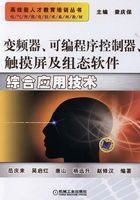
1.3 异步电动机的调速传动
由于直流电动机使用存在局限性,所以构造简单的异步电动机调速传动得到了迅速发展。
1.3.1 三相异步电动机的工作原理
三相异步电动机的定子上装有绕组,转子有绕线型与笼型两种,图1-6表示一台三相笼型异步电动机模型。电动机定子上装有互差120°的U、V、W三相绕组,转子为一个圆柱形的笼条。
图1-6 异步电动机模型
当三相绕组通以UU、UV、UW三相对称交流电压后,就产生三相互差120°的三相对称交流电流,其波形如图1-7上部所示。当在时刻“1”时U、W两相为正,V相为负,磁场如图1-7下部所示,当在时刻“3”时U、V两相为正,而W相为负,其磁场旋转了120°。同理在时刻“5”磁场又旋转120°,如此形成了旋转磁场。电源频率f1=50Hz时,流入定子绕组的三相对称电流就将在电动机的气隙内产生一个以转速为n0=60f1/pn的旋转磁场。当转子导体被此旋转磁场的磁力线切割时,导体内将产生感应电动势,在转子回路闭合的情况下,转子导体中就有电流流通。根据载流导体在磁场中产生电磁力的作用,用左手定则就可以判断出转子受到了一个与旋转磁场同方向的转矩。当此转矩大于转轴上的阻力矩时,转子就转动起来,这就是异步电动机的基本工作原理。
图1-7 三相交流波形及旋转磁场
电动机转子转动的方向与旋转磁场的方向虽然相同,但它们的转速却不相等,因为如果相等,转子导体就不可能切割磁力线,转子电动势、电流就不存在,当然转矩也就没有了。所以转子的转速一定小于旋转磁场的转速,这就是异步电动机名称的来源。如果在外力拖动作用下,转子的转速大于旋转磁场的转速,则电动机就成了发电机。如果用n0表示旋转磁场转速,n表示电动机轴实际转速,s表示转差率,则
s>0为电动运行;s<0为发电运行。
1.3.2 异步电动机的电磁转矩及自然机械特性
1.异步电动机的电磁转矩
异步电动机的电磁转矩公式,可以根据电磁关系进行定性分析而得出转矩基本表达式;进行定量分析得出转矩特性表达式。
(1)转矩基本表达式
三相异步电动机的转矩T是由转子感应电流I2与气隙旋转磁通相互作用产生的,因此转矩的大小与气隙磁通及转子感应电流I2的大小有关,此外,转矩的大小还与转子回路的功率因数cosΦ2有关,下面分别来看几种情况。
图1-8a是假设转子回路为纯电阻性的,即cosΦ2=1的情形,用右手定则可以确定转子导条感应电动势E2的方向。由于cosΦ2=1,I2与E2同相位,所以I2方向与E2方向一致。有了电流方向,即可用左手定则确定各导条的受力方向。
图1-8 异步电动机转矩与cosϕ2关系
a)cosΦ2=1 b)cosΦ2=0 c)0<cosΦ2<1
可以看出,cosΦ2=1时,作用在所有导条上的力产生的合成转矩使转子向同一方向旋转。再看图1-8b,假设转子回路为纯电感性的,即cosΦ2=0,此时I2比E2落后90°,各导条中电流方向如图所示,作用于转子各导条的力产生的转矩恰好互相抵消,合成转矩为零,转子不会转动。
实际上,转子回路既不是纯电阻性的,也不是纯电感性的,图1-8c所示为实际情况,I2落后于E2一个Φ2角,也就是0°<Φ2<90°,即0<cosΦ2<1。此时各导条所受力产生的转矩,有一部分互相抵消,剩下的部分仍使转子沿n1的旋转方向旋转。在同样的电流和磁通下,产生的转矩较cosΦ2=1时小。
可见,转矩与转子电流的有功分量成正比,用公式表达为
T=CtΦ1I2cosΦ2 (1-18)
式中 Ct——异步电动机结构系数;
Φ1——每极磁通;
I2——转子电流。
式(1-18)是异步电动机的电磁转矩的基本表达式。
(2)转矩特性表达式
从式(1-18)可知,异步电动机的电磁转矩主要由Φ1、I2与cosΦ2决定,而Φ1、I2与cosΦ2又分别由下列条件决定。
1)主磁通Φ1:从图1-9所示的异步电动机的单相等效电路可以计算出Φ1的数值,先求证定子反电动势E1。
一根导体电动势的有效值Ec1可以根据电磁力确定如下:
图1-9 异步电动机单相等效电路
式中 l——导体长度;
v——导体运动速度;——磁通密度有效值。
若定子内径为D(m),转子的转速为n(r/min),则导体运动速度(m/s)为
式中 pn——电动机的磁极对数;
τ——电动机极距,τ=πD/(2pn)。
把式(1-20)代入式(1-19)可得
Ec1=2fB1lτ (1-21)式中 f——电源频率,f=pnn/60。
考虑磁场在空间是正弦分布的(见图1-10),一个磁极下的平均磁通密度为
图1-10 磁场空间正弦分布
一个磁极下的磁通Φ1=平均磁通密度乘以每磁极下的面积,如图1-10所示。
于是,一根导体电动势的有效值可进一步改写成如下形式:
一匝线圈为两根导线,所以一相N匝导线产生的电动势为
E1=4.44NfΦ1 (1-25)
从式(1-25)可知磁通的表达式为
如果不考虑定子绕组的损耗,即U1≈E1,磁通的近似表达式为
2)转子电流I2:从图1-9所示的异步电动机的单相等效电路可以计算出I2的数值为
式中 E2=4.44f2N2Φ1。
又因s=f2/f1;当转子起动瞬间,n2=0时,s=1,f2=f1,旋转磁场以最大速度切割转子绕组,此时转子的感应电动势最大,用E20表示。同时,转子的频率也最高,感抗也最大,用X20表示。
E20=4.4 f1N2Φ1 (1-29)
X20=2πf1L2 (1-30)
不难分析
E2=sE20≈sE1≈sU1 (1-31)
X2=sX20 (1-32)
将式(1-31)、式(1-32)代入式(1-28)得
可见,转子电流大小也与s有关,当s=0时,I2=0。其物理意义是转子转速达到同步转速时,转子没有电流。
当s从小到大增加时,起初由于s较小,r2/s≫X20,所以式(1-33)分母中的X20可以忽略,因而可以近似认为
即I2与s成正比。当s再增加时,r2/s值变小,X20不能忽略。而当s接近于1时,(r2/s)2值接近r22值,I2值变化不大,近似于常数,据此可画出I2与s的变化的曲线,如图1-11所示。
3)转子回路的功率因数cosΦ2:由于转子电路中X2的存在,使转子电流I2落后转子感应电动势E2一个角度2,因而转子回路的功率因数为
同理,当s从小到大增加时,起初sX20很小,可以忽略不计,cosΦ2值接近于1;当s再增加时,sX20也就较大,不能忽略,同样可画出cosΦ2与s的变化曲线,如图1-12所示。
图1-11 异步电动机I2、cosΦ2与s的关系
图1-12 异步电动机I2、cosΦ2、T与s关系
把式(1-27)、式(1-33)和式(1-35)代入式(1-18)中得
这就是电动机转矩特性的表达式,它表明电动机转矩与定子每相电压U1的二次方成正比。所以,电源电压波动时,对电动机的转矩影响很大。异步电动机工作时,电源电压不宜在过大的范围内波动。在额定负载情况下,电动机的端电压变化率不得超过-5%~+5%。电压过高过低都会使电动机电流增加,导致发热增加。
2.自然机械特性曲线
在对异步电动机的运行特性进行分析时,经常要用到电动机的机械特性曲线,所谓电动机的自然机械特性曲线是指在额定的电源电压U1和转子固有电阻r2之下,转矩与转差率的关系曲线,由于转子感应电流I2及转子回路的功率因数cosΦ2都与转差率s有关,因此从公式T=CTΦ1I2cosϕ2可知,转矩T也是与转差率有关的。在不同的转差率下,电动机有不同的转矩输出,转矩T随转差率的变化曲线,可由转子回流I2与转子回路的功率因数随cosϕ2变化的曲线上直接作出,如图1-12所示。
从图1-12可见,在电动机起动瞬间s=1,起动电流虽然很大,但因功率因数cosΦ2很小,I2与cosΦ2的乘积并不大,因此起动转矩TQ不大;当电动机起动以后,转子的转速逐渐升高,转差率s逐渐减少,I2也逐渐减少,但cosΦ2逐渐增大,而且cosϕ2增大的影响比I2减少的影响要大,所以I2与cosΦ2的乘积是逐渐增大的,也就是说,转矩是逐渐增大的;当转速上升到某一值时,电动机产生的转矩最大,即Tmax,当过了这一转速后,I2迅速减少,T开始减少;当s=0,转速达到同步转速时,cosΦ2≈1,但是I2=0,所以转矩为零。
为了分析方便起见,可以将图1-12所示的T-s特性曲线换成n-T特性曲线,这只须将T-s曲线顺时针方向转过90°,再将表示T的横轴移下即可,如图1-13所示,此特性曲线是三相异步电动机的机械特性曲线的另一种形式。
现在我们来看电动机是如何带动负载进行起动的。
假设电动机带动一恒转矩负载(额定值)进行起动,负载的转矩曲线如图1-13所示。在起动瞬间,由于电动机起动转矩TQ大于负载转矩TL,于是电动机升速,沿着机械特性曲线上升。随着转速的上升,电动机的转矩在不断地增加,当电动机的转速到达某一值后,电动机产生的转矩达到最大(Tmax)。超过此转速后,电动机的转矩又开始减少,而且逐渐向负载转矩靠近,当电动机的转矩等于负载转矩时,电动机不再升速,这时电动机便稳定地运转于A点这一转速,起动过程结束。
图1-13 异步电动机TQ、TN、Tmax的关系
从上面的分析可以看到,在异步电动机机械特性曲线上有3个转矩点是在应用和选择电动机时最为关注的。
1)额定转矩TN:额定转矩TN(N·m)是指电动机额定状态工作时,轴上输出的转矩,电动机的额定转矩TN可根据其铭牌所标的额定功率PN(kW)和额定转速nN(r/min)求得
2)最大转矩Tmax:电动机在某一转速下产生最大转矩,这时所对应的转差率称为临界转差率sm,电动机的最大转矩应大于额定转矩,但不能太接近,否则电动机略一过载,便立即停转。因此,一般电动机的额定转矩要比最大转矩小得多。它们的比值叫做电动机的过载倍数,用符号Km表示。
异步电动机的过载能力一般为1.8~2.5。起重、冶金、机械用的电动机过载系数较大,可达2~3。
3)起动转矩TQ:电动机的起动转矩TQ是指电动机刚刚要起动时的转矩,起动转矩越大,则电动机的起动能力越好。一般在产品目录中,用KQ来表示电动机的起动能力,称为起动转矩倍数。
一般三相笼型异步电动机的起动能力为额定转矩的1.1~1.3倍,与绕线转子异步电动机相比,笼型异步电动机的起动能力较差。
1.3.3 异步电动机的调速方法
从异步电动机的转速关系式n=n0(1-s)=60f1(1-s)/pn可知,若要改变异步电动机转速,可以有以下3种方法:
①改变电动机的极对数pn,以改变电动机的同步转速n0,从而达到调速的目的。这种调速方法称为变极调速;
②改变电动机的转差率s,可采取的方法很多,如对笼型异步电动机,改变定子电压及电磁型调速、绕线转子异步电动机改变转子电阻或电动势等;
③改变异步电动机的电源频率f1,以改变n0进行调速,称为变频调速。
1.3.4 异步电动机的调速特性
1.变极调速
在电源频率f1不变的条件下,改变电动机的磁极对数,电动机的同步转速n0就会发生变化。电动机的磁极对数增加一倍,同步转速就降低一半,电动机的转速也下降一半,从而得到转速的调节,如图1-14所示。
图1-14 改变磁极对数的转矩特性
要改变电动机的磁极对数,可以在定子铁心槽内嵌放两套不同极数的三相绕组,从制造的角度看,这种方法很不经济。也可以利用改变定子绕组的接法来改变磁极对数,这种电动机称为多速电动机。多速电动机均采用笼型转子,因为这时转子的极数能自动地与定子极数相适应。多速电动机变极后,前后的极数比为整数,称为倍极比,如4极变8极,2极变4极等,否则就称为非倍极比,如4极变6极。一般对倍极比变极,变极后绕组的相序将发生变化,为了使电动机的转向不变,则在绕组改接时,应把接到电动机的3根电源线任意对调两根。对于非倍极比变极,绕组的相序可能变也可能不变,若相序改变,也应按倍极比的情况处理。
变极调速因为转速几乎是成倍地变化的,因此调速的平滑性差。但它在每个转速等级运转时,和通常的异步电动机一样,具有较硬的机械特性,稳定性较好,所以对于不需要无级调速的生产机械(如金属切削机床、通风机、升降机等),多速电动机得到比较广泛的应用。
2.调转差率调速
调转差率s实现调速主要有下列方法:
(1)笼型电动机的定子调压法和电磁转差离合器调速法。
1)定子调压调速法:根据异步电动机的机械特性方程式
可知,当转差率s一定时,电磁转矩与定子电压的二次方成正比,这就说明在不同的定子电压下,可以得到一组不同的人为机械特性,如图1-15所示。带恒转矩负载TL时,可得不同的稳定转速,如图中的A、B、C点。由于普通异步电动机工作段转差率s很小,因此对轻负载来说,调速范围很小。但是,对风机、泵类机械,由于其负载特性为TL=kna(a>1),采用调压调速则可得到较大的调速范围,如图1-15的D、E、F点。
图1-15 调压机械特性
所谓调压调速,就是通过改变定子外加电压来改变其机械特性的函数关系,从而达到改变电动机在一定输出转矩下转速的目的。
定子调压调速的方法有:定子串电抗、串电容、星/三角联结与晶闸管调压法等。在电动机调压调速诸多方法中,以晶闸管调压法最好。
由于异步电动机在低压时的机械特性很软,故工作不易稳定,负载稍有波动,就会引起转速很大变化。为了提高调压调速系统机械特性的硬度及电动机转速的稳定性,常采用闭环控制系统,图1-16a为转速闭环调压调速系统的原理图。
图1-16 转速闭环调压调速系统
a)原理电路 b)静态特性 ASR—转速调节器 GT—触发装置 TVC—双向晶闸管交流调压器
图1-16b是该调速系统的静态特性,这样的静态特性由于具有一定的硬度,所以不但能保证电动机在低速下的稳定运行,而且提高了调速的精度、扩大了调速的范围,一般可达10∶1。
2)电磁调速法:电磁调速法是用电磁调速电动机(也叫转差电动机或电磁转差离合器)进行调速。
转差电动机调速系统,是由笼型异步电动机、电磁转差离合器以及控制装置组合而成的。为改善其运行特性,常加上测速反馈形成反馈控制系统。笼型异步电动机作为原动机以恒速带动电磁离合器的电枢转动,通过对电磁离合器励磁电流的控制实现转速调节。
从结构上说,电磁转差离合器可分为单电枢感应子式和单电枢爪极式两种。它们的区别在于分别是同极性与异极性的磁场分布,因此磁路的机座材料也有所不同,前者用低碳钢,后者可用铸铁。但它们的工作原理是相同的。
图1-17为单电枢感应子式电磁转差离合器的结构示意图。
图1-17 电磁转差离合器结构
1—直流励磁绕组 2—机座 3—电枢 4—磁极 5—主动轴 6—从动轴 7—导磁体 8—磁通路径
它主要由电枢、机座、磁极、励磁绕组、导磁体所组成。一般可把它和交流原动机与测速发电机装成一个整体。图1-17中,1是直流励磁绕组,由控制装置送来的可变直流电压供电,产生固定磁场。2是机座,它既是离合器的结构体又是磁路的一部分。3是电枢,它为圆筒形实心钢体,兼有导磁、导电作用。它直接套在作为原动机的异步电动机的主动轴5的轴伸上,作为主动转子。运行时,在电枢中感应电动势并产生涡流。在电枢上同时还铸有风叶,以获得良好的散热效果。4是磁极,在单电枢感应子式结构中,它是齿轮形状,由低碳钢铸成,因此也称为齿极。它作为从动转子固定在从动轴6上而输出转矩。异步电动机作为原动机可与电磁转差离合器组成一个整体。7是导磁体,它既是结构体,又是磁路的一部分。
当励磁绕组通以直流电时,沿封闭的磁路就产生了主磁通,磁力线如图1-17中虚线8所示。它通过机座→气隙→电枢→气隙→磁极→导磁体→机座而形成一个闭合回路。由于磁极断面有齿有槽,在齿凸极部分分布的磁力线较密,而在槽间分布的磁力线较稀,因而沿气隙圆周上建立起空间的脉动磁场。由于电枢为原动机所拖动,以恒速定向旋转,因此电枢与磁极间有相对运动,电枢切割磁场,从而在电枢中产生感应电动势,并产生电流。此涡流是交变的,并产生一个幅向脉动的电枢反应磁场,它与主磁通的合成产生电磁力。此电磁力所形成的电磁转矩将驱使磁极跟着电枢同方向运动,这样磁极就带着生产机械一同旋转。主动轴的转速n1由异步电动机而定,由于异步电动机的固有机械特性较硬,所以认为n1为恒值。而从动轴的转速n的大小取决于磁极与电枢耦合力的大小,亦即取决于励磁电流的大小,当然也与从动轴的负载大小有关。对恒定负载,励磁电流越大,则从动轴的转速越高;而在恒定励磁电流下,负载越大,则从动轴的转速越低。所以调节励磁电流就可改变从动轴的转速。
但从动轴的转速始终低于n1,因为若没有n1-n这个转速差,那么电枢中就不可能产生涡流,也就没有电磁转矩了。同样,当磁极中不通励磁电流时,磁极也就不会转动,这相当于接在从动轴上的工作机械与主动轴“分离”;而一旦通上电流,磁极就会转动,相当于工作机械与主动轴“接合”,从而起到离合器的作用。因为这种“分离”与“接合”都是靠电磁作用产生的,故称为“电磁转差离合器”。将它与异步电动机合起来可称为转差电动机。必须指出,电磁转差离合器本身并不是一个原动机,只是一种传递功率的装置。
在不加反馈控制时,调速系统的机械特性就是电磁转差离合器的机械特性。由于转差离合器的工作原理与异步电动机相似,所以它们两者的调速特性也相似。
图1-18为电磁转差离合器机械特性,它是不同励磁电流时的一簇机械特性。也可用经验公式来表示为
式中 n1——原动机转速;
Te——电磁转差离合器轴上输出转矩;
IL——电磁转差离合器的励磁电流;
K——与电磁转差离合器结构有关的系数。
从图1-18可知,其机械特性很软,所以调速性能很差。如同调压调速系统一样,在工业中使用时,都加以转速反馈控制,从而可获得10∶1的调速范围。
由于这种调速系统控制简单、价格低廉,因此可广泛应用于一般的工业设备中。但由于它在低速运行时损耗较大、效率较低(高速时效率仅为80%~85%),所以特别适用于要求有一定调速范围又经常运行在高速小容量的装置中。
图1-18 电磁转差离合器机械特性
(2)绕线转子异步电动机的转子回路串电阻调速法与转子回路串电动势调速法。
1)转子回路串接电阻调速:这是用改变电动机转差率s进行调速的方法之一,它只能适用于绕线转子异步电动机。串接电阻的形式有水电阻、金属电阻与频敏电阻。
图1-19 绕线转子电动机串接电阻机械特性
图1-19绘出了电动机的固有特性和转子回路串接电阻时的人为特性。串入电阻后,电动机的工作点便由原来的A点移到人为特性的B点或C点,调速过程与直流电动机电枢回路串电阻调速相同。串接电阻调速方法的缺点是不能无级调速,并且浪费电能。
2)串级调速:对于绕线转子异步电动机,可通过在转子回路中串入附加电阻来改变转差率,实现调速,这种调速方法,因串入附加电阻而增加的转差功率以发热的形式消耗在附加电阻上,因此属于转差功率消耗型调速方法。如果在转子回路中串入附加电动势,同样也可以改变转差率而实现调速,这种方法称为串级调速。这种调速方法,因串入附加电动势而增加的转差功率回馈给电网或者回馈到电动机轴上,因此属于转差功率回馈型调速方法。串级调速的方法使系统获得较高的运行效率,曾经得到广泛应用。
下面分析串级调速的原理。假定异步电动机在自然机械特性上稳定运行,电源电压和负载转矩均不变。转子电动势为E2=sE20,转子电流I2的值为
式中 E20——s=1时,转子开路相电动势;
X20——s=1时,转子绕组的相漏抗。
当在转子中串入与E2同频率、反相的附加电动势Ef时,转子合成电动势为sE20-Ef。转子合成电动势的减小必然引起转子电流I2减小,相应地,使电动机转矩T=CtΦI2cosφ2也减小。电动机转矩小于负载转矩,迫使电动机降速,则转差率s增大。当s增大到某值s′时,使s′E20-Ef与sE20大小相等,I2回升到原值,电动机转矩与负载转矩重新达到平衡,电动机稳定运行在低于原值的某一转速上。这就是向低于同步转速方向调速的原理。
当串入与sE20同频率、相位相同的Ef时,转子合成电动势增大为sE20+Ef,I2和T都相应增大,使电动机升速,转差率s减小。当s减小到s′时,使s′E20+Ef=sE20时,电动机转矩与负载转矩重新达到平衡,电动机稳定运行在高于原值的某一转速上。若串入的Ef值足够大,就会使s′<0,电动机稳定运行在高于同步转速的某一转速上。这就是向高于同步转速方向调速的原理。
典型的电气串级调速系统称晶闸管串级调速系统,其基本构成如图1-20所示。
图1-20 绕线转子异步电动机串级调速电路
系统中,直流附加电动势Eβ是由晶闸管有源逆变器UI产生的,改变触发超前角β就改变了逆变电动势,相当于改变了直流附加电动势Eβ,实现串级调速。在不考虑损耗的情况下,这种调速系统电动机轴输出机械功率PM=(1-s)P2,角速度ω=(1-s)ω0,则电动机输出转矩为
可见,电气串级调速系统具有恒转矩调速特性。
图1-21所示为晶闸管串级调速系统的机械特性曲线,由图可见,串级调速系统的机械特性比异步电动机的自然机械特性软。
串级调速系统的优点是:当转子吸收电源能量时,可以高于同步转速调速;当电动机低于同步转速时,它可以把转差损耗的能量改变为电能而馈送回电源。串级调速的缺点是设备投资费用大、操作不方便。
图1-21 绕线转子电动机串级调速系统的机械特性曲线