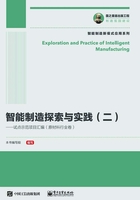
04 炼化智能工厂试点示范——中国石化镇海炼化分公司
一、项目实施背景与状况
(一)项目实施背景
炼化企业生产过程具有典型的流程化、连续性、物料关系极其复杂,以及高温、高压、易燃、易爆等特点。当前,国际炼化企业纷纷朝着大型化、一体化方向发展,产业集中度在不断提高;同时,生产安全、环境保护、油品质量等外部条件对炼化生产过程的要求也越来越高,如果没有信息化、智能化的手段作为支撑,企业将无法适应发展需要。中国石化镇海炼化分公司(以下简称“镇海炼化”)积极推进两化深度融合,建设智能工厂,实现企业快速升级转型,促进企业绿色低碳、健康环保高效发展,生产运行水平和经济效益持续保持国内领先地位。
通过实现智能化,企业能够根据市场波动不断对生产计划进行调整,能够准确地掌握生产中各个环节所产生的经济效益,跨领域进行团队的高效协作,有效地控制产品质量,使企业实现可持续、安全、环保及低碳的发展。
(二)项目实施的主要思路和目标
镇海炼化依托现有规模、成本、质量、技术等六大优势,以一系列重大管理变革和先进信息技术应用为主线,立足长远发展,确立智能工厂建设主要思路和目标:采取体制机制优化和业务流程再造,并不断采用新技术等变革,通过总体规划、分步实施,打造智能型炼化工厂。第一步,重点开展基础性工作,用3年时间完成试点建设,建成智能工厂应用框架;第二步,推广拓展,到2018年完成智能应用推广建设;第三步,智能化应用全覆盖,到2025年建成高度自动化、数字化、可视化、模型化和集成化的智能工厂。
项目整体技术达到国际先进、部分达到世界领先,装备与技术的国产化率达到80%以上,主要能耗、排放与产品质量指标、单位加工费用达到国际同类企业领先或先进水平,生产现场作业的劳动生产率提高20%,盈利能力继续保持国内领先。
二、项目主要实施内容和措施
围绕石化行业提质增效、转型发展,运用互联网、大数据、自动化等现代信息技术,建设以供应链—产业链—价值链协同优化驱动的炼化一体化生产智能制造示范工程,推动生产和经营管理模式变革,打造国际先进、国内领先的石化行业智能工厂。
项目主要实施内容如下:
(1)大数据驱动的企业运营智慧决策与管理。建立经营管理辅助决策系统和跨专业、纵向集成的管控一体化管理平台,以及融合知识、模型的企业管控体系。
(2)分子管理驱动的炼化一体化智能生产管控。实现从原油选择与调和、加工、成品油调和生产链的智能优化管控。
(3)面向绿色低碳发展的企业安全环保与能源智能化管理。实现废弃物、污染物和高危化学品的全生命周期足迹跟踪、溯源与调控,以及资源和能源的循环利用与清洁生产。
(4)面向高端制造的工艺流程创新与质量控制。通过装备的高端化改造和工艺流程的优化,研发高端产品,提高具有竞争力的生产能力,并对产品质量进行全生命周期管理,实现向价值链高端跃升。
(5)面向开放共享的上下游产业链协同优化。镇海炼化智能工厂与宁波化工园区、宁波智慧城市建设相结合形成“三位一体”,进一步拓展和整合供应链、产业链和价值链,促进上下游产业与宁波市临港工业的协同发展。
项目实施采取的主要措施如下:
1.经营决策智能化
在生产绩效管理模型的基础上扩展和完善,建设辅助决策管理系统,利用大数据技术,对企业生产经营数据进行统一的管理分析,为企业各级管理人员提供完整的、关联的、警示性的数据决策依据。建立业务流程管理(BPM)体系,包括以“制度”为核心的问题管理系统、以“流程”为核心的任务管理系统和以“价值”为核心的绩效管理系统,形成制度执行、任务落实和价值创造过程的全面管控体系。
(1)辅助决策。基于大数据的决策管理,以效益最大化为目标,针对生产经营过程中积累的海量数据,建设数据中心,运用大数据分析,并与生产运行实时数据、市场需求信息相关联,对日利润和生产成本进行实时分析预测,快速响应变化。
(2)业务流程管理。通过建设业务流程管理系统,加强部门之间的协作,实现投资管理、物资管理、配送管理等38类126条业务全流程的线上审批,同步开发了手机、iPad等移动终端办公平台,集成各类系统待办事项,通过移动短信网实现待办事项的定时短信推送提醒。
(3)督办管理。对承接各项工作任务的单位纳入系统管理,各环节协同配合完成任务。督办管理分为创建、承办、跟踪提醒、评价考核4个环节,实现了列入公司各项重要工作部署及生产经营重点工作决策的督办事项从发起、承办、过程跟踪、预警监控、评价考核的全过程在线管理。
2.生产运行智能化
建成全生产过程优化体系,生产计划优化主要采用PIMS,日生产计划优化主要借助ORION;在全流程安排上,利用RSIM(炼油)、SPYRO(化工)等流程模拟软件,实现全流程生产方案和效益最佳。主要生产装置投用了APC,乙烯装置建成了实时在线优化(RTO)系统。依托SMES将日计划转化为调度指令,实现指令从公司级调度→储运/港储调度→内操→外操的指令在线闭环管理,调度指令与SMES 3.X物料移动实时同步、业务联动。生产运行智能化架构如图4-1所示。

图4-1 生产运行智能化架构
(1)计划优化智能化。计划排产对于流程化、连续性、物料关系极其复杂的炼化企业至关重要。为确保装置、系统在平稳运行下生产最优,实现企业效益最大化,镇海炼化以“分子管理”为指引,以“整体效益最大化”为原则,通过智能化手段按不同的分子结构来精确定位物料流向,优化加工流程,提升了每个分子的价值和利用效率。
(2)生产操作智能化。在15套主要生产装置应用先进过程控制(APC)技术,实时检测诊断装置工况,动态自动优化运行参数。乙烯裂解装置和重油催化装置不仅投用了APC,而且建成了实时在线优化(RTO)系统,时刻确保装置按照效益最大化的方式运行。通过近红外光谱预测计算原油评价数据,在线优化调和12组原油并定向直送常减压装置,极大地提高了装置平稳率,降低了一线员工的劳动强度。
(3)生产管理智能化。升级完善生产管理平台SMES 3.X,集调度指挥、物料管理、能源管理于一体;实现调度自上而下、物料移动自下而上的业务流程自动化;创新物料统计平衡模式,实现班组、调度、统计数出一门。系统完整覆盖全公司生产业务调度指令流转体系,将日计划转化为调度指令,实现指令从公司级调度→储运/港储调度→内操→外操的指令在线闭环管理,调度指令与SMES 3.X物料移动实时同步、业务联动。
3.设备管理智能化
坚持“全生命周期管理”管理理念,首先通过工程管理信息系统,实现从立项→设计→采购→施工→验收的工程项目的全过程管理。工程建完后,一方面工程模型交付三维数字工厂;另一方面实物交付生产运行,开始设备的健康、可靠性和日常维修的管理,并建立装置检修项目立项、承包商、费用、合同和技术的“五流合一”管理,提高工作效率。设备管理智能化业务架构如图4-2所示。

图4-2 设备管理智能化业务架构
(1)建设工程管理。以中国石化颁布“3557”项目管理体系和《中国石化项目管理手册(标准模板)》为依据,以镇海炼化“三项制度”为基础,以标准化为手段;按照“统一标准、统一设计、分期建设、重点突破、有序推进”的思路,扎实推进工程建设管理信息系统试点项目建设。该项目是中国石化试点建设项目,填补该领域信息化的空白,实现工程项目管理“数字化”及工程“数字化”交付。
(2)数字工厂建设。利用正逆向建模、三维虚拟现实等技术对作为实物存在的设备、管道等用三维模型的方式进行展现,并以三维模型作为载体,集成工程建设阶段、运行维护数据,形成了“所见即所得”的设备管理平台。通过“虚拟工厂”与“现实工厂”之间的交互,使设备特性参数、工艺参数可视化有机地联系起来,为设备、生产、安全环保的业务三维应用提供数据支撑和可视化环境,使方案全景模拟成为可能,极大地推动了设备管理向现代管理模式迈进。同时也可为生产管理、安全管理、培训管理提供最方便、简洁的工具与方法,极大地提高了装置管理水平。
(3)设备预知性检维修。应用在线监测技术,自动诊断设备故障,预测设备剩余寿命,智能诊断设备故障,为设备预知性维修提供全面支持。例如,给重要机泵都安装了在线监测系统,实时进行状态监控,做好故障分析,及时发现隐性故障,做到预知性维修。又如,建设投用设备腐蚀监测系统,选取重要装置关键部位实施在线定点检测腐蚀速率,使管理人员能主动分析腐蚀情况,对腐蚀险情做到早发现、早处理。应用世界先进的基于风险的检测(RBI)、以可靠性为中心的维修策略分析(RCM)、安全完整性等级分析(SIL)等可靠性分析工具,对设备风险和可靠性进行分析,并据此编制设备的预防性检修预案,为检修计划的编制、故障的处理提供科学的依据。
4.绿色环保管理智能化
应用环保在线监测系统,对排放口位置、风险源、废水废气、污染物移动等智能实时分析监测及报警管理,营造企业友好的生态环境。运用能源管理系统,对能源的计划、生产、转换、使用、优化、考核等各方面进行管理,在线监控各类介质消耗,实现能效倍增。绿色环保管理智能化架构如图4-3所示。
(1)绿色生产智能化。建设投用环保在线监控系统实时监视各个环境监测点的环境监测数据,为管理人员及时做出相应的决策提供数据支持,提升企业环境监控能力。对污水、烟气排放等污染源实施24小时在线监测,监测数据直接与地方环保局和中国石化总部联网,发现异常情况及时反馈和处理。应用国际先进的泄漏检测与修复(LDAR)技术,以200mg/m3作为泄漏认定标准,形成了完备的泄漏检测与修复程序,改善了作业环境空气质量。配置了环境流动监测车,采用当前国际上最先进的离子分子反应质谱技术,分析精度达到ppb级(百万分之一),监测因子覆盖石化企业所有污染物,并配备卫星定位系统、气象测试系统和数模系统,能快速准确地锁定污染源。

图4-3 绿色环保管理智能化架构
(2)能源在线优化。建立了51套主要装置的实时能源消耗平台,包括蒸汽、瓦斯、氢气、电力等模块,实时监视所管辖装置的能耗以及每一个操作对装置能耗的影响,装置自身能源消耗的变化趋势。系统不仅保障了企业安全、平稳生产,也为节能减排做出了卓越贡献。
5.健康安全管理智能化
建设统一视频监控平台实现工业现场视频监控和事故联动管理;运用物联网和智能巡检等技术对现场作业、关键部位进行实时监管,实现异常主动预警、危害定量分析、隐患在线监控;完善应急指挥体系,建立远程专家支持系统,提高快速响应和协同处置能力。
(1)安全生产智能化。针对炼化企业易燃易爆、有毒有害的特点,在有可能产生有毒气体和可燃气体泄漏的危险源共安装了2 467台固定式和可燃气体报警仪;在关键生产装置、要害部位安装了工业电视系统,共878个摄像头和红外等多重监控设施。同时,上述仪表信息整合集成到自动报警管理系统,连锁回路达到10 752个。另外,还自主开发并投用一键停车系统16套、紧急停车辅助系统28套,打造了装置在紧急情况下的“安全着陆系统”。
(2)风险管控智能化。利用信息技术从关键装置、职业危害场所、环境排放等方面对HSE(健康、安全、环境)管理过程的风险防范能力进行提升,从应急联动、应急辅助决策、三维事故模拟和虚拟演练等方面进行应急指挥业务的整体提升,有效提高企业在HSE管理过程的监管、监控水平和应急能力。
6.上下游产业协同智能化
以物料、产品和能源为纽带,与宁波化工园区企业全面对接产业链,完善CRM;通过物流管理平台,监控危化品车辆运输,共享产耗和库存信息,建立循环经济,使智能工厂与宁波化工园区、智能制造城市建设相结合,形成“三位一体”,促进上下游产业与城市的协同发展。
(1)跨厂区、跨企业的区域生产管理。镇海炼化自主建设了生产运行监控平台,全程监控全局生产运行,包括园区互供料,并与园区企业分享监控数据。通过系统随时掌控物料流向、质量分析、系统平衡、产品进出、工艺指标等情况;与协作单位的生产运行及计量等数据实时交换,实现物流、物料流、信息流同步共享。
(2)进出厂物流智慧化。建成并投用进出厂物流管理系统,自动化优化承运商网上预约提货时间段,为公司最终缩小西区停车场提供了实用工具和有效手段;对危化品车辆、驾驶人等资质进行线上审查,利用移动设备实现装车过程检查并实时掌握车辆位置动态信息;借助数据集成平台,利用功能强大的统计报表和图形工具,为供应链管理提供辅助决策支持。
三、实施成效
(1)研制一批国际先进、国内领先的国产软件系统。镇海炼化在智能工厂建设过程中,非常注重利用现有成熟技术,以及联合华东理工大学等科研院校及石化盈科、东海蓝帆等石化行业领先IT企业创新研发流程行业智能应用软件系统。2015年,原油调和、SMES 3.X、工程项目管理、三维数字工厂、智能管线、设备可靠性及健康管理、视频统一平台、数据仓库ODS、企业数据共享服务总线ESB、云平台等智能工厂重点项目“十条龙”陆续出笼,均为流程型行业首创,智能化水平达到国际先进、国内领先。
(2)建立智能工厂标准化模板。镇海炼化不断总结智能化建设、应用及管理经验,在智能工厂建设过程中以最佳业务实践探索企业各个领域业务智能化,并进行标准化,形成了信息代码标准、数据指标标准、数据仓库ODS、企业数据共享服务总线ESB、工业分析、绩效管理、能源管理、三维数字平台、设备故障诊断与预测、设备可靠性、调度指挥等智能工厂标准化模板。
(3)企业竞争力进一步提升。智能工厂建设对镇海炼化的发展和经济效益具有良好的持续推动作用,充分发挥了供应链—产业链—价值链协同优化的效果,不仅提高镇海炼化核心竞争力,也促进了宁波地区石化下游产业链的快速形成,成为推动临港石化产业转型和发展海洋经济的引擎。2015年,镇海炼化实现利润108.41亿元,创中国炼化行业新纪录。
四、实施经验
(1)关注业务整合协同。智能工厂是两化深度融合的高级阶段,需要不断地整合优化业务,坚持信息技术与每一项业务、每一个环节、每一位员工融合,可以实现从“复杂烦琐”到“简单方便”的智能化转变。
(2)关注数据资源。智能工厂建设需要大量的数据资源,不仅仅要在系统整合集成上下功夫,更要在应用平台化上下功夫,实现业务全自动化流转,确保信息流高效、畅通和共享,更好地为生产经营提供预警及决策支持。
(3)关注信息安全。智能工厂建设为信息安全工作提出了新的课题,既要保证内部网的整体信息安全,又要保证必需的性能和管理的方便性。要从网络的整体性能和信息系统的整体安全出发,充分发挥信息系统的整体效能,要按照信息化建设和应用的要求,坚持统一规划、通盘考虑、统一标准、统一管理。
(金登峰、陈彬 供稿)