晶过程比较缓慢。另外,溶剂的扩散速度常低于反应速度,所以在纤维的表面首先形成皮膜,溶剂通过皮膜向内部渗透,形成截面结构不均匀的皮芯层结构。
3.拉伸在粘胶短纤维成形中的意义
粘胶短纤维的成形过程是在两个浴内完成的,由于凝固纤维所处的状态不同,所以不同部位拉伸所获得的效果亦不同。短纤维拉伸一般由喷丝头拉伸、导盘拉伸和塑化拉伸三个阶段组成。
(1)喷丝头拉伸:喷丝头拉伸率是指第一纺丝导盘的线速度与粘胶从喷丝头喷出速度之间的比值。
粘胶从喷丝头喷出时,粘胶细流尚处于粘胶态,不宜施加过大的喷丝头拉伸,否则容易造成断头和毛丝。纤维品种不同,酯化度不同,喷丝头拉伸率有较大差异。棉型短纤维控制一定的正拉伸,而高湿模量粘胶短纤维因酯化度较高,故常采用喷丝头负拉伸。
(2)导盘拉伸:亦称空气浴拉伸,它在导盘与第一集束辊之间进行。此时丝束上附着有一部分凝固浴液,纤维素黄原酸酯继续凝固并分解,大分子活动能力降低。经拉伸的纤维素大分子可以沿轴向达到一定程度的排列。但这一阶段的拉伸率较小。
(3)塑化拉伸:塑化拉伸在第一集束辊和第二集束辊之间进行。纤维丝束在高温酸性塑化浴中一方面得到完全再生,另一方面使丝条处于可塑状态,大分子链有较大的活动余地,加以强烈的拉伸,就能使大分子和缔合体沿拉伸方向取向。在拉伸的同时,纤维素基本全部再生,使拉伸效果得到巩固。塑化拉伸是拉伸中最有效的部分。
三、粘胶短纤维的后处理
1.后处理方式及工艺流程
短纤维纺丝机纺出的纤维经集束、塑化拉伸后,纤维含有一系列杂质,其中包括丝条所带出的酸性残余浴液、成形过程中生成的胶态硫黄及附着在纤维上的钙、镁等金属盐类。这些杂质的存在对纤维质量及其纺织加工有很大影响,必须加以清除。根据丝束是否被切断,后处理可以分成四种方式,如表2-6所示。
表2-6 粘胶短纤维后处理方式
目前,很多生产厂采用切断后再进行后处理的方法,其工艺流程:水洗→脱硫→水洗→漂白→水洗→酸洗→水洗→上油→烘干→打包。
2.后处理各工序的作用
(1)水洗:用清水可洗去纤维上的硫酸、硫酸盐及部分硫黄。每一次化学处理后还需进行水洗,以除去化学处理药液及生成的杂质。为提高水洗效果,水洗温度要适当。为减少用水量,除第一次洗水排放外,其余各道洗水一般都回收利用,并采用逆流方式,后一道洗水送至前一道使用。此外,硬水会在纤维上产生粘着的沉淀物,上油时易生成不溶性钙皂粘附在纤维表面,所以后处理过程必须使用软水。
(2)脱硫:附着在纤维上的硫黄会使纤维带有淡黄色,并使纤维手感粗糙,而且在以后的纺织加工中产生灰尘,恶化车间环境。
一般纤维表面的硫黄在热水中容易被洗掉,而内部的胶质硫黄却难以洗去。为此,需要借助化学药剂。常用的脱硫剂有:NaOH、NaOH与Na2S的混合液及Na2SO3,它们能和不溶性的硫黄生成可溶于水的多硫化物和硫代硫酸盐而被除去。
(3)漂白:由于原料和生产中带入的各种色素,使纤维的白度较低,如果要求纤维较白时,就需漂白。一般采用次氯酸钠和过氧化氢作为漂白剂,它们能氧化色素使纤维变白。
(4)酸洗:酸洗是为了除去纤维在处理过程中生成的不溶性氢氧化铁及其他重金属,以免影响纤维的质地和外观。常用的酸为盐酸或硫酸。
(5)上油:上油的目的在于改善粘胶纤维的纺织加工性能,调节纤维的表面摩擦力,使纤维既具有柔软、平滑的手感,又具有适当的抱合力。
纤维的上油率直接影响上油效果,通常上油率控制在0.15%~0.3%为宜。作为纤维用油剂,除要求能改善纤维的纺织加工性能外,其稳定性以及水乳液的稳定性要好,并且要求油剂应无臭,无腐蚀性,洗涤性好,价廉易得。
(6)切断:为使粘胶短纤维能像毛、棉纤维一样进行纺织加工,或能与毛、棉纤维及合成纤维进行混纺,就要将它切断成与毛、棉纤维相近的长度。
棉型纤维的长度为38mm左右,毛型纤维的长度通常为76~114mm,中长型纤维的长度为51~76mm。
(7)烘干:纤维在烘干前要先进行脱水,使含水率由300%~400%降至130%~150%。一般短纤维用轧辊脱水机脱水。烘干通常采用热风烘干,烘干速度取决于热空气的温度、湿度、循环速度以及纤维厚度、开松程度。烘干后纤维含水率一般为6%~8%,产品回潮率控制在8%~13%。
(8)打包:短纤维经烘干和干开棉后,借助气流或输送带被送入打包机,打成一定规格的包,以便运输和储存。成包重量一般为100~200kg。包上应注明生产厂家、纤维规格等级、重量、批号和包号等。