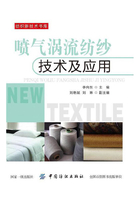
第二节 喷气涡流纺成纱结构与性能的关系
一、喷气涡流纺纱结构
喷气纺成纱过程为经罗拉牵伸机构牵伸后的须条进入喷嘴内进行加捻成纱,其为非自由端纺纱,即纤维一端由前罗拉握持,另一端被高速旋转气流加捻。
涡流纺成纱过程为经分梳辊分梳后的纤维流进入涡流管内进行加捻成纱,其为自由端成纱,即纤维一端脱离分梳辊成为自由短纤维,纤维被高速旋转涡流加捻成纱。
喷气涡流纺综合了以上两种成纱方法的优点并进行了改进,其成纱过程为经罗拉牵伸机构牵伸后的须条,先进入带有引导针棒的固定栓,再进入空心锭加捻成纱,其为自由端纺纱,即由于引导针棒的阻捻和引导作用,使得纤维尾端脱离前罗拉的握持,成为自由端纤维倒伏在空心锭顶端,由空心锭内高速旋转射流加捻成纱。
喷气涡流纺采用正向压缩空气,在凝聚腔体内形成高速旋转涡流场,对集聚在凝聚加捻口上的自由尾端纤维加捻成纱。其自由端纺纱原理完全突破了传统的喷气纺加工原理,是喷气纺与涡流纺加工原理的综合。该技术的进一步成熟,促使其产品替代了喷气纺和涡流纺,甚至转杯纺的产品领域,将成为21世纪最具潜力的纺纱技术之一。
不同纺纱系统导致不同的纱线结构,纱线结构的差异是引起纱线性能变化的主要原因。纱线都可看成由纱芯纤维、包缠纤维、包缠—浮游纤维、腹带纤维和浮游纤维组成,不同纺纱系统导致各成分比例存在差异。就市场现有主要纱线种类,即环锭纺、转杯纺与喷气涡流纺而言,环锭纺的纱线是由均匀一致的芯纤维以螺旋方式构成的纱体;喷气涡流纺的纱线具有周期性包缠纤维,纱芯纤维基本平行排列无捻度,而纱芯纤维的末端被包缠纤维束缚,具有纱芯和包缠纤维的双层结构;转杯纱外观不同于前两者,纤维的组成难以分类。图1-8为喷气涡流纺纱的理想结构和SEM图。

图1-8 喷气涡流纺纱结构
纺纱速度、较大的喷嘴角度及喷气压力、较短的前罗拉与空心锭距将导致较大的纤维平均转移强度与频率;低纺纱速度导致纤维束在加捻区中停留时间延长,纱线结构紧密,喷嘴角度越大,纱线越均匀;低喷嘴角度,高喷气压导致纤维包缠纱芯更加紧密。
小的空心锭直径致使纤维包缠较紧密,捻度损失少,纱体紧密,毛羽少;牵伸条件变化带来单纤维须条平行伸直度的变化。建立喷气涡流纺工艺参数与纱线结构的关系,确定工艺参数与喷气涡流纺纱线的包缠纤维量、包缠角度、纤维转移强度的定量表达,是对喷气涡流纺纱线结构与性能设计的关键,最终可指导喷嘴结构设计与工艺参数优化。
二、包缠纤维对成纱性能的影响
喷气涡流纺与喷气纺,其纱线的形成都离不开包缠纤维,两者最大区别是包缠纤维的数量差异(图1-9)。对喷气纺与喷气涡流纺而言,在旋转气流作用下,从牵伸须条中分离的边缘纤维量存在差异,前者须条一直处于非自由状态,对单纤维控制较强。在一个捻回内,喷气涡流纺的纱线内包缠纤维所占面积与纱表面之比达0.57,这意味着喷气涡流纺的纱线表面一半以上都被包缠纤维包覆。

图1-9 包缠纤维数量对比
1.纱线外观
喷气涡流纺的纱线比环锭纺、转杯纺具有更高频率的粗细节;喷气涡流纺与转杯纺的纱线均匀性均好于环锭纱;喷气涡流纺的纱线毛羽比环锭纺和转杯纺纱线的少;喷气涡流纺的纱线表观直径较环锭纺和转杯纺纱线的好。喷气涡流纺的纱线具有环锭纺的纱线外观,比环锭纺具有更好的均匀性、较少的粗节和毛羽(图1-10)。造成喷气涡流纺纱线外观特性不同的主要原因是其具有高比例包缠纤维。喷气涡流纺纱线中的螺旋包缠纤维占纤维总数的60%,而喷气纺纱线中外包纤维仅占纤维总数的20%~25%。喷气涡流纺纱线中高比例的包缠纤维使得大量纱芯的尾端纤维束缚在纱体上,减少了头端造成的毛羽,同时,圈状的包缠纤维使得喷气涡流纺纱线外观蓬松,实质手感滑爽。由于纤维长度分布不匀、弯钩纤维及单纤维脱离前罗拉约束时间存在差异,造成喷气涡流纺纱线包缠不匀,这将直接导致其粗细节较环锭纺和转杯纺纱线多。对喷气涡流纺纱线外表包缠纤维的有效控制涉及喷孔角度、喷嘴直径、前罗拉与空心锭距、导引针的长短等工艺参数的优化。

图1-10 不同纺纱方法纱线的外观差异
2.织物的耐磨性和抗起球性
喷气涡流纺纱线制成的针织物耐磨性较环锭纺纱线制成的织物优越,但抗起球性能不如环锭纱织物好。造成该现象的主要原因是,喷气涡流纺纱中的包缠纤维在摩擦过程中制约了纤维的运动,对纱线的解体起着决定作用;反之,因喷气涡流纺纱线大量包缠纤维的存在,摩擦中易使包缠纤维自由头端纠集成球,若采用低强度的纤维,该现象能得到有效缓解。
3.纱线强伸性能
喷气涡流纺纱线的断裂伸长略低于喷气纺纱线,断裂强力却明显高于喷气纺纱线。主要原因是喷气涡流纺纱线的包缠纤维紧紧地包覆纱体内部纤维,对纱线的强力起关键作用。喷气涡流纺纱线断裂区域的主要特征是,疏松的、有圈状、折叠状的包缠纤维和纱线直径较小(细节),说明包缠纤维螺旋包缠角对喷气涡流纺纱线的断裂贡献不显著;喷气涡流纺纱线断裂强力高于喷气纺纱线。其主要原因是,喷气涡流纺纱线拥有更多的包缠纤维量,喷气涡流纺纱线中大量的包缠纤维对纱芯平行单纤维的束缚限制了纤维间的滑移,制约了喷气涡流纺纱线断裂过程中纱线的解体。喷气涡流纺纱线外表包缠纤维的转移频率与强度对纱线强力的贡献也存在一定的规律。
三、纱芯纤维对成纱性能的影响
1.纱线弯曲性能
喷气涡流纺纱线的抗弯刚度都比环锭纺大。包缠纤维对喷气涡流纺纱芯纤维包缠紧密,使得芯纤维弯曲时相互滑移较少,较环锭纺纱线螺旋状分布的纤维抗弯矩大。环锭纱纤维的内外转移次数多,纱线相互缠结,纱线的结构紧密,造成了纱线的直径变小;这样纱线的拉伸模量较大,纱线中纤维的填充系数高,弯曲刚度相应也较大;对于自由端纺纱来说,纤维的内外转移次数较少,纱线结构疏松,纱线之间相对滑移较多,具有较小的弯曲刚度值。
2.纱线导湿能力
根据纱线毛细管导湿理论,纱线中毛细管长度:
L0=L/cosα
(1-12)
式中:L0——纱中毛细管长度;
L——纱线长度;
α——纱线捻角。
纱中毛细管液态水输运流量Q:Q~1/L0
(1-13)
纱中毛细管液态水输运的线速度v:v~1/L0
(1-14)
喷气涡流纺纱由平行纱芯单纤维与外包纤维两个部分组成,因此,平行纱芯单纤维捻角为0,由式(1-12)知:纱中毛细管长度(L0)最小。由式(1-13)、式(1-14)可知:毛细管液态水输运流量(Q)最大、输运线速度(v)最大;同时,喷气涡流纺纱线的纱芯单纤维平行排列使得毛细管的数量可能在一定程度上比同支环锭纱多,液态水输运能力进一步提高。理论分析表明,喷气涡流纺纱线比环锭纺纱线具有更高的导湿能力。不同的纱线结构导致纱线性能的变化。目前,人们对喷气涡流纺纱线性能的研究还停留在定性描述纱线结构对纱线性能的影响上。喷气涡流纺纱线导湿性能的定量研究仅是形成喷气涡流纺纱线“结构—性能”模型的开始,还需进一步构建“结构—强伸性能”“结构—品质指标”“结构—起毛起球”等数学模型或结构模型,最终通过模型定量研究和分析喷气涡流纺纱线结构与性能的关系,为设计纱线结构提供理论依据和实践支撑。